游艇船壳材料结构设计Word下载.docx
《游艇船壳材料结构设计Word下载.docx》由会员分享,可在线阅读,更多相关《游艇船壳材料结构设计Word下载.docx(22页珍藏版)》请在冰豆网上搜索。
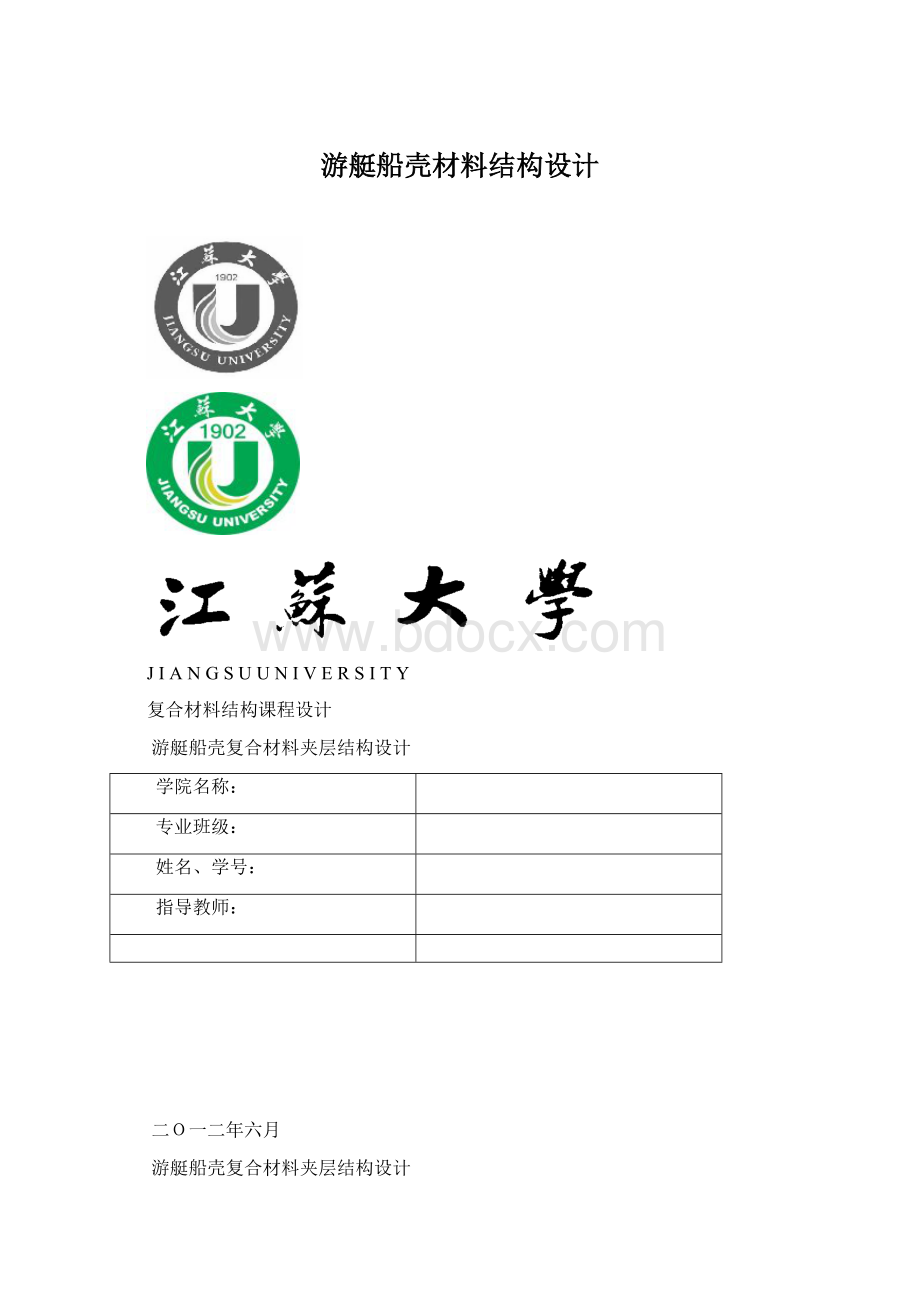
帆艇又分为无辅助动力帆艇和辅助动力帆艇。
机动艇又分为舷外挂机艇、艇内装机艇。
艇内装机艇还可分为小汽艇和豪华艇两个档次;
而按照品质又可以分为高档豪华游艇、家庭型豪华游艇、中档普通游艇及廉价游艇。
若按照游艇的船壳材料可分为有木质艇、玻璃钢艇、凯芙拉纤维增强的复合材料艇、铝质艇和钢质艇。
目前,玻璃钢艇占绝大比例,赛艇、帆艇、豪华艇使用凯芙拉增强材料的较多;
铝质艇在舷外挂机艇和大型豪华游艇中占一定比例。
1.2游艇的主要参数
1.2.1尺寸
欧美FRP游艇的尺度范围较大,艇长Loa=5m-44m,佛汝德数
,体积佛汝德数
(
)。
属于一种尺度相对较小、航速较高、受力复杂、布置难度大、使用要求高的过渡型快艇或滑行快艇。
一般情况下,艇长在12m以下属于小型快艇。
佛汝德数FN>
3.0时,艇体重量几乎全部由作用在艇底的流体动力所支持,即为滑行艇。
与排水型船考虑的因素不同,快艇主要参数的选择应在满足定员舱布置要求的基础上,着重考虑耐波性、操纵性及航行中的稳性等航海性能。
图1所示为游艇的L与B的关系曲线;
图2为L与L/B的关系曲线。
其回归方程为:
B=0.2022*Lw+1.8或Lw/B=0.0633*Lw+2.1
(1)
图1L与B的关系曲线图2L与L/B的关系曲线
据统计L/B=2.5-4.1,远小于FN在0.3左右的中速普通排水型船。
其目的在于增加艇体展弦比,以提高水动力性能。
从图中可以看出,在艇长较小时,对应的L/B较小,随着长度的增加,L/B呈增加趋势。
对B/d随艇长的变化统计值为:
在艇长为14m以下时的B/d=4.0-5.5;
艇长大于14m时,B/d值较平缓,在5.2-5.7之间,其值比中速普通排水型船高很多(如FN在0.3左右的渔船,其B/d≤3.0)。
这是由于快速游艇在航行状态受力复杂,对稳性要求较高的缘故。
另外,这些游艇的干舷值亦比普通排水型船的大,这一点与普通客船类似,因为大的干舷对大倾角稳性有利。
1.2.2船型
如上所述,FRP游艇属于过渡型快艇或滑行快艇范围,型线以折角型为主,尾部采用方尾。
一般常见的有单折角形(即在平板龙骨与舭部折角之间的艇底板有1道纵向折角线)和双折角形(即在平板龙骨与舭部折角之间的艇底板有2道纵向折角线)。
其特点是增加艇底板的褶皱,产生数个小滑行平面,在增加滑行效率的同时,增加艇底板的刚性。
舭部折角线还可以起到舭龙骨的减摇作用。
尾部采用方尾,方尾的相对宽度fB=BT/BX(BT:
方尾宽度;
BX:
艇的最大宽度)表征尾部的收缩程度。
