API 5L工艺卡273 635X65管线Word文档格式.docx
《API 5L工艺卡273 635X65管线Word文档格式.docx》由会员分享,可在线阅读,更多相关《API 5L工艺卡273 635X65管线Word文档格式.docx(15页珍藏版)》请在冰豆网上搜索。
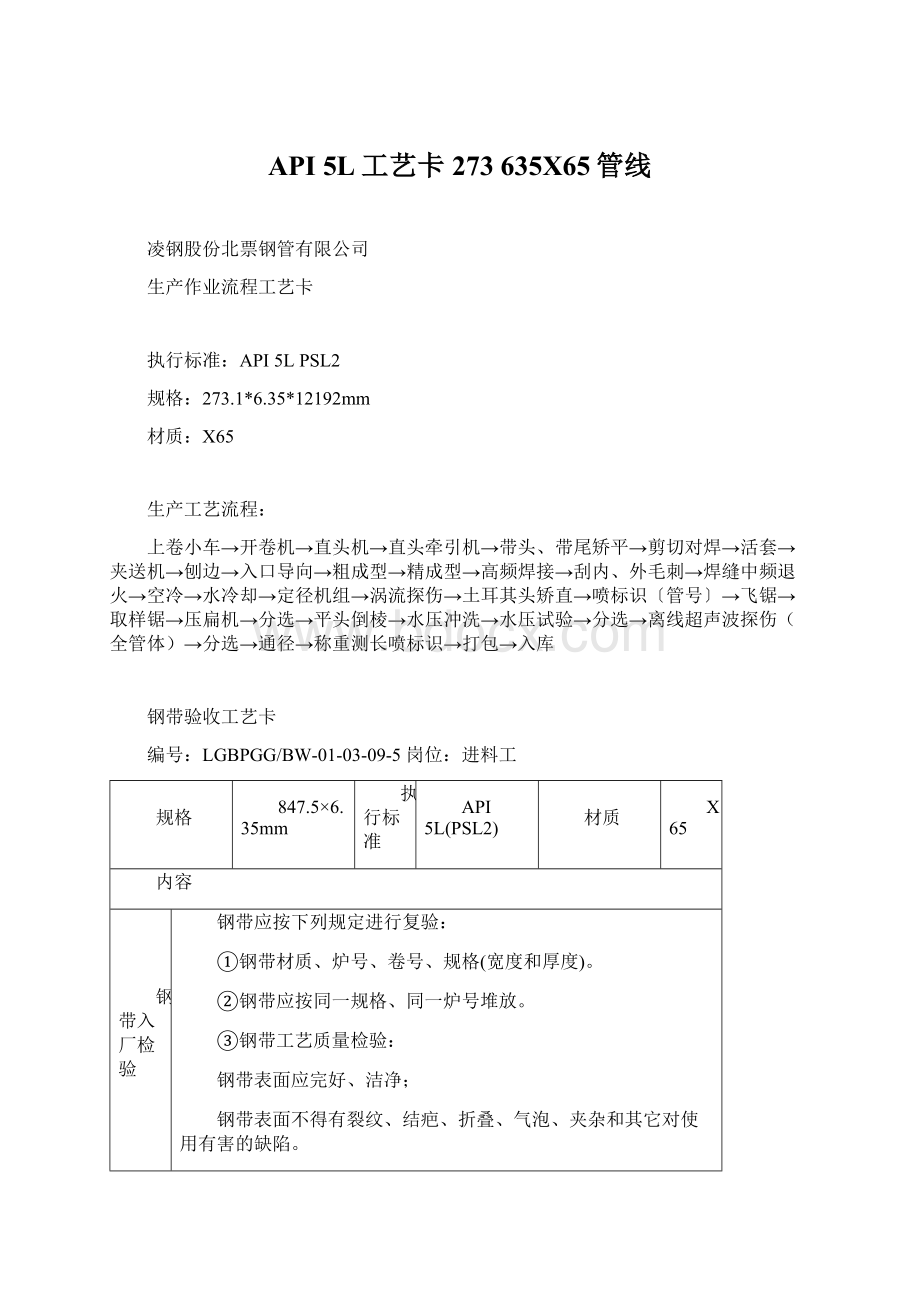
最大厚度(mm)
6.35
847.5
5.72
6.98
钢带宽度公差为0mm~+1mm。
备注:
1)做好相应的记录;
2)质量责任人为该岗位的操作者。
投料工艺卡
上料工
273.1×
6.35×
12192mm
API5L(PSL2)
工序名称
工艺参数与要点
操作要求
设备
控制措施
投料
按同一规格、同一炉号顺序投料
核对钢带尺寸(宽度、厚度),检查板面、板边是否有碰伤等缺欠
吊车
开卷机等
用校验后的测量尺复验钢带尺寸;
目测检查
接板
电压:
37~42V,电流:
387~500A;
直径为1.2mmCO2气体保护焊丝;
焊缝应均匀光滑且余高应不大于0.5mm;
焊缝宽度约为2倍壁厚;
焊透深度>70%。
采用二氧化碳气体保护焊
角向磨光机抛光
剪切对焊机
检验每个接头
12192
原料尺寸
847.5mm×
847.5~848.5
厚度(mm)
5.72~6.98
成型焊接工艺卡
LGBPGG/BW-01-03-09-5岗位:
调整工
成型
调整好轧制底线,将钢带通过各架成型机连续地成型为所要求的圆筒形.
1)轧辊与钢带接触变形处应喷洒足够的冷却水;
钢带成型时,两侧边应处于同一水平面内。
2)用卡尺和板尺调整各架次的平、立辊间距;
3)冷却水喷洒在各成型辊上部。
成型机
焊接
⑴速度:
15-25m/min
⑵温度:
1250~1430
⑶焊接电流:
700~900A
⑷焊接电压:
350~450V
1)安装好相应的挤压辊和挤压上辊;
2)用内卡尺、直板尺调好孔型;
3)保证有足够的冷却水喷洒在挤压辊上;
4)保证足够的挤压量,即内外毛刺均匀、适当;
1)挤压辊
2)高频焊接机
1)根据焊缝毛刺大小及状态调整挤压力、输入热量及焊速;
2)力学性能检验;
3)在线超声波检测。
除内毛刺
内毛刺高度为-0.05~+0.5mm,出现刮槽时,剩余壁厚不得小于规定的最小壁厚。
要有足够的冷却水,以防止刀架上的磁棒损坏,退磁和刀具退火。
调整好刀具高度
除内毛刺刀架
壁厚千分尺
除外毛刺
外毛刺清除至与钢管外轮廓基本平齐状态;
焊缝表面应平整、无划痕等缺欠。
刮掉的毛刺碴、焊瘤等应用水、风吹干净,漏焊的开口管,不准刮削毛刺。
