毕业设计方案英文翻译译文Word格式文档下载.docx
《毕业设计方案英文翻译译文Word格式文档下载.docx》由会员分享,可在线阅读,更多相关《毕业设计方案英文翻译译文Word格式文档下载.docx(18页珍藏版)》请在冰豆网上搜索。
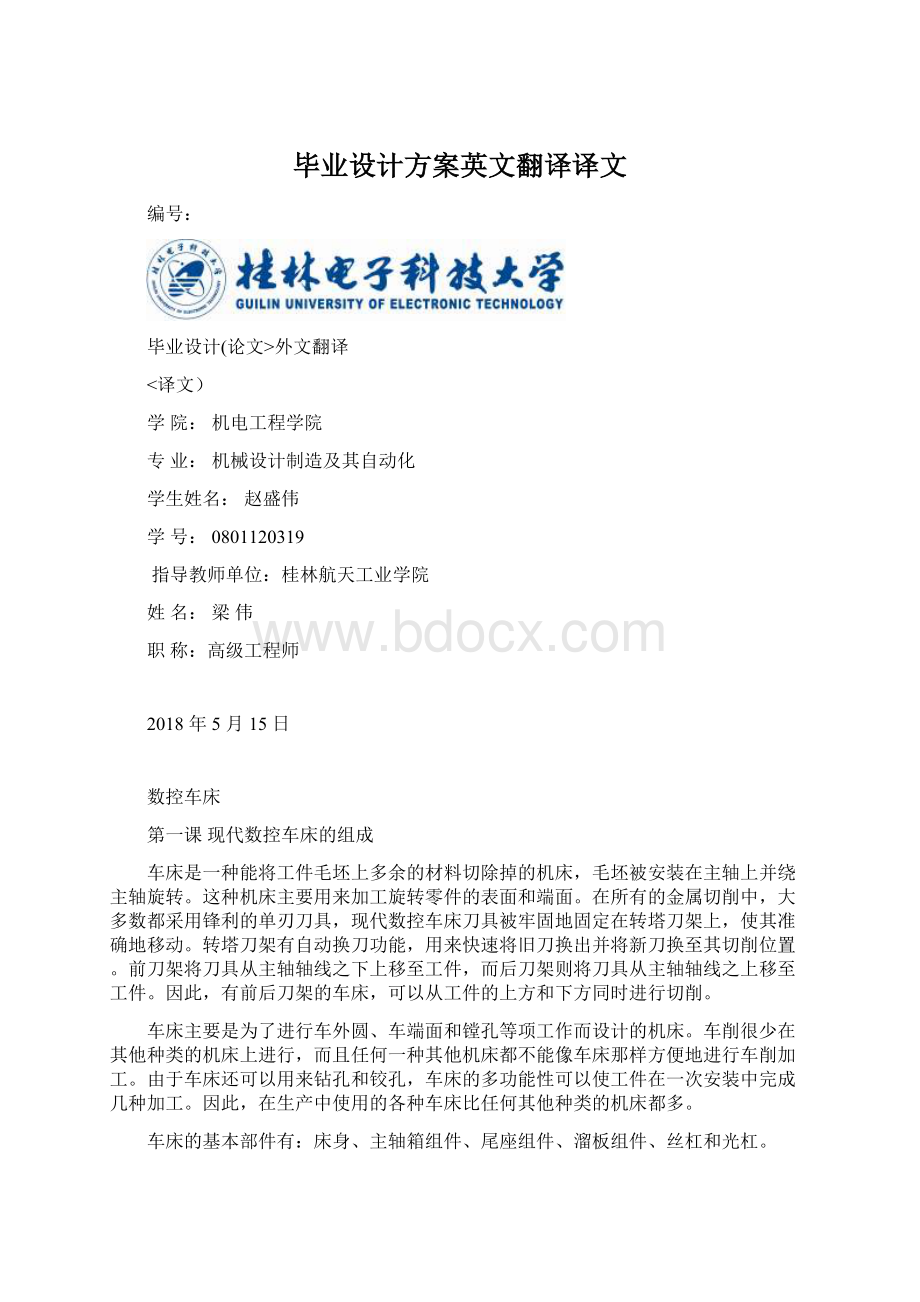
有些制造厂对全部四条导轨都采用导轨尖朝上的三角形导轨<
即山形导轨),而有的制造厂则在一组或者两组中采用一个三角形导轨和一个矩形导轨。
导轨要经过精密加工以保证其直线度精度。
为了抵抗磨损和擦伤,大多数现代机床的导轨是经过表面淬硬的,但是在操作时还应该小心,以避免损伤导轨。
导轨上的任何误差,常常意味着整个机床的精度遭到破坏。
主轴箱安装在内侧导轨的固定位置上,一般在床身的左端。
它提供动力,并可使工件在各种速度下回转。
它基本上由一个安装在精密轴承中的空心主轴和一系列变速齿轮(类似于卡车变速箱>
所组成。
通过变速齿轮,主轴可以在多种转速下旋转。
大多数车床有8~12种转速,一般按等比级数排列。
而且在现代机床上只需扳动2~4个手柄,就能得到全部转速。
一种正在不断增长的趋势是通过电气的或者机械的装置进行无级变速。
由于机床的精度在很大程度上取决于主轴,因此,主轴的结构尺寸较大,通常安装在预紧后的重型圆锥滚子轴承或球轴承中。
主轴中有一个贯穿全长的通孔,长棒料可以通过该孔送料。
主轴孔的大小是车床的一个重要尺寸,因此当工件必须通过主轴孔供料时,它确定了能够加工的棒料毛坯的最大尺寸。
尾座组件主要由三部分组成。
底板与床身的内侧导轨配合,并可以在导轨上作纵向移动。
底板上有一个可以使整个尾座组件夹紧在任意位置上的装置。
尾座体安装在底板上,可以沿某种类型的键槽在底板上横向移动,使尾座能与主轴箱中的主轴对正。
尾座的第三个组成部分是尾座套筒。
它是一个直径通常大约在51~76mm<
2~3英寸)之间的钢制空心圆柱体。
通过手轮和螺杆,尾座套筒可以在尾座体中纵向移入和移出几个英寸。
车床的规格用两个尺寸表示。
第一个称为车床的床面上最大加工直径。
这是在车床上能够旋转的工件的最大直径。
它大约是两顶尖连线与导轨上最近点之间距离的两倍。
第二个规格尺寸是两顶尖之间的最大距离。
车床床面上最大加工直径表示在车床上能够车削的最大工件直径,而两顶尖之间的最大距离则表示在两个顶尖之间能够安装的工件的最大长度。
普通车床是生产中最经常使用的车床种类。
它们是具有前面所叙的所有那些部件的重载机床,并且除了小刀架之外,全部刀具的运动都有机动进给。
它们的规格通常是:
车床床面上最大加工直径为305~610mm<
12~24英寸);
但是,床面上最大加工直径达到1270mm<
50英寸)和两顶尖之间距离达到3658mm的车床也并不少见。
这些车床大部分都有切屑盘和一个安装在内部的冷却液循环系统。
小型的普通车床—车床床面最大加工直径一般不超过330mm<
13英寸)--被设计成台式车床,其床身安装在工作台或柜子上。
虽然普通车床有很多用途,是很有用的机床,但是更换和调整刀具以及测量工件花费很多时间,所以它们不适合在大量生产中应用。
