注塑模具的设计及其热分析中Word文件下载.docx
《注塑模具的设计及其热分析中Word文件下载.docx》由会员分享,可在线阅读,更多相关《注塑模具的设计及其热分析中Word文件下载.docx(12页珍藏版)》请在冰豆网上搜索。
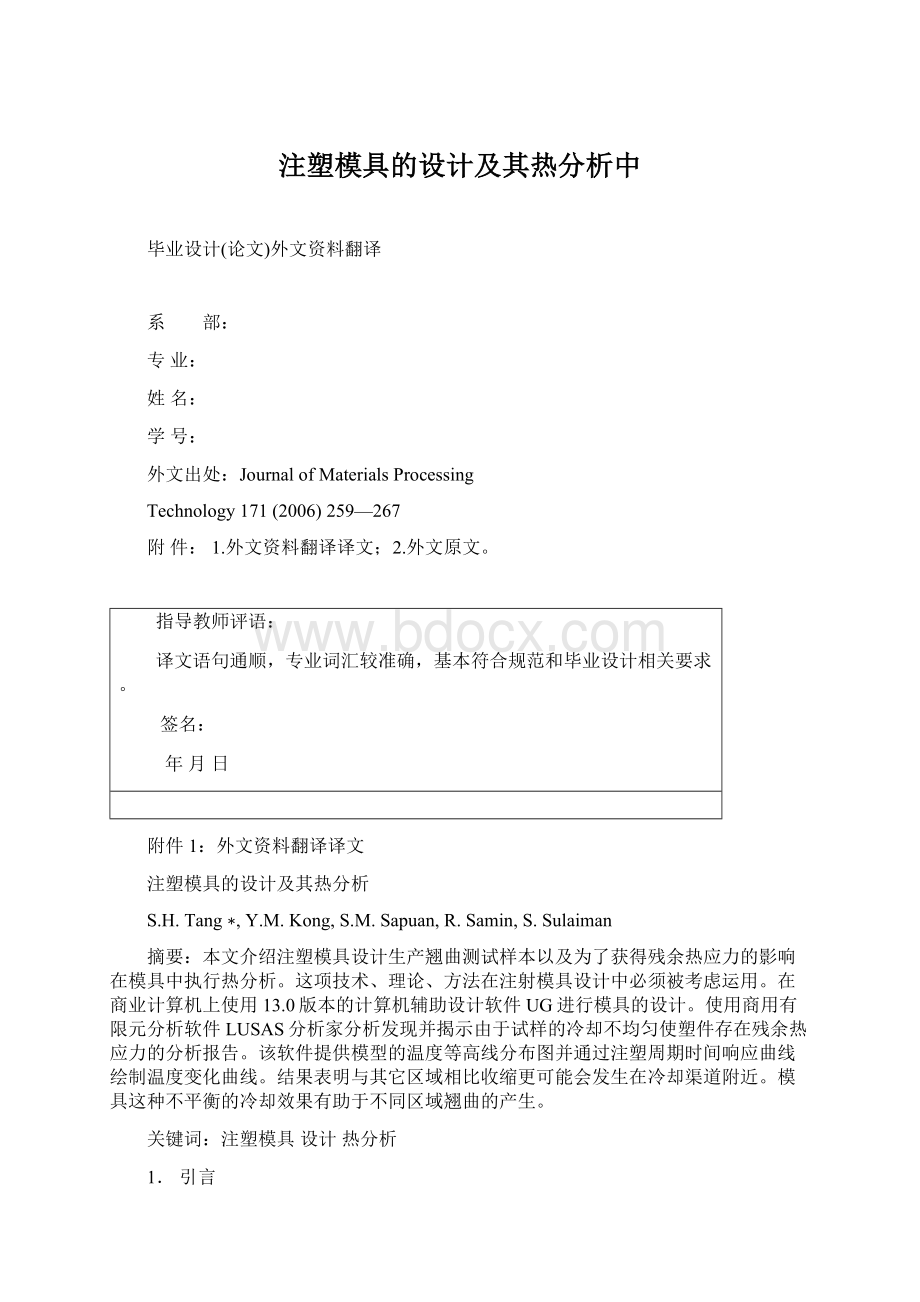
注塑模具的设计及其热分析
S.H.Tang∗,Y.M.Kong,S.M.Sapuan,R.Samin,S.Sulaiman
摘要:
本文介绍注塑模具设计生产翘曲测试样本以及为了获得残余热应力的影响在模具中执行热分析。
这项技术、理论、方法在注射模具设计中必须被考虑运用。
在商业计算机上使用13.0版本的计算机辅助设计软件UG进行模具的设计。
使用商用有限元分析软件LUSAS分析家分析发现并揭示由于试样的冷却不均匀使塑件存在残余热应力的分析报告。
该软件提供模型的温度等高线分布图并通过注塑周期时间响应曲线绘制温度变化曲线。
结果表明与其它区域相比收缩更可能会发生在冷却渠道附近。
模具这种不平衡的冷却效果有助于不同区域翘曲的产生。
关键词:
注塑模具设计热分析
1.引言
塑料工业被列为一个数十亿美元的产业,是世界上增长最快的行业之一。
在日常生活中几乎所有的用品都离不开塑料,而大多数这些塑料都可以用注塑的方法生[1]。
众所周知注塑成型加工是以较低的成本生产各种形状复杂的几何体产品[2]。
注塑成型加工是一个循环过程。
在注塑过程中有四个重要的阶段。
这四个阶段是加料阶段、保压阶段、冷却阶段和顶出顶出。
塑料注塑成型加工首先是往注射机料斗中添加树脂和适当的添加剂,并加热塑料注射机的料斗到喷嘴部分[3]。
在注射温度下模具型腔充满热聚合物熔体,在模具型腔填满后的保压阶段,更高压力下更多的聚合物熔体装入型腔,以补偿前期聚合物凝固引起的收缩。
接下来是模具的冷却阶段,塑件在排出前被冷却到足够的强度。
最后一步是顶出阶段,模具开模同时顶出塑件,然后模具再次合上并开始下一个周期。
事实证明设计和制造理想性能的高分子注塑成型零件是一个昂贵的工程,包括反复修改加工,在模具设计任务中,设计模具明确附加几何结构,核心方面通常包括相当复杂的凸凹面[5]。
为了设计模具必须考虑许多重要的设计因素。
这些因素分别是模具的尺寸、型腔数、型腔的布局、浇注系统、浇口系统、收缩和顶出机构[6]。
在模具的热分析中,其主要目的是分析影响残余热应力或压力对产品尺寸的影响。
热诱导应力主要发生在注塑成型的冷却阶段,主要是因为其热传导性低以及熔融树脂与模具之间的温差。
在冷却期间产品的冷却腔周围温度存在不均衡[7]。
在冷却时,冷却管道附近的冷却效果比远离冷却管道区域的冷却效果好。
不同的温度导致不同的收缩,不同的收缩导致热应力而显着的热应力可能会导致翘曲问题。
因此,在冷却阶段对注射工件进行残余热应力模拟分析是非常重要的[8]。
通过了解热应力的分布特点,可以预测残余热应力引起的变形。
本文介绍了注塑模具设计生产翘曲试样以及为了获得残余热应力影响而在模具中执行热分析。
2.方法
2.1设计翘曲测试样本
