丁基橡胶综述Word文档格式.docx
《丁基橡胶综述Word文档格式.docx》由会员分享,可在线阅读,更多相关《丁基橡胶综述Word文档格式.docx(15页珍藏版)》请在冰豆网上搜索。
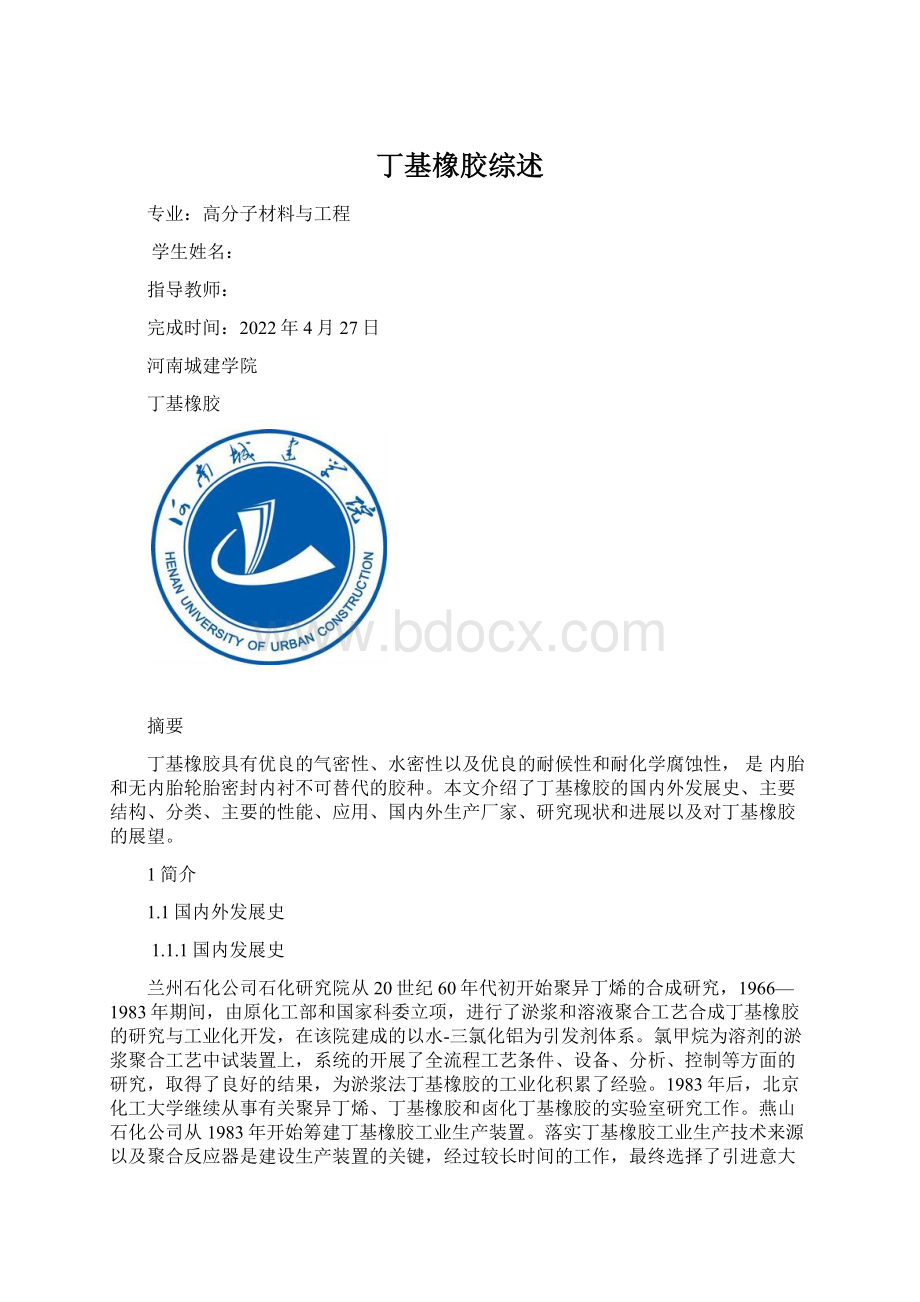
1943年Exxon公司在美国BatonRouge工厂实现了丁基橡胶的工业化生产,1944年加拿大Polysar公司采用美国技术在Sarnia建成丁基橡胶生产装置。
1959年后,法国、英国、日本也开始生产丁基橡胶。
1991年,Bayer公司购买Polysar全部合成橡胶业务,Exxon公司也收购了在法国的丁基橡胶生产装置,从此世界丁基橡胶的生产基本上被Exxon和Bayer两大公司所垄断。
1982年,前苏联在陶里亚蒂建成世界唯一的溶液聚合法丁基橡胶生产装置,所用聚合反应器由苏联合成橡胶研究院和意大利PI公司合作开发。
目前,世界上只有美国、德国、俄罗斯和意大利4个国家拥有丁基橡胶生产技术,在国际市场上,Exxon公司和Bayer公司的丁基橡胶产品处于垄断地位,生产能力约占世界总生产能力的80%,此外,这两大公司在新产品和新技术的开发方面也处于世界领先地位[3]。
1.2丁基橡胶的分子结构式
CH3—(CH3)2—[CH2—(CH3)2]m—CH2—(CH3)2—CH—CH2—[CH2—(CH3)2]n—
1.3丁基橡胶的分类
丁基橡胶(IIR)是第1个高饱和的橡胶品种,少量的异戊二烯的引入是为了获得可供硫化的双键。
由于结构上的特点,丁基橡胶有良好的气密性和耐老化性。
但也限制了其与聚二烯烃橡胶的并用,此外,分子中缺少极性基团,也使其与金属或橡胶的粘合性能差,随着合成橡胶工业发展和应用的需要,IIR现已开发成拥有衍生橡胶、改性橡胶、热塑性弹性体和热塑性硫化胶等品种通用橡胶[6]。
通常按照异戊二烯的含量即不饱和度及是否卤化来分类[1]:
⑴一般品种:
不饱和度为0.6~1.0%(mol)、1.1~1.5%(mol)、1.6~2.0%(mol)2.1~2.5%(mol)
⑵卤化品种:
氯化丁基橡胶、溴化丁基橡胶
①氯化丁基橡胶
氯化丁基橡胶(CIIR)的制备方法分干胶混炼氯化和溶液氯化两种方法。
前一法是在开炼机上把吸附了氯气的活性炭或其它氯化剂混入丁基橡胶中经加热和混炼后制得;
后一法是先把其橡胶溶于四氯化碳、氯仿或己烷等溶剂中,然后在常温下通过氯气进行氯化,即制得氯化丁基橡胶,由于该法已实现连续氯化工艺生产,故已成为主要的制造方法。
极性氯原子的引入,可克服丁基橡胶硫化速度慢、粘合性能差,与高不饱和橡胶难于共硫化等的问题。
该胶能以单用或并用方式制造无内胎轮胎的气密层、浅色或白色胎侧、内胎、胶带、胶管、密封、绝缘或粘合等用胶料[5]。
②溴化丁基橡胶
溴化丁基橡胶(BIIR)的制备方法分干混炼法和溶液法等两种方法。
按前一法可分别把N-溴代琥珀酰亚胺10%,二溴二甲基乙内酰脲7.5%或活性炭吸附溴(31.2%重量比)30%加入到在开炼机上的丁基橡胶中进行热混炼而制得;
