穿孔机技术附件文档格式.docx
《穿孔机技术附件文档格式.docx》由会员分享,可在线阅读,更多相关《穿孔机技术附件文档格式.docx(26页珍藏版)》请在冰豆网上搜索。
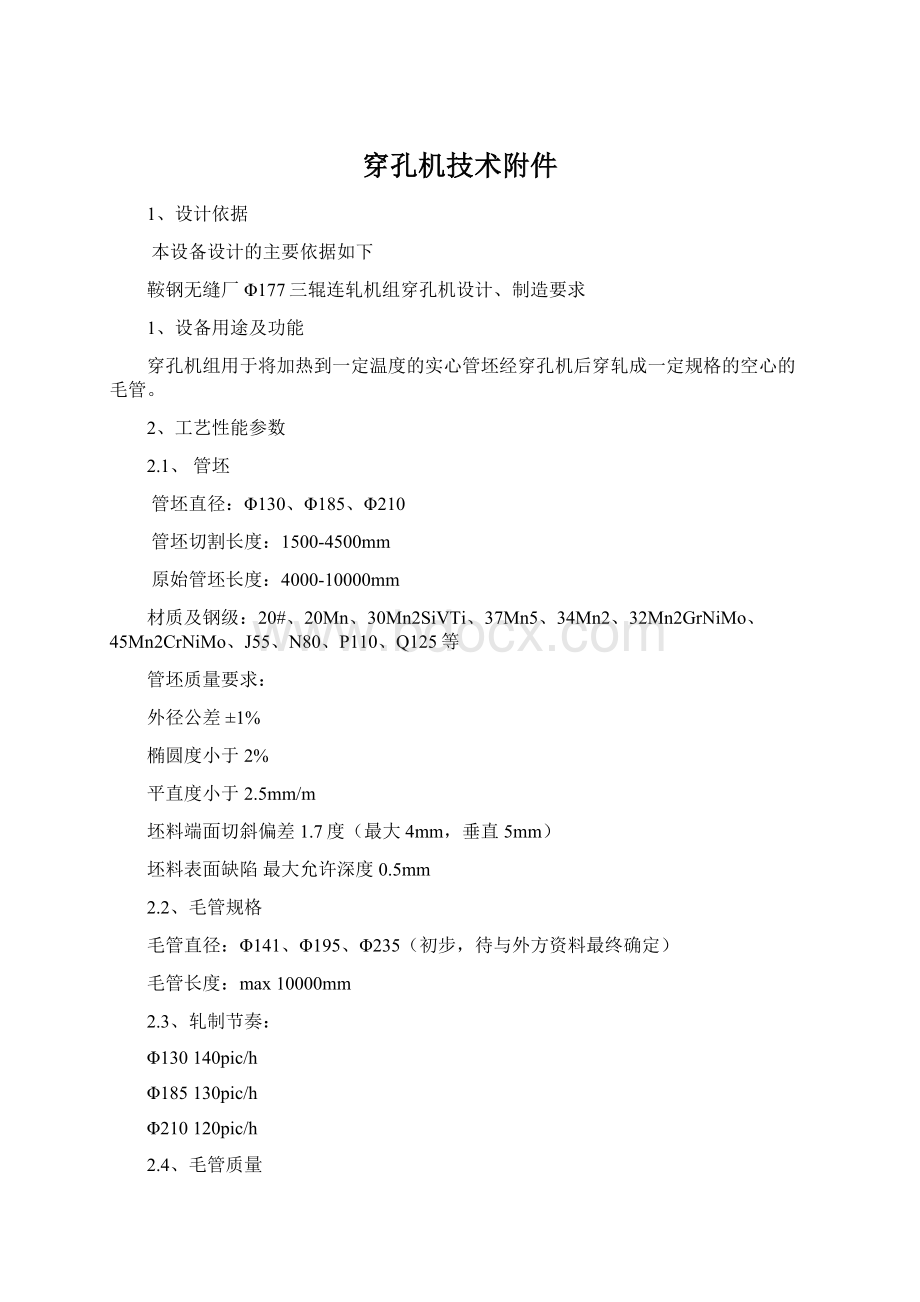
壁厚公差±
6%
毛管表面无擦伤和明显螺旋
3.机械设备技术规格说明
3.1穿孔机前上料设备
3.1.1结构功能概述:
穿孔机前上料设备将加热好的热管坯从加热炉出口运输到穿孔机进口台。
穿孔机前上料设备由以下部分组成:
●液压缸驱动的拨料钩,。
●一组斜篦条。
3.1.2技术参数:
液压缸规格(缸径/活塞杆径-行程,下同)Φ80/56-140mm
液压系统工作压力(下同)14Mpa
3.2穿孔机前运输设备:
穿孔机前运输设备包括输送辊道(主动),废料剔除设备
3.3穿孔机进口台
3.3.1结构功能概述:
穿孔机进口台是穿孔机组的重要组成部分,它接受由穿孔机前运输设备运输的热管坯,并将管坯推入主机座进行穿孔轧制。
主要由以下部分组成:
●进口导槽,接受加热后的管坯,功能为接受加热后的管坯,考虑废料剔除的方便。
进口导槽为铸钢件,装在焊接底座上,可摆动升降、液压缸锁紧,由一台电机通过换向器、万向接轴带动两台蜗轮丝杠升降机来调整高度。
●推坯机,液压缸式驱动。
功能为将管坯推入主机,辅助穿孔机咬入。
3.3.2技术参数:
调整电机功率0.55kW
锁紧缸规格Φ80/56-100mm
数量1
推坯缸规格Φ100/70-3750mm
3.4穿孔机主机座
3.4.1结构功能概述:
穿孔机主机座为实心管坯到空心毛管这一变形过程的主变形设备。
穿孔机主机座的布置形式为锥形辊立式布置,出口侧单独传动,左右导板水平布置。
其设备组成为:
●机架装置,机架装置为铸钢结构。
作用于上下轧辊的轧制力,通过上下转鼓装置,压下压上装置的压下螺丝、压下螺母传到机架装置的框架上。
机架装置的锁紧缸将上下转鼓装置无间隙地夹紧在机架里。
上轧辊装置由2个液压缸平衡,下轧辊装置由1个液压缸平衡,使得安装上轧辊的上转鼓装置紧紧压靠在压下螺丝上,安装下轧辊的下转鼓装置紧紧压靠在压上螺丝上。
●轧辊装置,轧辊装置是穿孔轧制、实现由管坯向空心毛管这一变形过程的主变形工具。
轧辊装置为互换件,分上轧辊和下轧辊,分别安装在上转鼓和下转鼓上,可以在机架装置的框架中滑动。
机组轧制中心线是固定的,通过上下轧辊的压下装置、压上装置,可以将安装在上下转鼓上的轧辊向着轧制中心线方向调整,并可通过一套数字显示系统显示轧辊的开口度(即轧辊距)。
