大颗粒小颗粒尿素质量比较文档格式.docx
《大颗粒小颗粒尿素质量比较文档格式.docx》由会员分享,可在线阅读,更多相关《大颗粒小颗粒尿素质量比较文档格式.docx(20页珍藏版)》请在冰豆网上搜索。
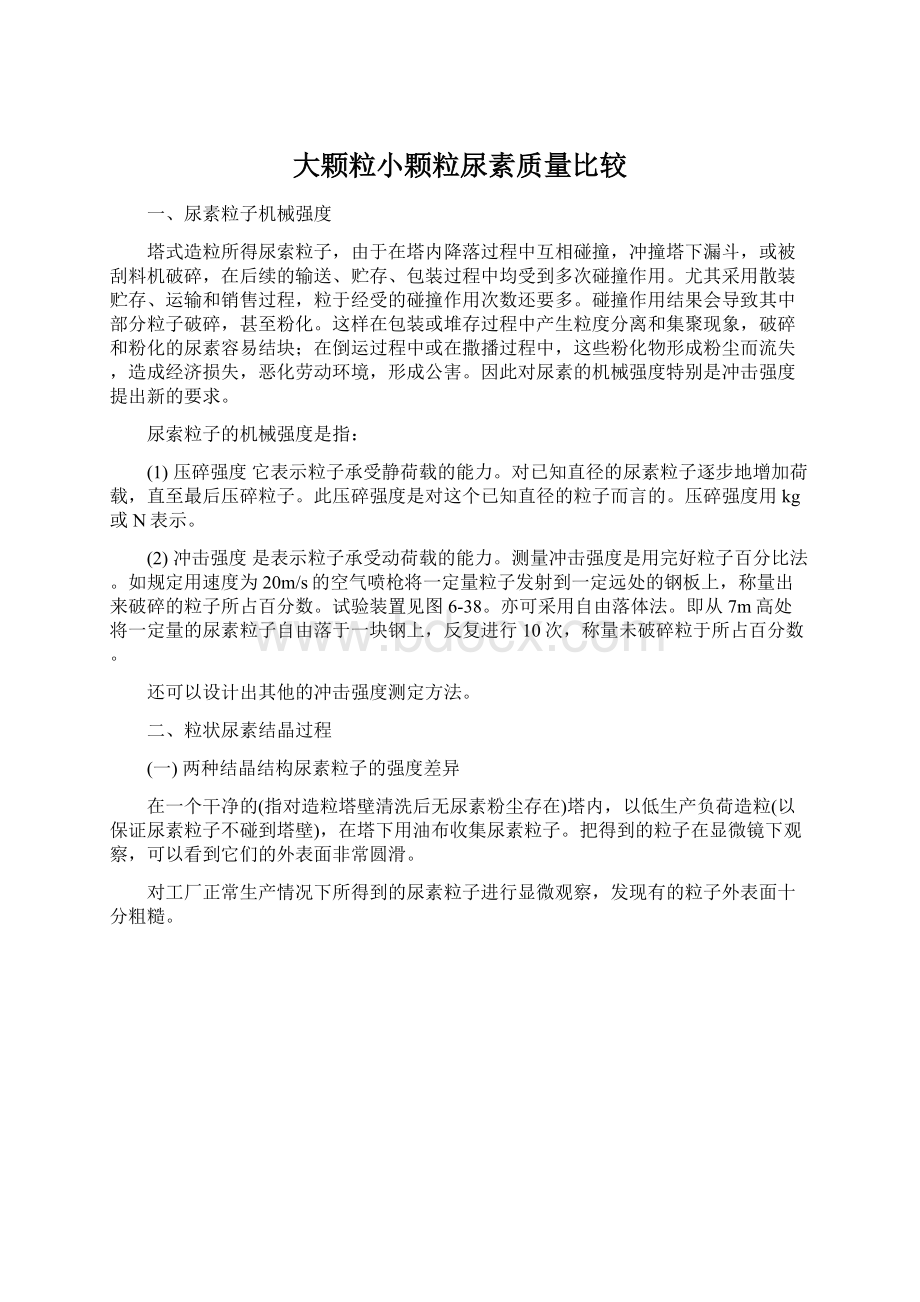
试验编号
冲击强度
有结晶种子
无结晶种子
1
57
34
4
55
20
2
62
52
5
60
13
3
42
11
6
80
14
(二)尿素粒子内部结构
对圆滑尿素粒子剖开放在显微镜下观察,发现结晶方向是一致的。
观察粗糙粒子剖面,发现其结晶是无方向性的。
(三)粒状尿素的结晶过程
在模拟造粒塔的操作条件下(空气呈滞流),在玻璃管中做实验。
将熔融尿素从玻璃管顶部滴下,与空气逆流接触,用高速摄影法拍摄液滴降落过程,可以看出:
当空气中没有微小的尿素粉尘作为结晶种子时,熔融尿素在降落时要经过4至6秒钟才开始结晶,估计过冷30℃~50℃。
当向空气中添加一些微小的尿素粉尘作为结晶种子时,熔融尿素在自由降落一开始就结晶。
用X射线分析结晶晶体,发现表面圆滑的尿素粒子内部呈单晶结构,碰撞时容易破碎;
而表面粗糙的尿素粒子内部结构呈夹层交错状态,冲击强度高。
三、晶种造粒系统流程
品种造粒流程见图6-39。
固体尿素和防结块剂一硬脂酸钙分别加入混合机3,经过充分搅拌混合,由蝶阀控制加入贮斗6,再经定量给料机(螺旋式)7将尿素和硬脂酸钙送入空气磨8,在压缩空气的冲动下,固体尿素颗粒相互摩擦而粉化成2.5~8μm的晶种,再经空气喷射器9把这些晶种输送到造粒塔的中部,分4个口喷入塔内。
亦可从塔下百叶窗进风口处吹入晶种。
加硬脂酸钙是为了增加晶种系统中的尿素粉尘的流动性,加入量为3%~5%(体积),加得太多不经济。
加得太少,可能引起加晶种系统的设备和管路堵塞。
尿素粉尘的用量为8~20kg/h(对直径20m造粒塔而言),粉尘量太少.不能提供足够量的晶核,太多则不经挤。
尿素粉尘的尺寸应当有90%以上是大于2.5μm的。
如果大于2.5μm的粉尘量大少,则粉尘微粒与下落的尿素液滴之间的碰撞机会较少,这样最终产品的冲击强度较低。
对生产能力为65~75t/h的尿素造粒塔而言,晶种系统尿素粉尘喷射器所需空气量为180~220m3(标)/h,空气量少,系统堵塞的危险性就高。
空气磨用气约100m3(标)/h。
空气进入空气磨8和喷射器9之前要预热到60~80℃。
四、加晶种的必要性
在正常条件下,造粒过程自身产生的尿素粉尘(尿素粒子相互碰撞,冲击塔下漏斗、地面,或被刮料机破碎等)随着进塔空气而向上流动,起到了晶种作用。
但是当大气中水蒸汽分压增高时,这些数量有限的粉尘在塔下部被溶解到固体尿素表面溶液中,而到达不了塔的上部,此时由于缺乏足够数量的晶种,会导致某些液滴的过冷现象而产生粘结和结块现象,以及尿素粒子冲击强度低。
因此在中国南方多雨地区.如采用加晶种措施会收到较好的的效果。
由于加晶种所得粒子内部结构呈夹层交错紧密状态,在造粒塔内降落过程中.水的溶解速度慢(即在尿素吸湿过程时)。
