NiMoP化学镀层热处理工艺优化文档格式.docx
《NiMoP化学镀层热处理工艺优化文档格式.docx》由会员分享,可在线阅读,更多相关《NiMoP化学镀层热处理工艺优化文档格式.docx(15页珍藏版)》请在冰豆网上搜索。
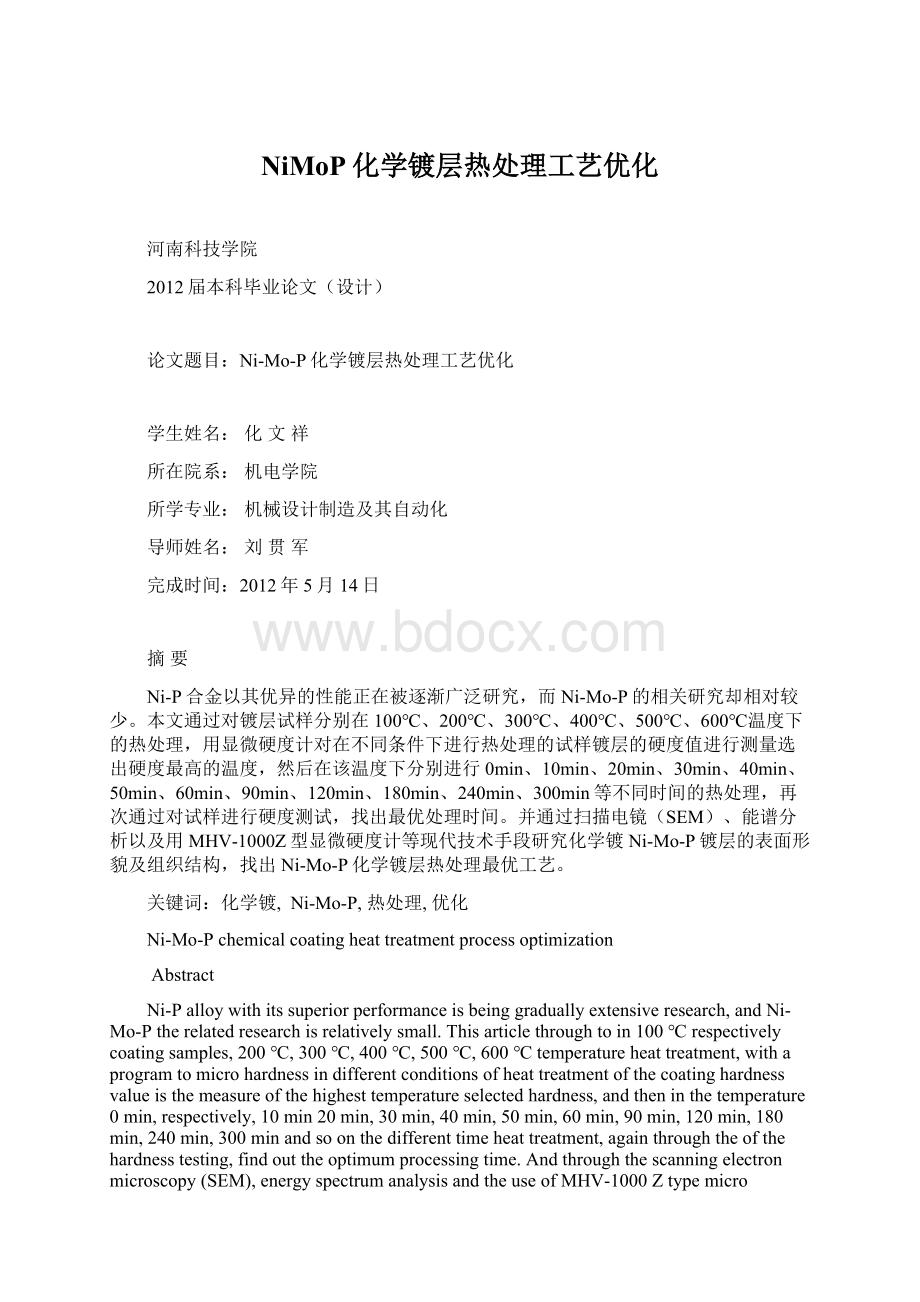
Abstract
Ni-Palloywithitssuperiorperformanceisbeinggraduallyextensiveresearch,andNi-Mo-Ptherelatedresearchisrelativelysmall.Thisarticlethroughtoin100℃respectivelycoatingsamples,200℃,300℃,400℃,500℃,600℃temperatureheattreatment,withaprogramtomicrohardnessindifferentconditionsofheattreatmentofthecoatinghardnessvalueisthemeasureofthehighesttemperatureselectedhardness,andtheninthetemperature0min,respectively,10min20min,30min,40min,50min,60min,90min,120min,180min,240min,300minandsoonthedifferenttimeheattreatment,againthroughtheofthehardnesstesting,findouttheoptimumprocessingtime.Andthroughthescanningelectronmicroscopy(SEM),energyspectrumanalysisandtheuseofMHV-1000Ztypemicrohardnesstester,andothermoderntechnologyresearchelectrolessplatingNi-Mo-Pcoatingsurfacemorphologyandorganizationstructure,andfindouttheNi-Mo-Pchemicalcoatingtheoptimalheattreatmentprocess.
