无凸缘筒形件的拉深模具设计.docx
《无凸缘筒形件的拉深模具设计.docx》由会员分享,可在线阅读,更多相关《无凸缘筒形件的拉深模具设计.docx(18页珍藏版)》请在冰豆网上搜索。
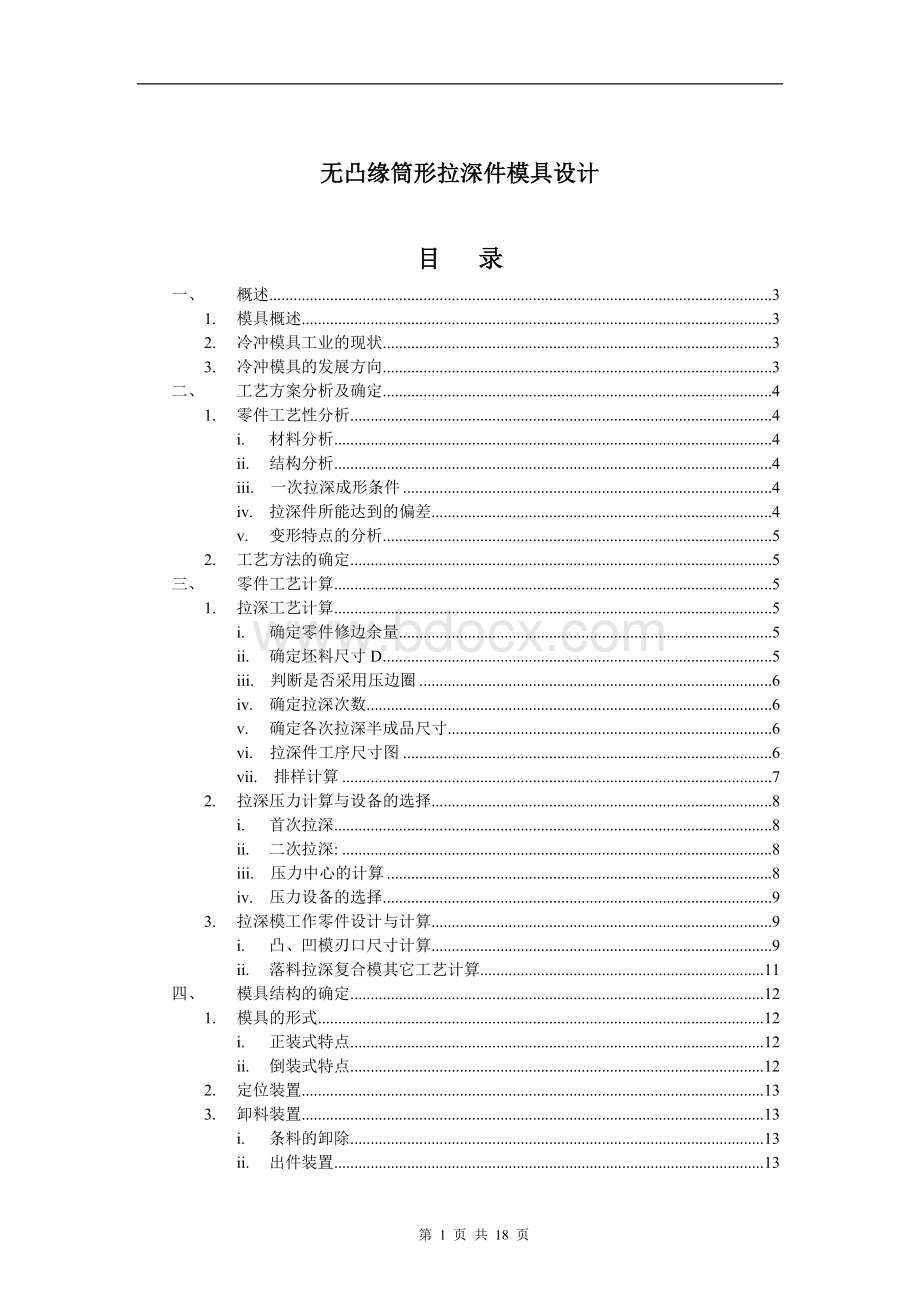
无凸缘筒形拉深件模具设计
目录
一、 概述 3
1. 模具概述 3
2. 冷冲模具工业的现状 3
3. 冷冲模具的发展方向 3
二、 工艺方案分析及确定 4
1. 零件工艺性分析 4
i. 材料分析 4
ii. 结构分析 4
iii. 一次拉深成形条件 4
iv. 拉深件所能达到的偏差 4
v. 变形特点的分析 5
2. 工艺方法的确定 5
三、 零件工艺计算 5
1. 拉深工艺计算 5
i. 确定零件修边余量 5
ii. 确定坯料尺寸D 5
iii. 判断是否采用压边圈 6
iv. 确定拉深次数 6
v. 确定各次拉深半成品尺寸 6
vi. 拉深件工序尺寸图 6
vii. 排样计算 7
2. 拉深压力计算与设备的选择 8
i. 首次拉深 8
ii. 二次拉深:
8
iii. 压力中心的计算 8
iv. 压力设备的选择 9
3. 拉深模工作零件设计与计算 9
i. 凸、凹模刃口尺寸计算 9
ii. 落料拉深复合模其它工艺计算 11
四、 模具结构的确定 12
1. 模具的形式 12
i. 正装式特点 12
ii. 倒装式特点 12
2. 定位装置 13
3. 卸料装置 13
i. 条料的卸除 13
ii. 出件装置 13
4. 导向零件 13
5. 模架 13
i. 标准模架的选用 13
五、 第二次拉深凹模零件图 15
i. 拉深凹模如图5-1所示 15
六、 第二次拉深凸模零件图 15
ii. 拉深凸模如图5-2所示 15
七、 模具的工作原理 15
1. 拉深的变形过程 15
2. 各种拉深现象 16
i. 起皱:
16
ii. 变形的不均匀:
16
iii. 材料硬化不均匀 16
八、 总结 17
九、 参考文献 18
一、概述
1.模具概述
模具是高新技术产业的一个组成部分,是工业生产的重要基础装备.用模具生产的产品,其价值往往是模具价值的几十倍。
模具技术是一门技术综合性强的精密基础工艺装备技术,涉及新技术、新工艺、新材料、新设备的开发与推广应用.是冶金、材料、计量、机电一体化、计算机等多门学科以及铸、锻、热处理、机加工、检测等诸多工种共同打造的系统工程。
用模具生产制品具有高效率、低消耗、高一致性、高精度和高复杂程度等特点,这是其他任何加工制造方法所不及的。
目前,模具制造业已成为与高新技术产业互为依托的产业,模具工业技术水平的高低已成为衡量国家制造业水平的重要标志之一。
2.冷冲模具工业的现状