本节说明了用于注塑模具的翘曲测试样品的设计。
很显然翘曲的主要问题存在于产品的薄壳特征。
因此,产品开发的主要目的是设计一个塑件,以确定注塑工件薄壳翘曲问题的有效因素。
翘曲测试样本是薄壳塑料。
样本的总体尺寸长120mm,宽50mm,厚1mm.用丙烯腈-丁二烯-苯乙烯共聚物(ABS)作为材料,在注射温度为210℃,压力为60MPa,持续3s时间生产翘曲测试样本。
图1显示了翘曲测试样本的制作
图1翘曲测试样本制作
2.2翘曲测试样本注塑模具的设计
本节介绍了设计生产翘曲测试标本时,在模具的设计方面和其他方面的考虑因素。
用于生产翘曲测试样本注塑模具的材料是AISI1050碳钢。
在模具设计时考虑了四个构思,其中包括:
.三板式模具(构思1)有一个型腔两个分型面。
由于成本高,所以不适用。
.两板式模具(构思2)有一个型腔一个分型面但无浇注系统。
由于单位时间内注射生产量低,不适用。
.双板模具(构思3)有一个分型面和两个型腔,带浇注和顶出系统。
由于塑件的是薄壳的,顶杆可能破坏工件,所以不适用。
.双板模具(构思4)有一个分型面和两个型腔带浇注系统,只用拉料杆为顶出机构,避免顶出时破坏塑件。
翘曲测试样本模具设计的第四个构思被应用。
在模具设计中,还有许多因素需要考虑。
首先,根据注塑机使用的压板尺寸设计模具。
注塑机行程是有限的,通过两个拉杆间的距离确定注射机的最大行程。
注射机两个拉杆间的距离为254mm,因此,最大模板宽度不应超过254mm这个距离。
此外在模具和两连杆中留出4mm的间隙便于模具的拆装。
这最终使模具最大宽度250mm。
250X250的标准模架最终被使用。
其他有关模板的尺寸则列于表1
成分
规格(mm)宽×
高度×
厚度
顶端夹紧板
定模座板
动模座板
支承板
推杆固定板
推板
夹紧板底
250×
250×
25
200×
40
37×
70
120×
15
20
模具已设计了夹紧压力,锁模力应高于内部腔力(反作用力)以避免飞边的发生。
以提供的标准模架尺寸为根据,凹模的宽度和高度的分别是200和250毫米,使得模板上的这些尺寸有足够的空间设计两个水平的型腔,而凸模只需留有固定浇口套的空间以便注入溶融塑料。
因此,在产品的表面只设计了一个分型面。
在开模的时候,塑件和流道在分型面上被分开。
模具设计了直接浇口或侧浇口。
浇口位于流道和塑件之间。
为了便于注入塑料浇口底部设计了一个20°
的锥角斜度和0.5mm的壁厚。
为了熔融塑料的流入,还设计了4mm宽,0.5mm厚的浇口。
在模具设计时,选定了抛物面类型的流道。
在这种情况下,它的优点是仅需简单的加工模具凸模部分。
然与圆形截面类型相比,这种类型的流道有不利之处,如更多的热量损耗和废料。
这可能会导致熔融塑料更容易固化。
所以在设计时应缩短流道长度并增大流道直径至少有6mm。
材料或熔融塑料在同一温度同一压力下同时被送到个模腔对于流道设计来说是很重要的一点。
基于这点,模腔的布局一般都是对称的。
另一个设计方面是考虑到了气孔设计。
凹模和凸模配合面之间有非常好的修整,以防止飞边的发生。
然而当模具闭合时,可能会导致空气闭于型腔内,导致塑件注射不足或不完整。
