铁系锌基合金电镀Word下载.docx
《铁系锌基合金电镀Word下载.docx》由会员分享,可在线阅读,更多相关《铁系锌基合金电镀Word下载.docx(6页珍藏版)》请在冰豆网上搜索。
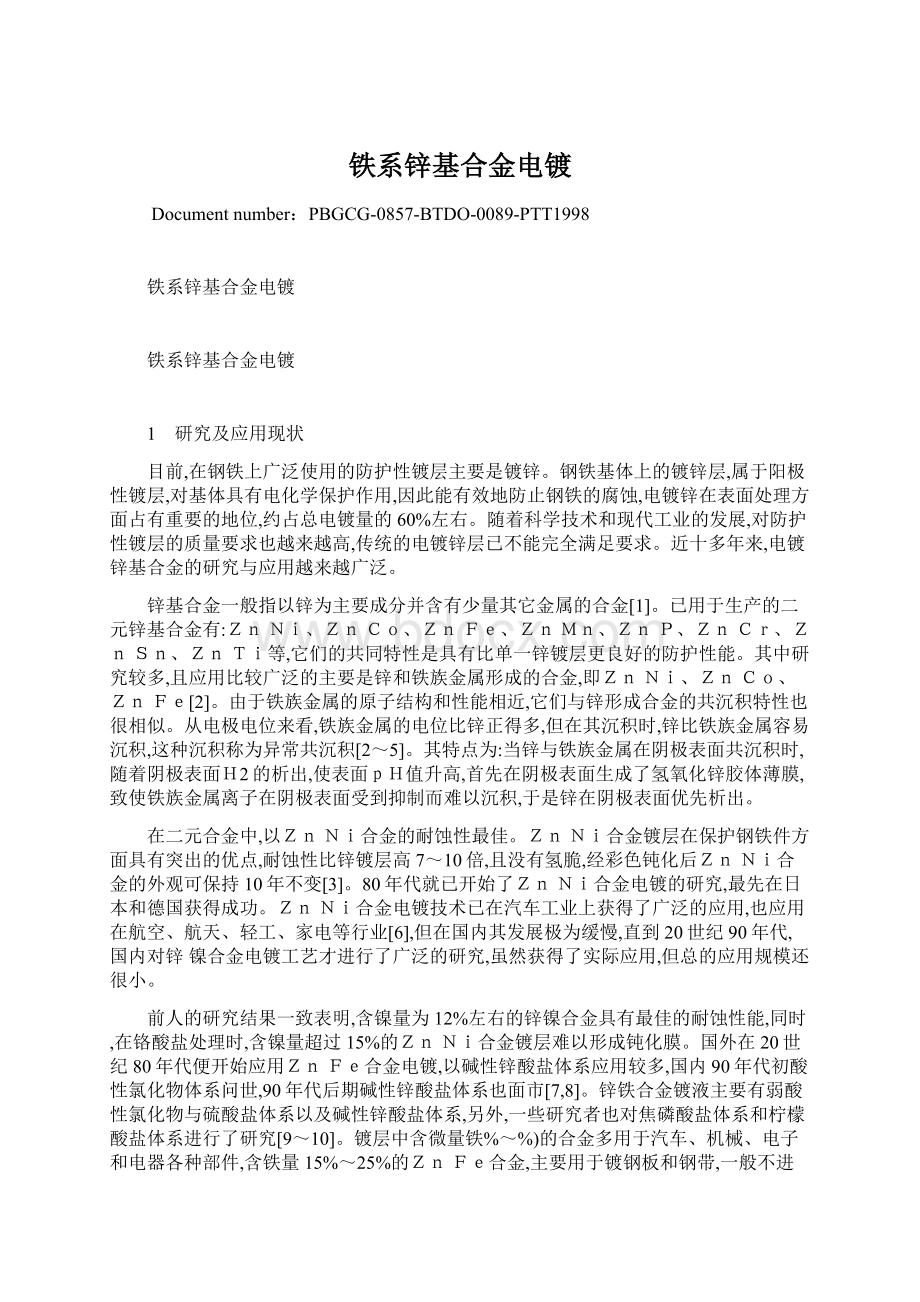
其特点为:
当锌与铁族金属在阴极表面共沉积时,随着阴极表面H2的析出,使表面pH值升高,首先在阴极表面生成了氢氧化锌胶体薄膜,致使铁族金属离子在阴极表面受到抑制而难以沉积,于是锌在阴极表面优先析出。
在二元合金中,以ZnNi合金的耐蚀性最佳。
ZnNi合金镀层在保护钢铁件方面具有突出的优点,耐蚀性比锌镀层高7~10倍,且没有氢脆,经彩色钝化后ZnNi合金的外观可保持10年不变[3]。
80年代就已开始了ZnNi合金电镀的研究,最先在日本和德国获得成功。
ZnNi合金电镀技术已在汽车工业上获得了广泛的应用,也应用在航空、航天、轻工、家电等行业[6],但在国内其发展极为缓慢,直到20世纪90年代,国内对锌镍合金电镀工艺才进行了广泛的研究,虽然获得了实际应用,但总的应用规模还很小。
前人的研究结果一致表明,含镍量为12%左右的锌镍合金具有最佳的耐蚀性能,同时,在铬酸盐处理时,含镍量超过15%的ZnNi合金镀层难以形成钝化膜。
国外在20世纪80年代便开始应用ZnFe合金电镀,以碱性锌酸盐体系应用较多,国内90年代初酸性氯化物体系问世,90年代后期碱性锌酸盐体系也面市[7,8]。
锌铁合金镀液主要有弱酸性氯化物与硫酸盐体系以及碱性锌酸盐体系,另外,一些研究者也对焦磷酸盐体系和柠檬酸盐体系进行了研究[9~10]。
镀层中含微量铁%~%)的合金多用于汽车、机械、电子和电器各种部件,含铁量15%~25%的ZnFe合金,主要用于镀钢板和钢带,一般不进行铬钝化处理。
在国内,ZnFe合金也开始应用于生产,如四川某厂采用酸性氯化物锌铁合金电镀超过两万升槽液,哈尔滨汽车制造厂采用碱性锌铁合金黑色钝化,都取得良好的经济和社会效益。
ZnCo合金电镀作为一种实用技术[11],欧洲早在20世纪60年代初就已开始了研究,镀液体系较多集中在碱性锌酸盐体系和酸性硫酸盐体系,其中,碱性锌酸盐体系研究得较少,硫酸盐体系研究得最早,由于前者电流效率不高,后者分散能力较差,而随着酸性氯化物体系镀锌工艺的成熟,酸性氯化物体系的ZnCo合金电镀逐渐受到重视,现大多应用的是氯化物体系[12]。
1982年欧洲首先将ZnCo合金(弱酸性镀液)电镀在工业上应用于汽车部件,如铸铁件、低碳钢冲压件和液压传动件(钴含量约08%左右)。
在中国,ZnCo合金电镀的研究起步较晚,进入90年代以后,才逐渐开始对ZnCo合金电镀进行研究。
近年来ZnCo合金电镀已在北京和沈阳等厂得到生产应用,效果和效益比较明显。
ZnCo合金镀层由于钴含量低,容易钝化处理,它属于阳极性镀层,对钢铁基体具有保护作用。