通常,它们的实际加工时间少于其总加工时间的30%。
此外,需要技术熟练的工人来操作普通车床,这种工人的工资高而且很难雇到。
然而,操作工人的大部分时间却花费在简单的重复调整和观察切屑过程上。
因此,为了减少或者完全不雇用这类熟练工人,六角车床、螺纹加工车床和其他类型的半自动和自动车床已经很好地研制出来,并已经在生产中得到广泛应用。
普通车床作为最早的金属切削机床的一种,目前仍然有许多有用的和为人要的特性和为人们所需的特性。
现在,这些机床主要用在规模较小的工厂中,进行小批量的生产,而不是进行大批量的和产。
在现代的生产车间中,普通车床已经被种类繁多的自动车床所取代,诸如自动仿形车床,六角车床和自动螺丝车床。
现在,设计人员已经熟知先利用单刃刀具去除大量的金属余量,然后利用成型刀具获得表面光洁度和精度这种加工方法的优点。
这种加工方法的生产速度与现在工厂中使用的最快的加工设备的速度相同。
普通车床的加偏差主要信赖于操作者的技术熟练程度。
设计工程师应该认真地确定由熟练工人在普通车床上加工的实验件的公差。
在把实验伯重新设计为生产零件时,应该选用经济的公差。
六角车床对生产加工设备来说,目前比过去更注重评价其是否具有精确的和快速的重复加工能力。
应用这个标准来评价具体的加工方法,六角车床可以获得较高的质量评定。
在为小批量的零件<
100~200件)设计加工方法时,采用六角车床是最经济的。
为了在六角车床上获得尽可能小的公差值,设计人员应该尽量将加工工序的数目减至最少。
自动螺丝车床自动螺丝车床通被分为以下几种类型:
单轴自动、多轴自动和自动夹紧车床。
自动螺丝车床最初是被用来对螺钉和类似的带有螺纹的零件进行自动化和快速加工的。
但是,这种车床的用途早就超过了这个狭窄的范围。
现在,它在许多种类的精密零件的大批量生产中起着重要的作用。
工件的数量对采用自动螺丝车床所加工的零件的经济性有较大的影响。
如果工件的数量少于1000件,在六角车床上进行加工比在自动螺丝车床上加工要经济得多。
如果计算出最小经济批量,并且针对工件批量正确地选择机床,就会降低零件的加工成本。
自动仿形车床因为零件的表面粗糙度在很大程度上取决于工件材料、刀具、进给量和切削速度,采用自动仿形车床加工所得到的最小公差一定是最经济的公差。
在某些情况下,在连续生产过程中,只进行一次切削加工时的公差可以达到0.05mm。
对于某些零件,槽宽的公差可以达到0.125mm。
镗孔和休用单刃刀具进行精加工时,公差可达到0.0125mm。
在希望获得最大主量的大批量生产中,进行直径和长度的车削时的最小公差值为0.125mm是经济的。
车床有以下几个部分组成:
1.倾斜的床身
床身是机床的基体,用来支承安装在它上面的所有零件,并且给落下的切屑提供路径。
床身一般都做成倾斜式的,目的是让切屑很容易地落下来。
为了衰减振动,车床床身通常是由灰铸铁或者球墨铸铁铸造而成的。
床身上有导轨,可以使拖板沿其长度方向滑动。
床身的高度应该合适,使技术人员能够容易且舒适地进行操作。
2.主轴箱
主轴箱安装在床身的左侧,里面包括主轴和能提供许多不同主轴转速的变速齿轮<