与不加晶种相比,出塔尿素含水量可降低0.05%。
图6-39晶种造粒流程[18]
1-贮斗;
2-加料斗;
3-混合机;
4-电机;
5-蝶阀;
6-贮斗;
7-给料机;
8-空气磨;
9-喷射器
第四节流化床造粒
一、国外流化床造粒工艺
现代广泛使用的流化床造粒工艺有:
挪威海德鲁(Hydro)法;
荷兰斯太米卡邦(Stamicarbon)法;
日本东洋工程公司(TEC)喷射流化床法。
图6-40是典型的流化床造粒工艺流程图。
图6-40典型的流化床造粒工艺流程图
1-熔融尿素给料泵;
2-造粒机上箱体;
3-造粒机下箱体;
4-造粒喷嘴;
5-流化(多孔)板;
6-鼓风机;
7-喷射(或雾化)空气加热器;
8-流化空气加热器;
9-后流化冷却器;
10-斗式提升机;
11-多层振动筛;
12-产品冷却器;
13-液氨蒸发制冷器;
14-产品冷却鼓风机;
15-产品计量和输送;
16-粉尘洗涤塔;
17-洗涤塔循环泵;
18-40~45%浓度尿素溶液送蒸发系统;
19-补充清洗水;
20-洗涤塔引风机;
21-烟囱;
22-甲醛-尿素溶液制备系统;
23-破碎机;
24-集液管;
S-中压蒸汽;
SC-蒸汽冷凝液;
LA-液氨;
GA-气氨;
LS-低压蒸汽。
流化床造粒工艺由下列四部分系统组成:
--造粒部分
--循环和产品冷却过程
--除尘和回收部分
--甲醛尿素系统
(一)造粒系统
造粒系统核心设备是造粒机,由上箱体2和下箱体3组成。
上箱体上部空间悬挂不锈钢丝网防止顶部结块尿素脱落砸坏造粒喷嘴4和多孔板5,下箱体顶面是流化(多孔)板5和造粒喷嘴4,集液管24。
先向多孔板加入细小粒子作为晶种,然后从多孔板下方通入加热空气使之形成流化床。
埋在流化床层中喷嘴将浓度95~97%的熔融尿素喷入流化床,熔融尿素被包围在喷嘴周围的热空气雾化为极细的雾滴粘附在晶种粒子的表面上,经过一定时间这些尿素晶种便长大到规定的尺寸,在造粒机内部后冷却床被冷空气从110~120℃冷却到90℃送到循环系统。
流化造粒床和流化冷却床可以合在一起,也可以分成两个设备。
(二)循环和产品冷却部分
1、循环系统
循环系统主要由多层振动筛11和破碎机23所组成。
常用三层式振动筛,尿素颗粒筛分为四种规格尺寸
--结块尿素
--超大颗粒
--产品颗粒
--小颗粒
(1)筛顶出来的结块尿素送到溶解单元,制成40~50%尿液送回尿素蒸发系统。
(2)超大颗粒来自中层筛,送至破碎机破碎成晶种返回造粒机流化床。
(3)出底筛下面的细小颗粒也返回造粒机流化床。
(4)来自底筛的合格产品尿素送到产品冷却器12,用冷冻空气(除去空气中的水分)将产品由90℃冷却到60℃左右,经过计量送去贮存和包装。
2、产品冷却系统
从图6-2曲线Ⅱ知道流化床成粒法尿素颗粒表面水蒸气压力是很低的,用普通的不加除湿的空气去冷却,则颗粒尿素表面处于吸水状态,将增加颗粒结块性。
在湿度大的天气条件下,采用氨冷除湿是合理的。
为了节能,改气-固冷却法为固-固水冷却法也是可取的。