到了21世纪.随着计算机软件的发展和进步.CAD/CAE/CAM技术日臻成熟,其现代模具中的应用越来越广泛。
目前我国冲压模具无论在数量上,还是在质量、技术和能力等方面都已有了很大发展,但与国民经济需求和世界先进水平相比,仍具有较大的差异,一些大型、精密、复杂、长寿命的高档模具每年仍大量进口,特别是中高档轿车的覆盖件模具。
目前仍主要依靠进口。
而一些低档次的简单冲模,则已供.过于求,市场竞争非常激烈。
3.冷冲模具的发展方向
发展模具工业的关键是制造模具的技术、相关人才以及模具材料。
模具技术的发展是模具工业发展最关键的—个因素,其发展方向应该为适应模具产品“交货期短”、“精度高”、质量好”和“价格低”的要求服务。
为此,急需发展如下:
1.全面推广模具CAD/CAM/CAE技术:
:
随着微机软件发展和进步,普及CAD/CAM/CAE技术的条件已基本成熟,各企业需要加大CAD/CAM技术培训和技术服务的力度,同时进一步扩大CAE技术的应用范围。
2.模具扫描及数字化系统:
高速扫描机和模具扫描系统具备从模型或实物扫描到加工出期望的模型所需的诸多功能,这样可以大大缩短模具研制制造周期。
3.电火花加工:
电火花加工(EDM)虽然已受到高速铣削的严峻挑战,但其固有特性和独特的加工方法是高速铣削所不能完全替代的。
4.优质材料及先进表面处理技术:
选用优质钢材和应用相应的表面处理技术来提高模具的寿命就显得十分必要。
5.模具研磨抛光将自动化、智能化:
模具表面的质量对模具使用寿命、制件外观质量等方面均有较大的影响,研究自动化、智能化的研磨与抛光方法替代现有手工操作,提高模具表面质量是重要的发展趋势。
二、工艺方案分析及确定
1.零件工艺性分析
如图2-1所示拉深零件,材料为08F,厚度为1mm。
其工艺性分析内容如下:
图2-1筒形件拉深零件图
i.材料分析
此拉深模选用材料为08F
08F是极软的低碳钢,强度、硬度很低,而塑性、韧性极高,具有良好的冷变形性和焊接性,正火后切削加工性尚可,退火后导磁率较高,剩磁较少,但淬透性、淬硬性极低。
因此,此材料具有良好的拉深成形性能。
ii.结构分析
零件为一无凸缘筒形件,结构简单,底部圆角半径为R3,满足筒形拉深件底部圆角半径大于一倍料厚的要求,因此,零件具有良好的结构工艺性。
iii.一次拉深成形条件
∵圆筒形拉深件一次成型条件为:
H≤0.5~0.7d
拉深件高度H=29mm;拉深件中径d=30+1=31mm
(0.5~0.7)d=(0.5~0.7)*31=15~21mm\该筒形件不能一次拉深成形
iv.拉深件所能达到的偏差
a)直径偏差
查文献[2]表4.4得此零件所能达到的直径偏差是±0.25,因此∅300+0.52满足条件。
b)高度偏差
