机械制造工程原理说明书Word下载.docx
《机械制造工程原理说明书Word下载.docx》由会员分享,可在线阅读,更多相关《机械制造工程原理说明书Word下载.docx(17页珍藏版)》请在冰豆网上搜索。
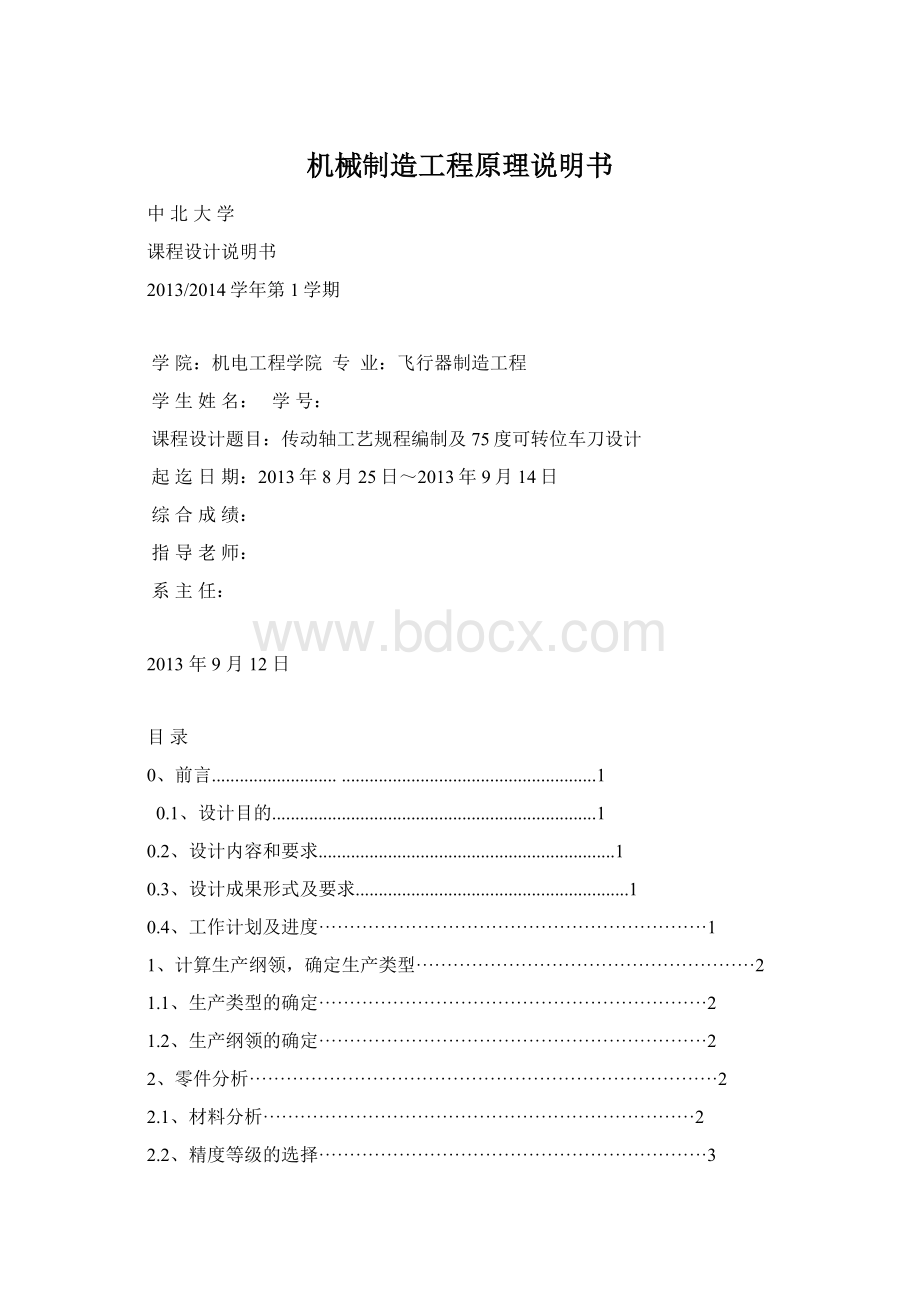
5
5.2.1、机械加工工序·
5.2.1、热处理加工工序·
6、余量与工艺尺寸的确定·
7、选择加工设备及工艺装备·
6
8、切削用量的确定·
7
9、刀具的设计·
9.1.选择刀片夹固结构·
9.2.选择刀片材料·
9.3.选择车刀合理角度·
9.4.选择切削用量·
9.5,选择刀片型号和尺寸·
9.6.确定刀垫型号和尺寸·
8
9.7.刀具角度换算·
9.8.选择刀杆材料和尺寸·
11
9.9.选择偏心角及其相关尺寸·
总结·
参考文献·
12
0、前言
0.1、设计目的
通过《机械制造工程原理》课程设计,锻炼学生查阅资料,查阅国标手册的能力;
培养创新能力,提高工艺设计能力、动手能力和初步的科学研究能力;
为以后的毕业设计和工作奠定基础
所加工的传动轴如下图所示
0.2、设计内容和要求(包括原始数据、技术参数、条件、设计要求等):
提供零件图1张,材料:
Cr40,生产纲领:
10000件/年,根据图纸参数、技术要求等编制工艺规程,并设计75。
机夹可转位车刀,并绘制图纸
0.3、设计成果形式及要求:
提供车刀设计图纸一套:
工艺规程一套;
设计说明书一份。
0.4、工作计划及进度:
2013年8月25日~8月28日查阅资料,熟悉任务书要求,绘制零件图
2013年8月29日~8月4日编制工艺规程
2013年9月5日~9月10日设计车刀
2013年9月11日~9月12日撰写设计说明书
2013年9月13日~8月15日答辩,成绩考核
