毕业设计塑料雨伞手柄注射成型设计Word文件下载.docx
《毕业设计塑料雨伞手柄注射成型设计Word文件下载.docx》由会员分享,可在线阅读,更多相关《毕业设计塑料雨伞手柄注射成型设计Word文件下载.docx(27页珍藏版)》请在冰豆网上搜索。
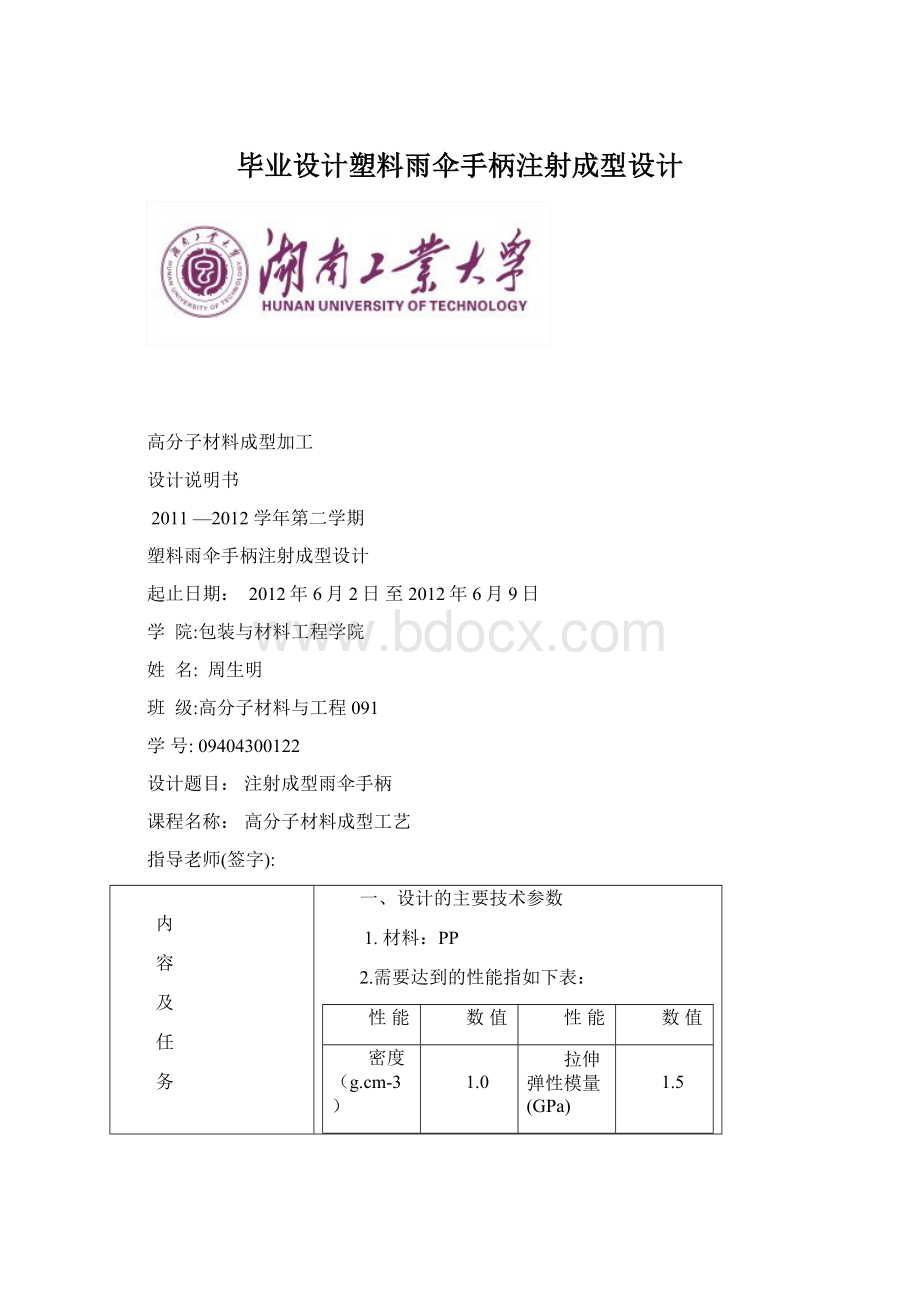
(缺口)冲击韧度(J/m2)
100
3.成型方法:
注射成型
2、设计任务
1、明确设计任务,收集有关资料:
(1)了解设计的任务、内容、要求和步骤,制定设计工作进度计划
(2)查阅、收集有关的设计参考资料
(3)了解设计零件的用途、结构、性能
(4)查阅有关的设备资料
2、根据制品的使用目的和用途,确定制品功能特点、载荷条件、环境条件、成本限制、适用标准等,制定生产批量,根据生产批量分析产品成本,阐明采用注射生产可取得的经济效益。
3、根据目标人群的身体特点,设计产品尺寸、形状。
用AutoCAD做出示意图及效果图,注意尺寸标注方法。
4、选材及配方设计:
自选材料,通过配方使材料在韧性、缺口冲击强度、断裂伸长率、制品表面质量及收缩率等方面均符合要求。
同时确保体系的流动性。
5、根据设计的材料配方,选择合适的设备并制定合理的工艺。
(1)注射量计算:
估算塑料的用量,及保证足够的塑料用量为原则。
初步选择注射机的规格型号,
(2)浇注系统设计计算:
包括浇道布置、主流道和分流道断面尺寸计算、浇注系统压力降计算和型腔压力校核。
(3)成型零件工作尺寸计算:
主要有凹模和型芯径向尺寸、高度尺寸。
为计算方便,凡孔类尺寸均用其最小尺寸作为公称尺寸,凡轴类尺寸均用最大尺寸作为公称尺寸;
