机械制造装备课程设计指导书Word文档下载推荐.docx
《机械制造装备课程设计指导书Word文档下载推荐.docx》由会员分享,可在线阅读,更多相关《机械制造装备课程设计指导书Word文档下载推荐.docx(20页珍藏版)》请在冰豆网上搜索。
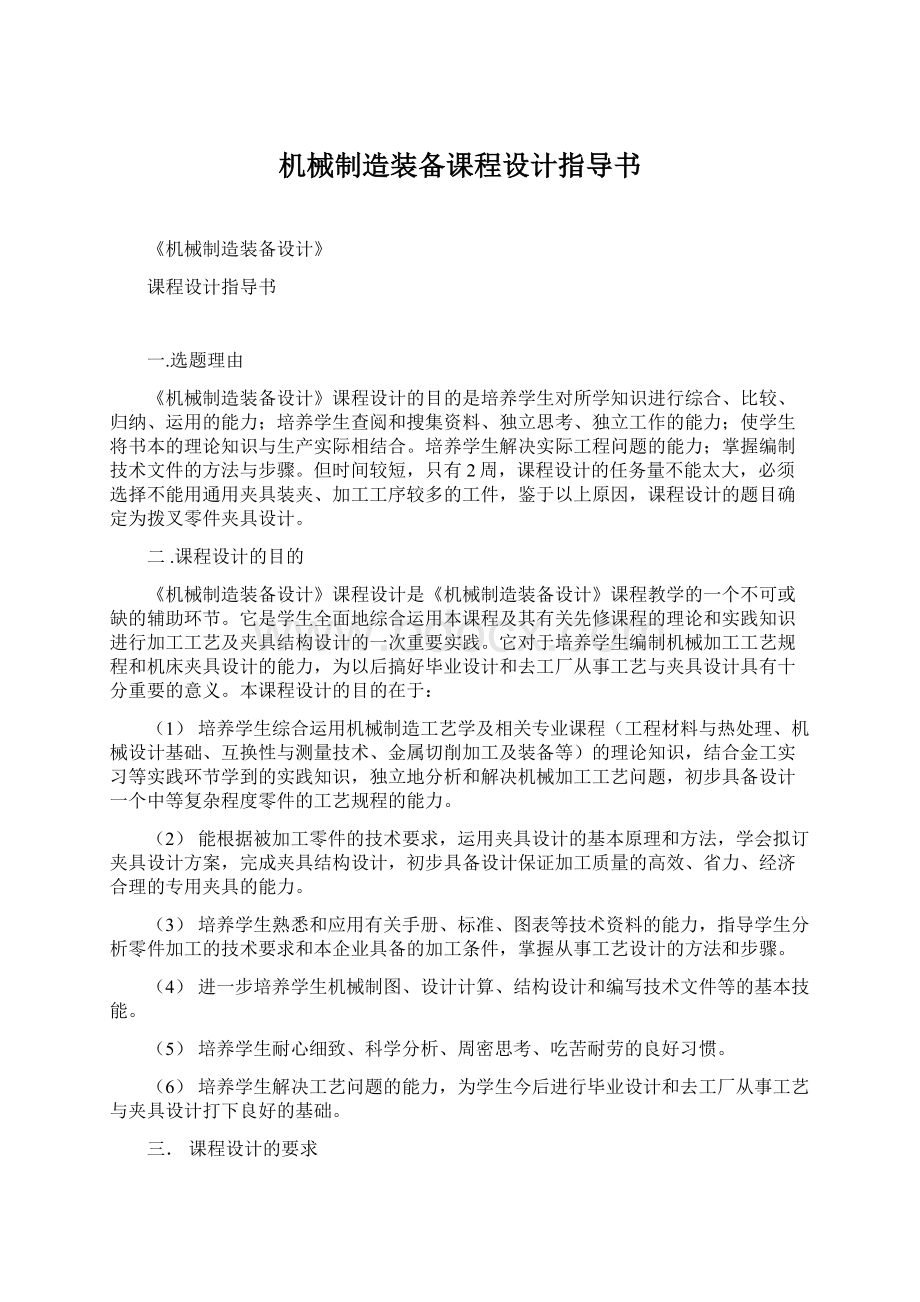
产品零件图1
机械加工工艺过程卡片1套
机械加工工序卡片1套
夹具总装图(0#或1#或2#图纸)1
夹具主要零件图(2#~4#图纸)若干
课程设计说明书(4000~6000字)1份
四.课程设计的容
(1)绘制产品零件图,了解零件的结构特点和技术要求。
(2)根据生产类型和所拟企业的生产条件,对零件进行结构分析和工艺分析。
有必要的话,对原结构设计提出修改意见。
(3)确定毛坯的种类及制造方法,绘制毛坯图。
(4)拟定零件的机械加工工艺过程,选择各工序的加工设备和工艺装备(刀具、夹具、量具、模具、工具),确定各工序的加工余量和工序尺寸,计算各工序的切削用量和工时定额,并进行技术经济分析。
(5)填写机械加工工艺过程卡片、机械加工工序卡片(可根据课程设计时间的长短和工作量的大小,由指导教师确定只填定部分主要加工工序的工序卡片)等工艺文件。
(6)设计指定工序的专用夹具,绘制装配总图和主要零件图。
(7)撰写设计说明书。
针对加工工序,以3~4人为一小组,学生应该翻阅和查找相关设计手册和资料,确定夹具设计方案,,每人设计一套完整的夹具工作图。
五.课程设计的步骤
(一)机械加工工艺规程设计
机械加工工艺规程是指导生产的重要技术文件,是一切有关的生产人员应严格执行、认真贯彻的法规性文件。
制订机械加工工艺规程应满足以下基本要求:
(1)保证零件的加工质量,可靠地达到产品图纸所提出的全部技术条件,并尽量提高生产率和降低消耗;
(2)尽量降低工人的劳动强度,使其有良好的工作条件;
(3)在充分利用现有生产条件的基础上,采用国外先进工艺技术;
(4)工艺规程应正确、完整、统一、清晰;
(5)工艺规程应规、标准,其幅面、格式与填写方法以及所用的术语、符号、代号等应符合相应标准的规定;
(6)工艺规程中的计量单位应全部使用法定计量单位。
为了保证工艺规程设计质量,在制订机械加工工艺规程时,应具备下列原始资料:
(1)产品的整套装配图和零件图;
(2)产品的验收质量标准;
(3)产品的生产纲领;
(4)现有的生产条件与设计条件;
(5)有关工艺标准、没备和工艺装备资料;
(6)国外同类产品的生产技术发展情况。
产品零件图样、生产纲领和工厂的生产条件是课程设汁的主要原始资料,根据这些资料确定了生产类型和生产组织形式之后,即可开始按以下步骤进行工艺设计,拟定工艺规程。
1.分析、研究零件图(或实物),进行结构工艺性审查
(1)熟悉零件图,了解零件性能、功用、工作条件及所在部件(或整机)中的作用。
(2)了解零件材料及其热处理要求,合理选择毛坯种类及其制造方法。
