红枣去核机的设计Word文档格式.docx
《红枣去核机的设计Word文档格式.docx》由会员分享,可在线阅读,更多相关《红枣去核机的设计Word文档格式.docx(33页珍藏版)》请在冰豆网上搜索。
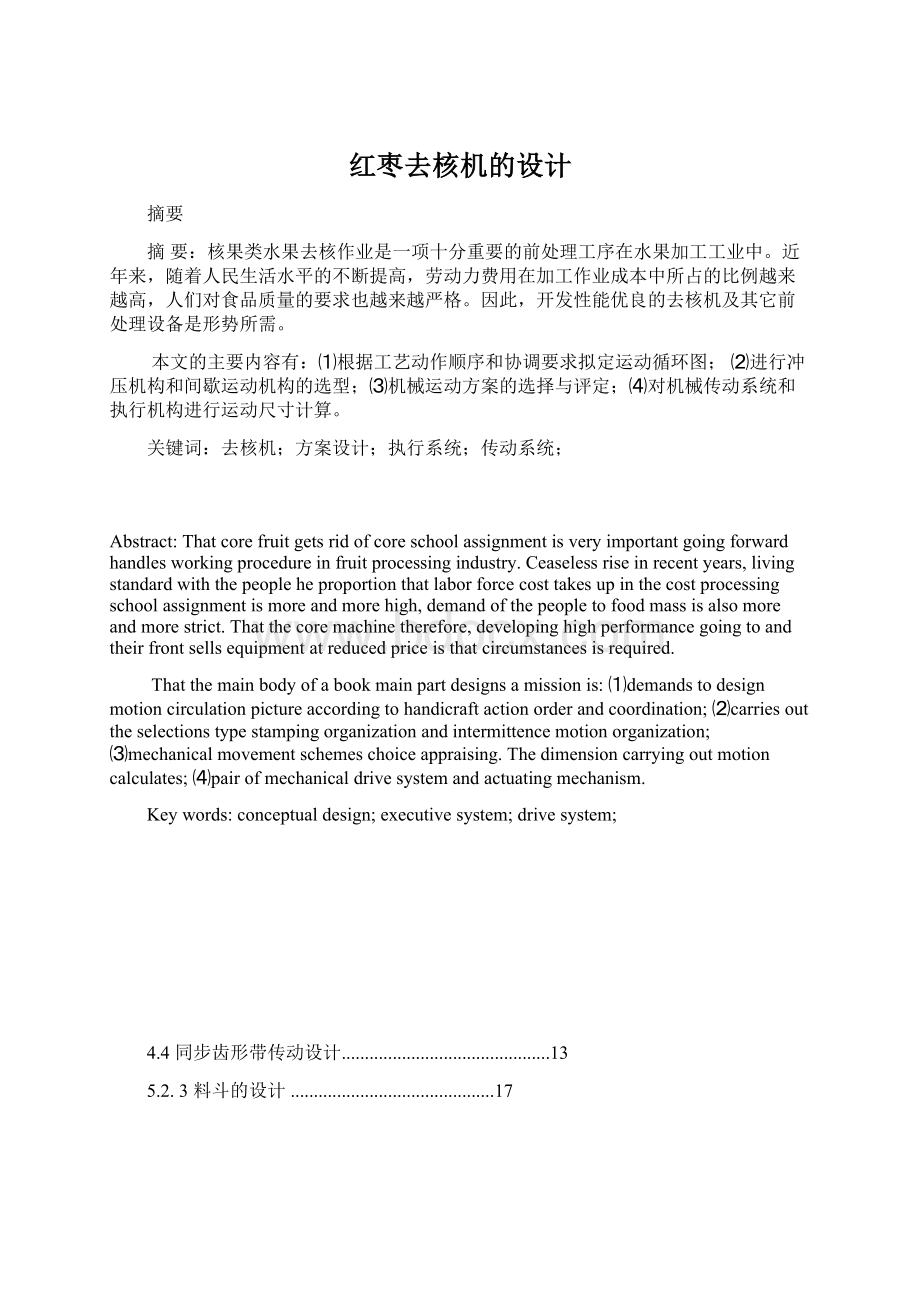
因此,实行水果去核的机械化作业是一种必然的发展趋势。
国外60年代就着手去核机的研制。
80年代初,美国、意大利和荷兰等国已相继出现了桃去核机、橄榄去核机等.去核工序基本上实现了机械化.我国是从80年代后期开始着手对去核机进行研制的,并陆续推出一些产品。
由于一些问题尚未真正解决,因此,真正在生产中推广应用的并不多,在众多的果品加工厂中,去核作业至今基本上仍依靠手工或者十分简陋的工具完成。
近年来,随着人民生活水平的不断提高,人们对食品质量的要求也越来越严格,生产厂家也意识到,前处理工序对产品质量有着不可忽视的影响,各厂家纷纷寻找合适的前处理设备,由于许多前处理设备在国内尚属空白,例如桃去核机等,故用户的需求难以满足。
二、红枣去核机的方案设计
2.1执行系统的方案设计
机械执行系统的方案设计是机械系统总体方案设计的核心,它对机械能否实现预期的功能、性能的优势、经济效益的好坏都起着决定性的作用。
2.1.1红枣去核机的功能
红枣去核机是将冲针的往复直线运动及旋转盘工作台的间歇转动来完成连续去核作业处理,其总功能可分解为送料、冲核、退回、冲枣四个分功能。
2.1.2红枣去核机的原始数据和设计要求
⑴加工红枣直径为15mm~20mm
⑵红枣去核时冲针压力最大可达3KN,
⑶要求冲针自上向下运动前,旋转盘做一次间歇转动,转角为90º
⑷红枣去核机使用寿命10年,每日一班制工作,载荷有轻微冲击。
2.1.3工艺动作分解
根据上诉分析,红枣去核机要求完成的工艺动作有以下几个动作。
1加料:
这一动作可利用人工加料。
⑵冲制:
其工艺动作可分为冲核和冲枣,要求冲针自上向下运动前,旋转盘做一次间歇运动,转动角度为90º
⑶旋转盘间歇运动:
以完成送料、冲核、冲枣三个工位的转换。
2.1.4冲针往复直线运动的实现机构
选择电动机为动力源,此机构是具有将连续的回转运动变换为往复直线运动的功能。
实现该功能的各机构比较如下:
⑴摆动从动件圆柱凸轮:
凸轮具有易设计的优点,它还能准确有效地预测所产生运动的基本趋势、工作行为、结构和寿命等,具有良好的运动性能和动力性能。
⑵对心曲柄滑块机构:
这种低副机构具有良好的动力特性和运动特性、运动副几何封闭、制造简单等优点。
⑶偏置曲柄滑块机构:
与对心曲柄滑块机构相比较,具有曾力、急回特性等优点。
2.1.5旋转盘间歇转动的实现机构
棘轮机构、槽轮机构、不完全齿轮机构均可实现间歇运动。
由于旋转盘间歇转动速度要求低速,且需要精确地转位,故选用槽轮机构。
