甲醇制氢装置操作规程Word文档格式.docx
《甲醇制氢装置操作规程Word文档格式.docx》由会员分享,可在线阅读,更多相关《甲醇制氢装置操作规程Word文档格式.docx(55页珍藏版)》请在冰豆网上搜索。
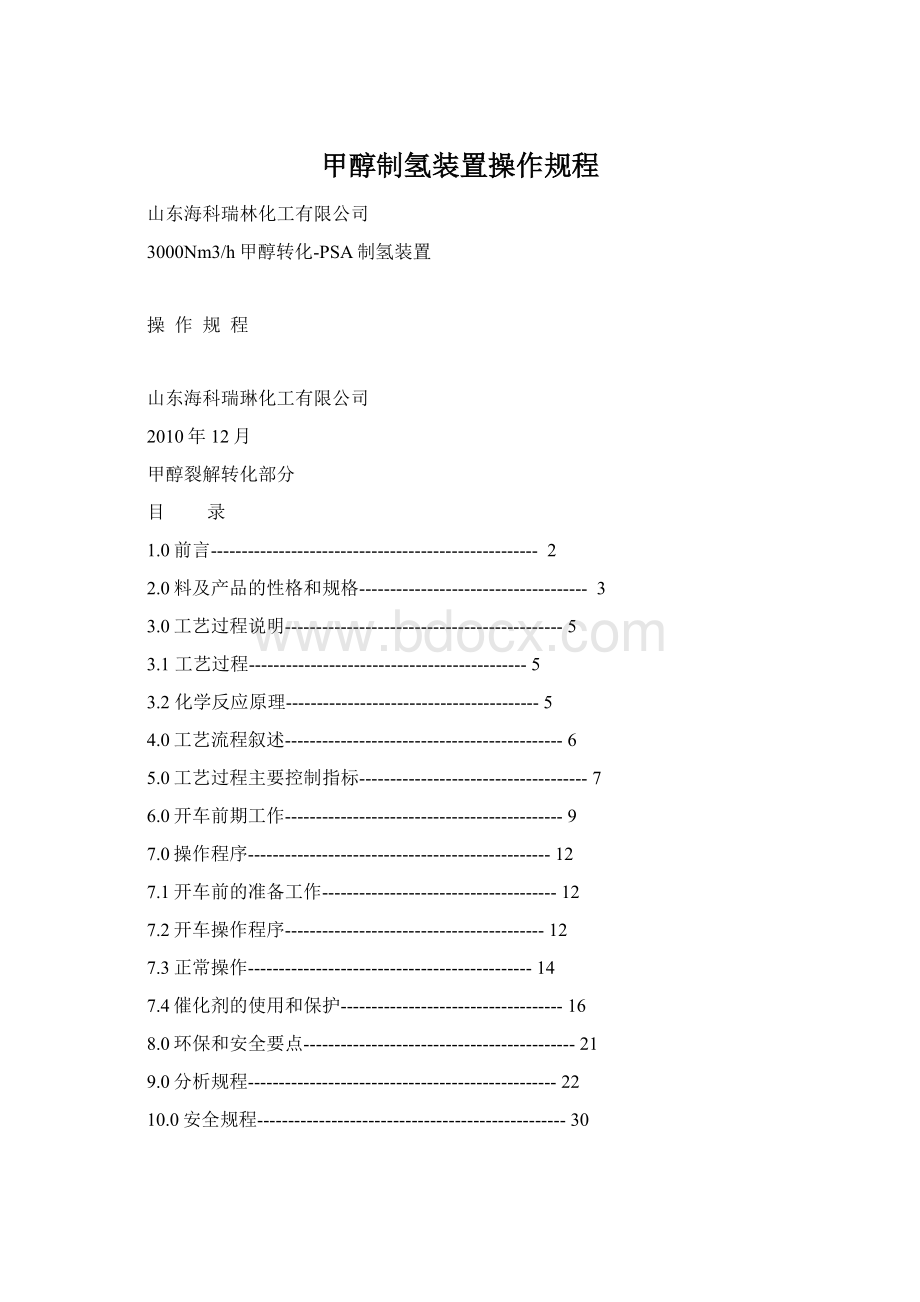
化学名称为甲醇,别名甲基醇、木醇、木精。
分子式CH3OH,分子量32.04。
是有类似乙醇气味的无色透明、易燃、易挥发的液体。
比重为0.7915。
熔点-97.80℃,沸点64.7℃,20℃时蒸汽压96.3mmHg,粘度0.5945厘泊,闪点11.11℃,自燃点385℃,在空气中的爆炸极限为6.0—36.5%。
甲醇是最常用的有机溶剂之一,能与水和多种有机溶剂互溶。
甲醇有毒、有麻醉作用,对视神经影响很大,严重时可引起失明。
(2)原料脱盐水性质(省略)
2.1.2产品性质
本装置生产的产品甲醇催化转化气,其主要组分为氢气和二氧化碳,性质分述如下:
(1)氢气性质
分子式H2,分子量2.0158,无色无臭气体。
无毒无腐蚀性。
气体密度0.0899Kg/m3,熔点-259.14℃,自燃点400℃,极微溶于水、醇、乙醚及各种液体,常温稳定,高温有催化剂时很活泼,极易燃、易爆,并能与许多非金属和金属化合。
(2)二氧化碳性质
化学名称二氧化碳,别名:
碳酸酐、碳酐、碳酸气。
分子式CO2,分子量44.01,无色无臭气体。
有酸味,气体密度1.977Kg/m3,熔点-56.6℃,沸点-78.5℃(升华),易溶于水成碳酸,可溶于乙醇、甲醇、丙酮、氯仿、四氯化碳和苯,属不燃气体,可做灭火剂。
2.2原料和产品规格
2.2.1原料规格
甲醇:
符合国标GB338-2004一级品标准要求。
建议用30Kt/y以上规模合成甲醇装置产品,运输过程无污染;
严禁使用回收甲醇。
脱盐水:
符合国标GB12145-89P(直流炉)要求,且氯离子含量小于或等于3ppm。
2.2.2产品规格
(1)转化气组成
H273—74.5%
CO223—24.5%
CO<0.9%
CH3OH300ppm
H2O饱和
(2)压力:
1.30MPa
(3)温度:
<40℃
3.0工艺过程说明
甲醇催化转化造气生产过程可分为:
原料液预热、汽化、过热、转化反应、产品气冷却冷凝、产品气净化等四个过程。
3.1工艺过程
3.1.1原料液预热、汽化、过热工序
将甲醇和脱盐水按规定比例混合,经泵加压送入系统进行预热、汽化过热至反应温度的过程。
其工作范围是:
甲醇计量罐V101、循环液贮槽V103、原料进料泵P101A/B、换热器E102、汽化塔T101、过热器E101等设备及其配套仪表和阀门。
3.1.2催化转化反应工序
在反应温度和压力下,原料蒸汽在转化炉R101中完成气固相催化转化反应。
工作范围是:
转化炉R101一台设备及其配套仪表和阀门。
该工序的目的是完成化学反应,得到主要组分为氢气和二氧化碳的转化气。
3.1.3转化气冷却冷凝工序
将转化炉下部出来的高温转化气经过冷却、冷凝降到40℃以下的过程。
换热器E102、冷却器E103二台设备及其配套仪表和阀门。
3.1.4转化气净化工序
含有氢气、二氧化碳以及少量一氧化碳、甲醇和水的低温转化气,进入水洗塔T102用脱盐水吸收未反应甲醇的过程。