上下轧辊分别由一套万向节轴、主减速机、主电机组成的主传动系统来驱动。
●上转鼓装置,上转鼓装置为铸钢结构,是上轧辊的支持装置,通过压下装置驱动升降,从而调节上轧辊的位置。
●下转鼓装置,下转鼓装置为铸钢结构,是下轧辊的支持装置,通过压上装置驱动升降,从而调节下轧辊的位置。
●压下装置,压下装置为电机驱动的螺旋升降结构,其主要功能是调整上轧辊的位置及轧辊距。
电机通过蜗轮减速机驱动4个压下螺丝升降,从而驱动上转鼓装置及上轧辊升降。
●压上装置,和压下装置相似,压上装置为电机驱动的螺旋升降结构,其主要功能是调整下轧辊的位置及轧辊距。
电机通过蜗轮减速机驱动4个压上螺丝升降,从而驱动下转鼓装置及下轧辊升降。
压上、压下装置的各4件压下螺丝和4套蜗轮减速机彼此之间由联轴器、及万向节轴联接,由电机驱动,集体调整。
压下装置的4根压下螺丝分别装在两个横梁上,换辊时横梁在移动缸的驱动下分别移向两边,这样就可以将转鼓装置连同轧辊装置一起从机架装置中吊出来。
工作时两个横梁上的8个锁紧缸将横梁无间隙地锁紧在机架上,组成一个封闭的框架结构,大大增加了机架的刚度。
●上送进角调整装置,上送进角调整装置的主要功能是调整上轧辊的送进角,上轧辊的送进角通过电动调整装置可以在6º
~15º
范围内无级调节,并通过一套数字显示系统显示。
●下送进角调整装置,和上送进角调整装置相似,下送进角调整装置的主要功能是调整下轧辊的送进角,下轧辊的送进角通过电动调整装置可以在6º
●左导板装置,左导板装置为旋转摆动结构,是左导板的支撑装置,导板是穿孔轧制的辅助变形工具,对变形区的金属起到良好的导卫作用。
轧制时导板由摆动液压缸摆至机架内,两个压紧缸将其压紧。
导板距离调整时,4个锁紧液压缸松开,调整电机通过升降机将导板按工艺要求调至轧制位,然后平衡锁紧。
更换时导板旋转90°
摆出,方便吊装。
导板与导板架安装采用导板凹操、导板架凸台方式。
顶头碾轧区长度至少两个螺距。
导板最高处、机械中心线、喉径中心线相对位置必须在导板处标出。
导板最小长度520—530mm。
●右导板装置和左导板装置相似,右导板装置为旋转摆动结构,是右导板的支撑装置,轧制时导板由摆动液压缸摆至机架内,两个压紧缸将其压紧。
●入口导套装置,入口导套装置为管坯咬入轧制的导卫装置,入口导套为旋转摆动结构,更换时导套旋转90°
导板及导套为更换件,随管坯的规格不同而更换。
3.4.2技术参数:
轧辊直径(喉径)Ф800~Ф1000mm
辊身长度750mm
辊形入口角16.5°
入口辊面长300mm(初步)
