PVC门窗异型材的生产工艺Word文档格式.docx
《PVC门窗异型材的生产工艺Word文档格式.docx》由会员分享,可在线阅读,更多相关《PVC门窗异型材的生产工艺Word文档格式.docx(13页珍藏版)》请在冰豆网上搜索。
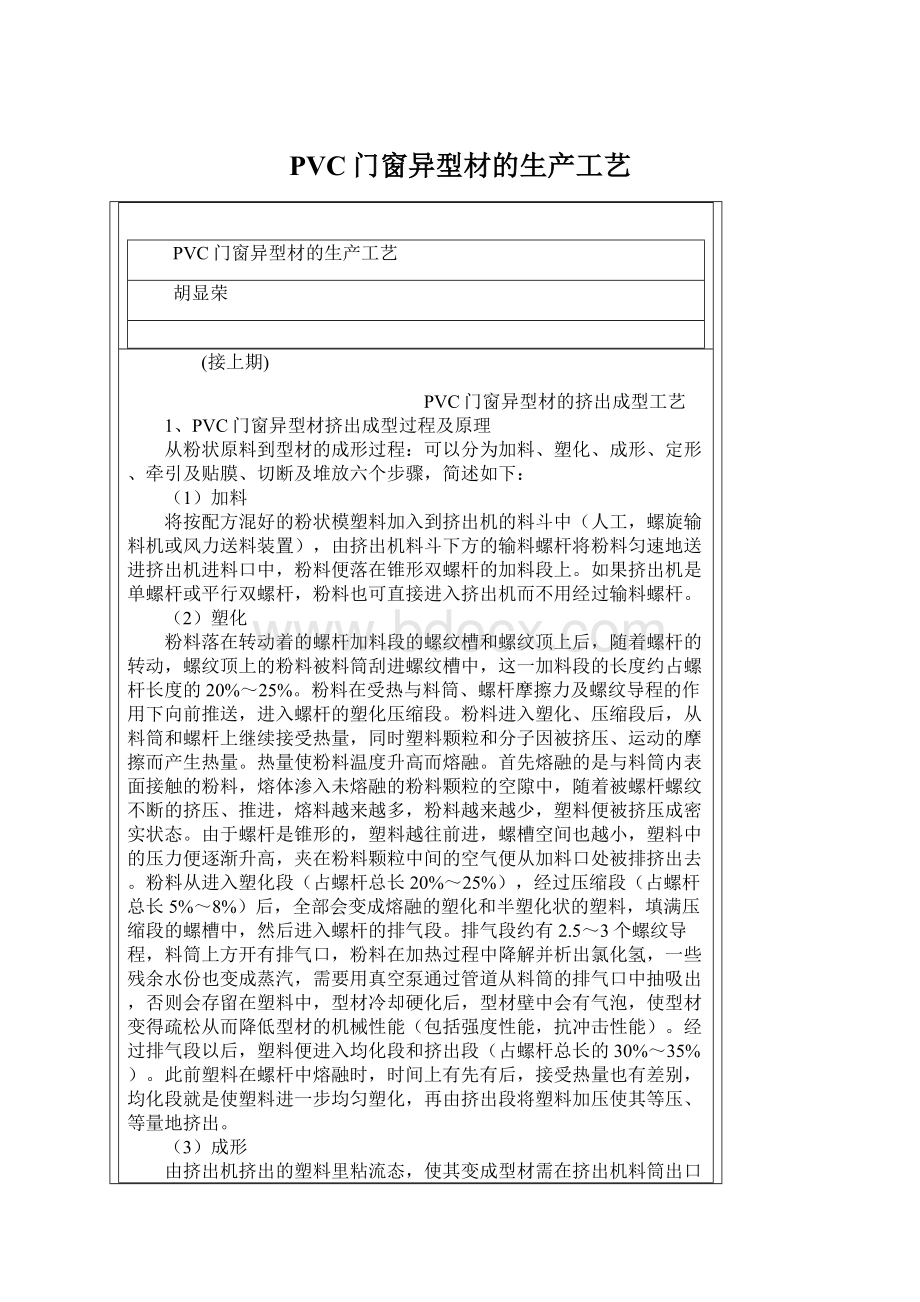
(4)定形
从模头挤出的型材虽然与图纸规定的剖面形状基本一致,但因塑料仍呈粘流态而无法保持形状,必须立即冷却以稳定挤出的型材剖面形状。
这由冷却定型模来完成。
冷却定型模与模头相距很近(约10mm左右或更小),使挤出的热型坯立即进入定型套迅速贴在它的内表面冷却变硬以稳定形状。
由于热胀冷缩,型材的剖面尺寸在冷却的过程中也将随温度降低而缩小,型材的外表因是紧贴着冷却定型套冷却变硬的,可保持外型尺寸与定型套的内腔形状尺寸一致。
型材从冷却定型模出口出来以后形状和尺寸基本稳定,但型材壁厚的中心部分由于塑料传热较差,温度仍比外表面高,加之型材内腔的一些筋、肋、凸台等是无法与冷却定型模内腔接触的,这些部位主要靠型材腔内的空气冷却,所以有的冷却定型台的后部还设有喷淋水箱以便继续冷却型材。
当型材从冷却定型模或喷淋水箱出来后,便有一套装在冷却定型台上的吹风装置吹出强风将型材各外表面的水份吹干,以免型材进入牵引机后因表面有水份打滑影响牵引速度的稳定和对型材保护膜贴附;
吹风还有进一步的散热作用,型材吹干后再经过装在冷却定型台尾部的四块加热板中央的空间进入牵引机。
正常情况下这四块加热板是不用的。