(三)除尘和回收部分
由于流化床造粒,流化冷却床,产品冷却和固体颗粒破碎和输送过程均产生大量尿素粉尘。
为防止粉尘外泄,上述各处均在负压下运行。
集尘管系与粉尘洗涤塔16相连。
16下部为填料段,用循环尿液进行洗涤,在中部和上部分设丝网除雾层,用补充清水喷洒洗涤,出洗涤塔顶气相含尿素粉尘符合设计要求,一般为30mg/Nm3。
根据当地环保排尘量的要求来决定洗涤塔内件设计。
粉尘洗涤塔有多中型式:
除立式塔外还有卧式洗涤塔;
除填料式外还有无填料空塔洗涤塔。
大量粉尘经过洗涤后得以回收。
循环洗涤尿素溶液浓度约增浓到40~50%(重量),抽出一部分送回上游尿素蒸发工序。
回收量约为产品的4%。
粉尘中还有较多的游离NH3:
它来自熔融尿素的溶解NH3,输送和造粒过程中缩二脲生成和尿素水解而释放的NH3,甲醛-尿素携带的NH3,在洗涤塔内仅以尿素-水溶液无法加以吸收。
如果环保有严格的NH3排放要求,需要在洗涤塔顶部增加酸洗段,可以用硫酸或硝酸来吸收NH3。
生成(NH4)SO4或NH4NO3。
(四).甲醛-尿素系统
由于尿素和甲醛可以生成单羟基甲醛尿素,然后再与尿素发生聚合反应生成聚亚甲醛尿素,从而提高了尿素产品的强度。
制取单羟基甲醛尿素有如下三种方法:
1、直接法
直接法就是把商品级甲醛水溶液用计量泵加入到熔融尿素泵入口,经泵送至塔式造粒或机械造粒,要求逗留时间不大于30秒钟。
直接法的优点是工艺过程简单,运行无结晶和堵塞。
但是存在诸多缺点不能忽视,主要缺点是:
(1)单羟基甲醛尿素生成是放热反应,该热量在熔融尿素泵进出口管系中无法除去,因此处于平衡状态,反应不能进行到底,因此对提高尿素产品硬度有一定影响。
例如,某厂流化床造粒原使用直接法添加甲醛溶液,抗破碎强度约为22.4~28.1N,改用UF45添加剂后,抗破碎强度提高到了36.4~37.9N[20],强度提高了47%。
(2)由于上述原因,游离甲醛会释放至大气(塔式造粒)或进入工艺水系统(机械造粒的粉尘回收溶液返回上游蒸发冷凝系统),并残留于最终尿素产品,最后进入土壤和水体,这种对环境影响尤待评估。
2、UF制备
(1)UF作为商品,通常名为UF85,组份为U:
F:
H2O=64:
21:
15(重量)。
UF85制备是在UF85工厂进行,然后用保温车辆送到用户。
UF85制备路线是:
商品尿素+商品甲醛溶液+苛性碱(如NaOH,KOH等)在反应釜内加热保温,并停留足够时间。
在碱性条件下生成单羟基甲醛尿素和二羟基甲醛尿素,经过浓缩和精制除去杂质和有害物,制得UF85商品。
(2)UF45
UF85作为商品,价格高,不利于长途运输和较长时间贮存。
往往用户自己根据需要制备UF稀溶液,例如UF45等,UF45组份为U:
H2O=12.5:
32:
55.5(重量),并含有少量游离NH3,在70~90℃下送入熔融尿素泵口,该方法的优点是浓度低,在输送过程中不发生结晶堵塞。
类似UF45制备方法,可以衍生出多种规格的UF稀溶液。