合金刮刀
目测检查外毛刺刮除情况
备注:
1)做好相应的记录;
2)质量责任人为该岗位的操作者。
定径切断工艺卡
LGBPGG/BW-01-03-09-5岗位:
定尺锯工
定径
管体外径(mm)
管端外径(卡尺测量)(mm)
min
max
271.05
275.15
271.74
274.46
管子表面不得有明显划伤,压痕等缺欠。
将孔型调整好;
保证各架的孔型中心对准轧制线中心;
冷却液要适量。
定径机
用经校验的卡尺测量管体及管端外径;
矫直
保证定尺切断后的每根钢管直度≤0.2%,局部的直度应小于4mm/m。
;
1)调整好孔型尺寸;
2)保证各架的孔型中心对准轧制线中心;
3)根据弯曲程度,调整八辊。
八辊矫直头
定尺切断
定尺长度12198mm,长度偏差-25~+25mm。
切断后钢管两端应与钢管轴线垂直
定尺锯
微机自动控制
喷管号
每一根管有一个可追溯的管号
管号喷涂应清晰可辩,保留长久。
油性粉笔
目测
1)做好相应的记录;
2)质量责任人为该岗位的操作者。
平头倒棱工艺卡
平头工
平头倒棱
钢管管端加工坡口,坡口角为30°
+5°
0
管端余留的厚度为1.6mm±
0.8mm,见图。
钢管切断后,钢管两端面应与其轴线垂直,切斜不得大于1.6mm。
平头倒棱机
用经校验的宽座直角尺、塞尺以钢管轴线为基准测量管端的几何尺寸。
静水压试验工艺卡
水压工
静水压试验
钢管应逐根进行静水压试验,试验压力为17.8MPa;
静水压试验的稳压时间至少应保持5s;
静水压试验全过程不允许渗漏。
静水压试验机的鉴定:
静水压试验开始前,静水压试验压力表应用静载试验机校准。
以后至少每周校准一次,每次爆管后也应校准一次;
试验时,钢管表面不能带水操作;
爆管应视为不合格管;
试验时,应使焊缝向上,以便随时观察焊缝水压后变化情况。
静水压试验机
静水压试验记录应能追踪到管号和熔炼炉批号,且有自动记录装置。
化学成分复验工艺卡
理化检验工
化学成分最大重量百分比含量要求:
C
Si
Mn
P
S
铌
Ni
铌、钒、钛含量之和
≤0.16
≤0.45
≤1.40
≤0.025
≤0.015
≤0.05
≤0.30
≤0.15
碳当量a%:
CEIIW≤0.43;
CEpcm≤0.25。
取样与试验频次:
①原材料化学成分分析用试样应取自钢带上,每熔炼批进行一次;
②钢管化学成分分析用试样应取自制管用钢带或钢管上,同一熔炼批取两根钢管进行试验,取样位置距焊缝至少90°
。
原材料复验要求:
原材料若复验不符合要求,可选择对该批判不合格或对该批的其余部分逐卷进行试验。