而后一法是将丁基橡胶溶解于氯化烃溶剂,再通入约3%的溴而制取的,该溴化过程是连续的,其产品质量均匀且稳定。
溴化丁基胶与上述氯化丁基胶比,有更多的活性硫化点,硫化速度快,与不饱和型橡胶能更好粘合,有更高的耐老化、较低的焦烧安全性。
主要可用作轮胎的气密层、胎侧、内胎、容器衬里、药品瓶塞和胶垫等。
⑶磺化丁基橡胶
磺化丁基橡胶(SIIR)是丁基橡胶经磺化后所得的产品,作为磺化剂可用二氧化硫或其它磺化物。
该橡胶由于也含极性基团,故也能得到用氯化或溴化的改性效果,因而也宜于作聚合物改性剂和胶粘剂等。
⑷马来酸酐改性丁基橡胶
马来酸酐改性丁基橡胶(MIIR)是在丁基橡胶上接枝马来酸酐的橡胶。
由于丁基橡胶大分子链上引入极性侧基,可提高生胶的硬度以及与其它聚合物材料相溶性或粘合性能,可用作聚合物增容剂、改性剂、溶剂型和热熔型胶粘剂以及热塑性体的原料等。
⑸交联丁基橡胶(又称三元丁基橡胶)
交联丁基橡胶是异丁烯,异戊二烯和二乙烯基苯的三元共聚物。
1.4丁基橡胶的优缺点
优点:
①透气率低,气密性好,丁基橡胶分子链中侧甲基排列密集,限制了聚合分子的热运动。
②热稳定性好:
可在100℃或稍低温度下于空气中长期使用。
脱硫的丁基橡胶使用温度可达150℃到200℃
③吸能性好:
丁基橡胶分子结构中缺少双键,且侧链甲基分布密度大
④耐臭氧和耐天候老化性
⑤化学稳定性好
⑥电绝缘性较好
⑦渗透率极低
缺点:
①硫化速度慢
②互黏性差
③相容性差
④与补强剂之间作用弱
1.5国内外生产厂家
2.主要特性及用途
2.1主要特性
①气密性:
在合成橡胶中,丁基橡胶具有最好的气密性,即有很小的透气率。
气体通过聚合物的透气率主要取决于气体在聚合物中的扩散速率,而扩散速率与聚合物的分子运动有关。
由于分子链中侧甲基密集排列限制了分子的热运动,所以丁基橡胶有很小的透气率。
②耐热老化性:
丁基橡胶硫化胶具有优良的耐热老化性。
有硫磺硫化的丁基橡胶,可于100℃的温度下,在空气中长期使用;
采用树脂硫化的丁基橡胶使用温度可达150~200℃。
③能量吸收性:
丁基橡胶的玻璃化转变温度为-65℃,虽然接近天然橡胶的-70℃,由于分子结构中有较少的双键和大量紧密排列的侧甲基,对弹性运动造成很大的位阻,因此其硫化胶具有非常低的回弹性,表现出很好的阻尼性,即吸收振动及冲击能量的特性。
④其他特性:
除以上特性外,丁基橡胶还具有以下化学稳定性:
由于其分子链的高度饱和,具有良好的耐臭氧性及耐天候性,对多数无机酸和有机酸均有良好的抗侵蚀性,耐碱和氨的作用[1]。
2.2用途
用途
所利用特性
轮胎
内胎、气密性
硫化胶囊
汽车
车身支座
医用
药瓶塞
建筑
屋顶防水卷材
贮罐衬里
不透气性、耐热老化性
耐热、耐蒸汽性
高度吸收能量性
不透气性、耐老化性
不透水性、耐天候及耐臭氧性
耐化学性
3.丁基橡胶的聚合机理、影响因素
3.1丁基橡胶的聚合机理
丁基橡胶的聚合反应历程可分为链引发、链增长、链终止等三个步骤。
随着采用的催化剂的不同,阳离子的聚合催化剂的引发机理有所不同。