稀的UF溶液中含有比较多的游离NH3,在造粒和回收过程对环境会有影响。
UF稀溶液含有大量水分,对造粒过程和产品尿素强度是不利的。
(3)MMU[21]
MMU是单羟基尿素(Monomethylolurea)的缩写。
MMU生产工艺是TEC的专利技术。
此特点是MMU的制备附属于流化造粒装置。
做到就地使用甲醛和尿素生产添加剂,用于成粒或造粒工艺。
MMU生产工艺的主要优点是:
①甲醛和尿素在合成塔进行约30分钟长时间的预反应,做到出合成塔物料中无游离甲醛,从而保证了生产过程,粉尘回收,最终产品都没有游离甲醛,对环境无甲醛污染。
②由于MMU预反应的完全性,在送入熔融尿素泵入口和泵出口管线中只需要很短的时间即可完成单羟基甲醛尿素聚合反应生成聚亚甲醛尿素,亚甲醛二脲,分散在整个熔融尿素体系中,起到增加最终尿素产品强度的作用。
③由于在线生产和使用MMU,其成本大大低于昂贵的UF85成本,所得到的产品强度两者是相同的。
其实MMU的组分U:
15(重量),与UF85相一致,只是生产过程不一样。
MMU溶液浓度高,在使用过程中存在易结晶堵塞的现象;
MMU工艺中需用液NH3,调节溶液的碱度,加入NH3最后送入粉尘洗涤塔再经烟囱排入大气,对环境不利。
国家标准规定农业用尿素含甲醛(HCHO)≤0.6%[22]
二、国内开发的流化床造粒工艺
天津大学化工学院造粒工程技术中心在多个喷动单元的喷动流化造粒器专利技术基础上开发的大颗粒尿素生产工艺可望逐步实现全部国产化[23]。
国外各种流化床造粒工艺的核心技术在于喷嘴。
国内在引进技术设备分交中,除了下箱体之外,所有设备均可在中国境内制造。
唯独下箱体由技术出售方供货。
秘密之处在于下箱体中喷嘴是核心秘密技术。
天津大学已开发出单喷嘴产量达到350kg/h,达到了工业化生产水平。
喷动流化床造粒工艺有如下特点:
(一)采用特殊结构的雾化喷嘴和喷动流化床,尿素颗粒在流化床内呈现有规律的上下环流运动,所得产品具有球形度好,颗粒均匀,返料量小。
(二)特殊的气体分布板(即多孔板或流化板)结构可以防止过大颗粒在流化床内累积,有利于流化床的连续稳定操作,生产周期长。
(三)全部设备均可实现国产化,装置投资可大幅降低。
第五节双转鼓流化床技术(DDG)
由北京达立科公司和清华大学双方共同开发的双转鼓流化床造粒专利技术已经实现了产业化。
建成投产了近20套装置。
目前最大单机能力为150Kt/a。
流称框图见图6-41
图6-41双转鼓流化床技术[24]
双转鼓是指转鼓造粒和转鼓产品冷却。
双转鼓流化床技术由4个实用新型专利组成:
尿素转鼓造粒装置ZL98249040.2;
尿素转鼓冷却装置ZL98250394.6;
净化含尿素粉尘气体的方法ZL99121906.6;
大颗粒尿素组合转鼓造粒工艺及设备ZL99122286.5。
ZL98249040.2的技术核心是在转鼓内加入小型流化床。
产品粒径2~6mm,强度高,过程耗气量低于流化床,粉尘少,能耗低。