也有一些使用摩擦力、电力或者液力以提供可变的主轴转速)。
主轴是通过变速箱驱动的。
它提供动力,并可使
工件在各种速度下回转。
3.支架
支架的功用主要是连接主轴并夹紧工件。
4.拖板
拖板是功用主要是将刀具向旋转着的工件移动。
包括床鞍、横向拖板和拖板箱。
5.尾架
尾架主要用来支撑工件的右端。
6.加工控制单元
由电子控制软件组成,读取和说明指令程序并将其转化成机床的机械运动或者其他处理设备的运动。
简单地说,MCU就是一个用来存储和处理输入的数字控制程序的计算机。
7.转塔刀架
不同的加工操作需要不同的刀具,转塔刀架就是用来夹持刀具并且在换刀过程中用新的刀具代替旧刀具。
大家都知道,数控车床上的转塔刀架主要是在需要的时候,迅速更换刀具。
因为大多数情况下,生产一个零件往往需要好几种刀具。
目前使用过的刀具必须快速被替换以进行接下来的加工操作。
基于这个原因,大多数的数控机床配备有自动换刀器,比如加工中心上配有刀库,数控车床上配有转塔刀架等。
他们允许在操作不中断的情况下换刀。
通常,自动换刀器用它的机械手将刀具夹紧,并拉出来用另外一个刀具替换。
在大多数有自动换刀器的机床上,转塔刀架可以向前或者向后任意转动。
转塔刀具上的每一把刀具都有编号,以区别于刀架上的其他刀具。
刀具可以安装在刀架正面,也可以安装在刀架侧面。
一旦接收到从MCU发出的换刀指令,刀架就移动到安全的换刀位置,找到并拉出旧的刀具,再换上新刀,然后继续移动到程序规定的用新刀切削工件的位置。
对于装备有可编程尾架的车削中心来说,在执行换刀操作之前,尾架必须先退回。
第二课数控车床的运动轴
CNC设备是通过多种直线运动和旋转运动完成某种加工操作的。
不同的机床的不同的运动,具体的运动方式是根据机床要制造的零件设计的,例如:
工作台可以在水平面运动<
沿X轴、Y轴线运动),主轴可以在垂直上运动<
沿Z轴线运动)。
基本的机床轴线运动应该遵守右手定则。
比如,主轴的运动基本上是沿着+Z轴方向的。
这个系统响应这样一种指令,主轴沿着+X或者+Y方向的运动要通过工作台沿着相反的方向即—X或者—Y方向的运动来实现。
我们讨论CNC车床时,在本文中只考虑基本的两轴运动。
数控车床中最重要的两个轴是Z轴和X轴。
Z轴表示沿着主轴轴线方向。
+Z表示远离主轴或者工件的方向,-Z表示靠近主轴或工件的方向。
X轴表示沿着横向托板运动方向。
+X表示远离主轴轴线的方向,-X表示靠近主轴轴线或者进入工件的方向。
除了Z轴和X轴,有些机床具有可编程尾座,用W轴表示尾座的运动,这时W轴就是这类机床的第三轴。
更复杂的车削中心也可以有第四个轴。
第三课数控车床加工用刀具
现代刀具技术已经主生了带有可转位硬质合金刀片的刀具,虽然这些刀具的初始研制投资有点高,但是从长远的利益来看,它们却节省了工作时间和刀具的重磨费用。
用坏的刀片只需要用工厂预定的新刀换掉就可以了。
只要改变机夹刀片的规格级别,就可以用同一把刀具加工不同的材料,因此刀具库存量也减少了。
高强度的硬质合金刀片使得刀具可以切削很硬的工件材料,然而,很大的切削要求有足够的主轴动力,因此机床必须有足够的刚度。
硬质合金刀片的主要缺点是它们的脆性和对振动有敏感性,因此,如果使用不当,会引起刀片的破损和开裂。