2.1.6执行机构的协调设计
红枣去核机由减速传动装置、冲压机构、间歇运动机构组成。
在送料期间,冲针不能压到旋转盘,显然,冲针自上向下运动前,旋转盘做一次间歇转动,所以冲针与旋转盘之间的运动,在时间顺序和空间位置上有严格的协调配合要求。
2.1.7机构运动循环图的设计
对于红枣去核机的运动循环图主要是确定冲针、旋转盘二个执行构件的先后顺序、相位,以利于对各执行构件的设计。
其红枣去核机一个工作循环的工作过程如图1所示。
为了保证机器在工作时其各执行构件间动作的协调配合关系,在设计机器时应编制出表明机器在一个运动循环中各执行构件运动关系的运动循环图。
表1表示红枣去核机二个执行构件的运动循环图,冲针和旋转盘都由工作行程和回程两部分组成,设每转一周为一个运动周期,其冲针的工作行程为0º
~180º
,回程为180º
~360º
,即一个运动周期做一次上下移动;
旋转盘的工作行程在冲针的回程后半段和工作行程的前半段完成,工作旋转盘由轴4带动,通过槽轮机构做间歇转位运动,转位过程对应于轴4转过90º
,停歇过程对应于轴4转过270º
。
图1红枣去核机的工作过程
表1执行构件运动循环图
冲针
工作行程回程
旋转盘
停止进给
主轴转角0º
90º
180º
270º
360º
2.1.8机械运动方案的选择和评定
现在可以按给定条件、各执行机构的相容性和尽量使机构简单、空间布局紧凑等要求来选择方案,由此可选择两个结构比较简单的方案。
方案1:
冲压机构为偏置曲柄滑块机构,旋转盘间歇机构为棘轮机构。
方案2:
冲压机构为摆动从动件圆柱凸轮机构,旋转盘间歇机构为槽轮机构。
评定:
偏置曲柄滑块机构的往复直线运动具有增力、急回特性等功能,但方案2具有易设计及机械效率高等优点,故最后选择方案2为红枣去核机的机械运动方案。
2.2传动系统的方案设计
2.2.1初选原动机
根据红枣去核机的工作情况和原动机的选择原则,初选三相异步电动机为原动机,额定转速为n=750r/min。
因额定功率需在力分析后确定,故电动机的具体型号待定。
2.2.2拟定传动系统方案
根据执行系统的工况和初选原动机的工况及要实现的总传动比,拟选用带传动机构和一级圆锥齿轮传动组成红枣去核机的传动系统。
2.2.3机械运动简图
按已选定的两个执行机构形式及机械传动系统,画出红枣去核机的机械运动简图。
如图2所示,其工作原理为:
电动机经过减速传动装置(带轮传动)带动执行机构(摆动从动件圆柱凸轮、间歇运动机构),完成冲针的往复直线运动和旋转盘工作台的间歇转动。
红枣去核机工作时,冲针由摆动从动件带动下行,冲针进行去核,称为工作行程,工作阻力F为常数;
冲针上行时,即为空回行程,此行程无工作阻力,在空回行程中,通过带轮→圆锥齿轮→槽轮机构,槽轮机构带动旋转盘工作台做一次进给运动,即送料,以便冲针继续冲核、冲枣。
