数学模型与计算机控制 第九章 热轧带钢厚度计算机自动控制Word文件下载.docx
《数学模型与计算机控制 第九章 热轧带钢厚度计算机自动控制Word文件下载.docx》由会员分享,可在线阅读,更多相关《数学模型与计算机控制 第九章 热轧带钢厚度计算机自动控制Word文件下载.docx(23页珍藏版)》请在冰豆网上搜索。
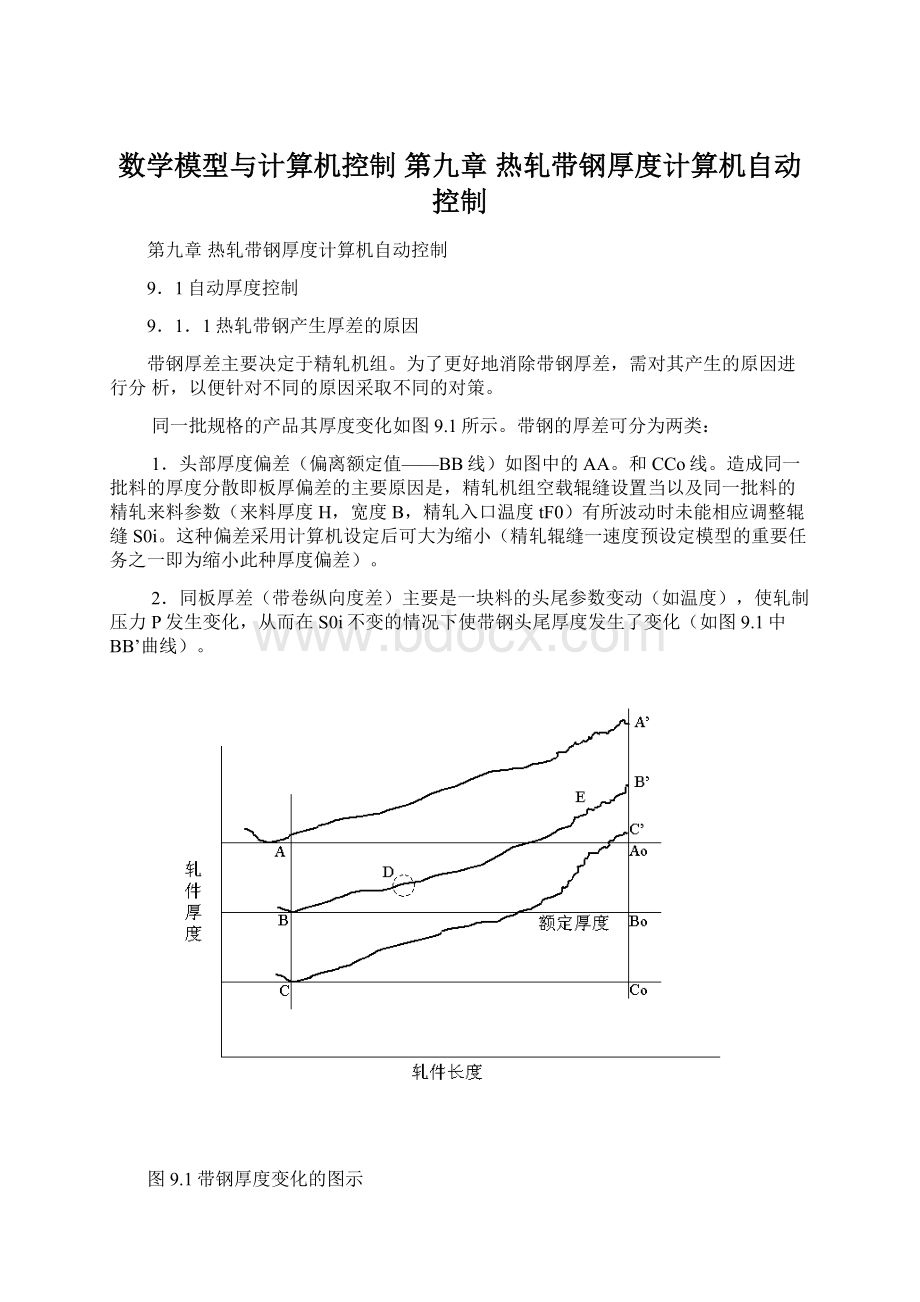
(9-3)
当
时,
。
但一般情况下精轧入口速度小于粗轧未架出口速度,即
因此
,亦即尾部在空气中停留时间比头部长一些,因而尾部温降比头部要大,形成头尾有温度差,这将使头尾轧制压力变化而产生头尾厚差。
头尾厚差是一逐渐变化的量(如图9.2中的BB’线),同此比较容易消除,目前主要通过轧制过程中逐渐调整日下螺丝来消除。
2.加热炉内导轨在钢坯表面造成的低温段称为水印,由于此段温度变化率大,厚度变动比较“陡”(如图9.2中的D段)。
一般反馈厚控系统由于有时间滞后,对这种厚差的调整效果较差。
计算机控制后,由于采用预控方式,这种厚差可大为减少。
3.尾部离开各机架时张力消失,使压力发生突增,造成台阶性厚差(如图9-2中的E段)。
一段采用“压尾”或“拉尾”的办法来改善。
4.现代带钢热连轧机都采用中速咬钢,待卷取机卷入带钢后再同步加速至高速的办法进行轧制。
在轧辊转速变动较大时,将使油膜轴承的油膜厚度发生变化而使实际辊缝变小,影响轧件厚度。
为此,现代厚控系统具有速度补偿(油膜厚度补偿)功能。
5.轧辊偏心(椭圆度)将直接使实际辊缝产生高频周期变化。
目前热轧调厚精度尚未达到如此高的水平,因此一般采用死区的办法(不灵敏区)来避免压下系统受此高频干扰的影响。
消除同板厚差的主要办法是采用自动厚控系统(AGC)。
近十年来,带钢热连轧机AGC系统有了极大的发展,特别是采用计算机厚控系统(DDC—AGC)增加了跟踪和预控功能,使调厚效果得到显著提高。
AGC系统工作的效果和Soi及voi设定的正确性直接有关。
如果Soi和voi设置不当,轧件厚度如图9-1的AA’曲线所示,则AGC不仅要承担消除同板厚差的任务,还要承担消除板厚偏差。
这样将使AGC任务过重,往往由于设备能力的限制,而不得不被迫停止工作。
为此,有些系统采用以带钢头部厚度作为控制其后厚度的标准(带钢厚度调整成图9-1中的AA0或CC0)。
·
这是头部厚度不准确(人工设定经验不足时)的情况下一般采用的方法。
因此区分这两种偏差,力争减少头部板厚偏差(此时的Soi和voi调整是空载调整),同时不断改进AGC系统的功能(特别是采用预控的原则),是提高权卷厚度精度和厚度均匀性的重要措施。
9.1.2带钢热连轧机自动厚控系统
由于带钢纵向厚度不均是产品质量的一个重要问题,因此热连轧自动化的一个重要课题即是厚度自动控制。
从1957年建立模拟厚控系统起,到发展为数字厚控系统乃至目前采用的计算机厚控系统,无论是新建的轧机,还是对老的热连轧机的改造,都设立了这一系统。