1、计算生产纲领,确定生产类型
1.1、生产类型的确定
(1)零件的生产类型是指企业生产专业化程度的分类,它对工艺规程的制定具有决定性的影响。
机械制造的生产类型一般分为大量生产、成批生产和单件生产,成批生产分为大批生产、中批生产、和小批生产。
产量越大生产专业化程度越高。
按重型机械、中型机械、和轻型机械的年生产量列出了不同的生产类型的规范如表1
表1各种生产类型的规范
生产类型
零件的年生产纲领/件/年
重型机械
中型机械
轻型机械
单件生产
≤5
≤20
≤100
小批生产
5~100
20~200
100~500
中批生产
100~300
200~500
500~5000
大批生产
300~1000
5000~50000
大量生产
>1000
>5000
>50000
(2)生产类型的划分要考虑生产纲领还得考虑产品本身的大小及其结构的复杂性。
1.2、生产纲领的确定
(1)生产纲领是产品的年生产量。
生产纲领的大小对生产组织和零件加工工艺规程起着很重要的作用,它决定了各工序所需的专业化和自动化的程度以及所选用的工艺方法和工艺装备。
生产纲领是由生产类型决定的
(2)根据任务书上所说的,该产品的年生产量为10000件\年,查上表可知,生产类型为单件大批生产
2、零件分析
2.1、材料分析
本课程设计的轴所用的材料为40Cr钢
40Cr钢用于较重要的调质零件,如连杆、螺栓、进气阀、重要齿轮、轴、曲轴、曲柄、汽轮发电机环形锻件。
本课程设计中该材料用于传动轴的制造,其表面淬火硬度HBS范围在297和327之间
2.2、精度等级的选择
经查表零件图得知,查《互换性与测量技术基础》书本表2-2可知,在本工件的公差最大为0.011mm,最大公差等级为IT5。
表面粗糙度最高要求为0.8。
而没有公差要求的一些加工表面,所选择的公差等级为IT11.
