工业金属管道安装规范Word格式文档下载.docx
《工业金属管道安装规范Word格式文档下载.docx》由会员分享,可在线阅读,更多相关《工业金属管道安装规范Word格式文档下载.docx(25页珍藏版)》请在冰豆网上搜索。
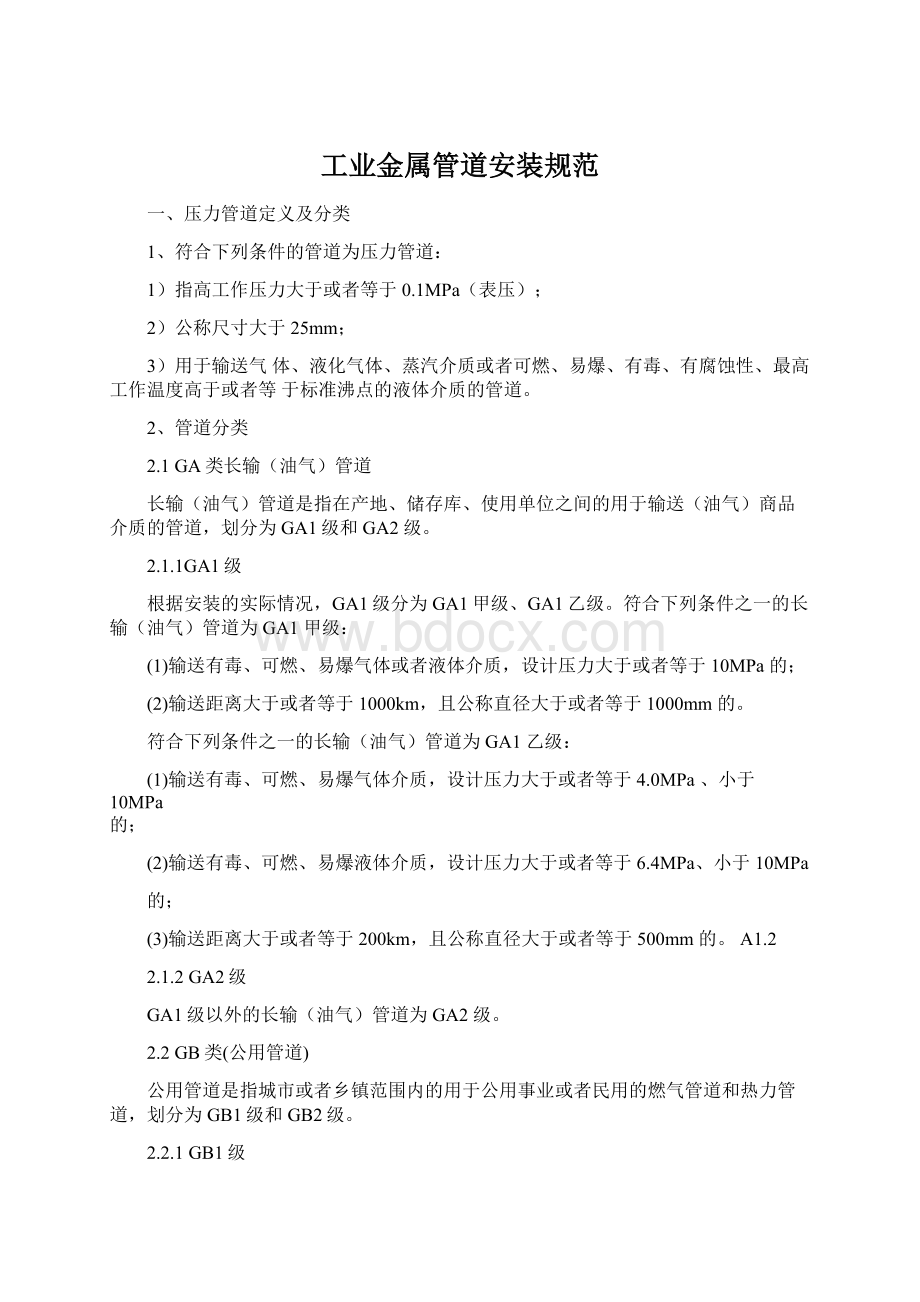
(2)设计压力小于或者等于2.5MPa。
2.3GC类(工业管道)
工业管道是指企业、事业单位所属的用于输送工艺介质的工艺管道、公用工程管道及其他辅助管道,划分为GC1级、GC2级、GC3级。
2.3.1GC1级
符合下列条件之一的工业管道为GC1级:
(1)输送GB5044—1985《职业接触毒物危害程度分级》中规定的毒性程度为极度危
害介质、高度危害气体介质和工作温度高于其标准沸点的高度危害液体介质的管道;
(2)输送GB50160—2008《石油化工企业设计防火规范》与GB50016—2006《建筑设计防火规范》中规定的火灾危险性为甲、乙类可燃气体或者甲类可燃液体(包括液化烃),并且设计压力大于或者等于4.0MPa的管道;
(3)输送流体介质,并且设计压力大于或者等于10.0MPa,或者设计压力大于或者等于4.0MPa且设计温度大于或者等于400℃的管道。
2.3.2GC2级
除GC1级、GC3级管道以外管道为GC2级。
2.3.3GC3级
输送无毒、非可燃流体介质,设计压力小于或者等于1.0MPa且设计温度高于-20℃、但是不高于185℃的工业管道为GC3级。
2.4GD类(动力管道)
火力发电厂用于输送蒸汽、汽水两相介质的管道,划分为GD1级、GD2级。
2.4.1GD1级
设计压力大于或者等于6.3MPa,或者设计温度高于或者等于400℃的动力管道为GD1级。
2.4.2GD2级
设计压力小于6.3MPa,且设计温度低于400℃的动力管道为GD2级。
二、压力管道材料
1一般规定
1.1工业金属管道元件和材料应具有制造厂的产品质量证明文件,并应符合国家现行有关标准和设计文件的规定。
1.2管道元件和材料在使用前应按国家现行有关标准和设计文件的规定核对其材质、规格、型号、数量和标识,并应进行外观质量和几何尺寸检查验收,其结果应符合设计文件和相应产品标准的规定。
管道元件和材料标识应清晰完整,并应能够追溯到产品质量证明文件。
1.3当对管道元件或材料的性能数据或检验结果有异议时,在异议未解决前,该批管道元件或材料不得使用。
1.4铬钼合金钢、含镍低温钢、不锈钢、镍及镍合金、钛及钛合金材料的管道组成件,应采用光谱分析或其他方法对材质进行复查,并应做好标识。
1.5设计文件规定进行低温冲击韧性试验的管道元件或材料,供货方应提供低温冲击韧性试验结果的文件,且试验结果不得低于设计文件的规定。
1.6设计文件规定进行晶间腐蚀试验的不锈钢、镍及镍合金管道元件或材料,供货方应提供晶间腐蚀试验结果的文件,且试验结果不得低于设计文件的规定。
1.7防腐蚀衬里管道的衬里质量应按国家现行标准的规定进行检查验收。
1.8检查不合格的管道元件或材料不得使用,并应做好标识和隔离。
1.9管道元件和材料在施工过程中应妥善保管,不得混淆或损坏,其标记应明显清晰。
材质为不锈钢、有色金属的管道元件和材料,在运输和储存期间不得与碳素钢、低合金钢接触。
1.10对管道元件的外观质量和几何尺寸检查验收结果,应填写管道元件检查记录。
2阀门检验
2.1阀门安装前应进行外观质量检查,阀体应完好,开启机构应灵活,阀杆应无歪斜、变形、卡涩现象,标牌应齐全。
2.2阀门应进行壳体压力试验和密封试验,具有上密封结构的阀门还应进行上密封试验,不合格者不得使用。
2.3阀门的壳体压力试验和密封试验应以洁净水为介质。
不锈钢阀门试验时,水中的氯离子含量不得超过25×
10-6(25ppm)。
试验合格后应立即将水渍清除干净。
当有特殊要求时,试验介质应符合设计文件的规定。
2.4阀门的壳体试验压力应为阀门在20℃时᳔大允许工作压力的1.5倍,密封试验压力应为阀门在20℃时᳔大允许工作压力的1.1倍。
当阀门铭牌标示对᳔大工作压差或阀门配带的操作机构不适宜进行高压密封试验时,试验压力应为阀门铭牌标示的᳔大工作压差的1.1倍。
2.5阀门的上密封试验压力应为阀门在20℃时᳔大允许工作压力的1.1倍。
试验时应关闭上密封面,并应松开填料压盖。
2.6阀门在试验压力下的持续时间不得少于5min。
无特殊规定时,试验介质温度应为5℃~40℃,当低于5℃时,应采取升温措施。
2.7公称压力小于1.0MPa,且公称尺寸大于或等于600mm的闸阀,可不单独进行壳
体压力试验和闸板密封试验。
壳体压力试验宜在系统试压时按管道系统的试验压力进行
试验。
闸板密封试验可用色印等方法对闸板密封面进行检查,接合面上的色印应连续。
2.8夹套阀门的夹套部分应采用设计压力的1.5倍进行压力试验。
2.9试验合格的阀门,应及时排尽内部积水,并应吹干。
除需要脱脂的阀门外,密封面与阀杆上应涂防锈油,阀门应关闭,出入口应封闭,并应作出明显的标记。
2.10阀门试验合格后,应填写“阀门试验记录”。
2.11安全阀的校验,应按国家现行标准《安全阀安全技术监察规程》TSGZF001和设计文件的规定进行整定压力调整和密封试验,当有特殊要求时,还应进行其他性能试验。
安全阀校验应做好记录、铅封,并应出具校验报告。
3其他管道元件检验
3.1GC1级管道和C类流体管道中,输送毒性程度为极度危害介质或设计压力大于或等于10MPa的管子、管件,应进行外表面磁粉或渗透检测,检测方法和缺陷评定应符合国家现行标准《承压设备无损检测》JB/T4730的有关规定。
经磁粉或渗透检测发现的表面缺陷应进行修磨,修磨后的实际壁厚不得小于管子名义壁厚的90%,且不得小于设计壁厚。
3.2合金钢螺栓、螺母应采用光谱分析或其他方法对材质进行复验,并应作好标识。
设计压力大于或等于10MPa的GC1级管道和C类流体管道用螺栓、螺母,应进行硬度
检验。
三、管道加工
1一般规定
1.1管道元件的加工制作除应符合设计文件和相应产品标准的规定。
1.2管道元件在加工过程中,应及时进行标记移植。
低温用钢、不锈钢及有色金属不得使用硬印标记。
当不锈钢和有色金属材料采用色码标记时,印色不应含有对材料产生损害的物质。
1.3管道组成件在加工制作过程中的焊接和焊后热处理、检验和试验应符合有关规定。
2下料切割
2.1碳素钢、合金钢宜采用机械方法切割,也可采用火焰或等离子弧方法切割。
2.2不锈钢、有色金属应采用机械或等离子弧方法切割。
当采用砂轮切割或修磨不锈钢、镍及镍合金、钛及钛合金、锆及锆合金时,应使用专用砂轮片。
2.3镀锌钢管宜采用钢锯或机械方法切割。
2.4切割质量应符合下列规定:
1)切口表面应平整,尺寸应正确,并应无裂纹、重皮、毛刺、凸凹、缩口、熔渣、氧化物、铁屑等现象。
2)管子切口端面倾斜偏差不应大于管子外径的1%,且不得大于3mm。
3弯管制作
3.1弯管宜采用壁厚为正公差的管子制作。
弯曲半径与直管壁厚的关系宜符合下表的规定:
3.2弯管弯曲半径应符合设计文件和国家现行有关标准的规定。
当无规定时,高压
钢管的弯曲半径宜大于管子外径的5倍,其他管子的弯曲半径宜大于管子外径的3.5倍。
3.3有缝管制作弯管时,焊缝应避开受拉(压)区。
3.4金属管应在其材料特性允许范围内进行冷弯或热弯。
3.5采用高合金钢管或有色金属管制作弯管时,宜采用机械方法;
当充砂制作弯管时,不得用铁锤敲击。
铅管加热制作弯管时,不得充砂。
3.6金属管热弯或冷弯后,应按设计文件的规定进行热处理。
当设计文件无规定时,应符合下列规定:
1)除制作弯管温度自始至终保持在900℃以上的情况外,名义厚度大于19mm的碳素钢管制作弯管后,应进行热处理。
2)公称尺寸大于或等于100mm,或名义厚度大于或等于13mm的碳钢、碳锰钢、铬钼合金钢、低温镍钢管制作弯管后,应按下列规定进行热处理。
3.7管子弯制后,应将内外表面清理干净。
弯管质量应符合下列规定:
1)不得有裂纹、过烧、分层等缺陷。
2)弯管内侧褶皱高度不应大于管子外径的3%,波浪间距不应小于褶皱高度的12倍。
3)对于承受内压的弯管,其圆度不应大于8%;
对于承受外压的弯管,其圆度不应大于3%。
4)弯管制作后的最小厚度不得小于直管的设计壁厚。
5)弯管的管端中心偏差值应符合下列规定:
GC1级管道和C类流体管道中,输送毒性程度为极度危害介质或设计压力大于或等于10MPa的弯管,每米管端中心偏差值不得超过1.5mm。
当直管段长度大于3m时,其偏差不得超过5mm。
其他管道的弯管,每米管端中心偏差值不得超过3mm。
当直管段长度大于3m时,其偏差不得超过10mm。
3.8Π形弯管的平面度允许偏差应符合下表的规定:
3.9GC1级管道和C类流体管道中,输送毒性程度为极度危害介质或设计压力大于或等于10MPa的弯管制作后,应按现行行业标准《承压设备无损检测》JB/T4730的有关规定进行表面无损探伤,需要热处理的应在热处理后进行;
当有缺陷时,可进行修磨。
修磨后的弯管壁厚不得小于管子名义壁厚的90%,且不得小于设计壁厚。
3.10弯管加工合格后,应分别填写管道弯管加工记录和管道热处理报告。
4卷管制作
4.1卷管的同一筒节上的两纵焊缝间距不应小于200mm。
4.2卷管组对时,相邻筒节两纵缝间距应大于100mm。
支管外壁距焊缝不宜小于50mm。
4.3有加固环、板的卷管,加固环、板的对接焊缝应与管子纵向焊缝错开,其间距不应小于l00mm。
加固环、板距卷管的环焊缝不应小于50mm。
4.4卷管对接环焊缝和纵焊缝的错边量应符合现行国家标准《现场设备、工业管道焊接工程施工规范》GB50236的有关规定。
4.5卷管的周长允许偏差及圆度允许偏差应符合下表的规定:
4.6卷管校圆样板的弧长应为管子周长的1/6~1/4;
样板与管内壁的不贴合间隙应符合下列规定:
1)对接纵缝处不得大于壁厚的10%加2mm,且不得大于3mm。
2)离管端200mm的对接纵缝处不得大于2mm。
3)其他部位不得大于1mm。
4.7卷管端面与中心线的垂直允许偏差不得大于管子外径的1%,且不得大于3mm。
每米直管的平直度偏差不得大于1mm。
4.8在卷管制作过程中,应防止板材表面损伤。
对有严重伤痕的部位应进行补焊修磨,修磨处的壁厚不得小于设计壁厚。
5夹套管制作
5.1夹套管预制时,应预留调整管段,其调节裕量宜为50mm~100mm。
5.2夹套管的加工,应符合国家现行有关标准和设计文件的规定。
当内管有焊缝时,该焊缝应进行100%射线检测,并应经试压合格后再封入外管。
5.3外管与内管间隙应均匀,并应按设计文件规定焊接支承块。
支承块的材质应与内管相同。
支承块不得妨碍内管与外管的热胀冷缩。
5.4内管加工完毕后,焊接部位应裸露进行压力试验。
5.5夹套管加工完毕后,外管部分应进行压力试验。
5.6夹套弯管的外管组焊,应在内管制作完毕并经无损检测合格后进行。
夹套弯管的外管和内管应保证其同轴度,同轴度偏差不得大于3mm。
5.7输送熔融介质管道的内表面焊缝,应平整光滑,质量应符合设计文件的规定。
5.8当夹套管组装有困难时,外管可采用剖分组焊的形式进行。
6斜接弯头制作
6.1斜接弯头的组成形式应符合下图的规定。
公称尺寸大于400mm的斜接弯头可增加中节数量,其内侧的最小宽度不得小于50mm。
6.2斜接弯头的焊接接头应采用全焊透焊缝。
当公称尺寸大于或等于600mm时,宜在管内进行封底焊。
6.3斜接弯头的周长允许偏差应符合下列规定:
1)当公称尺寸大于1000mm时,允许偏差为±
6mm。
2)当公称尺寸小于或等于1000mm时,允许偏差为±
4mm。
7支、吊架制作
7.1支、吊架的型式、材质、加工尺寸及精度应符合设计文件和国家现行有关标准的规定。
7.2支、吊架的组装、焊接和检验应符合设计文件和国家现行有关标准的规定。
支吊架的焊接应由合格焊工进行,焊接完毕应进行外观检查,焊接变形应予矫正。
所有螺纹连接均应按设计规定予以锁紧。
7.3制作合格的支、吊架应进行防锈处理,并应妥善分类保管。
合金钢支、吊架应有材质标记。
四、管道焊接及热处理
1工业金属管道及管道组成件的焊接与焊后热处理除应符合本章的规定外,尚应符合现行国家标准《现场设备、工业管道焊接工程施工规范》GB50236的有关规定。
2工业金属管道焊缝位置应符合下列规定:
1)2.1直管段上两对接焊口中心面间的距离,当公称尺寸大于或等于150mm时,不应小于150mm;
当公称尺寸小于l50mm时,不应小于管子外径,且不小于100mm。
2)除采用定型弯头外,管道焊缝与弯管起弯点的距离不应小于管子外径,且不得小于100mm。
3)管道焊缝距离支管或管接头的开孔边缘不应小于50mm,且不应小于孔径。
4)当无法避免在管道焊缝上开孔或开孔补强时,应对开孔直径1.5倍或开孔补强板直径范围内的焊缝进行射线或超声波检测。
被补强板覆盖的焊缝应磨平。
管孔边缘不应存在焊接缺陷。
5)卷管的纵向焊缝应设置在易检修的位置,不宜设在底部。
6)管道环焊缝距支吊架净距不得小于50mm。
需热处理的焊缝距支吊架不得小于焊缝宽度的5倍,且不得小于100mm。
3公称尺寸大于或等于600mm的工业金属管道,宜在焊缝内侧进行根部封底焊。
下列工业金属管道的焊缝底层应采用氩弧焊或能保证底部焊接质量的其他焊接方法:
1)公称尺寸小于600mm,且设计压力大于或等于10MPa、或设计温度低于-20℃的
管道。
2)对内部清洁度要求较高及焊接后不易清理的管道。
4当对螺纹接头采用密封焊时,外露螺纹应全部密封焊。
5需预拉伸或预压缩的管道焊口,组对时所使用的工具应在焊口焊接及热处理完毕并经检验合格后再拆除。
6端部为焊接连接的阀门,其焊接和热处理措施不得破坏阀门的严密性。
7平焊法兰、承插焊法兰或承插焊管件与管子的焊接,应符合设计文件的规定,并应符合下列规定:
1)平焊法兰与管子焊接时,其法兰内侧(法兰密封面侧)角焊缝的焊脚尺寸应为直管名义厚度与6mm两者中的较小值;
法兰外侧角焊缝的᳔小焊脚尺寸应为直管名义厚度的1.4倍与法兰颈部厚度两者中的较小值。
2)承插焊法兰与管子焊接时,角焊缝的最小焊脚尺寸应为直管名义厚度的1.4倍与法兰颈部厚度两者中的较小值,焊前宜控制承口与插口的轴向间隙为1.5mm。
3)承插焊管件与管子焊接时,角焊缝的最小焊脚尺寸应为直管名义厚度的1.25倍,且不应小于3mm。
焊前宜控制承口与插口的轴向间隙为1.5mm。
4)机组的循环油、控制油、密封油管道,当采用承插焊接头时,承口与插口的轴向不宜留间隙。
8支管连接的焊缝形式应符合下列规定:
8.1接支管或插入式焊接支管的接头、整体补强的支管座应全焊透,角焊缝厚度不应小于填角焊缝有效厚度。
8.2鞍形补强件的焊接应符合下列规定:
1)补强圈与支管应全焊透,角焊缝厚度不应小于填角焊缝有效厚度。
2)鞍形补强件与支管连接的角焊缝厚度不应小于支管名义厚度与鞍形补强件名义厚度中较小值的0.7倍。
3)补强圈或鞍形补强件外缘与主管连接的角焊缝厚度应大于或等于鞍形补强件名义厚度的0.5倍。
4)补强圈和鞍形补强件应与主管和支管贴合良好。
应在补强圈或鞍形补强件的边缘(不在主管轴线处)开设一个焊缝焊接和检漏时使用的通气孔,通气孔的孔径宜为8mm~10mm。
补强圈或鞍形补强件可采用多块拼接组成,拼接接头应与母材的强度相同,每块拼板均应开设通气孔。
8.3与主管连接焊缝的检查和修补合格后,再进行补强圈或鞍形补强件的焊接。
8.4效厚度可取支管名义厚度的0.7倍或6.5mm中的较小值。
9工业金属管道及管道组成件焊接完毕应进行外观检查和检验。
有无损检测要求的管道应填写“管道焊接检查记录”。
10业金属管道及管道组成件的焊后热处理应符合设计文件的规定。
当设计文件无规定时,应按下表规定执行。
焊后热处理的厚度应为焊接接头处较厚组成件的壁厚。
11热处理的加热速率和冷却速率应符合下列规定:
1)加热温度升至400℃时,加热速率不应超过205×
25/t℃/h,且不得大于205℃/h。
2)恒温后的冷却速率不应超过260×
25/t℃/h,且不得大于260℃/h,400℃以下可
自然冷却。
12焊后热处理应填写“管道热处理报告”。
五、管道安装
1.1工业金属管道安装前应具备下列条件:
1)与管道有关的土建工程已检验合格,满足安装要求,并已办理交接手续。
2)与管道连接的设备已找正合格,固定完毕。
3)管道组成件及管道支承件等已检验合格。
4)管子、管件、阀门等内部已清理干净、无杂物。
对管内有特殊要求的管道,其质量已符合设计文件的规定。
5)在管道安装前应进行的脱脂、内部防腐或衬里等有关工序已进行完毕。
1.2工业金属管道的坡度、坡向及管道组成件的安装方向应符合设计规定。
1.3法兰、焊缝及其他连接件的设置应便于检修,并不得紧贴墙壁、楼板或管架。
1.4脱脂后的管道组成件,安装前应进行检查,不得有油迹污染。
1.5当工业金属管道穿越道路、墙体、楼板或构筑物时,应加设套管或砌筑涵洞进行保护,应符合设计文件和国家现行有关标准的规定,并应符合下列规定:
1)管道焊缝不应设置在套管内。
2)穿过墙体的套管长度不得小于墙体厚度。
3)穿过楼板的套管应高出楼面50mm。
4)穿过屋面的管道应设置防水肩和防雨帽。
5)管道与套管之间应填塞对管道无害的不燃材料。
1.6当工业金属管道安装工作有间断时,应及时封闭敞开的管口。
7.1.7工业金属管道连接时,不得采用强力对口。
端面的间隙、偏差、错口或不同心等缺陷不得采用加热管子、加偏垫等方法消除。
1.8工业金属管道安装完毕应进行检查,并应填写“管道安装记录”。
1.9埋地工业金属管道防腐层的施工应在管道安装前进行,焊缝部位未经试压合格不得防腐,在运输和安装时,不得损坏防腐层。
1.10埋地工业金属管道安装,应在支承地基或基础检验合格后进行。
支承地基和基
础的施工应符合设计文件和国家现行有关标准的规定。
当有地下水或积水时,应采取排
水措施。
1.11埋地工业金属管道试压、防腐检验合格后,应及时回填,并应分层夯实,同时应填写“管道隐蔽工程(封闭)记录”。
2管段预制
2.1管段预制应按管道轴测图规定的数量、规格、材质选配管道组成件,并应在管段上按轴测图标明管线号和焊缝编号。
2.2自由管段和封闭管段的选择应合理,封闭管段应按现场实测的安装长度加工。
2.3自由管段和封闭管段的加工尺寸允许偏差应符合下表的规定:
2.4预制完毕的管段,应将内部清理干净,并应及时封闭管口。
管段在存放和运输过程中不得出现变形。
3钢制管道安装
3.1法兰安装时,应检查法兰密封面及密封垫片,不得有划痕、斑点等缺陷。
3.2当大直径密封垫片需要拼接时,应采用斜口搭接或迷宫式拼接,不得采用平口对接。
3.3法兰连接应与钢制管道同心,螺栓应能自由穿入。
法兰螺栓孔应跨中布置。
法兰间应保持平行,其偏差不得大于法兰外径的0.15%,且不得大于2mm。
法兰接头的歪斜不得用强紧螺栓的方法消除。
3.4法兰连接应使用同一规格螺栓,安装方向应一致。
螺栓应对称紧固。
螺栓紧固后应与法兰紧贴,不得有楔缝。
当需要添加垫圈时,每个螺栓不应超过一个。
所有螺母应全部拧入螺栓,且紧固后的螺栓与螺母宜齐平。
3.5有拧紧力矩要求的螺栓,应按紧固程序完成拧紧工作,其拧紧力矩应符合设计文件的规定。
带有测力螺帽的螺栓,应拧紧到螺帽脱落。
3.6当钢制管道安装遇到下列情况之一时,螺栓、螺母应涂刷二硫化钼油脂、石墨机油或石墨粉等:
1)不锈钢、合金钢螺栓和螺母。
2)设计温度高于100℃或低于0℃。
3)露天装置。
4)处于大气腐蚀环境或输送腐蚀介质。
3.7高温或低温管道法兰连接螺栓,在试运行时,热态紧固或冷态紧固应符合下列规定:
1)钢制管道热态紧固、冷态紧固温度应符合下表的规定:
2)热态紧固或冷态紧固应在达到工作温度2h后进行。
3)紧固螺栓时,钢制管道᳔大内压应根据设计压力确定。
当设计压力小于或等于6MPa时,热态紧固᳔大内压应为0.3MPa;
当设计压力大于6MPa时,热态紧固᳔大内压应为0.5MPa。
冷态紧固应在卸压后进行。
4)紧固时,应有保证操作人员安全的技术措施。
3.8螺纹连接应符合下列规定:
1)用于螺纹的保护剂或润滑剂应适用于工况条件,并对输送的流体或钢制管道材料不得产生不良影响。
2)进行密封焊的螺纹接头不得使用螺纹保护剂和密封材料。
3)采用垫片密封而非螺纹密封的直螺纹接头,直螺纹上不应缠绕任何填料,在拧紧和安装后,不得产生任何扭矩。
直螺纹接头与主管焊接时,不得出现密封面变形现象。
4)工作温度低于