对于高速快艇,适当增加fB可以增加尾部水压力作用不使艇体的航行纵倾过大,同时还可使尾部水流收缩不致太快,从而增加了“虚长度”,因而对阻力性能有利。
另外,方尾还具有有利于尾部上甲板、舵机舱和推进器等布置以及增加稳性,便于施工等优点。
对于FN>
3.0的高速游艇,一般采用深V型,底升角在首部较大,最大可达60°
,由舯向尾升角逐渐减小,到尾板处升角接近0°
。
以减轻高速航行中的首部拍击现象,有利于耐波性。
尾部采用较平坦的纵剖线,可以减小高速水流的能量损失,也可以使纵中剖面面积不至于过小,有利于满足操纵性的要求。
1.2.3纵稳性
与普通排水型船不同,因为小型快艇的L/B相对较小,导致纵稳心半径小,据统计艇长在10m以下的游艇,其H/LW=1.1-1.6(H--纵向初稳性高;
LW—水线长),因此保证纵向稳性是小型快艇设计中的一个重要问题。
应适当减小FRP游艇的进水角,并使浮心位置后移,这对减小剩余阻力是有利的。
为了减少高速艇的“海豚”现象,建议适当地把重心往前移向艇舯,浮心位置应位于重心之后附近,使游艇在静水中处于轻微首倾,在航行中随着速度的提高,浸水线不断向后缩短,浮心逐渐后移与水动力所产生的升力作用线合成使游艇首部抬起,这时不至于因升力作用点沿纵向变化而远离重心发生过大的纵向摇摆,即有利于纵向稳性。
笔者对艇长在10m以下的小型游艇的浮心纵向位置LCB进行了统计,其取值范围在舯后(7%-10%)L。
对于深V型滑行艇,建议使用文献[6]提供的计算方法。
克莱门特将62系列模型的稳定性试验资料整理为
对FNV关系曲线,如图3所示。
不发生海豚运动的限界曲线可以用如下方程式表示:
(2)
式中:
--压力中心,即重心在艇尾板前面的距离,m;
b—重心纵向位置处的艇体宽度(包括防溅条在内),m;
FNV—排水体积佛汝德数,CL--动载荷系数,
(3)
--艇的排水量,kg;
--水的密度,kgfs2/m4;
--艇的航速,m/s;
B—平均艇宽,
,m;
BX—艇中部折角线处宽度,m;
BT--艇尾板折角线处宽度,m。
使用图3曲线的方法是,先用(3)式计算系数CL;
再计算
和FNV,然后判断点(FNV,
)是否在稳定区内。
1.2.4快速性
过渡型快艇的棱形系数Cp值的选取与设计航速有关。
一般按略小于“理论最佳棱形系数”的原则选定。
这是因为这种艇的经常使用速度往往低于设计速度。
取略小于最佳的棱形系数,对阻力性能是有利的,相反的如果取“最佳值”,使艇经常处于不利状态下。
航速粗估在设计工作和营运工作中都是比较重要的,根据统计并回归,游艇航速与主机功率存在如下关系:
(4)
式中:
V—游艇航速,kn;
MHP—主机总功率,kw;
--游艇排水量,t;
L—水线长度,m。
若将估算航速的(4)式与游艇资料绘制成图4,能很好地反映游艇
与
的关系。
质艇在35米以上远洋大型豪华游艇中占比例较多。
图3系列62海豚运动界限图图4(3)式与实船资料比较
1.2.5游艇材料