图2机械运动简图
三、传动装置的总体设计
3.1选择电动机
3.1.1电动机的类型和结构形式
按工作要求和工作条件,选用一般用途的Y(IP44)系列三相异步电动机。
它为卧式封闭结构。
3.1.2确定电动机容量
⑴冲针的输出功率PW
根据设计要求和原始数据及实验分析可知:
F=2500N,设定冲针的速度为0.7m/s,则冲针的输出功率为:
PW===1.77KW
⑵电动机的输出功率Pd
传动装置的总效率:
η=η1η23η3η4η52
式中,η1,η2,η3,η4,η5为电动机至冲针的各传动机构的效率;
由机械设计课程设计手册:
表1-7查得:
V带传动:
η1=0.96,滚子轴承η2=0.98,锥齿轮传动η3=0.95,齿式联轴器η4=0.99,槽摩擦轮传动η5=0.89,
故η=η1η23η3η4η52=0.96ⅹ0.983ⅹ0.95ⅹ0.99ⅹ0.892=0.666
所以Pd===2.66KW
⑶电动机的额定功率Ped
由机械设计手册表12-1选取电动机的额定功率为Ped=3KW
3.1.3确定电动机转速
为了便于选择电动机的转速,先推算电动机转速的可选范围,V带轮传动常用传动比范围i=2~5,则电动机转速的可选范围为nd=284~710r/min,可见同步转速750r/min的电动机符合。
表2Y132S-8型电动机的主要性能
电动机型号
额定功率(KW)电动机同步转速(r/min)电动机满载转速(r/min)传动装置传动比
Y132S-8
37507107
3.2确定传动装置的传动比
总传动比id==7
3.3传动装置的运动和动力参数
3.3.1各轴的转速
电动机轴为0轴,各转速为
n0=710r/min
nⅠ=nⅡ=710/i=101/min
3.3.2各轴的输入功率
按电动机的额定功率计算各轴输入功率:
P0=Ped=3KW
PⅠ=P0•η1=3ⅹ0.96=2.88KW
PⅡ=PⅠη23η3=2.88ⅹ0.983ⅹ0.95=2.63KW
PⅢ=PⅡⅹη4=2.63ⅹ0.99=2.55KW
3.3.3各轴的转矩
T0=9550ⅹP0/n0=9550ⅹ3/710=40.35N•m
TⅠ=9550ⅹPⅠ/nⅠ=9550ⅹ2.88/142=193.69N•m
TⅡ=9550ⅹPⅡ/nⅡ=9550ⅹ2.63/142=176.88N•m
TⅢ=9550ⅹPⅢ/nⅢ=9550ⅹ2.55/142=171.5N•m
四、传动零件的设计计算
4.1普通V带传动的设计计算
⑴确定计算功率:
由机械设计手册表8-7查得工作情况系数KA=1.1,故
Pca=P•KA=1.1ⅹ3=3.3KW
2选取窄V带带型
根据Pca、nⅠ由图8-11确定选用A型
3确定带轮的基准直径
由表8-6和8-8取主动轮基准直径dd1=80mm