只有在发现型材轴向不直度太大,超过标准规定而在冷却定型模上又找不出原因及解决办法时才启用校直。
(5)牵引及贴膜
如前所述,从挤出机挤出的型坯是高温柔软状态,进入冷却定型模冷却变硬成形时会产生很大摩擦阻力,完全靠履带牵引机的上下两根转动着的履带将型材夹住从冷却定型模中拉出型材。
开始时型坯尚未与定型套贴合定形,冷却也不充分,需用人工将型坯送入两根履带之间,履带的夹紧力会将型坯夹扁,成为废坯。
为此需要预先准备两根方木,长约400~500mm,宽约40~60mm,高度比型材两夹紧面的距离相同或略低0.5~1mm。
等型材完全成形后将两根方木依次连续与已成形的型材同时平行地放进履带中,以分散履带的夹持力,在方木运动到履带末端出来时,操作者应及时拿出方木。
这时型材就不会被压扁了。
下次重新生产时,也可用两根长度与方木相近的型材代替方木。
等到型材剖面形状完整,各处尺寸及壁厚符合图纸规定后,就可贴保护膜了。
这时的型材只能算形状、尺寸部分合格,还应按GB8814-98取样送试验室检验、全部合格后才能贴合格证、包装。
(6)切断及堆放
型材由装在牵引机尾部的自动切割锯切断成规定的长度(6m),定货规定其它长度,只要调整一下终点开关的固定位置便可以了。
当每根型材全长运行到翻转架的托板上时,端头碰到终点开关,托板便向型材架倾斜,型材便自动滑落到型材架上,堆放到一定数量时,由人工包装运走,或搬到型材集装架上,集装架满后入库。
如果试验室通知有不合格项目,就必须检验、技术部门据不合格项目的具体情况商定是报废?
还是"
超差代用"
?