丁基橡胶的生产以淤浆法为主,其聚合机理是典型的阳离子聚合机理。
以氯甲烷为溶剂、三氯化铝为引发剂、水位共引发剂,在-103℃低温下进行阳离子共聚合,其反应机理如下[3]:
①链引发
②链增长
③链终止
a.自发终止
b.成键终止
丁基橡胶的聚合机理特征主要是:
快引发、快增长、易转移、难终止。
3.2影响聚合反应的主要因素
①杂质
在丁基橡胶的聚合体系中,有原料、惰性气体、聚合反应器、管道都可能带来杂质。
按照其作用原理,这些杂质可以分为给电子体和烯烃两大类。
给电子体如水、甲醇、氯化氢、二甲醚、二氧化硫和氨等,分子中均含有未共用的电子对,而催化剂AlCl3则有未排满的电子层,因而这些杂质均可与AlCl3反应生成络合物。
例如甲醇与AlCl3生成络合物[11]。
当这些杂质含量极少时,与AlCl3生成的络合物可以离解成为活性催化剂;
但是,杂质与AlCl3反应生成活性不高,会导致转化率降低。
因为这些杂质具有链转移作用,当他们超过一定量时,则会致使聚合物分子量明显降低。
分子量降低的程度与杂质和AlCl3反应生成的化合物的离解度的大小有关;
离解度越大,能够进行转移的负离子浓度越高,聚合物的分子量越小;
也与杂质AlCl3络合物的浓度有关;
浓度越高,分子量越小[12]。
②单体浓度和配料比
在丁基橡胶的聚合体系中:
单体浓度过高,反应温度升高的很快,反应过于激烈难以控制,容易导致结块,甚至催化剂还未加足量价被迫停止反应。
而单体浓度过低时,结冰现象严重,(CH3Cl的冰点为-97°
C)[15]也不能获得较高的转化率。
③聚合温度
随着聚合温度的提高,聚合物的分子量直线下降。
这是因为单体链转移活化能总是比链生长的活化能大17.56~19.23kJ/mol[20],因此低温能够抑制单体的链转移从而有利于分子量的增大。
需要指出的是,降低温度也有可能提高聚合速度,有利于生成高分子量的聚异丁烯。
因为催化体系的实际能力与下列平衡有关:
而离子对与自由离子对对单体的引发具有不同的活性,因此有两种链生长:
已经证明Kp1远较Kp2大,而降低温度有利于平衡向右移动,也就是增加自由离子的浓度,有利于按Kp1方式进行。
因此,聚合速度和分子量都将增加。
提高溶剂的极性有利于自由离子的存在,因此也有类似降低温度的效应。
④催化剂
催化剂的用量很小时,单体转化率低,用量大时,转化率高。
由于催化剂的用量少时杂质消耗了部分的催化剂,总督活性催化剂相对量较少,故导致转化率较低。
催化剂用量已经超过杂质消耗的低限时,随着催化剂用量增加,转化率迅速上升。
当催化剂用量达到一定程度时,聚合反应已经达到一定的深度。
单体浓度大大降低,催化效率降低。
工艺生产中引发剂一般为单体的0.02%~0.05%[18]。
⑤溶剂
溶剂决定了生成的聚合物的溶解度。
丁基橡胶均相溶液聚合法或非均相溶液淤浆聚合法所采用的溶剂是不同的。
用于淤浆聚合的溶剂要求沸点低于-100°
C,不溶解聚合物,对催化剂的惰性的,通常使用易于溶解催化剂AlCl3的CH3Cl。
采用正丁烷和异戊烷作溶剂的均相溶液聚合,最早是从减轻聚合物的挂胶结垢作用来设计的。
