精度测量实验方法Word格式.docx
《精度测量实验方法Word格式.docx》由会员分享,可在线阅读,更多相关《精度测量实验方法Word格式.docx(53页珍藏版)》请在冰豆网上搜索。
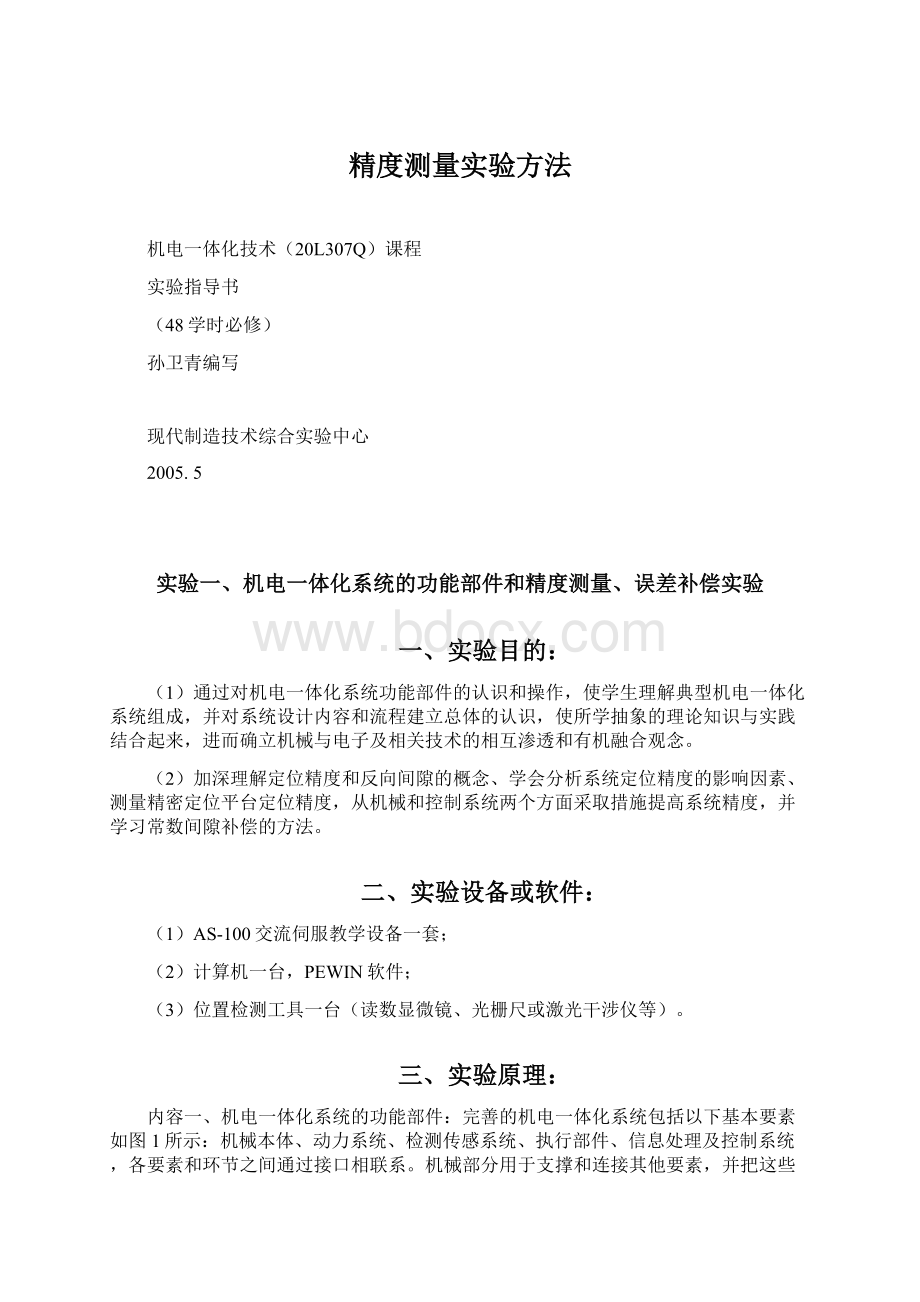
内容二、系统的精度测量及误差补偿
系统运动系统的精度是机电一体化系统的一个重要指标。
运动系统的精度包括运动精度、位置精度。
其中位置精度对精密定位系统最重要。
而定位精度对位置精度影响最大。
运动部分的定位精度是指运动部件实际位置和目标位置的接近程度。
在AS-100教学系统中,指平台在移动过程中,根据指令信号,沿某一坐标轴方向移动一段距离时,实际值与给定值的接近程度。
定位精度对系统性能的影响,例如把平台用做数控机床进给系统,将影响点位、直线控制系统的工件的尺寸精度;
对轮廓控制系统,将影响工件轮廓的加工精度,产生轮廓失真。
体现在AS-100教学实验中,将影响绘制的笔迹的尺寸精度和轮廓形状。
图2AS-100型交流伺服教学系统构成
定位精度的高低用定位误差的大小来衡量。
定位误差采用统计检验的方法确定。
定位精度受到所有电气控制系统和机械装置精度的综合影响。
不同的伺服控制方法对系统的精度影响不同。
1.定位精度分析
(1)开环系统的定位精度
在开环控制的系统中,指令经脉冲分配器、驱动器、步进电机、减速系统、滚珠丝杠螺母副转换为精密定位平台的移动。
平台的定位精度受到所有电气和机械装置及元件结构设计和制造精度的综合影响。
在使用过程中,定位精度进一步受到振动、热变形、导轨和滚珠丝杠螺母副的磨损以及控制元件特性变化等影响。
主要影响因素有:
1步进电机的误差:
步进电机步距角误差,伺服步进电机步距角误差一般为±
10~30";
步进电机动态误差:
步进电机单步运行时有明显的振荡,超调量一般为步距角的20~30%,在某些频率运行时有共振现象;
步进电机起停误差:
在步进电机启动和停止的过渡过程中,电机的转动滞后于控制脉冲。
②机械传动系统的几何误差:
包括所有传动副引起的传动误差及传动间隙。
如齿轮副,螺旋副等。
以教学设备的滚珠丝杠螺母副为例说明。
滚珠丝杠螺母副的传动误差及传动间隙,滚珠丝杠螺母副处于传动链末级,其传动误差直接影响平台的定位精度。
当丝杠转动时,螺母随着丝杠的转动做直线运动。
螺母的实际运动曲线与理想运动曲线之间的最大差值为其传动误差。
主要由于螺旋副本身的制造误差如螺距累积误差、螺纹滚道型面误差、直径尺寸误差、螺旋副的装配误差及其在装置上的安装误差等综合形成。
其中最主要的是螺距累积误差。
滚珠丝杠螺母副的接触变形比滑动副大,其引起的误差影响传动精度和间隙。
润滑、摩擦条件、表面粗糙度及材料质量、热处理硬度等都有影响。
增大预紧力可以提高接触刚度,但会增大摩擦温升,引起热变形,因此预紧力要合理取值。
③热变形影响
由于长时间工作,产生摩擦温升引起的热变形造成的定位误差。
包括电机发热、滚珠丝杠螺母副、轴承以及导轨副等相对运动部分的摩擦热。
负载部分带来的热影响等。
有丝杠和螺母相对运动产生的热伸长严重影响定位精度。
热伸长与材料热膨胀系数、温升、平台行程有关。
