年产1000吨丙烯酸乙酯生产设计汇总Word文件下载.docx
《年产1000吨丙烯酸乙酯生产设计汇总Word文件下载.docx》由会员分享,可在线阅读,更多相关《年产1000吨丙烯酸乙酯生产设计汇总Word文件下载.docx(34页珍藏版)》请在冰豆网上搜索。
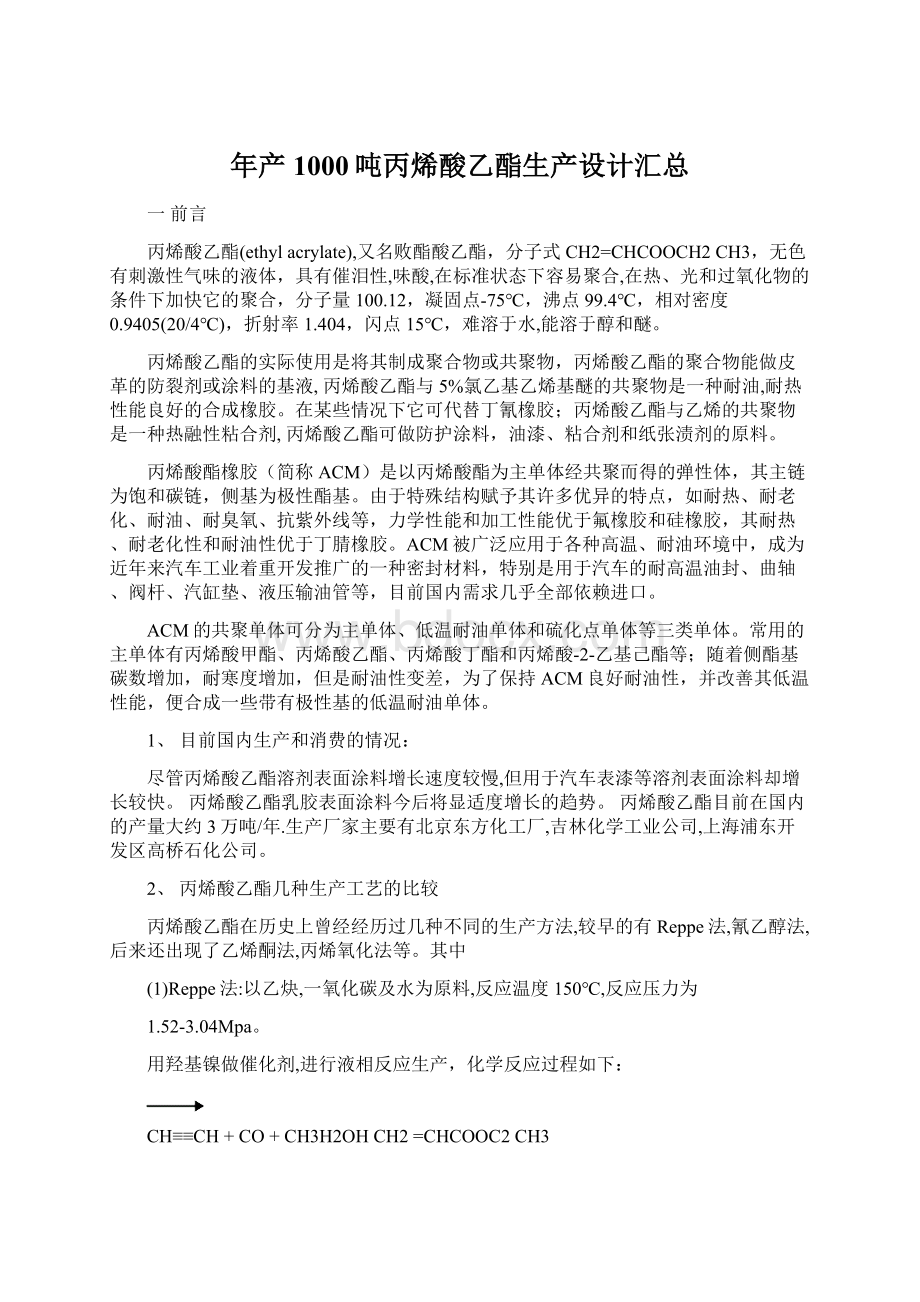
年产1000吨的丙烯酸乙酯的生产车间设计
2产品名称:
丙烯酸乙酯
3原料规格:
丙烯酸95%(wt)乙醇95%(wt)
4产品规格:
纯度99.5%
催化剂
5生产方法:
丙烯酸在甲苯为反应介质以浓硫酸为催化剂的作用下与乙醇发生酯化反应,生成丙烯酸乙酯。
采用间歇操作,反应方程式:
CH2=CHCOOH+CH3CH2OHCH2=COOCH2CH3+H2O
6反应工艺参数:
1)反应温度:
110℃
2)反应压力:
0.1Mpa
3)原料配比:
醇:
酸=1:
1.8(摩尔比)
4)反应转化率:
96%(限量物)选择性:
97%
5)反应时间:
4h
6)催化剂:
浓硫酸
7)年生产时间:
330天,每天三班
8)年生产能力:
折算为100%丙烯酸乙酯1000吨/年
三设计指导思想和设计原则
1指导思想:
通过毕业设计使化工专业的学生初步地掌握工艺设计的一般程序和方法,受到化工设计的训练,使其具有一定的化工设计能力,对今后不论从事生产、基建、还是从事科研或管理工作都有十分重要的意义,对化工过程有更深地了解。
2设计原则:
包括各专业、各方面的设计原则,如工艺路线的选择,设备的选型和材质选用,自控水平等原则。
一般来说,总的设计原则是安全性、经济性、环保性、方便易行等。
四生产方式的选择
化工生产的操作可分为全间歇,半间歇,连续,半连续四种由于本设计仅为1000吨的小型设计,采用间歇操作比较有利