ZnCo合金的耐蚀性随镀层中钴含量的增加而提高,但钴含量超过1%以后,提高的幅度比较小,从经济和镀液的维护考虑,多使用钴含量为%~%的ZnCo合金。
当镀层中含钴量为%时,经钝化处理的合金镀层,其耐蚀性是镀锌层(经钝化)的3倍左右[13~15]。
在铁系锌基合金电沉积机理研究方面,目前主要有以下几种理论:
量子化学机理、欠电位沉积机理、膜吸附机理、电化学动力学机理、抑制机理、热力学机理等[16~18]。
其中,量子力学从分子水平对铁族锌基合金的异常共沉积进行了描述,从理论上预测了铁族锌基合金的耐蚀性;
热力学从热力学参数上证明铁族锌基合金的耐蚀性;
电化学动力学则从锌与铁族金属的电化学动力学参数的差别(锌的交换电流密度远大于铁族金属的交换电流密度)来说明铁族锌基合金的耐蚀性。
当然,几种机理各有优势与不足。
目前对其机理仍不完全清楚,电沉积工艺条件对电沉积机理的影响仍待进一步研究。
因此,关于铁系锌基合金电沉积机理的研究在今后仍是一个活跃的研究领域。
2 铁系锌基二元合金电镀工艺的影响
因素铁系锌基合金电镀的镀液主要由金属离子盐、添加剂、缓冲剂等组成,镀层性能受各组分含量的影响很大,同时,电镀过程中的电流密度、溶液pH值、溶液温度等的影响都有不可忽略的作用。
添加剂对铁系锌基合金镀层的影响
添加剂对ZnFe、ZnNi及ZnCo合金镀层起着至关重要的作用[19~21],它不仅可以改变电极反应的过电位,增加阴极极化,使镀层晶粒细化及改变晶粒取向,增加镀层光亮性,还可以改变镀层的内应力、延展性、硬度和其它性能。
锌基合金电镀添加剂是在纯锌电镀添加剂的基础上研制开发的,与其它电镀添加剂一样,一般由四部分组成:
主光亮剂、载体、辅助光亮剂和扩散剂。
制备方法一般可分为3种:
机械复配法、化学合成法与综合法。
目前工业或实验普遍采用后两种制备方法。
对于添加剂中成分的选择要依据合金类型,溶液酸碱性,实验条件等加以筛选。
2.1.1 添加剂种类的影响[22~26]
铁系锌基合金电镀添加剂的选择一般遵循以下原则:
所选用的系列添加剂,必须反应完全;
添加剂的分子量要适中,分子结构最好是线性结构,有较好的亲水性,以提高镀液的极化度;
添加剂的补加周期要长,镀液老化要慢;
可获得光亮的合金镀层,光亮区范围应尽可能地宽;
有机添加剂电解后,分解的产物易于处理,补加添加剂后镀液性能不受影响。
依据此原则,可以选择适当的金属离子(Zn2+、Fe2+、Ni2+、Co2+)络合剂,镀液稳定剂,光亮剂,改善电极性能的各种表面活性剂等。
络合剂的选择以金属离子种类和溶液酸碱性作适当选择,如在碱性锌酸盐体系的ZnFe合金电镀中,可供选择的络合剂有醇胺、羧基羧酸盐、多元醇、聚胺类等。
对铁系锌基合金电镀中主光亮剂的选择,在酸性镀液中,大多是酮类、饱和或不饱和芳香醛、杂环醛,如苄*丙酮、邻氯苯甲醛、对氯苄*丙酮、洋茉莉醛、茴香醛等,以上几种可以使用其中一种,也可以几种一起使用,一般来讲,几种同时使用时,若搭配恰当,效果最好。