2.3、热处理要求
热处理要求的种类有:
调质、正火、退火、淬火、渗碳淬火、渗氮等。
而本工件的要求是调质,故选用调质处理,即淬火加高温回火。
调质可以有效的提高工件的综合机械性能。
硬度的表示方法有布式硬度、洛式硬度、维式硬度。
而本工件是选用布式硬度表示的(HBS297-327)。
3、毛坯的确定
3.1、毛皮种类可分五种:
(1)铸件:
适用于形状较复杂的零件毛坯,其铸造方法有砂型铸造、金属型铸造、精密铸造、压力铸造。
铸件材料有铸铁、铸钢及铜、铝等有色金属。
(2)锻件:
适用于强度要求高、形状比较简单的零件毛坯。
其锻造方法有自由锻和模锻两种。
自由锻毛坯精度低、加工余量大、生产率低,适用于单间小批量生产以及大型零件毛坯。
模锻毛坯精度高、加工余量小、生产率高,但成本也高,适用于中小型零件毛坯的大批量生产。
(3)型材:
有热轧和冷拉两种。
热轧适用于尺寸较大、精度较低的毛坯;
冷拉适用于尺寸较小、精度较高的毛坯。
(4)焊接件:
是根据需要将型材或钢板焊接而形成的毛坯件,它简单方便,生产周期短。
(5)冷冲压件:
毛坯可以非常接近成品要求,适用于大批量生产。
3.2、零件毛坯的确定
因该零件为传动轴,要求的扭力强度,拉力强度较高,强度要求高、形状比较简单的零件选择锻件。
由于单件小批量生产,所以选择自由锻件。
根据零件尺寸可知,选择直径为45mm的,长度为155mm的棒料比较合适
4、定位基准
4.1、选择基准的原则
正确的选择定位基准是设计工艺过程中的一项重要的内容,也是保证加工精度的关键,定位基准分为精基准和粗基准。
(1)选择精基准时主要应考虑保证加工精度和工件安装方便可靠,有如下原则:
(书340页)
1)基准重合原则;
2)基准统一原则;
3)自为基准原则;
4)互为基准原则;
(2)选择粗基准时主要要求保证各加工面有足够的余量,并注意尽快获得精基面,有如下原则:
(书339页)
1)选加工余量小的、较准确的、表面质量较好的’面积比较大的毛面作粗基准。
2)先重要表面为粗基准。
3)选不加工的表面作粗基准。
4)粗基准在同一尺寸方向上只能使用一次。
由于两轴面的精加工工序要求余量小且均匀,可利用其自身作为基准。
根据传动轴的技术要求和装配要求以及基准重合原则,选用中心轴线为定为基准,可保证表面最后的加工位置精度,实现了设计基准和工艺基准的重合。
4.2、零件加工时选择基准的方法
(1)当加工零件外圆到直径为40时,选择毛坯刚开始的外表面为粗基准
(2)当车棒料左端时,选择右端面为粗基准
(3)当加工其它表面时,都是用以加工成直径为40的表面为定位基准
(4)当加工各轴肩确定各不同直径的轴向长度时,以左端面为定位基准
(5)当车棒料右端时,选择已加工的左端面为定位基准
(6)当铣键槽时,轴向长度以右端面为定位基准
5、工艺路线
5.1、零件表面的加工方法
根据零件图表各表面得加工要求,以及材料性质等各因素该轴为阶梯轴,该轴的各表面具体的加工方法如表2
表2该零件各表面加工方法
加工表面
尺寸精度等级
表面粗糙度Ra(µ
m)
加工方法
φ40外圆面
IT11
12.5
粗车——半精车
φ
外圆面
IT5
0.8
粗车——半精车——粗车
IT6
1.6
粗车——半精车——精车
φ32外圆面
IT9
6.3
左右端面
粗车
普通圆头平键
3.2
粗铣——半精铣
5.2、加工路线的确定
5.2.1机械加工工序
①按先基准平面后其他的原则:
机械加工工艺安排是总是先加工好定位基准面,所以应先安排为后续工序准备好定为基准。