丙烯酸乙酯生产能力根据设计任务规定为年产100%丙烯酸乙酯1000吨/年,取年工作日为330天,每天生产三班,则每班生产能力为1010kg/d。
这样的规模采用间歇操作是比较合理的。
生产控制参数及具体操作:
⑴原料配比
丙烯酸:
甲苯:
乙醇:
催化剂;
阻聚剂=1:
2.1053:
1.8:
0.1053
⑵酯化温度、压力和酯化时间
生产过程酯化温度:
起始温度27℃终止温度110℃
压力:
酯化时间:
⑶酯化的具体操作
将乙醇、丙烯酸、甲苯、阻聚剂、催化剂按比例(见工艺流程方框图)加入酯化反应器中,开始搅拌,用夹套蒸气加热,使温度缓慢匀速上升,酯化4小时,并不断蒸出水及恒沸物,经冷凝器冷凝后进入分离器,上层油层返回酯化反应器,下层水层弃去。
将所得反应物转入贮槽内,将所得反应物冷却,将贮槽内反应液转至中和洗涤器,用浓度为20%的碳酸钠液中和至PH值为7.0,搅拌半小时,静置分层后分取,粗酯再用20~30℃水洗涤。
水洗后在蒸馏器中在减压条件下,蒸馏回收未反应的甲苯、醇,用直接蒸去低沸物,得到粗制酯,粗酯用占总物料0.01%的脱色剂脱色。
过滤得丙烯酸乙酯成品。
整个流程为酯化、中和、水洗、蒸馏、脱色。
流程简图如下:
图4.1,生产流程简图
五初步物料衡算
(一)所用原料及产品的基本物性数据表
表5.1原料及产品的基本物性数据
名称
密度(kg/m3)
分子量
比热容
j/(g·
℃)
熔点℃
沸点℃
乙醇
789
46
109.7925134.74110
-179
78.9
780.3
100
195.9725222.85110
-72
99.4
丙烯酸
1045
72
156.2825165.114110
13.5
141.