辊形出口角11°
轧辊转速115~120r/min(额定)
轧辊数量2
轧辊冷却方式间歇喷水冷却(自动控制)
轧制速度0.54-1.1m/s
送进角6~15°
可调
辗轧角14°
固定
轧制力max3000kN
轧制力矩max600kNm
轴向力max1200kN
压上压下电机功率15kW
转速970r/min
数量2
左、右导板调整电机功率1.1kW
转速60r/min
上、下送进角调整
功率0.55kW
轧辊压上、压下行程各200mm
左、右导板压进行程各100mm
轧辊压上、压下速度0.59~0.094mm/s
左、右导板压进速度0.5~0.08mm/s
入口导套锁紧缸规格Φ80/56-130mm
数量1
入口导套旋转缸规格Φ80/56-300mm
上轧辊平衡缸(柱塞缸)规格Φ130-210mm
数量2
下轧辊平衡缸规格Φ63/45-350mm
上转鼓锁紧缸(柱塞缸)规格Φ190-5mm
下转鼓锁紧缸(柱塞缸)规格Φ190-5mm
右导板平衡缸规格Φ80/45-120mm
数量2
右导板摆出缸规格Φ140/90-650mm
右导板锁紧缸(柱塞缸)规格Φ80-10mm
数量4
右导板压紧缸规格Φ125/90-400mm
左导板平衡缸规格Φ80/45-120mm
左导板摆出缸规格Φ140/90-650mm
左导板锁紧缸(柱塞缸)规格Φ80-10mm
左导板压紧缸规格Φ125/90-400mm
机架上盖移动缸规格Φ63/45-600mm
数量4
机架上盖锁紧缸规格Φ80/50-15mm
数量8
3.5穿孔机主传动
3.5.1结构功能概述:
穿孔机主机的上、下轧辊分别以送进角和辗轧角组成的空间角度安装,其运转的动力系统就是穿孔机主传动,穿孔机主传动的功能是驱动穿孔机轧辊实现管坯的咬入和穿孔,该系统具有支撑、伸缩万向节轴的功能,可实现快速换辊,提高生产率。
实际上穿孔机主传动分为上主传动和下主传动两部分,分别驱动上轧辊和下轧辊。
穿孔机主传动由以下部分组成:
●主电机,通过联轴器驱动主减速机。
●主减速机,通过万向接轴驱动主机座的轧辊。
●万向接轴,联结主减速机与主机座,传递扭矩。
●联轴器,联结主减速机与主机座,传递扭矩。
●上托架,上托架由底座、托臂、导向架、托槽、中间架、托臂摆动缸、导向架移动缸、导向轴等组成。
上托架为快换上轧辊的专用设备,换上轧辊时摆动缸驱动托臂绕导向轴摆动,托起万向节轴,中间架安装于托臂上,可根据需要调整其安装位置。
托槽安装在中间架上,随托臂升起直接与万向节轴的轴环配合,拉动万向节轴伸缩,导向架带动托臂由移动缸驱动实现万向节轴的伸缩运动。