根据式8-15,从动轮基准直径dd2
dd2=i•dd1=5ⅹ80=400mm
按式8-13验算带的速度:
V==2.97m/s30m/s
故带的速度合适
4确定窄V带的基准长度和传动中心距
根据0.7(dd1+dd2)≤a0≤2(dd1+dd2),初步确定中心距a0=650mm
根据式8-22计算带所需要的基准长度:
Ld′=2a0+(dd1+dd2)+=2ⅹ650+(400+80)+=2093mm
由表8-2选带的基准长度:
Ld=2000mm
按式8-23计算实际中心距a
a=650+=604
⑸验算主动轮上的包角α1
由式8-25得
α1=180º
-(dd2-dd1)ⅹ57.3º
/α=149.6º
>
90º
故主动轮上的包角合适
⑹计算窄V带的根数:
由式8-26知:
Z=
由nⅠ=710r/min,dd1=71mm查表8-4a和表8-4b得
P0=0.4KWP0=0.09
查表8-5得Kα=0.92,查表8-2得KL=1.03
则Z==2.7
取Z=3根.
⑺计算预紧力F0
由式8-27知F0=500
由表8-3得q=0.1kg/m,故
F0=500
⑻计算作用在轴上的压轴力FP
由式8-28得:
FP=2ZF0=2ⅹ7ⅹ135.8=1835N
⑼带轮的结构设计
由于d≤500mm,适宜采用腹板式结构,绘制带轮的零件图如图3所示:
图3带轮零件图
4.2直齿圆锥齿轮传动设计计算
4.2.1选择齿轮类型、精度等级、材料及齿数
⑴按图所示的传动方案,选用标准直齿圆锥齿轮传动
⑵精度等级选7级精度
⑶材料选择:
选两齿轮均为45钢(调制处理),硬度为240HBS。
⑷选齿轮齿数Z1=Z2=30
⑸选取分度圆锥角δ1==45δ2=90º
-δ1=45º
4.2.2按齿面接触强度设计
由设计计算公式10-26进行试算,即:
d1t≥2.92
⑴试选载荷系数Kt=1.6
⑵计算齿轮传递的转矩:
⑶齿宽系数,取
⑷由机械设计教材表10-6查得材料的弹性影响系数
⑸由图10-21d按齿面硬度查得两齿轮的接触疲劳强度极限σHlim=550MPa
⑹由式10-13计算应力循环次数:
N1=N2=60n1Jlh=60ⅹ142ⅹ1ⅹ(8ⅹ300ⅹ10)=2.04
⑺由图10-19查得接触疲劳寿命系数KHN1=KHN2=0.98
⑻计算接触疲劳许用应力
取失效概率为1%,安全系数s=1,由式10-12得
1=2==0.98ⅹ550MPa=539MPa
试算齿轮分度圆直径d1t,代入中较小值
d1t≥2.92=2.92=160.8mm
⑼计算圆周速度
V==1.195m/s
⑽计算齿宽
b=R•=0.33ⅹ160.8ⅹ=37.5
⑾计算载荷系数
根据v=1.195m/s,7级精度,动载荷系数KV可按图10-8中低一级精度线查得KV=1.16,取齿间载荷分配系数KHa=KFa=1
