组合机床的总体设计Word文件下载.docx
《组合机床的总体设计Word文件下载.docx》由会员分享,可在线阅读,更多相关《组合机床的总体设计Word文件下载.docx(13页珍藏版)》请在冰豆网上搜索。
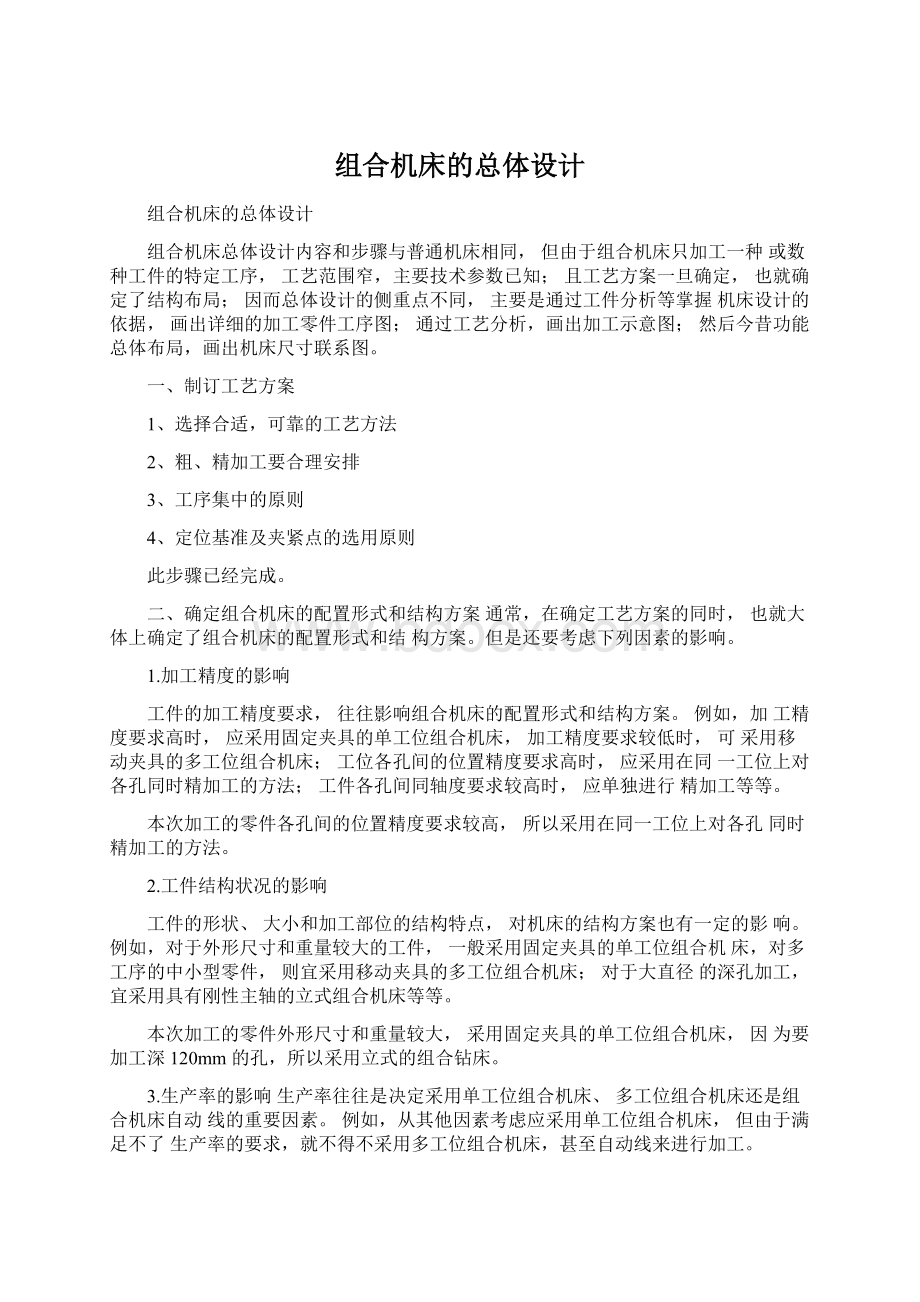
工位各孔间的位置精度要求高时,应采用在同一工位上对各孔同时精加工的方法;
工件各孔间同轴度要求较高时,应单独进行精加工等等。
本次加工的零件各孔间的位置精度要求较高,所以采用在同一工位上对各孔同时精加工的方法。
2.工件结构状况的影响
工件的形状、大小和加工部位的结构特点,对机床的结构方案也有一定的影响。
例如,对于外形尺寸和重量较大的工件,一般采用固定夹具的单工位组合机床,对多工序的中小型零件,则宜采用移动夹具的多工位组合机床;
对于大直径的深孔加工,宜采用具有刚性主轴的立式组合机床等等。
本次加工的零件外形尺寸和重量较大,采用固定夹具的单工位组合机床,因为要加工深120mm的孔,所以采用立式的组合钻床。
3.生产率的影响生产率往往是决定采用单工位组合机床、多工位组合机床还是组合机床自动线的重要因素。
例如,从其他因素考虑应采用单工位组合机床,但由于满足不了生产率的要求,就不得不采用多工位组合机床,甚至自动线来进行加工。
4.现场条件的影响使用组合机床的现场条件对组合机床的结构方案也有一定的影响。
例如,是使用单位的气候炎热,车间温度过高,使用液压传动机床不够稳定,则宜采用机械传动的结构形式;
使用单位刃磨刀具、维修、调整能力以及车间布置的情况,都将影响组合机床的结构方案。
三、“三图一卡”的编制被加工零件工序图是根据选定的工艺方案,表明零件形状、尺寸、硬度、以及在所设计的组合机床上完成的工艺内容和所采用的定位基准、夹压点的图纸。
它是组合机床设计的主要依据,也是制造、验收和调整机床的重要技术条件。
1.在被加工零件工序图上应标注的内容
1)加工零件的形状、主要轮廓尺寸和本机床要加工部位的尺寸、精度、表面粗糙度、行位精度等技术要求,以及对上道工序的技术要求等。
行位精度等技术要求,以及对上道工序的技术要求等。
2)本工序所选定的定位基准、夹紧部位及夹紧方向。
3)加工时如需要中间向导,应表示出工件与中间向导间有关部位结构和尺寸,以便检查工件、夹具、刀具之间是否相互干涉。
4)被加工零件的名称、编号、材料、硬度及被加工部位的加工余量等。
2.绘制被加工零件工序图的一些规定
1)本工序的加工部位用粗实线绘制,其余部位用细实线绘制。