如果全部合格,则在型材上贴合格证(或盖"
合格品"
印)入库。
2、PVC门窗异型材挤出成型的工艺参数
优质的原料及助剂、科学合理的配方、良好的挤出生产设备、模具的先进设计与精确加工、型材剖面系统优秀的设计与工艺性等是生产高质量PVC门窗异型材的"
基础"
;
而生产操作是否正确,则是最后决定型材质量的关键。
衡量生产操作是否正确,除了操作程序、注意事项要符合工艺要求以外,各个操作程序中所控制的"
度"
(或程度)就靠许多工艺参数来决定。
工艺文件上规定的工艺参数在一定范围内起指导作用。
是需要在实际操作中依据理论原理结合操作者的经验和对"
的了解,经过不断实践摸索和总结才能制定。
各个工艺参数的具体数值也并非一成不变,往往需要根据不同的变化了的情况在一定范围内调整。
这些工艺参数主要有:
成型温度、螺杆转速、挤出压力、挤出速度和牵引速度、冷却定型、输料速度、功率比例、排气真空度、牵引机履带夹持力等。
下面以锥形双螺杆挤出机组成的生产线为依据,对各工艺参数分别叙述:
(1)成型温度
如上所述,要把固体颗粒的粉状模塑料变成有一定剖面形状的硬PVC型材需要加热升温,使之由80℃以下的固体颗粒的"
玻璃态"
,经过升温至160℃以下变为柔软的富有弹性的"
高弹态"
。
之后继续加温至220℃以下成为塑化了的液状熔融体,称为"
粘流态"
再从模头以型材剖面形状挤出并立即冷却变硬定形。
从玻璃态经高弹态到粘流态这一变化过程,是在挤出机的料筒和锥形双螺杆中完成的。
料筒外面分四段包围着四组电加热圈;
每组加热圈与料筒之间还缠绕着螺旋形内通循环冷却油的铜管,冷却油由外部的油泵、冷却管系统独立供应。
这样,既可加热升温也可冷却降温。
由传感器、温控表按预先设定的温度工作,以达到自动控制温度的目的。
塑料加热升温除靠料筒外的电加热圈提供热量外,塑料与料筒和螺杆之间、塑料内部分子之间的摩擦、剪切运动也会发生热量。
料筒的四组加热圈从加料口起依次分为1、2、3、4个加热区,在2、3区之间有一个排气口,上方有玻璃盖,可以观察塑料塑化情况。
排气口侧有管子通真空表、过滤器及真空泵,从塑料中分解析出的气体和水蒸汽由排气口经管子、过滤器被真空泵抽吸出去,真空表用以指示抽吸力度。
螺杆上的排气段正处于排气口的位置。
加热1、2区则分别处于螺杆的加料段和塑化压缩段。
螺杆上的均化段和挤出段(总称为计量段)处于料筒加热的3、4区。
从料筒和螺杆端挤出的塑料剖面呈"
∞"
形并且塑化良好。
把"
形的剖面形状塑料变成所需的型材剖面形状,是经由过渡段先将"
形变成圆形,经过圆形多孔板扩散,成型材轮廓,再经模头分流、成形、稳压定型逐渐完成的。
为了保持塑料温度不致影响其流动成形,必须在过渡段、进入模头前由多孔板整流、均压再经扩散段、分流段、成型、稳压段,并在这些段的外部加装电加热圈或加热板。
以使塑料从模头挤出时各处流速均匀、温度大体一致。
因此控制加热、检测温度的加热圈、加热板和温度传感器在一台挤出机及其模头上分别达到8~10个。
国外的研究证明:
硬PVC异型材最优的塑化温度是在180℃~190℃之间,低于或高于这个温度区间成型的制品,其物理机械性能和化学性能都将降低为此,对上述各区、各处的温度控制提出如下数据建议:
料筒1区:
160℃~175℃
料筒2区:
170℃~185℃
料筒3区:
料筒4区:
175℃~185℃
模具过渡段:
165℃~170℃
模头分流段:
175℃~180℃
模头上部:
180℃~195℃
模头下部:
185℃~200℃
模头两侧:
180℃~195℃(有的模头可以无侧部检测点)
说明:
a、上述工艺参数供用国产挤出机及模具的厂家参考,选用上述数据还应考虑设备性能、模具设计、制造等具体情况;
b、主原料PVC最好用SG-5型,其次为SG-4型。
c、模塑料配方中的稳定剂如为有机锡或者cd-Ba镉-钡稳定剂,宜选用上列数据中偏低的数值;
如为铅盐稳定剂宜选用偏高的数值。
d、如挤出机为平行双螺杆挤出机,宜选用上述数据中间或中间偏低的数值。
e、上列的温度数值只是温度控制表上指示的温度数值,它们是温度传感器附近金属体的温度,与塑料中心部位和螺杆上的温度是有所区别的,一般说来塑料的温度略低一些。
但在料筒3区、4区处由于锥形双螺杆与料筒的空间越来越小,塑料分子之间挤压、摩擦加剧,产生热量加大,温度有可能升高。
这时螺杆芯部中装的热管会自动将热量传到螺杆1、2区以防止3、4区温度过高。
同时温控器也会自动打开通往3、4区的冷却油管的电动阀门,让冷却油循环流动,带走热量,使温度降到规定数值。
f、判断型材成型温度是否正确的方法。
判断型材成型温度是否正确的最可靠方法是按照技术标准GB8814-98对型材成品进行检测,如果各项数值都是规定数值的最佳值,便可以确认该型材的成型温是正确的;
如果是在合格指标范围内,则只是基本正确;
如果有一项或几项超出规定范围,则可能是在成型温度上或其它问题上有不正确的地方。
但是这种判断时间滞后,所以在生产现场凭经验也可以初步判断温度是否合适:
如果成型温度合适,从模头挤出的型坯内外表面光亮细腻、颜色均匀、呈瓷白色,各剖面出料速度均匀一致,当用铜铲刀从模口铲断,型坯继续挤出40~60mm之间时,如果不用手托住,型材会因重量自然下垂(未人工牵引前);
挤出机扭矩表指示在45%~65%之间,其它仪表指示符合工艺规定,则塑化良好。
如果成型温度过高,型坯颜色就会微微泛黄;
型坯内腔表面会产生微气泡,用手指抚摩有凹凸感、不光滑,内腔中的筋、肋明显弯曲;
用铜铲刀在模口快速铲断型坯后,挤出长度不到40mm时,温度偏高就会因型坯太柔软而下垂,扭矩表指示也会下降到30%以下;
温度过低,型坯外观颜色虽白,但表面发暗而不光亮,用铜铲刀从模口铲断型坯,其断口粗糙,型坯挤出长度超过60mm以上才开始因自重而弯曲下垂,扭矩表指示会达到75%~80%甚至更多。
螺杆和料筒温度应大体一致,不能相差太多,以免塑化、出料不均匀,在铲断型坯后观察:
如果型坯中心部分出料快,就会产生断口向外扩大现象,说明螺杆温度比料筒高;
如果断口向内收缩,则相反,料筒温度偏低。
g、对不同厂家生产的挤出机,在温度设定上要注意区别对待。
使用进口挤出机和进口模具时,温度的设定往往比国产挤出机低一些,因其设计制造质量上较好,精度高、间隙小,物料产生剪切内热较多。
(2)螺杆转速
螺杆转速是根据型材的大小、形状、单位长度重(kg/m)、冷却定型台、冷却定型模和牵引机的能力综合考虑决定的。
在冷却定型台、冷却定型模及牵引机的能力得到充分利用的原则下,挤出机的螺杆转速应尽量大一些,以提高生产率。
通常挤出机的螺杆转速大都在10~35转/分的范围内调节。
螺杆转速大的好处是使塑料受到较强的剪切作用而有利于塑料的塑化、均化,从而提高塑料制品的机械性能(如抗拉强度、抗冲击强度等)。
但是螺杆转速也不能过高,过高会使塑料受到过强的剪切作用而使温度"
跑高"
,型坯会产生过大的离模膨胀而使表面质量下降;
此外,料筒内塑料流动时产生过多的漏流量和逆流;
增加了挤出机电力消耗,加快螺杆磨损而挤出量并不能得到明显提高。
另一方面螺杆转速过低也是不好的。
过低的转速度造成生产率过低,塑料得不到充分的塑化和均化,型材质量会下降。