但是在-100°
C的低温下,均相溶液的粘度非常的大,给传质传热带来很大的困难,所以一般要求聚合物浓度不超过4%~5%。
使单位体积的聚合物溶剂和未反应单体的回收量增加,同时,也大大地降低了聚合物的生产能力。
而挂胶和结垢同样不可避免,所以工业上仍普遍采用氯甲烷为溶剂【14】。
4.生产工艺、改性及装备
4.1淤浆法工艺
淤浆法是以氯甲烷为稀释剂,以H20-A1Cl3.为引发体系,在低温(-100°
C左右)下将异丁烯与少量异戊二烯通过阳离子聚合制得的。
淤浆法生产技术主要包括聚合反应、产品精制、回收、循环以及清釜4个部分[9]。
①聚合反应:
在用丙烯作冷却剂的带夹套的配制槽内,将精制的异丁烯和异戊二烯单97%~98%(质量分数)和1.4%~1.5%(质量分数)以25%(质量分数)的氯甲烷配制成混合溶液。
同时将催化剂级的无水粒状A1Cl3加入到上述配制的氯甲烷混合溶液中搅匀。
单体溶液和催化剂溶液分别经丙烯和乙烯冷却至-100℃后送人聚合反应釜,经搅拌接触,单体在形成的阳离子A1Cl3-MeCl催化剂体系下发生聚合反应[12]。
这种悬浮聚合反应是在足够的低温(-90℃以下)下进行的,聚合反应不到1S即可完成,反应热由通人反应釜内冷却列管的液态乙烯带出。
②产品精制:
聚合反应完成后,含丁基胶粒的淤浆从聚合釜上部导出管溢流入闪蒸塔,在搅拌中与热水和蒸汽接触,未反应的单体和溶剂从塔顶蒸出,丁基胶淤浆进入真空脱气塔。
为防止胶粒粘结,脱气塔内加入1.5%(与橡胶质量之比)分散剂(如硬脂酸锌或硬脂酸钙)和0~3%(质量分数)的防老剂水悬浮液,或相对分子质量高的多酚类脱气用抗氧剂。
含水胶粒混合物在真空脱气塔内脱除残余氯甲烷及未反应单体后送往后处理系统,经振动筛、挤压、脱水、压缩膨胀,在活性氧化铝上干燥,再经压片、称量、包装得成品[13]。
③回收循环:
从闪蒸塔及真空脱气塔顶出来的未反应的单体和氯甲烷气体冷却除水,压缩冷却再脱水后,经中性氧化铝或沸石分子筛干燥精制送入回收精馏塔。
为改进固体吸附干燥工艺,可采用乙二醇或二甘醇脱水精制法,从压缩机出来的氯甲烷与未反应单体混合物进入吸收塔下部,乙二醇从顶部加入,含水和氯甲烷的乙二醇送入解析塔,再生乙二醇循环使用。
④清釜:
由于聚合过程催化剂分布不均匀热量集中会造成局部过热或单体中有害物质的存在,形成低聚物附集在反应釜内壁上形成粘结挂胶,所以必须采用清釜过程将其进行处理。
清理挂胶一般采用溶剂法,溶剂用加热至6O℃的己烷或石脑油,清理与置换时问为1O~12h。
清釜液可经凝聚、干燥来回收其中的聚合物。
该生产技术由Exxon公司和朗盛公司所垄断。
1—进料混合,2—C2H4冷却器,3—NH3冷却器,5—反应器,6—闪蒸罐,7—过滤器,8—脱水挤出机,9—干燥挤出机,10—打包机
该工艺流程即将粗异丁烯和氯甲烷分别在脱水塔和精馏塔进行脱水和精制以后,与异戊二烯在混合槽忠按一定的比例混合。
混合液在冷却器里冷至-100°
C,然后送人反应器。
同时配制好催化剂溶液并冷却。
