钻井平台工艺DOCWord格式文档下载.docx
《钻井平台工艺DOCWord格式文档下载.docx》由会员分享,可在线阅读,更多相关《钻井平台工艺DOCWord格式文档下载.docx(16页珍藏版)》请在冰豆网上搜索。
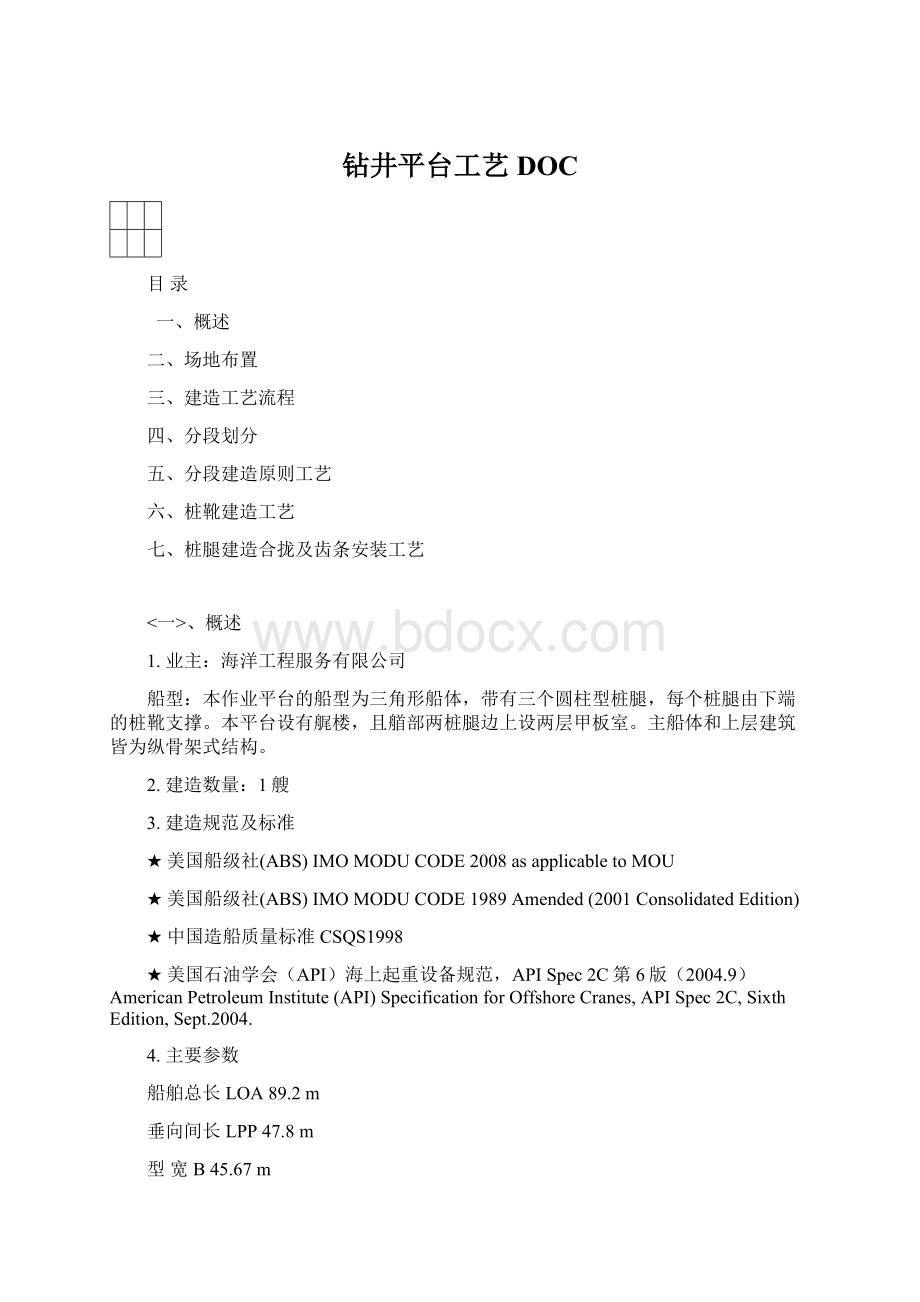
二>
、场地布置
平台分段在分段场地上制作,桩腿与桩靴就在船台300吨龙门吊下进行合拢。
三>
、主要建造流程
根据公司的设备设施条件,对该船按分段模块式制作,在分段上完成预舾装和完整性涂装,在水平船台上合拢主船体。
主要建造流程如下:
生产设计→钢材订货→钢材预处理→数控切割→材料配套→小组装→中组装→大组装→分段预舾装→分段密性试验→分段涂装→分段舾装→船台合拢→船台舾装(含吊机安装)→合拢桩靴和桩腿下部2个分段→X光拍片→舱室密性交验→涂装→下水→合拢桩腿上部3个分段→系泊试验→升降试验→倾斜试验→航行试验→交船。
四>
、分段划分
1.船体分段划分原则:
1)最大板幅控制在:
3m×
12m,单张钢板重量控制在10吨以下;
分段纵向长度不超过12m;
2)分段结构重量控制在160t以内,加上舾装重量,分段总吊装重量控制在180t以内;
船台总组重量控制在270t以内。
3)考虑公司分段涂装厂房的大门尺寸:
宽×
高=29m×
12m;
规定:
分段尺寸长×
高不大于12m×
18m×
8.5m;
4)尽量考虑机舱区分段预舾装的完整性。
5)根据分段结构特点,考虑分段建造及翻身运输的工艺性。
6)考虑板材的利用率;
2.分段划分
1)上甲板以下自艉至艏分30个分段
2)生活楼共有10个分段
3)甲板上围井共有3个分段
4)3个桩靴各为独立分段
5)3个桩腿共分为15个分段
五>
、分段建造原则工艺
一、说明:
在总体建造方案确定的分段划分及建造原则基础上,细化分段结构和预舾装施工要领。
二、全船区域划分:
2.1按照“壳、舾、涂”一体化建造方式,船体建造过程中综合考虑机、电安装及预舾装。
2.2全船区域划分:
全船共划分45个分段,其中包括主船体30个,上层建筑15个。
三、在区域化生产设计的基础上,进行区域化生产和管理:
船体工程按照建造流程划分成下料加工、组件(拼板、部件、组合件)装焊、立体分段装焊、总段组装、区域合拢、船台合拢六个中间产品生产阶段,通过各个中间产品的成组制造提高配套和完整性,确保生产安全、施工质量,提高生产效率。
舾装工程与船体工程的各个阶段对应,分别进行分段预舾装、区域舾装(含单元舾装)、船台舾装和码头舾装。
涂装工程对应船体建造的各个阶段分别进行预处理涂装、分段涂装、船台涂装和码头涂装。
舾装阶段与船体制造相对应:
阶段
船体工程内容
舾装工程内容
涂装阶段
1
下料加工
自制舾装件制造
表面预处理
2
组件装焊
舾装单元内场组装
3
立体分段装焊
分段预舾装
分段涂装
4
总段组装、区域合拢
区域舾装
5
船台
船台舾装
船台涂装
6
(下水)
码头舾装和系泊试验
码头涂装
7
(试航交船)