甲苯
923.4
92
155.3525186.89110
-95
110.8
(二)初步物料衡算:
根据设计任务,丙烯酸乙酯的年生产能力为1000吨/年(折算100%)。
开工因子=生产装置每年开工时间/年自然时间。
为充分利用设备,开工因子应取得较大,接近1,但是有不可能等于1,因为还要考虑到设备的检修以及开停车等情况。
开工因子一般取为0.9~0.95,全年365天,则年生产300~330天。
因此除去季保养、月保养、修理、放假等总计35天,则年工作日为:
365-35=330天
每天分为三班,每班的操作时间(min)大致分配如下:
表5.2时间表
工序名称
预热
反应
冷却
中和
水洗
蒸馏
脱色过滤
时间(min)
20
240
40
30
90
以此作为物料衡算的基准。
(三)质量守恒定律
质量守恒定律是“进入一个系统的全部物料量必等于离开这个系统的全部物料量,再加上过程中损失量和在系统中积累量。
”依据质量守恒定律,对研究系统作物料衡算,可用下式表示:
∑G进=∑G出+∑G损+∑G积
式中∑G进——输入物料量总和;
∑G出——离开物料量总和;
∑G损——总的损失量;
∑G积——系统中积累量。
(四)进入酯化器的物料衡算
分批操作(间歇操作)的设备,当终点时,物料全部排除则系统内物料积累量为零。
在此情况下,上式可写成:
G进=G出+G损
1进料量
对间歇生产可确定计算基准为公斤/班,则需计算每班产量及原料投料量。
本工艺设计以两个反应釜并联来完成生产任务,以每班生成目的产物为基准计算,反应式如下:
CH2=CHCOOH+CH3CH2OH→CH2COOCH2CH3+H2O
原料规格:
丙烯酸95%乙醇95%
每班生产丙烯酸乙酯:
1010kg
丙烯酸:
甲苯:
乙醇=1:
2.1053:
1.8
每班理论投料(纯)kg
乙醇836.28
丙烯酸727.2
催化剂85.4
阻聚剂31.2
每班实际投料
乙醇880.29
丙烯酸765.47
催化剂85.8
阻聚剂31.84
2酯化过程计算
设转化率为96%选择性为97%以丙烯酸计
酯化物丙烯酸乙酯=1010kg
表5.3进出酯化器的物料衡算表(公斤/班)
输入物料
输出物料
序号
物料
组成%
数量kg
物料名称
1
95
880.29
1010
2
765.47
324.87
3
99
938.59
5
阻聚剂
98
31.84
6
85.8
29.09
7
水
181.8
合计
2701.99
六设备设计和热量计算
(一)设备设计计算
6.1.1反应釜(酯化器)釜体及夹套设计计算:
6.1.1.1确定筒体和封头:
经综合考虑,选圆柱形筒体,椭圆形封头。
确定筒体和封头直径
用两个反应器并联来完成生产,计算其中一个。
首先计算加入酯化器物料的总体积,计算份额最多的主要进料,其他的物料可忽略不计;
再计算反应后体积变化,其中丙烯酸、甲苯和乙醇为主要成分,通过计算它们的体积来决定容积大小。
表6.1进料中三种主要成分的质量,体积
物质
质量(kg)
体积(m3)
363.6
0.348
469.29
867
0.5413
418.14
0.53
VP=0.53+0.5413+0.348=1.4193m3
又因投料后体积略有增大,还有其他进料的估算,故操作容积Vp取2.0m3。
设备容积V与操作容积Vp的关系为Vp=ηV,因反应状态平稳,η取0.8,故设备容积V=Vp/η=2.0/0.8=2.5m3取2.6m3
反应物料液-液相型,查得知H1/D1=1~1.3,因容器体积属中小型,故选取H1/D1=1.2。
D1由下式计算:
D1=
=1.403m
反应釜内径D1的估算值应圆整到公称直径DN系列,根据查表取D1=1400mm。