任何形式的系统,对产品质量提高的效果,都是十分显著的。
厚度自动控制系统的基本功能为典型的反馈闭环控制系统,整个系统包括以下四部分:
1.测厚仪,用来检测轧件的实际厚度(热连轧一般用间接测厚的办法);
2.厚度调节器,根据结定厚度值和实测值相比输出厚度偏差信号(并加以某种运算处理);
3.执行机构,根据偏差信号调节压下系统以改变轧件厚度,消除厚度偏差;
4)被调对象(轧件的变形区),它也是闭环系统中的一环,因此它的特性将直接影响控制系统的工作效果。
研究厚度自动控制系统时,应把机电设备(包括仪表)及轧件看成一个整体来分析。
厚度自动控制系统的作用是当某些工艺参数变化而使此综合系统失去平衡时(轧件厚度产生了偏差),能调节压下机构,使轧件厚度偏差消除,以得到厚度均匀的产品。
测厚仪可以是各种直接和间接检测轧件厚度的装置。
对于带钢热连轧机组除入口和出口处设有γ一射线及X一射线测厚仪外,其它各架的轧出厚度基本上采用间接测厚法测量,即利川用压力P(弹跳)来测量。
因此,这种系统又称为P-AGC,其关系式为:
(9-4)
或中S——空载辊缝,mm;
P——轧制压力,吨;
C——机架总的刚度系数,吨/mm;
Δ——辊缝变动量(mm),由油膜厚度变化造成,它随轧制速度和轧制压力的变化而变化。
间接测厚法的优点是简单,便于维护,同时,传递时差小(所测的是辊缝处的轧件厚度);
但缺点是精度差一些,主要是有些因素不易考虑,如辊缝磨损、热胀、轴承间隙、轧辊不圆等都将使实际空载辊缝改变,影响h的测量精度。
这一缺点目前利用出口侧X一射线测厚仪信号(积分后的平均值)来不断校正。
最初P-AGC只用于精轧机组2号及3号轧机。
由于P-AGC效果比较明显,使产
品质量大为提高,因此获得了迅速的发展。
P-AGC是目前带钢热连轧机厚度控制系统的基本形式,但它还存在以下缺点:
1.加重了设有AGC系统的机座的压下系统负荷和主电机负荷。
当厚度偏差较大时,厚度自动控制系统往往因设备能力的限制而被迫停止工作。
此外,由于压下系统动作过于频繁而剧烈地加快了机构的磨损,而.且当调节量过大时,由于恢复原位的时间太长,影响下一块料轧制。
2.压下机构移动时(厚度调节),将使机架间的张力发生变化,其结果是减弱了厚度调节的效果。
3.由温度产生的厚差具“重发性”,即在前架消除后在后几架中仍将产生。
因此,仅仅头几架设有AGC,不能完全解决成品厚度波动的问题。
4.来料温度波动所形成的板厚差,P一APC只能待钢轧入后根据实测压力P的信号来判断,加以调节。
因此此,当来料温度变动大时压下系统负荷太重(需带负荷压下)。
5.尾部张力消失造成的台阶形厚差,对于一般的P—AGC来说很难完全消除(调节速度跟不上)。
为了克服这些缺点,AGC系统在使用过程中不断发展,增加了许多新的功能,归纳起来有以下几个方面:
1.在克服压下机构的负荷和主电机负荷过重方面
1)设立一定大小的不灵敏区,即当厚度偏差小于一定量及变动频率过高时压下机构不动作。