使用硬质合金刀片有很多优点。
首先,它具有高速切削能力<
大约比高速刚速度高2~3倍),此外还能减少刀具的库存量和节省重磨时间和费用。
单点刀具和另外一个优点是用于切削的机夹刀片的刀尖圆弧半径数值十分精确。
这样,对于任何刀具,它的刀尖圆弧的中心都可以精确地确定。
这就使得刀具补偿和数控编程工作更加简单。
1.刀片材料
关于车削加工,有四种重要材料可以用来做刀片:
(1>
硬质合金
硬质合金是通过有晶格中烧结碳化钨形成的。
(2>
涂层硬质合金
给硬质合金刀片镀一层耐磨材料可以使其耐磨提高200%~500%。
涂层材料包括碳化钛和氧化铝<
一种陶瓷)。
涂层工艺还给钢、铸铁以及非铁材料提供了优良性能。
(3>
陶瓷
陶瓷是一种不含有金属结合的非常硬的材料。
它具有优越的抵抗磨损和热负荷的能力。
形成陶瓷的最常用的材料是氧化铝。
经常向氧化铝里面加入诸如碳化钛或氧化钛的添加剂,可以用很高的切削速度加工很硬的材料,而且几乎不会影响刀具寿命。
另外,它加工出的表面质量也比其他材料的刀具加工出的好。
陶瓷的主要缺点是它们的耐冲击和耐振动性差,如此一来,仅能用于冲击载荷比较低的加工中。
(4>
金刚石
有两种类型的的金刚石刀具材料。
一种是单晶天然金刚石片,它有很强的耐磨性但抗冲击性差。
另外一种是由较小的人造金刚石晶体在高温、高压下与碳化物基材料溶合而成的。
这种材料具有比较好的抗冲击载荷的能力。
金刚石刀具比硬质合金刀具有了很大的改善。
在刀具寿命得到很大改善的前提下,可以用很高的切削速度得到比较好的加工表面。
2.刀片形状
刀片有不同的形状和尺寸。
刀片的形状决定了它的强度和切削刃的数目。
车削加工所使用的刀片主要有六种:
圆形刀片、六边形刀片、方形刀片、平行四边形刀片、菱形刀片和三角形刀片。
其中最硬的是圆形刀片,然后是六边形刀片、方形刀片、平行四边形刀片、菱形刀片和三角形刀片。
因为这些刀具非常坚硬,所以使用时可以得到比较高的精度等级。
当硬质合金刀具用于镗削时,也可以磨出更精确的刀尖圆弧直径,同时可以缩短磨削时间。
根据所切削的材料,切削速度经常可以提高2~3倍,进给量也可以增加25%或者更多。
为车削加工选择刀片时,可参考发以下原则:
(1)尽可能选择强度最高的刀片形状;
(2)选择最小的刀片尺寸;
(3)尽可能选择最大的刀尖圆弧半径;
(4)选择柄径最大、悬臂最小的镗刀。
第四课车床的基本操作
本课将讨论最基本的车床操作:
车端面、车外圆、车槽、切断、钻孔、镗孔和车螺纹。
其中有一些切削是要在零件的外表面<
用OD表示)和内表面<
用ID表示)上完成。
1.端面车削
端面车削得到的是一个平面,既可以是工件的整个端面,也可以是类似轴肩的环状中间平面。
这种操作只切削毛坯的顶端,这样产生的端面垂直于毛坯的中心线,也比较光滑,刀具以垂直天工件中心线的方向进给。
在端面车削过程中,进给是由横向拖板提给的,而切削深度是由拖板或者复合支架控制的,在端面车削中,刀具通常被夹在拖板上,防止切削力将刀具推离工件,在大多数的端面的车削中,工件都是被装夹在支架或者法兰盘上的。
2.外圆车削