查文献[2]表4.5得此零件所能达到的高度偏差是±0.06,因此29±0.06满足条件。
v.变形特点的分析
1)拉深时的变形区在毛坯的凸缘部分,其它部分为传力区,不参与主要变形;
2)毛坯变形区在切向压应力和径向拉应力作用下,产生切向压缩和径向拉长变形;
3)极限变形参数主要受到毛坯传力区承载能力的限制。
2.工艺方法的确定
由上面分析可知,为了保证工件的性能,该工件不能一次拉深到位,至少需经过两次拉深。
而完成该工件需经过落料、拉深工序。
综合实际情况,可有以下3种方案(如表格2-1所示)供选择:
表2-1
序号
工艺方案
结构特点
1
单工序模生产:
先落料,再进行第一次拉深、第二次拉深,最后切边
模具结构简单,但需要两道工序、两套模具才能完成零件的加工,生产效率低。
2
复合模生产:
先落料、第一次拉深复合、继而进行后续拉深,最后切边
同一副模具完成两道不同的工序,大大减小了模具规模,降低了模具成本,提高生产效率,也难以提高压力机等设备的使用效率;操作简单、方便,适合中小批量生产。
3
连续模生产:
落料后正、反拉深,最后切边
正、反拉深模具结构比较复杂,要求工步精确,并需要采用双动力压力机,生产效率高,适合于大量而且具备双动力机的情况。
根据本零件的设计要求以及各方案的特点,决定采用第2种方案比较合理。
三、零件工艺计算
1.拉深工艺计算
零件的材料厚度为1mm,以下所有的计算以中线为准。
i.确定零件修边余量
零件的相对高度,由文献[1]表6-2查得修边余量,故修正后拉深件的总高应为。
ii.确定坯料尺寸D
由公式D=d2+4dh-1.72rd-0.56r2计算出D
其中:
d=31mm,h=28.5mm,r=3.5mm
则:
D=68mm
iii.判断是否采用压边圈
零件的相对厚度,由文献[2]表4-11知:
该拉深工艺须可用可不用压边圈,为保险起见,第一次拉深采用压边圈。
iv.确定拉深次数
先判断能否一次拉出
由文献[1]表6-8,,,
由此可知:
故判断不能一次拉深成形。
故可根据公式求得取较大整数:
v.确定各次拉深半成品尺寸
1)调整各次拉深系数,使各次拉深后系数均大于文献[1]表6-6、6-7查得的相应极限拉深系数。
调整后,实际选取,。
所以各次拉深的直径确定为:
2)各次半成品的高度计算:
取各次的r凹分别为:
由公式r凹1=0.8D-d1t,r凸=(0.7~1)r凹,
计算得:
r凹1=4.4mm,r凸1=3.08~4.4mm,取r1=4mm,r2=3.5mm
则由公式可计算出各次h:
h1=0.25D2d1-d1+0.43r1d1d1+0.32r1
h2=0.25(D2d2-d2)+0.43r2d2(d2+0.32r2)
将所有已知数据带入可求得:
h1=23.2mm,h2=31.1mm.