定位基准、夹紧部位、夹紧方向等需用符号表示;
本道工序保证的尺寸、角度等,均在尺寸下用横线标出。
2)加工部位的位置尺寸应由定位基准算起。
但有时也可将工件某一主要孔的位置尺寸从定位基准算起,其余各孔的位置尺寸再从该孔算起。
当定位基准与设计基准不重合时,要进行换算。
位置尺寸的公差不对称时,要换算成对称公差尺寸。
3)注明零件对机床加工提出的某些特殊要求,如对精镗孔机床应注明是否允许留有退刀痕迹。
4)对简单的零件,可直接在零件图上作必要的说明,而不必另行绘制被加工零件工序图。
设计加工零件的14个紧固孔,14个孔的孔径都为18mm,以底面为第一基准面,前侧为第二基准面,右端面为第三基准面,在后侧施以夹紧力,固定零件加工时以孔1的位置为基准,其余各孔再从该孔算起。
换算如下:
孔2:
根据封闭环的上偏差等于所有增环的上偏差之和减去所有减环的下偏差之和;
其下偏差等于所有增环的下偏差之和减去所有减环的上偏差之和。
(二)加工示意图
加工示意图是被加工零件工艺方案在图样上的反映,表示被加工零件在机床上的加工过程,刀具的布置以及工件、夹具、刀具的相对位置关系,机床的工作行程及工作循环等,是刀具、夹具、多轴箱、电气和液压系统设计选择动力部件的主要依据,是整台组合机床布局形式的原始要求,也是调整机床和刀具所必需的重要技术文件。
1.在加工示意图上应标注的内容
1)机床的加工方法,切削用量,工作循环和工作行程。
2)工件、夹具、刀具以及多轴箱之间的相对位置及其联系尺寸。
如工件端至多轴箱端面之间的距离,刀具刀尖至多轴箱端面之间的距离等。
3)主轴的结构类型、尺寸及外伸长度;
刀具类型、数量和结构尺寸;
接杆、浮动卡头、导向装置、攻螺纹靠模装置的结构尺寸;
刀具与导向装置的配合,刀具、接杆、主轴之间的连接方式。
刀具应按加工终了位置绘制。
2.绘制加工示意图之前的有关计算加工示意图绘制之前,应进行刀具、导向装置的选择以及切削用量、转矩、进给力、功率和有关联系尺寸的计算。
1)刀具的选择
选择刀具,应考虑工艺要求与加工尺寸精度、工件材质、表面粗糙度及生产率的要求。
只要条件允许,应尽量选用标准刀具。
为了提高工序集中程度或满足精度要求,可以采用复合刀具。
孔加工刀具的长度应保证加工终了时刀具螺旋槽尾端与导向套之间有30〜50mm勺距离,以便于排出切屑和刀具磨损后有一定的向前调整量。
刀具锥柄插入接杆孔内的长度,在绘制加工示意图时应注意从刀具总长中减去。
2)导向套的选择
组合机床加工孔时,除采用刚性主轴加工方案外,零件上孔的位置精度主要靠刀具的导向装置来保证。
