新入厂职工培训教材文档格式.docx
《新入厂职工培训教材文档格式.docx》由会员分享,可在线阅读,更多相关《新入厂职工培训教材文档格式.docx(98页珍藏版)》请在冰豆网上搜索。
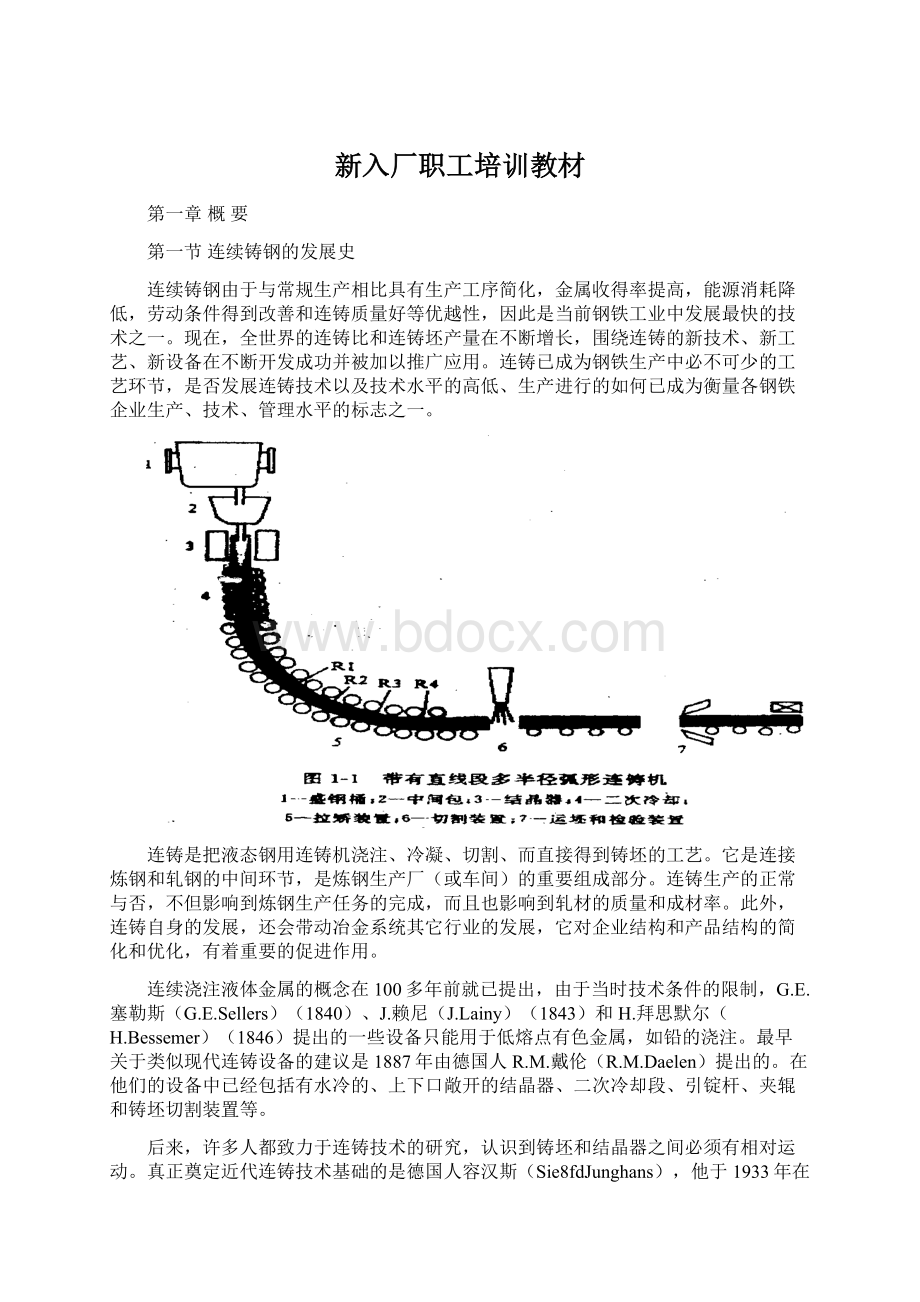
1962
法国SAFE和西德曼内斯曼采用保护渣浇注:
钢包回转台取得专利
德国曼内斯曼(Mannesmann)建成多用途连铸机,可浇4流板坯(最大宽度1500mm),或8流大方坯或8流小方坯或圆坯
1964
德国迪林根(Dillingen)厂建成立宽板坯弧型连铸机德国曼内斯曼(Mannesmann)建成2100mm宽的多点矫直弧型板坯连铸机。
第一台具有扇形段结构的超低头板坯连铸机(铸机总高4m)
曼内斯曼-德马克
1966
德国曼内斯曼(Mannesmann)板坯连铸机内采用多辊驱动的矫直机
1967
德国曼内斯曼(Mannesmann)采用快速更换的铸坯导向段(振动台加上扇形段0段)
1972
日本新日铁采用浇注时宽度可调的分段式板坯结晶器
1976
日本川崎制钢水岛厂建成特大型板坯连铸机,最大宽度2500mm
日本新日大分厂板坯连铸机月产能力超过2.5×
106t
日本川崎制钢水岛厂采用浇注时调宽的无级调节板坯结晶器
曼内斯曼-德马克-日立造船
1981
日本新日铁设计了用于连铸—直接轧制的板坯连铸机
1985
德国曼内斯曼(Mannesmann)采用“干式浇注”生产钢板厂,只在结晶器下方使用0.05l/kg钢的水
日本钢管福山厂连铸机最大拉速2.5m/min,平均拉速大于2.0m/min的高拉速板坯连铸机
第二节连续铸钢的特点
连铸和模铸(钢锭生产)的比较
图1-2是模铸工艺流程和连铸工艺流程的比较。
可以看出二者的根本差别在于模铸是在间断情况下,把一炉钢水浇注成多根钢锭,脱模之后经初轧机开坯得到钢坯的;
而连铸是把一炉(或多炉)钢水连续注入结晶器,得到无限长的铸坯,经切割后直接生产铸坯的。
基于这一根本差别,连铸和模铸比较,就具有许多明显的优越性。
1.提高综合成材率
采用连铸工艺的直接经济效益,首先是提高综合成材率。
通常采用钢锭开坯方式,切头切尾损失一般为10%左右,从钢水到成坯的收得率大约为84~88%;
而连铸的切头切尾少损失为1%~2%,从钢水到成坯的收得率为95%~96%,即采用连铸可节约金属损失10%左右。
金属收得率的提高必然导致综合成材率可达95%以上。
据测算连铸比每提高1.0%,可使综合成材率提高0.8%~1.5%
2.降低能耗
连铸的节能主要体现在因省去开坯工艺的直接节能,以及由于提高成坯率和成材率的间接节能两方面。
据有关资料介绍,连铸时因省略开坯工艺,生产一吨钢坯比模铸节能627~1046kJ,相当于21.4~35.7kg标准煤。
在加上提高综合成材率的节能,按我国目前能耗水平测算,每吨连铸坯综合节能约130kg标准煤。