换辊完毕后再由摆动缸驱动托臂回到原位。
●下托架,下托架由底座、托臂、导向架、托槽、中间架、托臂摆动缸、导向架移动缸、导向轴等组成。
下托架为快换下轧辊的专用设备,换轧辊时摆动缸驱动托臂绕导向轴摆动,托起万向节轴,中间架安装于托臂上,可根据需要调整其安装位置。
根据生产需要,在更换轧辊时,由上、下托架与主机配合,完成轧辊的快速更换。
换辊时,送进角在15º
,压上压下装置在换辊位。
●上底座,驱动上轧辊的主电机、主减速机支撑设备。
●下底座,驱动下轧辊的主电机、主减速机支撑设备。
3.5.2技术参数:
主电机功率2000KW
电压750VDC
额定转速(范围)550r/min(0~850r/min)
过载要求1.额定转速时,过载2.5倍持续时间20S后,空载10秒为一周期。
按此工况循环工作。
2.额定转速时,带1.3倍负载可连续工作。
万向接轴回转直径Ф550mm
回转点间距离9500mm
减速机速比4.8
输出扭矩370000Nm
托架摆动缸规格Φ125/70-260mm
数量2
移动缸规格Φ200/125-455mm
3.6穿孔机出口台一段
3.6.1结构功能概述:
穿孔机出口台一段与穿孔机出口台二段组合在一起,配合工作,共同完成穿孔过程。
出口台一段主要由以下部分组成:
●三辊导向装置2,三辊导向装置2由三个导向辊、一组连杆机构、一个装在摆动杠杆上的液压缸、焊接机架和一个装在机架上的液压缸等组成。
它除了具有抱紧顶杆和为毛管导向的功能外,还有一个功能就是三个导向辊中的上辊可单独抬起,以便于毛管从侧面拨出。
三辊导向装置2的三个导向辊以轧制线为中心呈圆周分布,分别通过杠杆、连杆与联动板相连,回转杠杆由一个装在机架上的液压缸(开口缸)驱动,三个导向辊随着联动板同步摆动,其中与上辊摆动杠杆相连的连杆是一个摆动液压缸(上辊缸)。
管坯穿孔前,此液压缸伸出,开口缸也伸出,通过连杆机构的作用,使三个导向辊抱紧顶杆,当穿出的毛管到达三辊导向装置2前时,开口缸缩回,三个导向辊打开到毛管导向位置,穿孔完毕,顶杆从毛管中抽出时,上辊缸缩回,与其相连的上辊抬起,使毛管从轧制线中拨出。
三辊导向装置2的开口度调整是由三辊导向定位装置实现的。
●三辊导向装置1(机内定心),三辊导向装置1的结构与三辊导向装置2相似,不同之处就是三辊导向装置1没有驱动上辊大打开的上辊缸,上辊无大打开的功能。
●三辊导向定位装置,三辊导向装置1和三辊导向装置2的开口度调整由一组可集中传动的蜗轮丝杠升降机实现,蜗轮丝杠升降机由带减速机电机驱动,万向接轴相连,同步调整。