如温升为3℃,行程为100mm,材料为GCr15钢,其热伸长量为:
④导轨的误差
导轨副的导向精度对开环和闭环系统都非常重要。
当导轨副的导轨面存在直线度误差、平面度误差、两导轨间的平行度误差,导轨导向面的V形角误差及滚动体的形状、尺寸误差时,都会使运动体不能沿给定方向直线运动,产生运动轨迹非直线性,使运动体颤摆(上下摆动)或摇摆(左右摆动),产生导向误差,直接影响定位精度。
滚动导轨中滚动体的接触变形影响也较大,通过适当的预紧,增大接触刚度可以减小其影响。
以上各种因素中,由固定不变的或按规律变化的因素引起的定位误差是系统性误差,如导轨的形位误差、齿轮分度误差、丝杠的螺距误差等。
由不确定的,随机变化的因素引起的误差是随机性误差,如轴承游隙的变化量、摩擦力变化、表面粗糙度不均引起的误差等。
机械系统中各种机构间隙、结构弹性变形等综合形成的反向运动时的矢动量(反向间隙),是定位误差中系统性误差的一个组成部分。
(2)闭环系统的定位精度
闭环系统由于在移动台上安装了位置检测装置,把位移信号反馈到输入端与输入信号进行比较,实现对运动的反馈控制,因而各部分的误差对平台的定位精度没有直接影响。
定位误差主要取决于位置检测系统的误差,如分辨率,线性度等,以及由于检测元件的安装调整引起的误差,包括如安装倾斜、自重变形、短尺接长等产生的检测误差和安装中检测元件离被测物体距离太远引起的阿贝误差。
闭环系统中的矢动量虽不直接影响定位精度,但实际上过大的矢动量会造成伺服系统的动态不稳定和振荡,使系统的性能下降。
因此,闭环系统对机械系统的精度要求要高,一般轮廓控制的闭环数控机床的矢动量控制在≤4
。
半闭环系统的定位精度由于只在电机轴上安装的反馈元件,因此其反馈实现的控制精度只能局限在驱动环路部分,环路之外的丝杠、螺母副、和平台本身所有传动误差、制造误差、热变形等引起的误差不能由环路所矫正。
因此,针对不同系统,可以在机械设计制造过程中和电气控制系统控制中采取相应措施,以提高系统的定位精度。
2.提高定位精度的措施
因为系统性误差在总误差中占较大比重,必须采取措施减小系统误差来提高系统定位精度。
主要采取的两种最基本的方法是:
(1)从误差产生的根源采取措施——如从结构设计和制造及在安装上提高精度。
(2)采用误差补偿的方法——采用电气补偿或软件补偿的方法补偿。
①定位误差补偿方法
a.定位误差补偿原理:
人为地制造一个与原误差大小相等、方向相反的误差去补偿修正原有误差。
即
式中:
——各定位点的定位误差值,
——误差修正值。
只要实测出各坐标轴的定位误差后,就可以确定误差修正值对空间或平面任一点的定位误差进行补偿。
一般用于补偿系统误差,因为系统误差总是大于随机误差,可以取得显著效果。
b.电气补偿法
在控制系统中设置相应的间隙补偿电路和螺距补偿电路以达到误差补偿的目的。
具体实现请参考相关文献。
c.软件补偿法
利用软件进行计算机辅助补偿的方法消除定位误差,可以包括螺距累积误差补偿、方向间隙误差补偿及热变形误差补偿。
还可以根据定期测定的定位误差值,补偿由于磨损等引起的精度损失。
灵活性大,补偿量可以方便地改变。
四、实验要求:
1.实验前要首先了解机电一体化系统组成的有关知识;
2.熟悉AS-100教学设备的使用及常用各种操作;
熟悉测试仪器的使用;
3.实验前复习定位精度有关知识,了解定位精度的方法,重点复习误差补偿的原理和方法;
4.本实验必须在控制系统伺服环调整的特性非常好的情况下执行,否则影响补偿精度甚至看不出效果;
5.本实验最好使用平台(机械运动体)上直接安装位置反馈元件,反馈实际位置;
6.实验前需要调整每台机器的伺服环,使之响应特性良好。
若无高精度位移检测仪器,则该实验可能达不到预期效果。
测量不出真正的定位误差,而得到的是测量误差。
五、实验特点:
由于机电一体化技术是综合机械工程学科和电子工程学科、控制工程学科以及信息工程学科等多学科的综合技术,通过本实验的认识和操作,可以使学生对机电一体化系统设计内容和流程有总体的认识,使所学的抽象的理论知识与实践紧密地结合在一起,进而确立机械与电子及相关技术的相互渗透和有机融合,而不是这些技术的简单组合,对本课程以后章节的单元关键技术的学习以及系统设计奠定基础。
系统精度测量及误差补偿部分使学生了解影响系统精度的因素及误差补偿的方法,初步认识精密机械技术的重要性,具有较强的实践性和实用性,由于本实验综合多门技术的知识,需要掌握较多的相关领域知识,因此为综合型实验。
六、实验内容:
内容一、机电一体化系统的组成及功能部件
通过对典型机电一体化系统的功能及组成的认识实验及分析,使学生认识到机电一体化系统设计的基本内容,进而确定系统设计的基本流程,具体如下:
(1)认真分析系统操作目的,确定系统的操作功能;
(2)然后根据系统操作功能确定系统的工作机构和运动组合顺序;
(3)确定操作力的大小和方向,并据此确定动力源和驱动装置;
(4)选择并确定控制所需检测参数的各种传感器;
(5)确定控制算法和控制系统,用框图或流程图来表达所要控制的目标;
(6)对上述各项进行机械、电气、硬件和软件的设计;
(7)必要时进行模拟仿真,对算法和系统进行检验。
内容二、定位精度测量
实际定位误差包括系统性误差和随机性误差两类。
对于某一目标位置,当移动部件沿某一坐标轴从一个方向按给定指令移动时,其实际到达的位置与目标位置之间总存在误差。
重复定位的次数越多,误差值越可能呈现出围绕某一平均值的两侧做正态分布,如图3所示,该平均值与目标值之间的位置偏差反映了该移动部件系统存在的系统性误差。
误差的离散带宽(分散范围)反映了该系统的随机性误差。
在误差呈正态分布的情况下,离散带宽等于6σ,σ为均方根误差,计算公式为:
——重复定位(测量)次数(
足够大时,
)
——实测误差值
——实测误差的平均值,即位置偏差
某点的定位误差定义为该点的位置偏差与该点离散度之和,并取其最大绝对值
(取绝对值较大的一个)
误差的离散带宽表示了该点的重复定位精度,即重复定位精度为
当移动部件从正反两个方向多次重复趋近某一点定位时,正反两个方向的位置偏差不同,即反向时产生了不灵敏区,称之为反向差值(或称矢动量)。
如图4为从双向趋近某一定位点时误差分布曲线。
从正、反方向趋近定位点时,位置偏差分别为
与
,反向差值
为
图3定位精度示意图
图4双向趋近目标值时的误差分布曲线