装饰涂装
四、建造工艺流程:
原材料进厂预处理切割下料小组立中组立
大组立并舾装总组立并舾装船台大合拢下水
涂装涂装涂装
交船海上试验码头调试
五、船体分段制作:
将船体分段作为中间产品,严格按生产流程组织生产。
5.1分段施工要领
--主体结构在横向、纵向上的每个肋骨间距加焊接补偿量,垂向上的焊接收缩补偿量加在每个水平合拢口上。
--分段精度检验:
按分段精度检验图表要求检验每个立体段外形尺寸,尤其是合拢口尺寸。
对每个分段外形尺寸检验数据做好记录,按照相关标准验收。
--分段预舾装要求:
分段上需预装管子或管子单元、铁舾装件(人孔、梯子、带缆桩、导缆孔等)、设备或设备单元等分段预舾装率:
铁舾装件(人孔、梯子、踏步、锌块)为90%,管子为80%,电装60%。
--设备进舱方案:
根据设备到货时间,并结合各分段施工计划,在分段上或船台合拢阶段将设备安装到位;
因到货时间无法保证须在结构上开临时工艺孔进舱的部分设备,要通过专业协调,预先拿出设备进舱方案,经厂内各部门统一讨论并提交船东、现场验船师同意后,方可实施。
5.2钢材预处理:
板材、型材在下料之前经预处理流水线喷丸除锈达Sa2.5级,并涂车间保护底漆。
5.3下料切割:
采用等离子切割机、火焰数控切割机、多头平行切割机等自动切割设备。
5.4板材、型材加工:
-板材应用压力机进行初步弯曲成型,再采用水火弯板方法加工成型。
-型材弯曲采用肋骨冷弯机加工成型。
-型材上的流水孔、过焊孔切割时要用靠模或仿形切割机,且需对流水孔、过焊孔进行打磨倒角。
5.5小组装:
在车间内,将板材零件和型材零件组焊成小片。
5.6拼板:
采用双面埋弧自动焊进行拼板。
5.7中组装:
在车间内将零件及小组装部件装焊在拼焊后的板上。
5.8大组装即立体分段制作。
5.9分段预舾装:
在分段上把铁舾装件焊接完成。
六、船体分段建造工艺
船体的平面分段和立体分段的小合拢都在水平船台一侧的车间内和1#码头内侧的装配场地上完成。
曲率较复杂的首尾分段结构,将利用胎架建造,以保证成形精度。
平面分段将以船底、舱壁、甲板、上层建筑围壁甲板等作为基准进行建造,每个平面分段的重量控制在100吨以下。
完成后的平面分段,用液压平板车输送到装配场地合拢成立体分段。
每个立体分段重量控制在不大于270吨范围内。
最后把这些立体分段再运送到船台合拢成前后大分段。
用于组装的分段尽量构成立体形状,以增加刚性。
必要时将安装保证刚性的临时构件。
以保证从装配场地运送到合拢场地,以及在合拢吊装中,能够比较容易控制其变形。
平面分段和立体分段的建造顺序,将按照模块场地的大分段合拢计划安排。
并且尽可能将部分平面分段在车间进一步装配成小立体分段后(如纵横舱壁与船底、纵横舱壁与舷侧结构等),再送到装配场地合拢成大的立体分段,以便于运送和利于分段的变形控制和减少装配时间。
七、典型分段装备要领:
1、概述
根据基本结构图、典型横剖面图、分段划分图,一般分段包含了上甲板、舷侧、内底、船底等结构。