水洗塔T102、脱盐水中间罐V105、气体缓冲罐V104、脱盐水进料泵P102A/B、五台设备及其配套仪表和阀门。
3.2化学反应原理
甲醇与水蒸气混合物在转化炉中加压催化完成转化反应,反应生成氢气和二氧化碳,其反应式如下:
主反应:
CH3OH+H2O=CO2+3H2+49.5KJ/mol
副反应:
CH3OH=CO+2H2+90.7KJ/mol
2CH3OH=CH3OCH3+H2O-24.9KJ/mol
CO+3H2=CH4+H2O-206.3KJ/mol
主反应为吸热反应,采用导热油外部加热。
转化气经冷却、冷凝后进入水洗塔,塔釜收集未转化完的甲醇和水供循环使用,塔顶转化气经缓冲罐送变压吸附提氢装置分离。
4.0工艺流程叙述
参看甲醇转化工序甲醇裂解制氢工艺管道仪表流程图(图号:
0769-32-101)
来自界外的脱盐水经V1093阀进入脱盐水中间罐V105,经脱盐水进料泵P102A/B计量后送入水洗塔T102,吸收未冷凝的甲醇,吸收液从塔底流入循环液贮槽V103,微量溶解在混合液中的二氧化塔和二甲醚由循环液贮槽放空排出。
来自甲醇贮罐的甲醇用泵输送进入甲醇中间罐V101,靠位差从V101流出的原料甲醇用FV-101调节并经FIC101计量后与来自循环液贮槽V103的循环液混合,用原料进料泵P101A/B将混合液加压送出,进入换热器E102与高温转化气换热而被预热,然后进入汽化塔T101汽化并经过热器E101过热到接近反应温度后进入转化炉R101,在转化炉中发生催化转化反应,出口高温转化气在换热器E102中被原料液换热冷却,在经冷却器E103被冷却冷凝后进入水洗塔T102,冷凝液和吸收液一起经液位调节阀LV-102减压后排入循环液贮槽V103循环使用,转化气经流量计FIQ103计量后经PV-101稳压调节后进入缓冲罐V104后送至变压吸附系统提纯。
催化剂使用前要进行还原。
还原过程氢气为还原气,氮气作稀释载气。
过程氮气在系统循环。
还原气经罗茨风机进入换热器E102与转化炉R101出来的热还原气换热,经过热器E101过热到还原温度后进入转化炉R101进行催化剂还原反应,热还原气经换热器E102换热,再经冷却器E103冷却、冷凝后还原气回罗茨风机在系统循环,冷凝水靠位差进水洗塔T102由排污阀排放。
5.0工艺过程主要控制指标
5.1原料汽化热
5.1.1原料甲醇流量~1427Kg/h
5.1.2原料液流量~3186Kg/h
5.1.3汽化过热塔进料温度~165℃
5.1.4汽化过热塔塔釜压力(表压)1.30MPa
5.2转化反应
5.2.1进料温度200~260℃
5.2.2反应温度220~280℃
5.2.3导热油温度235~290℃
5.2.4换热器出口转化气温度110~140℃
5.2.5冷却气出口转化气温度<40℃
5.2.6反应压力(表压)~1.30MPa
5.3水洗分离
5.3.1进塔脱盐水量820Kg/h
5.3.2循环液量(出塔)~1764Kg/h
循环液组成(wt%):
甲醇0~25%
5.3.3出塔转化气量~3968Nm3/h
转化气组成(V%):
氢73~74.5%
二氧化碳23~4.5%
一氧化碳~0.9%
甲醇0.03%
甲烷0.20%
5.4催化剂还原
5.4.1还原循环气量~3000Nm3/h
5.4.2还原气氢含量0.5~10%
5.4.3还原温度110~230℃
5.4.4还原压力~0.05MPa
5.5其它