转速低,塑料在料筒及模头中停留的时间加长,会使塑料中的稳定剂、抗冲剂等被分解、消耗的量增加,不利于型材生产后的使用寿命。
一般情况下20~25转/分的转速是可行的。
螺杆转速选定后须保持稳定,否则会造成塑料挤出量不均匀,型材的壁厚、形状都不稳定。
(3)挤出压力
模塑料在挤出机中一面被加热熔融,一面被旋转着的螺杆推动挤压流向模头并从模口被挤压出来,说明塑料内是产生着压力的。
否则就克服不了料筒、螺杆、过渡段、多孔板、模头等的重重阻碍和塑料分子间的摩擦。
各种挤出机的大小和螺杆、料筒的设计结构决定了挤出机有各种不同的工作性能和特点,各自在不同塑料温度和螺杆转速的条件下会产生不同的工作压力。
不同型材剖面有不同的模头,各自有各自流道形状、长度和塑料流过时产生的阻力和压力的变化。
当挤出机与模头结合在一起时,一定的螺杆转速就会在模头内产生相对应的压力把型坯挤出,这个压力是随螺杆转速的变化而变化的。
但压力的大小要适当。
压力越高,型坯被挤出模口时产生的膨胀发胖现象越明显,塑料容易过热,有时还会因塑料回流从排气口处"
冒料"
,压力过低,型材材质会不密实。
两种情况都不利于型材的质量,会使其机械性能尤其是抗冲击和抗拉强度下降。
通常,压力数值在过渡段测量,大致在15.5~27.5Mpa之间调节和选择。
调节压力的方法是变动螺杆转速。
(4)牵引速度与挤出速度
牵引速度是指履带牵引机夹持型材后拉动型材运动的速度,单位为m/分。
挤出速度是指每分钟从挤出机模头中挤出型坯的长度,单位也是m/分,也可换算成单位时间内从挤出机和模头中挤出的塑料重量、单位为g/分或kg/时,具体数值按型材的单长重量(g/m或kg/m)每分钟(或小时)挤出的长度而定。
两者之间的关系为:
V1/V2=1.01~1.10其中:
V1--牵引速度;
V2--挤出速度。
简单地说:
牵引速度必须略大于挤出速度,但不能大得太多。
如牵引速度小于挤出速度,会因型坯挤出后不能及时被牵引进入冷却定型模,在第一节定型套入口处发生堆积(俗称"
堵料"
),使生产无法正常进行;
理论上牵引速度等于挤出速度时生产可以连续运转,实际上两者完全相等,只能在短暂时间中发生,因为螺杆和履带的转速、塑料的温度、压力都在一定范围内波动,使两者不能长时间完全相等,再加上型坯的离模膨胀,很难避免发生"
,生产也就难以不停地连续进行。
但是牵引速度比挤出速度又不能大得太多。
因为从模口挤出的型坯是处在180℃以上的粘流态物质,进入冷却定型模要变成50℃~60℃的硬质型材再进入牵引机,在冷却定型模中型坯降温时必然要经过160℃→80℃这个区间,在此区间型坯从粘流态要转为高弹态,此时在牵引拉力的作用下型坯内部会产生拉伸应力将型材拉长。
过大的牵引速会使型材产生过高的拉伸应力,当型材冷到80℃以下成为玻璃态的固体时,就会因内部拉伸应力过大使长度方向的收缩率加大。
不但如此,型材被拉长后,还会使型材壁变薄、超差,对其机械性能也产生不利影响(主要是轴向抗拉强度有所增加(而抗冲击性能、抗变性能和径向抗拉强度降低)。
如螺杆转速提高,挤出速度和挤出量增加,牵引速度就必须随之加快,以保持两者的比例(1.01~1.10)此外,牵引速度、挤出速度也和型材大小(单重g/m)、挤出机最大挤出量(kg/h)有关。
在冷却定型模能力和挤出机挤出量范围之内,大型材的牵引速度要小一些,小型材的牵引速度可大一些。
牵引机牵引速度调节必须是无级调节,还要能长时间保持稳定,只有这样型材的质量和尺寸才能稳定。
