机械制造技术基础课程设计指导书文档格式.docx
《机械制造技术基础课程设计指导书文档格式.docx》由会员分享,可在线阅读,更多相关《机械制造技术基础课程设计指导书文档格式.docx(24页珍藏版)》请在冰豆网上搜索。
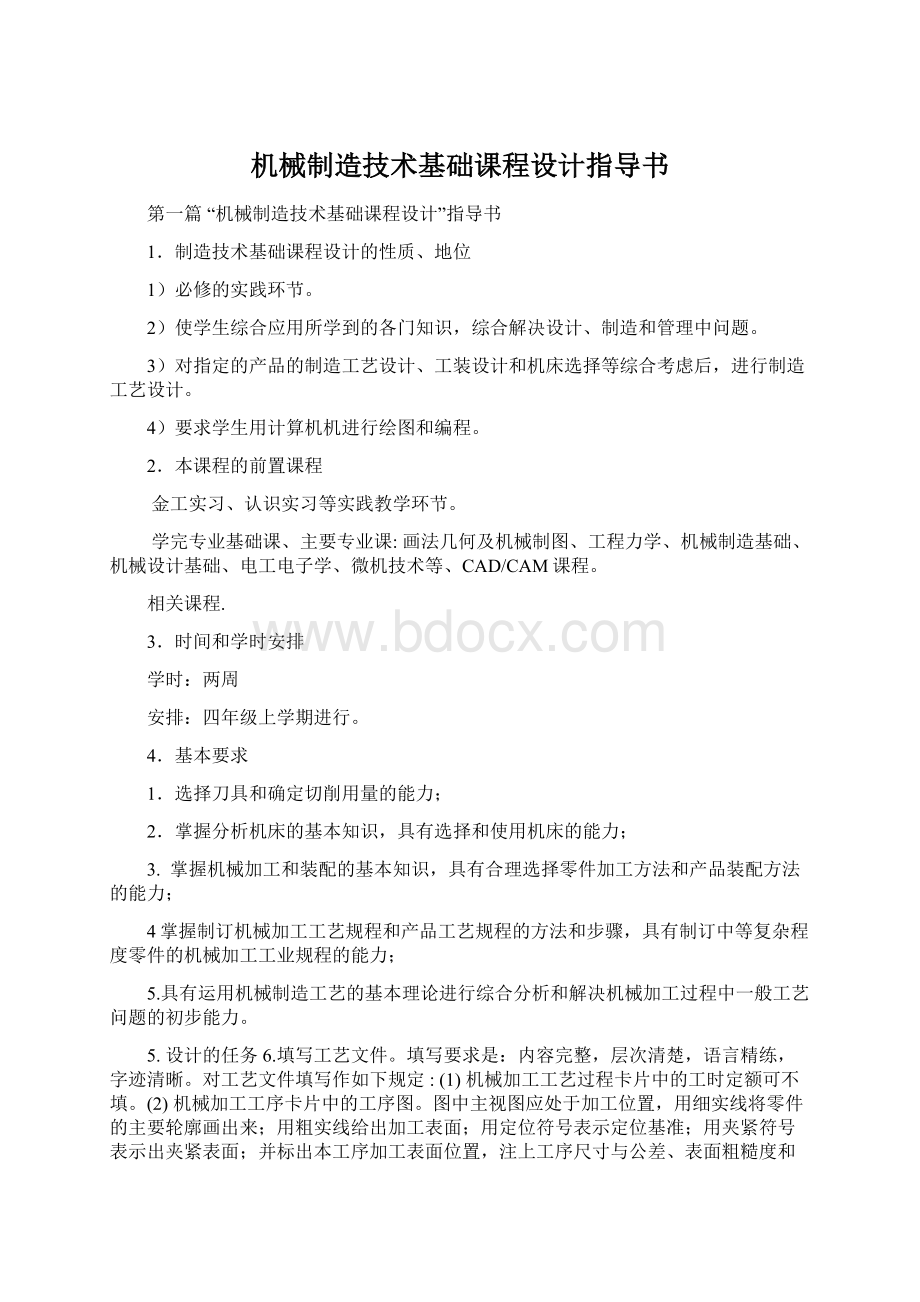
(6)生产效率分析。
7.考核办法
(1)实物:
工艺卡、工装图纸、说明书和程序等。
(2)答辩。
(3)评分方法:
等级制:
优秀、良好、中等、及格和不及格共五个等级。
(4)考勤。
8.工艺规程的制订过程
(1)
概述:
生产过程与工艺过程,机械加工工艺过程的组成,生产纲领与生产类型,机械加工工艺规程(内容,作用,格式,制订原则,原始材料及制订步骤)。
(2)零件的工艺分析:
结构工艺性分析,技术要求分析。
(3)毛坯的选择。
毛坯加工余量的确定。
(4)基准及其选择:
基准及其分类,定位基准选择(粗基准选择,精基准选择)。
(5)工件在夹具中的定位与夹紧。
(6)工艺路线的拟订:
方法选择,阶段的划分,顺序的安排,工序的集中与分散。
(7)加工余量的确定:
加工余量的概念,确定加工余量的方法。
(8)工序尺寸及其公差的确定:
工艺尺寸链,工序尺寸及其公差的确定方法。
(9)机床、工艺装备及切削用量的选择
(10)机械加工的时间定额与技术经济分析:
时间定额、工艺过程的技术经济分析(工艺成本计算,工艺方案比较),提高劳动生产率的工艺途径。
9.机械加工精度
(1)概述:
机械加工精度的概念,影响机械加工精度的因素。
(2)工艺系统的几何误差对加工精度的影响:
原理误差,机床的几何误差,刀具和夹具的制造和磨损误差,工艺系统的定位和调整误差。
(3)工艺系统的受力变形对加工精度的影响:
工艺系统的刚度,受力变形引起的加工误差,减少受力变形的主要途径。
(4)工艺系统的热变形对加工精度的影响:
工艺系统的热变形及其引起的加工误差,减少热变形的主要途径。
(5)工件内应力引起的变形对加工精度的影响:
内应力产生的原因及其引起的误差,消除内应力的方法。
(6)加工误差的综合分析实例。
(7)加工误差的统计分析。
(8)保证和提高加工精度的途径。
10.机械加工表面质量
表面质量的概念,表面质量对零件使用性能的影响。
(2)影响零件表面粗糙度的因素及其改善的工艺措施。
(3)影响零件表层物理机械性能的因素及其改善的工艺措施。
(4)机械加工中的振动及其对加工表面质量的影响。
11.典型加工工艺
11.1.
轴类零件的加工工艺
掌握轴类零件的功用、结构特点、技术要求和轴类零件的材料及毛坯。
掌握轴类零件的预加工。
