材料成型及控制工程生产实习报告 第二部分共12页word资料.docx
《材料成型及控制工程生产实习报告 第二部分共12页word资料.docx》由会员分享,可在线阅读,更多相关《材料成型及控制工程生产实习报告 第二部分共12页word资料.docx(11页珍藏版)》请在冰豆网上搜索。
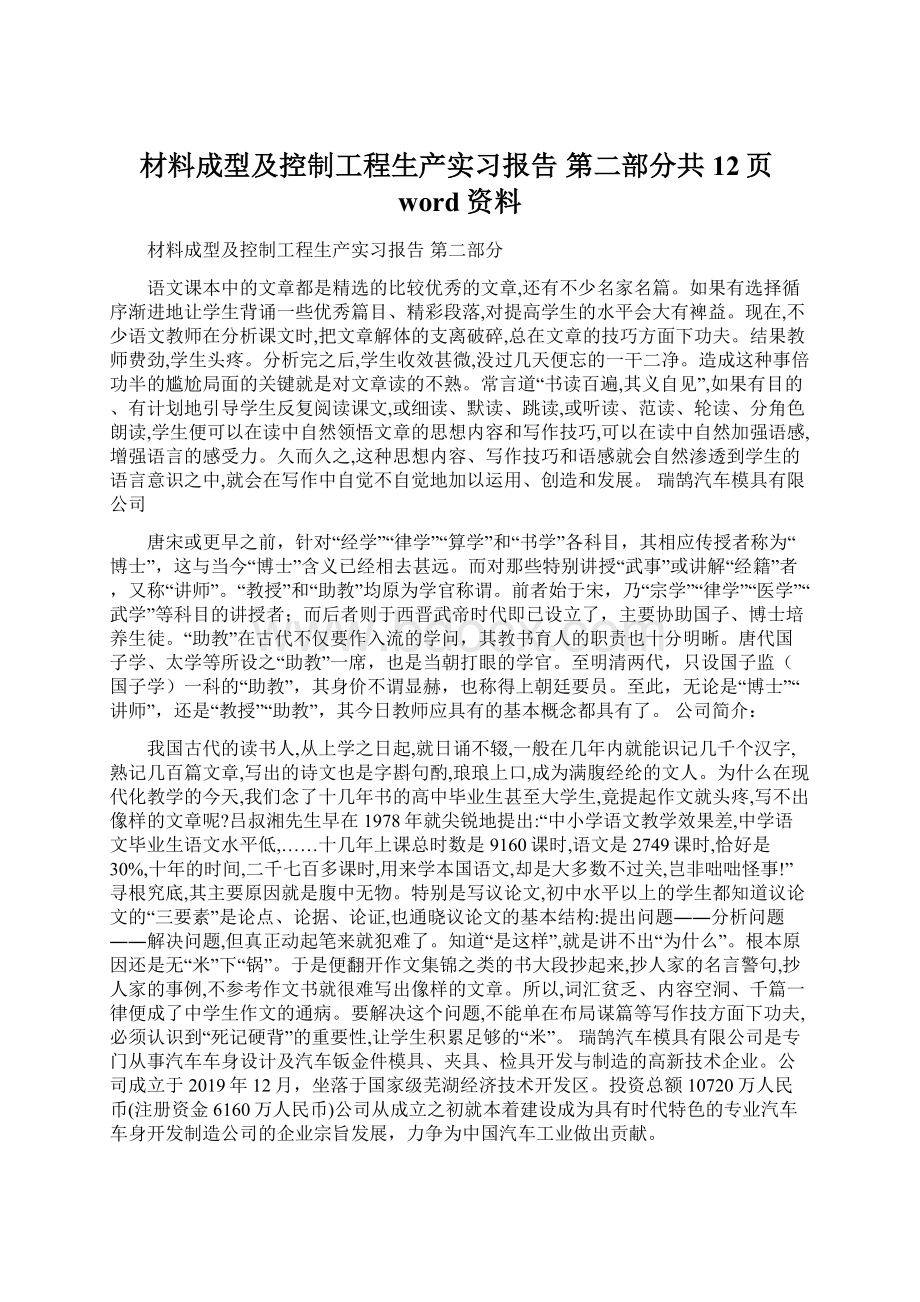
材料成型及控制工程生产实习报告第二部分共12页word资料
材料成型及控制工程生产实习报告第二部分
语文课本中的文章都是精选的比较优秀的文章,还有不少名家名篇。
如果有选择循序渐进地让学生背诵一些优秀篇目、精彩段落,对提高学生的水平会大有裨益。
现在,不少语文教师在分析课文时,把文章解体的支离破碎,总在文章的技巧方面下功夫。
结果教师费劲,学生头疼。
分析完之后,学生收效甚微,没过几天便忘的一干二净。
造成这种事倍功半的尴尬局面的关键就是对文章读的不熟。
常言道“书读百遍,其义自见”,如果有目的、有计划地引导学生反复阅读课文,或细读、默读、跳读,或听读、范读、轮读、分角色朗读,学生便可以在读中自然领悟文章的思想内容和写作技巧,可以在读中自然加强语感,增强语言的感受力。
久而久之,这种思想内容、写作技巧和语感就会自然渗透到学生的语言意识之中,就会在写作中自觉不自觉地加以运用、创造和发展。
瑞鹄汽车模具有限公司
唐宋或更早之前,针对“经学”“律学”“算学”和“书学”各科目,其相应传授者称为“博士”,这与当今“博士”含义已经相去甚远。
而对那些特别讲授“武事”或讲解“经籍”者,又称“讲师”。
“教授”和“助教”均原为学官称谓。
前者始于宋,乃“宗学”“律学”“医学”“武学”等科目的讲授者;而后者则于西晋武帝时代即已设立了,主要协助国子、博士培养生徒。
“助教”在古代不仅要作入流的学问,其教书育人的职责也十分明晰。
唐代国子学、太学等所设之“助教”一席,也是当朝打眼的学官。