因此,正确选择导向装置的类型,合理确定其尺寸、精度,是设计组合机床的重要内容,也是绘制加工示意图时必须要解决的问题。
导向装置有两大类,即固定式导向和旋转式导向。
在加工孔径不大于40mm或摩擦表面的线速度小于20m/mm时,一般采用固定式导向,刀具或刀杆的导向部分,在导向套内即转动又作轴向移动。
固定导向装置一般由中间套、可换导套和压套螺钉组成。
中间套的作用是在可换导套磨损后,可较为方便的更换,不会破坏钻模体上的孔的精度。
加工孔径较大或线速度大于20m/mm时,一般采用旋转式导向装置。
旋转式导向装置将旋转副和直线移动(导向)副分别设置,按旋转副和直线副的相对位置分为内滚式和外滚式导向两种;
滚动轴承安装在刀杆上的旋转导向装置为内滚式导向,中间导向套只作直线移动,导向长度为(2〜3)d,di为刀杆直径),导向至工件端面的距离为20〜50mm视导向结构而定;
滚动轴承内圈安装在中间导向套上,中间导向套不随主轴一起移动的旋转导向为外滚式导向装置,导向长度为(2.5〜3.5)d1。
旋转式导向装置的极限转速由轴承的极限转速和刀具允许的切削速度决定,导向精度由轴承精度和刀杆、导向套的精度决定。
旋转式导向一般通过滑块联轴器与主轴“浮动”联接。
本次加工的14个孔的孔径都为18mm,所以都采用固定导向装置。
查表4-2选择固定导向装置的尺寸如下图:
(3)初定切削用量
组合机床往往采用多轴、多刀、多面同时加工,且组合机床上的刀具要有足够的使用寿命,以减少频繁换刀。
因此,组合机床切削用量一般比通用机床的单刀加工要低30%以上。
同一多轴箱上的刀具由于采用同一滑台实现进给,所以,各刀具(除丝锥外)
的每分钟进给量应该相等。
因此,应按工作时间最长、负荷最重、刃磨较困难的所谓“限制性刀具”来确定;
对于其它刀具,可以在这基础上进行调整其每转进给量,以满足每分钟进给量相同的要求。
另外,在多轴箱传动系统设计完毕、传动齿轮齿数确定之后,还要反过来调整初定的切削用量。
查《组合机床设计》表2-7,已知HT250的HB=19〜240HB可得:
v=10:
18mm/min选取v=15mm/min
f=0.18:
0.25mm/r选取f=0.20mm/r
(4)确定切削转矩,轴向力和切削功率
确定切削转矩、轴向力和切削功率是为了分别确定主轴及其其它传动件尺寸、选择滑台及设计夹具、选择主电动机提供依据。
切削转矩、轴向力和切削功率可利用计算图或利用下列公式计算
采用高速钻头钻铸铁孔时
F=26Df0.8HB0.6
1.90.80.6
T=10DfHB
Tv
P=
9550二D