1.定位精度测定
定位精度一般可以用刻线基准尺和读数显微镜、激光干涉仪、光栅尺、感应同步器等测量工具进行测量。
根据国家标准(GB10931—89或GB/T17421.2-2000)进行直线运动位置精度检测时,如果行程≤1000mm,定位点数及定位点测量次数均应≥5。
为了得到某一点的定位精度,需要对该点重复定位若干次(通常为5~15次,本实验取10次)进行测量以便计算出
和
为了得到一个坐标轴的的定位精度,必须随机测量坐标轴上的若干点(本实验取10个),还要从正反两个方向移动,测量和评定一个坐标轴的定位精度。
2.实际测量定位精度计算
(1)轴线重复定位精度
由于实际测量中测量次数
较小(本实验
),宜用下式计算标准偏差值
代替
各测量点的重复定位精度为
=(1,2,3,…
),为坐标轴上各测点的位置序号。
轴线重复定位精度为各测点重复定位精度中的最大值:
(2)轴线的定位精度A:
轴线的定位精度为从正反两个方向趋近各目标位置时,
、
中的最大值与
最小值之差即
轴线反向差值B:
为目标位置反向差值中的最大绝对值
七、实验步骤:
(一)定位精度、重复定位精度测定与分析
1、打开计算机和教学设备电源。
2、运行PMAC执行程序PEWIN32。
3、检查系统伺服环参数和响应特性,确保系统特性良好。
4、先让电机X回零,并在终端窗口发送“#3HMZ”,将当前光栅位置清零。
5、运行自动程序3,X轴电机将自动往复间隔运行,每15mm停一次,共走10个点,往复3次。
在电机停止时,利用光栅读出当前实际位置(速度稳定后,光栅读数是1个脉冲代表1微米)。
6、计算所测点绝对位置精度、重复定位精度,求出R,A,B值。
(二)反向间隙补偿
接上步骤,运行PMAC执行程序PEWIN32。
1、检查系统伺服环参数和响应特性,确保系统特性良好。
2、先让X轴电机走到中间位置,发送“#3HMZ”,将当前光栅位置清零。
3、在终端窗口发送“#1j:
8192”指令,让电机正转一圈,记录下此时光栅的值。
然后发送“#1j:
-8192”反转一圈,记录下此时光栅的值。
4、计算得到X轴正反转所产生的误差W(光栅读数,单位微米)。
将W值换算成X轴电机的脉冲个数,即W*1.6384(向X轴电机发送1.6384个脉冲,X轴走1微米),由于PMAC补偿的单位是1/16个脉冲,所以最终要补的数据V=W*1.6384*16。
在终端窗口键入“IX86=V”,“IX85=5”。
5、重复3、4两步,观察光栅尺正反转后反馈值的变化。
八、实验报告要求:
机电一体化系统的功能部件和精度测量、误差补偿实验报告
报告日期:
年月日
班级
学号
姓名
根据实验结果填写以下表格并进行结果分析,写出实验报告。
定位精度测定(X轴)
定位精度主要检测项目
指令值
实际值
误差值
轴线重复定位精度R
轴线的定位精度A
轴线反向差值B
九、实验考核要求:
课程期末总成绩=平时考勤成绩+平时作业成绩+实验成绩+考试成绩。
实验考核总体分为三部分:
实验预习:
20%;
实验操作:
50%;
实验报告质量:
30%。
十、实验参考资料:
1.陈林才,张鄂.精密仪器设计.北京:
机械工业出版社,1991.