聚合反应在-98°
C左右进行,几乎瞬时完成。
聚合物在氯甲烷中沉淀形成颗粒状浆液。
聚合后的淤浆从反应器中溢流出来进入盛有热水的闪蒸罐,在此蒸发氯甲烷和未反应单体。
橡胶的水淤浆液用泵送到挤出干燥系统,干燥后包装成品。
闪蒸罐出来的蒸气经活性氧化铝干燥、分馏后送到进料和催化剂配制系统循环使用[2]。
4.2溶液法工艺
传统的淤浆法IIR生产工艺技术成熟,但由于聚合反应温度低,制冷设备庞大,聚合釜连续运转周期短,能耗高(1kg胶能量消耗约35~5MJ)。
为了能提高反应温度,对用溶液法进行了大量的研究。
溶液法是以烷基氯化铝与水的络合物为引发剂,在烃类溶剂(如异戊烷)中于-90~-70℃下,异丁烯和少量异戊二烯共聚而成,聚合釜的连续运行周期为10d,聚合釜内胶液中的干胶质量分数在12%以下。
溶液法的优点是可以用聚合物胶液直接卤化IIR。
避免了淤浆法工艺制卤化IIR所需的溶剂切换或胶料的溶解工序,可根据控制工艺条件制备相对分子质量不同的产品。
但溶液法IIR相对分子质量分布较宽,分子链存在支化现象,性能与淤浆法产品还有一定的差距。
该技术由俄罗斯陶里亚蒂合成橡胶公司与意大利Pressindustria公司合作开发,目前,世界上仅俄罗斯的一家工厂采用溶液法生产IIR[1]。
4.3丁基橡胶的改性
①卤化丁基橡胶
在丁基橡胶的己烷溶液中通入氯气,可发生取代反应,使大分子长链中带有氯原了,这种橡胶称为氯化丁基橡胶。
也可采用适当的方法制取溴化丁基橡胶,两者统称为卤化丁基橡胶。
通常它们的含氯量及含溴量各为1.1%一1.3%(质量)和1.8%一2.4%(质量)。
卤化丁基橡胶除了保持丁基橡胶的特性外,由于引入了卤素原子,从根本上克服了高度不饱和结构对于丁基橡胶硫化的阻碍作用。
卤素的存在不仅使硫化是双键活性提高。
并增加了活性中心。
是丁基橡胶对多种硫化剂的反应能力大大提高,硫化速度明显加快;
也使丁基橡胶更容易与其他橡胶甚至高度不饱和的硫化胶掺混,共硫化,牢固地粘接制成理想性能的并用胶。
(主要用于轮胎的气密层、胎侧、耐热内始及一些高温橡胶制品等。
)
②交联丁基橡胶
交联丁基橡胶是由异丁烯、异戊二烯及少量二乙烯基苯三种单体共聚而成。
由于引入了二乙烯基苯,使大分子链上带有少量的侧链乙烯基,易于交联。
由此合成所得的共聚物具有一定程度的交联,是一种工业中所需要的非硫化的丁基型密封材料。
但它也可用一股丁基橡胶的硫化方法硫化。
交联丁基橡胶不冷流、不塌陷,具有较高的弹性复原性。
硫化后具有优异的耐老化、耐候、耐臭氧和良好的气密性。
最大的优点是它既可用普通的琉黄体系来硫化,也可用有机过氧化合物来硫化交联。
用后者方法硫化时,在135℃下的耐热性优于硫黄硫化的普通丁基橡胶。
若加入适当的防老剂,便可改善在150℃~l70℃下的高温性能[4]。
交联丁基橡胶与丁腈橡胶并用后,可改善耐臭氧性能,降低压缩变形和提高耐热性能.常用作耐热的O型垫圈。
4.4生产设备
丁基橡胶生产要求反应器具有物料混合与分散能力强,传热、传质效率高的特点,以适应低温反应速率快的要求。
①轴流列管循环式反应器
反应器特点:
高强度的强制循环,可使引发剂与单体迅速混合均匀,不产生死角,温度分布差较小;
传热面积小,传热系数高;
单位容积的生产能力大;
结构复杂,加工要求严格。
按照容积的大小轴流列管循环式反应器分为7m3、14m3、20m3等不同的规格[1]。
反应特点:
①聚合反应速率快
阳离子聚合的特点之一是聚合反应速率快,即使在低温下进行反应也能在瞬间完成。
因此,聚合热的去除就成了很重要的问题。
聚合反应热常借助反应器夹套中液体乙烯的蒸发而移出。
②对原料的纯度要求很高
水、醚、醇和氨等极性物质都会使引发剂失去活性;
正丁烷有链转作用;
不饱和杂质丁烯-1和丁烯-2则会生成凝胶。
聚合前原料必须提纯,一般要求异丁烯的纯度要达到99%以上,异戊二烯的纯度要达到98%,氯甲烷的纯度要>95%
②多层搅拌内冷管束式反应器
特点:
结构比较简单;
传热系数低而传热面积较大;
反应器内物料分布温度差小于1.5℃;
单位容积的生产能力不及轴流列管循环式。
该反应器有容积为14m3和16m3两种规格,并用于工业生产装置。
5.国内外生产现状和研究进展
5.1国内生产现状
中国丁基橡胶的研究开发始于20世纪60年代,并建立了中试生产装置,后因各种原因而停止。
1999年,合成橡胶厂引进PI公司技术,建成中国惟一的一套30kt/a丁基橡胶生产装置。
该装置能够生产ⅡR1751、ⅡR1751F和ⅡR0745三个牌号的普通丁基橡胶产品,其中ⅡR1751属于内胎级产品,中等不饱和度,高门尼粘度,相当于Exxon公司的268、Bayer公司的301及俄罗斯的BK1675N产品牌号,主要用于制造轮胎内胎、硫化胶囊和水胎等制品;
IR1751F是食品、医药级产品,中等不饱和度,高门尼粘度可用于口香糖基础料以及医用瓶塞的生产;
ⅡR0745是绝缘材料、和薄膜级产品,极低不饱和度、低门尼粘度,主要用于电绝缘层和头薄膜的生产。
最初两年,由于技术、设备等方面的原因,该装置难以连续稳定运行,开工率较低,产品合格率低,原材料消耗、动力消耗及成本偏高。
2000年和2001年产量分别只有4.055kt以及和4.190kt。
经过近两年的技术攻关,生产装置的运行状况有了很大程度的改善,产量逐年增加,2002年产量达到21.545kt,其中产品合格率为84.7%,2003年产量进一步增加到27kt,其中产品合格率达到95.4%[6]。
5.2国外生产现状
截止到2009年底,全世界共有6家生产商的11套装置生产IIR,总产能为109.0万t/a,11套装置分布在8个国家。
目前,世界IIR主要的生产商是埃克森美孚、郎盛Nizhnekamskneftekhim公司(俄罗斯)。
其中,埃克森美孚公司IIR产能最大,为54.8万t/a(含合资企业产能),约占世界总产能的50.2%;
朗盛公司产能第二,为26.5万t/a,约占世界总产量24.3%;
Nizhnekamskneftekhim全球现有的IIR生产装置中,采用埃克森公司专利技术的有6套,其中3套可兼产HIIR;
采用朗盛公司生产技术的装置有2套,均可生产IIR和HIIR;
俄罗斯的2套IIR装置也可生产IIR(T厂)和HIIR(N厂);
中国仅有的1套装置目前还只能生产IIR。
目前,国外各大公司均有意向扩大IIR产能以满足全球IIR市场不断增长的需求。
其中,朗盛公司计划投资4亿欧元(约5.4亿美元)在新加坡新建一套1O万t/a的IIR生产装置,该装置将建在裕廊岛,计划在2010年5月份进行奠基仪式,并将在2013年第l季度开车,比原计划2014年开车有所提前,原因是该公司想利用目前亚太地区IIR市场看涨的有利条件[2];
埃克森美孚与日本合成橡胶公司(JSR)的合资公司日本II公司准备将其位于川崎的IIR装置扩能1.8万t/a至9.8万t/a,拟于2010年底完成,本次扩能将采用埃克森美孚的工艺技术,这项新专利技术可使生产IIR的聚合温度从-95℃提高-75℃,从而可节约能源和资本投资[3]。
俄罗斯Nizhnekamskneftekhim公司计划到2012年将现有的10万t/a产能分2期增加到20万t/a[7]。
5.3技术进展
传统氯甲烷-三氯化铝低温淤浆聚合工艺虽然历史悠久、技术成熟,但聚合温度低、能耗高、聚合连续运转时间段,导致生产成本高,气成品胶价格高于一般通用的橡胶,为此出现许多改进工艺。
①采用烃类溶剂的溶液聚合工艺
原苏联以烷基氯化铝与水的络合物作催化剂,在烃类溶剂如异戊烷忠于-90℃~70℃下聚合,据称工艺过程经济性较好。
其特点是可减轻聚合釜挂胶、延长运转周期,胶液中冷量便于回收,无需溶剂转换,脱除为反应单体后即可直接进行氯化或溴化,可采用一般溶液聚合过程回收聚合物,避免采用氯甲烷引起设备腐蚀及环境污染等问题。
②添加界面活性剂改进淤浆的稳定性
苯乙烯与氯代乙烯基苯(后者为单体总量的1%)在甲苯中的自由基共聚合产物为稳定剂源,按照常规丁基橡胶淤浆聚合工艺,由于异丁烯聚合活性链向稳定剂源链转移从而形成嵌段共聚物(即稳定剂)。
该嵌段共聚物的亲液部分能溶于氯甲烷,憎液部分不溶于氯甲烷而与丁基橡胶或吸附在丁基橡胶的表面上,由此是橡胶颗粒子即使碰撞也不聚结。
由于改进了聚合淤浆的稳定性,可使聚合物浓度从28%提高到35%,从而提高生产能力15%。
且降低能耗30%。
使聚合釜运转周期延长,这是淤浆聚合工艺的重要突破[8]。
6.存在问题
通过引进国外技术,中国建成了一套30kt/a的丁基橡胶生产装置,并且通过近几年的不断努力,实现了安全平稳生产,产量不断提高,在国内市场中所占的份额逐渐扩大,在一定程度上满足了国内实际生产的需求。
但与国外发达国家相比,还存在一定的差距,主要表现在以下几个方面[12]:
(1)生产能力小,产量少,产品自给率低。
目前中国丁基橡胶的生产能力只有30kt/a,远低于其经济规模50kt/a的生产水平,更低于Exxon公司和Bayer公司70kt/a以上的生产规模,造成生产成本相对较高,产品自给率只有30%左右,在国际市场中缺乏竞争力;
(2)技术力度开发不够,品种牌号仍显单一。
目前中国引进的3个普通丁基橡胶产品牌号还不