4.2.3按齿根弯曲疲劳强度设计
由式10-24得弯曲疲劳强度的设计公式:
确定公式内的各计算数值:
⑴由图10-20c查得两齿轮的弯曲疲劳强度极限
σFE1=σFE2=380MPa
⑵由图10-18查得弯曲疲劳寿命系数KFN1=KFN2=0.92
⑷计算动载荷系数K
K=KAKVKFaKFβ=1ⅹ1.6ⅹ1ⅹ1.875=2.175
⑸计算当量齿数
ZV1=ZV2===42.4
5查取齿形系数:
由表10-5,利用插值法计算齿形系数和应力校正系数
对比计算结果:
由齿面接触疲劳强度计算的模数m大于由齿根弯曲疲劳强度的模数,由于齿轮模数m的大小主要取决于弯曲强度所决定的承载能力,而齿面接触疲劳强度所决定的承载能力仅与齿轮直径有关,可取由弯曲疲劳强度算得的模数4.51并就圆整为标准值m=4.5mm,按接触强度计算得的分度圆直径d1=178.1mm,算出齿轮齿数Z1=Z1=Z2=40
这样设计出的齿轮传动,既满足了齿轮弯曲疲劳强度,并做到了结构紧凑。
4.2.4几何尺寸的计算
⑴计算分度圆直径:
d1=mZ1=40ⅹ4.5=180mm
d2=mZ2=40ⅹ4.5=180mm
⑵计算齿轮宽度:
b=R=42mm
da1=d+2ha=m(Z1+2)=186mm
df1=d+2hf=m(Z1-2)=172mm
4.2.5结构设计及绘制零件图
由于齿轮齿顶圆直径大于150mm,而又小于500mm,所以设计锥齿轮为锻造锥齿轮,选用腹板式结构为宜。
其它有关尺寸计算从略,并绘制齿轮零件图如图4所示:
图4齿轮结构简图
4.3联轴器的选择
4.3.1选择联轴器的类型和型号
⑴类型选择
因为减速器与工作机不在同一底座上,传递转矩较大,且要求有较大的轴线偏移补偿,故选用齿式联轴器。
⑵载荷计算
公称转矩:
由机械设计教材表14-1查得,故由式14-1得计算转矩为:
⑶型号选择
从手册表8-3中查得GICL1型鼓形齿式联轴器的公称转矩为800N·
m,许用转速为7100r/min,轴径为16~38之间,故合用。
4.4同步齿形带传动的设计
由于传动具有中间挠性件,所有能缓和冲击,吸收震动,传动平稳无噪声。
传动特点,,
(1)带与轮间无相对滑动,传动比准确,传动效率高
(2)带轻而薄,适于高速传动
(3)传动比大,可达10
(4)传递功率范围广,可达200KW
选用梯形同步带
由设计知电动机额定功率P功率3Kw,轴工作转速102r/min,传动比I=7,每天两班制工作
(1)设计功率Pd(由机械设计手册2表14-1-55得)Ka=1.5Kw,
Pd=Ka*P=1.5x3=4.5Kw
(2)选定带型和节距
根据Pd=4.5Kw和n1=750r/min,由图14.1-14确定为XH型
由表14.1-50得Pb=12.7mm.