封头取相同直径,其直径高度h2查表初选h2=50mm。
6.1.1.2确定筒高Ht
当DN=1400mm,h2=0mm时,查得椭圆形封头的容积V封=0.436m,查得1m高的的容积=1.690查得筒体1m高的容积V1=1.327,按式Ht=(V-V封)/V1=[(2.6-0.436)]/V1m=1.82m.取V1=1.7m3,于是H1/D1=1.6/1.3≈1.2
6.1.2确定夹套
6.1.2.1夹套直径
查得:
D2=D1+100=1400+100=1500mm,夹套封头也采用椭圆形并与夹套筒体去相同直径。
6.1.2.2确定夹套高度
按式H2≥(
)/V1即H2≥[(0.8×
2.6-0.436)]/1.327]m=1.3m,取H
=1.3m
6.1.3校核传热面积(能达到的传热面积)
查得封头表面积F封=4.09m
,则实际总传热面积F釜=F筒+F封=4.09
1.3+1.99=7.31m
6.1.4釜体及夹套的强度计算
6.1.4.1选择设备材料确定设备压力
由已知建设并分析工艺要求,选用OCr19Ni9高合金钢板,在100~150℃下的许用力为
=
148MPa
夹套的筒体和封头既受内压的作用。
内压设计压力P=0.1MPa,设计外压的取法是考虑操作过程出现的最大压力差,所以取P=1.5MPa为外设计压。
6.1.4.2夹套的筒体和封头壁厚计算
夹套筒体壁厚Sd
式中P=1.5MPa;
D2=1500mm;
[σ]=115MPa
φ为焊缝系数,由于采用单面焊的对接焊缝,在焊接过程中沿焊缝根部全长有紧贴基本金属的垫板。
100%无损探伤,查得φ=0.9
壁厚附加量C由钢板负偏差(或钢管负偏差)C1和腐蚀裕量C2两部分组成,即
根据钢板规格取δ
=12mm
夹套封头壁厚δ=
11.9
其中:
P,D1,[σ],Φ同上式,由于封头裕量C3-0.5mm
C=C1+C2+C3=0.8+0+0.5=1.3mm
按钢板规格取δ=12mm。
工程上筒体和封头往往取同厚,这样焊得牢固。
按承受的筒体和夹套壁厚计算
按承受0.1MPa的内压设计δ
设计外压为1.5MPa
设简体的计算厚度S0=12mm,由此决定L/D0,D0/S0之值;
D0——筒体外径,D0=DN+2S0=(1400+2×
12)mm=1424mm
L——简体高度,L=H2+h/3=[1400+(325+12)/3]mm=1521mm,则L/D0=1521/1324=1.07,D0/S0=1424/12=118.7。
查得A=0.0012,B=120MPa,则许用外压[P]=BS0/D0=120×
12/1324=1.09MPa<1.5MPa,因此壁厚12mm不满足外压特定要求,需增大壁厚重新计算。
现再设S0=16mm,则D0=1332mm,L=1414mm,L/D0=1.06,D0/S0=83.25,查得A=0.0019,B=130MPa,则许用外压[P]=BS0/D0,1.56MPa>1.5MPa。
可见S0=16mm满足1.5MPa外压稳定要求。
考虑壁厚附加量C=0.8mm,简单壁厚S=S0+C=16+0.8=16.8圆整到钢板规格,S取18mm。
考虑到封头与筒体的焊缝方便取封头与筒体等壁厚δ=18mm
6.1.4.3水压试验校核
确定试验水压Pt,据表得:
釜体水压取Pt=P+0.1=0.1+0.1=0.2MPa
Pt=1.15P[σ]/
=0.129MP
夹套水压取Pt=1.5+0.1=1.6MPa
[σ]——试验温度(20)下的材料许用应力,MPa
——试验温度(20)下的材料许用应力,MPa
两者取较大值,故Pt=0.2MPa。
压力试验时,由于容器承受的压力Pt高于设计压力P,所以必要时需进行强度校核。