应该指出,随着浇注钢种、铸坯断面和轧制工艺的不同,连铸节能的具体效益也有所不同。
3.连铸产品的均一性高、质量好
由于模铸锭凝固时间长,元素偏析显著。
特别是钢锭头部和尾部化学成份差别更大。
而连铸坯冷却速度大、树枝晶间距小、偏析程度较轻,尤其是沿铸坯长度方向化学成份均匀。
连铸坯轧材的均一性较模铸锭高。
随着炼钢工艺的发展,和一系列连铸新技术的应用,目前连铸坯产品质量的各项性能指标,大都优于模铸锭轧材产品。
4.易于实现机械化、自动化
在炼钢生产过程中,模铸是一项劳动强度大、劳动环境恶劣的工序。
而连铸由于其自身设备和工艺的特点,则易于实现机械化、自动化。
近年来,随着科学技术的发展,电子计算机已广泛用于连铸生产的控制,使连铸的这一优越性更加显著。
这不但可以使操作者从模铸的繁重体力劳动中解脱出来,而且有利于提高劳动生产率。
除上述一些突出优点外,连铸还有占地面积小、生产周期快、吨坯成本低等优点。
因而当连铸在钢铁工业中成功应用之后,整个钢铁工业发生了巨大的变化。
一方面铸锭车间、均热炉和初轧机已随着连铸技术的发展逐步被淘汰;
另一方面连铸的发展正改变着从炼钢到轧钢的工艺流程,正向炼钢—薄板坯连铸—连轧发展。
第三节连续铸钢的原理
连续铸钢法有很多,现在就一般的方法进行原理性的说明。
构成连铸设备的主要要素是:
一台连铸机主要由钢包运载装置、中间包、中间包车、结晶器(一次冷却)、结晶器振动装置、二次冷却装置、拉坯(矫直)装置(夹紧)、切割装置和铸坯运出装置等部分组成的。
浇钢时把装有钢水的钢包,通过钢包运载装置运送到连铸机上方,经钢包底部的流钢孔把钢水注入到中间包内。
打开中间包塞棒(或滑动水口)后,钢水流入已对在正常位置,用引锭杆头堵塞并能上下振动的结晶器中。
钢液沿结晶器周边冷凝成坯壳。
当结晶器下端出口处坯壳有一定厚度时,带有液芯并和引锭装置连在一起的铸坯在拉坯机驱动下,离开结晶器,在夹辊的支撑下移动。
与此同时,铸坯被二次冷却装置进一步冷却并继续凝固。
为了要以适当的压力保持铸坯和拉出铸坯,采用了装有驱动马达的夹紧辊,铸坯在全部凝固或带有液芯状态下被矫直。
当引锭装置拉出铸坯脱去引锭装置。
随后在水平位置被切割成定尺长度。
置放于运坯装置上运送到规定地点。
上述整个过程是连续进行的。
为了保证铸坯的表面质量和保护结晶器内的铜板,需添加适当的润滑剂,并使结晶器上下振动,起到如同模铸脱模的作用。
思考题
1.连续铸钢的原理?
2.连续铸钢有哪些优越性?
第二章连铸板坯的传热和凝固理论
第一节连铸过程的热量传输
从本质上说,连铸是一个热量传输过程,也是把液体钢转变为固体钢的加工过程。
钢水由液体转变为固体传输的热量包括:
1.过热,由注温冷却到液相线温度放出的热量;
2.潜热,由液相线温度冷却到固相线放出的热量;
3.显热,由固相线温度冷却到某一温度放出的热量。
在连铸机内,钢水热量的传输分别在一次冷却区(结晶器),二次冷却区(喷雾水)和三次冷却区(辐射)进行的。