小带轮齿数为Z1,根据带型XH和小带轮转速n1,由表14.1-56得Z1最少齿数为22,此处取Z1=24
(3)小带轮节圆直径d1===97.07mm
由表14.1-60得外径da1=d1-2&
=80.90-2.79=77.11mm
(4)大带轮齿数Z2=IZ1=24X2.4=57.6
由表14.1-59得Z2取60
(5)大带轮节圆直径d2=1===242.7mm
由表14.1-60得其外径da2=d2-2&
=242.7-97.07=145.63mm
(6)带速V
V==0.518m/s
(7)初定轴间距a0
0.7(d1+d2)≤a0≤2(d1+d2)
0.7(97.07+242.7)≤a0≤2(97.07+242.7)
237.84≤a0≤679.54
取a0=450
(8)带长及齿数
LO=2a0+(d1+d2)+
=2*450+(97.07+242.7)+=1445.22mm
(9)所需带宽bs
bs=bs0
由表14.1-57得查的XH型带bs0=101.6,Kz=1
bs=101.6=42.74
由表14.1-52得应选带宽代号为200的XH型带,其bs=50.8mm
(10带轮结构和尺寸
小带轮Z1=24,d1=97.07mmm,da1=77.11mm
大带轮Z2=60,d2=242.7mm,da2=145.63mm
五、执行机构的设计计算
5.1冲压机构的设计计算
5.1.1冲压机构的选型
能实现往复直线运动的机构有:
摆动从动件圆柱凸轮机构、对心曲柄滑块机构、偏置曲柄滑块机构,按图2所示的传动方案,选择摆动从动件圆柱凸轮机构,结构如下图5所示:
图5摆动从动件圆柱凸轮机构
5.1.2摆动从动件圆柱凸轮机构中心距a的确定
图6是简化了的滚子摆动从动件圆柱凸轮机构,摆动从动件轴线A与圆柱凸轮轴线OO间的最短距离就是摆动从动件圆柱凸轮机构的中心距a,AB1和AB3是摆动从动件的两个极限位置,AB2是摆从动件的中间位置,为了使滚子中心B的轨迹量与同一个圆柱接近,取B1B3//OO,CD=DB2,
则:
a=AD=AC+CD=AC+1/2(AB2-AC)=1/(AB2+AC)=1/2(L+Lcosψmax/2)
即:
a=L/2(1+cosψmax/2)
式中,a:
凸轮机构的中心距;
L:
摆动从动件的长度;
ψmax:
摆动从动件的最大摆角
由空间结构决定,取ψmax=90º
,L=60mm
故a=L/2(1+cosψmax/2)=15(2+)
图6摆动从动件圆柱凸轮机构简图
5.1.3摆动从动件运动规律的选择
用解析法设计圆柱凸轮廓线,首先需要建立摆动从动件运动规律的解析式:
ψ=F(φ)
式中,ψ:
摆动从动件的摆角;
φ:
圆柱凸轮的转角。
去核机对摆动从动件的摆角规律有较严格的要求,所以应首先满足摆角的要求。
选择摆动从动件运动规律的一般原则:
⑴仅需从动件实现一定的摆角,而对于行程中的运动规律并无严格要求时,常选用便于加工的简单几何曲线(如圆弧、圆弧直线)作为圆柱凸轮轮廓线。
⑵对摆动从动件的摆角规律有严格要求的,应首先满足摆角的要求,然后考虑角速度和角加速问题。
⑶对高转速圆柱凸轮机构的摆动从动件的运动规律,主要考虑从动件的动力特性,力求避免过大的惯性力,为了便于比较、选取,现将几种常用的摆动从动件规律特性列于表3:
表3各种运动特性的比较
运动规名称
最大角速度Ωmax最大角加速度max应用
等速
改进等速(余弦)
改进等速(正弦)
等加速等减速
余弦加速度
正弦加速度
五次多项式
改进正弦加速度
改进梯形加速度
1.00∞低速轻负载
1.227.68低速重负荷
1.338.38低速重负荷
2.004.00中速轻负荷
1.574.93中低速轻负荷
2.006.28中高速轻负荷
l.885.77高速中负荷
1.765.33中高速重负荷
2.004.89高速轻负荷
本设计中的摆动从动件符合第五种运动规律特性。
5.1.4圆柱凸轮中径Dˊ的确定
由于展开圆柱面的直径愈大则对应的凸轮理论廓线的变化率愈小,也就是说,外圆柱面上的凸轮理论廓线的变化率比槽底圆柱面土的理论廓线的变化率小。
因此取圆柱凸轮的中径圆柱面作为理论设计的理论圆柱面。
即:
max
式中,一一圆柱凸轮旋转角速度;
一一摆杆从动件的角速度;
一一凸轮的压力角;
一一摆动从动件的摆角。
许用压力角〔a〕一般取35º
~45º
由上表数据,得:
Dˊ80,所以取凸轮直径D=85mm
5.1.5圆柱凸轮转向与摆动推杆位置的凸轮廓线方程
⑴理论轮廓线方程:
x=rpφ+Lcos(ψmax/2)-Lcos(ψmax/2-ψ)
y=Lsin(ψmax/2)-Lsin(ψmax/2-ψ)
式中,x、y为理论轮廓线上点的直角坐标;
rp为凸轮的平均圆柱半径;
φ为凸轮的转角;