分段将划分成上甲板分片、舷侧分片、船底分片3个分片,每个分片单独小组、中组,最后3个分片组立成完整分段。
2、工艺要求
2.1拼板时以肋骨检验线、板端部对合线为准,误差≤1mm。
2.2纵骨、纵桁以对合线为准安装,误差≤1mm。
2.3中组立时分段主尺度、构件垂直度、甲板平整度、围壁平整度等符合Q/CMHI001-2008《船舶建造质量标准》。
2.4大组立时分段四周内外底板垂直度和内、外纵骨垂直度,误差≤3mm。
2.5分段两端面平面度误差≤4mm,极限≤8mm。
2.6纵向构件以对合线为准,误差≤1mm。
3、分片装备顺序
3.1上甲板分片装备顺序
上甲板板拼板→安装纵骨→安装强横梁→安装上甲板纵桁→添加平台支撑→安装上平台→安装纵壁
3.2舷侧分片顺序
舷侧板拼板→安装舷侧纵骨→安装舷侧强肋骨→安装舷侧纵桁
3.3船底分片装备顺序
内底板拼板→安装内底纵骨→安装肋板→安装纵桁→安装船底纵骨→铺上船底板→翻身
分段装备顺序
船底分片→支柱、平台临时支撑→上甲板分片→舷侧分片→散装零件、肘板
八、余量与焊接补偿的加放:
1、补偿量
考虑到船体零部件在焊接等施工过程中产生的收缩变形,造成板材变短而要求板材下料时加放一定的量,称为补偿量。
2、由于本平台在板材普遍较薄,因材在纵、横、垂向构件均根据角焊缝数量增放补偿量,本补偿量在分段工作图不体现,标示仅为标准数据,具体补偿数据将体现在板材放线图中。
3、下附表CO2角焊缝补偿量原则:
根据以上补偿原则,如本船中大部分7mm纵向构件纵向间距为1200mm,则增加补偿量后长度为1200.3。
在围阱区局部范围内由于角焊缝间距变为400mm,则增加补偿量后为400.3mm,即肋骨间距变为1200.9mm。
数控下料零件由于带有自动喷粉,补偿量自动添加,放线图中不体现;
手工下料零件图纸中会增加包含补偿量的放线图。
六>
、桩靴建造工艺
一、概述:
(本平台3个桩靴结构完全一样。
)本平台桩靴为正四边形,长宽均为11.7m,高1.5m。
设置16道四周辐射板、若干横隔板。
所有外板、辐射板和横隔板材质均为ABS-DH36AH36,折角处多采用圆弧过渡。
二、建造:
1、根据桩靴结构特点,整个桩靴以甲板片为基准反造型式预制成上下5个中组单元和若干合拢分片。
七>
、桩腿建造合拢及齿条安装工艺
一、概述
本文件作为平台的《建造方针》及《船体建造施工要领》在船体专业方面的细化补充,主要统筹和协调本平台的桩腿建造阶段制作环节相关工作的工艺文件。
本工艺仅对桩腿分段制作与安装进行描述,焊接工艺及涂装工艺另见相关文件。
质检部门、生产部门应按本方案的要求,制定出各个建造阶段的现场工艺,对桩腿的尺寸精度进行检测,并对结果进行跟踪汇总。
主要程序有:
1.焊缝编号及检验程序
2.材料跟踪程序
3.齿条、桩腿材料来料检验程序
4.各种胎架精度检验程序
5.各个阶段桩腿尺寸检验程序
6.焊接顺序的控制程序
7.焊接过程中的焊接预热、层间温度、焊后保温控制程序
本工艺文件的主要参考图纸或文件如下:
a.桩腿结构图
b.建造技术规格书
c.建造方针