2)当带钢头部厚度与额定厚度间差距较大时(这主要是由于各架辊缝设定当造成的),为了避免AGC系统调节量太大,可使AGC系统改为锁定头部厚度作为标准来调节其它段的厚度。
3)增加设置AGC系统的机架数。
目前各架都设有AGC系统,这可使各架分担厚度调节负担,同时可减小成品厚差。
AGC只用于一架时,厚度偏差约可减少50%;
用于二架时则减小75%;
三架时为90%;
四架时为94%;
五、六架时则为95~97%。
因此,在改造现有轧机时,一般采用三~四架设段置AGC的方案。
新轧机由于统筹考虑,设置AGC的投资并不增加多少,因此,一段各架都设有AGC系统。
2.在加强消除温度影响方面
温度是厚度变化的主要原因,因此,增设t一AGC(t代表温度),让温度信号参与厚度自动控制系统以加强克服温度所产生厚差的能力,是理所当然的。
1)利用精轧机组入口侧的测温仪信号,用前一块钢的头部温度作为标准,当下一块钢的头部温度有偏差时,则在钢料尚未进入轧机前先将各架空载辊缝调整一定量,以减少P—AGC系统带负荷压下的调整量,并使头部比较接近额定值(这功能目前由计算机设定控制——二次设定——来解决)。
2)将温度信号和压力信号一起送入AGC系统,引起一个“过补偿”调整,以适当克服在下一架又“重发”产生厚差的现象。
3)用上一架压力信号(间接反映了温度状况)和本架压力信号同时送入系统以引起“过补偿”调整——过补偿AGC。
3.在克服张力影响方面
l)采用恒定小张力活套控制系统保持厚度调节过程中张力恒定。
2)为了减轻张力恒定系统工作负担,加快张力恒定过程,有些AGC系统设有辅助调速功能,即利用厚差信号给主电机速度调速系统一信号(估计到调压下时张力要变的程度),预先调整各架转速使张力变化尽最小。
然后再靠张力恒定系统来恒定张力。
各架转速调节装置的分配比内实践经验来确定,对于DDC-AGC系统则由DDC计算机计算确定。
3)采用专门的R一AGC(R代表尾部)即利用前一架的抛钢信号(压力的消大)来压下后几架(称为压尾),或者调节后几架的转速改变张力(称为拉尾,此时恒定小张力系统应停止工作),来提高消除尾部厚差的能力。
现代AGC系统(特别是数字AGC)已开始包含一些预控成分(即前馈,而一般反馈在时间上总是滞后的),但由前馈量的比例无法根据实际生产情况来调整,同此只能起一些改善系统工作的作用,而在定量上不能充分发挥预控的优越性。
这一问题只有在引入计算机控制后才能解决(即计算机厚度控制系统)。
9.1.3计算机厚度控制系统DDC-AGC
计算机在厚度控制系统中的应用,进一步扩大了厚控系统的功能。
此外,一台定型小型计算机可以用来代替20~40个点的数字或模拟系统,使控制柜、接触元件等大为减小,减轻维修工作量(实际上用计算机的软件代替了传统调节器的大量硬件)。
因此,当小型计算机的可靠性大大提高以后,必然会发展到采用计算机厚控系统,即所谓DDC—AGC系统。
对于DDC系统来说,最关键的是计算机的可靠性。
否则一出事故,将影响一大片自动控制系统的工作。
DDC—AGC利用的基本方程,仍然是弹跳方程:
但为了进一步提高精度,需对各种影响间接测厚精度的因素增加补偿措施,方程可为:
(9-5)
其中,Δ为考虑轧机速度变化使支撑辊的油膜轴承的油膜厚度发生变化,从而对辊缝产生的影响(速度变大,油膜厚度加大,因而使辊缝减小)。
油膜轴承的油膜厚度和轧制压力大小及轴承的线速度有关,因此:
的曲线一般用实验的方法直接在现场生产轧机上求得。
为了区分轧机刚度和油膜厚度,一般规定轧机的刚度实验应在轧辊线速度固定在某一数值时进行,在此基础上进一步求油膜哈度。
实验方法是每次提高一级线速度,调整压下螺丝位置,使之得到几种轧制压力,记录下每一种情况下的压下螺纹位置;
然后时提高一级线速度,再调整压下螺丝取得几种不同压力下的压下螺丝位置。
假设在轧机刚度试验的线速度和预压靠力时油膜厚度为起点(亦即将这种条件下的油膜厚度归入了轧机刚度),则通过所记录的压下螺丝位置的变化,可以求出压力和线速度对油膜厚度变化的影响曲线。
将曲线用表格法存贮于计算机内存,计算机使用时可根据工作压力和线速度值用内插法查用。
DDC—AGC的计算框图如图9-3所示。
图9-3DDC—AGC的计算框图
图上除和上述公式有关的一些框图外,还包括以下一些内容:
锁定方式;
输出量不是δh,而是δS;
预控问题(前馈控制);
同时输出δv信号(活套补偿);
辊缝零位常数);
射线测厚仪监视控制;
尾部补偿;
自动复位。
现分别对上述八个方面作进一步阐述。
1.厚度锁定方式
对于厚度锁定方式,目前存在着两种观点。
第一种观点是由计算机或人工根据厚度分配方案,对各架结出h0值,当轧件轧出后根据S0、P等反馈实测信号,按式9-5运算后,与此目标值相比,如不同就输出δh进行调厚,直到δh=0为止。
这种方案要求将整个带钢的厚度都调到目标值——额定值。
但如果由于空载辊缝设置不当,轧件头部的厚度已经与目标值差得较多的情况下,若一定要强求压下系统将带钢厚度调到h0,势必会造成压下系统负荷过大,同时亦将把带钢调成楔形厚差(即头部厚,尾部逐渐调成h0),反而不利于带钢质量。
基于这种情况,有人提出第二种观点,即不论带钢头部是否符合目标值,厚度控制系统以头部的实际厚度为标准,即用头部实测的S0、P等算得h值送回系统,作为给定值h0*。
厚控系统应使带钢各点的厚度向此值看齐,这样有利于得到厚度均匀的带钢。
但此带钢的厚度值不一定符合产品所要求的额定值。
新设计的系统往往这两种功能都有,由工人根据情况决定采用哪种方式工作。
2.输出量δS
采用数字AGC系统时,须确定的不是δh,而是辊缝调整量δS。
由于轧机刚度为有限值,为了得到需要的δh量,压下螺丝必须调整δS量,以补偿调厚过程中轧制压力变动所引起的弹跳变化。
其变化量为:
(9-6)
式中
为S和h的影响系数,其大小决定于轧机弹性刚度系数C初轧件塑性刚度系数Q之比:
式中C——轧机的弹性刚度系数,其物理意义为辊缝弹跳一毫米所需的压力,它在轧制过程中基本上为一常数,只同板定和支撑辊直径有关,C=f(B,D);