进行工作尺寸计算时应考虑塑料的收缩率和模具寿命等因素。
(4)模具冷却与加热系统计算:
冷却系统计算包括冷却时间和冷却参数计算。
冷却参数包括冷却面积、冷却水孔长度和孔数的计算及冷却水流动状态的校核和冷却水入口与出口处温差的校核。
模具加热工艺计算主要是加热功率计算。
(5)注射压力、锁模力和安装尺寸校核:
模具初步设计完成后,还需校核所选择的注射机注射压力和锁模力能否满足塑料成型要求,校核模具外形尺寸可否方便安装,行程是否满足模塑成型及取件要求。
6、确定所选注射机型号、工艺参数、型腔的尺寸与形状。
画出型腔的示意图及模具结构简图。
说明模具工作过程,特别注意脱模和顶出过程的实现。
三、设计工作量
按教学计划规定,课程设计总学时数为1周。
进
度
安
排
起止日期
工作内容
6.2—6.3
初步查询资料,确定制品性能要求
6.4—6.5
确定制品基本参数,绘制产品示意图与效果图
6.6
设计配方,确定注射成型工艺
6.7
查询相关书籍,确定各种成型参数
6.8—6.9
用CAD绘制型腔的示意图及模具结构简图;
复查整个设计过程,作出相应修改
主
要
参
考
资
料
[1]申开智.塑料成型模具[M].北京:
中国轻工业出版社,2006.
[2]陈志刚.塑料模具设计[M].北京:
机械工业出版社,2002.
[3]吉卫喜主编.机械制造技术[M].北京:
机械工业出版社,2001.
[4]王伯平主编.互换性与测量技术基础[M].北京:
机械工业出版社,
2004.
[5]丁闻.实用塑料成型模具设计手册—注射模、压缩模和压注模[M].西
安:
西安交通大学出版壮出版,1993.
[6]张可惠.塑料材料学[M].西安:
西北工业大学出版社,2009.