随着科技的发展,船艇设计的性能不断提高,人们对快艇速度的要求也在不断提高。
快速游艇受到更高的强度负荷,这就要求其必须具备较高的强度和刚度。
而具有刚性不足、强度有余特点的传统玻璃钢结构已不能满足现代高速艇的发展要求。
近几年对玻璃钢材料的改进主要体现在夹层结构、增强材料及树脂系统。
对于夹层结构,目前采用夹心结构代替过去的单板结构。
实践证明,夹心结构在刚性方面明显地优于单板结构。
目前国外出现了聚丙烯蜂窝状夹心材,这种夹心材的抗弯、抗冲击强度都优于其它夹心材,而且还能达到阻燃效果,单位重量也低于其它夹心材,施工方法也比其它夹心材简单。
对增强材料和树脂系统的改进。
近年来复合毡—合成纤维与玻璃毡组成的混合材料已得到应用。
这种材料可提供更优的性能,更低的树脂含量,能更好地控制船体重量。
例:
将Kevlar纤维与玻璃纤维组成混合增强材料,用于对强度负荷要求较高的高速船体上,仍能使船体重量减少12%,而且完全可以满足它的强度要求。
对表面胶衣系统的改进。
现在世界上制造豪华玻璃钢游艇的厂家已开始使用一种称作Barriercoat的树脂。
这种Barriercoat树脂用在胶衣层后面,湖制层前面。
起到了一个胶衣层和湖制层之间压力传递和缓解的作用。
有很好的防渗透能力。
Barriercoat树脂与胶衣层和湖制层有着非常好的化学共溶性,非常强的粘接强度。
在玻璃钢船艇上使用结果表明,Barriercoat树脂层还能减少胶衣层的破裂现象。
2.游艇受力分析及性能要求
2.1作用在船体上的力
船舶从建造、下水、停泊、航行及进坞修理等全部过程中,受到各种外力的作用,这些外力常常会使船体结构产生变形或损坏。
船体受力主要有总纵弯曲力、横向载荷和其它局部力。
2.1.1船体的总纵弯曲
船体的总纵弯曲是指作用在船体上的重力、浮力、波浪水动力和惯性力等而引起的船体绕水平横轴的弯曲。
它由静水总纵弯曲和波浪总纵弯曲两部分迭加而成。
(1)船体静水总纵弯曲
船舶在静水中受到的外力有船舶及其装载的重力和水的浮力。
重力P的方向向下,浮力D的方向向上。
重力和浮力在静水中处于平衡状态,即重力和浮力大小相等方向相反,作用在同一铅垂线上,见图5-a)。
但对于船体的某一段,重力和浮力的大小并不相等,如图5-b)所示。
重力大的一段有下移的趋势,浮力大的一段有上移的趋势。
由于船体是一整体结构,各段不可能发生上下移动,在船体结构内必然有内力产生,使船体发生弯曲。
当船体中部向上弯曲时,称为中拱弯曲;
当船体中部向下弯曲时,称为中垂弯曲。
船体弯曲时,在船体内产生弯曲力矩,弯矩的最大值在船体的中部,向首尾部逐渐减小,见图5-c)。
由于船舶装载情况及船体浸水部分形状总是变化,因而船体各段重力和浮力的不平衡也总是存在。
图5船体静水总纵弯曲图6波浪中的总纵弯曲
a)中拱弯曲b)中垂弯曲
(2)船体波浪总纵弯曲
在波浪状况下,船体内产生的总纵弯矩会比静水中大。
当波长与船长相等或接近时,船体的弯曲最严重。