ZL98250394.6的技术核心是引入循环水列管式冷却器和板式冷却器,实现直接风冷和间接水冷,把90℃左右的尿素颗粒冷却到50~60℃。
ZL99121906.6的技术核心是把转鼓造粒和转鼓冷却所产生的尿素粉尘用引风机送入在线造粒塔。
对在线造粒塔而言,送入的尿素粉尘相当于第三节的晶钟造粒所需要的晶钟,提高塔式造粒尿素产品的强度;
对DDG而言,尿素粉尘得到一定程度的净化。
该技术使用有局限性。
ZL99121906.6的核心内容是一种组合工艺和设备工艺参数的要求。
确定了如果没有在线造粒塔,则把尿素粉尘送往粉尘洗涤塔。
第六节旋转成粒法[27]
1983年山特维克(Sandvik)开发了旋转成型工艺,采用一步法把液态或熔融态产物转变成均匀的高质量物锭(半球形固体),该方法具有速度快,效率高和较大的灵活性。
该法具有多种用途,如硫磺,制蜡,松香,食品和精细化工。
在世界范围内已经有1500多台旋转成型机。
它也可以用于熔融尿素造粒。
其过程原理见图6-42;
6-43;
6-44。
图6-42旋转成粒机示意图
1-旋转成粒机;
2-钢带冷却器;
3-出口刮刀;
4-水槽
图6-42是旋转成粒机示意图。
熔融尿素经泵送入旋转成粒机1,在下端经过小孔滴向特制的不锈钢输送带2,2的底侧用冷却水喷射,移走熔融尿素的冷却和结晶热。
熔融物在钢带表面快速地成锭,即半球形或球台形固体颗粒,当固体温度降至50~60℃时到达终端,由刮刀把颗粒从钢带上刮下来。
直接就地包装或经胶带输送至散装仓库。
图6-43旋转成粒机功能示意图
1-计量;
2-旋转机壳;
3-蒸汽管;
4-熔融尿素室
在图6-43中,旋转机壳2圆周速度与钢带冷却器的速度同步,保证熔融尿素滴下来不变形,形成一个适宜的形状。
蒸汽进出管3维持温度,防止熔融尿素结晶堵塞。
计量栏1起计量控制液滴的流出作用。
图6-44产品冷却示意图
图6-44是图6-42的断面图,上层钢带的背(底)面与水接触,起到冷却作用。
水与钢带之间有密封。
水不会溅到钢带顶面与成粒接触,所以颗粒尿素始终保持干燥状态。
旋转造粒特点:
一.尿素产品质量高
1.粒度分布均匀,直径3~4mm占99%;
2.平均压碎强度高达56N±
20N;
3.冲击强度高,碎粒率仅有0.49%;
4.在后处理过程摩擦系数低,产生粉尘很少;
5.缩二脲含量<
1%;
6.不需要添加甲醛。
二.环境效益
1.非直接传热,产品和冷却剂不直接接触;
2.不需要空气净化处理;
3.污染低,空气中粉尘量<
5mg/m3;
NH3<
50mg/m3(取决于熔融尿素中的氨含量)。
三.系统效率
1.一步法完成液态到固态过程;
2.过程单一,只需要最少的设备;
3.不需要专用的空气洗涤;
4.不需要筛分;
6.无需大量冷却;
7.能够控制好冷却时间,有效地完成结晶化。
四.生产灵活性
1.高的产品产量的弹性,用并联配置成粒机组,现有成粒机组生产能力为120t/d.台;
机组宽度5m,长度25m;
2.可以快速改变局部操作,无需停产,也不改变产品质量;
3.工厂开车和停车快速。
五.经济效益