5.5.1进工段冷却水压力0.3MPa
5.5.2进工段仪表空气压力0.4~0.60MPa
5.5.3导热油流量~240m3/h
6.0开车前期工作
装置安装竣工后到开车前所必须完成的一切工作,统称为开车前期工作。
为了开车顺利,下列各项工作均应逐项完成。
6.1现场清查、检查
安装竣工后,首先要清理现场,清除一切与安装无关的东西。
特别是进出口道路,安全消防通道必须畅通。
按设计要求,对照图纸对全系统进行逐项对照检查,考察设备、管道、阀门、仪表、电气及土建等项是否设计要求;
查外接管口有无差错,如有错误,应立即改正。
要特别注意检查与安全有关的设施是否符合安全规范、齐备完好,如消防栓、灭火器、安全阀、阻火器、放空管、电气防爆设施等。
清理现场的同时,还应对设计、施工中的各类技术资料、图纸、文件、现场修改设计、各种使用说明书、产品样本等进行整理归档。
6.2系统吹除
吹除的目的是吹除设备、管道本身带来的或安装中遗留下来的杂物,保证投产后的产品质量及防止堵塞阀门、管道和仪表等影响正常生产甚至造成安全事故。
吹除前应拆除或用盲板堵死不需吹除或不能吹除的有关阀门、仪表、转子流量计、液位计和视镜,吹毕再分别装好。
不需吹除的管道设备要加盲板,防止赃物吹入。
吹出过程中要用小锤敲各处焊缝,以便将焊渣吹尽。
本装置应逐段用仪表空气吹除,吹除压力不能大于气密实验的压力,但吹除管内流速最好能大于20m/s。
吹除的检验可用贴有白布或白纸的木板对着空气排出口放置3~5分钟,未发现板上有污点时为合格。
6.3气密性试验
气密性试验的目的是检查设备、阀门、管线、仪表、连接法兰、焊缝是否密封,有无泄漏。
气密性试验采用压缩空气,试验压力一般采用最高操作压力的1.15倍。
在测定压力下,保持1小时,如压力不下降为合格。
鉴于本装置的主要物料甲醇、氢气为易燃易爆、有毒性物料,故在气密性试验中还需测定泄漏率。
泄漏率试验压力为设计压力,时间为24小时,泄漏率≤0.5%为合格。
泄漏率按下式计算:
式中:
P1、P2和T1、T2分别为测试开始及结束时的绝对压力和绝对温度(K),t为试验时间(小时)。
各系统气密性试验压力及要测定泄漏率的系统表示如下:
表一气密性试验要求
序号
系统名称
试验压力(MPa)
备注
1
T101、E101、E102
主系统R101、E103、T102
V104、P101、P102
1.50
需测定泄漏率
2
低压部分V101、V103、V105
0.06
3
导热油系统
0.69
4
冷却水系统
0.50
6.4单车试车
单机试车目的是考验主要设备性能及组装质量,可按设计要求,使用说明书等有关规定进行,包括如下几项主要内容:
6.4.1各台泵类的运转性能、输送量和出口压力;
6.4.2有关仪表的安装及指示控制性能,必要时应进行刻度校验;
6.4.3各调节系统的安装质量、控制、调节、检测能力及调节特性;
6.4.4测出原料贮罐、中间计量罐及气、液各类贮罐的体积,液体贮罐要标出液面计对应刻度的体积;
6.4.5校准并标出流量计的刻度值对应的流量值;
6.4.6各消防栓、灭火器使用是否灵活、方便。
6.5管道、设备清洗
管道、设备、阀门等在制造过程表面积有不少油污、杂物,单靠吹出一般处理不干净,油污杂质在生产中带到催化剂上会毒害催化剂,带入产品会影响产品质量。
当杂物太多时还会造成管道、阀门、仪表的堵塞,因而必须清除。