2.张建民.机电一体化原理与应用.北京:
国防工业出版社,1992.
3.李建勇.机电一体化技术.北京:
科学出版社,2004.
十一、思考题:
1、开环控制、半闭环控制以及闭环控制有哪些原理上和实际接线的不同?
2、详述机电一体化系统的结构组成和工作原理。
3、什么是定位精度,精密平台的定位精度用什么指标表示?
4、如何测量一个坐标轴的定位精度?
5、本实验机定位精度的影响因素有哪些?
采取了那些措施来提高系统定位精度?
6、预紧力调整对定位平台精度有什么影响?
7、导轨装配平行度对平台有什么影响?
8、PMAC对机械平台有何补偿作用?
9、定位精度和重复定位精度有何区别?
10、平台定位误差的来源有哪些?
11、双稳定反馈在精度控制方面有什么作用?
12、减小误差的方法有哪些?
如何实现?
13、什么是系统的传动间隙,它是什么原因产生的。
14、在PMAC控制器中如何对间隙误差进行补偿?
实验二、交流伺服电机控制方式及伺服驱动原理及特性实验
(1)了解交流伺服驱动器控制方式及接线。
(2)熟练进行交流伺服驱动器的参数修改及手动操作
(3)了解永磁同步驱动系统的控制原理;
(4)掌握永磁同步驱动系统的空载调节特性及负载特性
1、AS-100教学设备一台。
2、计算机一台,PEWIN软件。
3、AS-100教学设备附件——永磁制动器1套。
内容一、交流伺服电机的控制方式
目前常用的交流伺服驱动器多为智能型驱动器,即除了电流放大作用外,也存在简单的控制功能。
一般的永磁同步伺服电动机即AC伺服电动机有位置(脉冲)控制、速度(模拟量)控制和转矩(模拟量)控制以及复合控制,控制方式的选择取决于系统的要求。
它们的主要区别在于控制信号是一个什么指令以及使用的哪一环进行闭环(相对于驱动器,如图5所示)。
位置控制时,控制信号是一个位置指令,速度环2、电流环1都是内环;
速度控制时,控制信号是一个速度指令,位置环1没有接进来;
转矩控制时,控制信号是一个转矩(电流)指令,位置环1和速度环2都未接入。
复合控制用于一些特殊场合,或者先位置控制,后速度控制,或者先速度,后转矩控制。
由于控制方式不同,控制信号及驱动器参数设置,外部接线都不一样。
位置控制信号大都是脉冲加方向信号,而速度和转矩指令大都是模拟电压信号。
内容二、交流伺服控制原理
永磁同步电机是由永磁材料制作的转子和通三相交流电源产生旋转磁场的定子构成。
目前常用的永磁同步伺服驱动的调速主回路采用矢量变换SPWM变频控制方式。
矢量变换的基本思路是将定子电流分解成励磁电流和转矩电流,在调速过程中保持转子磁链(即定子的励磁电流分量)不变,此时交流电机的调速原理就和直流电机相同了,这样就可以通过改变供电电源的频率即PWM控制来实现调速了。
AS-100教学设备采用的富士交流伺服电动机,驱动器也是采用矢量变换正弦波PWM控制方式,由内部微处理器对定子电流进行矢量变换运算,然后进行PWM调制来调速。
其控制原理方框图如图6所示,控制框图只画出了速度环和电流环部分。
光电编码器产生的脉冲信号经速度解码器处理成数字信号直接送到CPU,在数字调节器中与速度给定信号进行比较运算(PID)后产生三相交流的电流幅值信号IM。
为了提高速度调节品质,现在的驱动器大都采用了以下两项关键技术:
一是在速度解码器中采用M/T测速方法,即在电动机高速运转时,通过记录单位时间内的脉冲个数来实现速度测量,而在电动机低速运转时,通过记录两脉冲之间的时间长短来实现速度测量。
这样无论是在高速或低速时都能很准确的测定电动机的转速。
二是数字调节器算法中采用先进的滑模算法,这种算法根据电动机在高速和低速运行状态上的不同特性,分别给定不同的PID调节参数,使各阶段的参数都能得到优化。
这样就使电动机在低速运行时平稳性好,高速时跟随误差小,富士伺服驱动器采用了这种算法。
图6交流伺服控制原理
为生成三相交流电,需通过乘法器将电流幅值信号IM与电动机转子位置信号θ通过矢量乘法运算来合成(按以下公式)。
