六边形垫片冲压模具课程设计说明书文档格式.docx
《六边形垫片冲压模具课程设计说明书文档格式.docx》由会员分享,可在线阅读,更多相关《六边形垫片冲压模具课程设计说明书文档格式.docx(21页珍藏版)》请在冰豆网上搜索。
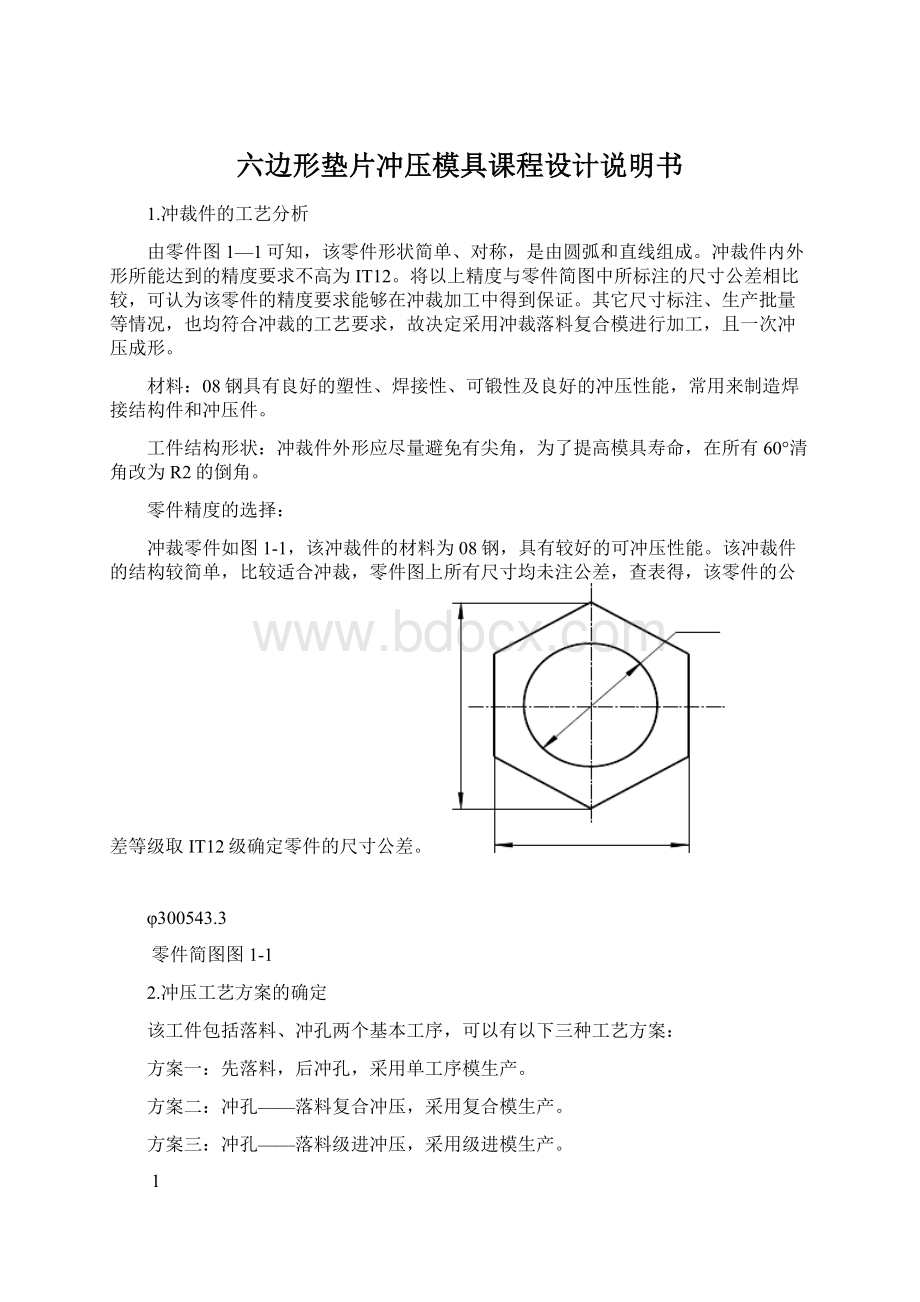
搭边过大,浪费材料、搭边过小,冲裁时容易翘曲或被拉断,不仅会增大冲件毛刺,有时还有拉入凸、凹模间隙中损坏模具刃口,降低模具寿命或影响送料工作。
2
2.02.45.3
排样图图3-1
搭边值通常由经验确定,表所列搭边值为普通冲裁时经验数据之一。
a数值3-1搭边a和表1
50mm矩形工件边50mm
矩形工件边圆件2的工的工2材料厚aa沿工件沿aa1
工件a1
沿工件a1
3.02.52.81.80.252.02.2
2.52.01.51.21.80.25~0.52.2
2.01.21.81.51.81.00.5~0.8
1.81.51.00.8~1.20.81.21.5
2.01.2~1.61.81.01.51.81.2
2.21.6~2.01.82.01.21.52.0
2.52.02.0~2.52.21.81.52.2
2.82.22.5~3.01.82.52.52.2
3.22.22.53.0~3.52.82.52.8
3.52.53.23.5~4.02.82.53.2
4.54.03.53.04.0~5.04.03.5
0.9t
0.8t
0.7t
0.6t
5.0~12
3
根据制件厚度与制件的排样方法可以查表3—1得:
搭边值工件间a1为2.0mm
沿边a为2.2mm
3.2.2条料宽度的确定
计算条料宽度有三种情况需要考虑:
1、有侧压装置时条料的宽度。
2、无侧压装置时条料的宽度。
3、有定距侧刃时条料的宽度。
该零件采用无侧压装置的模具,其条料宽度应考虑在送料过程中因条料的摆动而使侧面搭边减少。
为了补偿面搭边的减少部分,条料宽度应增加一个条料的摆动量。
故条料宽度为:
0]B=[D+2a+c(3-1)△-式中:
B——条料宽度的基本尺寸;
D——条料宽度方向冲裁件的最大尺寸;
a——侧搭边值。
C——条料与导料板之间的间隙(即条料的可能摆动量):
B≤100,
c=0.5~1.0B>100c=1.0~1.5
表3-2剪料公差及条料与导料板之间隙(mm)
条料宽度B/mm~50材料名称普通碳素钢
~1
材料厚度t/mm2~31~2
3~5
牌号
0.4材料状态
0.5抗剪强度
0.7抗拉强度
申长率
0.9屈服强度
50~100100~150150~220220~300
Q195Q235Q27508F
0.50.60.70.8火未退
0.60.70.80.9260—310——400—220
0.80.91.01.1—320320—380380—500500310280—
400—2847021—62015—32390
1.01.11.21.3200332402528019180
导料板之间的距离,应使条料与导料板之间保持一定的间隙查表3—3,以保证送料畅通。
4
表3-3条料宽度偏差(mm)
条料宽度材料厚度
B|mm~0.5>0.5~1>1~2
0.1200.050.08
~0.15>20~300.080.1
0.2
0.1
30~50
0.15
>D取值由设计条料宽度方向冲裁件的最大尺寸为60(mm)
侧搭边值a可以从表3—1中查出为2.2(mm)
故带入条料宽度公式得;
查表3—2可得条料宽度偏差下偏差—△为-0.8(mm)
0D+2a+c]B=[△-=(60+2×
2.2+0.8)-00.6
