第七章氧化Word下载.docx
《第七章氧化Word下载.docx》由会员分享,可在线阅读,更多相关《第七章氧化Word下载.docx(27页珍藏版)》请在冰豆网上搜索。
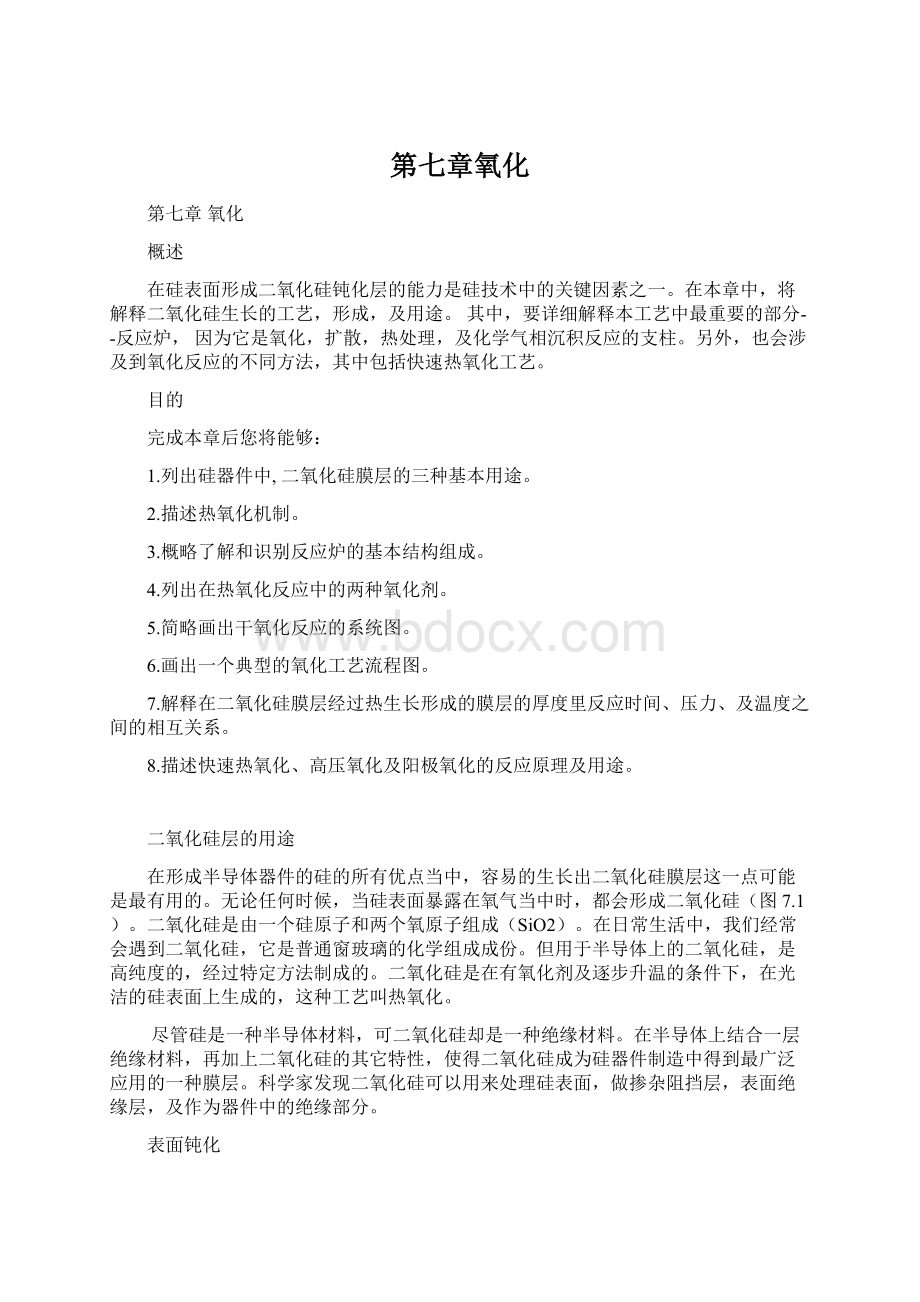
另一方面,二氧化硅对器件的保护是源于其化学特性。
不管工艺过程多么洁净,总有一些电特性活跃的污染物(移动的离子污染)最终会进入或落在晶圆表面。
在氧化过程中,硅的最上一层成为二氧化硅,污染在表面形成新的氧化层,远离开了电子活性表面。
其他污染物被禁锢在二氧化硅膜中,在那里对器件而言伤害是很小的。
在早期的MOS器件工艺中,通常在晶圆氧化后和在进行下一步工艺之前,要去除氧化物以去掉表面那些不需要的移动离子污染物。
表面钝化
图7.1表面用二氧化硅钝化
掺杂阻挡层
在第五章中,掺杂被定义为四种基本工艺制造之一。
掺杂需要在表面层上建立一些洞,通过离子注入或扩散的方法把特定的掺杂物引入到暴露的晶圆表面。
在硅技术里,最常见的表面层是二氧化硅(图7.2)。
留在硅表面上的二氧化硅能够阻挡掺杂物浸入硅表面。
在硅技术里用到的所有掺杂物,其在二氧化硅里的运行速度低于在硅中的运行速度。
当掺杂物在硅中穿行达到所要求的深度时,它在二氧化硅里才走了很短的路径。
所以,只要一层相对薄的二氧化硅,就可以阻挡掺杂物浸入进硅表面。
另一个钟爱二氧化硅的原因,是因为它的热膨胀系数与硅的热膨胀系数很接近。
在高温氧化工艺、掺杂扩散或其他一些工艺中,晶圆会热胀冷缩。
二氧化硅与硅胀缩的速率接近,这就意味着,在加热或冷却时,晶圆不会产生弯曲。
表面绝缘体
二氧化硅被归类为绝缘材料,这意味着在正常情况下它不导电。
当它用于电路或器件时,它们被称作绝缘体。
作为绝缘体是二氧化硅扮演的一个重要角色。
图7.3表示了一个晶圆的侧切面,二氧化硅层的上面是一层金属导电层。
氧化层使得金属层不会与下面的金属层短路,就像电线的绝缘材料保护电线不会短路一样。
氧化层的这种能力要求氧化层必须是连续的,膜中不能有空洞或孔存在。
氧化层必须足够厚,以避免感应现象的产生。
感应产生于足够薄的金属层,以至于电荷在晶圆表面产生聚积效应。
表面电荷可导致短路及不希望的电荷影响。
足够厚的膜层可防止在晶圆表面感应产生电荷。
绝大多数晶圆表面被覆盖了一层足够厚的氧化层来防止从金属层产生的感应,这被称为场氧化物。
掺杂
图7.2作为掺杂阻挡层的二氧化硅
图7.3做为绝缘层的二氧化硅层
器件绝缘体
从另一个角度讲,感应现象就是MOS技术。
在一个MOS三级管中,栅级区会长一层薄的二氧化硅(图7.4)。
氧化层起到介电质的功能,它的厚度是专门选定的,用来让氧化层下面栅级区产生感应电荷。
栅级是器件中控制电流的部分。
大规模集成电路中的MOS技术,使得栅级的形成成为工艺发展中关注的焦点。
热生成的氧化层也可用来做硅表面和导电表面之间形成的电容所需的介电质(图7.5)。
二氧化硅介电层也用在两层或多层金属层的结构中。