这套机构就是三辊导向定位装置。
调节蜗轮丝杠升降机上的行程,与三辊导向装置的连杆机构上的碰块配合,便可控制三个导向辊的开口度,以适应不同管径的需要。
●输出辊道,输出辊道由1组(6个)升降辊及相应的驱动装置、夹送辊、辊道调整装置等组成。
前5个辊子均单独传动,最后一个辊子为惰辊。
为了实现管坯穿孔前辊子托顶杆、穿孔时辊子离开毛管、穿孔完毕辊子托毛管的要求,六个升降辊都装在各自的摆动杠杆上,这些摆动杠杆用拉杆串连在一起,由一个液压缸驱动,使6个辊子同步摆动升降,并能调整其摆动的高度。
第一个辊道上装有夹送辊,夹送辊由摆动马达驱动摆动,使毛管能顺利拉出。
●拨出装置,拨出装置可以将三辊导向装置1从主机内部拨出,便于换辊、维修等操作。
●拨料装置,毛管拨出装置由拨料钩、回转轴、轴承座等组成。
当毛管到达脱管位置且顶杆及顶头从毛管中抽出后,液压缸驱动拨料轴回转,拨料钩完成向轧制线侧面拨出毛荒管的操作。
●脱管装置,脱管装置是将毛管与顶杆(顶头)分离的设备,由支架和脱管模组成,脱管模为更换件,脱管模上有U形模口,其尺寸根据毛管及顶杆(顶头)规格的变化而变化,主要作用是将毛管头部挡住使毛管定位,允许顶杆(顶头)通过模口抽出。
●连接底座,连接底座由为三辊导向装置、三辊导向定位装置、输出辊道、拨料装置、脱管装置的支撑底座。
穿孔前,三辊导向装置抱紧顶杆,保证顶头位于轧制中心线上的预设定位置;
穿孔过程中,随着毛管的旋转前进,三辊导向装置逐次打开,为毛管导向,使其沿轧制线稳定前进;
穿孔结束后,毛管与顶杆分离,并且将毛管从侧面拨离轧制线。
3.6.2技术参数:
3.6.2.1三辊导向装置1
数量1套
开口度Φ55~Φ300mm
导向辊直径Φ230mm
导向辊长度390mm
开口液压缸规格Φ100(缸杆与缸头做成一体)
3.6.2.2输出辊道
辊子规格(大径/喉径-辊身长)Φ247/Φ180-250mm
辊子数量8(其中包括1个自由辊)
辊道电机功率11kW
输出转速200r/min
输出辊道升降缸1规格Φ80/56-40mm
输出辊道升降缸2规格Φ80/56-155mm
输出辊道夹送辊摆动马达
3.6.2.3三辊导向装置1拨出装置
液压缸规格Φ63/45-300mm
拨出行程350mm
3.6.2.4三辊导向装置2
数量7套
开口度Φ55~Φ300mm
导向辊直径Φ230mm
导向辊长度390mm
开口液压缸规格Φ80/56-135mm?
数量5
上辊液压缸规格Φ80/56-190mm?