(3)分析零件的确切形状和结构特点,分析零件图上各项技术要求制定的依据,找出关键技术问题。
(4)确定主要加工表面和次要表面,确定零件各表面的加工方法和切削用量。
(5)分析零件的结构工艺性。
从选材是否得当,尺寸标注和技术要否合理,零件的结构是否便于安装和加工,零件的结构能否适应生产类型和具体的生产条件,是否便于采用先进的、高效率的工艺方法等方面进行结构分析,对不合理之处可提出修改意见。
所谓具有良好的结构工艺性,应是在不同生产类型的具体生产条件下,对零件毛坯的制造、零件的加在和产品的装配,都能采用较经济的方法进行的结构。
使用性能完全相同的零件,因结构稍有不同,其制造成本就有很大的差别。
绘制零件图的过程也是一个分析和认识零件的过程。
零件图应按机械制图国家标准精心绘制。
除特殊情况经指导教师同意者外,通常均按1﹕1比例绘出。
2.根据生产纲领和生产类型,确定工艺的基本特征
生产纲领和生产类型不同,产品零件的制造工艺、所用设备及工艺装备、对工人的技术要求、采取的技术措施和要求达到的技术经济效果也会不同。
3.确定毛坯的类型和制造方法,绘制毛坯图
(1)毛坯的类型及其特点。
机械零件常用的毛坯类型有:
①型材:
含各种冷拔、热轧的板材、棒料(圆的、六角的、特形的)、丝材;
②铸件:
含砂型铸件(包括木模手工造型、金属模机械造型)、金属型铸件、离心浇注铸件、压力或熔模精密铸件;
③锻件:
自由锻锻件、模锻(立式锻、卧式锻)锻件、精密锻造锻件;
④焊接件
⑤压制件
⑥冲压件
(2)选择毛坯的制造方式,确定毛坯的精度。
选择毛坯的制造方式,确定毛坯的精度,都应综合考虑生产类型和零件的结构、形状、尺寸、材料等因素。
此时,若零件毛坯选用型材,则应确定其名称、规格;
如为铸件,则应确定分型面、浇冒口系统的位置;
若为锻件,则应确定锻造方式及分模面等。
(3)确定余量。
可查阅有关的机械加工工艺手册,用查表法确定各表面的总余量及余量公差,也可用计算法确定。
(4)绘制毛坯图。
确定总余量之后即可绘制毛坯图。
其步骤为:
①用双点划线画出经简化了次要细节的零件图的主要视图,将已确定的加工余量叠加在各相应的被加工表面上,即得到毛坯轮廓;
②用粗实线绘出毛坯形状,比例1﹕1;
③标注毛坯的主要尺寸及公差,标出加工余量的名义尺寸;
④标明毛坯的技术要求,如毛坯精度、热处理及硬度、圆角尺寸、拔模斜度、表面质量要求(气孔、缩孔、夹砂)等;
⑤和绘制一般的零件图一样,为表达清楚毛坯的某些部结构,可画出必要的剖视、剖面图,对于实体上加工出来的槽和孔,则可不必这样表达;
⑥注明一些特殊的余块,如热处理工艺的夹头、机械试验和金相试验用试棒、机械加工用的工艺夹头等的位置。
4.拟定工艺路线
零件的机械加工工艺过程是工艺规程设计的核心问题。
对于复杂零件,设计时通常应以“优质、高产、低消耗”为宗旨,拟出2~3个方案,经全面分析对比,从中选择出一个较为合理的方案。
(1)选择定位基准。