可供选择的助光亮剂有苯甲酸钠、NNO(亚甲基二萘磺酸钠)、十二烷基苯磺酸钠等。
目前商品化的高温载体多为活性剂的酯化产物或磺化产物,如果商品载体和烷基酚聚氧乙烯醚等非离子性表面活性剂混用,效果更好。
在碱性镀液中,可选用烟酸的季胺化合物、苄基吡啶翁羧酸盐、甲氧基苯甲酸等,助光亮剂有DPEⅢ或咪唑的环氧化合物,聚乙烯亚胺及呱吩、呱啶等的环氧化合物等。
几种不同类型的光亮剂需很好配合,才能起到良好作用。
如苄*丙酮在硫酸盐锌铁镀液中的溶解性比在氯化镀锌液中还要差,只有选一种阴离子型表面活性剂作载体,光亮剂对苄*丙酮才有良好的溶解性。
添加剂用量的影响
在铁系锌基合金电镀中,在不同工艺条件下添加剂的加入量需通过实验确定出最佳值。
当添加剂的含量过高时,它在阴极表面的吸附率较高,影响金属粒子放电速度,因此镀层中镍、铁或钴的含量随着光亮剂用量的增加而下降;
当添加剂浓度较低时,金属离子的放电速度主要受化学因素的影响,光亮剂在阴极表面的吸附对Zn2+放电速度的抑制作用远大于对Fe2+、Ni2+或Co2+的抑制作用,所以随着光亮剂浓度的上升,镀层中的铁系金属含量随之增加。
由于镀层中Fe、Ni或Co的含量都有一个最佳范围,光亮剂含量过高时,其带出量多,加大了消耗,还会分解,夹杂在镀层中,使镀层发脆、起泡,影响镀层质量;
含量过低,镀层发暗,光亮度降低。
同时,添加剂的加入可使镀液中其它因素对镀层中铁系金属的含量的影响发生变化。
例如酸性锌镍合金电镀的特征是低阴极电流密度区所沉积的ZnNi合金镀层中的镍可高达百分之几十,远远高于中、高阴极电流密度区所沉积的ZnNi合金镀层中镍的含量,选择适当的添加剂,可以使电流密度对镀层镍含量的影响变小,抑制低电流密度区镍的析出,获得光亮度高的锌镍合金镀层。
欧雪梅[27]在锌镍合金电镀试验中发现,无添加剂时pH对镀层镍含量的影响比有添加剂时小得多。
这是因为镍为铁族金属,在有添加剂的情况下,当降低pH值不再提高过电位时,可能转变为对金属离子的沉积产生作用,而镍的沉积比锌的沉积更易受到影响,从而使镍含量急剧下降。
镀液中主盐浓度对电镀锌基合金镀层的影响
ZnNi合金电镀中的Zn2+/Ni2+(浓度比)
在ZnNi合金电镀中,通过改变镀液锌、镍离子浓度比可以控制镀层中锌和镍的含量比。
此外,镀液中锌、镍离子浓度比(Zn2+/Ni2+)不仅影响镀层成分,而且对镀层的外观影响甚大。
Zn2+/Ni2+过高,镀层的光亮性大大下降,甚至造成灰雾状;
反之,Zn2+/Ni2+过低,镀件的低电流密度区镀层呈现灰黑色。
据报道迄今为止用于工业生产的弱酸性电镀液中的锌、镍离子浓度比大都在~的范围内,但由于各家公司选用的添加剂、工艺条件等不同,其最佳锌、镍离子浓度比的范围也各不相同。