Keywords:
Chemicalplating,Ni-Mo-P,Heattreatment,Optimization
目录
1绪论1
2实验材料与方法2
2.1实验方案2
2.2实验材料和实验装置3
2.3试验流程3
2.4试样前处理3
2.5镀层制备4
2.5.1镀液的配方4
2.5.2配制方法4
2.5.3施镀过程5
2.6镀后试样处理5
2.8Ni-Mo-P镀层结构形貌分析7
2.9能谱分析7
2.10镀层硬度测试9
3实验结果及分析10
3.1热处理温度对镀层硬度的影响10
3.2热处理时间对镀层硬度的影响11
4结论12
致谢12
参考文献12
1绪论
化学镀也称为自催化镀,是指在没有外加电流通过的情况下,利用还原剂将溶液中的金属离子,在呈催化活性的物体表面进行有选择地还原沉积,使之形成金属镀层。
它是提高金属等材料表面的耐磨性、耐腐蚀性、抗高温氧化性以及其它性能的一种表面强化方法。
化学镀的发展史可以说是化学镀镍的发展史。
早在1844年,A.Wurtz发表了以次亚磷酸盐作还原剂用于镀液的论述。
1916年,Roux用次亚磷酸盐进行了化学镀镍,但此时的镀液极不稳定,自发分解倾向大,只能在制件表面获得黑色粉末附着物。
但化学镀镍技术的奠基人是美国国家标准局的A.Brenner和G.Riddell。
他们在1944年进行了第一次实验室试验,并获得了较为稳定的化学镀镍溶液,直到1947年提出了沉积非粉末状镍的方法,弄清了形成涂层的催化特性,使化学镀镍技术工业应用有了可能。
所以,化学镀镍技术的历史比较短暂。
到了二十世纪七十年代,随着科学技术的进步和工业的发展,化学镀镍的应用和研究发展较快。
到了八十年代后期,化学镀镍技术有了很大突破,一些长期困扰着人们的问题如镀液的稳定性和寿命等得到了初步解决。
基本上实现了镀液的自动控制,使连续化的大型生产有了可能。
因此化学镀镍的应用范围和规模越来越大。
据估计,八十年代中期化学镀镍的年产量为1500t,按厚度为25µ
m计,面积达到7.5×
106㎡。
其中美国占40%,远东地区占20%,其余为南非和南美洲。
在美国大约有900个化学镀镍的工厂,其中40%加工本厂的产品,总产值约为2亿美元。
化学镀镍在计算机和电子行业的应用份额最大,在美国约占化学镀镍总产值的20%,另外,阀门制造占15%,飞机和汽车制造占10%。
由于市场和应用领域的不同,美国和欧洲化学镀镍的发展不同。
美国化学镀镍最早源于通用运输公司的kanigen工艺的商品化。
此工艺得到8w%-10w%含磷量的镍磷合金镀层,适用于大的槽容量操作,开始用于生产核工厂的贮槽和槽车内衬,后用于航天、食品、化工、钢铁等行业。
60-70年代研究人员主要致力于改善镀液性能,而不是镀层性能。
80年代高磷化学镀镍应用增加,这是因为其耐蚀性较好的缘故。
还出现低磷化学镀镍和其它化学镀镍工艺。
在欧洲,早期的化学镀镍直接针对工程应用的需要,特别是耐蚀性的需要,所以在德国主要使用镍硼合金而不是镍磷合金。
Dupont公司引入的含铭镍硼合金具有很高的耐磨和耐蚀性,用于航天、汽车、纺织工业,并用于代替硬铬。
化学镀层作为功能性镀层,未来将向两方面发展。
一方面在已有的基础上进一步完善和提高。
另一方面,发展功能多样化和与其他先进的辅助技术相互融合,包括印刷电路板的计算机的辅助设计、激光、紫外光、红外线、超声波的诱导化学镀、纳米颗粒的掺杂和特殊性能的LCR元件的织造等先进技术。