d.全船分段划分图
e.全船分段搭载顺序图
本平台设有三条圆柱型桩腿,其上附有齿条,每条桩腿由下端带有小段圆筒的桩靴支撑,尺寸为11.7x11.7x1.5米,每条桩腿的高度约为91.44米,重量约为443吨。
桩腿圆筒尺寸外径2800mm,壁厚40/45/50/55/60mm,材料为ABSEQ43。
(一)主要参数
桩腿结构参数
桩腿总高(含桩靴)~101.44米
桩腿高度~98.94米
桩腿直径Φ2.800米
水平构件间距1800毫米
(二)桩腿结构特点
为全钢质圆筒型焊接结构,圆筒内部设有环形框架和环形水密隔板,圆筒外部设有一组对称齿条。
除圆筒和内部加强筋(与齿条相对应)材料为ABSEQ43外,次要附件所用材料主要为AH36、DH36级钢。
材料的化学成份和机械性能均须满足ABS或CCS规范的有关技术条件的规定,施工中若有材料代用,则须满足规范要求并取得船东、船检及设计部门的同意;
船用钢材到厂必须核对材质证件并进行外观质量检查。
(三)分段划分及分段建造方式
1、分段划分
根据船厂的起重和运输能力以及场地条件,并结合桩腿材料及齿条的订货情况,将桩腿划分为5个合拢分段。
2、桩腿分段建造方式
桩腿分段的建造方式为侧造。
3、桩腿与齿条分段编号
定义:
桩腿合拢状态的5条桩腿分段称为大分段;
组成大分段的分段称为小分段;
由若干(2到3)小分段对接的过程称为小组立;
由小组立再对接成大分段的过程称为中组立;
由大分段合拢的过程称为大组立。
为了反映该材料在整个桩腿上的位置,便于对材料进行跟踪,每条桩腿圆筒、齿条、内部加强筋以及焊缝的编号都是唯一的。
材料到货时按如下的规则进行编号,登记入库。
a.桩腿编号
||--------P:
船首左舷桩腿;
S-船首右舷桩腿;
C-船尾中部桩腿
|-------分段名如601/602/603/604/605
b.齿条编号
R-XXXX-X–X
|||-数字:
1,2,3,4,5…依次为各段齿条从下而上的顺序号
|||-字母:
C为嵌补段
||----字母:
P为左舷方向;
S为右舷方向
|-----见桩腿编号说明
焊缝的编号见质检部门的NDT焊缝检验文件。
(四)建造流程
桩腿建造流程按如下进行:
(五)建造遵循的规范和标准
建造质量按以下有关标准与准则执行:
1.ABSMODURULE
2.ABS钢质海船入级与建造规范
3.海上移动平台入级与建造规范
4.中国造船质量标准CB/T4000-2005
5.A.W.SD1.12004
6.材料与焊接规范
二、桩腿建造
(一)桩腿有关材料的来料检验
检验内容包括下面几个方面:
1、证书检验
证书包括船级社认可的材料证明、焊材测试证书、尺寸检测报告、NDT报告和热处理报告等,各种证书、报告等应满足船级社以及船东的要求。
2.表面检验
齿条表面不允许有飞溅和焊渣等缺陷。
3.编号、检查线及各种标记应清晰、齐全。
每一段桩腿与齿条的编号都是唯一的,它反映了该材料在整个桩腿上的位置,并且便于对材料进行跟踪。
4.尺寸检验