(2)轴类零件外圆面的车削、磨削及精密加工和花键及螺纹加工:
1)车削的工艺范围、加工阶段的划分及特点,重点为细长轴。
2)掌握外圆磨削的特点、工艺范围及磨削方式,掌握顶尖孔的作用、技术要求及对加工质量的影响。
了解顶尖孔的加工及修研。
3)了解外圆表面精密加工的方法:
细车、超精加工、高光洁度磨削、研磨滚压。
4)了解花键及螺纹加工。
(3)典型轴类零件工艺分析:
定位基准的选择,热处理工序的安排,加工阶段的划分,工序顺序的安排。
了解丝杠加工工艺分析。
●典型轴类加工工艺:
装载机输出轴工艺
表1.装载机输出轴加工工艺过程工艺卡
机械加工工艺过程卡片
产品型号
ZL40/50
零(部)件图号
403309d
共3页
产品名称
装载机
零(部)件名称
输出轴
第1页
材料牌号
42CrMo
毛坯种类
毛坯外形尺寸
每毛坯件数
每台件数
备注
序号
工序名称
工序内容
车间
工
段
设备
工艺装备
工时
准终
单件
1
正火:
HB170~~~207,校直
综
2
粗车:
见工艺附图
金
车
B4中心钻
3
精车:
4
1)
銑矩形花键盘16-72b12×
62dq×
6d12,键宽铣至6+0.25+0.20,键底铣至ф62+0.20+0.15(6.3√),有效长度加4mm
花键铣
16—72×
62×
6.4B铣刀
2)
铣两端渐开线花键,M=53.450-0.05,花键节跳≤0.04
5
去刺
钳
M2.5/1.25α30p花键铣刀
6
油淬,硬度HRC45~50,(在Φ66外圆检查),淬火时加保护套,
保护螺纹及Φ42面
热
7
校直:
两端花键跳动≤0.05,(Ф66外圆检查)
8
两端螺纹磁力探伤
检
9
研磨两端中心孔
10
两端上顶尖,磨矩形花键,键宽至6-0.09-0.15,键底至Ф62-0.13-0.17
花研磨
11
两端上顶尖,磨两端Ф60m6和Ф42h8,磨3.2√端面至图要求
外磨
12
过牙
13
总检入库
编制
日期
标记
处记
更改文件号
签字
日期
11.2.套筒类零件加工
(1)概述
掌握套筒零件的功用、结构特点、技术要求,套筒零件的材料和毛坯。
掌握套筒零件加工的主要工艺问题。
(2)套筒类零件的内孔加工的一般加工方法和内孔的精密加工
1)掌握内孔表面常用的加工方法,掌握钻孔、扩孔、铰孔、镗孔、磨孔、拉孔、深孔加工的工艺特点。
2)了解内孔表面精密加工的加工方法,了解精细镗、珩磨、研磨、滚压的工艺特点。
(3)套筒零件加工工艺分析
掌握短套筒类零件加工工艺分析;
保证套筒表面位置精度的方法,防止分简变形的工艺措施。
了解长套简零件加工工艺特点。
11.3.