=65.2-00.4(mm)
3.3材料利用率
材料利用率通常以一个进距内制件的实际面积与所用毛坯面积的百分率η表示;
η=(nA/hB)×
100%(3-2)1式中η——材料利用率(%);
n——冲裁件的数目;
2);
(mm——A1冲裁件的实际面积B——板料宽度(mm);
h——进距;
计算冲压件的面积;
A1=25×
21.65×
6-3.14×
15×
15
2)=2541(mm条料宽度计算:
B=50+2×
2.2
=54.4(mm)
送进距离计算:
5
h=43.3+2
=45.3(mm)
一个进距的材料利用率;
100%1=[1×
2541÷
(45.3×
54.4)]×
100%
=91.3%
由此可之,η值越大,材料的利用率就越高,废料越少。
工艺废料的多少决定于搭边和余量的大小,也决定于排样的形式和冲压方式。
因此,要提高材料利用率,就要合理排样,减少工艺废料。
4.冲裁力相关的计算
4.1计算冲裁力
计算冲裁力的目的是为了选择合适的压力机,设计模具和检验模具的强度,压力机的吨位必须大于所计算的冲裁力,以适宜冲裁的要求,普通平刃冲裁模,其冲裁力Fp一般可以按下式计算:
Fp=KtLτ
式中τ——材料抗剪强度,见附表(MPa)
L——冲裁周边总长(mm)
t——材料厚度(mm)
安全系数K,一般取1.3
可用抗拉强度σb代替τ,Fp=Ltσb
表4—1常用冲压材料的力学性能
优质碳素结200
32
450330360已退火260—08—构钢210
—26010
—340
300440
29
6
20
—400280
510360—
25
250
45
440—560
550—700
16
360
65Mn
600
750
12
400
代替抗σb~360,故取起抗拉强度查(表4—1)可得:
抗剪强度τ=260=360(MPa)。
σb=Kτ剪强度τ,查表可知4.2总冲裁力、推料力、卸料力、顶件力和总冲压力由于冲裁模具采用弹性卸料装置和上出件方式。
F——总冲压力。
Fp——总冲裁力。
——卸料力FQ——推料力。
FQ1——顶件力FQ2Fp=F1+F2计算总冲裁力——落料时的冲裁力。
F1——冲孔时的冲裁力。
F2)冲裁周边的总长(mm6×
落料周长为:
L2=25)=150(mm30×
冲孔周长为:
L1=3.14)(mm=94.2τ落料冲裁力为:
F1=KptL2360×
×
150=1×
2=108000(N)
τ冲孔冲裁力为:
F2=KptL1360×
94.2=1×
2=67824(N)
Fp=F1+F2所以可求总冲裁力为:
=108000+67824
N)=175824(7
表4-2卸料力、推件力和顶件力系数
钢
料厚t/mm
Kx0.065~0.0750.045~0.055
KtKd
≤0.1
0.10.14
>0.1~0.5
0.063
0.08
>0.0550.04~0.050.060.5~0.25
>0.0452.5~6.50.050.03~0.04
>0.025
0.03
0.02~0.03
6.5
按卸料力公式计算卸料力FQ=KxFp
查表4—2得Kx=0.04
根据公式得FQ=KxFp
=0.04×
175824
=7032.96(N)
按推料力公式计算推料力FQ1=nKtFp
取n=2
查表4—2得Kt=0.055
n——梗塞在凹模内的制件或度料数量(n=h/th直刃口部分的高度,t材料厚度)
根据公式得FQ1=nKtFp
=2×
0.055×
=19340.64
按顶件力公式算顶件力FQ2=KdFp
Kd查表4—2得0.06
根据公式得FQ2=KdFp
=0.06×