3.6.2.5翻料装置(S形)
翻料采用交流电机驱动,速度要满足穿轧节奏的要求。
3.6.2.6三辊导向定位装置
减速电机功率5.5kW
输出转速100r/min
数量1
3.7穿孔机出口台二段
3.7.1结构功能概述:
出口台二段和出口台一段组合在一起,共同配合穿孔机完成管坯的穿孔,穿孔时,它使顶头、顶杆牢固地位于轧制位置,顶头位置可以根据工艺要求轴向调整,由闭锁装置双向锁紧。
出口台二段主要由以下部分组成:
●机座装置,机座装置主要由焊接机座、滑轮装配、导板等组成。
机座装置为闭锁装置、支撑车、顶杆止推小车的支撑装置,在轧制过程中,它承受由顶杆止推小车通过闭锁装置传递的轧制轴向力,并传递到基础上。
●闭锁装置,闭锁装置由锁紧装置及闭锁调整装置等组成。
锁紧装置为固定顶杆止推小车的专用设备,采用闭锁液压缸和夹紧液压缸双向锁紧,当顶杆止推小车由后位前进到设定的工作位时,闭锁液压缸和夹紧液压缸伸出,驱动闭锁杠杆和夹紧杠杆处于自锁状态,将顶杆止推小车锁定,使顶杆小车牢固地锁紧在机座装置中。
轧制结束后,闭锁液压缸和夹紧液压缸缩回,驱动闭锁杠杆和夹紧杠杆打开,使顶杆止推小车带动顶杆及顶头运行到后位。
闭锁调整装置可根据工艺要求,前后调整锁紧装配的位置,从而控制顶头前伸量。
调整由电机带动蜗轮减速机来完成,调整到位后,由两个平衡用的液压缸来消除螺纹间隙,避免顶杆止推小车在轧制过程中震动。
●顶杆止推小车,顶杆止推小车由车体、芯轴、止推轴承等组成。
止推小车由钢丝绳拖动,穿孔时,运行到闭锁位置,由闭锁装置锁紧,承受穿孔时产生的轴向力,轧制完成后,闭锁装置打开,顶杆止推小车后退,使顶杆及顶头从毛管中抽出。
顶杆内通水冷却,冷却水由止推小车尾部进入,经冷却水管与芯轴的缝隙间流出,实现循环冷却。
。
●支承车,支撑车是用来支撑Φ28钢丝绳的,由Φ14钢丝绳拖动,与顶杆止推小车同向运行,但速度约为顶杆止推小车的50%。
支撑车包括支撑车1和支撑车2。
支撑车1是用来支承顶杆的,位于顶杆止推小车前部,由Φ14钢丝绳拖动,与顶杆止推小车同向运行。
支撑车1的托辊(托顶杆)高度通过人工调整拉杆(螺纹连接)的长度实现。
支撑车2是用来支承Φ28钢丝绳的,位于顶杆止推小车后部,由Φ14钢丝绳拖动,与顶杆止推小车同向运行。
●导轨装置,导轨装置由轨道、支架及等组成。
其前端与机座装置相连,后端装在卷筒装置上,作为顶杆止推小车和支撑车的运行轨道,它可以保证上述机构快速平稳地运行。
●钢丝绳装配,钢丝绳装配由Φ28和Φ14两套钢丝绳组成,Φ28的钢丝绳驱动顶杆小车运行,而Φ14钢丝绳则驱动支承车运行,Φ14钢丝绳的运行速度约为Φ28钢丝绳的50%。
●卷筒装置,卷筒装置由底座、张紧卷筒、张紧滑轮等组成。
张紧卷筒为Φ28钢丝绳的主动端,通过传动装置驱动,张紧滑轮为Φ14钢丝绳的从动端,张紧卷筒和张紧滑轮由液压缸张紧,以保证钢丝绳有足够的拉力,保证顶杆止推小车能够高速平稳运行。
●传动装置,传动装置由电机、减速机和万向节轴等组成,为顶杆止推小车及支撑车提供动力。
●拖链装置,拖链装置为设备上有关电缆管线、流体管路的支撑设备,随小车一道运动。
3.7.2技术参数:
3.7.2.1闭锁装置
蜗轮减速机中心距200mm
速比10
减速电机功率5.5kW
转速60r/min
数量1
闭锁液压缸规格Φ63/45-225mm
夹紧液压缸规格Φ63/45-225mm
平衡用液压缸规格Φ63/45-455mm
闭锁轴向调整行程+85/-215mm
(远离穿孔机为正)
3.7.2.2顶杆止推小车
止推力max1500kN
运行速度max6m/sec
3.7.2.3卷筒装置
张紧卷筒调整距离-50/+200mm
(远离穿孔机为正)
张紧卷筒液压缸规格Φ200/125-250mm
张紧滑轮液压缸规格Φ100/70-250mm