[7]郭晓俊.Pro/ENGINEERWildfire3.0中文版模具设计基本技术与案例
实践M].北京:
清华大学出版社,2007.
[8]王孝培.塑料成型工艺及模具简明手册[M].北京:
2000.
[9]邱会朋.Pro/ENGINEERWildfire3.0中文版注塑零件和注塑模具:
设
计分析•工程图[M].北京:
电子工业出版社,2007.
[10]黄鹤汀.机械制造装备[M].北京:
机械工业出版社,2001.
[11]李德群,唐志玉.塑料与橡胶模具设计[M].北京:
电子工业出版社,
2007.
[12]钱志峰,刘苏.工程图学基础教程[M].北京:
科学出版社,2003.
[13]王旭,王积森.机械设计课程设计[M].北京:
机械工业出版社,2003.
指导教师(签字):
年月日
系(教研室)主任(签字):
第一章:
制品分析与选材配方
1.1制品设计分析
注射成型制品为一般雨伞的手柄塑料件,位于雨伞末端,主要起方便握伞的作用。
适用地区为:
下雨程度中等及以下的华北、华中等地区;
伞的使用寿命为二至三年;
并要考虑部分适用者可能将伞当做遮阳伞适用;
伞柄的外观美观且手感舒适。
华北、华中等地区降雨量中等,基本无台风、特大暴雨,因此对伞柄的力学性能要求不是很高:
有适度的强度、韧性、硬度即可。
该地区的温度波动范围为10℃到40℃,湿度10到30,且雨伞的使用环境多为户外、雨天,因此伞柄材料应有较好的耐候性能、良好的防水性、并在波动温度范围内保持力学性能的特点。
此外,考虑到某些使用者将伞用作遮阳,伞柄还需有中等的防老化性能,以免降低伞的使用寿命。
对伞柄有一定的外观要求,需要其手感舒适、易于装饰。
1.2选材及配方
1.2.1制品性能要求
表1--1制品性能指标
从伞柄的使用性能指数来看,综合力学性能要求中等可考虑选用常用易得且经济适用的材料。
1.2.2各种材料比较及选择
PVC树脂:
最突出的缺点是热稳性差,低温变脆,对光和机械作用比较敏感。
其在热、光、机械作用下,容易分解脱出氯化氢,对设备有腐蚀作用,此外,PVC的熔体黏度高,使加工困难且难以控制温度。
其突出特点是综合力学性能较好,价格便宜,使用广泛。
PE树脂:
常用的有一般PE、HDPE等类型,总的说其力学强度不高。
其突出的缺点是结晶度高,收缩率大,不利于加工成型精确高的制品,且影响制品性能,容易应力开裂。
其突出的优点是耐腐蚀性好。
PP树脂:
常用的有PP、BOPP等类型。
相比PE树脂,PP的结晶度大大降低,有优异的抗弯曲疲劳性,加工性能良好,耐高温蒸煮,良好的耐化学性。
突出的缺点是:
易氧化降解,常需添加抗氧剂以增强其耐热氧老化性能。
ABS树脂:
使用广泛的工程塑料,有很好的综合力学性能,加工性能十分优异,且可电镀、易得到表面美观的产品。
但含有部分碳碳双键,耐候性较差,从而影响力学性能。
因为是工程塑料,相对以上塑料价格贵些。
以上树脂,可通过添加适量的助剂来改善性能。
在市场中,常见的伞柄树脂材料有PP、ABS、EVA等。
考虑到树脂本身的成本和制品的性能要求,同时考虑到添加助剂对原料成本和加工成型成本的影响,选择PP为本次设计的树脂原材料。
PP树脂的性能基本可满足制品性能要求,只需在耐热氧老化性能、收缩率等性能方面改进则可达到制品性能要求。
1.2.3聚丙烯(PP)性能指标
表1--2PP材料性能
0.90~0.91
1.1~1.6