=10549.44(N)
4.3压力机公称压力的选取
冲裁时,压力机的公称压力必须大于或等于冲裁各工艺力的总和。
采用弹压卸料装置和上出件的模具
8
表4—3常用冷冲压设备的工作原理和特点
类型设备名称材料08、10、35、1.680
8.0
1.200
工作原理16Mn
40、50
特点65Mn
厚度小于0.50.50.6
利用摩擦盘与飞轮之间相互接触传递动力,皆助螺杆与螺母相对运动原理而工摩擦压力作。
机Q23509Mn、2Zmax
2Zmin2Zmin0.0400.0600.0400.0720.0480.048
2Zmax
2Zmin极小间隙0.0400.0600.0480.072
荷时,摩擦盘之间的滑动,不致损坏机件。
2Zmax0.0600.072
结构简单,当超负只会引起飞轮与2Zmin0.0400.048
但飞轮轮缘摩擦损坏适用于大,生产率低。
中小件的冲压加工,
亚印和成形等于校正、
冲压工序尤为适宜。
机械式利用曲柄连杆机构进行工作,电机通过压力机皮带轮及齿轮带动曲轴传动,经连杆使滑块作直线往复运动。
曲柄压力机分为适用于各类曲柄式压生产率高,偏心压力机和曲轴压力机,二者区别主力机冲压加工。
要在主轴,前者主轴是偏心轴,后者主轴是曲轴。
偏心压力机一般是开式压力机,而曲轴压力机有开式和闭式之分。
适用于大工作原理与曲柄压力机相同,但其刚度、生产率很高,高速压力模具一般采精度、行程次数都比较高,一般带有自批量生产,机用多工为级进模。
动送料装置、安全检测装置等辅助装置。
0.0640.70.0640.0920.0640.0920.0640.0920.0720.1040.1040.0640.80.0720.1040.0720.0900.1260.1260.1260.0900.90.0900.0920.1400.1401.00.1400.0900.1000.1000.1001.20.1800.1320.1260.1800.1320.180
0.2400.2400.1701.50.2400.1700.132
0.3201.750.3200.2200.2200.3200.220
0.3802.00.2600.2600.3800.3600.246
0.4000.2800.3800.2800.2602.10.400
0.5400.3800.3800.2602.50.5400.500
0.6000.4202.750.5600.4000.6000.420
0.6600.6600.4800.4600.4800.6403.0
0.7800.7800.5400.7400.5803.50.580
0.9200.6100.6800.9204.00.6800.880
1.0400.7204.50.9601.0000.6800.780
1.3205.51.2801.1000.9800.9400.780
1.5001.4401.2001.1401.0806.00.840
1.3006.50.940
根据公式得F=Fp+FQ+FQ2
=175824+7032.96+10549.44
=193406.4(N)
常用冷冲压设备的工作原理和特点如表4—3
根据综上所计算出来的总压力与常用冷冲压设备的工作原理和特点选取压力机为J23—25。
9
5.模具压力中心的确定
模具压力中心是指冲压时诸冲压力合力的作用点位置。
为了确保压力机和模具正常工作,应使模具的压力中心与压力机滑块的中心相重合,否则,会使冲模和力机滑块产生偏心载荷,使滑块和导轨之间产生过大的摩擦,模具导向零件加速磨损,降低模具和压力机的使用寿命。
冲裁模的压力中心,可按下述原则来确定:
1、对称形状的单个冲裁件,冲模的压力中心就是冲裁件的几何中心。
2、工件形状相同且分布位置对称时,冲模的压力中心与零件的对称中心相重合。
3、形状复杂的零件、多孔冲模、级进模的压力中心可用解析计算法求出冲模的对称中心。
根据制件图可以得出该工件形状相同且分布位置对称,所以冲模的压力中心与零件的对称中心相重合。
5-1制件图纸
6.冲裁间隙
设计模具时一定要选择合理的间隙,以保证冲裁件的断面质量、尺寸精度满足产品的要求,考虑到模具在使用过程中的磨损使间隙增大,故设计与制造新模具时要采用最小合理间隙值Cmin。
10
表6—1冲裁模初始用间隙2c(mm)
2Zmax0.0600.0720.0920.0920.1260.126
注:
取08号钢冲裁皮革、石棉和纸板时,间隙的25%。
根据表6—1查得:
材料08钢的最小双面间隙2Zmin=0.246mm,最大双面间隙2Zmax=0.360mm,为了保证初始间隙值小于最大合理间隙2Cmax,必须满足:
δ=0.6(2Zmax-d2Zmin),δ=0.4(2Zmax-2Zmin);
|δ|+|δ|+2Zmin≤2Zmax。
PdP11
7.凸模与凹模刃口尺寸的计算
7.1刃口尺寸计算的基本原则
1、落料尺寸由凹模尺寸决定,冲孔时孔的尺寸由凸模尺寸决定。
故落料模时,以凹模为基准,间隙取在凸模上;
设计冲孔模时,以凸模为基准,间隙取在凹模上。
2、考虑到凸、凹模的磨损,设计落料模时,凹模基本尺寸应取尺寸公差范围的较小尺寸;
设计冲孔模时,凸模基本尺寸则应取工件孔尺寸公差范围内的较大尺寸、这样,在凸凹模磨损到一定程度的情况下,仍能冲出合格的制件。
凸、凹模间隙则取最小合理间隙值。
3、确定冲裁模的刃口制造公差时,应考虑制件的公差要求。
7.2刃口尺寸计算方法
对该制件应该选用凸模和凹模分别加工的方法,按图纸加工之尺寸。
要分别标注凸模和凹模刃口尺寸和制造公差(凸模δp、凹模δd),它适用于圆形或简单形状的制件。
为了保证初始间隙值小于最大合理间隙2Zmin,必须满足下列条件:
∣δp∣+∣δd∣≤Zmax-Zmin
下面对落料和冲孔两种情况进行讨论。
1、落料:
Dd=(D-X△)0+δd
Dp=(Dd-2Zmin)0-δp=(D-X△-2Zmin)0-δp
2、冲孔:
dp=(d+x△)0-δp
dd=(dp+2Zmin)0+δd=(d+x△+2Zmin)0+δd
Ld=(Lmin+0.5△)±
0.125△
式中Dd——落料凹模基本尺寸(mm);
Dp——落料凸模基本尺寸(mm);
D——落料件最大极限尺寸(mm);
dd——冲孔凹模基本尺寸(mm);
dp——冲孔凸模基本尺寸(mm);
12
d——冲孔件孔的最小极限尺寸(mm);
Ld——同一工步中凹模孔距基本尺寸(mm);
Lmin——制件孔距最小极限尺寸(mm);
△——制件公差(mm)可查表7—1;
2Zmin——凸、凹模最小初始双面间隙(mm);
δd——凸模下偏差,可按IT6选用(mm);
δp——凹模上偏差,可按IT7选用(mm);
X——磨损系数,可查表7—2
表7-2磨损系数x
t(mm)
料厚
1
非圆形0.75
0.750.5
圆形0.5
工件公差△
/mm
121~
≥0.16<0.350.16<≥0.360.160.17~<0.21~0.41≥0.420.200.20≥<0.20
2~4>4
<<
0.240.30
0.490.25~0.31~0.59
≥≥
0.500.60
<0.24<0.30
7.3刃口尺寸计算
根据计算原则,落料时以凹模为设计基准。