如,冯力群[19]在弱酸性电镀锌镍合金研究中,综合Zn2+/Ni2+对镀层镍含量、镀层光亮性、低电流密度光亮区范围以及阴极电流效率的影响基础上,确定其电镀体系的适宜Zn2+/Ni2+的范围是~;
而关兵[28]在电镀锌镍合金工艺探讨中,Zn2+/Ni2+保持在~之间时镀层中镍含量为10%~15%。
ZnFe合金电镀中主盐的浓度
目前,对弱酸性锌铁合金电镀的研究较多,其电镀体系中的Zn2+、Fe2+的含量对镀液稳定性和镀层质量有很大的影响。
在保证镀层质量的前提下,尽量采用高含量,以提高允许电流密度,提高生产率。
但含量过高,阴极极化作用减小,镀层结晶粗糙;
含量过低,允许电流密度降低,电沉积速度降低,而且镀层呈暗灰色。
Fe2+在溶液中以络离子的形式存在,若含量过高会发生水解生成Fe(OH)2沉淀,也会被氧化成Fe3+,影响镀液的稳定性。
另外,铁盐浓度决定镀层铁含量,浓度高镀层铁含量高,不仅影响镀层防护性能,还不能用常规方法钝化;
浓度过低,起不到提高镀层防护性能的作用。
试验与生产表明Zn2+、Fe2+的浓度还与铁质基体材料以及施镀方法的不同而异。
如在氯化物光亮锌铁合金电镀中[8],一般挂镀时,ZnCl2为80~100g/L、FeSO4·
7H2O为5~12g/L;
而滚镀时,ZnCl2为50~70g/L,FeSO4·
7H2O为5~12g/L。
对于碱性锌铁合金电镀工艺,随着镀液中Fe2+含量的增加,镀层中的含铁量也增加。
因此为达到较好的镀层铁含量标准,一般在低铁含量的电镀工艺中,ZnO为14~16g/L,FeSO4·
7H2O为1~15g/L或ZnO13g/L,FeCl21~2g/L。
ZnCo合金电镀中主盐浓度
在酸性氯化物ZnCo合金电镀中,锌、钴离子总浓度对镀层质量有一定影响。
当共沉积金属离子总浓度较低时,镀层光亮度较差,略泛灰白色,电镀过程中有少量氢气析出;
随着金属离子总浓度的增加,镀层逐渐变为全光亮,表面细致、光滑、平整,析氢现象大大减少,这是因为金属离子总浓度较低时,合金共沉积受浓差极化控制。
但随着金属离子总浓度的进一步增加,镀液的深镀能力和分散能力下降。
一般在酸性氯化物镀液中,共沉积金属离子控制在~mol/L较为适宜。
同时,在总浓度一定的情况下,当锌、钴离子摩尔比太小时,共沉积时阴极析氢较严重,需较多的抑氢剂才能保证镀层的光亮及光滑,而抑氢剂过高又会降低镀层中的钴含量,一般锌、钴离子的摩尔比取6∶1~4∶1较为合适。
碱性的ZnCo合金镀液具有优良的分散能力和覆盖能力,镀层光亮范围宽,适用于复杂零件的电镀,但电流效率较低。
一般ZnO~mol/L,CoSO~mol/L。
pH值的影响[27~30,3,8,12]
在弱酸性锌基合金电镀中,pH值的大小是影响电镀的一个主要因素。
当pH值过高时阴极析氢剧烈,H+消耗迅速,生成的氢氧化物吸附于电极表面形成薄膜,抑制锌沉积,铁、镍或钴沉积加快,导致镀层中铁系元素含量增加,重则溶液浑浊,沉积速度慢,镀层灰暗、粗糙、孔隙增多、结合力下降,因而镀层耐蚀性下降;