外圆车削是沿着旋转工件的外圆去除多余的材料。
这种操作可以产生不同的轮廓外形,包括圆柱、圆锥面、成形面以及轴肩。
圆柱车削是所有车削加工最简单和常见的。
工件旋转一周可以产生一个圈,其圆心落在车床主轴轴线上;
轴线进给使得这个运动一次次重复。
最终,已加工表面就是一个圆柱面。
一般先粗加工一次,再跟一道或几道精加工。
3.切槽和切断
在切槽和切断操作中,刀具只有横向进给,也就是说,这两种操作都要求刀具沿着垂直工件轴线的方向进给。
切削刃在刀具的一端,车螺纹之前通常要有退刀槽,从而保证螺纹与轴肩完全切合。
切断指从棒形主材上切下零件。
切断操作使用切断刀,切断刀是一端有切削刃锥形体。
刀具沿着垂直工件的方向进给,直到零件彻底从棒形主材上分离下来为止。
4.钻孔
钻削加工通常都是在钻床是完成的。
有时钻削加工也可以在车床上完成,加工时,工件被装在夹头里并随着夹头一起旋转。
钻头通常安装在钻头卡盘或轴衬中,并向旋转的工件进给。
使用高速钢的螺旋钻配备中心钻,但如果使用扁钻或硬质合金钻就没在这个必要了。
中心钻中能用来扩大预先加工的孔,而不能在实体材料上钻孔。
中心钻的特点是有较高的生产力、较高的加工精度和优良的钻削表面质量。
5.镗削加工
镗削加工是一种内圆加工。
这种操作是用镗杆或者合适的内圆加工刀具在工件内表面完成的。
如果工件的初始状态是实体的,则需要先进行钻削加工。
这时,钻头被装夹在尾座里并向工件进给。
镗孔可以使孔的尺寸更精确、圆度更高,此外还能加工内部锥度和轮廓。
6.螺纹车削
当进行螺纹车削时,车床主轴必须保持一个不变的转速决定。
两者之间的关系主要取决于所要切削的螺距大小。
这种包括在圆柱或圆锥体的外表面或者内表面切削出螺纹槽。
这些螺旋线一般都有一定的角度,多为
。
两个齿形之间的距离叫做螺距。
刀具向工件材料进刀时,其切削通常为
,进给方向与工件的中心线垂直,进给率等于螺距。
在切削螺纹操作中,工件也可被夹持在夹盘里,所使用的刀具形式必须和将要切削的螺旋线轮廓精确符合,例如,三角形刀具必须用来切削三角形螺纹等。
第五课车削加工的切削速度和进给量
对于车削来加工来说,刀具速度定义为工件边缘上一点经过刀具的线速度。
它在数值上等于每1min内工件边缘上的指定点沿切线方向移动的距离。
工件表面的速度与其转速之间的关系如下:
切削速度=
式中D——工件的外径;
N——机床主轴的转速。
表面切削速度主要取决于被加工材料和切削刀具的材质,这个数值可以从切削工具制造商所提供的手册和资料上查到。
还有一些可变因数会影响切削速度的最佳值,包括刀具的几何参数、所用润滑或冷却液的类型、进给量和切削深度。
刀具进给率是指工件每转一周,刀具相对工件的进给速率。
进给量的多少取决于许多因素,例如要求的已加工表面、切削深度和所采用的刀具几何参数。
比较小的进给量能产生较好的已加工表面,而在刀具和工件直接接触期间,比较大的进给量能减少加工时间。
因此,一般情况下,常常使用较大的进给量进行粗加工,而使用较小的进给量进行精加工。
再一次说明,从手册中可以得到加工制造者所提供的推荐进给量值,仅作为参考。
第六课车削加工中的一些定义
1.进给方向