0.03~0.04
200
19
95~105
抗拉强度(MPa)
35~40
1.0~3.0
42~56
10~100
比较表1、表2,聚丙烯的力学性能基本达标,但存在以下缺陷:
收缩率过大、韧性不够,此外抗热氧老化性能差。
可通过配方设计加以改善。
1.2.4配方设计
表1--3制品配方
序号
物料名称
用量
功能
特点
1
树脂基材
综合力学性能基本满足制品要求,收缩率和韧性还不达标,抗热氧老化性能差;
2
碳酸钙
(轻质)
40
填料(增强)
增强改性PP,适宜范围为树脂含量的10%-50%,可起提高硬度、刚度、弹性模量,降低收缩率;
此外,可大大降低成本;
3
硬脂酸
0.3
偶联剂
提高碳酸钙与PP的结合能,使相容性改善,有利于力学性能;
4
汽油
溶剂(表面处理用)
用硬脂酸对碳酸钙进行表面处理时,要先用汽油做为溶剂使两者混合;
之后可以蒸除;
5
1010
0.5
抗氧剂
目前PP中使用最广的抗氧剂,有优异的耐水抽出性、挥发性小,与PP相容性好;
辅助抗氧剂DLTDP并用于PP树脂中,可以显著地提高其热稳定性;
对PP树脂的抗氧性改善明显。
6
DLTD
辅抗氧剂
1.2.5成本限制
市场上,此类PP伞柄的市场批发价格为3050元/100个,参考质量中等及偏下的雨伞的市场批发价格为812元/把。
初定每100个伞柄的成本价格应该为12元/100个。
其中:
PP树脂参考价格为1800元/吨,轻质碳酸钙参考价格为800元/吨。
第二章:
制品示意图与效果图
2.1制品效果图
图2--1制品效果图
2.2制品示意图(CAD)
图2--2制品示意图(CAD作图)
第三章:
注射机型号选取
3.1初选注射机
注射机的主要参数有注射量、注射压力、注射速度、塑化能力、锁模力等,这些参数是设计、制造、购买和使用注射机的主要依据。
(1)注射量:
指在对空注射的情况下,注射螺杆或柱塞做一次最大注射行程时,注射装置所能达到的最大注射量,反应了注塑机的加工能力。
(2)注射压力:
为了克服熔料流经喷嘴、浇道和型腔时的流动阻力,螺杆或柱塞对熔料必须施加足够的压力,此压力即为注射压力。
(3)注射速率:
为了使熔料及时充满型腔,除了有必须有足够的注射压力外,熔料还必须有一定的流动速率,此参数即为注射速率。
(4)常用的注射速率如表所示。
表3--1注射量与注射施加的关系
注射量/cm3
125
250
500
1000
2000
4000
6000
10000
注射速率/cm/s
333
570
890
1330
1600
注射时间/s
1.25
1.75
2.25
3.75
(5)塑化能力:
单位时间内所能塑化的物料量。
塑化能力应与注塑机的整个成型周期配合协调,若塑化能力高而机器的空循环时间长,则不能发挥塑化装置的能力,反之则会加长成型周期。
(6)锁模力:
注射机的合模机构对模具所能施加的最大夹紧力,在此力作用下模具不应被熔融的塑料所顶开。
注射量的计算:
V1=π(R12-r12)×
H=3.87cm3
V2=π(R22-r22)×
h=0.70cm3
V3=πr2b=1.70cm3
V=V1+V2+V3=3.87+0.70+1.70=6.18cm3
其中,V1—外圆柱的体积
V2—内圆柱的体积
V3—底面圆的体积
另有塑件的投影面积为7.89cm2
M=VD′=6.18×
9.05=5.59cm3
一般的,熔体密度在0.7左右,故取值0.72g..cm-3