目前国内多数厂家用国产挤出生产线设备生产框、扇类主型材时,牵引速度大多在1.2~2.8m/分之间,型材单重在800~1200g/m上下,挤出机最大挤出量一般只能达到250kg/h;
而进口同规格的挤出机可达300~400kg/h,牵引速度可达4m/分以上,但多数厂家使用实际只在2.5~3.5m/分之间。
(5)冷却定型
型坯的冷却和定型是同时进行和完成的。
但首先是定型,使型坯用真空吸附的原理贴在定型套内腔表面,型坯上的热量才能传递给定型套被吸收带走,型坯温度下降,材质逐渐变硬,外形便被固定下来。
定型的工艺参数主要是反映定型套内吸附型坯能力的真空度,可从定型台上的真空表指示出来。
第一节冷却定型套正常工作时的真空度应在-0.065~-0.085Mpa之间(相当于495mmHg~650mmHg的汞柱高)。
型材壁厚和剖面形状复杂程度不同,真空度也应有区别。
薄壁型材(≤1.5mm)比厚壁型材所需的真空度要小一些。
调节真空度的方法是:
适当打开或关小接在定型套上的真空开关,控制它吸入空气的多少,真空度便会下降或上升。
当型材壁厚在2.0~2.6mm、型材剖面形状复杂或不对称时较好的真空度为-0.08mpa左右,真空度太高,吸附力过大,对型材定型没有必要,而且还使牵引机负荷太大,有时会使造成牵引速度不均匀而产生"
真空度不能过小,如低于-0.05mpa,则有可能使型材不能完全被吸附在定型套内腔表面上,不能保证型材外形尺寸符合图纸要求。
如果经过多次调节,即使关闭定型套所有通大气的开关仍不能达到所需真空度,可以在注意不发生"
的情况下,适当降低螺杆转速和牵引速度,待真空度达到使型材完全贴合定型套、真空度提高、外形合格后再慢慢提高牵引速度和螺杆转速以达到工艺要求的速度和真空度。
当冷却定型套有2节以上时,第二节以后的各节定型套的真空度要求并不一定要和第一节的真空度一样高,可以依次略低一些,当第一节为-0.085mpa时,最末一节可以低至-0.055mpa,但不宜低到-0.04mpa以下。
冷却的工艺参数主要是冷却水的温度和供水压力。
应将水温控制在10℃~18℃之间,水压在4~6pa之间。
理想的水温是12℃~15℃。
水温过高或水压不足,不能及时冷却,会使型材变形、弯曲、成型困难;
在水温超过28℃时是难以成型连续生产的。
水温在20℃~25℃时须降低螺杆转速和牵引速度以延长冷却时间。
水温过低,会使型材脆化,产生过大的内应力,型材抗冲击性能下降。
实际生产中保持恒定水温是很困难的,水温波动与供水系统的状况有密切关系。
为了节水应使用循环水冷却。
在循环水系统中应设有冷却塔(供冬天使用)和冷水机(供夏天使用)。
此外,水的硬度不宜过大,最好在8~10dH范围,以免使设备和冷却定型套过快地结垢而频繁地分解除垢,还应经过滤再使用以免堵塞。
(6)输料速度和排气真空度
输料速度前面已作了基本叙述。
应该指出的是,输料螺杆的转速与挤出机螺杆转速的匹配,要按实际情况灵活选择。
原料是粉状模塑料,或是粉碎回收的颗料、还是粉料中掺有颗粒料,它们的匹配转速比例是有区别的。
从排气口中观察螺杆的螺槽中的物料填充螺槽和塑化情况,塑料应基本填满螺杆,没有粉料。
如果有大的间隙或螺槽没有填满,说明输料量不足;
应增加输料螺杆转速以增加供料。
否则,开动排气真空泵时,真空泵就会将空气从进料口经螺杆上的螺槽、排气口及管子吸入过滤器,真空表指示的真空度很低或不指示,因为螺槽没有被物料填满,有空隙可以通过空气。
流动的空气还会将没有塑化的粉料,颗粒料从排气口吸出进入过滤器,很快将过滤器灌满、堵死,使排气无法进行,型材挤出也无法正常进行。