1)齿条在出厂前,需要供货方按照齿条订货技术协议的要求进行检验,检验项目应包含齿条精度要求,并在交货时出具船东认可的检验报告。
2)齿条来料后,建造方的检验部门需对来料进行检验,主要是检查齿条的主尺度、挠度、水平度及齿间距等是否满足精度要求。
对检查结果记录到检查表格当中,对超差部分,应进行处理并记录,检查表格应由质量管理部门统一管理。
3)检测方法
齿距的检测可以用专用的滑尺沿PITCHLINE线进行;
齿板宽度可以用直角尺沿PITCHLINE线和齿条端部中心线进行;
齿条长度检测可以用量尺沿PITCHLINE线进行;
齿切口垂直度需要沿PITCHLINE线进行;
平面度和拱高检测可以用激光经纬仪进行,平面度的检测基准为PITCHLINE线,拱高的检测基准为齿顶或PITCHLINE线。
5.重量检验
1)桩腿的重量检验是该产品重量控制的重要环节,按桩腿的重量检验分为两部分进行,第一部分为齿条来料重量检验,用专用磅秤进行;
第二部分为桩腿分段重量检验。
2)检测原则是普通检验,即对每一根来料的齿条的重量进行检验,并做好记录。
对每个桩腿分段的重量进行检验,并做好记录。
最后对记录进行汇总,作为桩腿重量控制的依据。
6.齿条的涂装
由于来料没有油漆保护,所以在齿条的来料检验及相关划线工作完毕后,需要运送到涂装厂房进行喷砂和涂漆工作。
在喷砂和涂漆之前,需要对齿条上的一些标记划线进行有效的保护。
详见相关的涂装工艺文件。
(二)建造过程中所需的主要工装与设备仪器
1.三锟非对称卷板机
2.滚轮托架、施工支撑架、固定胎架等
3.激光经纬仪、无损探伤设备、测温枪、测量表、拉力器、桩腿内外靠板等
4.吊装工装、预合拢工装、杠杆螺旋拉紧器、正反丝扣推撑器、对接微调工装等
5.焊条烘箱、焊机、工具箱及焊接所需要的相关耗材与设备
6.焊条、电热片、保温设备记录(温度感应器)、打磨机、碳棒等
7.钢丝绳、线锤、透明塑料软管等
8.挡风雨棚
(三)桩腿的建造
1、桩腿的制作顺序及焊接要求:
1)桩腿划线
桩腿来料按照工艺要求,进行预处理,按照实模试验得出的数据下料,划线(坡口位置),加工横向坡口,坡口按焊接工艺卡进行加工;
纵向坡口先只加工内部坡口,外部坡口待卷板完成后进行加工,坡口形式见下图所示。
坡口加工采用数控火焰切割,切割时必须留边1-2毫米,然后打磨至划线要求位置。
卷板之后,划出圆周八等分线(8条纵向线,用于测直径、直线度)、纵向两等分线(3条环向线,用于测椭圆度)。
2)钢板卷制
利用三锟非对称式卷板机进行小分段圆筒卷制,按照桩腿的制作精度要求进行检验。
3)下面以小分段制作为例进行说明。
将滚轮托架置于地面上铺设的轨道上,调节每组滚轮托架之间的间距(每个主动轮与被动轮合为一组),支撑一段桩腿小分段。
4)桩腿卷制完毕后,将三个小分段分别吊至滚轮托架,检测纵缝之间的间距是否符合焊接工艺要求,利用内外靠板进行检测椭圆度,利用激光经纬仪检测直线度。
对于纵缝间距超差的桩腿应采用紧固设备加以约束以满足焊接工艺要求,见纵缝抱紧工装。
