铜电解精炼冶金计算.docx
《铜电解精炼冶金计算.docx》由会员分享,可在线阅读,更多相关《铜电解精炼冶金计算.docx(14页珍藏版)》请在冰豆网上搜索。
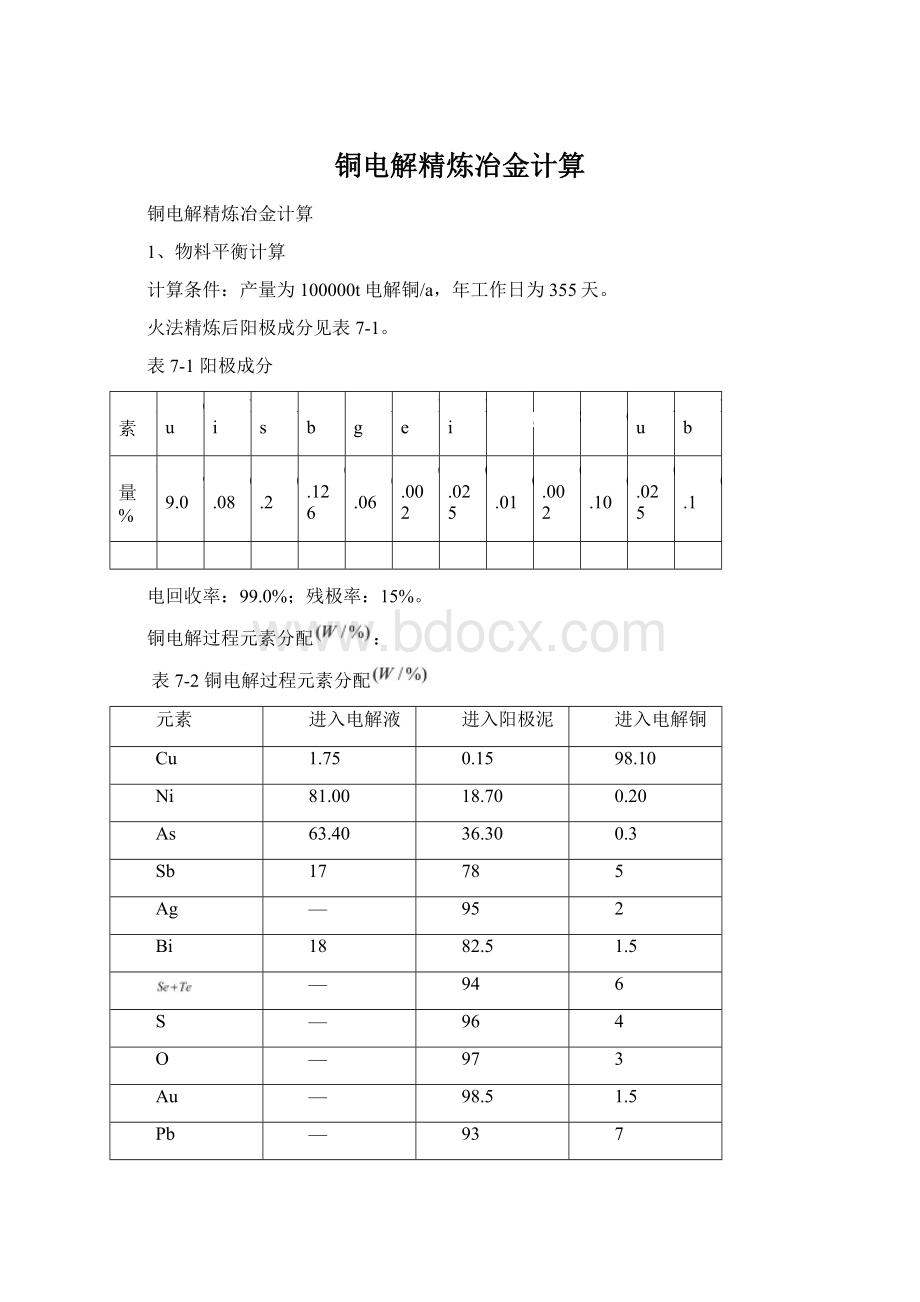
铜电解精炼冶金计算
铜电解精炼冶金计算
1、物料平衡计算
计算条件:
产量为100000t电解铜/a,年工作日为355天。
火法精炼后阳极成分见表7-1。
表7-1阳极成分
元素
Cu
Ni
As
Sb
Ag
Fe
Bi
S
O
Au
Pb
含量%
99.0
0.08
0.2
0.126
0.06
0.002
0.025
0.01
0.002
0.10
0.025
0.1
电回收率:
99.0%;残极率:
15%。
铜电解过程元素分配:
表7-2铜电解过程元素分配
元素
进入电解液
进入阳极泥
进入电解铜
Cu
1.75
0.15
98.10
Ni
81.00
18.70
0.20
As
63.40
36.30
0.3
Sb
17
78
5
Ag
—
95
2
Bi
18
82.5
1.5
—
94
6
S
—
96
4
O
—
97
3
Au
—
98.5
1.5
Pb
—
93
7
Fe
74
53
21
假设以溶解100kg的阳极铜平衡进行计算
1.1阴极铜产量和电铜品味计算
Cu:
99.0×98.1%=97.119kg
Ni:
0.08×0.2%=0.00016kg
As:
0.2×0.3%=0.0006kg
Sb:
0.126×5%=0.0063kg
Ag:
0.06×5%=0.003kg
Bi:
0.025×1.5%=0.000375kg
Se+Te:
0.01×6%=0.0006kg
Fe:
0.002×21%=0.00042kg
S:
0.002×4%=0.00008kg
O:
0.1×3%=0.003kg
Au:
0.025×1.5%=0.000375kg
Pb:
0.1×7%%=0.007kg
合计:
97.141kg
电铜品位:
97.119÷97.141=99.98%
1.2阳极泥率和成份计算
Cu:
99×0.15%=0.1485kg
Ni:
0.08×18.7%=0.1496kg
As:
0.2×36.3%=0.0726kg
Sb:
0.126×78%=0.09828kg
Ag:
0.06×95%=0.057kg
Se+Te:
0.01×94%=0.0094kg
S:
0.002×96%=0.00193kg
O:
0.1×97%=0.097kg
Au:
0.025×98.5%=0.024625kg
Pb:
0.1×93%=0.093kg
Fe:
0.002×3%=0.00006kg
合计:
0.5449kg
阳极泥率:
0.55%(对溶解阳极铜)
1.3电解物料平衡计算
(1)1t阴极铜需要溶解的阳极量
(2)阳极实际需要量
(3)阳极实际溶解的量
(4)阳极铜的含量
(5)残极量
(6)残极铜的含量
(7)阳极的泥量
(8)阳极泥含铜量:
150.5716t/a
(9)电解液中各个元素的含量:
根据阳极成分和计算的阳极泥中各元素量及其成分见表7-3
表7-3阳极泥中各元素重量级百分比
元素
进入阳极泥的量t/a
阳极泥成分,%
元素
进入阳极泥的量t/a
阳极泥成分,%
Cu
101395.073799%0.15%=150.5716
23.28
Au
101395.07370.025%98.5%=24.9685
3.86
As
101395.07370.2%36.3%=73.6128
11.37
Ag
101395.07370.06%95%=57.7951
8.93
Sb
101395.07370.126%78%=99.6510
15.46
Fe
101395.07370.002%3%=0.06170.0608
0.01
Ni
101395.07370.08%18.70%=15.1687
2.34
S
101395.07370.002%94%=1.9062
0.29
Pb
101395.07370.1%93%=94.2974
14.56
O
101395.07370.10%97%=98.3532
15
Bi
101395.07370.025%82.5%=20.9127
3.23
其它
Se+Te
101395.07370.01%94%=9.5311
1.47
共计
表7-4电解液中各元素的含量
装入
物料
名称
物料量
Cu
As
Ni
Au
Ag
t/a
%
%
%
%
%
阳极
119288.3
99.0
118095.4
0.2
238.5
0.08
95.4
0.025
29.8
0.06
71.5
合计
118095.4
238.5
95.4
29.8
71.5
产出
物料
名称
物料量
Cu
As
Ni
Au
Ag
t/a
%
%
%
%
%
电解铜
10000
99.98
99980
残极铜
17893.2
99..0
17714.3
0.2
35.78
0.08
14.3
0.025
4.47
0.06
10.73
阳极泥
557.6279
7.97
75.32
16.84
159.1
1.6
15.12
0.8
7.56
10.1
94.5
电解液
2936.25
292.97
60.66
损失及计算误差
300.5
0.04
合计
177327.6
5302
89.2
8.92
115.96
+7.3铜电解精炼热平衡计算
仪器及实验条件参数设定如下:
电解槽的外形尺寸:
5100×1265×1395;
电流强度:
10000A;
槽间电压:
0.3V;
电解槽的数量:
560;
电解槽的外壁温度:
35°C
电解车间温度:
2°C5
电解液的温度:
60°C
电解液循环速度:
20L/min(商品槽与种板槽共用一个循环系统);
7.3.1热量支出
(1)槽液面上水蒸气的热损失q1
槽的总液表面积
S=4.9×1.065×560=2922.36m2
每平方电解槽液面在无覆盖时的水分蒸发量查表得1.35kg/(m2·h).
