设计说明书同心垫圈级进模设计冲压课设类Word下载.docx
《设计说明书同心垫圈级进模设计冲压课设类Word下载.docx》由会员分享,可在线阅读,更多相关《设计说明书同心垫圈级进模设计冲压课设类Word下载.docx(25页珍藏版)》请在冰豆网上搜索。
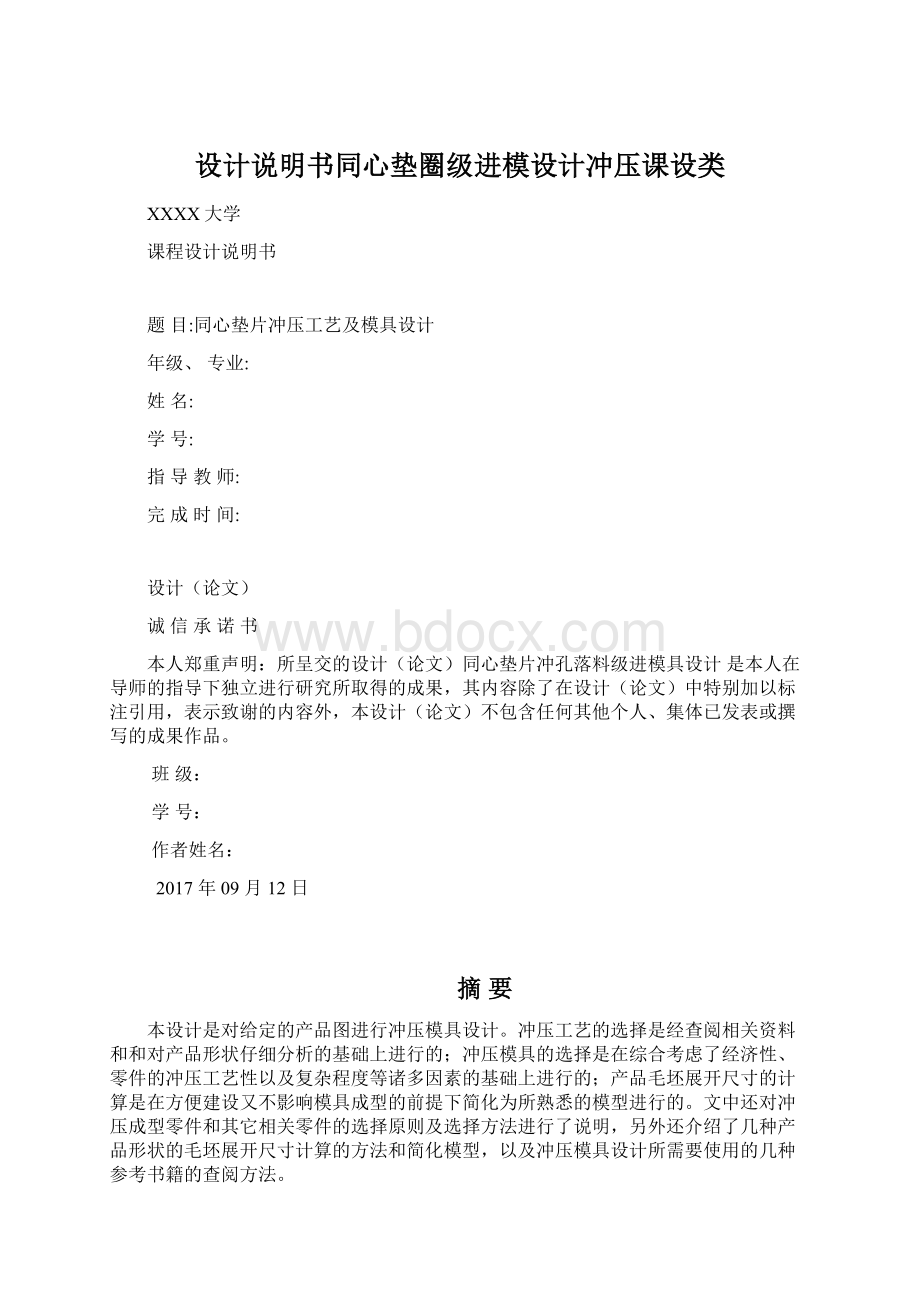
第六章、压力机的校核23
6.1.压力机的校核23
第七章、模具的动作原理及综合分析24
7.1.模具的动作原理24
7.2.模具的装配24
设计心得26
致谢27
主要参考文献28
前言
随着经济的发展,冲压技术应用范围越来越广泛,在国民经济各部门中,几乎都有冲压加工生产,它不仅与整个机械行业密切相关,而且与人们的生活紧密相连。
冲压工艺与冲压设备正在不断地发展,特别是精密冲压。
高速冲压、多工位自动冲压以及液压成形、超塑性冲压等各种冲压工艺的迅速发展,把冲压的技术水平提高到了一个新高度。
新型模具材料的采用和钢结合金、硬质合金模具的推广,模具各种表面处理技术的发展,冲压设备和模具结构的改善及精度的提高,显著地延长了模具的寿命和扩大了冲压加工的工艺范围。
由于冲压工艺具有生产效率高、质量稳定、成本低以及可加工复杂形状工件等一系列优点,在机械、汽车、轻工、国防、电机电器、家用电器,以及日常生活用品等行业应用非常广泛,占有十分重要的地位。
随着工业产品的不断发展和生产技术水平的不断提高,冲压模具作为个部门的重要基础工艺装备将起到越来越大的作用。
可以说,模具技术水平已成为衡量一个国家制造业水平的重要指标。
冲压工艺是塑性加工的基本加工方法之一。
它主要用于加工板料零件,所以有时也叫板料冲压。
冲压不仅可以加工金属板料,而且也可以加工非金属板料。
冲压加工时,板料在模具的作用下,于其内部产生使之变形的内力。
当内力的作用达到一定程度时,板料毛坯或毛坯的某个部位便会产生与内力的作用性质相对应的变形,从而获得一定的形状、尺寸和性能的零件。
冲压生产靠模具与设备完成加工过程,所以它的生产率高,而且由于操作简便,也便于实现机械化和自动化。
利用模具加工,可以获得其它加工方法所不能或难以制造的、形状复杂的零件。
冲压产品的尺寸精度是由模具保证的,所以质量稳定,一般不需要再经过机械加工便可以使用。
冲压加工一般不需要加热毛坯,也不像切削加工那样大量的切削材料,所以它不但节能,而且节约材料。
冲压产品的表面质量较好,使用的原材料是冶金工厂大量生产的轧制板料或带料,在冲压过程中材料表面不受破坏。
因此,冲压工艺是一种产品质量好而且成本低的加工工艺。
用它生产的产品一般还具有重量轻且刚性好的特点。
冲压加工在汽车、拖拉机、电机、电器、仪器、仪表、各种民用轻工产品以及航空、航天和兵工等的生产方面占据十分重要的地位。
现代各种先进工业化国家的冲压生产都是十分发达的。
在我国的现代化建设进程中,冲压生产占有重要的地位。
当今,随着科学技术的发展,冲压工艺技术也在不断革新和发展,这些革新和发展主要表现在以下几个方面:
(1)工艺分析计算方法的现代化
(2)模具设计及制造技术的现代化
(3)冲压生产的机械化和自动化
(4)新的成型工艺以及技术的出现
(5)不断改进板料的性能,以提高其成型能力和使用效果。
本次设计的目的:
一、综合运用本专业所学的理论与生产实际知识,进行一次冲压模设计的实际训练,从而提高我们独立工作能力。