Q——轧件塑性刚度系数,其物理意义为轧件塑性变形一毫米所需的压力,它决定于轧件的厚度、轧件材料和轧制温度等等。
当轧制条件不同时,Q的数值亦不同,需由计算机根据轧制实际情况来确定。
Q值有。
两种确定方法:
l)利用精轧设定模型中轧制压力计算所用的方法,在已知带钢本道次轧的厚度H、轧出厚度h以及具体轧制条件(轧件宽度B,轧辊半径R,轧制温度t0,轧制速度V和钢种成分)下,可计算出应有的轧制压力大小Pa(图9-4的a点压力)。
用同样的方法可算出b点的压力Pb,这时的计算应该用h’代替h,假设取h’=h+Δ,则可用Pb和Pa算出Q值:
(9-7)
图9-4Q值计算的图示
此法的实际含义为用ab直线段来代替a点的切线(a点切经表示a点条件下,变动单位压下量将造成的压力变化,亦即为Q值)。
因此,当Hab曲线非线性较大时,Δ值取得越小,上式将越接近Q值。
但实际应用时,如果Δ值取得太小将由于压力计算误差,而产生较大的Q值误差。
因此Δ值一般应取0.1~0.5(前几架轧机可取较大值,后几架轧机则可取较小值)。
2)考虑到对于带钢热连轧机精轧机组压力曲线Hab(图9-4)基本接近于直线,为了简化计算方法也可采用下式计算Q值:
(9-8)
式中P*——实测压力;
KK——压力曲线非线性修正系数,一般为0.9~1.1,当轧辊半径较大,轧件厚度较小时,取较小数值;
Δh*——实际压下量,i机架压下量为:
和
可用X一射线测厚仪实测得到的未架出口厚度以及各架轧制速度实测值利用
秒流量法则推算而得。
应用电子计算机直接控制的厚度自动控制系统(DDC一AGC)将能显著提高厚度调节的精度。
目前,在实行计算机分级控制时,精轧机组七架轧机的7个位置调节系统和7个人AGC系统一般是由一个DDC计算机实现的。
3.预控
采用DDC一AGC后就有可能增加AGC系统的功能,首先是有可能引人“预控”功能(亦称为前馈)。
“预控”和“反馈”是相对立的一种控制观点。
预控不是根据过程进行完了后的效果,而是根据来料情况,提前调整以便达到顶期的目标。
这只能是电子计算机在应用相应的数学模型后才能实现)其优点是可以克服时间上的滞后现象,加快系统的响应性”。
因此,对于一些突变性参数,例如对于水印造成的厚差等的调整比较有效。
图9-3中的虚线即为这一部分控制框图,即根据上一梁的δh(亦即下一架的δH),延时后控制一下架的辊缝,以保证更好的调节效果。
此时可得:
(9-9)
图9-5表示了对于具有阶跃形δH的轧件咬人轧机后,在反馈系统作用下δh的变化,由于系统存在滞后时间Δτ1,加上压下螺丝移动δS需要一定的时间Δτ2,因此其在轧件的一段长度上,有较大的厚度波动。
图9-6表示了采用预控后的情况,由于两个机架间距离为定值,而前一架轧机速度能实测,因此可用下式确定此阶跃形δH进入下一架的时间,及时给于控制:
式中f——前滑值,可根据前一架轧机压下量计算得出。
为了进一步发挥预控的优点,可用下式计算延时时间:
(9-10)
δ值取得合适可得到图9-7所示的结果,这样δh绝对值将进一步降低。