化学镀与电镀相比,虽然具有一定的不足,如所用的溶液稳定性较差,溶液的维护、调整和再生都比较复杂;
但亦具有更多的优势,如下:
(1)镀层厚度非常均匀,化学镀液的分散力接近,无明显的边缘效应,无论工件如何复杂,只要采取适当的技术措施,就可在工件上得到均一的镀层。
因此特别适合形状复杂工件、腔体件、深孔件、盲孔件、管件内壁等表面施镀。
电镀法因受电力线分布不均匀的限制是很难做到的。
由于化学镀层厚度均匀、又易于控制,表面光洁平整,一般均不需要镀后再加工,适合做加工件超差的修复及特殊选择性施镀。
(2)通过敏化、活化等前处理,化学镀可以在非金属如塑料、玻璃、木材、叶、纤维、复合材料陶瓷及半导体材料表面上进行,并且由于化学镀具有自动催化功能,因此可获得任意厚度的镀层。
而电镀法只能在导体表面上施镀,所以化学镀工艺是非金属表面金属化的常用方法。
(3)由于化学镀具有自动催化功能,因此可获得任意厚度的镀层。
(4)工艺设备简单,不需要电源、输电系统及辅助电极,操作时只需把工件正确悬挂在镀液中即可化学镀是靠基材的自催化活性才能起镀,其结合力一般均优于电镀。
(5)镀层有光亮或半光亮的外观、晶粒细、致密、孔隙率低,某些化学镀层还具有特殊的物理化学性能。
(6)化学镀层具有良好的化学、机械和磁学性能。
同时化学镀层和基体结合致密均匀,腐蚀介质不易透过镀层达到基体材质,起到了良好的防腐层的作用。
化学镀镍由于镀层的结晶细致、孔隙率低、硬度高、镀层均匀、化学稳定性好,已广泛用于电子、航空、航天、机械、精密仪器、日用五金、电器和化学工业中。
近十几年来,化学镀合金镀层已被广泛用作功能性电子材料,如印刷电路中的联接导体,簿层电阻以及镀膜磁盘等,为了满足高温特殊环境的要求,研究这些镀层的热稳定性是很有必要的。
化学镀Ni-P合金镀层,因其优异的物理、化学和力学性能使其在各工业部门的应用不断扩大,Ni一P合金镀层的性质,很大程度取决于镀层中磷的含量,但简单地用改变磷含量的方法改变镀层的性质,远不能满足实际应用的需要。
因此有必要引入第三种元素如W或Mo。
钼这样熔点较高的金属元素的加入,可以调整和改变材料的微观结构,从而改善镀层在镀态下的物理、化学性能,使镀层合金的热稳定性增强,化学性质也进一步提高。
2实验材料与方法
2.1实验方案
选取六块试块,分别在100℃,200℃,300℃,400℃,500℃,600℃温度下进行90min的热处理,之后用显微硬度计测出各个试块的硬度,选出硬度最高的试块。
在选出最佳处理温度的基础上改变处理时间。
分别将热处理时间设为0,10,20,30,40,50,60,90,120,180,240,300min,再次通过显微硬度计测试出各个试块的硬度,选出最佳热处理时间。
通过以上两次步骤即可得出最佳热处理温度和时间,从而完成对Ni-Mo-P镀层热处理工艺的优化。
2.2实验材料和实验装置
本实验所采用的集体试样为常用钢片,将其切割成(4*40*1.5)mm的长方体,在其一段钻上一个小孔,以便在进行化学镀是牵挂,下图为化学镀镍的实验装置图,包括电热恒温水浴装置,数显pH计,烧杯,搅拌器,挂具,MHV-1000Z型显微硬度计等。
2.3试验流程
试验流程为:
试样的选取与制作--预磨试样--水洗--除油--除锈(酸洗)---水洗--超声波除污--化学度层--水洗干燥---热处理---数据分析
图1镀层实验装置
2.4试样前处理
(1)试样的选取和制作