位置信号θ由光电编码器产生的脉冲信号经位置解码器处理成数字的电动机转子角位置。
iu=IMsinθ
iv=IMsin(θ+120o)
iw=IMsin(θ+240o)
当三相电流获得后送入电流调节器同反馈回来的电流信号进行比较运算后经PWM调制后到驱动电路,最后驱动伺服电动机工作。
除了这些基本结构外,电路中还加入了故障处理和保护环节,如过压、欠压、过流、断相及电动机过热等硬件检测及保护电路。
一旦出现故障将通知CPU并封锁输出。
同步电机转子转速与定子旋转磁场的转速相同,当电源频率不变时,同步电动机的转速为常数,与负载无关。
(f为电源频率,p为转子磁极极对数)
同步电机的转速正比于电源的线电压(在额定速度以内,超出额定速度时由于弱磁控制,电压将被嵌位于定值),这就是永磁同步伺服电机的调节特性。
如图7所示:
交流永磁同步电机在额定速度以内具有恒转矩的特性,超出额定速度后,由于弱磁控制,具有恒功率的特性。
这样在额定速度以内,负载一定时,交流永磁同步伺服电机就不像步进电机、直流伺服电机一样,随着速度的增加,输出转矩下降。
这样的特性非常适合于恒转矩类型的负载,比如机床的进给系统。
交流电机的输出功率计算公式为:
(W:
单位瓦,V:
单位转/分,N:
单位牛.米)
由上式可以看出,在负载一定时,伺服电机的输出功率同速度成正比。
交流伺服驱动器输入功率计算公式为:
(U:
线电压,I:
线电流)
1、操作时请注意安全,不要造成短路以及接触电源动力线。
2、详细阅读伺服驱动器操作说明及本书后控制方式的接线参考图。
3、熟悉富士交流伺服的相关参数设定。
4、熟悉富士交流伺服驱动器做位置、速度、转矩控制时的接线以及相关参数设置
5、复习交流伺服电机的空载调节特性和机械特性。
6、每次读数需等到速度稳定后再读。
交流伺服电机控制方式及伺服驱动原理及特性实验综合应用了伺服驱动技术、自动控制技术和机械电子技术等多学科的综合知识,通过本实验加深学生对理论知识的理解,并增强动手能力和综合实践能力。
交流伺服电机控制方式实验学生可通过改变接线来实现伺服驱动器控制方式的改变,在实际操作中理解伺服驱动器的各种操作模式,通过这些操作(手动正反转及速度调整)理解交流伺服驱动器相关控制参数的设定,掌握伺服驱动器进行位置、速度以及转矩控制时的参数设置。
通过伺服驱动控制原理及特性实验了解永磁同步驱动系统的控制原理,掌握永磁同步驱动系统的空载调节特性及负载特性,进一步加深机电一体化系统中伺服驱动系统知识的理解和实际应用,可培养学生综合运用所学知识和实验方法、实验技能,分析、解决问题的能力
因此本实验为综合型实验。
内容一:
富士交流伺服驱动器参数调整及操作应用
富士交流伺服驱动器接线图可以参见图8,由于AS-100系列教学设备选用的是单相200V的电源供电,所以主电源只需要接L1、L2,控制端子CN1用于接受控制指令以及数字IO,编码器输出等;
控制端子CN2用于接受编码器反馈;
CN3A、CN3B为通讯接口(同上位机以及驱动器之间通讯);
CN4为模拟量监视输出。
CN1主要接口说明:
P24、M24:
用于为驱动器控制电路提供DC24V电源;
CONT1:
如果该端子和控制电源地(M24)相连,则伺服驱动器将允许工作,如果断开,则驱动器禁止输出。
该信号已做连接,用于急停按钮(此端子功能由伺服驱动器参数定义,缺省定义为伺服ON);
CA、*CA、CB、*CB:
本端子用于位置控制时的信号输入(脉冲及方向信号);
Vref、M5:
用于控制信号输入,本端子用于速度控制或转矩控制时的信号输入;
FFA、*FFA、FFB、*FFB、FFZ、*FFZ:
编码器脉冲输出端,富士伺服驱动器可以将码盘反馈回来的脉冲信号同步的发送给其它的控制器,AS-100也采用了这种接法,可以将反馈的脉冲同时送到驱动器和PMAC控制卡中。
图8富士交流伺服驱动器接线图
CN2主要接口说明:
该端子为富士伺服电机码盘反馈信号输入端,AS-1