然后将桩腿纵向焊缝置于270O的位置上,调节主动轮与被动轮托架,利用激光经纬仪使小分段的中心轴与地面划线相平行,利用埋弧自动焊机进行内部纵向焊接,焊接完毕,分别将小分段旋转180O,进行外部焊缝清根,再进行外部纵向焊接。
等到焊缝温度缓慢降至常温,72小时后再进行NDT探伤并打磨外焊接余高至0.5mm,然后检测直线度及椭圆度。
其他小分段类似制作。
利用滚轮托架下面的滑轨调整小分段间距,调节主动轮与被动轮托架,利用激光经纬仪使各小分段的中心线共轴且与地面划线相平行,利用对接微调工装将小分段进行对接点焊定位,再检测其直线度,然后进行间断加固焊,检测直线度。
等到焊缝温度降至常温,72小时后再进行NDT探伤并打磨外焊接余高至0.5mm。
其他分段类似进行制作。
将预制好的纵向加强筋定位于小分段内270O位置(此时纵向焊缝位于135O位置),进行间断加固焊。
利用滚轮托架翻身180O,定位另一侧的纵向加强筋,然后全面施焊。
再翻身,对已加固的纵向加强筋进行全面施焊。
验焊完毕,安装环向筋板,直至完成该小分段内部的结构安装。
将制作好的小组立分段进行中组立对接,同样每段小组立分段下面有一组主动轮和被动轮支撑(90吨),即通过调整滚轮托架下面的滑轨来支撑小组立分段,对接过程同小组立类似。
焊接完毕后,进行桩腿直线度的检验。
5)考虑到桩腿材料的特殊性,任何在桩腿上的焊接必须严格按照桩腿焊接工艺进行,包括引弧板、熄弧板的烧焊,定位焊等。
焊接时应时刻注意环境影响,做好防风措施。
未经船东与船级社同意,不可以随意在桩腿上烧焊。
6)桩腿小分段对接时,应注意各小分段的纵向焊缝相互错开180O(自桩腿下端开始依次交错布置至桩腿顶端)。
7)桩腿、齿条的编号和安装顺序详见齿条安装详图。
8)桩腿中组立完成后,进行桩腿大分段整体测量测绘,并记录。
9)桩腿内纵向加强筋的预制
加强筋预先根据设计的长度在场地专用胎架上组合接长,按焊接工艺要求进行施焊。
加强筋的形式为两块25x305mm与一块38x165mm的面板组合件,组合件的制作在专门的胎架上制作。
齿条对接也在此胎架上进行。
10)安装内部隔板及其他附件
隔板的安装应从中间往两侧安装,格栅和菱形的加强隔板可以采用散件进行安装,5片水密隔板可以采用如右侧方法将隔板分成3块,在桩腿内部定位后拼装,水密隔板在下料时可以使隔板的直径比桩腿内径小3毫米,这样可以使水密隔板顺利地装配。
同时预制内部的冲桩管线,直梯等附件。
11)桩腿各大分段合拢口400mm范围内如无桩腿环形结构,则应在桩腿合拢口端内缘200~250mm设置临时内部环形结构支撑,有利于控制各桩腿大分段合拢端口的圆度精度,待桩腿分段合拢焊接后拆除。
13)分段预合拢,将做好的四段合拢分段吊运到预合拢场地,在固定胎架上进行整体预合拢。
预合拢的工装如下图所示。
在桩腿整体预合拢结束后,做分段最终测量、数据记录并交验,测量过程应严格按照尺寸检验程序及桩腿建造精度要求进行。
14)齿条与桩腿的焊接
齿条预先根据设计的长度在场地胎架上接长,按焊接工艺要求进行施焊,焊后打磨。