设计足够多的通风孔以确保型腔内的空气可以被释放,避免不完整的塑件发生。
为了让冷却更均匀,冷却系统沿着模具型腔水平设置。
在紊流的情况下,冷却渠道提供了足够的冷却水冷却模具。
图2显示了在凸模上气孔和冷却管道的布局。
图2凸模上气孔和冷却管道的布局
在此模具设计中,顶出系统只由推杆固定板、拉料杆,浇口套组成。
拉料杆设置与凸模的中心位置,在模具打开时不仅承担拉着塑件到适当的位置,而且在顶出阶段,作为推杆从模具中推出塑件。
因为生产的产品仅有1毫米非常薄的,所以没有额外推杆被使用或设置。
在顶出阶段额外的推杆可能会造成塑件产生孔或破坏塑件。
最后,为补偿材料的收缩足够的尺寸偏差被考虑。
图3显示三维实体造型,以及利用UG开发的模具的线框模型
图3三维实体造型以及利用UG开发的模具的线框模型
3.结果和讨论
3.1塑件的制作生产及调整
从模具设计和制作的角度看,在试运行阶段制作的翘曲测试样本存在缺陷。
该缺陷是注射不足,飞边和翘曲。
飞边后来通过在型腔角上铣削额外的气孔让空气排除的方法解决。
同时,通过减小注塑机压力减少了飞边的产生。
通过控制注射时间、注射温度、熔融温度等不同参数,控制翘曲变形。
经过这些修改,模具在低成本的情况下生产出了高质量的翘曲测试样本,这些试样还需要修整。
图4显示修整后的模具,这是加工额外的排气孔可以消去注射不足。
图4加工额外的排气孔可以消去注射不足
3.2.模具和产品详细分析
在塑料注射成型过程中,熔融ABS在210◦C温度下通过凹模上的浇口衬套直接注射到模具型腔,经过冷却,塑件就成型了。
塑件的生产周期需要花35秒,包括20秒冷却时间。
用于生产翘曲测试样本材料的是ABS在注射温度、时间、压力分别为210℃,3秒和60MPa。
运用有限元软件分析材料性能在决定温度上非常重要。
表2列出了ABS以及AISI1050碳钢的性能。
模具分析主要是凹模和凸模,因为他们是形成塑件的地方。
因此,使用13.5版本的商用有限元分析软件LUSAS分析家研究不同时段温度的分布。
使用二维热分析研究残余热应力在不同区域对模具的影响。
由于对称性,只要通过凸模的垂直断面或在注射阶段当凸凹模合在一起时的侧面图建立模型执行热分析。
图5所示的是模板的热分析模型。
图5模具热分析
建立模型包括分配各部分的性能以及模型的循环周期。
这样可以用有限元分析软件用造型模拟模具模型进行分析,还可以绘制时间响应曲线显示再某段时间内特定区域的温差变化。
对试样分析,使用13.5版本的LUSAS分析家进行双向拉伸应力分析。
一般只需在试样的一端施加拉力另一端则固定住,然后慢慢增加拉力一直到达塑性极限。
图6所示的是分析的负载模型。
图6负载模型分析的产品。
3.3.模具及试样分析的结果及讨论
模具分析过程对不同时间段的热量分布作了观测。
图7所示是在一个完整的注塑周期中不同时间段的二维等高线热量分布图。
图7不同时段温度分布图
对模具进行二维分析后,可绘制出时间响应曲线以分析残余热应力对制件的影响。
图8所示是绘制时间响应曲线所选的节点。
图8绘制时间响应曲线所选的节点