当pH值过低时,溶液酸度大,阳极溶解加快,锌盐和铁系元素盐增多,镀层中铁含量增加,影响正常钝化,同时析氢也加剧,使镀层质量欠佳,溶液不稳定。
所以在电镀过程中确定一个合适的pH值范围至关重要。
一般酸性镀锌镍合金工艺中氯化钾型的pH值在~之间,氯化钠型维持在pH=,而硫酸盐体系中pH维持在3~4之间;
酸性电镀锌铁合金工艺采用氯化钾型时,pH值维持在~之间,而氯化钠型酸性电镀锌铁合金工艺中,pH为~;
在氯化物体系中电沉积ZnCo合金,当pH值保持在~左右时,合金镀层中钴含量基本不随pH值的变化而变化。
镀液中影响pH值的因素很多。
析氢时氢消耗量大,pH值上升加快,当pH值超过上限时,镀液稳定性受到影响;
电流密度的大小决定了析氢量,也影响着pH值的上升速度,电流大,析氢多,酸度增大快,pH值自然上升;
金属离子盐也对pH值产生影响,特别是在锌铁合金电镀过程中,空气中的氧不断渗入溶液内,逐步将Fe2+氧化成Fe3+,pH值随之缓慢上升。
镀液温度的影响[26~30,12]
温度的高低也会对铁系锌基合金电镀产生重要影响。
随着镀液温度的提高,镀层中铁系金属元素含量随之明显增加。
这一变化规律可以采用Zn(OH)2成膜理论解释:
温度升高,离子运动加速,阴极附近的氢氧化锌膜减薄,从而使铁系金属离子通过氢氧化锌膜放电容易,因此随着温度的升高,镀层铁系金属含量增加。
镀液温度不仅对镀层中铁系金属元素含量影响大,而且对低电流密度光亮区范围、镀层外观都有影响。
镀层的光亮度一般随着温度提高而增加,但温度过高,允许电流密度增大,由于电流大,镀层结晶粗糙,镀层颜色又变暗。
温度的影响除要考虑镀层铁系金属含量及镀层光亮程度外,还与镀液各成分的性能密切相关,对锌镍合金电镀,一般在25~45℃范围内,而在锌铁合金电镀中,温度的选择范围一般在10~37℃以内,锌钴合金的电镀温度范围更低一些,一般在30℃以下。
电流密度的影响[8,28,21~35]
前人在ZnNi、ZnFe合金电镀实验研究中得出结论,镀层镍或铁含量随电流密度升高而降低,尤其是在电流密度较小时,锌镍合金镀层中镍含量随电流密度的增加而降低很快。
采用氢氧化锌成膜理论可以很好地解释,电镀时由于pH值的升高首先生成Zn(OH)2,而Zn(OH)2吸附在阴极表面,锌离子从氢氧化锌薄膜即可还原析出,而镍离子或铁离子则须经过氢氧化锌膜才能析出,阻力很大,从而镍离子、铁离子沉积受到抑制。
同时,当电流密度太大时,酸度(H+浓度)下降快,pH值上升,生成氢氧化物的几率上升,轻则镀层粗糙,重则高电流密度区烧焦。
因此,电镀时电流密度需严格控制在操作参数范围内。
一般这两种合金电镀中电流密度都在~A/dm2范围,依据不同的实验条件,可确定出更小的范围,上下限之间通常不超过A/dm2。