δ值可通过实验求出,也可利用数学模拟法求出。
图9-5AGC系统控制的δh过渡曲线
图9-6预控AGC系统的δh过渡曲线
图9-7预控AGC系统提前动作时的δh过渡曲线
4.活套补偿
AGC系统工作的后果,除轧件厚度变化外,将导致张力产生波动,这可以由活套调节系统改变主电机转速实现速度调节来使张力恒定。
但完成调速过程,需有一定的时间,而在调速过程中张力的变化将影响产品质量。
为了克服这一问题,现代AGC系统在发出辊缝调整信号的同时,亦给主电机发出相应的调速信号,以使张力不产生波动。
如何定量计算应该发给主电机的调速信号,目前存在几种不同的观点,比较常用的一种是流量法的观点,亦即认为i机架调厚前轧机已处于稳定状态,各架轧机流量相等,i机架流量为(单位宽度):
式中。
V‘——轧件入口速度;
v——出口速度;
V0——轧辊线速度;
H——轧前厚度;
h——轧出厚度;
hr——中性面处的厚度。
当压下系统调厚辊维变动δS值后,将使轧出厚度变化一个δh值,为了保持流量不变,则应使主电机转速有δv变化,即:
因此:
(9-11)
为辊缝变化量对轧出厚度变化的影响系数,一般称为压下效率:
考虑到hri不易确定,因此改用hi,此时可写为:
(9-12)
式中系数G可由实验确定。
我们认为利用流量概念来研究张力变化是不合适的,由于流量为轧出厚度和轧出速度的乘积(假设宽度不变),而轧出厚度变化造成的流量改变并不一定会造成张力波动,如图9-8所示情况,
图9-8连轧动态状态
当压下系统下压而使出口厚度变薄时,流量虽变了,但当速度不变时,张力或套量将不会变化,轧出厚度变化必须经过一定时间才能到达下一架产生影响。
因此我们认为压下系统移动影响张力的现象应该用“速度观点”来解释。
所谓“速度观点”即认为压下移动将改变轧件的入口和出口速度(特别是入口速度变化将大些),其原因是压下量变化将影响前滑量和后滑量变化,而轧件入口速度为(假设H,t0等不变,。
因此前滑和后滑只随δS变):
(9-13)
轧件出口速度为
(9-14)
调厚前如果轧机处于平衡状态,因此在一定张力作用下:
式中vi-1和vi——i-1架和i架的出口速度;
v‘i和v‘i+1——I架和i+1架的入口速度。
因此当调厚时由fδSi产生了δv‘i和δvi后将使i-l架和i架问张力以及i架和i+1架间张力发生变化,为了防止张力变化可采用以下调速方案。
调动i架轧机(调厚的轧机)古电机速度使补偿δvi的变化,考虑到δS造成的前滑变化为:
因此i架轧机应调速δv0i,可用下列速度不变关系式算出应调速δv0i:
(9-15)
忽略δv0i、δSi从项后得:
(9-16)
调动i-1机架速度使δv‘i=δvi-1,将先9-16和9-14代入式9-13得:
(9-17)
由于压下移动对张力影响是一个比较复杂的问题,上述两种观点的实用性都有待于通过实验和生产实践进一步验证和考核。
5.辊缝零位常数G
间接测厚法(公式9-5)是利用辊缝仪信号来表示轧辊辊隙的,但实际上轧辊直径由于磨损和热胀将产生缓慢的变动,其结果将使实际辊隙和辊缝仪指示有差异。