二、巩固复习三年以来所学的各门学科的知识,以致能融贯通,进一步了解从模具设计到模具制造整个工艺流程。
三、掌握模具设计的基本技能,如计算、绘图、查阅设计资料和手册,熟悉标准和规范等。
由于本人设计水平有限,经验不足,错误难免,敬请老师批评、指导,不胜感激。
第一章、零件图及工艺方案的拟订
1.1.零件图及零件工艺性分析
1.1.1.零件图
图(1—1)
工件图:
如图1—1所示
材料:
10#
板厚:
1.5mm
产品外形是圆形,所以模具加工方便,且不容易开裂。
1.1.2.零件的工艺性分析
产品所用的材料为10#钢,其力学性能如下:
τ=260-340Mpa,σb=300-440Mpa,(《冷冲压工艺与模具设计》P322),零件图上未注公差等级,属自由尺寸,按IT08级确定工件尺寸的公差.该制件形状简单,尺寸较小,厚度一般,属于普通冲压件,但有几点应该注意:
①该冲裁件的材料10#,具有较好的可冲压性能。
②由于板料厚度一般,
③有一定的生产批量,应重视模具材料的选择和模具结构的确定,保证模具的寿命。
④制件较小,从安全考虑,要采取适当的取件方式,模具结构上设计好推件和取件方式。
1.2.工艺方案的确定
对工序的安排,拟有以下几种方案:
①落料—冲孔,单工序模生产。
②落料—冲孔复合冲压。
③冲孔—落料连续冲压,采用级进模生产。
方案①模具结构简单,容易制造。
但成形制件需要两道工序、两套模具才能完成零件的加工,工序分散,搬运半成品要浪费大量时间。
生产效率较低;
工件的精度也难以保证。
方案②复合模结构一般,比较容易制造。
节约了半成品搬运的时间提高了生产效率且易于保证孔的质量和制件精度。
但齿比较多,而且,距离比较近,采用复合模,凸凹模的强度不够,容易裂开,模具寿命不长
方案③级进模结构复杂;
难以制造。
有较高的生产效率且能保证制件的精度。
模具寿命长。
综上所述,根据生产效率、精度、所使用的机床、卸料方式、废料出料、板料的定位方式、制造成本等方面分析最终确定方案三。
第二章、工艺设计
2.1.确定排样方案
外形最大尺寸为长度Dmax=25,材料厚度为1.5,根据材料性能,由《冲压工艺与模具设计》P45表2.5.2确定搭边值:
工件间:
a1=1.0;
沿边:
a=1.2,
条料下料宽度为25+2×
1.2+2×
1.2=29.8,剪切公差:
δ=0.2
条料与导料板之间的间隙:
c=0.5
送料步距为25+1=26;
一.计算工件实际面积
工件实际面积为3.14×
12.5×
12.5=490.625,
材料利用率的计算:
一个步距内的材料利用率η为
η=nF/Bs×
100%
η=1×
490.625/26×
29.8×
100%=63.32%
式中F——一个步距内冲裁件面积(包括冲出的小孔在内);
n——一个步距内冲裁件数目;
1
B——条料宽度(mm);
29.8mm
s——步距(mm);
26mm
二.分析排样方案
为保证条料送进的刚性和稳定性以及正确处理工件送料与载体的连接关系,应考虑沿零件纵向排样和横向排样,由于本设计中产品外形是比较规则,纵向和横向,无论是操作,还是在材料利用率上是完全一样的,所以无需考虑如何排样。
具体排样图如下:
图2—2)
2.2.计算各工序的压力
已知工件的材料为材料是10#,厚度为1.5mm,抗剪切强度τ=340Mpa,抗拉强度σb=440Mpa,