1.在欧洲市场初始投资费用低于竞争对手,一台能力120t/d旋转成粒机组价格约100万欧元(注:
编者:
类似成粒机国内进行过研制,实现工业化后,价格会大幅下降);
2.电耗很低,吨尿素耗电4kwh;
3.不需要化学剂,如甲醛;
4.安装费用低;
5.不需要特殊地基,可直接位于地面。
第七节产品贮运
随着市场经挤的发展,“施用效率”(指尿素施向农田时的结块性和粉尘性对工作效率的影响)对产品尿素的销售产生直接影响日趋显著。
经常出现用户不买本地区的尿素,而买外地价高质优尿素的事例。
尿素从生产到最后施于土壤为止的这一段时间里,必然要贮存,或者是袋装贮存或者是散装贮存。
贮存时间长短不一,少则几周,长则1年或更久。
在贮存期间,尿素或者是完全疏松(可以自由流动),或者虽然有少量结块,但只要稍加处理就可以恢复原来自由的流动状态。
但是,尿素在贮存期间过度结块,在运输过程中的粉化问题经常出现,必须予以解决,提高“施用效率”,增强产品竞争能力。
一、产品贮存
尿素贮存结块的原因是尿素颗粒间晶体的结晶键增长引起的,贮存期间晶体有所发展,颗粒状尿素或粉化状尿素晶粒交互生长导致结块。
影响尿素结块的原因和对策:
(一)含水量的影响
1.袋装贮存
尿素包装在采用不透水的袋子里,保护得很好,不受外界水分的影响,但还是经常出现结块现象。
其原因是尿素在蒸发造粒时所含有的水分引起的。
此水分是“游离水”,是以溶液状态存在于尿素颗粒表面,这对贮存期间的结块有很大影响。
因此要求尿素含水量尽量地低,一般含水量≤0.3%(质量)。
尿素采用的包装袋应以牢固、不透水为前提。
2.散装贮存
尿素散装贮存时,因尿素自身所含水分导致料堆内部严重结块;
因吸收外界空气中的湿气水分,料堆表面会潮湿和结块,散装贮存时间长了以后,料堆表面的水分可以向内部渗透,引起较严重的结块。
为了防止尿素在大气中运输、包装或散装贮存过程中吸湿,需采取下列处理办法:
①根据传质过程分析,提高尿素出塔温度,使得颗粒尿索表面水蒸汽分压大于环境空气中的水蒸汽分压;
②胶带输送栈桥建筑结构物要密闭,尽量减少透气性;
③包装厂房采取空气除湿措施,即将一定量空气经过降温除湿(或化学法吸收水分),再加热至室温后送入包装厂房,这种正压送入干燥空气方法,可防止尿素在包装过程中的吸湿或结块(干燥空气送入贮斗或料斗等处)}
④散装仓库应尽量减少漏风,同时敷设加热库内空气用的蒸汽管道(或加热器等)以提高库内空气温度,降低空气相对湿度;
⑤散装仓库内建筑物表面要干燥,不得漏雨、雪及地面渗水现象。
(二)贮存温度的影响
贮存温度高,有增加尿素结块的趋势。
因为温度高,颗粒尿素表面水蒸汽分压高。
当温度降低之后,即有一部分蒸汽冷凝于颗粒表面,即会造成结块。
因此,在袋装或散装堆放贮存以前,充分冷却新鲜尿素是必要的。
一般应冷却到55℃以下,一是避免对塑料包装袋的损坏;
二是降低颗粒尿素表面水蒸汽分压。
具体冷却到什么温度为宜,需要根据具体的空气相当湿度,可在图6-2上进行选择。