在这种应用里,二氧化硅层用化学气相沉积(Chemicalvapordeposition,CVD)的方法而不是用热氧化的方法形成的(见12章)。
图7.4在MOS栅极中,二氧化硅做为场氧化
图7.5在固态电容里的二氧化硅层
器件氧化物的厚度
应用在硅材料器件中的二氧化硅层的厚度的变化范围是很大的。
薄的主要有MOS器件里的栅级,它的厚度是在35埃至80埃这个范围。
1厚的氧化层主要用于场氧化层,图7.6列出了不同厚度范围及其相对应的主要用途。
图7.6二氧化硅厚度表
二氧化硅厚度,埃应用
60---100隧道栅极
150---500栅极氧化,电容绝缘层
200---500LOCOS氧化
2,000----5,000腌膜氧化,表面钝化
3,000-----10,000场氧化
图7.7氧于硅反应生成二氧化硅的化学反应方程式
热氧化机制
热氧化生长是非常简单的化学反应,见图7.7。
这个反应甚至在室温条件下也能发生。
可是,在实际应用中,需要用阶梯式升温方法来在合理的时间内获得高质量的氧化层。
氧化温度一般在900摄氏度到1200摄氏度之间。
尽管化学方程式表示了硅与氧所发生的反应,但并没有说明氧化的生长机制。
为了理解生长机制,我们可以想象把一片晶圆放到加热室中,暴露在氧环境中(图7.8a)。
开始时,氧原子与硅原子结合,这一阶段是线性的,因为在每个单位时间里,氧的生长量是一定的(图7.8b)。
大约长了500埃以后,线性生长率达到极限。
(10,000埃等于1微米)。
图7.8硅二氧化物生长阶段:
(a)初始(b)线性(c)抛物线
为了保持氧化层生长,氧原子与硅原子必须接触。
可是,在硅表面生长的一层二氧化硅层阻挡了氧与硅原子的接触。
为了氧的继续生长,一则让晶圆中的硅浸入到氧气中,或者让氧必须进入到晶圆表面。
在二氧化硅的热生长中,氧气通过现存的氧化层进入到硅表面(技术上称为扩散)。
因此二氧化硅从硅表面消耗硅原子,氧化层长入硅表面。
随着每一个新的生长层,扩散的氧必须移动更多的路程才能到达晶圆。
其后果是,从时间角度来讲,氧生长率会变慢,这一阶段被称为抛物线阶段。
当你画出图形,就会发现氧化膜厚度,生长率及时间的数学关系是抛物线型。
其它描述这个阶段的词是受限反应(transportlimitedreaction),或受限扩散反应(diffusionlimitedreaction)。
这意味着生长率受限于氧在已形成的二氧化硅里的传输和扩散。
图7.9表示的是线性和抛物线型的两个阶段。
图7.10的公式表述了大约超过1200埃时,基本的抛物线关系。
图7.9二氧化硅的线性和抛物线生长
图7.10二氧化硅生长参数的抛物线关系
因此,生长氧化层会通过两个阶段:
线性阶段和抛物线阶段。
从线性阶段到抛物线阶段的变化依赖于氧化温度和其他因素(见“氧化率的影响”)。
通常讲,小于1000埃的氧化受控于线性机制。
这是大多数MOS栅级氧化的范围。
关于二氧化硅生长机制更详细的解释,请参考Wolf和Tauber合著的”SiliconProcessing”一书。
2