箱体类零件的加工工艺
掌握箱体零件的功用、结构特点、主要技术要求、毛坯、材料及结构工艺性,掌握箱体零件加工的主要工艺问题。
(2)箱体零件的平面加工方法
掌握机体平面常用的加工方法,掌握平面刨削、铣削、磨削、刮研的工艺特点。
(3)箱体的孔系加工
掌握孔系的概念、分类及孔系加工应解决的工艺问题,掌握平行孔系加工常用的加工方法及它们的特点,掌握同轴孔系的加工常用的加工方法。
(4)箱体零件加工工艺分析
掌握车床主轴箱加工艺过程分析:
主要表面加工方法的选择,拟定工艺过程的原则,定位基准的选择。
掌握分离式齿轮箱箱体的工艺特征:
加工路线的拟定,定位基准的选择。
11.4.圆柱齿轮的加工工艺
要求注意齿轮的功用、结构特点、技术要求及齿轮的材料和毛坯,拿握齿轮加工的主要工艺问题和一般工艺路线,掌握圆柱齿轮加工工艺过程分析:
定位基准的选择,齿轮的热处理,齿形加工方案的选择,精基准的修正。
了解齿坯加工的各种工艺方案及齿端加工,掌握展成法加工齿轮齿形的常用方法,了解滚齿、插齿、剃齿、挤齿、珩齿、磨齿的工艺特点。
●典型壳体类加工工艺:
表2装载机差速器右壳加工工艺过程工艺卡
华侨大学机电学院
机械加工工艺
过程卡片
502340A
504322B
共2页
差速器右壳
第1页
QT450—10
球铁
工序号
工序
名称
工段
工时
01
铸造
铸造毛坯
02
时效
03
清洗检查
铸件内外非加工表面彻底清洗干净,涂耐油漆同时检查铸件是否有缺陷
04
粗车
转塔六角
车床
三爪自定心卡盘、球面加工辅具
05
数控车床
专用夹具
06
半精车
精车
三爪自定心卡盘
07
止口定位螺栓压板
08
钻孔
锪孔
见工艺附图(12-φ16.5、8-φ14.5)
见工艺附图(12-φ33、8-φ33)
摇臂钻床
钻模板、专用夹具
编制(日期)
审核(日期)
会签(日期)
XXX
04.07.08
共2页
第2页
09
见工艺附图(φ18盲孔)孔口去刺
磨削
见工艺附图-装配图(φ75m6
外圆磨床
心轴、专用夹具
扩孔
镗孔
见工艺附图(4-φ28H7)
卧式镗床
14
喷丸
15
各工序必须检验
差速器右壳毛坯图
差速器右壳部分工序图
●典型轴类加工工艺:
.倒顺轴齿轮工艺
(1)说明
1)零件的工艺分析
从倒顺轴齿轮的零件图上可以看出,齿轮轴两个支承轴颈的精度和同轴度要求较高,所以必须正确选择定位基准;
工序按粗、精加工分开;
合理安排工序。
⒉)选择毛坯
零件的材料是合金钢1818CrMnTi,生产类型为大批生产,采用在锻锤上合模模锻毛坯。
⒊)工艺过程设计
●●定位基准的选择
在轴类零件加工中,为保证各主要表面的相互位置精度,选择定位基准时,应尽可能使其与装配基准重合并使各工序的基准统一,而且要考虑在一次安装中尽可能加工出较多的面。
●精基准的选择
为保证支承轴颈与主轴内锥面的同轴度要求,当选择精基准时,要根据互为基准的原则。
先加工好前、后锥孔,以便安装锥堵,为半精加工、精加工外圆准备定位基准。
当加工齿轮圆周面时,以外圆ф50及齿轮两端面为定位基准。