一般可用干净清水冲洗,水冲洗应连续进行,流速应不小于1.5m/s,以出口水色和透明度与入口处目测一致为合格。
若油污严重,则要先用稀碱液(2%以下)清洗,然后再用干净水冲洗干净。
6.6保温、油漆
6.6.1对于需要保温的设备、管道等必须进行保温。
详见《设备管道保温一览表》
6.6.2防腐:
本装置设备、管道表面采用油漆防腐。
保温设备和管道涂两道防锈漆作为防锈层。
不保温设备和管道涂两道防锈漆后再刷两道面漆。
不锈钢设备不涂漆。
6.6.3涂色与注字
设备、管道防腐面漆的颜色可根据情况确定。
本装置按习惯规定静止设备用银白色面漆,机泵类用浅绿色面漆。
冷却水、消防水管道用绿色面漆,工艺物料管道用红色面漆,仪表空气用深蓝色面漆。
在设备保温和涂色后,应在醒目处注明名称及其位号,重要物料管道还应标示物料流向。
6.7冷态联动试车
冷态联动试车的目的是在于考察运转设备及仪表自动控制能力。
冷态试车中气态物料为空气代替,液态物料以水代替。
先分工序联动试车,最后进行全工段冷态联动试车。
可按下列步骤进行。
6.7.1开启所有仪表、调节装置及传动设备并通电;
6.7.2启动各输液泵、调节流量向有关设备内送水;
6.7.3按正常操作要求,调节各控制点,并按时做好记录,使操作人员熟悉操作,并作预想事故处理。
6.8吹干
上述各项工作完成后,开车前的工作已基本完成。
打开设备管道的排污阀,将水排净。
因为反应系统、还原系统及导热油系统不允许存水,故必须吹干。
6.9导热油锅炉开车
上述工作完成后,导热油锅炉工段必须在装催化剂前预开车试运转一次,详细操作按导热油锅炉使用说明进行,测定导热油流量等,保证正常开车时的供热量。
7.0操作程序
7.1开车前的准备工作
7.1.1一般准备和检查
1、检查水、电、汽、软水、仪表空气、氮气、氢气、燃料气等的供应情况,并与有关部门联系,落实供应数量和质量要求。
2、关闭所有排液阀、排污阀、放空阀、进料阀、取样阀。
开启冷却水、仪表空气等进工段总阀。
3、通知导热油锅炉房准备开车,并联系确定开车的具体时间和质量数量要求(压力、温度、流量等)。
4、通知分析室准备生产控制分析工作。
5、检查动力设备的完好情况,检查所有仪表电源、气源、信号是否正常。
6、落实产品用户。
因转化催化剂不希望中途频繁停车,如用户没落实不要急于开车。
7、检查消防和安全设施是否齐备完好。
8、操作人员、分析人员、管理和维修人员经技术培训,并考核合格方能上岗。
7.2开车操作程序
投料开车程序应在催化剂还原结束后进行,无时间间隔。
催化剂还原将在7.4中专门叙述。
开车时序一般为:
水洗塔开车、汽化塔开车、转化炉开车、系统升压。
还原结束后,关闭还原系统阀V1058、V1069、V1046,开启转化炉后直到V104后放空管线间所有阀门,关闭R101前阀V1051,准备系统开车。
7.2.1准备
1、检查工具和防护用品是否齐备完好。
2、检查动力设备是否正常,对润滑点按规定加油,并盘车数圈。
3、检查各测量、控制仪表是否失灵,准确完好,并打开仪表电源、气源开关。
4、通知甲醇库和脱盐水站向本装置送原料。
使甲醇中间罐V101和脱盐水中间罐V105的液位达~90%,停止送料。
5、催化剂还原系统所有阀门、仪表维持原开车状态不变(具体状态参看7.4催化剂的使用和保护)。
6、通知导热油炉工序,做好开车准备。