抛物线关系的主要涵义是指厚氧化层比薄氧化层需要更多的时间。
例如,在1200摄氏度的干氧反应中,生长2000埃厚的膜,需要6分钟。
3如果加倍到4000埃,则需要220分钟,超过原来的36倍。
这样长的时间,对于半导体工艺来讲是个问题。
当用纯氧作为氧化气体,生长厚的氧化层需要更长的时间,特别是在低温的条件下。
一般来讲,工艺工程师希望在保证质量的前提下,时间越短越好。
在前面的例子中提到的220分钟实在太长了,一个氧化反应,需要一个班次的时间才能完成。
一个加速氧化的方法是用水蒸气(H2O)来代替氧气做氧化剂。
图7.12说明了在水蒸气中生长二氧化硅的过程。
在气态时,水以H-OH基离子的形式存在。
它由一个氢原子和一个带负电的氢氧根组成,这个分子叫作氢氧基离子。
氢氧基离子扩散穿过晶圆上的氧化层的能力比氧气快。
如图7.11所示的生长曲线,这是一个比较快的硅氧化过程。
图7.11二氧化硅厚度与时间,温度在(a)干氧化(b)蒸气
图7.12硅和水蒸气反应形成二氧化硅和氢气
水在氧化反应的温度时,是以蒸气的形态存在的,这种工艺叫做蒸气氧化(steamoxidation),或湿氧化(wetoxidation),或高温蒸汽氧化(pyrogenicsteam)。
湿氧化一词来源于那个时代,当时汽态水来源于液态水。
只有氧参与的氧化叫干氧化(dryoxide)。
如果只用氧气,一定是无水蒸气的。
请注意,当水蒸气与硅反应时,方程的右面有两个氢分子(2H2)。
初始时,这些氢分子被陷在二氧化硅层中,使其密度低于干氧生成的二氧化硅层。
可是在惰性气体中进行氧化加热后,例如在氮气中(见“氧化工艺”一书,第154页),这两种氧化在结构和性能上就非常相似了。
氧化率的影响
原始的氧化厚度与时间的曲线是由<
111>
晶格方向及未掺杂的晶圆所决定的。
4MOS器件是在掺杂后的<
100>
晶格方向的晶圆表面上制造的。
这两个因素在特定的温度和氧化剂环境中影响氧化率。
其它影响氧化率的因素包括在多晶硅层中有意地使氧化物和氧化不纯,例如加入氯化氢。
晶格方向。
晶格方向对氧化生长率有影响。
<
晶圆比<
晶圆有更多的原子。
大量的原子使得氧化层生长得更快。
图7.13表示不同的晶格方向有不同的氧化生长率。
这种不同,在低温时的线性阶段中表现得尤为突出。
图7.13<
和<
型硅,在水蒸气中的氧化
晶圆掺杂物的再分配。
氧化过的硅表面永远有杂质。
在开始生产的硅片上,一般被掺杂为N型半导体或P型半导体。
在以后的工艺中,晶圆表面用扩散或离子注入工艺完成掺杂。
掺杂元素和浓度都对氧化生长率有影响。
例如,在经过高浓度的磷掺杂后的表面上,氧化层比在其它层上生长的氧化层的密度低。
这些磷掺杂的氧化层被刻蚀得很快,并且由于光刻胶的脱落及快速的钻蚀现象的存在,使得刻蚀工艺更加难做,面临一个新的挑战。
另一个对氧化生长率有影响的是氧化完成后,在硅中掺杂原子的分布。
5回想在热氧化时,氧化层长入晶圆。
问题是“在硅转化成二氧化硅后,掺杂原子发生了什么?
”答案取决于掺杂物的传导类型。