其弯曲形式如图6所示:
(a)波峰在船中时——中拱弯曲——甲板受拉伸、底部受压缩;
(b)波谷在船中时——中垂弯曲——甲板受压缩,底部受拉伸。
2.1.2作用在船体上的横向载荷
船体在静水或波浪中,它的各部分结构还受到局部的水压力和货物等横向载荷,会产生局部弯曲及其它局部受力情况。
作用在船体上的其它力有:
船体上机器和螺旋桨运转时的振动力,船首端的波浪砰击和水面漂浮物的撞击等局部的外力,油船的油货舱内液体的晃动载荷,以及船舶进坞或搁浅时受到船底下墩木或河床的反力作用等。
此外,船舶在波浪状态下航行,由于升降、俯仰和摇摆等运动而产生惯性力,这对船体结构会产生不利的影响,例如船舶横摇时会引起肋骨的歪斜和船体的扭曲。
2.1.3其它局部受力情况
2.2船壳性能要求
作为良好的船壳材料应该具备以下一些特点:
1.质量轻强度大;
2.耐腐蚀好、能够抗海生物附着,从而更加适应在海洋环境中使用;
3.能够吸收高能量,冲击韧性好,这样船舶不易因一般的碰撞、挤压而损坏;
4.导热系数低,隔热性好;
5.船体表面能达到镜面光滑,色彩多样,从而可以建造结构复杂、款式多样、外形美观的游艇;
6.可设计性好,能按船舶结构各部位的不同要求,通过选材、铺层研究和结构选型实现优化设计;
7.整体性好,可以做到整个船体无接缝和缝隙;
8.船体成型简便,可以批量生产,低价制造;
9.易于保养,使用寿命长,维修成本低。
3玻璃钢船壳结构设计
3.1玻璃钢的特点
目前使用比较广泛的船壳材料是玻璃钢,因为玻璃钢可以满足很多作为船壳材料所需的特殊性能,并且要优于很多传统船壳材料:
1轻质高强
玻璃钢的相对密度在1.5-2.0之间,只有碳钢的1/4-1/5,可是拉伸强度却接近甚至超过碳素钢,而比强度可以与高级合金钢相比。
因此,在航空、火箭、宇宙飞行器、高压容器以及在其他需要减轻自重的制品应用中,都具有卓越成效。
某些环氧FRP的拉伸、弯曲和压缩强度均能达到400Mpa以上。
2耐腐蚀性能好
玻璃钢是良好的耐腐材料,对大气、水和一般浓度的酸、碱、盐以及多种油类和溶剂都有较好的抵抗能力。
3热性能良好
玻璃钢热导率低,室温下为1.25-1.67kJ/(mhK),只有金属的1/100-1/1000,是优良的绝热材料。
在瞬时超高温情况下,是理想的热防护和耐烧蚀材料,能保护宇宙飞行器在2000℃以上承受高速气流的冲刷。
4可设计性好
(1)可以根据需要,灵活地设计出各种结构产品,来满足使用要求,可以使产品有很好的整体性。
(2)可以充分选择材料来满足产品的性能,如:
可以设计出耐腐的,耐瞬时高温的、产品某方向上有特别高强度的、介电性好的,等等。
5工艺性优良
(1)可以根据产品的形状、技术要求、用途及数量来灵活地选择成型工艺。
(2)工艺简单,可以一次成型,经济效果突出,尤其对形状复杂、不易成型的数量少的产品,更突出它的工艺优越性。
3.2玻璃钢复合材料的泡沫夹层结构