这种现象可归结为辊缝零位发生了“漂移”,为此引入了辊缝零位常数G。
辊缝零位常数确定方法是利用上一卷带钢在稳定轧制条件时,各架“实测”出口厚度h*和用间接法算出的厚度力h之差来求得:
(9-18)
所谓“实测”厚度h*是利用稳定轧制条件时X一射线测厚仪所实测的成品厚度为依据,用秒流量相等法则推算出的各架出口厚度,由于稳定轧制是指轧件已全部通过各架轧机,活套动作已基本结束,而厚控系统尚未开始工作的状态,因此,秒流量相等法则在一定精度的含义下可以认为是成立的。
所以:
(9-19)
式中v0m——末架轧辊线速度;
v0i——i架轧辊线速度;
fm和fi——末架和i架的前滑量;
h‘m——X一射线测厚仪实测的成品厚度(以此作为基准数据);
h‘i——推算得的各架“实测”出口厚度。
考虑到辊缝零位漂移是一缓慢过程,因此可用上一卷钢所求得的零位常数G,利用下式求得本卷钢所用的辊缝零位常数(各个机架都用此形式):
(9-20)
即为对n根钢用9-18式求得的辊缝零位常数,第n+1根钢可用
作为图9-3中所示的辊缝零位常数进入厚控系统。
6.X一射线测厚仪监视控制
间接测厚的厚控系统虽然考虑了各种补偿因素(如油膜厚度,辊缝零位常数等),其精度总是低于X一射线测厚仪直接测量出的厚度值。
因此,在本卷钢厚控系统投入后,仍需以X一射线测厚仪所测得的成品厚度实测值(其精度较高)为基准对AGC系统进行监视。
当成品厚度和设定值有偏差时,将此偏差值反馈到每个机架的AGC系统中(积分控制)。
对于机架后面直接设有测厚仪的系统,其积分控制的框图如图9-9所示。
图9-9用测厚仪的厚控系统
图中
为积分环节,
为滞后环节,即X一射线测厚仪测得的厚度
是
时间以前轧出的厚度
,
为反馈用的X一射线测厚仪测得成品厚度的偏差量。
如图9-9所示的带有滞后时间的系统,其稳定性条件(考虑到控制系统本身还具有滞
后时间)要求K0不能太大,可用下式求得K0:
(9-21)
式中的K精根据实际情况调试,一般K>3。
对于热连轧精轧机组由于仅在最后机架后设置有一射线测厚仪,对于前面各机架的AGC系统,只能借用9-21式计算。
但此时tL应是轧件从该机架运动到X一射线测厚仪所需的时间,因此i机架的
(9-22)
式中vj——j机架的出口速度(
);
vm——最后一机架(设共有m个机架)的出口厚度;
L——机架间距离;
Lx—一最后机架到X一射线测测厚仪的距离。
于是在DDC一AGC系统中,每个机架的监视值Kx,可由下列积分式表示:
(9-23)
式中tL对于每个机架不同,都用9-22式计算。
β为监视增益系数,根据实际系统调整(实际工作时可将
于作为一个参数在调试中进行调整)。
X-射线测厚仪监视控制(Kx)和上一段介绍的辊缝令为常数(G)的区别在于G是不断递推,由n根钢测行后进机到第n+1根钢应用,而Kx仅用于本卷钢,当尾部一离开第一机架即停止工作,并将累计的Kx值清零(尾部离开第一架后转入尾部外偿控制)。
7.尾部补偿