图9到图17显示了在图8中被标注的不同节点的温度分布曲线
图9节点284温度分布
图10节点213温度分
图11节点302温度分布
图12节点290温度分布
图13节点278温度分布
图14节点1838温度分布
图15节点1904温度分布
图16节点1853温度分布
图17节点1866温度分布
从图9—17中很显然被选择用来绘制曲线的每一个节点的温度都是递增的,也从室温到高于室温,然后再次温度下保持一段时间。
这些温度上升是由于塑料溶液注入到了塑件的型腔内造成的。
经过一段时间后,温度进一步上升直至达到最高温度,然后保持在最高温度下。
由于保压阶段涉及高压导致温度上升。
温度保持不变直到冷却阶段开始,从而导致模具温度减小到一个低值,然后保持该低值。
绘制的曲线是不平滑的,因为注入熔融塑料的速率和冷却速率是相应的。
绘制的曲线图仅仅显示了在周期内温度能达到的最大值。
冷却阶段是决定残余热应力的最关键阶段。
这是因为冷却阶段,材料冷却从上面到下面玻璃化转变温度。
物质的不均匀收缩可能产生热应力从而引起翘曲。
如图9-17中所示冷却阶段后的温度,很明显在冷却管道附近的塑件由于温度减小的更多,塑件获得了更好的冷却而远离冷却管道区域的塑件冷却效果差。
冷却效果好、冷却速度快意味着在该区域发生更多的收缩。
最远的区域节点284,虽然远离冷却管道,但由于向空气中散热冷却更快。
因此,冷却通道设在产品型腔的中心,造成冷却管道附近和其他区域间产生温差。
由于发生收缩使得在塑件的中心区域产生压应力以及由于发生不均衡的收缩导致翘曲。
然而,在冷却后不同节点的温差很小,翘曲变形也不是很明显。
对设计师来说设计一副残余热应力效果小和高效的冷却系统是非常重要的。
对于产品分析,从被实行开始到分析塑料产品,在产品上不同载荷因素的状态下的应力分配情况可以通过观察生成的二维曲进行线分析。
图18—21显示了不同荷载增量下的等效应力图。
图18荷载增量1下的等效应力图
图19荷载增量14下的等效应力图
图20荷载增量16下的等效应力图
图21荷载增量23下的等效应力图
在关键的127节点,选定产品的最大拉应力进行分析。
应力应变曲线和应力负载增量曲线。
如图22和23
图22应力应变曲线
图23应力与负载增量曲线
参考负载应力曲线如图23,它很清楚表明产品在增加拉力载荷,直到它达到了23的负载因数,这意谓产品能抵抗的1150N的拉力。
由图23可知,对产品的固定端以施加最大应力3.27×
107Pa时损坏可能发生在其附近区域。
该产品应力分析资料十分有限,因为生产产品的目的是为了翘曲测试,所以没必要进行拉伸负载分析。
但是在未来,应当确定产品情况,以便在其他各种负载情况下执行进一步的分析。
4.结论
经过翘曲测试试样的分析确定影响翘曲的参数来设计的模具已经使产品质量达到最高。
生产测试试样所需的成本很低而且只需经过很少的表面处理。
通过注塑模的热分析得出残余热应力对试样的影响,对加载拉应力的分析也可以预测到翘曲测试试样所能承受的最大拉力。
鸣谢
作者要感谢马来西亚博特拉大学工学部发行出版了本文。
参考文献
附件2:
外文原文(复印件)