冲侧刃力:
F1=1.3nLtτ
=1.3×
2×
(2.4+26)×
1.5×
340
=37658.4(N)
=37.66KN
冲中间孔力:
F2=1.3πDtτ
3.14×
12×
=24981.84(N)
=24.98KN
落料力:
F4=1.3πDtτ
25×
=52045.5(N)
=52.05KN
卸料力:
P2=k卸F(查《冷冲压工艺与模具设计》得:
k卸=(0.025~0.08)
冲压力大小为F=F1+F2+F3+F4
=37.66+24.98+52.06=114.69
P2=k卸F=114.69×
0.06
=6.88KN
这一工序的最大总压力为:
P=F+P2=114.69+6.88
=121.57KN
2.3.压力机的选择
根据以上计算和分析,再结合车间设备的实际情况,选用公称压力为160KN的单柱固定台压力机(型号为JH23—16)能满足使用要求。
压力机的具体参数如下
公称压力:
160KN
滑块行程:
50mm
滑块行程次数:
150次/min
最大封闭高度:
250mm
最大装模高度:
180mm
封闭高度调节量:
45mm
模柄孔尺寸:
直径40mm,深度60mm
工作台面尺寸:
300mm(前后)×
450mm(左右)
垫板厚度:
40mm
2.4.压力中心的计算
模具压力中心是指冲压时诸冲压力合力的作用点位置。
为了确保压力机和模具正常工作。
采用解析法求压力中心,
首先,:
F1——冲侧刃力F1=KLδτ,得F1=18.83KN
F2——冲侧刃力F2=KLδτ,得F2=18.83KN
F3——冲中间孔力F3=KLδτ,得F3=24.98KN
F4——落料力P4=KLδτ得F4=52.05KN
Y1——F1到X轴的力臂Y1=13.7
X1——F1到Y轴的力臂X1=13
Y2——F2到X轴的力臂Y2=-13.7
X2——F2到Y轴的力臂X2=13
Y3——F3到X轴的力臂Y3=0
X3——F3到Y轴的力臂X3=0
Y4——F4到X轴的力臂Y4=0
X4——F4到Y轴的力臂X4=-26
根据合力距定理:
YG=(Y1F1+Y2F2…)/(F1+F2…)
XG=(X1F1+X2F2…)/(F1+F2…)
YG——F冲压力到X轴的力臂;
YG=0
XG——F冲压力到Y轴的力臂;
XG=-7.53
所以该模具压力中心为(-7.53,0)
第三章、模具类型及结构形式的选择
根据确定的工艺方案和零件的形状特点,精度要求,预选设备的主要技术参数,模具的制造条件及安全生产等,选定模具类型及结构形式。
3.1.级进模的设计
本设计中采用冲孔落料级进模。
工件厚度一般(t=1.5mm),故采用弹性卸料装置,弹性卸料装置除了卸料的作用外,在冲孔时还起到压紧工件的作用。
上模弹性力由橡皮产生。
级进模的结构形式如图3—1所示。
图3—1)
第四章、模具工作零件刃口尺寸及公差的计算
4.1.冲孔、落料模
落料,冲孔尺寸刃口设计和计算
该冲裁件外形尺寸为落料件,选凹模为设计基准件,只需计算落料凹模刃口尺寸由凹模的实际尺寸按间隙要求配做。
工件精度要求为IT12级查《冲压工艺与模具设计》P31附表2.2.1:
冲模制造精度为IT9~IT11级,取IT10级。
冲孔凸模和落料凹模尺寸按下列公式计算:
冲孔时凸模Aj=(Amin+XΔ)+Δ/4