尽管玻璃钢作为一种造船材料已经确定无疑,然而,在实践中人们发现玻璃钢应用于造船方面还有很大的潜力。
当初玻璃钢能够成为新兴船壳材料并逐渐发展成为最重要的船壳材料之一的原因就在于其质量轻强度高,而现在就要在保证其强度的基础上进一步减轻其重量,以提高其性能,由此想到了在玻璃钢材料中添加泡沫夹层。
泡沫芯材为孔隙材料芯材,可以起到减轻结构的重量,增加结构的刚度,提高结构的强度等作用。
夹层结构一般是由上面板、上面板与芯材的粘结层、芯材、下面板与芯材的粘结层以及下面板所构成,这五个要素组成了一个整体的夹层结构。
夹层结构传递荷载的方式类似于工字梁(见图7),上下面板(翼板)主要承受由弯矩引起的面内拉压应力和面内剪应力,而芯材(腹板)主要承受由横向力产生的剪应力(见图8)。
图7工字梁和夹层结构的对比图8夹层结构对称间支梁的弯曲
为了使夹层结构的各要素能协同承载,面板与芯材之间的粘接层必须能传递荷载,这样至少应具备和芯材一样的强度。
通常,如果加载以后,夹层结构的芯材发生破坏,其破坏位置一般位于粘接层下面的芯材部分,因为粘接层芯材表面的孔隙中由于填充了胶粘剂/树脂,提高了粘接层泡沫的强度。
选择正确的胶粘剂对夹层结构的强度也有非常重要的意义,通常在选择胶粘剂的时候除了强度以外,还需要考虑使用温度、烟雾条件及其与芯材的面板材料的兼容性。
如果选择与面板材料共固化,则胶粘剂或胶膜的固化条件需要与面板的共固化条件相一致。
表1夹层结构和非夹层结构的刚度和重量之对比
表1中的结构构造是常见的FRP船舶中的铺层设计。
可以看出,在弯曲刚度相近的情况下,夹层结构的重量比非夹层结构减轻很多。
泡沫夹层结构的优点还有:
良好的隔热和隔音性能、抗冲击损伤性能及施工简便性等。
在夹层结构中由于芯材是孔隙材料,整个夹层结构的导热系数和R值均比非夹层结构低。
由于层合板的层数减少,降低了铺层制作成型的工作量,同时因为夹层结构的刚度较高,减少了加筋的数量,这有利于冲击荷载的扩散。
此外,孔隙芯材还能降低船舶航行中的噪声。
3.3玻璃钢夹层结构的设计
高速船为了减轻船体重量,在舷侧板、甲板、舱壁板、尾封板(通常为胶合板芯)和上层建筑甲板室的壁板采用玻璃钢夹层结构。
这些板的基本受力形式有横向弯曲、板面内压缩和剪切等。
由于夹层结构中芯材性能较低,故在进行夹层结构设计时有一些特殊要求。
3.3.1 玻璃钢夹层结构弯剪强度设计
玻璃钢夹层结构弯剪时剪切强度主要由芯子承受,面板仅起部分作用。
相对于航空产品结构,船用夹层结构的面板是较厚的,故在船舶设计的规范中应计及此影响。
设夹层板条梁的跨距即板格短边长为S,受均布载荷P,则夹层板条梁端点处剪应力τ最大为
(5)
式中d为夹层板面面板中心线间的距离。
夹层板总厚度,
,
为面板厚度。
中国船级社的《海上高速船入级与建造规范》中规定,夹层结构的许用剪切应力
(6)
为为夹层结构板的弯剪强度,可以表示为
(7)
式中
为芯材的剪切强度,k为系数,与泡沫塑料的品种及