正确地选择定位基准是设计工艺过程的一项重要容,也是保证零件加工精度的关键,而且对确定加工顺序、加工工序的多少、夹具的结构等都有重要影响。
设计时,应根据零件的结构特点、技术要求及毛坯的具体情况,按照粗、精基准的选择原则来确定各工序合理的定位基准。
当定位基准与设计基准不重合时,需要对它的工序尺寸和定位误差进行必要的分析和计算。
零件上的定位基准、夹紧部位和加工面三者要互相协调、全面考虑。
(2)决定各表面的加工方法,划分加工阶段。
各表面的加工方法主要依据其技术要求,综合考虑生产类型、零件的结构形状和尺寸、工厂的生产条件、工件材料和毛坯情况来确定。
根据各表面的加工要求,先选定最终的加工方法,再由此向前确定各准备工序的加工方法。
决定表面加工方法时还应对照每种加工方法所能达到的经济加工精度,先主要表面、后次要表面。
再根据零件的工艺分析,毛坯状态和选定的加工方法,看一看应采用哪些热处理;
是否需划分成粗加工、半精加工、精加工等几个阶段。
(3)工序的集中与分散。
各表面加工方法确定之后,应考虑哪些表面的加工适合在一道工序中完成,哪些则应分散在不同工序为好,从而初步确定零件加工工艺过程中的工序总数及容。
一般情况下,单件小批量生产只能采取工序集中,而大批量生产则既可以工序集中,也可以工序分散。
从发展的角度来看,当前一般采用工序集中原则来组织生产。
(4)初拟加工工艺路线。
加工顺序的安排一般应按“先粗后精、先面后孔、先主后次、基准先行”的原则进行,热处理工序应分段穿插进行,检验工序则按需要来安排。
通常应初拟2~3个较为完整合理的该零件的加工工艺路线,经技术经济分析后取其中的最佳方案实施之。
(5)工艺装备的选择。
选择工艺装备的总原则是根据生产类型与加工要求,使之既能保证加工质量,又经济合理。
工艺装备的选择应与工序精度要求相适应、与生产纲领相适应、与现有设备条件相适应。
批量生产条件下,通常采用通用机床加专用工、夹具;
大量生产条件下,多采用高效专用机床、组合机床流水线、自动线与随行夹具。
设计时,应认真查阅有关手册,尽量进行实地调查,应将所选机床或工艺装备的相关参数(如机床型号、规格、工作台宽、T形槽尺寸;
刀具形式、规格、与机床的连接关系;
夹具、专用刀具的设计要求,与机床的连接方式等记录下来,为后面填写工艺卡片作好准备。
(6)填写工艺过程卡片。
选定工艺装备后,看是否要对先前初拟的工艺路线进行修改。
确认后,即可填写机械加工工艺过程卡片。
机械加工工艺过程卡片应按照JB/Z187.3—88中规定的格式及原则填写。
5.机械加工工序设计
(1)确定加工余量。
毛坯余量已在画毛坯图时确定。
这里主要是确定工序余量。
合理选择加工余量对零件的加工质量和整个工艺过程的经济性都有很大影响。
余量过大,将造成材料和工时的浪费,增加机床和刀具的损耗;
余量过小,则不能去掉加工前存在的误差和缺陷,影响加工质量,造成废品。
因此,应在保证加工质量的前提下,尽量减少加工余量。