vi.拉深件工序尺寸图
根据前面分析计算,可知本零件须两次拉深,各工序尺寸如图3-1所示
图3-1各工序尺寸图
vii.排样计算
零件采用单直排排样方式,查文献[1]表3-10得零件间的搭边值a=0.8mm,零件与条料侧边之间的搭边值a1=1.0mm,若模具采用无侧压装置的导料板结构,则条料上零件的步距S=D+a=68+0.8=68.8mm,由文献[1]式3-26可知条料的宽度应为
B=D+2a1+2∆+b0-∆0=68+2×1+2×0.5+0.5-0.50=71.5-0.050mm
其中,b0=0.5由文献[1]表3-12查得。
故一个步距内的材料利用率为:
=A/BS100=p(D/2)2/BS100
=π(68/2)2/(71.5×68.8)×100%=73.8%
零件的排样图如图3-2所示:
图3-2排样图
2.拉深压力计算与设备的选择
i.首次拉深
模具为落料拉深复合模,动作顺序是先落料后拉深,现分别计算落料力
拉深力和压边力。
F落=KLtτ,t=295mPa,
则F落=1.3*3.14*68*1*295=81884.92N=81.88kN
P卸=K卸F落
式中K卸—卸料系数,查参考文献[1]表3-8知k卸=0.025~0.06,取K卸=0.04,
所以P卸=0.04*81,88=3.28kN
F拉=πd1tσbk1,sb=295mPa,d1=38mm,由文献[1]表6-11查取K1=0.965
则:
F拉=π×38×1×295×0.965=33967.42N=33.97kN
F压=π4D2-d1+2r12P,其中r1=4mm,由文献[1]表6-13查P=2.75mPa
则:
F压=π4682-38+2×42×2.75=5416.89N=5.42kN
F拉+F压=33.97+5.42=39.39kNF公称压力>1.6~1.8P=131~147kN,故F公称压力至少要131~147kN
为方便取件,工作行程s≥2.5h工件=2.5×23=57.5mm。
初选设备J23-25。
ii.二次拉深:
F拉=πd2tσbk2,sb=295mPa,d2=31mm,由文献[1]表6-11查取K2=0.78
则:
F拉=π×31×1×295×0.78=22397.93N=22.40kN
F公称压力>1.6~1.8P=35.84~40.32kN,故F公称压力至少要131~147kN
为方便取件,工作行程s≥2.5h工件=2.5×31=77.5mm。
初选设备JA21-35。
iii.压力中心的计算
图3-3压力中心图
由于是圆形工件,如图3-3所示,所以工件的压力中心应为圆心即O(34,34)
iv.压力设备的选择
1)落料拉深复合模设备的选用
根据以上计算,同时考虑拉深件的高度选取开式可倾压力机J23-25,
其主要技术参数为:
公称压力:
250KN
滑块行程:
65mm滑块行程次数:
105次/min
最大装模高度:
220mm最大闭合高度:
270mm
连杆调节长度:
55mm工作台尺寸:
370´560mm
模柄孔尺寸:
f40´