冲孔时凹模Bh=(Bj+Z)-Δ/4
落料时凹模Aj=(Amax-XΔ)-Δ/4
落料时凸模Ah=(Aj-Z)+Δ/4
孔心距Lp=L±
δp’
式中AhAj——分别为落料和冲孔凸模的刃口尺寸(mm);
Amax——为落料件的最大极限尺寸(mm);
Amin——为冲孔件的最小极限尺寸(mm);
Δ——工件公差;
Δp——凸模制造公差,通常取δp=Δ/4;
δp’——刃口中心距对称偏差,通常取δp’=Δ/8;
Lp——凸模中心距尺寸(mm);
L——冲件中心距基本尺寸(mm);
Zmin——最小冲裁间隙(mm);
本次课题查表得Zmin=0.16
落料凹模尺寸:
Aj=(Amax-XΔ)-Δ/4
=25.2-0.5×
0.4=25-0.02;
落料凸模尺寸:
Ah=(Aj-Z)+Δ/4
=25-0.16=24.84+0.02;
冲孔凸模尺寸:
Aj=(Amin+XΔ)+Δ/4
=11.9+0.5×
0.2=12+0.02
=25.8+0.5×
0.4=26+0.02
=2.3+0.5×
0.2=2.4+0.02
冲孔凹模尺寸:
Bh=(Bj+Z)-Δ/4
=12+0.16=12.16-0.02,
=26+0.16=26.16-0.02
=2.4+0.16=2.56-0.02
Lp1=26±
0.01,节距保持不变
Lp2=29.8±
0.01,
Lp3=13±
第五章、模具零件的选用,设计及必要的计算
5.1.模具零件的选用
一、凸模
凸模材料选用Cr12MoV,淬火硬度达到58-62HRC。
采用台阶式凸模(如图5-1所示),圆形凸模采用台阶式固定,异形凸模与固定板采用过盈配合的方式,
图5-1)
二、凹模
凹模材料选用Cr12MoV,淬火硬度达到58-62HRC。
凹模采用螺钉固定结构,与上模板配合,这样简化了模具的结构,节省了材料的成本。
外形尺寸
凸模采用台阶固定结构,与固定板配合,外形直接线割加工。
螺钉孔固定在上模板上。
②支撑固定零件
上、下模座中间联以导向装置的总体称为模架。
通常都是根据凹模最大外形尺寸,模具闭合高度,选用标准模架。
凹模最大外形尺寸L=170mm,B=140mm,选用17#后侧导柱标准模架。
模具的闭合高度h=139~160mm,
上下模座选用材料为HT200,下模板厚度35,上模板厚度30。
再由凹模板和模架尺寸确定其它模具模板的尺寸如下:
上垫板:
170×
140×
8
凸模固定板:
18
凹模:
30
上模板:
250×
205×
下模板:
35
③卸料零件
采用弹性卸料板卸料,根据卸料力的大小取卸料板的厚度为18mm。
由于卸料板与导料板在安装时有干涉,因此,在设计卸料板时需加工让位,这样,卸料板需要加厚到23,由《冲压手册》表10-1选用树脂,设使用树脂的个数为8个,F=6880N则每个树脂所承受的负荷为F顶=6880/6=860(N),由Fj>
F顶,选择树脂直径规格为:
φ25,Fj=1390,hj=23,h顶=hj/FjxF顶=23/1390x860=14.23
∴h顶+h工+h修模=14.23+1.5+3=18.73<
hj
∴选用的树脂及数量满足要求
上、下模座螺钉选取
由凹模周界170×
140选用M10的内六角圆柱头螺钉
参照模具各零件的具体情况,
上模座选用4颗M10X50的内六角圆柱头螺钉固定。
下模座选用4颗M8X50的内六角圆柱头螺钉固定。
(螺钉)