确定工序余量的方法有三种:
计算法、经验估算法和查表法。
本设计可参阅有关机械加工工艺手册,用查表法按工艺路线的安排,一道道工序、一个个表面地加以确定,必要时可根据使用时的具体条件对手册中查出的数据进行修正。
(2)确定工序尺寸及公差。
计算工序尺寸和标注公差是制订工艺规程的主要工作之一。
工序尺寸公差一般通常查阅加工工艺手册,按经济加工精度确定。
而工序尺寸的确定有二种情况:
①当定位基准(或工序基准)与设计基准重合时,可采用“层层包裹”的方法,即将余量一层层叠加到被加工表面上,可以清楚地看出每道工序的工序尺寸,再按每种加工方法的经济加工精度公差按“入体方式”标注在对应的工序尺寸上。
例如,某加工表面为φ100H6的孔,Ra为0.4μm,其加工工艺路线为粗镗—精镗—粗磨—精磨。
②当定位基准(或工序基准)与设计基准不重合时,即加工基准多次变换时,此时应按尺寸链原理来计算确定工序尺寸与公差,并校核余量层是否满足加工要求。
(3)确定各工序的切削用量。
合理的切削用量是科学管理生产、获得较高技术经济指标的重要前提之一。
切削用量选择不当会使工序加工时间增多,设备利用率下降,工具消耗增加,从而增加产品成本。
确定切削用量时,应在机床、刀具、加工余量等确定之后,综合考虑工序的具体容、加工精度、生产率、刀具寿命等因素。
选择切削用量的一般原则是保证加工质量,在规定的刀具耐用度条件下,使机动时间少、生产率高。
为此,应合理地选择刀具材料及刀具的几何参数。
在选择切削用量时,通常首先确定背吃刀量(粗加工时尽可能等于工序余量);
然后根据表面粗糙度要求选择较大的进给量;
最后,根据切削速度与耐用度或机床功率之间的关系,用计算法或查表法求出相应的切削速度(精加工则主要依据表面质量的要求)。
本设计一般参阅有关机械加工工艺手册,采用查表法。
下面介绍常用加工方法切削用量的一般选择方法:
①车削用量的选择
背吃刀量。
粗加工时,应尽可能一次切去全部加工余量,即选择背吃刀量值等于余量值。
当余量太大时,应考虑工艺系统的刚度和机床的有效功率,尽可能选取较大的背吃刀量值和最少的工作行程数。
半精加工时,如单边余量h>
2mm,则应分在两次行程中切除:
第一次ap=(2/3~3/4)h,第二次ap=(1/3~1/4)h。
如h≤2mm,则可一次切除。
精加工时,应在一次行程中切除精加工工序余量。
进给量。
背吃刀量选定后,进给量直接决定了切削面积,从而决定了切削力的大小。
因此,允许选用的最大进给量受下列因素限制:
机床的有效功率和转矩;
机床进给机构传动链的强度;
工件的刚度;
刀具的强度与刚度;
图样规定的加工表面粗糙度。
生产实际多依靠经验法,本设计可利用金属切削用量手册,采用查表法确定合理的进给量,
切削速度。
在背吃刀量和进给量选定后,切削速度的选定是否合理,对切削效率和加工成本影响很大。
一般方法是根据合理的刀具寿命计算或查表选定v值。