右手刀具通常沿着主轴轴线方向从右向左进刀,左手刀具正好相反。
2.术语
用于车外圆和端面的单点刀具的刀刃必须有一些特定角度,这样可以延长刀具的寿命并提高切削效率。
这些角度可在图6-1中找出,图6-1有以下一些角度:
(1)刀具圆弧半径:
有刀尖圆弧半径的刀具产生令人满意的已加工表面,而且能延长刀具的寿命。
(2)切深方向前角:
切深方向前角在刀具上的作用是引导切屑离开工件并流向刀架。
这个角度做在硬质合金刀片的顶面和沿长度方向的刀杆之间。
(3)进给方向前角:
进给方向前角在刀具上的作用是引导切屑离开工件并流向刀具的一面,这个角度做在硬质合金刀片的顶面和沿宽度方向的刀杆之间。
(4)进给方向后角:
切深方向后角使刀具的侧面进入工件进行<
切削)。
(5)切深方向后角:
切深方向后角使刀具的端面进入工件进行<
(6)主偏角:
在切削过程中,主偏角能提高刀具的剪切力并产生比较薄的切屑。
(7)副偏角:
在车削过程中,副偏角能使刀具和工件之间保持一定的距离。
3.前角和切削力
如前所述,刀具的前角有助于清除切屑。
此角度也有助于保护刀具免受过多的热载荷与摩擦作用。
在大多数情况下,使用来产生负的前角和进给方向前角。
对于较软的材料和较脆的零件,一般采用正的前角和进给方向前角<
参考图图6-2)。
图6-2前角和切削力
摘要
精密车床主轴箱的最佳设计进行了研究。
三种不同的外部形状主轴箱探索。
由于热变形产生的热量是主轴轴承所考虑的。
我们的目标是尽量减少在切削点的工件整体变形。
约束是强制的基本自然频率,比工作频率更高,以降低动态挠度。
设计变量包括外形尺寸,主轴轴承的位置,主轴轴承的刚度,散热片的尺寸和散热片的位置。
利用遗传算法来解决这些混合变量优化问题。
通过三个不同类型的主轴箱,发现和讨论最佳的解决方案。
关键词:
优化设计;
车床主轴箱
文章概要
1.简介
2.遗传算法
3.发热和轴承的刚度
4.设计实例
4.1.1例1:
I型启闭
4.1.2例2:
II型启闭
4.1.3例3:
III型启闭
5.结论
参考文献
精密车床主轴箱的优化设计
1.简介众所周知,为了设计一个高品质精密车床,静态和动态载荷必须加以考虑。
该车床的静态和动态刚度对工件的几何形状,加工精度的影响。
在以前的研究中,最常用的参数,优化主轴刚度,主轴轴承数量的安排。
除了这些加工过程的精度,也由工件的几何结构参数和直径的影响。
最近的研究表明,在切割过程主轴轴承产生的热量也是造成加工误差的主要因素。
该结构中的温度分布是由热源,传导结构材料的系数,对流结构和空中接口几何系数。
因此,一个全面的解决方案,设计精密车床应该包括上述所有因素。
本文的目的是在最佳的设计过程中包括精密车床最大产量,刚度主轴箱大多数参数。
设计变量使用的径向和轴向的主轴轴承刚度,这些轴承的部位,车头形状,散热片的位置和散热片的尺寸。
这种优化设计的目标是尽量减少工件的整体变形和约束,需要从根本上启闭自然频率,要远远高于运行速度。
工件的变形是由于立体静态切削力以及车头的热变形。
主要热源假设来自三个主轴轴承,热传导和对流两种传输也需考虑。
由于一些设计变量是离散变量,有些是连续变量,优化问题是一个混合变数的问题。