从已有的试样中选取24个外形大小差别较小的试样,打孔。
(2)试样的预磨
将试样的一个工作面在机器上用1200的砂纸打磨,其目的是出去工作表面的划痕,锈污,氧化皮以及其他表面杂质和缺陷,从而获得平整光滑的表面。
(3)清洗
对待镀的试样进行清洗,洗去其表面上的杂质,这是十分必要的,也是进一步提高镀件镀层的外观质量。
(4)分组称重
将清洗干净的试样随机分成四组并标号,在每一组中随机选取一个进行称重,记录数据。
(5)除油
除油的目的是清除试样表面的各种因为多种原因使上面带有的各种动、植物及矿物油、脂肪、油污。
使镀层与基片有良好的结合力,对于零件表面油污较多或者经过机械抛光的试样,应先用有机溶剂或者除油剂进行清除,然后和一般零件一样进行化学除油,常有的化学除油药品有氢氧化钠,碳酸钠,磷酸钠等,为降低实验成本并且达到实验目的,我们采用皂粉进行除油。
(6)除锈(酸洗)
利用酸的腐蚀性除去试样表面的氧化膜,将试样表面的残余锈皮溶解和剥离掉。
盐酸对金属氧化物具有较强的溶解能力,对试样溶解缓慢,过腐蚀危害小,酸洗后的试样工作表面干净,实验表明;
在2%-15%盐酸溶液中酸洗,铁离子含量小于16%时,酸洗效果最好。
(7)超声波除污
将酸洗后的试样在蒸馏水中再次清洗,除去表面的酸液,然后放入盛有蒸馏水的烧杯中,在超声波除污仪器中除污,除污完成后放在一旁待镀层(这一步骤的结束时间应该与镀液的加热相协调,以防试样放置时间过长而表面再次被氧化)。
2.5镀层制备
2.5.1镀液的配方
硫酸镍——————25g/L
次亚磷酸钠————28g/L
乳酸————————5g/L
柠檬酸钠——————20g/L
钼酸钠———————0.8g/L
醋酸钠———————15g/L
十二烷基硫酸钠———0.03g/L
T=85~90℃
PH=8.5~8.8
T=2h
2.5.2配制方法
(1)该镀液的各个成分均需用蒸馏水溶解稀释;
(2)按配制溶液的体积(4L)算出各个成分需要的量,分别按照各个药品的计算量称出;
(3)将各个成分分别预先溶解好,并过滤,由于硫酸镍的溶解速度较慢,可以在溶解搅拌的过程中加热,以加快溶解;
(4)再一个4L的量具中依次加入各个药品,并在添加的过程中均匀搅拌,让各个成分混合均匀;
(5)加入适量的蒸馏水,然后用氨水调镀液的pH值,添加氨水搅拌均匀后用数显pH计测量,使得镀液的pH值位于85--9.0之间;
(6)补充蒸馏水到镀液4L,用量筒平均分配到四个1L的烧杯中;
2.5.3施镀过程
(1)打开水浴炉开关,添加适量的水,加热。
待温度上升到90度左右时将四个1L的烧杯分别放入,加热;
(2)待镀液的温度上升至85-90度之间时,将事先处理好的试样放入溶液中施镀;
(3)在镀层的过程中,溶液的温度、pH值、搅拌速度等各种因素都会影响到镀层的效果和质量因此要严格控制;
(4)镀层时间为两个小时,时间结束后取出试样。
镀的过程中要注意PH值的控制。
表1施镀过程中PH控制记录。
2.6镀后试样处理
试样施镀结束后应将试样清洗干净,除去其表面残留的化学成分,保证试样镀层的良好外观质量,烘干后找出镀前所称重过的试样进行再次称重,用游标卡尺测量试样的长、宽、厚并记录数据,根据已有的测量数据计算出试样的镀速。
其公式如下:
表2镀速计算公式
表3镀速计算结果
表3为从四组镀过层的试块试块中选出的一个样品,通过对抽样出的试块进行镀速计算,从而反应出四组镀速是否正常。