精加工时,应选取尽可能高的切削速度,以保证加工精度和表面质量,同时满足生产率的要求。
粗加工时,切削速度的选择,应考虑以下几点:
硬质合金车刀切削热轧中碳钢的平均切削速度为1.67m/s,切削灰铸铁的平均切削速度为1.17m/s,两者平均刀具寿命为3600~5400h;
切削合金钢比切削中碳钢切削速度要降低20%~30%;
切削调质状态的钢件或切削正火、退火状态的钢料切削速度要降低20%~30%;
切削有色金属比切削中碳钢的切削速度可提高100%~300%。
②铣削用量的选择
铣削背吃刀量。
根据加工余量来确定铣削背吃刀量。
粗铣时,为提高铣削效率,一般选铣削背吃刀量等于加工余量,一个工作行程铣完。
而半精铣及精铣时,加工要求较高,通常分两次铣削,半精铣时背吃刀量一般为0.5~2mm;
精铣时,铣削背吃刀量一般为0.1~1mm或更小。
每齿进给量。
可由切削用量手册中查出,其中推荐值均有一个围。
精铣或铣刀直径较小、铣削背吃刀量较大时,用其中较小值。
大值常用于粗铣。
加工铸铁件时,用其中较大值,加工钢件时用较小值。
铣削速度。
铣削背吃刀量和每齿进给量确定后,可适当选择较高的切削速度以提高生产率。
选择时,按公式计算或查切削用量手册,对大平面铣削也可参照国外的先进经验,采用密齿铣刀、选大进给量、高速铣削,以提高效率和加工质量。
③刨削用量的选择
刨削背吃刀量。
刨削背吃刀量的确定方法和车削基本相同。
刨削进给量可按有关手册中车削进给量推荐值选用。
粗刨平面根据背吃刀量和刀杆截面尺寸按粗车外圆选其较大值;
精加工时按半精车、精车外圆选取;
刨槽和切断按车糟和切断进给量选择。
刨削速度。
在实际刨削加工中,通常是根据实践经验选定切削速度。
若选择不当,不仅生产效率低,还会造成人力和动力的浪费。
刨削速度也可按车削速度公式计算,只不过除了如同车削时要考虑的诸项因素外,还应考虑冲击载荷,要引入修正系数k冲(参阅有关手册)。
④钻削用量的选择。
钻削用量的选择包括确定钻头直径D、进给量f和切削速度v(或主轴转速n)。
应尽可能选大直径钻头,选大的进给量,再根据钻头的寿命选取合适的钻削速度,以取得高的钻削效率。
钻头直径。
钻头直径D由工艺尺寸要求确定,尽可能一次钻出所要求的孔。
当机床性能不能胜任时,才采取先钻孔、再扩孔的工艺,这时钻头直径取加工尺寸的(0.5~0.7)倍。
孔用麻花钻直径可参阅JB/Z228—85选取。
进给量f主要受到钻削背吃刀量与机床进给机构和动力的限制,有也受工艺系统刚度的限制。
标准麻花钻的进给量可查表选取。
采用先进钻头能有效地减小轴向力,往往能使进给量成倍提高。
因此,进给量必须根据实践经验和具体条件分析确定。
钻削速度。
钻削速度通常根据钻头寿命按经验选取。
(4)制定工时定额。
主要是确定工序的机加工时间,也可包括辅助时间、技术服务时间、自然需要时间及每批零件的准备、终结时间等。
工时定额主要按经过生产实践验证而积累起来的统计资料来确定,随着工艺过程的不断改进,需要经常进行相应的修订;