至明清两代,只设国子监(国子学)一科的“助教”,其身价不谓显赫,也称得上朝廷要员。
至此,无论是“博士”“讲师”,还是“教授”“助教”,其今日教师应具有的基本概念都具有了。
公司简介:
我国古代的读书人,从上学之日起,就日诵不辍,一般在几年内就能识记几千个汉字,熟记几百篇文章,写出的诗文也是字斟句酌,琅琅上口,成为满腹经纶的文人。
为什么在现代化教学的今天,我们念了十几年书的高中毕业生甚至大学生,竟提起作文就头疼,写不出像样的文章呢?
吕叔湘先生早在1978年就尖锐地提出:
“中小学语文教学效果差,中学语文毕业生语文水平低,……十几年上课总时数是9160课时,语文是2749课时,恰好是30%,十年的时间,二千七百多课时,用来学本国语文,却是大多数不过关,岂非咄咄怪事!
”寻根究底,其主要原因就是腹中无物。
特别是写议论文,初中水平以上的学生都知道议论文的“三要素”是论点、论据、论证,也通晓议论文的基本结构:
提出问题――分析问题――解决问题,但真正动起笔来就犯难了。
知道“是这样”,就是讲不出“为什么”。
根本原因还是无“米”下“锅”。
于是便翻开作文集锦之类的书大段抄起来,抄人家的名言警句,抄人家的事例,不参考作文书就很难写出像样的文章。
所以,词汇贫乏、内容空洞、千篇一律便成了中学生作文的通病。
要解决这个问题,不能单在布局谋篇等写作技方面下功夫,必须认识到“死记硬背”的重要性,让学生积累足够的“米”。
瑞鹄汽车模具有限公司是专门从事汽车车身设计及汽车钣金件模具、夹具、检具开发与制造的高新技术企业。
公司成立于2019年12月,坐落于国家级芜湖经济技术开发区。
投资总额10720万人民币(注册资金6160万人民币)公司从成立之初就本着建设成为具有时代特色的专业汽车车身开发制造公司的企业宗旨发展,力争为中国汽车工业做出贡献。
该公司采用先进的设计技术,在汽车车身开发领域保持国内领先!