有关,
是表征面板对弯剪强度的贡献。
通过对试验结果的回归统计,得出下列统计曲线公式:
对于聚氨酯泡沫塑料为:
(8)
(9)
对于聚氯乙烯泡沫塑料为:
(10)
(11)
对于胶合板芯为:
(12)
用式(7)~(12),并用许用剪切应力,可按式(5)求出d。
通过上述统计分析,得出下述简化公式(适用于
范围):
PU芯夹层板:
(13)
PVC芯夹层板:
(14)
胶合板芯夹层板:
(15)
3.3.2 夹层结构骨材的弯曲强度设计
通常玻璃钢船体的板,不论是单板还是夹层板,都是借助骨材来加强的。
这些板从局部强度角度看,主要承受与板表面垂直的横向载荷,因而支撑板的骨材主要受弯曲。
中国船级社的《海上高速船入级与建造规范》中,根据弯曲强度提出了骨材的最小剖面模数要求(包括骨材的有效带板)。
3.3.2.1 骨材本身的剖面模数
通过试验实测证明,对于PU、PVC泡沫塑料骨材,泡沫塑料可视为无效芯材,计算剖面模数时可忽
略不计。
对于胶合板芯和松木芯的骨材,芯材应视为有效芯材,这种骨材的弯曲刚度D及惯性矩J按下二式计算:
(16)
(17)
式中Jf、Jc为惯性矩,Ef、Ec为弹性模量,其下标“f”表示玻璃钢,“c”表示芯材。
在计算骨材的剖面模数时,应计及玻璃帽型腹板和芯子受剪变形对弯曲应力增加的影响。
实测结果说明:
对于空心及无效芯材的骨材,弯曲应力增加至1.5~1.7倍;
对于胶合板、松木芯骨材,弯曲应力增加至1.2倍左右。
另外,在实际成型骨材中多少有一些工艺质量缺陷,通过人为皮芯脱胶骨材(脱胶面积随机,分别为10%,20%,30%)试验表明,由于皮芯的随机脱胶,使骨材弯曲强度降低10%左右。
3.3.2.2 有效带板宽度
玻璃钢帽型骨材及其附连翼板(简称“带板”)在承受弯曲时,带板上的应力分布沿板宽度方向是不均匀的。
从试验实测的应变分布,按下式求出实测的有效带板宽度be
(18)
式中b为骨材间距;
ϵ(y)、ϵmax分别为应变、最大应变。
3.3.3夹层结构纵桁的剪切强度设计
针对玻璃钢高速艇的船底纵桁或龙骨在受到船底波浪冲击力作用时,纵桁或龙骨的跨距端点处将受到最大剪切力的作用,通常玻璃钢高速艇的船底纵桁或龙骨采用高矩形剖面,以胶合板或松木为芯材外包玻璃钢的夹层结构梁形式。
通过试验及分析认为,夹层结构纵桁剪切强度计算可按包括玻璃钢表皮在内的横剖面面积,许用剪切应力可采用芯材的许用剪切应力(即不计及玻璃钢表皮对纵桁剪切强度的影响)。
根据以上公式可以计算出理论上船壳的厚度,以及表面玻璃钢硬质层与夹层泡沫芯材厚度之比。
但是在实际制造过程中,玻璃钢船壳厚度与船体长度有关,其平均厚度约为艇长的千分之一(对于具有大面积非支撑加强的扁平船体的机动艇,壁厚往往要增加百分之二十)。
对于玻璃钢夹层结构,泡沫芯材夹层占总厚度的3/4,两面玻璃钢硬质层厚度占1/4,这样的比例可以保证作为船壳的强度要求,同时将质量降到最低。