7、确定开车投料量,明确投料量与各参数间关系。
7.2.2水洗塔开车
1、开脱盐水中间罐V105出料阀、P102A/B进口阀、旁路阀,启动P102A/B泵,使泵运转正常。
2、开泵P102A/B出口阀,关P102A/B旁路阀。
3、当水洗塔T102塔釜出现液位后,开T102塔釜排液调节阀旁路阀V1080,向循环液贮罐V103送脱盐水,然后开调节阀前后阀V1081V、1082,关V1080,用LV-102阀控制T102液位LIC102在30~40%。
7.2.3汽化塔开车
1、开甲醇中间罐V101出口阀、FIC102前后阀、FV-101前后阀,开循环液贮槽V103出口阀,使水甲醇混合,开泵P102A/B进口阀、旁路阀,启动P102A/B泵,调节流量使FIC102正常。
2、开P102A/B出口阀,关P102A/B旁路阀,调节进料泵刻度向系统送水甲醇。
在A102取样点取样分析,通过FV-101调节原料甲醇的流量,使水甲醇配比达到要求值。
3、当汽化塔T101塔釜液位达10%时,开启汽化塔顶放空阀,缓慢开启T101塔釜导热油进口阀V1039、关部分短路阀V1038,调节进汽化塔导热油量。
当塔顶排放气量稳定时,关部分汽化塔顶放空阀,开启过热器E101底部排污阀V1048、V1049,无液珠排除时关闭排污阀V1048、V1049,即可转入转化炉开车。
7.2.4转化炉开车
1、开转化炉R101进口阀V1051,全部关闭汽化塔顶放空阀,即向转化炉R101送水甲醇原料气。
2、使导热油炉温度稳定至230℃,检查装置设备、管线、阀门、仪表等运转是否正常,并观察各工艺参数间关系,若无异常现象便可进行系统升压。
7.2.5系统升压
1、开系统压力调节阀PV-101及其前后阀,关闭旁路阀。
缓慢关小PV-102阀,使系统升压,直至达1.30MPa。
注意:
必须保证原料气体适量通过催化剂床层,所以系统调压阀不能处于全关状态。
2、调节系统压力调节阀PV-101开度,使系统压力、转化气量稳定。
3、检查原料液进料量及其水甲醇配比,使达要求值;
检查转化气量,通过LV-101阀调节进T101下部的导热油流量,控制好T101塔釜液位在15~30%。
4、调节FV-101使甲醇量稳定并达要求值,调节P102的刻度使V103液位LIA103稳定。
此时已完成系统投料开车工作。
观察全系统运行情况,若无异常现象便可进行下述操作使系统转入正常工作。
7.2.6系统稳定
1、检查冷却器E103冷却水量,使进入水洗塔T102的转化气温度≤40℃。
2、检查缓冲罐出口转化气组成,调整水甲醇配比,控制转化气出口气中一氧化碳、甲醇、水等组分达要求值。
3、全系统操作稳定后,即可向后工段PSA-H2装置输送转化气。
7.3正常操作
全系统开车完成后,即可逐步转入正常操作。
7.3.1正常操作状态的建立和维持
1、根据原料液进料量、转化气流量、水甲醇配比、汽化塔液位、导热油温度、转化气组成、循环液组成及各控制点参数对各控制点参数进行适当调整,使系统操作处于正常范围内。
2、根据所需转化气量及水甲醇配比确定甲醇流量,将FV-101投入自动调节。
3、根据所需原料的流量,调节P-101的刻度。
4、根据所需水洗塔的液位,调节P-102的流量,使V103的液位稳定。
5、根据循环液流量,将LV-102投入自动调节。