遗传算法<
GA)是采用的最佳解决方案。
2.遗传算法
遗传算法已被广泛应用于近年来的各个领域。
三个主要业务是建立了模拟的生物世界自然演化过程。
该复制操作的父代更好的选择个人和再现他们的后代一代。
通过这一行动,在后人中更好的人的比例将逐渐增加。
交叉操作负责的是由父母之间基因互换产生新的后代。
新的后代有些可能是比他们的父母更好,但是有些人可能会更糟。
更好的将有更大的机会在下一代服务繁殖力的行动。
该行动旨在恢复突变在其他两个操作失去有用的遗传模式。
在这次行动中,通过改变一个人基因中一个非常小的随机过程和概率创建一个新的个人。
同样,这可能是更好的新的个人或比原来的差。
如果是更好,这将有一个接受手术繁殖的好机会。
由于变异操作,不如其他两个操作重要的是突变率通常很低。
重复执行这些操作,好几代人创建和最佳的个人将最终出现。
要实现一个遗传算法通常使用二进制字符串。
一代中的每一个二进制字符串代表一个人。
在每个设计变量占用一个字符串中指定位的特定位置和长度。
每个设计变量的二进制值表示该变量的编码值。
该设计变量的实际值可以通过一个解码公式获得。
由于二进制变量的值是整数和离散的,具备了遗传算法的性质,用它来解决离散变量问题。
然而,总是可以连续变量离散化,划分为许多离散点之间的上限和下限,因此遗传算法仍然可以被用来获取具有连续变量的最优解。
一般的数学优化公式如下
目标功能,
和
是平等的和不平等的限制,xk代表第k个设计变量,P,M和ndv代表平等的约束,不等式约束和设计变量的数目。
xlk和xuk是第k个设计变量的下限和上限。
由于遗传算法是一种无约束最大化算法,使用GA约束优化问题首先转换为一个无约束问题。
它的外部函数通过转换的方法来进行。
原来的目标函数
是增加了一个项,形成了新的目标函数
其中r是给定的参数,如果是违反约束
,否则
很明显,如果没有约束冲突,等式2是没有原来的目标函数。
另一方面,较大的约束违规时,考虑到较大的原始成本函数的罚项。
最终在最佳的罚项,收益率应该成为零一个可行的办法。
对于最小化问题,增广目标函数<
公式2)进一步转化为
其中fmax是一个常量,它比最大的
一代更大。
转换后的目标函数
作为适应度函数来解决约束优化问题,使用遗传算法。
3.发热和轴承的刚度在机床操作的主要热源,包括切割过程中热量和主轴轴承产生的热量。
据推测,大部分的切削热是由冷却液通过主轴产生,因此产生的热量带走主要是轴承热引起的热变形。
Hf=1.047×
10−4nMn是轴承<
转)旋转速度,M是总的轴承<
不适用毫M),摩擦产生的扭矩和Hf<
W)的热量。
式中的摩擦力矩M是两个力矩的总和。
其一是由于扭矩载荷,另一条是扭矩润滑油黏度。
(5>
Ml=f1p1dmf1是关系到一个轴承类型和负荷因子,p1是轴承的负荷<
N),dm是轴承<
毫M)的平均直径(6>
Mv=10−7f0(ν0n>
2/3d3如果ν0n≥2000(7>
Mv=160×
10−7f0d3如果ν0n<
2000F0是与轴承类型和润滑方法,ν0是润滑油运动粘度(mm2/s>
(8>
C=KdC是径