液压试验时要求满足的强度条件
釜体和夹套筒体的许用应力:
σt=Pt(D1+δe)/2δeΦ≤0.9σs
釜体和夹套封头的许用应力:
σt=Pt(D1+0.5δe)/2δeΦ≤0.9σs
σt釜筒=0.2×
(1400+18)/(2×
18×
0.9)=8.75MPa
σt夹筒=1.6(1500+12)/(2×
12×
0.9)=112MPa
σt釜封=0.2×
(1300+0.5×
18)/(2×
0.9)=8.70MPa
σt夹封=1.6(1400+12)/(2×
0.9)=104.58MPa
查表得OCr19Ni9不锈钢的屈服限δs=148,则0.9δs=148×
0.9=123.2MPa,由此可知σt釜筒、
σt夹筒、σt釜封、σt夹封都小于0.9δs,故安全。
计算结果如下所示
表6.2筒体,封头壁厚
釜体
夹套
筒体壁厚
18mm
12mm
封头壁厚
6.1.5支座的选择
因反应釜需外加保温,故选B型悬挂式支座。
反应釜质量W=W1+W2+W3+W4
式中W1——釜体和夹套筒体总重
查表知:
DN=1400mm,S=18mm的一米高筒体重q1=591Kg:
DN=1500mm,S=12mm的一米高封头q2=468Kg,
故W1=q1×
H1+q2×
H2)Kg=1731Kg;
W2釜体和夹套的封头总重。
查表得,DN=1400mm。
S=18mm的一米高筒节重q1=321Kg,DN=1500mm,S=12mm的一米高封头重q2=251Kg,
故W2=926Kg
W3——料液重,按水压试验时充满水汁,查附表H-1、H-2知DN=1300mm封头容积Vh=0.436,
一米高筒体容积V1=1.327m3
故W3=Vp
W4——保温层+附件重,入孔重100Kg,其它接管和保温层按150Kg计,
故W4=100+150=250Kg
W=W1+W2+W3+W4=5431.6Kg按两个支座承载计,每个支座承载2711.1Kg,查表选支座,JB1165-81
6.1.6搅拌器选形:
因为料液是粘度较高的流体,搅拌主要是使反应的物料充分混合,在经济的操作范围内,不可能获得高度湍流而只能在层流状态下流动,此时的混合机理主要依赖于充分的总体流动,同时希望在浆叶端部造成高剪切口,借剪切区分割液体,达到预期的宏观混合,而高粘度流体中,搅拌器所提供的机械能会因巨大的粘性阻力而很快被消耗不仅湍流动程序随出口距离急剧下降,还有总体流动的范围也大大的缩小,又底部封头为椭圆型,所以选用低转速、大叶片的筐式搅拌器。
这种搅拌器的转速半径与容器的内径基本相同。
间隙很低,端部切向速度为0.5~1.5m/s,它只在浆叶外缘与容器内壁之间产生较强剪切作用、搅拌的范围大,并可以防止器壁沉积现象,一般搅拌器的直径d与釜体内径D之比为dD为0.9/0.98,转速n一般为1~100r/min,适合高粘度μ<105cp的液体的搅拌,因此一般不用挡板。
由搅拌器标准直径系列,取搅拌器直径d=1140mm。
6.1.7计算搅拌器的转速:
从理论上只要搅拌液体的上升速度等于或大于固体的沉降速度就可以是颗粒悬浮,因此搅拌器的转速在“粒子悬浮临界转速”以上,以保持全部颗粒离开釜底。
粒子悬浮临界转速可采用下面的公式进行计算:
nc=Ψ(dt/d)a·
g0.45(ρs-ρL)0.45μ0.1ds0.2(100R)0.13/d10.85ρL0.55
式中:
ds固体颗粒直径m,ρs固体颗粒密度kg/m3,ρL液体密度kg/m3,μ液体粘度pa·
s,d搅拌直径m,d1搅拌釜内径m,g重力加速度m/s,R固体对液体的重量比。
Ψ和a是与叶轮形式和安装位置有关的系数。