6、调节冷却器E103进水阀,使转化气出E103的温度在40℃以下。
7、当系统转化气流量稳定后,将系统压力PV-101投入自动调节。
8、根据所需转化气量及组成,适当调整进系统导热油温度。
9、由汽化塔下部排液阀连续排出少量废水,排出量控制在15.0~20.0Kg/h。
全系统已处于正常稳定运转。
系统处于正常操作时,按时记录各操作参数并巡回检查各控制点、设备、仪表、阀门等是否处于正常状态,发现异常现象,应立即查明原因,及时处理,排除故障,维持系统正常操作状态。
7.3.2正常停车操作
1、停止导热油炉加热,维持导热油循环,待反应温度将至200℃以下后,导热油炉房停止向造气装置送导热油,即开启导热油装置内部短路阀。
导热油炉停车按导热油炉停车要求进行。
2、在导热油炉降温的同时,手动调节系统压力调节阀PV-101,使系统缓慢将压至0.4MPa(或切开气体缓冲罐V104,转化气可备用转化炉置换,开启水洗塔T102顶放空阀降压)。
3、关闭进转化炉阀门V1051,缓慢开启汽化塔顶放空阀V1044,汽化塔前系统降压常压。
4、汽化塔系统降压的同时,停P101A/B,停止向系统进料。
5、转化炉后系统继续降压,待降压至0.2MPa时,关闭PV-101阀的前后阀、旁路阀。
6、停P102A/B,停止向T102送脱盐水。
关闭T102塔釜排液阀。
7、分别用氮气或气体缓冲罐V104转化气对转化炉R101前后分段置换,考虑到降温对系统压力的影响,最后系统分段用氮气或氢气保压至0.2MPa。
导热油按要求将至一定温度后,停导热油循环泵。
若长期停车,则用加压氮气将导热油从系统压回导热油贮罐。
8、对催化剂实行保护操作或钝化处理(具体操作见7.4催化剂的使用和保护)。
7.3.3紧急停车操作
1、凡遇下列情况之一应采取紧急停车操作:
(1)停电
(2)停冷却水
(3)设备、管道爆炸断裂、起火
(4)设备、管道或法兰严重漏气、漏液无法处理
(5)重要控制仪表失灵
2、操作步骤
(1)紧急通知导热油装置停止加热,打开导热油装置内部短路阀,停止向造气装置送导热油。
(2)关闭转化炉前阀V1051,切开汽化塔系统与反应系统。
转化炉后系统适当泄压。
汽化系统可维持压力稳定。
(3)停原料进料泵P101A/B。
(4)停脱盐水进料泵P102A/B。
(5)对催化剂实行特殊保护操作(具体操作见7.4催化剂的使用和保护)。
(6)查明事故原因后再做进一步处理。
7.4催化剂的使用和保护
7.4.1转化炉的清洗和准备
1、将转化炉上、下人孔拆下,先检查转化炉质量是否符合要求,再将转化炉内上下封头、列管内、板管和花板上的铁锈杂物全部清除干净,必要时可进行酸洗、水洗,再擦净、吹干备用,要求无铁锈、无杂物。
2、下封头花板上按要求规格放2层12目丝网,往花板上堆满已经洗净吹干的Φ10~12mm的氧化铝瓷球,将瓷球上表面推平,要求瓷球上表面与转化炉下花板面保持有10~15mm高的空间。
3、重新装好下封头和上封头人孔,通气对转化炉再次进行试漏查漏,当确认下封头人孔法兰不漏气后,方可泄压排气,准备装填催化剂。
7.4.2催化剂的装卸
1、准备
(1)检查检修工具及防护用品是否齐全完好。
(2)准备好装催化剂专用的量杯、漏斗、标尺等专用工具。
(3)对催化剂开通进行质量检查,用6~10目的钢网筛将催化剂中的碎粉筛除备用。
在运输或库存中不当受到污染或被水浸泡变质的催化剂一般