三元合金普遍沉积速率不高,以上测得几组速率比较正常。
镀层的沉积速率并不是越快越好。
一方面,镀速过快会使生成的颗粒粗大,导致镀层的孔隙率增大。
另一方面,镀速过快会使镀液消耗过快,从而导致镀层中合金元素的含量波动较大。
对于化学沉积Ni-Mo-P,在沉积过程中,镀速并不是一直不变的,沉积速率随着沉积时间的延长有变化,镀层可能生成钝化膜,或者表面附近溶液浓度降低,从而导致镀速下降,这些因素还没有做系统研究。
2.7试块热处理
在经过镀层的试样中拿出6块分别在箱式炉中进行热处理,由于本次实验旨在得到温度以及时间对镀层硬度的影响,故先实验温度对镀层硬度的影响,热处理时,控制热处理时间为90min,热处理温度分别设为100℃,200℃,300℃,400℃,500℃,600℃。
然后通过硬度测试,通过不同温度热处理后得到的试样镀层硬度的对比,得出对镀层硬度影响最大的热处理温度。
确定热处理温度后,改变热处理时间,分别做时长为0min、10min、20min、30min、40min、50min、60min、90min、120min、180min、240min、300min的热处理。
通过这一步的热处理可以找出最佳热处理时间。
2.8Ni-Mo-P镀层结构形貌分析
图2电镜扫描所放大的镀层表面
化学镀层的性能与镀层的结构及表面状态有关,因此有必要对镀层结构形貌进行分析。
本实验采用扫描电子显微镜(SEM)对Ni-Mo-P镀层表面进行观察,在已经镀层的24块试样中,随机抽取一块进行观察分析,在视野中随机选取一块区域,进行放大,在1000倍的放大倍率下,进行拍照,并通过仪器采集成为感兴趣区,然后在所在的感兴趣区中选取三个部分进行光谱分析,测试镀层中Ni、Mo、P、等元素的含量比例,并绘制曲线图。
下图为镀层形貌,镀层已经完全覆盖基体,表面由胞状物覆盖,无明显缺陷,从图上可以看出其呈现典型的菜花状结构。
各个团簇在自己的质点上,倾向于垂直方向生长。
而且团簇颗粒呈球形,且球大小相差不大,分布比较均与;
另外在实验中发现,沉积镍钼磷过程中气泡细小,所以表面没有发现气孔存在。
如上所述在生成感兴趣区后,在感兴趣区随机选择三个部分依次进行能谱分析,在能谱分析结束后,对谱图进行处理,去除不予研究的元素,只观察Ni、Mo、P三种元素,由于在镀层中Mo元素的含量较其他元素较少,谱图上面会对Mo元素没有显示,于是需要手动添加元素到比较的三种元素中。
2.9能谱分析
图3能谱分析点一
图4能谱分析点一元素曲线图
图5能谱分析点二
图6能谱分析点二元素曲线图
2.10镀层硬度测试
对100℃,200℃,300℃,400℃,500℃,600℃温度下进行热处理的六个试样分别进行硬度测试,根据实验要求及实验条件,我们采用MHV-1000Z显微硬度计对六个试样分别进行硬度测试,施压载荷F=25g,保持时间T=10s,记录数据。
以400℃第二步热处理工艺的温度,根据Ni-Mo-P合金镀层性能及研究需要,分别做时长为0min、10min、20min、30min、40min、50min、60min、90min、120min、180min、240min、300min的热处理实验。
之后对各个试样采MHV-1000Z显微硬度计进行硬度测试,所加载荷F=25g,保持时间T=10s,记录测得的数据。
3实验结果及分析
3.1热处理温度对镀层硬度的影响