因此,
注射量V′=M/D=5.59/0.72=7.76cm3
根据塑件的大小和实际中常用的注射机,注射端盖塑件选用XS-YZ-60型螺杆式注射机
3.2注射机参数的校核
1)、最大注射量的校核
注射机的额定注射量为60cm3
塑件体积:
6.18cm3,每次成型4个塑件。
假设浇道凝料为20cm3。
实际注射量=6.18×
4+20=44.72cm3<
60×
80%=48cm3
最大注射量满足要求。
2)、注射压力的校核
PP塑料的注射压力为70100MPa,取80MPa;
SX-ZY-60注射机的注射压力为122MPa
注射机的注射压力满足要求。
3)、锁模力的校核
注射机的锁模力为500KN;
PP塑料的注射压力为70100MPa,取80MPa;
单个塑件在分型面上的投影面积为7.89cm2;
浇道凝料为20cm2;
注射时模具的膨胀力=(7.89×
4+20)×
10-4X80×
106=412.5KN<
500KN
锁模力满足要求。
4)、最大注射成型面积的校核
SX-ZY-60注射机的最大注射成型面积为130cm2;
注射时模具的成型面积=(7.89×
4+20)=51.56cm2<
130cm2
最大注射成型面积满足要求。
故最后选择注射机型号为XS-Z-60型注射机。
XS-Z-60型注射机︰注射量为60cm3的柱塞式塑料注射成型机,其主要参数如下表:
表3--2XS-Z-60型注射机的主要参数
额定注射量---60cm3
注射压力----122MPa
锁模力----500KN
最大成型面积--130cm2
最大开模行程--180mm
最大模具厚度--200mm
最小模具厚度--70mm
喷嘴圆弧半径--12mm
喷嘴孔直径---Φ4mm
模板尺寸----330mmX440mm
拉杆空间----190mmX300mm
定位孔直径:
Φ55+0.06
注射机的顶出方式:
机械式顶杆顶出。
单根顶杆设在模板中心。
模板面上螺纹孔M12X25共24个
第4章浇注系统设计
浇注系统的设计原则:
浇口位置应尽量选择在分型面上,以便于制品加工及使用时浇口的清理;
浇口位置距型腔各个部位的距离应尽量一致,并使其流程为最短;
浇口的位置应保证塑料流入型腔时,对着型腔中宽敞、壁厚位置,以便于塑料的流入;
避免塑料在流入型腔时直冲型腔壁,型芯或嵌件,使塑料能尽快的流入到型腔各部位,并避免型芯或嵌件变形;
尽量避免使制件产生熔接痕,或使其熔接痕产生在之间不重要的位置;
浇口位置及其塑料流入方向,应使塑料在流入型腔时,能沿着型腔平行方向均匀的流入,并有利于型腔内气体的排出。
4.1主流道设计
主流道是指浇注系统中从注射机喷嘴与模具处到分流道为止塑料熔体流动通道,是塑料熔体进入模具型腔是最先经过的部位,它将注塑机喷嘴注出的塑料熔体导入分流道或型腔,其形状为长圆锥形,流道宽度随着连接分流道的距离的减小而比增大,便于熔体顺利的向前流动,开模时主流道凝料又能顺利拉出来,主流道的尺寸直接影响到塑料熔体的流动速度和充模时间,由于主流道要与高温塑料和注塑机喷嘴反复接触和碰撞,通常不直接开在定模上,而是将它单独设计成主流道套镶入定模板内。
主流道套通常用高碳工具钢制造并热处理淬硬。
塑件外表面不许有浇口痕,又考虑取料顺利,对塑件与浇注系统联接处能自动减断。
根据选用的型号注射机的相关尺寸得:
喷嘴前端孔径:
d0=4.0mm;
喷嘴前端球面半径:
R0=12mm;
根据模具主流道与喷嘴的关系
取主流道球面半径:
R=13mm;
取主流道小端直径:
d=4.5mm
为了便于将凝料从主流道中取出,将主流道设计成圆锥形,起斜度为
,此处选用2°
,经换算得主流道大端直径为8.03mm。
4.1.1充模时的体积流率
q=
(4-1)
VP—塑料件体积,cm3;
ti—注射时间,s。
注射时间调定范围随注塑机规格不同而异。
由
表4—5可查,计算出当注塑机额定注射量为60cm3时,可取
值为0.64s,故可求出:
4.1.2:
主流道截面尺寸计算
(4-2)
其中,q—充模时的体积流率,
—相应的浇注部分的截面半径;
γ—熔体剪切速率;
一般地,主流道的熔体剪切速率为γ=102~5
103s-1,取γ=2
102s-1,故由式4-2得:
即主流道的截面半径尺寸为0.37cm。
4.2分流道的设计
分流道是主流道与浇口之间的通道,一般开设在分型面上,起分流和转向作用,分流道的长度取决于模具型腔的总体布置和浇口位置,分流道的设计应尽可能短,以减少压力损失,热量损失和流道凝料。
常用分流道断面尺寸推荐如表4-1所示。
表4-1流道断面尺寸推荐值
塑料名称
分流道断面直径mm
分流道断面直径mm
ABS,AS
聚乙烯
尼龙类
聚甲醛
丙烯酸
抗冲击丙烯酸
醋酸纤维素
聚丙烯
异质同晶体
4.8~9.5
1.6~9.5
3.5~10
8~10
8~12.5
5~10
聚苯乙烯
软聚氯乙烯
硬聚氯乙烯
聚氨酯
热塑性聚酯
聚苯醚
聚砜
离子聚合物
聚苯硫醚
6.5~16
6.5~8.0
3.5~8.0
6.5~10
2.4~10
6.5~13
分流道的断面形状有圆形,矩形,梯形,U形和六角形。
要减少流道内的压力损失,希望流道的截面积大,表面积小,以减小传热损失,因此,可以用流道的截面积与周长的比值来表示流道的效率,其中圆形和正方形的效率最高,但正方形的流道凝料脱模困难,所以一般是制成梯形流道。
采用的材质为聚丙烯时,其分流道截面半径为5~10mm,故取值为6mm,采用圆形截面的分流道。
分流道选用圆形截面:
直径D=6mm
流道表面粗糙度
一般地,分流道的熔体剪切速率为γ=5
102103s-1,取γ=6
102s-1
由式4-2可知分流道的截面半径尺寸可求为:
cm
4.3浇口的设计
浇口又称进料口,是连接分流道与型腔之间的一段细短流道(除直接浇口外),它是浇注系统的关键部分。
其主要作用是:
(1)型腔充满后,熔体在浇口处首先凝结,防止其倒流。
(2)易于在浇口切除浇注系统的凝料。
浇口截面积约为分流道截面积的0.03~0.09,浇口的长度约为0.5mm~2mm,浇口具体尺寸一般根据经验确定,取其下限值,然后在试模是逐步纠正。
当塑料熔体通过浇口时,剪切速率增高,同时熔体的内磨檫加剧,使料流的温度升高,粘度降低,提高了流动性能,有利于充型。
但浇口尺寸过小会使压力损失增大,凝料加快,补缩困难,甚至形成喷射现象,影响塑件质量。
浇口位置的选择:
(1)浇口位置应使填充型腔的流程最短。
这样的结构使压力损失最小,易保证料流充满整个型腔,同时流动比的允许值随塑料熔体的性质,温度,注塑压力等的不同而变化,所以我们在考虑塑件的质量都要注意到这些适当值。
(2)浇口设置应有利于排气和补塑。
(3)浇口位置的选择要避免塑件变形。
采侧浇口在进料时顶部形成闭气腔,在塑件顶部常留下明显的熔接痕,而采用点浇口,有利于排气,整件质量较好,但是塑件壁厚相差较大,浇口开在薄壁处不合理;