●粗基准的选择
工艺过程一开始就选择以外圆柱作粗基准车端面,打中心孔,为粗车外圆准备了基准。
而车外圆又为深孔加工准备了基准。
●●加工方法的选择
ф84齿轮的加工方法为粗滚、精滚。
ф50h7
、ф50k6
外圆的终加工为互为基准进行精磨,其前面的工序可为粗车和精车。
●●加工工艺过程的分析
由于主轴精度要求高,且在加工过程中要切除大量金属,因此必须将其工艺过程划分为几个阶段,将粗加工和精加工安排在不同的阶段:
●粗加工阶段
①毛坯处理备料、锻造和正火(工序1~3)。
②粗加工锯去多余部分、铣端面,打顶尖和粗车外圆等(工序4~8)。
这阶段的主要目的是:
用大的切削用量切除大部分余量,把毛坯加工到接近工件的最终形状和尺寸,只留下少量的加工余量。
该阶段还可及时发现锻件裂缝等缺陷,以采取相应的措施。
●半精加工阶段
①半精加工前热处理对合金钢采用渗碳处理。
②半精加工车工艺锥孔(定位锥孔),半精车外圆端面等,该阶段的主要目的是为精加工做好准备,尤其是为精加工做好定位基准的准备。
●精加工阶段
①精加工前热处理淬火处理(工序11)。
②精加工前各种加工精车与粗磨外圆,铣花键以及车螺纹等。
③精加工精磨外圆以保证主轴最重要表面的精度(工序14),该阶段的目的是把各表面最终加工到图纸规定的要求。
●●制订工艺路线
制订工艺路线的出发点,应当是使零件的几何形状、尺寸精度及位置精度等技术要求能得到合理的保证。
表3倒顺齿轮轴加工路线
其中:
图11.4-1倒顺齿轮轴的毛坯件
粗车外圆的具体工艺:
①夹左端外圆车右端面打一中心孔
②上尾顶尖,车右端各部,留余量至ф54.8
③夹右端外圆车左端面打一中心孔
④上尾顶尖,车左端各部,留余量至ф54.8
⑤车削齿轮部分外圆,留余量至ф103.86
(⒋)填写工艺文件(附件)
表4倒顺州齿轮加工工艺过程卡。
福建三明齿轮
YZ14B.4.6-3
共1页
倒顺轴齿轮
材料
18CrMnTi
模锻件
毛坯尺寸
610mm
105mm
毛坯件数
大批生产
序号
工序内容
设备
工艺基准
工时
备料
锻造
模锻
热处理
正火
划线平台
车端面
龙门铣床
毛坯外圆
粗车外圆
①夹左端外圆车右端面打一中心孔;
;
③夹右端外圆车左端面打一中心孔;
⑤同时车齿轮部分外圆,留余量至ф103.86
顶尖孔
精车外圆
①两端上顶尖,车两端外圆,留余量至ф52.3
②齿轮部分外圆加工至ф101.36
锥堵顶尖孔
粗精滚齿轮
齿轮公法线按上差加工k=33.323-0.105、m=7、Z=12
外圆ф50及齿轮两端面
钳工
修毛刺锐角
卧式镗铣床
热处理
渗碳处理
淬火前精车,留余量至ф50.5
淬火处理
车两端面
车两端面至要求、修中心孔
ф50外圆
粗磨端面
粗磨齿轮两端面至要求
精磨外圆
精磨齿轮两侧ф50h7、ф50k6外圆
粗精铣花键
铣两端ф50f7花键
清洗机
16
钻攻螺纹
钻螺纹孔并攻牙M16
17
18
检验
按图纸要求全部检验
审核(日期)
合签(日期)
标记
签字
日期
下图为倒顺轴齿轮工作图。
11.5.