先加工精基准面,转中心孔及车表面的外圆。
②按先粗后精的原则:
先安排粗加工工序,后安排精加工工序。
先安排精度要求较低的各主要表面,后安排精加工。
③按先主后次的原则:
先加工主要表面,如车外圆各个表面,端面等。
后加工次要表面,如铣键槽等。
④先外后内,先大后小原则:
先加工外圆再以外圆定位加工内孔,加工阶梯外圆时先加工直径较大的后加工直径小的。
⑤次要表面的加工安排:
键槽等次要表面的加工通常安排在外圆精车之后。
⑦先面后孔原则:
先加工端面,再铣键槽
5.2.2热处理加工工序
在切削加工前宜安排正火处理,岂能提高改善轴的硬度,消除毛坯的内应力,改善其切削性能。
在粗加工后进行调质处理,能提高轴的综合性能。
在粗加工和热处理后,安排校直工序。
在半精车加工之后安排去毛刺和中间检验工序。
在精加工之后安排去毛刺、清洗和终检工序。
综上所述,该轴的工序安排顺序为:
基准加工——主要表面粗加工——热处理——主要表面半精加工——主要表面的精加工——铣键槽——去毛刺——检测。
6、余量与工艺尺寸的确定
表3加工余量与工艺尺寸
φ40
工序名称
工序余量
公差等级
工序基本尺寸
工序尺寸
半精车
IT11(0.16)
40
φ40-0.160
IT12(0.25)
40+1=41
φ41-0.250
毛坯
41+4=45
φ45±
φ35
精车
IT5(0.011)
35
1.2
IT8(0.039)
35+0.8=35.8
35.8+1.2=37
φ37
38+2=40
φ25
IT6(0.013)
25
IT10(0.084)
25+0.8=25.8
13
IT11(0.13)
25.8+1.2=27
φ27
15
27+13=40
φ32
32
φ32-0.0390
IT10(0.1)
32+0.8=32.8
φ32.8-0.10
32.8+1.2=34
φ34
34+6=40
IT6(0.016)
37+3=40
7、选择加工设备及工艺装备
各加工方式所选用的加工设备,加工夹具和量具的选择如表4所示
表4加工设备与工艺设备
加工方式
加工设备
加工夹具
选择量具
普通车床
三爪自定心卡盘、固定顶尖
游标卡尺
铣键槽
万能卧式升降铣床
专用铣夹具
检验
游标卡尺,通规,
粗糙度仪
8、切削用量的确定
经查《机械加工工艺手册》得:
(1)粗车加工时,取f=0.5mm/r,Vc=90m/min,ap=2mm
(2)半精车加工时,取f=0.3mm/r,Vc=100m/min,ap=1mm
(3)精加工时,取f=0.08mm/r,Vc=130m/min,ap=0.4mm
9、刀具的设计
已知:
工件材料40Cr,使用机床CA6140,加工后dm=26,Ra=3.2,需粗、半精车完成,加工余量3.0mm,设计装C刀片75°
直头外圆车刀。
设计步骤:
9.1、选择刀片夹固结构
考虑到加工是在CA6140普通机床上进行,属于连续切削,参照表2-1典型车刀夹固结构简图和特点,采用偏心式刀片夹固结构。
9.2、选择刀片材料
由原始条件结构给定:
被加工工件材料为灰铸铁,连续切削,完成粗车、半精车两道工序,按照硬质合金的选用原则,选取刀片材料(硬质合金牌号)为YG6。
9.3、选择车刀合理角度
根据刀具合理几何参数的选择原则,并考虑到可转位车刀:
几何角度的形成特点,选取如下四个主要角度:
(1)前角=14°
,
(2)后角=6°
(3)主偏角=75°
,(4)刃倾角=-6°
后角
的实际数值以及副后角和副偏角在计算刀槽角度时,经校验后确定。
9.4、选择切削用量