而设在厚壁处,有利于补缩,可避免缩孔、凹痕产生。
(4)浇口位置的设置应减少或避免生成熔接痕。
熔接痕是充型时前端较冷的料流在型腔中的对接部位,它的存在会降低塑件的强度,所以设置浇口时应考虑料流的方向,浇口数量多,产生熔接痕的机会很多。
流程不长时应尽量采用一个浇口,以减少熔接痕的数量。
对于大多数框形塑件,浇口位置使料流的流程过长,熔接处料温过低,熔接痕处强度低,会形成明显的接缝,如果浇口位置使料流的流程短,熔接处强度高。
为了提高熔接痕处强度,可在熔接处增设溢溜槽,是冷料进入溢溜槽。
筒形塑件采用环行浇口无熔接痕,而轮辐式浇口会使熔接痕产生。
(5)浇口位置应避免侧面冲击细长型心或镶件。
因点口在脱开时会伤塑件的内表面在这里是可以的,考虑到点浇口有利浇注系统的废料和塑件的脱离,所以本次设计选取用点绕口。
在利用了Pro/E的塑料顾问对其进行模仿CAE的注塑之后选择了更具优势的浇口。
根据浇口的位置选择要求,尽量缩短流动距离,避免熔体破裂现象引起塑件的缺陷,浇口应开设在塑件壁厚处等要求。
采用扇形浇口可以保持产品外观精度。
本设计采用边缘浇口,边缘浇口(又名为标准浇口、侧浇口)该浇口相对于分流道来说断面尺寸较小,属于小浇口的一种。
边缘浇口一般开在分型面上,具有矩形或近矩形的断面形状,其优点是浇口便于机械加工,易保证加工精度,而且试模时浇口的尺寸容易修整,适用于各种塑料品种,其最大特点是可以分别调整充模时的剪切速率和浇口封闭时间。
,其有以下特性:
(1)形状简单,去除浇口方便,便于加工,而且尺寸精度容易保证;
(2)试模时如发现不当,容易及时修改;
(3)能相对独立地控制填充速度及封闭时间;
(4)对于壳体形塑件,流动充填效果较佳。
浇口的形式一般分为:
一般浇口γ=5
103~5
104s-1,取γ=104s-1
点浇口γ=105s-1,
该浇口设计采用一般浇口形式。
由式4-2可知,浇口截面半径尺寸可求为:
4.4浇注系统示意图
图4-1主流道示意图图4-2浇注系统示意图
第五章塑料件的工艺尺寸计算与侧向分型设计
5.1型腔、型芯工作尺寸计算
PP塑料的收缩率1.0%~3.0%
平均收缩率:
=(1.0%~3.0%)/2=1.0%
型腔内径:
=46mm
型腔深度:
=31.15mm
型芯外径:
=40.2mm
型芯深度:
=29.65mm
型腔径向尺寸(mm);
-塑件外形基本尺寸(mm);
-塑件平均收缩率;
-塑件公差
-成形零件制造公差,一般取1/4—1/6
;
-塑件内形基本尺寸(mm);
-型芯径向尺寸(mm);
-型腔深度(mm);
-塑件高度(mm)
-型芯高度(mm);
-塑件孔深基本尺寸(mm);
型腔:
钢材选用P20,使用数控精雕及电火花加工成型
型芯:
5.2模架的选择
注塑模模架国家标准有两个,即GB/T12556——1990《塑料注射模中小型模架及其技术条件》和GB/T12555——1990《塑料注射模大型模架》。
由于塑料模具的蓬勃发展,现在在全国的部分地区形成了自己的标准,该设计采用龙记标准模架,型号为:
AI-1525-A30-B45-C60。
图5-1模架模型图
第六章导向机构的设计
导向机构的作用:
1)定位作用;
2)导向作用;
3)承受一定的侧向压力
6.1导柱的设计
6.1.1长度导柱导向部分的长度应比凸模端面的高度高出812