力学性能工艺卡
LGBPGG/BW-01-03-09-6岗位:
168.3×
API5L(PSL2)
X60
力学性能应符合下表的规定:
屈服强度(Mpa)
抗拉强度(包括焊缝)(Mpa)
伸长率A(%)
屈强比Rt0.5/Rm
Rt0.5≥450
Rm≥535
≥18
0.9
力学性能试验的频次、取样数量、取样位置及方向应符合下表的规定:
项目
取样频次
取样位置
备注
原材料
同一熔炼批进行一次。
钢带宽度方向1/4处
纵试样
钢管
同一熔炼批1次/400根
在焊缝90°
以外取
纵向试样
钢管复验要求:
若试验不合格,应在同一批钢管中另抽两根钢管做复验。
若复验钢管均符合要求,除首次试验不合格的钢管外,该批钢管均合格。
若复验仍不符合要求,可选择对该批钢管判不合格或对该批的其余钢管逐根进行试验。
压扁和金相试验工艺卡
压扁和金相试验应符合下表的规定:
压扁试验
金相试验
两压平板间距离,mm
热处理前
热处理后
2/3D
1/3D
贴合
焊缝不得开裂
母材不得出现裂纹或断裂
不得出现分层或金属过烧等
观测熔合线宽度,热影响区的中心宽度和内、外壁宽度
是否存在未回火马氏体。
检查热处理效果
压扁和金相试验的频次、取样数量、取样位置及方向应符合下表的规定:
种类
试验频次
取样数量、方向及位置
每班一次
2W(热处理前后各一)
2W—2个焊缝试样;
逐卷
首尾两根管端头各取1个试样,在两个不同的中间位置再取两个试样。
端头两个试样将焊缝置于与受力方向成90°
位置,中间位置的试样置于与受力方向成0°
位置进行压扁试验。
停车前后的试样全部为90°
位置进行压扁试验,这时的两个压扁可代替钢带中间位置的压扁试验。
试样长至少63.5mm。
故障停车,前后各取1个试样
压扁试验复验要求:
如果任一试验结果不符合规定要求,应对该卷钢带不合格钢管取样端相邻钢管的每一端进行复验,焊缝分别置于0°
和90°
的位置。
若复验合格,则该卷钢带生产的钢管除首次试验不合格的钢管外,其它钢管均合格,若复验结果仍不符合要求,可将该卷钢管判不合格或再在其相邻钢管的每一端进行复验,焊缝交替置于0°
的位置,依次类推。
金相试验复验要求:
若金相试验不符合要求,应立即通知调整工,以便及时调整焊接工艺参数。
无损检测工艺卡
无损检测工
全管体超声波探伤与管端超声波探伤
焊缝手动超声波探伤
设备型号
TBCT(DSP)A
HS600
设备校验频次
每工作班(4小时)校验1次。
每班开始前进行校验,每个工作班(4小时)校验1次。
探头类型
组合探头
5P6*6k3、2.5P9*9K2
对比标样