卸料螺钉
查《冲压模具简明设计手册》表15-34选取卸料螺钉
选用M8X50的圆柱头内六角卸料螺钉
(卸料螺钉)
其主要参数:
d1=16l=14d2=24H=10
t=8s=10d3=14.5d4=6.9
d5=9.5L=50
根据模具的实际情况
上模座选用两颗Φ10×
50的圆柱销钉定位
下模座选用四颗Φ8×
(圆柱销钉)
参照模具各零件的具体情况,合理布置螺钉、圆柱销的位置,从GB70—76和GB119—76中选适当的规格与尺寸。
⑤导向装置
本模具采用圆形导柱、导套式的导向装置。
导柱与导套之间采用间隙配合,配合精度为H7/R6。
导柱与导套相对滑动,要求配合表面有足够的强度,又要有足够的韧性。
所以材料选用20钢,表面经渗碳淬火处理,表面硬度为58~62HRC。
导柱选用GB2861.2—81中的B型导柱,直径d=25mm、极限偏差为R7、长度L=140mm。
导套选用GB2861.6—81中的A型导套,直径d=25mm、D=38mm、极限偏差为H7、长度L=80mm。
确定其他零件的尺寸参数
由《模具设计指导》表5-4,可得典型组合尺寸170×
140(单位为mm)。
而由此典型组合标准,即可方便的确定其他冲模零件的数量、尺寸及主要参数。
其零件参数如下表所示:
凹模周界
凸凹模长度
配用模架闭合高度H
孔距尺寸
最小
最大
S
S1
S2
S3
55
139
160
零件名称及标准编号
垫板
凸模固定板
凹模
卸料板
23
螺钉
圆柱销
树脂
M10×
60
φ10×
50
M8×
5.2.选择标准模架
由凹模周界尺寸及模架闭合高度在139~160mm之间,查《模具设计指导》表5-7选用标准模架:
17号后侧导柱标准模架250×
139—160ⅠGB/T2851.1—1990,上模座250×
30,下模座250×
35,导柱25×
140,导套38×
80×
60。
5.3.卸料、压边弹性元件的确定
冲压工艺中常用的弹性元件有弹簧和橡胶,但是由于这副模具所需的卸料力较大,如果选用弹簧,即使使用8个弹簧,每个弹簧所承担的负荷也将达到F预=F卸/n=6880/8N=860N。
同时由于这是一落料模,模具的行程较大,也给弹簧的选用带来困难。
即使试用了弹簧,也势必造成为了安装弹簧而选用较大的模架。
因此我们选用橡胶作为卸料的弹性元件。
1、确定卸料橡胶
(1)确定橡胶的自由高度H自,由《模具设计指导》表3-9得:
H自=L工/0.25~0.30+h修模
L工——冲模的的工作行程(mm).对冲裁模而言,L工=t+1
h修模——预留的修模量
式中,L工为模具的工作行程再加1~3mm。
本模具的工作行程为材料的厚度加1.0mm。
故L工=2.5mm,h修模的取值范围为2~6mm,在这取中间值3mm。
H自=(2.5/0.25+3)mm=13mm
(2)确定L预和H装。
由表3-9可得如下计算公式:
L预——橡胶的预压缩量
H装——冲模装配好以后橡胶的高度
L预=(0.1~0.15)H自=0.1×
13mm=1.3mm
H装=H自-L预=(13-1.3)mm=11.7mm
(3)确定橡胶横截面积A(mm²
)
A=F/q
F——所需的弹压力
q——橡胶在与压缩状态下的单位压力
F由前可知为F=6880N,q=0.26~0.50Mpa。
在这里由于根据模具的行程,取q=0.5Mpa