N型掺杂物,例如磷、砷、锑,它们在硅中比在二氧化硅中有更高的溶解度。
当氧化层碰到他们时,它们进入晶圆里。
在硅及二氧化硅之间,就象铲雪机推个大雪堆。
结果就是,N型掺杂物在硅及二氧化硅之间比在晶圆里有更高的浓度(称之为“堆积”)。
当掺杂物是P型材料的硼元素时,就会产生相反的结果。
硼原子被拉入二氧化硅层,导致在交界处的硅原子被硼原子消耗尽。
堆积和消耗这两种不同作用的结果,会显著地影响器件的电特性。
堆积和消耗对于掺杂浓度的精确影响,将在第十七章中说明。
掺杂浓度对氧化率的影响随着掺杂物的类型及浓度的不同而变化。
通常来讲,高掺杂区比低掺杂区氧化得快。
高浓度磷掺杂区是不掺杂区氧化率的2到5倍。
6可是,掺杂氧化影响在线性阶段(薄氧化层)表现得更为显著。
氧化杂质。
特定的杂质,特别是氯化氢(HCl)中的氯,被包含在氧化环境中。
这些杂质对生长率有影响。
在有氯化氢的情况下,生长率可提高百分之一到百分之五。
7
多晶硅氧化。
多晶硅的导体和栅极是大多数MOS器件或电路的特性。
器件或电路工艺要求多晶硅氧化。
与单晶硅相比,多晶硅可以更快、更低或相似。
和多晶硅形成相关的一些因素会影响接下来的氧化。
这些因素包括多晶硅沉积方法、沉积温度、沉积压力、掺杂的类型和浓度及多晶硅的晶体结构。
8
不均匀的氧化率及氧化步骤。
经过器件或电路制造工艺的初始氧化后,晶圆表面的条件会有所不同,有的是场氧化,有些是掺杂的,有些是多晶硅区,等等。
每个区有不同的氧化率并且依赖不同的条件氧化厚度会增长。
氧化厚度的不同被称做不均匀氧化(differentialoxidation)。
例如,在相邻的经过轻度掺杂的漏极和源极,形成的多晶硅栅极,可以导致在栅极上的氧化层比较厚,这是因为二氧化硅在多晶硅上生长的比较快(图7.14a)。
不同的氧化率导致了在晶圆表面形成台阶(图7.14b)。
图中显示的是与比较厚的场氧化区相邻的氧化区形成了一个台阶。
在暴露区的氧化反应比较快,因为抛物线特性的限制,场氧化里的再氧化会受到限制。
在暴露区,快速的氧化会比在场氧化层里消耗更多的硅。
图7.14c显示了这个现象。
图7.14硅氧化的不同区分
热氧化方法
氧化反应方程式的反应方向的箭头下,有一个三角。
这个三角表示化学反应需要能量。
在硅技术里,这些能量来源于对晶圆的加热,所以被称为热氧化反应(thermaloxidation)。
二氧化硅层在常压或高压条件下生长。
常压氧化发生在不必有意控制压力的系统中。
有两种常压技术:
炉管反应炉和快速氧化系统(图7.15)。
图7.15氧化方法
热氧化
.常压炉管反应炉干氧
湿氧化
气泡发生器
闪光系统
干氧化
快速热氧化干氧化
.高压炉管反应炉干或湿氧
化学氧化
.阳极氧化电解槽化学的
水平炉管反应炉
水平炉管反应炉从上世纪60年代早期开始应用在氧化、扩散、热处理及各种沉积工艺中。
它最先被开发用在鍺技术里的扩散工艺中。
直到如今一直被简单地称作扩散反应炉(diffusionfurnaces)。
更准确、更通用的词叫炉管反应炉(tubefurnace)。