始终坚持以客户为中心,以人为本,回馈社会。
公司积极进行技术提升,以技术为基础,不断研发精进,大力引进专业化技术人才。
技术领先是我们追求的目标。
公司于2019年3月和日本富士株式会社签定了长期技术合作协议并每年多次派员赴日学习,并且日方长期派员驻厂指导。
公司主要业务范围包括从车身开发造型设计、油泥模型制作到模、夹、检具工装设备设计、制作、安装直至调试移交汽车厂投产等一系列环节。
公司拥有各类专业技术人才,确保了设计、生产的每一环节的质量。
公司成立至今已经有多个整车开发项目成功高质量的完成,并得到客户及市场的肯定。
汽车的发展离不开模、夹、检具,汽车工业的发展也会极大程度地推动模、夹具工业的发展。
相反的,只有模、夹具生产水平提高才能促进汽车制造水平提高。
公司正积极地加大对高新科技、先进设备和高级人才等软件、硬件的投入,企业已经达到了国际先进水平,拥有了一定的竞争力。
汽车行业是传统行业中最具发展潜力的行业,在国民经济持续稳定发展的中国更是不可限量。
一、概述
近年来,我国汽车工业的快速发展极大地带动了汽车模具行业的发展。
由于汽车模具是技术型产品和典型的定制产品,尤其是汽车覆盖件模具的技术含量非常高。
如何提高生产效率、缩短开发周期、提高模具技术水准、降低生产成本一直是模具企业面临的难题。
结合在中日合资汽车模具制造企业5年多的实践经历,我们想对目前汽车模具的生产技术谈一些体会,供大家探讨。
二、现代汽车模具制造基本流程
由于各个模具生产企业具体情况的不一样,以及承接到的业务的不同,各家企业汽车模具制造的具体流程不尽相同,目前汽车模具制造的基础流程基本如下:
冲压工艺模具设计NC编程实型制作铸造机械加工钳工装配模具调试;
三、模具生产技术准备阶段的一些新做法
1.充分利用整车厂资源
为缩短模具的开发周期,目前在模具生产的技术准备阶段,整车制造厂家一般都提供其整车或零件的设计版数模供模具制造厂家进行模具开发方案的策划、制定开发预算、计划和冲压工艺方案、开展DL图设计、进行拉延模初步设计和铸造实型加工等工作。
2.专业分工与经验积累的充分运用
现在汽车换型周期越来越短,按一年平均更换15个当量的车型计算,一个车型平均约需大中型覆盖件模具260套,平均每套模具约需2400个工时,一年需要有936万个工时的制造能力,所以一个模具企业想什么模具都干是不现实的,只有向只做几种件(只干车身内外覆盖件或者地板、甚至只做侧围、翼子板、顶盖等有限的几种外覆盖件)更专业方向发展才能找到自己生存发展的空间。
通过不段做自己熟悉的产品,才能不段提高技术加快速度;
同时模具设计技术都特别强调经验积累,利用数据的统一管理、设计标准、规范的经常性增改等办法,使公司在设计相同或相似的零件的模具时做的更好更快。
经验积累机制是不断提高模面设计的主要手段。
比如:
模具加工完成之后,一般模具型面不用研合,刃口不必对间隙,钳工只负责安装,在初次试模时也不能随便修调模具,调试模具有模面设计人员在场,初次试模缺陷需要记录下来。
最后的休整结果,像拉延筋、拉延圆角变动、对称件的不对称现象等,还要进行现场测量。
这些数据的积累、整理、分析、存盘,都是模面设计的经验积累,并随时加入到下一次的设计中去,借助于这种自我完善的经验积累机制,模具的设计越来越精细,越来越准确。
3.标准化
模具设计时尽量使用整车厂提供的或公司自己的模具设计标准数据库,包括单独零件的标准零件、含有装配结构的标准部件、模架结构数据库及典型模具结构数据库,供技术人员设计模具时调用拷贝,提高设计效率和模具标准件使用率,实现模具结构的规范化、系列化和标准化。
全面推广使用模具标准件,包括中小模具模架、冲切装置、导向装置、限位装置、定位装置、压退料装置、斜楔侧冲装置、气动装置和氮气弹簧、弹簧回程装置等对缩短交货周期、稳定模具质量能起至关重要的作用。
4.成型模拟技术的运用
目前在模具技术中应用有限元法做计算机模拟成型分析运用的越来越广泛。
主要应用的解算软件有AUTOFORM、dyna3D等,通过模拟能使整个生产过程少走弯路,进一步缩短交货周期。
5.对大规模生产的适应
A.提高材料利用率:
对于大批量汽车生产来说,提高板料的利用率是模具设计的第一大事。
只要把材料利用率提高几个百分点,模具的成本就可乎略不计了。