则A=6880/0.5mm²
=13760mm²
第六章、压力机的校核
6.1.压力机的校核
1、闭合高度的校核
所选压力机的最大装模高度为180mm,闭合高度的调节量为45mm
Hmin=180-45=135mm
本次设计模具的的闭合高度
H=H上模座+H垫板+H凸模+H凹模+H固定板+H下模座-1
=30+8+55+30+35-1
=157
Hmax-5=175Hmin+5=140
Hmax-5>H>Hmin+5,所以满足设计要求。
2、工作台面尺寸的校核
所选压力机的工作台尺寸为:
左右:
450前后:
300
而模具的外形尺寸为:
205
根据工作台面尺寸一般应大于模具底座50~70mm,
∴工作台面尺寸满足。
3、滑块行程的校核
滑块行程应保证方便地放入毛坯和取出零件,
所选压力机滑块行程为50mm,满足。
综上,所选压力机JH23-16满足需要。
第七章、模具的动作原理及综合分析
7.1.模具的动作原理
本模具(装配图如图所示)在一次行程过程中完成制件的落料、冲孔全部工作:
当压力滑块下行时,毛坯料被压在凹模与各冲孔,落料凸模与凹模之间作用下一次完成工作。
本次设计的级进模,在压力机的一次行程中,经一次送料定位,在模具的同一部位同时完成多道工序,其冲裁件的相互位置精度高,对条料的定位精度也比较高,因为需要用导料板对条料宽度进行导向。
冲压件精度高,可以很好的保证工件的形状和尺寸精度,模具结构较一般,制造精度要求比较高,制造周期短,价格相对较低,节约了成本。
工序较集中排除了半成品搬运时间,提高了生产效率。
这种模具适用于生产批量大,精度要求高,内外形尺寸差较大的冲裁件。
冲孔废料由凹模孔向下排除,同时错位落料的产品也由凹模孔向下排除,这样操作方便,生产效率提高很多。
每步送料步距靠侧刃定位,有导正销定位。
所选的模架螺钉等零件都是从标准件中选取,这样可有效的降低成本。
7.2.模具的装配
根椐级进模装配要点,选凹模作为装配基准件,先装下模,再装上模,并调整间隙、试冲、返修。
序号
工序
工艺说明
1
凸、凹模预配
1装配前仔细检查各凸模尺寸以及凹模形孔,是否符合图纸要求尺寸精度、形状。
2将各凸模分别与相应的凹模孔相配,检查其间隙是否加工均匀。
不合适者应重新修磨或更换
2
凸模装配
以凹模孔定位,将各凸模分别压入凸模固定板的形孔中,并挤紧牢固
3
装配下模
1在下模座上划中心线,按中心预装凹模、固定板;
2在下模座上,用已加工好的凹模板分别确定其螺孔位置,并分别钻孔,攻丝;
4
装配上模
1在已装好的下模上放等高垫铁,再在凹模中放入0.3mm的纸片,然后将凸模与固定板组合装入凹模;
2预装上模座,划出与凸模固定板相应螺孔、销孔位置并钻铰螺孔、销孔;
3用螺钉将固定板组合、垫板、上模座连接在一起,但不要拧紧;
4将卸料板装在已装入固定板的凸模上,装上橡胶和卸料螺钉,并调节橡胶的预压量,使卸料板高出凸模下端约1mm;
5复查凸、凹模间隙并调整合适后,紧固螺钉;
6安装导料板;
7切纸检查,合适后打入销钉
5
试冲与调整
装机试冲根椐试冲结果作相应调整
设计心得
通过本次课程设计,在理论知识的指导下,结合认识实习和生产实习中所获得的实践经验,在老师和同学的帮助下,认真独立地完成了本次设计。
在本次设计的过程中,通过自己实际的操作计算,我对以前所学过的专业知识有了更进一步、更深刻的认识,能够把自己所学