一般Ψ取1~2,a近似取1.4,∵ds=1.75×
104m(80~100,取80目,颗粒直径最大),ρs=1.721×
103kg/m3,ρL=1233.43kg/m3,μ=12.46Mpa·
s,d=1.14m,dt=1.2m,g=9.81m/s2,
R=90.40÷
3263.66=0.0277,Ψ取2,a取1.4,将上面已知数据带入上式得:
nc=0.2261r/s=13.6r/min,转速向上取为n=15r/min=0.25r/s。
则浆叶端部线速度u=nπd=0.25×
3.14×
1.14=0.895m/s.搅拌雷诺数
Rcs=nρd2/μ=0.25×
1242.99×
1.142÷
12.46×
10-3=3.3×
104.查图得:
功率数KN=0.40。
所以搅拌功率N=KNn3ρd5=0.40×
0.253×
1.145=15.00kW。
6.1.8搅拌轴的直径计算:
考虑到温度以及强酸腐蚀,搅拌轴材料选用不锈钢Cr18Ni9Ti,圆钢冷拉,GB905-82,直径一般在8~250mm,查得其[τ]=15~25Mpa.搅拌器由于摩檫损耗功率不大,直接用电动机功率来计算轴径:
N电=6kw,N电为电动机的功率,n=90,[τ]K=15Mpa。
∴搅拌轴直径d≥36.5×
(N电/n[τ]K)1/3=50.62mm.考虑到开链键、钻孔、轴径要适当加大,为了选用标准机械密封件,并和减速机轴径一致,搅拌轴直径取700mm。
6.1.9密封形式选择:
选择机械密封,它的功耗小、泄露低、密封性能可靠,使用寿命长。
本设备采用单端面,小弹簧,平衡形,其标准号为204DgMKT-6010HG21571-95。
6.1.10计算电机功率:
因为采用机械密封,齿轮传动,假定摩檫功率约占搅拌功率的5%,传动机构效率为90%,则电机功率:
N电=NρN/η=14.95×
1.05÷
90%=17.44kW。
6.1.11电动机和减速机选型:
反应釜的电动机大部分与减速度即配用,只有在搅拌转速很高的时候,才会有电动机不经减速而直接驱动搅拌轴。
因此,电动机的选取一般应与减速机的选用配合考虑。
在很多场合中,电动机与减速机疫病配套供应,设计时可根据选定的减速机配套的电动机。
已知搅拌轴转速n=15r/min,电动机使用功率N电=18kW,由此选择电动机,减速器形式:
电动机(三相异步电动机YB型,急隔暴型异步电动机,额定功率6kw,同步转速1500r/min.);
减速机(谐波减速机,额定功率6kw,同步转速1380r/min,立式,功称减速比为90,标准号为XB145-10)。
6.1.12机座与连轴器的选择:
由于反应釜传来的轴向力不大,故采用不带支撑的机座,其标准号为J-A-60。
连轴器功称直径Dg为60mm,夹壳式,其标准号为HG5-213-65。
(二)热量衡算
按能量守恒定律,在无轴功条件下,进入系统的热量与离开热量应该平衡,在实际中对传热设备的热量衡算可由下式表示:
Q1+Q2+Q3=Q4+Q5+Q6
Q1——所处理得物料带入设备总的热量KJ
Q2——加热剂或冷却剂与设备和物料传递的热量(符号规定加热剂加入热量为“+”,冷却剂吸收热量为“-”)KJ
Q3——过程的热效率,(符号规定过程放热为“+”,过程吸热为“-”,注意Q与热焓符号相反,即Q=△H。
如过程放热则△H为“-”,则Q为“+”)KJ;
Q4——反映终了时物料的焓(输出反应器的物料焓)
Q5——设备各部件所消耗的热量KJ
Q6——设备向四周散失的热量,又称热损失KJ
热量衡算的时间基准可与物料衡算相同,即对间歇生产可以每日或每批处理物料基准。
(计算传热面积的热负荷,必须以每小时做基准,而该时间必须是稳定传热时间)热