装配工艺
了解装配的概念、基本内容及组织形式。
(2)机械产品的装配精度:
了解装配精度的概念及装配精度与零件精度间的关系,了解装配尺寸链的概念及建立。
(3)装配方法及其选择
1)掌握保证产品装配精度的装配方法。
2)掌握互换法的概念、特点及实质,掌握完全互换法、大数互换法和分组互换法的概念、特点、实质及应用范围。
3)掌握修配法的概念及特点,了解修配法的型式及各种修配法的特点,掌握修配环的选择原则。
4)掌握调整法的概念、特点,了解调整法的形式,掌握可动调整法和固定调整法。
5)掌握装配方法的选择原则。
12.课程设计选题与实践
12.1选题
所选零件的结构应具有工艺方案及加工方法选择上的多样性,零件的复杂程度要适中,加工工序数以8~10道为宜。
12.2具体要求
(1)总概念
1)分析机械加工工艺过程的组成、工序的概念、划分及构成工序的四个要素,掌握工步的概念及其划分。
了解走刀、安装、工位的概念及划分.掌握生产纲领的概念、计算、生产类型的划分,本握各生产类型的特点及应用。
2)了解机械加工工艺规程的作用和制订工艺规程的基本原则。
原始资料及步骤,掌握常见工艺文件的类型及各类型的特点及应用。
(2)零件的工艺分析:
掌握零点件结构工艺性。
(3)毛坯选择:
注意毛坯的种类、特点、选择原则、毛坯形状和尺寸确定。
(4)工件的定位及定位基准的选择
1)了解基准的分类,掌握获得表面尺寸精度的试切法和调整法的概念及特点,掌握工件在机床上定位的三种方法的概念、特点及应用。
2)掌握粗、精基准的概念和总的要求,掌握粗、精基准选择的原则及特点,能对简单零件的各加工工序选择合理的粗、精基准。
(5)工艺路线的拟定
1)掌握表面加工方法和加工方案的选择,能对简单零件的外圆、内孔和平面等加工表面选择适宜的加工方法和加工方案。
2)掌握加工工艺过程阶段划分及各加工阶段的特点,了解划分加工阶段的目的。
3)掌握工序集中和分散的含义及特点。
4)掌握机械加工工序的安排原则,掌握预备热处理、最终热处理的目的及安排,掌握预备热处理常用的热处理方法(退火、正火、调质、时效)和最终热处理方法(淬火回火、渗碳淬火、氮化)的作用及在工艺过程中的安排。
了解辅助工序包括的内容及安排。
(6)加工余量的确定:
注意加工余量的概念、影响加工余量大小的因素及确定加工余量的方法。
(7)工序尺寸及其公差的确定:
l)注意工艺尺寸链的概念、主要特征和建立,掌握封闭环、组成环、增环、减环的概念和判断,掌握极值法解尺寸链的基本计算公式(封闭环的基本尺寸、封闭环的上、下偏差、封闭环的公差)。
2)掌握工序尺寸及其公差的确定:
工艺基准与设计基准重合时工序尺寸及公差的确定、工艺基准与设计基准不重合时工序尺寸及公差的确定,中间工序的工序尺寸及公差的计算、保证渗氮、渗碳层深度的工序尺寸及公差的计算。
(8)了解机床、工艺装备等的选择。
(9)分析和制订中等复杂零件的工艺过程,填写工艺文件。
13.参考文献
1)黄鹤汀、吴善元主编,机械制造技术,机械工业出版社。
2)孟少农,机械加工工艺手册,北京,机械工业出版社,1991。
3)王树兜等,机械制造工艺学,福建科技出版社出版,1985。
福州。
4)张才芳等,机械制造工艺学,哈尔滨船舶工程学院出版社1990,哈尔滨。
5)9.李华,机械制造技术,机械工业出版社,1996,北京。
第二篇“专业综合课程设计”指导书
一、目的要求
通过设计实践进一步树立正确的设计思想。
在整个设计过程中,坚持实践是检验真理的唯一标准,坚持理论联系实际,坚持与机械制造生产情况相符合,使设计尽可能做到技术先进、经济合理、生产可行、操作方便、安全可靠。
通过本次设计实践,培养学生分析和解决生产技术问题的能力,使学生初步掌握工装(机床夹具、刀具、检验夹具等)的基本方法,并巩固、深化已学得的理论知识,进一步培养学生熟悉和运用有关图册、图表等技术资料的能力,训练学生识图、制图、运算及编制技术文件的基本技能。
二、设计对象
面向机械制造行业,面向中、小型制造厂,生产规模为中、大批生产。
因此,在设计夹具时,应结合制造厂的实际情况,采用较先进的、经济合理的夹具方案。
三、设计步骤及内容
机床夹具设计的一般步骤:
根据工艺规程,由指导教师指定其中一道主要工序的专用夹具设计任务。
⒈夹具结构的设计
根据工艺设计,进行夹具结构方案的选择。
(1)本工序所定的原则和要求
①所设计夹具的工序内容。
②所设计夹具的工序技术要求。
③所设计夹具的工序所用机床和刀具。
④前后工序的关系。
⑤工艺设计所选用的工艺基准。
⑥同时加工的零件数。
(2)夹具设计应满足
①保证零件机械加工精度。
②保证生产率。
③尽力做到结构简单,操作方便,安全可靠,经济合理。
④尽可能采用标准的元件。
(3)绘制结