如果一套模具40万人民币,只相当于100吨钢板的价格,以寿命50万件计算,平均每件节约0.2Kg钢板,就足可节约出这套模具费用了。
B.减少冲压工序:
模具设计的趋势是,零件的合并,左右对称件合模,前后顺序件合模等等,原来几个件合成一个件,不同的件合在一套模,模具越来越大,单件工序大大减少,整车模具数量越来越少,这对降低冲压的成本起关键作用。
C.冲压自动化:
为适应冲压线完全自动化,模具必须考虑机械手上下料,废料的自动排出,气动、自动和传感装置普遍采用等等。
D.模具的快速装换:
冲压线的换模时间,也成为一个模具设计必须考虑的问题。
如:
拉延模完全以单动代替双动,模具自动卡紧,换模不换气顶杆等等。
6.模具材料的选用
不同整车厂对模具材料的选用都有不同的要求,目前一般的拉延模材料主要采用球墨铸铁而不是合金铸铁。
球墨铸铁焊接性能、可加工性能好、耐磨性能和表面淬火硬度都比较理想,而成本比合金铸铁要低得多了。
修边刃口材料,选用型材镶块而不是符型的铸钢,主要是因为铸钢成本要高得多。
大量采用基体与刃口一体化的特殊铸铁材料作修边模,使模具的机加工成本大为降低。
请注意这里的刃口既不堆焊,也不是钢材,铸铁整体刃口只经表面火焰淬火,直接用于几十万次寿命的薄板料修边模。
而且这种铸件的成本还不高。
四、模具生产制造过程中的一些新特点:
1.生产组织的并行
目前在模具的生产组织中,并行工程运用广泛。
一般在模具开发过程中的技术准备、生产准备、模具加工和调试各工序之间尽可能地实行并行,即生产准备、加工工艺及数控程序设计并行。
生产计划一定要首先安排拉延、成型类模具,其次是翻边整型类模具,然后是修边冲孔类模具,最后是落料冲孔类模具,唯有这样才能做到均衡生产,提前给汽车厂提供样件;
2.实型的数控加工
目前各模具制造厂家已基本都在使用实型制作工艺。
实型的数控化加工生产,就是通过对实体模型的工艺编辑(如:
加工面贴加工余量,模型分层编辑等),再经过数控编程,泡沫毛坯下料,数控加工,人工粘接和修整等几道工序完成的。
从而将实型的生产员工从手工制作转变到大量的数控编程上来了,现场的简单人工粘接和修整工作,由临时工所充当。
实型的数控化生产直接提高了铸件的精度,为后序的精细加工带来极大的优势。
3.机械加工中粗精加工分开进行
汽车模具企业的加工设备的突出特点为"多、大、精"。
所谓"多",是因为汽车模具结构复杂,加工工序多,各工序都需要一定数量的加工设备。
大型关键设备主要有三轴以上的数控铣床、研配压床、试模压力机、五轴数控激光切割机、三坐标测量机等。
所谓"大",是因为现在汽车制造水平越来越高,车身装焊工艺越来越简单,冲压件分块越来越大,使得冲压模具也越来越大,越来越复杂,因此开发模具的各种加工设备都很大,工作范围一般在2000mm×4000mm以上。
所谓"精",模具加工设备必须具备精度高、功能多等特点,如五轴联动数控铣床及高速精密数控铣。
通过调整生产组织方式和加工流程能够缓解企业的投资压力,降低模具开发成本。
采用粗加工和精加工分开进行可满足这一要求,粗加工在大陆或台湾设备上进行,精加工在欧美设备上进行。
大陆或台湾的数控铣床的刚性好、价格低(为欧美设备价格的1/5~1/3)、滑枕尺寸大、主轴电机功率高、转速低,用来粗加工。
五轴联动高速铣床主要从欧美进口,具有设备投入大、主轴转速高、进给速度快、加工精度高等特点,能够满足精细化加工要求,只用来精加工。
一般由4台粗加工设备和1台精加工设备组成一个加工单元,即一个模具企业要达到合理的规模和一定的水平,数控铣床不应小于5台,根据数控铣床的加工能力来配置人员和其它设备。
4.精细化加工一次到位
精细化加工的目的是大大减少钳工研修,一次加工到位,降低反复加工、后序弥补、人工修整及模具品质对钳工技艺的依赖等。
如上下模刃口间隙直接加工到位,不用钳工开间隙;冲孔凸/凹模直接安装无需调试;拉延模型面的高光顺性无接刀痕迹,减少研合;内覆盖件拉延模不用去刀痕,不推磨;凹圆角过切加工,不用清根等。
通过精细化加工和采用高水平的标准件,再使零件的加工基准和装配基准一致,实现钳工制造的只装不配少修,即所谓的"直接装配法",是现代模具生产的管理方向。
实现精细化加工要从模具