桩腿预合拢完毕,进行齿条定位划线(齿条中心线及板厚线),以及前后对称齿条在高度上的定位线。
然后拆开四大合拢分段,按照齿条焊接工艺进行焊接。
考虑到桩腿材料与齿条材料的不一致,在分段对接时焊接收缩量不同,应在焊评时对收缩量作详细记录,以便作为桩腿合拢齿条安装时的参数之一。
15)焊接
所有的焊接必须严格按照要求进行施焊。
16)分段涂装
中组立分段完成后,必须对四大合拢分段进行涂装,涂装应按照相关的涂装工艺进行。
17)分段重量检测
分段重量检测应按照重量控制程序进行。
2、桩腿制作精度要求
桩腿整体的直线度及椭圆度等精度要求均基于
船级社和船东认可的基本设计文件。
椭圆度公差:
+/-3mm;
直线度公差:
+/-3mm/10m;
桩腿周长公差:
+/-6mm
齿条安装垂直度公差:
齿条对正公差:
180o+/-0.05o
3、分段施工质量控制要点
1)桩腿小分段圆筒卷制精度,保证桩腿小分段的椭圆度与直线度满足船东与船级社要求。
2)卷制后的纵焊对接口左右200mm范围内圆弧线应光顺。
3)桩腿小分段对接的安装定位,保证小分段的直线度满足船东与船级社要求。
4)桩腿中组立对接的安装定位,保证桩腿中组立的直线度满足船东与船级社要求。
5)齿条的装配精度,焊接变形的控制。
6)注意焊接次序及焊角大小的控制,防止焊接变形。
7)前后对称齿条的安装定位偏差的控制
8)每个工序完成后都要进行尺寸检验。
4、桩腿制作过程应关注的要点
必须考虑应急电源,以防突然断电,断电后应立即启动应急电源,使加热片能够按焊接保温要求缓慢冷却。
三、桩腿之间的预合拢
1.预合拢胎架制作
地面划胎架位置线,确定桩腿胎架中心线、水平高度基准线、按照桩腿分段图将桩腿小分段上下接口位置线及桩腿外径轮廓线投影到地面上做永久标记。
胎架的设置要牢固,每1.8米设有一道胎架,胎架与地面、胎架与胎架之间均要设置支撑或拉撑并交验。
支胎架时应当注意两边的胎架与对接缝的距离应约为0.8米,便于桩腿大分段预合拢时有足够的空间进行安装合拢工装,见桩腿胎架与工装图。
2.由于桩腿的直径、中心直线度、齿条直线度等精度公差要求较高,因此,应将建造完成的桩腿5大分段,在胎架上按次序串联衔接摆放,注意每个对接口处的纵向焊缝的位置。
分段预合拢前的总体测量测绘,做好有关数据的记录。
桩腿分段上下合拢口100mm的位置划好检验线并做标记,为下一步的搭载合拢做好准备,另外在桩腿上应做好分段号及上下、左右、首尾等方向性标记,以示区分和识别方便。
制作与安装四个大分段的合拢工装,工装详细安装图见桩腿胎架与工装图,桩腿预合拢的同时,须对每个步骤的进行测量,确保整条桩腿的直线度控制在要求范围之内。
预合拢报验合格之后,利用激光经纬仪进行齿条定位划线工作,应以齿条板的板厚中心线和水平中心线进行齿条左右和水平定位,划出齿条板厚两侧的定位线。
所有划线工作完成之后,拆开桩腿四大合拢分段,将桩腿在胎架上移开,使每段桩腿间距约为2米,进行齿条焊接,注意每段齿条的编号在桩腿上的位置。
焊接时严格按照焊接工艺