邓朝阳等在酸性氯化物ZnCo合金电镀中,得到的结论是:
阴极电流密度增大,镀层中钴含量随之增大,当电流密度大于A/dm2以后,镀层中钴含量随电流密度的继续增大已变化不大,考虑到ZnCo合金镀层中钴含量与耐蚀性的关系,选择电流密度为~A/dm2,镀层质量较好。
其它因素的影响[28,32,36~38]
铁系锌基合金电镀中的质量优劣,除了以上几方面的影响因素外,还与导电盐、缓冲剂、基底材料、电沉积时间以及镀前镀后处理都有关系。
导电盐常用的有氯化钾、氯化铵、氯化钠、硫酸钠等。
相比较,氯化钾的导电性优于其它三种,它不仅使镀液导电性好,促进镀层结晶细致,而且对锌离子,还有微弱的络合作用,有时用氯化钾和氯化铵一起做导电盐,氯化铵也能起到络合作用。
对导电盐的用量也应控制在一定的范围内。
pH值稳定,镀液相对稳定,镀层光亮度也就不受影响,这对铁系锌基合金电镀至关重要,特别在弱酸性镀液中,缓冲剂是必不可少的组分,在弱酸性铁系锌基合金电镀液中,常以H3BO3作缓冲剂,有些情况下也用柠檬酸等。
基底材料和电沉积时间对镀层结构也有很大影响,在电沉积的初始阶段,如果电流密度比较小,往往有保持基体金属晶格取向的趋势,沉积原子并入已有的点阵位置,沿着基体的晶格进行外延式生长,因此基底材料性能很重要。
随电沉积时间的延长,镀层厚度不断增加,镀层的择优生长方向会发生变化,错配程度也会增大,镀层的表面形态就会与基底有较大的差别,镀层的结晶粗大,致密程度下降,表面的气孔和其它缺陷明显增多,因此控制电沉积时间也很重要。
镀前镀后处理好坏也直接影响铁系锌基合金镀层的质量。
氧化皮、锈斑等污物去除不净,则影响镀层与基体的结合力,镀层发花发雾或斑点、脱落等。
只有加强前处理,电镀质量才有保障,后处理也是如此。
钝化与干燥是后处理中的重点,铁系锌基合金镀层钝化的难易主要取决于组成合金中另一组分的性能及含量,经钝化处理后,镀层耐蚀性可以大大提高。
当然,在铁系锌基合金电镀过程中,各个因素对镀层质量的影响不是孤立的,而是相互关联、相互牵制的。
因此在选择镀液组成和工艺条件时,要充分考虑各方面的因素,从而确定出最佳的镀液组成和工艺条件。
3 铁系锌基合金电镀的新发展
虽然铁系锌基合金镀层的耐蚀性比传统镀锌层有了明显的提高,但随着现代化工业的快速发展以及自然环境日愈恶劣的状况,许多领域对材料的耐蚀性提出了更高的要求,因此,研究者们不断寻求新的防护性合金镀层。
最近研究了不少以锌基二元合金为基础的高耐蚀性的锌基三元合金,如ZnNiP、ZnNiCo、ZnCoP、ZnNiCd和ZnFeP等[39~42],它们的耐蚀性比相应的二元合金优异得多,有的可达到10倍以上。
由于铁系锌基合金具有良好的防护性能价格比,已成为防护性合金发展的方向,所以对其镀层和工艺进行研究,对提高防护层质量、减薄镀层、节约金属、减少污染、降低成本等都具有重要意义。