3.3.4结构设计图及尺寸
(1)游艇整体结构及船体尺寸如图9:
图9游艇外观及尺寸
(2)船壳玻璃钢泡沫芯材示意图及尺寸如图10(图注尺寸为船壳厚度的理想平均值)
图10玻璃钢泡沫芯材尺寸
针对上面的设计图所示的游艇,其艇长为5.22m,船壳厚度约为艇长千分之一,实际制造中往往还会预留10%~20%的壁厚,所以船壳总厚度约6cm,再由船壳玻璃钢硬质层与泡沫芯材厚度比为1︰3,由此可得船壳玻璃钢复合层尺寸,如图10所示。
4.泡沫芯材的选择
玻璃钢/复合材料(FRP/CM)中常用的泡沫芯材有聚氯乙烯(PVC)、聚苯乙烯(PS)、聚氨酯(PUR)、丙烯腈-苯乙烯(SAN)、聚醚酰亚胺(PEI)及聚甲基丙烯酰亚胺(PMI)等泡沫,其中PS和PUR泡沫通常仅作为浮力材料,而不是结构用途。
目前PVC泡沫已几乎完全代替PUR泡沫而作为结构芯材,只是在一些现场发泡的结构中除外。
4.1泡沫芯材的发展历程
严格意义上讲,第一种用在承载构件夹层结构中的结构泡沫芯材是使用异氰酸酯改性的PVC泡沫,或称交联PVC。
第一个采用PVC泡沫夹芯的夹层结构是保温隔热车厢。
交联PVC的生产工艺是由德国人林德曼在上世纪30年代后期发明的。
二次大战以后法国将该工艺列入战争赔偿中,由克勒贝尔蕾洛雷特塑料公司(KleberRenolit)开始生产Klegecell交联PVC泡沫,主要是一些用在保温隔热车厢中的低密度产品。
上世纪50-60年代,克勒贝尔蕾洛雷特塑料公司给几家欧洲公司发放了PVC泡沫的生产许可证。
另外两家美国公司,B.F歌德雷奇(B.FGoodrich)和佳士迈威(Johns-Manville)也买到了许可证开始生产,但是几年以后就停产。
当所有的生产许可证都过期以后,交联PVC的生产工艺过程转为公开。
进入70年代以后,多数原来的欧洲许可生产厂家也已停产。
目前两个主要的生产厂家是戴博(Diab)公司的Divinycell和Klegecell系列PVC泡沫及爱瑞柯斯(Airex)公司的Herex系列PVC泡沫。
20世纪40年代后期,林德曼使用高压气体作为发泡剂,制造出未经过改性的PVC泡沫,也叫线性PVC泡沫。
英国于1943年首先制成聚苯乙烯泡沫塑料,1944年美国道化学有限公司用挤出法大批量的生产聚苯乙烯泡沫塑料。
第二次世界大战期间,德国拜尔的试验人员对二异氰酸酯及羟基化合物的反应进行研究,制得了PUR硬质泡沫塑料、涂料和粘合剂。
1952年,拜尔公司报道了软质聚氨酯泡沫塑料的研究成果。
1993年,加拿大的ATC公司开始生产SAN泡沫。
其制造工艺和线性PVC相似。
PMI泡沫是由德国罗姆(Rohm)公司于1966年首先用丙烯腈、甲基丙烯腈、丙烯酰胺和甲基丙烯酸酯热塑性树脂在180下发泡并交联制作聚甲基丙烯酰亚胺泡沫的技术,接着日本的积水化学公司于1967年使用辐射交联方法制作聚甲基丙烯酰亚胺泡沫。
4.2常见泡沫芯材的性能和应用
交联PVC泡沫:
这种