如果输料螺杆转速过快,与挤出机螺杆转速比过大,虽然不会发生物料被吸入过滤器的情况,但因供料多,挤出压力高,塑料回流现象加重,多余的塑料就会从排气口被挤出"
输料螺杆的转速与挤出机螺杆转速应该以多大比例运行,主要依据不同挤出生产线设备状况、原料状况、挤出压力等,由操作者的经验判断决定。
至于排气真空度,在实际操作中控制在-0.04~0.08mpa即可。
真空太高,吸力太大,有可能增加吸出塑料小颗粒,加快过滤器的堵塞。
真空度太低,吸力不足,塑料分解析出的气体和蒸发的水蒸汽排得不彻底,残留在型材壁中的微气泡增多,不利于型材的机械性能,会降低质量。
调节排气真空度的方法是:
适当打开排气口旁一根小管子上的开关,使排气口通大气,排气泵吸入一定量的空气,真空度便会降低;
适当关小此开关,外部空气被吸入的少了,真空度就会提高。
如果完全关闭此开关真空度仍然低于-0.04mpa,则可能是真空系统中某处有漏气,应当检查、排除故障。
最有可能漏气的地方是排气口观察窗盖没盖严实;
还有可能是过滤器清理内部滤网堵塞的废料后,过滤器外壳的盖子没盖好,漏气。
这两处发生不密封的情况多一些。
(7)牵引机履带夹持力
牵引机要将模头挤出的型坯从冷却定型模中拽出来,旋转着的上下履带必须将型材夹紧才能克服型坯在冷却定型模中的摩擦阻力而不打滑,否则会因打滑使牵引速度减慢而产生"
但又不能夹得太紧,以致将型材夹变形成为不合格品。
因此,如果型材剖面的高度尺寸比进入牵引机前小,超过规定公差,应减小履带夹紧力。
上履带是装在两个摇臂上的,摇臂又连接着气压作动筒,气压作动筒可以通过气体压力调节阀将摇臂及履带向下拉,使上履带向下将型材压紧在下履带上,上、下履传动系统均速转动,上、下履带无级变速,只要夹持住不打滑,履带运动速度就是型材被牵引速度。
观察气体调压阀门后的压力表,就知道可以增加或减少上、下履带的夹持力。
当型材剖面和壁厚较大时,调节后的气压可大一些,夹紧力也随之加大;
当型材剖面较小、壁厚较薄时,夹紧力就不能太大,以防型材变形,这时应将气压调小。
由于上履带本身就有相当的重量,可以将型材压在下履带上产生一定的夹紧力,对于剖面小、壁厚簿的型材只需很小一点气压就足够了。
不同生产厂生产的牵引机结构不同,但大同小异者居多,履带夹持力所需气压的具体数值,按各厂生产的设备情况,由操作者结合该牵引机在使用中的情况进行调试,一般在0.3~2.5之间调整。
PVC门窗异型材的质量要求及质量保证应具备的条件
1、国家技术标准GB/T8814-98的要点及关键:
国家技术标准GB/T8814-1998对门窗框用硬聚氯乙烯(PVC)型材的要求作了具体规定,其要点包括:
适用范围、需引用的其它有关国家技术标准、对型材的技术要求、试验方法、检验规则、标志、包装、运输、贮存等方面。
此项技术标准对型材的质量要求,在技术标准的第三部分--技术要求中作了规定,主要内容包括:
型材的外观和颜色,型材的尺寸偏差,型材质量的偏差及12项物理机械性能的数值指标。
在生产实践中,型材质量在以下一些项目上出问题多,成为型材质量不合格的关键,它们是:
(1)外观与颜色:
型材剖面形状不完整,外表面不光滑,型腔内表面有微气泡,颜色不均匀,颜色耐久性差,变成粉红或泛黄。
(2)尺寸偏差不符合要求,尤其是一些功能尺寸,如装毛条的"
T"
形槽、装玻璃压条的槽和玻璃压条脚、装密封条的槽、拧螺钉的"
十"
字形孔等。
(3)物理机械性能的十二个项目中,出现质量问题最多的项目是低温落锤冲击、加热后尺寸变化率两项。
其次是简支梁冲击强度和耐候性。
此外,型材的焊接强度不合格,也时有发生,成为关键问题。
2、PVC门窗异型材的其它质量要