从水平炉管反应炉发展到有许多优点的垂直炉管反应炉设计,将在接下来的几章中进行详细叙述。
但两种系统的基本工作原理是一样的。
图7.16单炉管,三加热区的水平炉的截面图
源区中央区装载区消声器氧化炉管比例控制器温度平区距离
图7.16显示了一个有三个加热区的水平炉管反应炉的横截面图。
它包含一个由多铝红柱石材料制成的陶瓷炉管,管的内表面有铜材料制成的加热管丝。
每一段加热炉丝决定一个加热区并且由相应的独立的电源供电,并由比例控制器控制其温度。
反应炉最多可以有七个独立的加热区。
在反应炉里有个石英的炉管,它被用作氧化反应室。
反应室可以在一个瓷套管里,瓷套管叫作套筒(muffle)。
它起到一个热接受器的作用,可以使得沿石英炉管的热分配比较均匀。
热电偶紧靠着石英炉管,并把温度信号发回比例控制器。
控制器按比例把能量加到炉丝上,炉丝靠热辐射和热传导加热。
热辐射来源于炉丝的能量蒸发和炉管的反射。
控制器非常复杂,可以通过控制使得中央区的温度精度达到正负0.5摄氏度。
对于一个在1000摄氏度反应的工艺来讲,温度变化只有0,05%。
对于氧化工艺,晶圆被放在承载器中,置于中央区,氧化气体进入石英炉管,在那里发生氧化反应。
详细的实际应用将在接下来的章节中详细论述。
生产中的石英反应炉是一个由各种部件组成的集成系统(图7.17)。
它们是:
1.反应室。
2.温度控制系统。
3.反应炉。
4.气体柜。
5.晶圆清洗站。
6.装片站。
7.工艺自动化。
图7.17炉管反应炉
气源柜反应炉墙板升降机叉杆升降机系统升降机石英舟存储装载站清洁站
反应室
前面已经描述了炉管反应炉的基本操作。
系统的一个重要部件是反应室,它保护晶圆不受外界污染,并且使炉管中的温度均匀。
炉管反应炉的反应室是圆型的,有个气体入口和装片入口。
气体进口端就是所说的气体源端口,它从上到下,逐渐变细,直到一个圆形接口,在此处与气源密封无泄漏相连。
装片口与密封盖或晶圆传送单元连接,以阻止脏东西进入炉管(见自动晶圆传送和手动晶圆传送一章)。
传统的制造反应室的材料是高纯度石英。
石英由于它与生俱来的在高温时的稳定性和洁净度,深受高纯玻璃的喜爱。
它的缺点是脆性,及一些金属离子的存在。
钠离子可以从加热线圈进入反应室。
另一个缺点是在1200摄氏度时,易破碎,易松弛。
破碎叫做钝化(devitrification),这会产生一些碎片掉到晶圆表面。
松弛会阻止晶圆承载器很容易地进出炉管。
石英炉管由两种方法制成:
电熔合与火焰熔合。
就象名字所暗示的那样,两种不同的加热源被用来熔化石英。
两种不同制成的材料含有相同水平的微量金属,但有一种评估显示,用火焰熔合法制成的炉管生产出的器件,其特性会更好。
9
石英炉管需要定期清洗。
一种方法是把它放入氢氟酸或盛有氢氟酸与水的混合溶液的槽里。
这个清洗工艺应在洁净室外进行,炉管应被拆下并已充分冷却。
冷却或加热会加速钝化过程。
氢氟酸清洗可以去掉一层薄的石英。
不断的刻蚀最终会减弱炉管的壁厚,因此,石英炉管的使用寿命是有限的。