带液心的铸坯边运行、边放热、边凝固,直到完全凝固为止。
铸坯中的热量向外传输的主要方式:
1.对流,中间包注流进入结晶器,在液相穴内的强制对流运动而传递过热;
2.传导,凝固前沿与坯壳外表面形成的温度梯度,把液相穴内热量传导到表面;
3.对流十辐射,铸坯表面的辐射传热以及铸坯表面与喷雾水滴的热交换,把热量传给外界。
铸坯在三个冷却区以不同的传热方式,把热量从凝固前沿向外界传递使其逐渐凝固。
凝固速度决定于从坯壳传走的热流,而热流决定于坯壳与冷却区的界面状态。
从结晶器→二冷区热传递速率决定了铸坯液相穴深度,而液相穴深度不能超过连铸机的冶金长度,因而拉速受到限制,也就是限制了铸机生产率。
同时传热速率也会影响到铸坯低倍结构(柱状晶与等轴晶比例)、铸坯表面和内部裂纹的形成。
控制了铸坯质量。
因此必须充分认识传热在连铸过程中的重要作用,定量地理解热量在连铸过程中的传递,对能动地控制铸机生产率和铸坯质量有重要的意义。
第二节结晶器传热与凝固
一、结晶器的作用
结晶器是连铸机的关键部件,它的重要作用表现在:
1.在尽可能高的拉速下保证出结晶器时形成足够的坯壳厚度,以抵抗钢水静压力而不拉漏;
2.结晶器周边坯壳厚度能均匀稳定生长;
3.结晶器内的钢水一渣相一坯壳一铜壁之间的相互作用,对铸坯表面质量有决定性影响。
上述第一个作用决定了连铸机的生产率,而2、3的作用决定了铸坯表面质量。
二、结晶器导出热流
水冷结晶器是一个很强的热交换器。
钢水的凝固速度决定于导出的热流,导出热流越大,出结晶器的坯壳就越厚。
1.平均热流密度
测定通过结晶器的冷却水量和进出水温差,可求出平均热流密度:
Q=WC(θ2一θ1)
式中Q—结晶器导出热量;
W—冷却水流量;
C—水的比热;
θ2—结晶器出水温度;
θ1—结晶器进水温度;
φ=Q/S
式中φ—结晶器平均热流密度;
Q—结晶器导出热量;
S—结晶器有效传热面积。
对190×
(780~860)mm的板坯,结
晶器长度700mm,测得结晶器平均热流
密度与拉速关系如图2一1。
由图可知:
1)热流密度主要决定于钢水在结
晶器内的停留时间。
拉速增加,停留时
间减少,热流增加。
这是因为凝固坯壳
较薄;
坯壳温度高,钢水静压力使坯壳与铜壁均匀接触,有利于传热;
拉速一定时,热流密度决定于保护渣的粘度。
粘度低,渣膜薄,热流密度大。
2.瞬时热流密度
了解沿结晶器高度热流密度的变化,对于观察结晶器局部散热状况和坯壳生长的均匀性是非常重要的。
为此,在板坯结晶器内外弧宽面的中心,1/4和角部处,沿铜板高度每隔100mm,靠近钢水面和冷却水面分别插上热电偶,记录拉坯过程的温度变化,以计算沿高度热流密度的变化(图2-2)。
由图可知,使用同一保护渣条件下,随结晶器高度增加,热流密度下降。
在钢水弯月面附近,热流密度为220~230W/cm2;
在出结晶器处为85W/Cm2。
拉速为1m/min的热流密度比1.5m/min要低20W/cm2。
三.结晶器传热阻力
由图2-2可知,沿结晶器高度热流是逐渐减少的,这说明导出的热量决定于坯壳与铜板表面的接触状态。
在弯月面区域(150~200mm)、热流密度最大,以后逐渐减少。
这说明坯壳到一定厚度就开始收缩,首先在结晶器角部形成气隙,然后向中心扩展。
但由于钢水静压力作用把坯壳贴向铜板,又使气隙消失,可以说沿结晶器高度是气隙形成和消失的平衡过程;
当坯壳厚度达到能抵抗钢水静压力时,形成稳定的气隙,使结晶器热流密度大大减少。
结晶器内钢水热量传到外界被冷却水带走,经过以下传热式。
1.钢水对坯壳的对流传热
中间罐注流动能使钢水沿结晶器中心下降,沿凝固前沿上升的对流运动。
2.坯壳的传导传热
对板坯坯壳的传热,传热速率决定于垂直于板坯表面的温度梯度。
3.坯壳与铜板间的传热
当坯壳与铜板间产生了气隙,此时坯壳表面向铜板表面的热交换靠辐射和对流传热(或气层导热)。
气隙的产生使坯壳与铜板交界面热阻增大,减少了传热。
热阻的大小决定于:
1)结晶器铜板的表面状态;
2)润滑剂的性质;
3)坯壳与铜板间的气隙大小。
实验室测定坯壳与铜板之间的传热系数为0.22W/(Cm2·
℃),相当于14mm厚钢板的传热。
4.结晶器铜板传热
图2-3表示了带水槽的铜板厚度方向等温线分布示意图,可用等温线来估算铜板厚度上某一点温度。
当铜板厚度为40mm,计算的传热系数为2W/(cm2·
℃)。
铜板厚度从40mm减少20mm,热流仅增加10%,可见铜板对传热影响是很小的。
5.结晶器铜板与冷却水的传热
结晶器铜板与冷却水界面传热可能有3种情况:
1)强制对流冷却良好;
2)沿铜板壁上凝聚有水气泡;
3)水槽内的水有沸腾现象。
后两种情况恶化了结晶器传热,应力求避免,尽量保证水与铜板冷却良好。
根据计算可知,冷却水流速为6m/S时,就可避免水的沸腾。
此时界面热阻很小,传热良好。
从上面结晶器传热分析可知,钢水把热量传给冷却水要经过以下环节,即钢水→坯壳→坯壳与铜壁界面→铜壁→铜壁与冷却水界面,这五个方面的热阻,根据计算所知,气隙热阻大约占了75%~90%之间。
由此可见,气隙热阻对结晶器传热起了决定性作用。
在浇注钢种一定时,改善结晶器传热速率的关键在于控制气隙形成的动力学条件和气隙传热条件。
四、改善结晶器传热
由上述可知,结晶器传热速率主要取决于气隙形成的动力学,而气隙的形成和演变,又取决于坯壳收缩、高温强度、结晶器润滑以及结晶器几何形状等因素。
改善结晶器传热,应了解影响它传热的各种因素。
1.结晶器设计参数对传热的影响。
1)结晶器锥度的影响:
对结晶器热流研究表明,结晶器热传递过程中,气隙热阻最大,占总热阻的70~90%。
结晶器设计为上大下小具有合适的倒锥度,可以减小下部气隙厚度,改善传热。
锥度应按钢种和拉速来选择。
结晶器断面尺寸的减小量应不大于铸坯的线收缩量。
收缩量△L可根掘从弯月面到结晶器处坯壳温度变化△T和坯壳收缩系数β来确定,即
△L=△T·
β
β值:
对于δFe,β=16.5×
106/℃;
对于γFe,β=22.0×
106/℃。
若锥度过大,拉坯阻力大,产生拉裂,拉坯困难。
通常方坯结晶器锥度为0.6-0.9%/m,板坯结晶器锥度按宽面收缩0.8一0.9%来考虑。
若板坯宽度为1m,拉速为0.8m/min,结晶器从上口到下口的凝固收缩为9mm。
板坯在厚度方向,控制上口尺寸为正公差,下口尺寸为负公差。
有的厂将结晶器锥度做成抛物线形式,或做成双锥度,这是考虑凝固坯壳增长与凝固时间的平方根成正比的规律。
使锥度适应凝固壳收缩的特点。
2)结晶器长度的影响:
结晶器内钢导出热最给铜壁,上半部占50%以上,当气隙形成后,结晶器下部导出热量减少。
从传热的角度考虑,通常把结晶器长度设计成700mm左右。
近年来,为了提高拉速并减少漏钢,通常将结晶器增长,大板坯结晶器长度为900mm。
3)结晶器铜壁厚度的影响:
板坯结晶器铜板厚度包括冷却水槽部分的厚度和承受温度梯度的有效厚度两部分。
图2-4表示结晶器铜壁厚度与热流的关系。
从该图可知,若结晶器冷面温度保持100℃,要使结晶器热面温度小于铜的再结晶温度(300℃),当热流为293J/㎝2·
s(70cal/㎝2·
s)时,铜板厚度以50mm为宜。
有的文献指出,铜壁厚度在一定范围内对传热影响不大,热流变化很小,板坯结晶器铜壁厚度由40mm减薄到20mm时,热流仅增加10%。
沿结晶器高度方向,铜壁热面和冷面的温度分布如图2-5所示。
最高热面温度和最
高冷面温度发生在距结晶器钢液面以下附近,该处发生周期性的热波动。
如果水流速较低(小于5m/s)时,有可能导致结晶器液面附近水缝中的水沸腾;
水流速较高时,冷面温度低,不会产生水沸腾。
4)结晶器材质的影响:
正常通水情况下,结晶器内壁的使用温度为200-300℃。
特殊情况时,最高处可达500℃。
要求结晶器材质导热性好,抗热疲劳,强度高,高温下膨胀小,不易变形。
纯铜导热性最好,但弹性极限低,容易产生永久变形。
所以多采用强度高的铜合金,如:
Cu-Cr、Cu-Ag合金等。
这些合金高温下抗磨损能力强,使结晶器壁寿命比纯铜高几倍。
其性能比较见表2-1。
有研究者建议,将铜合金中Ag含量从0.075%提高到0.3%,可改善结晶器的使用性能。
不同合金的硬度和温度的关系见图2-6。
表2-1铜合金性能比较
铜类型
弹性极限
kg/㎝2
断裂强度
延伸率
%
再结晶温度℃
导热系数cal/㎝2·
s
纯铜
7
23
45
200
0.93
Cu-Ag合金
>25
>30
>5
350
0.90
Cu-Cr合金
28-36
40-45
18-25
475
0.85
Cu-Zr-Cr合金
49
52
10
>500
-
5)结晶器内表面形状的影响:
有人曾实验过波浪形表面的结晶器,它可使冷却面积增加8-9%,从而减少气隙,改善传热,但由于加工困难,寿命较低,未能得到推广应用。
目前仍多采用平壁表面。
2.操作因素对结晶器传热的影响
1)冷却水流速和流量的影响:
单位时间内通过结晶器水缝中的水量,对其传热有重要的影响。
冷却水应保证迅速地将钢水凝固所放出的热量带走,使铜壁冷面上没有热的积累。
实验室中试验表明,冷却水与铜壁的界面上,有三种传热状况。
(1)强制对流:
热流与铜壁温度呈线性关系,水流速增加,热流增大。
(2)核沸腾:
铜壁局部区域处于高温状态,靠近铜壁表面过热的水层中,有水生成蒸汽并产生沸腾。
在这种情况下,结晶器与冷却水之间热交换不决定于水流速,而主要决定于钢壁表面的过热和水的压力。
(3)膜态沸腾:
温度超过某一极限值时,靠近铜壁表面的水形成蒸汽膜,热阻增大,热流减小,导致铜壁表面温度升高,造成结晶器损坏。
实际生产中,正常情况是处于第一种状况,应尽力避免后两种情况发生。
结晶器内水沸腾,会造成水和热的脉动,对结晶器寿命和铸坯质量都非常有害。
为了保证结晶器有良好的传热性能,除了在铜壁的材质、厚度及冷却水质等方面给予注意外,水缝中的水的流速最为重要。
一般水流速在6~12m/s范围。
试验表明,水速增加,可明显降低结晶器冷面温度,避免间歇式地水沸腾,消除了热脉动,可减少铸坯菱变和角部裂纹。
但是,水速超过一定范围时,随着水速增加热流增加很少。
据试验,流速从6m/s增加到12m/s,总传热系数仅增加3%,但系统的阻力却增加4倍。
因而水速过大也没有必要。
水缝尺寸大小是以保证冷却水具有所要求的水速为原则。
结晶器水缝厚度一般为4~6mm。
为了保证均匀冷却,水缝应按设计要求,周边对称均匀。
为避免水缝中水产生沸腾,进水与出水温差应控制在5~6℃,不大于10℃。
保持结晶器冷却水2bar(2×
106Pa)的反压是必须的。
结晶器的最大供水量,对于板坯和大方坯,每流为500~60Om3/h,对于小方坯为100~150m3/h,连铸生产过程中,结晶器的供水量一般很少调节变动。
2)冷却水质影响:
结晶器的传热速率达84×
105kJ/m2·
h,这是高压锅炉传热速率的十倍。
这样大的热量通过铜壁传给冷却水,铜壁冷面温度很有可能超过1O0℃,使水沸腾,水垢沉积在铜壁表面形成绝热层,增加热阻,热流下降,导致铜壁温度升高,更加速了水的沸腾。
所以,结晶器必须使用软水,要求其总盐含量不大于400mg/l,硫酸盐不大于150mg/l,氯化物不大于50mg/l,硅酸盐不大于40mg/l,悬浮质点小于50mg/l,质点尺寸不大于0.2mm,碳酸盐硬度不大于1~20dh,PH值为7~8。
3)结晶器润滑的影响:
结晶器润滑可以减小拉坯阻力,并可由于润滑剂充满气隙而改善传热。
通常连铸机采用保护渣,保护渣粉加在结晶器内钢液面上,形成液渣层,结晶器振动时,在弯月面处液渣被带入气隙中,坯壳表面而形成均匀的渣膜,既起润滑作用,又由于填充气隙而改善传热。
渣膜使结晶器上部传热减少15%左右,但使下部的传热增加20~25%,而且整个传热比较均匀,这对于获得均匀并且有足够厚度的坯壳起着重要作用。
保护渣对结晶器热流影响与渣膜厚度有关。
渣膜厚度(也代表保护渣消耗量)是渣粘度和拉速的函数。
当拉速一定时,保护渣膜厚度主要决定于渣粘度。
粘度太高,渣流动性不好,形成厚薄不均连续的渣膜;
粘度太低,渣膜也厚薄不均。
在这两种情况下,测得的热流不稳定。
当粘度值合适(如在1300℃,η=2.2×
10-1Pa·
S)时,热流稳定,说明渣膜厚度稳定。
通常把保护渣的ην2值作为形成
稳定渣膜的最佳润滑条件(ν为
拉速)。
如果ην2值太高或太
低,也就是渣膜不稳定。
坯壳
有部份表面直接与铜壁接触,局
部热流增加,从而导致局部区域
收缩而形成凹陷或厚薄不均,这
对于碳含量小于0.2%的钢更为
明显。
因此,使保护渣具有合适的粘度值(ην2值),是得到均匀渣膜,使结晶器导热稳定,控制结晶器内坯壳均匀生长的重要手段。
4)拉速的影响:
提高拉速使结晶器导出的平均热流增加。
但是单位钢水质量从结晶器导出的热量减少,致使坯壳减薄,因此选择最佳拉速时,应既保证结晶器出口处坯壳厚度;
又能充分发挥铸机的生产能力。
5)浇注温度的影响:
试验表明,在拉速和其他工艺条件一定时,过热度增加10℃,敞开浇注和保护浇注条件下,结晶器的最大热流量仅分别增加7.5%和4%,可见,钢的过热度对平均热流影响极小。
当注温分别为1577℃,1593℃,1622℃时,结晶器对流传热的热流差别不大,出结晶器时,铸坯四边的中部坯壳厚度基本相同,但铸坯角部坯壳厚度随注温增高而减薄,增加了拉漏的危险。
按理论计算,过热度每增加10℃,出结晶器的坯壳厚度约减少3%。
过热钢水的动能,在凝固前沿会形成对流运动,可能冲刷,熔化已凝固的坯壳。
由此可知,高温浇注不但不利于传热,而且对坯壳均匀生长有害。
3.钢水成分的影响。
对结晶器导出热量的研究发现,当钢中碳含量在0.12%左右时,热流最小。
此时结晶器铜壁温度波动较大,约为100℃。
当碳含量大于0.25%时,热流基本不变。
此外,对坯壳研究发现,当含碳量在0.12%左右时,坯壳内外表面均呈波纹状,随着含碳量增加,波纹减小。
通常认为,这是因为含碳量为0.12%时,坯壳有最大的收缩(0.38%),因而形成较大的气隙,而且此时硫、磷的枝晶偏析小,坯壳高温强度高,钢水静压力要将坯壳压向铜壁比较困难,钢水在弯月面下凝固后,形成较大的弯曲和气隙,导致坯壳表面与结晶器壁接触面减小,所以热流最小。
形成坯壳最薄,而且不均匀。
这是此种含碳量的钢容易产生裂纹和拉漏的原因。
从研究影响结晶器传热的因素可知,结晶器是一个复杂的传热系统。
通过研究结晶器导出热流的大小和变化,以及它与坯壳生长厚度的关系,可作为调整结晶器热工状态的