首先确定凹模尺寸,使凹模基本尺寸接近或等于制件的轮廓的最小极限尺寸,再减小凸模尺寸以保证最小合理间隙值2Zmin。
=(50-0.75×
0.30)0+0.025
=49.775+0.025
Dp=(Dd-2Zmin)0-δp
=(49.775-0.246)0-0.016
=49.529-0.016
校核∣δp∣+∣δd∣≤Zmax-Zmin
0.016+0.025≤0.360-0.246
0.041≤0.114
(满足间隙要求)
13
根据计算原则,冲孔时以凸模设计为基准,首先确定凸模刃口尺寸,使凸模基本尺寸接近或等于工件孔的最大极限尺寸,再增大凹模尺寸以保证最小合理间隙2Zmin。
=(30+0.75×
0.21)0-0.013
=30.1575-0.013
dd=(dp+2Zmin)0+δd
=(30.1575+0.246)0+0.021
=30.4035+0.021
0.013+0.021≤0.360-0.246
0.034≤0.114
=(40+0.5×
0.39)±
0.125×
0.39
=40.195±
0.049
8.模具总体设计
8.1模具类型的选择
由冲压工艺分析可知,采用复合冲压,所以模具类型为复合模。
8.2定位方式的选择
毛坯在模具中应该有正确的位置,正确位置是依靠定位零件来保证的。
定位包括控制送料进距的挡料和送料定距的挡料。
8.2.1送进导料方式的选择
选择复合模设计中导料销导向,在模具中设计两个导料销,并位于条料的两侧,该模具是从右向左送料,所以导料销装在前后各一侧。
形式为固定导料销。
如图8—1所示。
14
固定导料销图8-1
送料定距方式的选用8.2.2
8-2限位销用来限制条料送进的距离,根据国家标准选用活动挡料销如图所示,其结构简单、制造容易,用途广泛。
活动挡料销图8-2
卸料、出件方式的选择8.3
常用的卸料方式有刚性卸料和弹性卸料两种。
,相对较薄,卸料力也比较小,故可采用弹性卸料。
2mm因为工件料厚为标准模架导向方式的选择8.4
对角导柱导柱模架的基本型式有四种:
按导柱在模架上的固定位置不同,模架;
后侧导柱模架;
中间导柱模架;
四导柱模架。
为了提高模具寿命和工件质量,方便安装调整,该复合模采用后侧导柱的导向方式。
主要零部件的设计9.凸凹固定板、适宜采用线切割加工凸模固定板、结合模具的特点,卸料板、凹模及冲孔凸模、凸凹模。
除凸凹模外,在采用线切割后,还得采用数控车床使装配加工其形腔锥度。
这种加工方法可以保证这些零件各个内孔的同轴度,工作简化。
9.1工作零件的结构设计
9.1.1凸凹模的设计
因为该制件形状复杂,所以将落料凸模与冲孔凹模设计成一个整体为凸凹模。
直通式凸模工作部分和固定部分的形状做成一样,直通式凸模采用线切割机床加工。
凹模和工作部分与凸模联在一起,为保证废料直接由凸模从凸凹模内孔推出。
凹模洞口若采用直刃、则模内有积荐废料,胀力较大。
通过固定板把凸凹模固定。
固定板与凸凹模的配合按H7/m6。
凸凹模材料应选T10A,热处理58~60HRC,凸凹模与卸料板之间的间隙见表9—1查得凸凹模与卸料板的间隙选为0.035mm。
凸凹模高度是固定板、卸料板和弹簧间隙组成。
凸凹模高度为:
H=H1+H2+(15~20)mm
H1——固定板厚度;
得H1=0.8×
H=0.8×
16=12.8mm(标准为15mm)凹H2——卸料板厚度;
查表9—4得H2=10mm
(15~20)——附加长度,包括凸凹模的修磨量,凸模进入凹模的深度及固定板与卸料板间的安全距离。
(附加长度取18)
H=15+10+18
=43mm
表9-1凸凹模与卸料板、导柱与导套的间隙
序号>
100~200