60℃的水气化为2358.42
则q1=2922.36×1.35×2358.42=9304405.566kJ/h
(2)槽液面上对流传热与辐射损失q2
根据化工原理的傅立叶传热公式:
Q=KS(t1-t2)
式中:
—辐射与对流联合导热系数,kJ/(m2·h·℃)取39.35;
S—传热面积,㎡;
—电解液与车间空气温度差,℃。
则:
q2=39.35×(60-25)×2922.36=4024820.31kJ/h
(3)槽外壁的对流传热与辐射损失q3
槽壁总面子S总=560×(5.1×1.265+1.265×1.395×2+5.1×1.395×2)=13557.516m2
根据化工原理的傅立叶传热公式:
Q=KS(t1-t2)
式中:
—对钢筋混凝土槽壁辐射与对流联合导热系数,kJ/(m2·h·℃),当槽外壁温度为35℃,车间室温为25℃时,取35.17
则:
q3=35.17×(35-25)×13557.5
(4)循环管道溶液热损失为q4
电解液的循环量为:
(7-7)
式中:
—电解液循环量,;
—电解液热容量,KJ/(kg·℃),3.43;
—电解液密度,;
—电解液在循环管道的温度降,根据车间规模大小取2~4℃,本设计取3℃。
q416=4768178.377kJ/h
7.3.2热量收入
热量收入为电流通过电解液时所产生的热:
式中:
I—电流强度,A;
E—消耗于克服电解液阻力得到槽电压/V,为槽电压的50%左右;
N—电解槽数;
t—时间,取3600s。
则热量收入:
Q=4.18×0.239×0.3×0.5×10000×3600×560×10-3=3021036.48/h
综上热量衡算可得
整个车间需补充的额外热量为:
q1+q2+q3+q4-Q=9304405.566+4024820.31+4768178.377
+8643600-3021036.48。
表7-5电解精炼系统热量衡算
热量流入
热量流出
加热器补充的热量
电解槽外壁的辐射与对流热损失
4768178.377
电流通过电解液产生的热量
3021036.48
电解槽液面水蒸发热损失
9304405.566
电解槽液面辐射与对流热损失
4024820.31
循环管道溶液热损失
8643600
合计
26741004.257
合计
26741004.257
7.4净液量的计算
本设计铜净化的过程主要采用的流程有中和结晶、脱铜电解、电热浓缩生产粗硫酸镍。
设计规模为产量100000t/a电解铜,阳极板成分为:
Cu:
99.0%,Ni:
0.08%,As:
0.2%,Fe:
0.002%,Sb:
0.126%,Bi:
0.025%。
生产1t的电铜所溶解的阳极板量为1.0119t,在净化过程中铜、镍、砷、锑、铋和铁的脱出率分别为98%、75%、85%、85%、85%、和80%。
本设计所取有害杂质在电解液中的允许含量如下表所示:
表7-6各种有害杂质元素在电解液中的允许含量
元素
Cu
Ni
As
Fe
Bi
含量
<50
<20
<7
<0.5
<0.6
<0.5
净液量的计算公式如下:
(7-8)
式中:
m—每溶解100㎏阳极后某元素进入溶液的数量㎏;
k—元素在整个净化过程中的脱除率%;
c—元素允许的极限浓度(即允许含量)。
设计中主要元素净液量的计算分别如下:
表7-7主要元素的净液量
元素
Cu
Ni
As
Fe
Bi
净液量
35777.893
5828.544
2156.425
2936.4941
42499.8
9523.7647
根据上表可知,净液量需求最大的是铜,其次的是铋。
本设计采用在电解工序电解槽中增加不溶阳极的方法脱出,则净液量以铋的净液量为准,取为44000。
按照44000的净液量可以推算出电解液的实际含量():
由以上的计算可知,电解液的实际含量():
Bi:
0.1218、As:
3.4307、Sb:
0.5795、Cu:
40.6567、Ni:
1.9870、:
180。
7.5硫酸盐生产物料衡算
衡算的基本数据如下;
加入铜料的品位99.95%;
硫酸铜平均结晶率60%;
中和终液含铜:
120;
中和过程溶液体积缩率70%;
硫酸铜含铜24.4%;
一次结晶液体缩率81%;
铜回收率98%。
硫酸铜结晶水返回中和系统;
7.5.1需加入铜料的量
根据经验选取结晶所需的洗水成分为Cu:
40g/l,H2SO4:
50g/l。
本设计的流量取1388。
则中和过程进料成分为: