清洁生产技术改造示范项目可行性研究报告Word格式文档下载.docx
《清洁生产技术改造示范项目可行性研究报告Word格式文档下载.docx》由会员分享,可在线阅读,更多相关《清洁生产技术改造示范项目可行性研究报告Word格式文档下载.docx(51页珍藏版)》请在冰豆网上搜索。
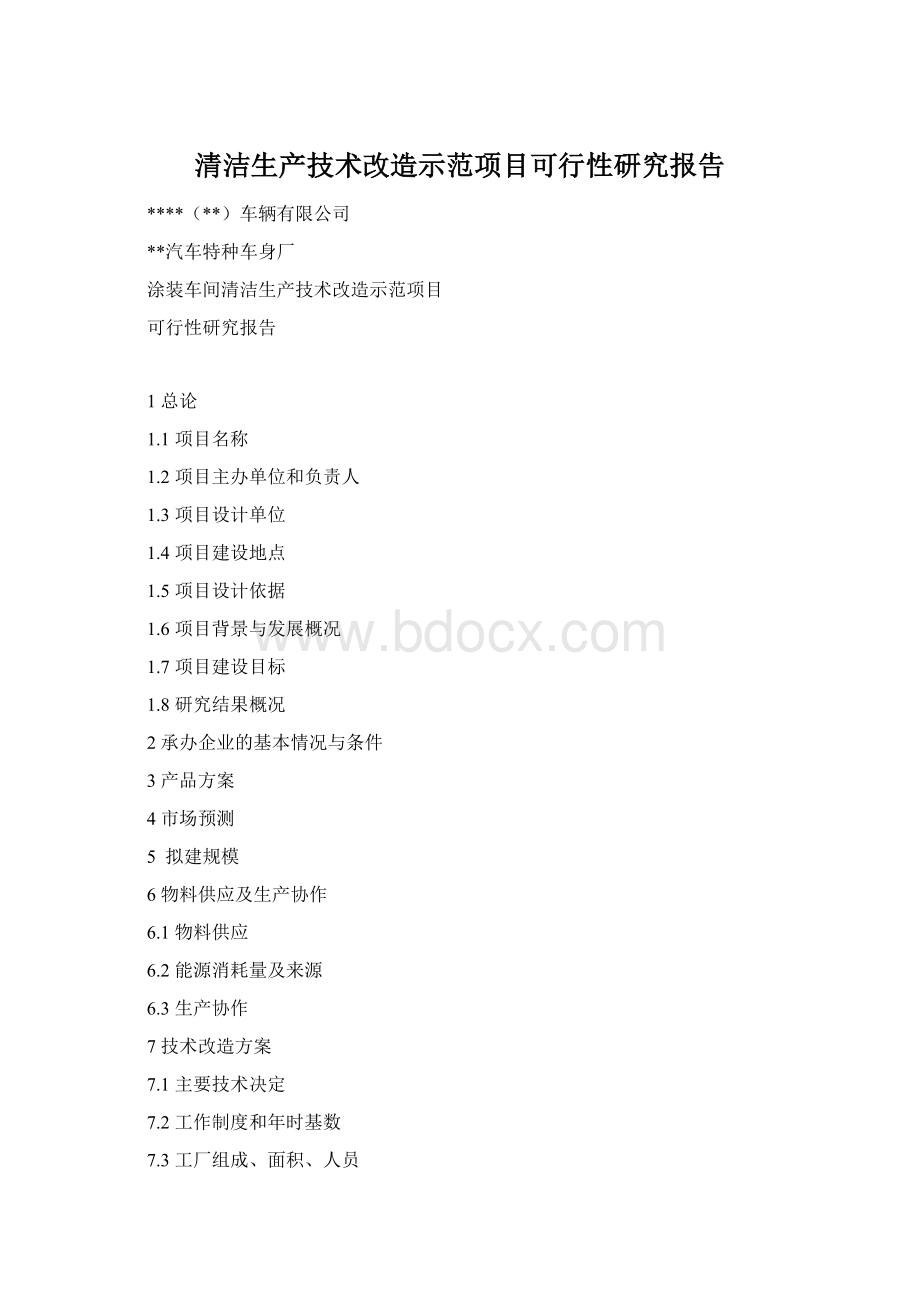
14财务评价及经济分析
15结论和建议
16附件
16.1附件
16.2附表:
设备明细表(共2页)
16.3附图(共4张)
1、总平面布置图 图号:
特身-可-总
2、工艺图 图号:
特身-可-艺
3、建筑平、立面图 图号:
特身-可-建
****(**)车辆有限公司**汽车特种车身厂涂装车间清洁生产技术改造示范项目
主办单位:
****(**)车辆有限公司**汽车特种车身厂
湖北省**市车城路东岳南村88号
1.5.1**实业有限公司文件**实有司发[2004]46号《关于下达2004年第二批投资项目计划的通知》。
1.5.2**(**)**车辆有限公司(注:
原**汽车管型件有限公司)“十五”规划及十年发展纲要中关于产品开发与技术创新总体纲要。
1.5.3**汽车特种车身厂提供的有关产品、财务、宗地图等设计基础资料。
1.5.4**汽车特种车身厂与**设计研究院签订的可行性研究报告工程咨询合同书。
1.6.1项目背景
汽车产业是产业关联度高、规模效益明显、资金和技术密集的重要产业,国家将其定为国民经济支柱产业,国家十五规划纲要中明确要求“发展经济型轿车,提高汽车关键零部件制造水平”。
面对入世后关税降低和非关税壁垒的逐步取消,尤其是服务贸易的开放,将使我国汽车市场国际化,汽车零部件的竞争变得更为激烈,面临着前所未有的挑战。
《中华人民共和国清洁生产促进法》第四条明文规定:
国务院和县级以上地方人民政府,应当将清洁生产纳入国民经济和社会发展计划以及环境保护、资源利用、产业发展、区域开发等规划。
要求将清洁生产纳入国民经济计划
****(**)车辆有限公司**汽车特种车身厂是**汽车公司特种车身定点制造企业,拥有车身的焊接、油漆、内饰装配三大工艺生产线,固定资产2600余万元,具备年产21000台各类车身的能力。
企业自1999年被****(**)车辆有限公司重组以来,取得了良好的发展,特别是2003年以来实施公司“十五”规划项目——高顶双卧车身开发以来,企业呈现强势发展,2003年共创销售收1.3亿元,2004年共创销售收3.45亿元,利润总额也由2003年的130余万元增长到2004年的1150余万元,新产品市场占有率(同类产品)由2003年的20%提高到45%。
由于****(**)车辆有限公司**汽车特种车身厂涂装车间现生产环境达不到清洁生产标准的要求,产品油漆质量受环境的影响,已无法满足**汽车商用车有限公司和社会市场对产品质量方面的要求,严重制约了该厂的发展。
在以上背景下,****(**)车辆有限公司的上级主管部门**实业有限公司专门召开了总经理办公会专门研讨该厂目前的现状,同意该厂对现有涂装车间进行技术改造,并明确要求对改造后的涂装车间在技术水平上要达到清洁生产的国家标准。
1.6.2企业目前现状
**(**)**车辆有限公司特种车身厂是**汽车公司特种车身定点制造企业,拥有生产车身的焊装、油漆、内饰装配三大工艺线和部分冲压件声产能力,固定资产2600余万元,具备年产21000辆各类车身的生产能力。
1999年底被**(**)**车辆有限公司(原**汽车管型件有限公司)重组以来,企业得到了很好的发展,2000年至今共生产各类车身36700余台,共创销售收入56000万元。
为适用汽车市场的发展需要,市场对汽车特种车身新产品开发和生产要求也越来越多样化。
**汽车特种车身厂产品开发和生产的主要阵地—冲压车间、焊装车间、涂装车间、内饰车间均在20世纪90年代初期建成,特别是涂装车间设备陈旧、工艺落后、环境恶劣,达不到清洁生产标准中:
“节能、降耗、减污、增效”的要求,难以保证产品的质量、成本以及交付,严重制约着该厂发展的步伐,主要表现在以下几个方面:
(1)前处理水洗后采取直排方式,每日用水量达1000余吨,水耗大,不利于企业内部挖潜以降低产品成本,且直排对环境污染的影响非常大;
(2)底漆喷涂采取传统的溶剂型涂料空气喷涂,涂料利用率低,(仅为30~60%),机械化,自动化程度不高,工人劳动强度大,特别是溶剂型涂料含有苯类溶剂排放,对环境污染大;
(3)烘干室采用电加热,产生的有机溶剂气体直接排放,环境污染严重,且用电量大,不利于成本控制;
(4)面漆喷漆室为干式喷漆室,喷涂方式为空气喷涂,涂料的利用率仅为30-60%,苯类溶剂排放较多;
(5)现有的车间在涂装过程的打磨工序时没有除尘和通风措施,对打磨产生的灰尘没有控制措施,易使车身涂装产生颗粒等质量缺陷,并对外部环境产生污染;
(6)风机等设备采用的是老式风机,噪声大(最高达92dB),厂房低且无采光带,视线不好,影响车间工人操作,易产生质量事故。
综上所述,对该厂涂装车间进行清洁生产技术改造迫在眉睫。
1.6.3项目建设的必要性
(1)特种车身厂产品以车身为主,尤其是其封闭开发的高顶双卧车身,弥补了**公司无高顶双卧车身的空白,市场需求量大,但受现生产环境的影响,车身外观质量(主要是涂装质量)严重影响产品的销售,特别是该厂目前无电泳底漆设备,产品易产生“流黄水”、油漆表面颗粒严重等质量缺陷,若不及时解决该厂涂装车间恶劣的现生产环境,企业产品市场占有率将有直线下滑的危险,企业将无法生存;
(2)国家对经济的宏观调控使得原材料上涨,该厂若不及时采取新的涂装工艺以消除能耗大、劳动生产率低、污染严重等清洁生产的薄弱环节,其产品成本将直线上升,不再具有价格竞争的优势;
(3)企业内部清洁生产审计表明该厂目前的清洁生产原材料指标和产品指标以及污染物产生等指标均有不同程度的超标,部分指标超标严重。
综上所述,该厂涂装车间清洁生产技术改造项目实施势在必行。
该公司利用本部厂区现有空置场地进行技术改造。
本次技术改造建设形成年产30000辆各类车身以及覆盖件的涂装的生产阵地,并带动特种车身品质的提高。
技术改造主要是对原有车间生产工艺进行调整,新建特种车身涂装车间,以及相应的配套辅助、公用动力设施,设计中并留有今后建设发展的余地。
同时,利用本次技改的契机,在设计和生产中,坚持采用新工艺、新技术,通过生产全过程的排污控制和资源、能源的合理配置,最大限度地把原料转化为产品,把污染消灭在生产过程中,从而起到节能、降耗、减污、增效的目的,实现经济效益和环境效益的协调发展的清洁生产工厂目标。
1.8研究结果概况(见表1-1)
表1-1 主要数据和经济评价表
序号
项目名称
单位
数据
备注
一
主要数据
1
年产量
辆
30000
2
年销售收入
万元
48200.34
3
工作人员
人
75
原有人员调整
4
主要工艺设备
台/条/套
53
5
建筑面积
平方米
4212
6
新增投资总额
785.46
其中:
固定资产
564.65
流动资金
220.81
含贷款利息
含外汇
二
财务、经济评价
投资利润率
%
29.62
投资回收期
年
3.23/3.98
税前/税后
全部投资财务内部收益率
48.79/34.97
资产负债率
74.52/26.46
最高/最低
贷款还款期
财务净现值(ic=16%)
1043.63/637.78
7
利润总额
271.70
正常年(增量)
8
盈亏平衡点
45.18
2.1 基本情况
****(**)车辆有限公司**汽车特种车身厂座落于**市车城南路东岳南村,是**实业有限公司下属企业—****(**)车辆有限公司的下属工厂;
是一家以生产驾驶室为主,改装车二类底盘为辅的综合汽车企业;
是**公司生产特种车身的定点企业。
该厂1992年建厂以来,一直致力于车身生产工艺的技术改进和产品的研发以及人才的培养。
现已发展成为集焊装、油漆和内饰装配的车身生产企业,现有固定资产2600万元,拥有职工200余人,其中工程技术人员20人,高级工程师4人,工程师11人。
2004年销售收入1.3亿,2004年销售收入3.45亿,企业净利润980余万,经过近三年的发展,已具备了一定技术改造实力。
2.2 有利条件
(1)此次技术改造在该厂厂内,地形平整,三通一平工程已完毕,具备施工条件。
(2)产品目前已趋成熟,正在为**商用车有限公司配套,年供货量达21000余台。
(3)凭借**集团内部技术力量,可以封闭开发车身产品,并被**汽车公司授权使用其**商标。
(4)该厂凭借**公司的集团优势,建立了较完善的配套协作网络及售后服务网络。
(5)该厂在工艺参数管理、涂料质量管理、工艺文件管理、设备管理、环境管理等方面已有较好的基础,已有了完整的清洁生产审计制度并建立了环境管理体系。
产品主要有长头、平头、高顶、高顶双卧四大系列,其中长头、平头又有单排、卧铺、双排之分,按车型算有100余个。
车身经过前处理工艺后进入底漆烘干室,再经过中涂、面漆喷涂烘干后进入内饰装配车间装配。
表3-1 产品技术参数表
产品名称
产品结构
主要技术参数及特征
技术来源渠道
**140系列
单排
1700×
2100×
1600
**公司拓展产品
**153系列
卧铺
1910×
2315×
1930
**高顶双卧系列
双层卧铺
2050×
2480
自有研发产品
**高顶系列
2060
4 市场预测
随着国家加大基础建设的投入,特别近两年来西部大开发战略的推进和2002年国家80亿美元进口车配额限制,国内重型载货车需求量大增。
据统计2001年8~10T的重型车占总销量的27.7%,15T以上的重型车占总销量的6.9%,其中重型牵引车销售增幅最大,达41.8%。
2002年重型车仍保持持续增长势头,市场需求量为24.5万辆左右,2003年经过井喷式发展至2004年的已发展为以**、解放为主、中国重汽、重庆红岩、福田欧曼次之的格局,其间重型车产销增长率分别为11.77%和15.66%,随着国家交通部等7部委联合治理超载超限行为并对在用车强制恢复吨位政策的出台,重型车的发展将步入一个良性的稳步发展的局面。
特种车身厂作为**公司车身厂生产能力的补充,拥有**公司商标使用权,自2001年以来,该厂已建立了自己良好的配套关系,年供近4000辆EQ1141G普通平头车身和3000辆EQ1092F长头系列车身,并为**公司定点生产系列双排座车身(年产量达350辆)。
2002年6月以来,由该厂试制的EQ4160W高顶双卧系列车身,经过道路试验表明其质量可靠,其产品可覆盖15~30T所有车型,2003年为**公司总装配厂和重型车厂配套供货6000余台,2004年(截止12月)供货15000台,最高月供货量超过2000辆。
据销售部市场需求预测,2005年需求量在25000辆以上,最高月供货量有望超过3000辆。
5拟建规模
生产纲领:
形成年产30000辆各类车身以及覆盖件涂装的能力
6 物料供应及生产协作
6.1主要原材料、燃料和辅助材料用量
表6-1主要原材料、燃料和辅助材料用量表
名 称
年消耗量
名 称
年需求量
擦洗剂
kg
15600
12
密封胶
22500
脱脂剂
48000
13
抗石击涂料
3000
表调剂
2280
14
各色氨基面漆
66000
磷化液
51000
15
氨基漆固化剂
600
电泳漆
180000
16
氨基稀料
33000
中涂
36000
17
玻璃限位片
块
360000
中涂稀释剂
12000
18
阻尼片
60000
柴油
336000
19
各色氨基金属底漆
9
原子灰
19500
20
罩光清漆
10
3M抛光蜡
90
21
罩光清漆稀释剂
15000
11
粘性纱布
45000
6.2生产协作
水、电、压缩空气由**市市政管网提供,主要原材料由**汽车公司材料供应处提供,辅助材料由特种车身厂自行采购。
按照盘活现有存量资产的原则,充分利用该公司的现有生产阵地、设备、场地、技术力量和人力资源优势等条件进行技术改造。
利用自身的车身设计和制造技术,其产品质量应达到**商用车有限公司产品质量标准要求。
工艺及设备必须与生产大纲及产品质量要求相结合,并考虑今后的发展水平,使技术先进、性能稳妥、可靠、经济合理。
选用工艺设备及动力设备必须是节能、无污染或少污染的设备。
厂房、设备布置必须遵循消防、安全、维修方便,以及环保、劳动安全卫生要求,并按工艺流程布置,减少运输距离。
设计必须作到生产设施与环保设施三同时。
在进行年产30000辆各类车身涂装设计时,工艺、总图、公用动力各专业必须预留今后扩建的建设余地。
必须作到人货流不交叉、不倒运,工位器具化,确保零件不落地,防止磕碰伤。
工作制度:
采用JBJ/T2-2000机械工厂年时基数设计标准,全年工作251天,三班制,每班工作8小时。
年时基数
表7-1 年时基数表
部门名称
工作班制
年时基数(h)
设备
工人
涂装车间
三
5500.5
1700.5
7.3车间组成、面积、人员
表7-2 车间组成、面积、人员表
新增建筑面积
(m2)
工作人员(人)
备注
基本工人
辅助工人
技术人员
管理人员
服务人员
合计
一、生产部门
63
小计
二、办公及辅助部门
公用动力站房
60
合计
4272
77
7.4.1车间任务
承担载货车驾驶室前处理、阴极电泳、涂胶、涂刮腻子、打磨、擦净、中涂、面漆及返修任务。
7.4.2主要设计原则和工艺说明
产品规划要求,车间要具备年产30000万辆驾驶室的能力,提高车身涂装质量,降低废气,废水,粉尘的污染并具备宽体车的通过性,对车间前处理、底漆线、面漆线及废气、废水、粉尘的治理进行改造。
针对产品涂装特点,采用完善的工艺和设备,克服现生产不足,改善薄弱环节,使产品质量有较大的提高,达到国际通行的卡车涂层标准(3C3B)。
采用重点设备重点投入,次要设备次要投入的原则,合理配置涂装设备。
关键的喷漆设备进口,以保证面漆质量。
(1)前处理增加预擦洗,高压水冲洗工序,磷化后的水洗采用电泳前纯水槽的更换水,脱脂后的水洗采用纯水机排放的原水进行清洗,节水量约为240吨/天,前处理采用先进的槽底形式,并配置磷化除渣装置,对磷化渣进行集中定期处理,减少对环境的污染。
车间污水进入厂区污水处理站(详见环保篇)。
(2)将传统的溶剂型涂料空气喷涂底漆方式改为具有国家先进水平的电泳涂装,电泳涂装较之传统溶剂型涂料具有无可比拟的少污染的突出优点。
电泳涂装易实现自动流水线生产,机械化,自动化程度高,大大减轻了劳动强度,提高了劳动生产率。
涂料利用率高,可达95%以上。
涂层均匀,边缘覆盖性高,具有优异的附着力及冲击强度。
电泳涂装基本不含有机溶剂,没有溶剂中毒和发生火灾的危险,不存在漆雾,从根本上改善了劳动条件及对环境污染。
(3)烘干室由电加热改为燃油加热,1公斤柴油燃烧放出的能量相当于11度电加热的能量,升高同样高的温度用燃油加热比用电加热节能20%,烘干室产生的有机溶剂气体通过催化燃烧室燃烧后排放。
其净化效率达到95%。
(4)面漆喷漆室和中涂喷漆室由现在的干式喷漆室改为水漩式,该设备的用水是循环水,半年排放一次。
废漆渣回收后外运处理。
其对漆雾的去除率达到99.8%以上。
喷涂方式由现有的空气喷涂改为静电涂装。
与空气喷涂相比涂料利用率大幅度提高,空气喷涂涂料的利用率仅为30-60%静电喷涂利用率比空气喷涂提高1-2倍。
劳动生产率比空气喷涂提高1-3倍,可获得均匀,平整,光滑,丰满的涂层,达到高装饰的目的,产生漆雾少,显著改善作业环境,有利环保治理及改善劳动条件。
涂料供给方式为人工输调漆方式。
建立调漆间在调漆间人工调漆,通过小车送至喷漆室。
喷漆室内设一套喷涂设备。
此系统采购国外成套设备,适用于多品种、小批量的生产方式。
(5)建立封闭式打磨室和擦净室,采用下部抽风和过滤的方式,使打磨产生的粉尘经过滤装置除去,确保车间洁净度要求及减少对外部污染。
(6)采用洁净设备二层布置,产尘设备一层布置的原则,可充分保证车间洁净度要求,最终确保面漆质量。
(7)车间生产线,动力管道及厂房采用规范新颖的色彩设计,由于生产管理和设备维修。
(8)工艺设备选型时采用低噪声设备,减少噪声对外界环境的影响。
厂房按封闭(留采光带)洁净厂房设计,人门设空气沐浴,可有效提高一次下线合格率。
7.4.3 主要工艺过程
焊装的白件车身-预擦洗-高压水冲洗-预脱脂(喷-浸-喷)-脱脂(喷-浸-喷)-循环水洗(浸)-表调(浸)-磷化(浸-喷)-新鲜水洗(浸)-新鲜纯水洗(浸-喷)-阴极电泳-槽上冲洗(喷)-循环超滤洗(浸)-新鲜超滤水洗(喷)-循环纯水洗(浸)-新鲜纯水洗(喷)--电泳烘干-涂刮腻子-涂密封胶-烘干-打磨-填砂眼-精磨)-擦净-离子化吹风-湿碰湿中涂-贴阻尼片-晾置-中涂烘干-强冷-打磨-擦净-离子化吹风-涂抗石击涂料-湿碰湿面漆-晾置-面漆烘干-强冷-检查点补-合格品去内饰线(不合格品去返修)。
7.4.4 质量保证措施
(1)喷漆室送风经严格过滤,保证喷漆环境的洁净度。
(2)喷漆室与烘干室相接,避免了灰尘粘附在湿膜上。
(3)烘干室送风循环管路上设高温过滤器,减少烘干后的打磨工量。
(4)设有封闭的打磨返修间,减少灰尘外逸,影响车间环境。
7.4.5 节能及能耗
(1)本次设计在前处理工艺上采用了手工擦洗,较大地节省能耗。
(2)烘干室外壁设有保温层,两端设门,减少热量损失,节省了大量能源。
7.4.6 职业安全卫生、环境保护
(1)防火、防爆
面漆喷漆室及调漆间设自动报警及灭火装置。
设备和电气及建筑严格按国家防火防爆规范设计。
建筑严格按国家防火防爆规范设计。
(2)防机械伤害
涂装设备的操作平台及风机平台均设置保护栏杆。
风机旋转部件外均有保护罩。
(3)防尘、防毒、防腐蚀
涂装设备采用了水漩式喷漆室,排风漆雾净化率达99.8%。
喷漆室及烘干室排放的含有机溶剂废气采用催化燃烧处理,本车间绝大部分设备均带有通风装置,并且厂房和调漆间内全室换气。
且喷涂区送空调风以保证空气的温度及洁净度。
(4)防噪声、防振动
车间内噪声和振动的主要来源是风机,为了减弱噪声和振动,风机均设有减振装置。
外设隔音室。
7.4.7 工艺概算
本项目工艺设备新增投资为275万元人民币。
清洁生产的实质就是在生产和建设中,坚持采用新工艺、新技术,通过生产全过程的排污控制和资源、能源的合理配置,最大限度地把原料转化为产品,把污染消灭在生产过程中,从而起到节能、降耗、减污、增效的目的,实现经济效益和环境效益的协调发展。
7.5.1 清洁生产的原材料使用
在产品生产中,必然会使用到各种各样的原材料,它们对环境的污染程度各不相同。
在工艺设计时应优先采用清洁的原材料,以减少生产过程中污染物的产生,从源头上确保清洁生产。
比如:
底漆采用无铅型阴极电泳底漆,减少了对环境的污染。
对于一些污染较大而现阶段尚无其它成熟代用产品的原材料,尽量设法提高其利用率,减少其用量,以减少其污染程度。
在生产过程中,时刻注意材料技术的发展,及时使用环保的替代产品。
7.5.2 清洁生产的能源使用
在汽车涂装过程中,能源使用量比较多,一方面要保证采用较清洁的能源,另一方面要考虑节约能源降低成本。
需要在工艺设计中综合考虑。
7.5.2.1 在本项目中,主要使用能源为电能和燃油(柴油)。
前处理各种泵、电机、喷漆室、打磨室采用电能。
烘干加热炉的加热采用燃用柴油,排放的污染物量很少。
前处理中槽液的加热采用市政蒸汽加热。
7.5.2.2 根据国家相关的节能规定,本项目中工艺设计经过多方论证和比较,认为上述的工艺方案能满足节能要求。
因此,本工程中能源的使用上符合有关清洁生产和节能的要求。
7.5.2生产工艺先进:
本工程是在引进国内同行业车身先进生产技术、引进国外部分设备的基础上,成功地完成了卡车车身的涂装技术改造,其生产工艺和技术具有国际二十世纪90年代先进水平。
7.5.3节能措施:
本项目前处理工艺采用了循环水洗、喷漆室采用水漩式、喷涂方式采用静电喷涂、烘干炉加热方式采用燃油加热。
照明电器采用节能型灯具,降低了电能损耗。
在工艺设计中设置有监测点对水、电、气消耗量进行计量管理。
7.5.4循环、回收利用资源
本项目实施后,将原有工艺的水洗直排改为循环水洗,循环率为95%,减少了新水耗量,节约了水资源,达到了清洁生产的目的。
7.5.5污染控制效果
该项目对工业“三废”污染源采取了有效的治理措施,废气、废水主要污染物均达标排放,排污总量得到了了控制(详环保篇)。
总之,技改工程采取了一系列“清洁生产”的措施。
表一:
清洁生产原材料指标和产品指标
表二:
清洁生产管理指标
表三:
工艺清洁生产和污染物产生指标