式中F——轴向切削力(N);
D钻头直径(mm);
f每转进给量(mm/r);
T切削转矩(N.mm);
P——切削功率(KW);
v切削速度(m/min);
HB材料硬度,〔HB1—般取HB最大值。
根据上列公式,计算出本工序钻孔的轴向力、切削转矩、切削功率如
F表。
孔位
孔数
钻头直径
D/mm
轴向力
F/N
切削转矩
T/(Nmm)
切削功率
P/KW
1〜14
14
钻①18
3461
17946
14X0.5
(5)计算主轴直径
主轴材料一般为40Cr钢。
强度条件下40Cr钢质主轴的直径为
刚度条件计算时主轴直径为
=B4T
式中P——轴直径(mm);
T——轴所承受的转矩(N・mm);
!
.——许用剪应力(MPa);
40Cr钢!
.l-39-51MPa,取45;
B——系数,当材料的剪切弹性模量G=8.1104MPa,刚性主轴
vu0.25m,B=2.316;
非刚性主轴V】=0.5,m,B=1.948;
传动轴1,
B=1.638
计算得出:
强度条件下d-12.67mm;
刚度条件下d—26.8mm。
根据上述条件,查表4-7选取合适的主轴参数:
d=30mm,主轴外伸长度为:
L=100mm,内径为D=36H7mm,内孔长
度为:
l1=91mm
(6)选取刀具接杆
多轴箱各主轴的外伸长度为一定值,而刀具的长度也是一定值。
因此,为保证多轴箱上的各刀具能同时到达加工终了位置,就需要在主轴与刀具之间设置可调环节。
这个可调环节在组合机床上是通过可调整的刀具接杆来解决的。
查表4-8选取可调接杆尺寸如下:
1、d=36mm,13=90mm的接杆用于钻孔深为120mm和50mm的钻头,
标注为:
B36/1/90;
2、d=36mm,l3=60mm的的接杆用于钻孔深为25mm的钻头,标注为:
B36/1/60。
(7)确定加工示意图的联系尺寸
加工示意图中最重要的联系尺寸是工件端面到多轴箱端面之间的距离。
它等于刀具悬伸长度,螺母厚度,主轴外伸长度与接杆伸处长度之和,再减去加工孔深(如加工通孔,还应减去刀具的切出值)。
(8)工件进给长度的确定
工件进给长度应按加工长度最大的孔来确定。
工作进给长度等于刀具的切入值、加工孔深及切出值之和。
(9)绘制加工示意图的注意事项
1)加工示意图的位置,应按加工终了时的状况绘制,且其方向应与机床的布局相吻合。
2)工件的非加工部位用细实线绘制,其余部分一律按机械制图标准绘制。
3)同一多轴箱上,结构,尺寸完全相同的主轴,不管数量多少,允许只绘一根,但应在主轴上标注与工件孔