3.7.2.4传动装置
传动电机功率240kW、DC
转数550/1000r/min
过载倍数2倍(30秒)
冷却方式IC06
防护等级F
减速机速比5
4.流体系统组成及功能描述
流体控制系统共有三部分组成:
液压系统、稀油润滑系统、干油润滑系统。
液压系统主要用来完成入口台坯料的喂入,受料槽拨料,入口导槽锁紧,主机上各执行机构的工艺动作以及出口一段三辊导向装置导向、运输辊道升降,出口台二段闭锁装置闭锁、平衡,卷筒、滑轮张紧的工艺动作要求,以实现穿孔工艺。
稀油润滑系统用于满足主传动减速机的润滑与冷却要求。
干油集中润滑系统是向穿孔机组各润滑点供送润滑脂。
根据设备润滑点的分布及润滑制度的不同,选用两套干油润滑系统(长、短周期各一套)。
4.1 液压系统
4.1.1液压系统性能参数
工作压力14MPa
公称流量360L/min
油箱容量2500L
工作油泵130ml/r26MPa(3台,1台备用)
油泵电机55kW1500rpm(3台,1台备用)
循环油泵203L/min1台
循环油泵电机7.5kW1500r/min1台
加热器9kW1套
冷却器冷却面积14m21套
主回油过滤器660L/min20um
循环过滤器330L/min10um
工作油温15-60℃
工作介质L-HM46抗磨液压油
4.1.2液压系统组成
液压系统分为两部分:
液压泵站及液压控制阀台。
液压泵站包括:
液压油箱组件、循环过滤冷却装置、油泵电机装置、调压阀组及回油过滤器装置。
液压油箱:
公称容积2500L,包括空气滤清器、液位液温计、液位控制继电器、电子温度继电器等油箱附件。
循环过滤冷却装置:
包括双螺杆泵装置(203L/min1.0MPa7.5kW1500r/min)、管路加热器、板式冷却器、循环回油过滤器等。
调压阀组:
包括电磁溢流阀、单向阀、压力表等。
液压阀台包括:
蓄能器组件、插装阀组、电磁换向阀、双单向节流阀、溢流阀、单向阀、液压锁及电子压力继电器等。
4.1.3液压系统元件的选型
液压系统设计的好坏直接关系到主机设备是否能正常运行,而高质量的元件又是液压系统质量和可靠性的重要保证。
为此在此设计中对关键的元件选用了进口元件,并充分考虑了元件的互换性。
油泵选用VICKERS。
液压阀选用Rexroth、VICKERS,发讯元件如电子压力开关,温度开关选用HYDAC产品,液压附件、管路附件选用国内优质产品。
4.2稀油润滑系统
稀油润滑系统包括上辊主传动稀油润滑系统和下辊主传动稀油润滑系统。
4.2.1上辊\下辊主传动稀油润滑系统性能参数
工作压力0.63MPa
公称流量260L/min
工作油泵276L/min(2台,1台备用)
工作电机7.5kW1500r/min(2台,1台备用)
油箱容量5000L
电加热器30kW220VAC
换热面积20m2
过滤器过滤面积0.52m2精度0.08mm
工作油温35~45℃
工作介质重负荷工业齿轮油N320
4.2.2稀油润滑系统组成
稀油系统分为两部分:
稀油润滑泵站、润滑管路。
稀油泵站包括:
油箱、油泵(双螺杆泵)装置、双筒过滤器、冷却器、仪表盘、流量指示器、阀门等。
润滑管路包括:
钢管、管夹、管路附件组成;
回油管按3:
100的坡度安装。
上辊主传动润滑系统和下辊主传动润滑系统相同,各一套。
4.3干油集中润滑系统
4.3.1干油润滑系统参数
干油润滑泵7L/h(120mL/min)
Pmax40MPa0.75kW
贮油桶容积60L
二位四通换向阀220VAC40W
压差开关Umax500VImax15A
润滑点数
润滑周期依润滑制度而定
适用润滑剂针入度不低于220润滑脂
4.3.2干油润滑系统组成
干油润滑系统包括以下三部分:
长周期干油润滑系统、短周期干油润滑系统以及干油集中润滑系统管道及其附件。