同钢级、同规格2500mm长管样
同钢级、同规格2500mm长管样、荷兰试块
人工缺陷
焊缝:
Ф3.2直通孔
藕合剂
水
浆糊
检测时机
水压试验前
水压试验后
扫查速度
同焊速
150mm/s
探伤方式及部位
全管体范围内自动探伤
补焊部分及管端300mm焊缝手动探伤
灵敏度
焊缝Ф3.2直通孔波幅80%作为探伤灵敏度;
检测灵敏度加2~3db。
Ф3.2直通孔作为探伤灵敏度
验收标准
缺欠信号大于合格极限信号均视为缺陷
成品检验工艺卡
成品检验工
规定要求
检测频次
管体外径/mm
271.05~275.15
逐根
管端外径/mm(卡尺测量)
271.74~274.46
壁厚/mm
5.72~6.98mm
单根长度/mm
100%
12167~12217
坡口角/°
30°
~35°
钝边/mm
0.8~2.4
直度/%
0.2
切斜/mm
1
外毛刺
——
基本平齐
内毛刺/mm
-0.05~+0.5
错边/mm
0.5
表面质量
内、外表面应清洁、光滑、无缺陷
剩磁测量、光照度测量工艺卡
检斤工
剩磁测量:
管端剩磁量采用特斯拉计随机检测,最大为3mT(30Gs),按剩磁量测量作业规范(编号:
LGGF/BW-10-2007)进行测量。
光照度测量:
厂房的光照至少为300lx。
按光照度测量作业规范(编号:
LGGF/BW-11-2007)进行测量。
标识包装工艺卡
LGBPGG/BW-01-03-09-5岗位:
包装工
标识
LGAPI5L-0611
07-10(按生产月-日)10-3/4″0.250″X60
PSL2HFW2970psiHEATNO.(炉号)PIPENO.(管号)CHINA
备注:
括号内中文字为注解不在喷标范围内
在距管端150mm范围内且至少距焊缝25mm处。
手动刮块干漆
包装
⑴钢管逐支涂油,涂层应光滑硬实,无多余流挂。
37支/捆,12道包装带包装,分成4组,每组三道,两端包装带距离端头350~400。
另外两组在中间均布。
每捆配带2根吊带。
⑵每捆挂两个标牌,一个放在包装带上面,一下放在包装带下面。
(标牌待厂家答复)
⑴包装带对接处卡扣必须卡紧;
⑵包装台架应垫10mm厚1m宽2m长的胶皮,以免磕伤管体;
⑶逐支检查管体内是否有杂物;
⑷钢管一端保持平齐;
⑸用8t尼龙吊装带吊运;
⑹按炉号标记,呈“井”字摆放。
吊装工艺卡
装卸工
吊装
⑴钢管吊运必须用8t尼龙包装带吊装;
⑵装车时两层钢管间必须用软木或草把加垫;
⑶吊运过程中必须保持平稳,轻起轻放,以免磕伤管端及管体;
⑷检查钢管表面是否完好,管体内是否有杂物,并做相应处理。