有些公司用手提式等离子发生器进行在线炉管清洗。
把等离子发生器放在炉管中以产生刻蚀气体,并使之进入炉管中。
氨气和刻蚀气体可以去除污染。
第二种在线清洗方法用在炉管中产生等离子气体。
这种方法更适用于化学气相沉积工艺,该工艺产生的颗粒比氧化工艺产生的要大。
另一个石英炉管和晶圆承载器的替代材料是碳化硅。
碳化硅结构非常硬,并且经过多次加热和冷却后,不容易破碎。
这种冷热循环的不敏感性,使得它也成为一个好的金属离子阻挡器。
在一些有氧气的工艺里,内壁会生长一层薄的二氧化硅。
当用氢氟酸清洗后,不会对影响它寿命的材料有破坏作用。
碳化硅的炉管和晶圆承载器的广泛应用由于其价格的昂贵和重量问题而使其发展得较慢。
温度控制系统
温度控制是这样一个系统,它把紧靠反应管的热电偶连接到比例控制器上,比例控制器把能量加到加热炉丝上。
比例控制器上按照炉管与设定值的差值按比例的开关通向炉丝的电流以保持在炉管里温度的均匀。
温度越接近设定值,供给炉丝的能量就越少。
此系统可以使炉管在没有超调的状态下,快速从冷态恢复。
偏差调整一直在进行,直到达到温度设定值。
超调现象是由于控制温度时,给线圈施加了太多的能量,以至于温度超过设定值的一种现象(图7.18)。
图7.18氧化中不同的温度水平
在高级系统里,热电偶紧靠炉管外壁。
它通过微处理器给控制器提供信息,这种系统叫自动温度分布曲线控制系统(autoprofiling)。
10好的系统要求炉管内的温度曲线可以定时检测,并由独立的记录仪记录温度。
对于较大直径的晶圆,我们关心晶圆的翘曲问题。
快速的加热和冷却使得晶圆容易发生翘曲现象。
在超过1150摄氏度以上,随着温度的升高,翘曲的程度会越高。
有两种方法可以减轻晶圆的翘曲:
一种是逐渐加温(ramping)。
这种技术是让炉管在平常时保持在一个低于反应温度几XX的温度上,晶圆在此温度下被缓慢送入炉管,然后经过一个短暂的温度稳定期,控制器自动把温度加到设定值。
在工艺反应的最后,炉管被冷却到低温,然后卸载晶圆。
在逐步温控时,控制器必须保持炉管中央区的温度控制。
由于石英炉管的钝化现象和需要很长时间来使中央区温度稳定,反应炉需要一天24小时的保持接近工艺所需的温度。
但从经济角度来考虑,一些晶圆制造商,喜欢在不生产时把温度保持在一个低温,这叫待机状态(idle)。
第二种防止晶圆翘曲的方法是缓慢地把装载晶圆的石英舟推进炉管。
推进速率在每分钟1英寸时,翘曲最小。
对于大直径晶圆,和多晶圆批量生产时,以上两种方法会同时使用。
另一个对加热系统的要求是在装载晶圆进入炉管后,要有一个快速的恢复时间。
当满载时,温度会下降50摄氏度或更多。
11加热系统应在不引起翘曲或温度超调的前提下,尽快达到工艺要求的温度。
图7.18表示了一个有五个加热区的反应炉的典型的温度恢复曲线。
反应炉结构
一个在实际生产应用中的炉管反应炉有三到四个炉管,每个炉管有自己的温度控制器。
这些炉管垂直的一个摞在一个上,炉管接在排风腔上,排风腔把反应完的气体和热气排出炉管。