对于流水线和自动线,由于有规定的切削用量,工时定额部分通过计算,部分应用统计资料得出。
在计算每一道工序的单件时间后,还必须对各道工序的单件计算时间进行平衡,以最大限度地发挥各台机床的生产效率,达到较大的生产率,保证生产任务的完成。
本设计作为对工时定额确定方法的一种了解,可只确定一个工序的单件工时定额。
可参阅有关的机械加工工艺手册,采用查表法或计算法得出。
(5)填写机械加工工序卡片。
加工工序设计完成后,要以表格或卡片的形式确定下来,以便指导工人操作和用于生产、工艺管理。
工序卡片填写时字迹应端正,表达要清楚,数据要准确。
机械加工工序卡片应按照JB/Z187.3—88中规定的格式及原则填写。
机械加工工序卡片中的工序简图按如下要求制作:
①简图应按比例缩小,用尽量少的视图表达。
简图也可以只画出与加工部位有关的局部视图,除加工面、定位面、夹紧面、主要轮廓面外,其余线条均可省略,以必需、明了为度。
②被加工表面用粗实线表示,其余均用细实线。
③应标明本工序的工序尺寸、公差及粗糙度要求。
④定位、夹紧表面应以JB/T5601—91规定的符号标明。
(见附件2)
(6)夹具的易损件应便于更换和维修。
六.设计时间及安排
1.设计时间:
2周
2.时间安排:
2013年6月3日--6月14日
(1)了解本课题的设计容、任务及有关要求。
查阅和搜集相关的资料
(2)从设计、工艺、质量等方面进行技术分析,确定设计方案
(3)绘制设计图
(4)编写设计说明书
(1)、
(2)两项工作3-4天时间必须完成;
(3)、(4)两项工作在剩余的时间必须完成。
七.工作图的绘制
1.工作图中的工件画法
与其他机械装配图不同的是,夹具装配图除了表达夹具本身的零部件外,被加工的工件也出现在夹具装配图中,但是以双点划线勾勒工件外形和主要结构,尤其是定位基准面。
2.图号编制
(1)总图号图号标注示例
在铣床上铣削Φ24H7孔长端端面夹具:
XCDJ•00
在钻床上钻削Φ24H7孔夹具:
ZKJ•00
在铣床上铣削小台阶面夹具:
XXTJ•00
在铣床上铣削大台阶面夹具:
XDTJ•00
在铣床上铣削R25弧形面夹具:
XHJ•00
在铣床上铣削R25弧形端面夹具:
XHD•00
在钻床上钻削M8-6H螺纹底孔并攻螺纹夹具:
ZLK•00
在铣床上铣削长端端面:
XCDJR•00
在铣床上铣削长端反端面:
XCFDJR•00
在铣床上铣削短端端面XDDJR•00:
在钻床上钻削Φ10H8孔:
ZKJRY•00
在钻床上钻削Φ12H7、Φ25H7:
ZKJRR•00
(2)图号标注示例
一级部件图号标注示例:
ZLK•00•01
一级零件图号标注示例:
ZLK•00--01
二级部件图号标注示例:
ZLK•00•01•01
二级零件图号标注示例:
ZLK•00•01—01
3.标题栏画法
(1)装配图标题栏画法
(2)零件图标题栏画法
4.夹具设计常用国家标准
八.参考文献.