在经过镀层的试样选出6块分别在箱式炉中进行热处理,由于我们是在寻求最优温度和最优处理时间,所以我们先将温度作为变量来讨论,而时间暂时作为定量,在热处理时,控制热处理时间为90min,热处理温度分别为100℃,200℃,300℃,400℃,500℃,600℃。
进行完热处理之后分别对这6块试块进行硬度测试,找出硬度最大的试块,以此找出最优处理温度。
下表为在25g压力,保持时间为10s情况下测得的6个试块的硬度及平均值。
表4硬度测试结果1
图7表4所生成的线图
3.2热处理时间对镀层硬度的影响
以第一步热处理得出的温度做为定量,此时以处理时间做为变量,分别处理0min、10min、20min、30min、40min、50min、60min、90min、120min、180min、240min、300min。
然后通过再一次的硬度测试,选择出硬度最好的试样,这样我们就可得到对于Ni-Mo-P合金镀层能使其表面硬度(即耐磨能力)达到最大的热处理温度和热处理时间。
此时应尽量仍选用25g压力进行硬度测试,尽量减少变量从而使测量结果更具说服力。
每次测得三组硬度数据并求出平均值,画出表格及曲线图,更加直观的表明热处理对于试块镀层硬度的影响趋势。
表5热处理后25g压力下测得的硬度
将以上处理结果绘制成线图
图11表5所生成的线图
4结论
(1)相对热处理时间,热处理温度对镀层硬度影响更大。
(2)通过对Ni-Mo-P化学镀层的热处理实验数据的分析,改变热处理温度时测得硬度,在400℃时试块镀层硬度最大。
(3)通过改变热处理时间得出试块镀层在经过90min热处理后测得硬度最大。
(4)对两次实验综合分析知热处理时间为90min;
温度为400℃时处理所得的试块镀层硬度最高。
致谢
在近一学期的毕业设计过程中,首先要感谢刘贯军教授在生活和学习中对我的关心和照顾。
感谢导师在课题上给我的悉心指导。
刘老师严谨的科研作风,忘我的工作态度也深深的影响了我,使我在今后的工作和学习中受益匪浅。
感谢同宿舍同课题的各位同学在生活和学习上对我的支持和帮助,使我能够在快乐的生活学习环境中顺利的完成学业。
最后还要感谢父母家人对我经济上精神上的支持,使我能够静心于学习和科研,较好的完成毕业。
参考文献
[1]姜晓霞,沈伟著.化学镀理论及实践.北京:
国防工业出版社,2000。
[2]李宁著.化学镀实用技术.北京:
化学工业出版社,2004。
[3]胡信国,张钦京.化学镀镍技术新进展.新技术新工艺,2001。
[4]张翼,范洪富,林玉娟,等.化学镀非晶态Ni-Mo-P合金析出机
理研究.电镀与环保,1996,16(6):
16-18。
[6]闫洪.现代化学镀镍和复合镀新技术[M].北京:
国防工业出版社,1999:
7-127.
[7]张刚,陆柱.化学镀Ni-Mo-P合金及其在5%NaCl溶液中的耐蚀性[J].华东化工学院院报,1992,18
(2):
254-256。
[8]张信义.化学镀Ni-Mo-P合金镀层的结构及耐蚀性能[J].机械工程材料,1997,2
(1):
23-25。
[9]王森林,蓝心仁,黄婷婷,等.化学沉积Ni-Mo-P合金及性能[J].电化学,2005,11
(2):
182-187。
[10]谭凤铃,姜秉元.化学沉积Ni-Mo-P合金工艺参数对性能的影响[J].材料开发与运用,2001,16(6):
26-28。
[11]余祖孝等:
化学镀Ni-Mo-P合金镀工艺及镀层性能,四川理工学院材料与化学工程学院,2009第四期。