根据切削用量的选择原则,查表确定切削用量为:
粗车时:
切削深度ap=2mm,进给量f=0.5mm/r,切削速度v=90m/min
半精车时:
ap=1mm,f=0.3mm/r,v=100m/min
9.5、选择刀片型号和尺寸
(1)选择刀片有无中心固定孔
由于刀片夹固结构已选定为偏心式式,因此应选用有中心固定孔的刀片。
(2)选择刀片形状
按选定的主偏角=75°
,选用棱形80°
刀片。
(3)选择刀片精度等级
选用U级
(4)选择刀片边长内切圆直径d(或刀片边长L)
根据已选定的ap,Kr,λs,可求出刀刃的实际参加工作长度Lse。
为;
Lse=
=
=3.123mm
L﹥1.5Lse=4.685
因为是棱形,d›4.525。
(5)选择刀片厚度S
根据ap,f,利用诺模图,得S≧4.8。
(6)选择刀尖圆半径rε:
根据ap,f,利用诺模图,得连续切削
=0.8mm
(7)选择刀片断屑槽型式和尺寸
根据条件,选择V型。
当刀片型号和尺寸确定后,断屑槽尺寸便可确定。
确定刀片型号:
CNUM160608-V1,尺寸为L=16.1mm,d=15.875,S=6.35mm,
d1=6.35mm,m=3.97mm,
=0.8mm粗车刀尖角
=80°
刃倾角λs=-6°
,法后角αsn=0°
,法前角rsn=20°
,断屑槽宽度Wn=4mm
9.6、确定刀垫型号和尺寸
硬质合金刀垫型号和尺寸的选择,取决于刀片夹固结构的需要及刀片型号和尺寸:
适合于偏心式夹固结构的需要,并于刀片型号CNUM160608-V2相对应的硬质合金
刀垫得型号为:
C16B,其具体尺寸为:
L=14.77mm,S=3mm,d1=6.1,
=1.2mm,D=8.5,C=2.0
9.7、计算刀槽角度可转位车刀几何角度、刀片几何角度和刀槽几何角度之间的关系,刀槽角度计算步骤:
(刀具角度换算)
(1)刀杆主偏角
Krg=Kr=75°
(2)刀槽刃倾角λsg
sg=
s=-6°
(3)刀槽前角γog刀槽底面可看作前刀面,则刀槽前刀角γog的计算公式为:
tgγog=
将γo=14°
,γab=20°
,λs=-6°
代入式
得:
=-0.107
则γog=-6.107°
取γog=-6°
(4)验算车刀后角α0
车刀后角α0的验算公式为
tgα0=
当αab=0°
时,则
Tgαo=-tgγogcos²
λs
将γog=-6°
代入
得;
tgαo=-tg(-6°
)cos²
(-6°
)=0.104
则αo=5.937
与所选后角值相近,可以满足切削要求。
而刀杆后角αab=αa
故αab=5.937°
,取αab=6°
(5)刀杆副偏角K′rg
∵K′rg=K′r
而K′r=180°
-Kr-
r
又∵
rg=
r,Krg=Kr
∴K′rg=180°
-Krg-
rg=180°
-Kg-
g
车刀刀尖角
r的计算公式为
ctg
r=[ctg
rg√1+(tgγrgcosλs)²
-tgγrgsinλs]cosλs
当
rg=80°
时,则为
ctg
r=[ctg80
-tg
sin
]cos
将γrg=-6°
得ctg
-tg(-6
)sin(-6
)]cos(-6
)=-9.516
则
r=80.63°
故K′rg=K′r=180°
-75°
-80.63°
=24.37°
取K′rg=24.5°
(6)检验车刀副后角α′g
车刀副后角α′g的验算公式为
tgα′r=
当αrg=0°
时,则式为
tgα′r=-tgγ′rgcos²
λ′rg
而tgγ′rg