1.所学课程教科书
2.机械设计手册
九.设计说明书的撰写(见附件2)
附件1:
拨叉的作用
拨叉零件主要用在操纵机构中,比如改变车床滑移齿轮的位置,实现变速;
或者应用于控制离合器的啮合、断开的机构中,从而控制横向或纵向进给。
拨叉应用于机床变速机构中如下图:
变速操纵机构
1——拨叉;
2——曲柄;
3——凸轮;
4——轴;
5——杠杆;
6——轴;
7——螺钉
轴2的双联滑移齿轮和轴3上的三联滑移齿轮用一个手柄操纵。
变速手柄每转一转,变换全部6种转速,故手柄共有均布的6个位置。
变速手柄装在主轴箱的前壁上,通过链传动轴4。
轴4上装有盘形凸轮3和曲柄2。
凸轮3上有一条封闭的曲线槽,由两段不同半径的圆弧和直线组成。
凸轮上有1-6个变速位置,如图所示。
位置1.2.3使杠杆5上端的滚子处于凸轮槽曲线的大半径圆弧处。
杠杆5竟拔叉6将轴2上的双联滑移齿轮移向左端位置。
位置4.5.6则将双联滑移齿轮向右端位置。
曲柄2随轴4转动,带动拔叉,拔动轴III上的三联齿轮,使它位于左、中、右三个位置。
顺次转动手柄,就可使俩个滑移齿轮的位置实现六种组合,使轴III得到6种转速。
拨叉在纵、横向进给机构中的应用:
当需要纵向进给时,扳动手柄1向左或向右,使手柄1绕销轴2左、右摆动,手柄座3下端的开口槽拨动轴5上的球头销4左、右移动,轴5左端的开口槽推、拉杠杆11,使连杆12左右移动,连杆12左端通过销子推、拉凸轮13转动,凸轮13上的曲线槽通过销子14使拨叉16向里或向外移动,从而带动离合器M8,使之与轴XXⅡ上的两个空套齿轮中的一个的端面齿啮合,实现向左或向右的纵向机动进给。
纵、横向机动进给操纵机构的结构原理图。
1、6--手柄2、21--销轴3--手柄座4、9--球头销5、7、23--轴8--弹簧销
10、15--拨叉轴11、20--杠杆12--连杆13、22--凸轮14、18、19--圆销16、17--拨叉
当向里或向外扳动手柄1时,带动轴23连同其左端的凸轮22转动,凸轮22上的曲线槽通过圆销19使摆杆20摆动,摆杆另一端的圆销19推动拨叉17向里或向外移动,使离合器M9与轴XXV上两个空套齿轮中的一个端面齿啮合,实现向里或向外的横向机动进给。
当手柄1处于中间位置时,离合器M8和M9也处于中间位置,此时设有纵、横向机动进给。
当手柄1扳至左、右、里、外任一位置,并同时按下手柄1顶端的按钮S时,刀架即在相应方向作快速移动。
附件2:
定位符号(/T5061-1991)
定位支
承类型
符号
独立定位
联合定位
标注在视图轮廓线上
标注在视图正面1)
固定式
活动式
夹紧符号(/T5061-1991)
夹紧动力源
类型
独立夹紧
联合夹紧
标注在视图正面
机械夹紧
液压夹紧
气动夹紧
电磁夹紧
大学机
械工程学院
机械加工工序卡片
产品型号
零件图号
产品名称
旋耕机
零件名称
犁刀变速齿轮箱体
共