反应炉的这部分叫“清除机”。
清除机连接到厂务的排气系统上,此系统包含一个废气处理器来进行废气处理。
一排炉管可以用于同一种工艺,例如氧化工艺;
或被设计成不同的操作,例如依据工艺要求和生产的批量要求进行氧化、扩散、合金或化学气相沉积。
变换用途需要变换炉管并进行污染监测以确保每个炉管没有交叉污染。
气体柜
每个炉管需要一定数量的不同气体来完成所要求的化学反应。
在氧化反应的例子里,作为氧化剂的氧气和水蒸气已被详细论述过。
几乎所有的炉管工艺都有通入氮气的能力。
氮气用来在装片或卸片时防止意外氧化。
在待机状态时,氮气一直在流过炉管以保持炉管的洁净。
每个工艺要求气体以一定的次序、一定的压力、一定的流量和一定的时间流入炉管。
用来调节气体的设备附着在炉管部分,被称为气体柜(sourcecabinet)。
还有个独立单元,叫气体控制面板(gascontrolpanel)或叫气体流量控制器(gasflowcontroller),它连到每个炉管上。
控制面板由电磁阀,压力表,物流控制器或流量计和计时器组成的。
在最简单的版本里,气体控制器由手动阀和计时器组成的。
在生产系统里,进入炉管的各种气体和先后次序是由微处理器来控制的。
工艺所需的气体被接到面板上。
在操作时,计时器打开阀门让所需的气体流入。
压力由压力表来控制,流量由物流控制器或流量计控制。
物流控制器(massflowmeter)由于它特有的高精度,使得它比流量计更好。
化学计量要求流入炉管的气体用物量来计算。
标准的流量计计算物质的体积,由于温度和压力的不同,一定体积的物质所含的物质量可能不同。
半导体工艺用热型的物流流量计,这个系统包含一个有两个传感器的加热气体的通道。
当没有气体流过时,温度传感器的温度一样;
当有气体流动时,下游的传感器读数比较高。
两个传感器的读数的偏差与流过的热物流(而非体积)有关。
控制器有个反馈机构来控制气体以稳定的一定量的物流流过物流控制器。
气体源也有一个由微处理器控制的阀门来计量气体以一定的次序和一定的时间流入炉管。
图7.19显示了一个物流控制器的基本结构。
物流控制器可以被设计为一定量的物流值和在线传感器检测和反馈输出控制系统12。
气体流量控制器中的管路材料是不锈钢材料的,用来保持高洁净度,使气体与炉管材料之间的化学反应达到最小化。
图7.19(a)物流控制器的操作原理(b)切面图
气体进入传感器管温度传感器加热器温度传感器气体出传感器惠丝通桥
电压输出与温度变化及物流成比例去电源
器件主体结构电屏蔽可选择的电磁阀门可互换的的阀座进口层流单元传感器管
通常,气体控制器被称做“丛林(jungle)”。
当在厂务装配气体控制器时,那些管子和阀门看起来是乱的就象是丛林。
气体有来自厂务的液态气源或附着在机器内部的小瓶气源,经过管道流入气体控制器。
有些工艺要求的化学气体用气体形式传输起来非常困难。
在这种情况下,气泡器和液体源就应运而生。
气泡器包含一个石英部件,它用来使气体液化。
当气泡通过液体,和在气泡器顶端的载体气体混合,由载体气体