即是按照当时的环境空气温度和相对湿度(或水蒸汽分压)在图6-2的曲线Ⅲ找到一坐标点,过该点作温标平行线与曲线I相交于一点,这点对应的温度数值加3℃~5℃,就是出塔颗粒尿素的适宜冷却温度。
附加温度3℃~5℃,是供胶带输送过程热损失之用,视输送路程的长短和实验测试数值来确定附加温度值。
对于成粒法大颗粒尿素,贮存温度的选择,利用图6-2中曲线Ⅲ和曲线Ⅱ按前述方法进行即可。
(三)贮存压力(高度)的影响
尿素结块的程度与贮存压力有较大的关系。
因此要控制码包高度或散装堆积的高度。
对袋装尿素而言,码堆底层一袋上的压力可以通过测量该包的承载面积(袋与袋之间的接触面积)以及经由这个面积所分摊的该堆的重量来计算。
对于塔式造粒所得粒径Φ0.8~Φ3.0mm的小球粒状尿素,抗压强度很低,对于Φ2.4~Φ2.8mm的尿素颗粒抗压强度只有1.0~1.3×
105Pa。
粒径越大,抗压强度越大;
粒径愈小,抗压强度愈小。
对于平均粒径为1.5mm的尿素来言,抗压强度只有0.4~0.6×
l05Pa,塔式粒状尿素的堆密度为740kg/m3。
在包装袋中的密度约增加5.0%。
即777kg/m3。
袋装码堆中,袋与袋之间接触面积约90%,所以袋堆最大高度为:
0.9×
(0.4~0.6)×
104/777=4.6~6.9m
堆高超过这个数值,最下层的尿素颗粒即被压碎,增加了结块程度。
对于散装贮存时,一个圆锥形料堆底部尿素的平均压力P
P=d×
h/3(6-21)
堆中心最大压力Pmax
Pmax=2×
d×
h/3(6—22)
式中d——尿素的堆密度,kg/m3,取740;
h——贮堆的高度,m。
对于抗压强度为0.4~0.6×
105Pa尿素而言,其堆高
h=3×
Pmax/2d;
=3×
104/(2×
740)
=8.1~12.2m
散堆顶高大于以上数值.则堆顶底部尿素会被压碎而粉化,易于结块。
在海运过程中,船仓高度很大,无论是袋装或是散装尿素,其高度均大于上述抗压强度所限制的堆高数值。
因此要求在尿素生产过程中添加一些外部调节剂或“内部”调节剂,以增强尿素颗粒的流动性或增加颗粒的抗压强度。
常用的“外部”调节剂有两类,一类是非常细的粉末粘附在尿素颗粒表面上,常用的有硅藻土、高岭土、滑石和白垩,要求这些固体粉剂粒度非常细,90%<
10μm,在涂层转鼓中保持最适宜的滚程,则可得到良好的粘附力。
固体粉剂通常应用比例在l%~4%(重量)范围内。
他们防结块功能如同颗粒之间的机械栅栏,也起吸水、扩散并在颗粒表面上形成无活性的液相作用。
在因结块而形成粘接的地方,由于调节剂的存在,即可减轻这种粘接,因此使结块不严重。
另一类是液态调节剂,通用的有38℃时粘度为20厘沲(1厘沲=10-3Pa·
s)至100厘沲的油品,其功能是抑制或者减轻结晶增长。
用量一般为0.2%~0.5%(质量)。
在尿素造粒之前即把某种称为“内部”调节剂加入到熔融尿素中,常用的有甲醛或者UF水溶液,作为固化剂和防结块添加剂。
加入量为0.3%~0.5%,抗压强度可以提高20%~70%。
二、产品运输