FMECAWord格式文档下载.docx
《FMECAWord格式文档下载.docx》由会员分享,可在线阅读,更多相关《FMECAWord格式文档下载.docx(28页珍藏版)》请在冰豆网上搜索。
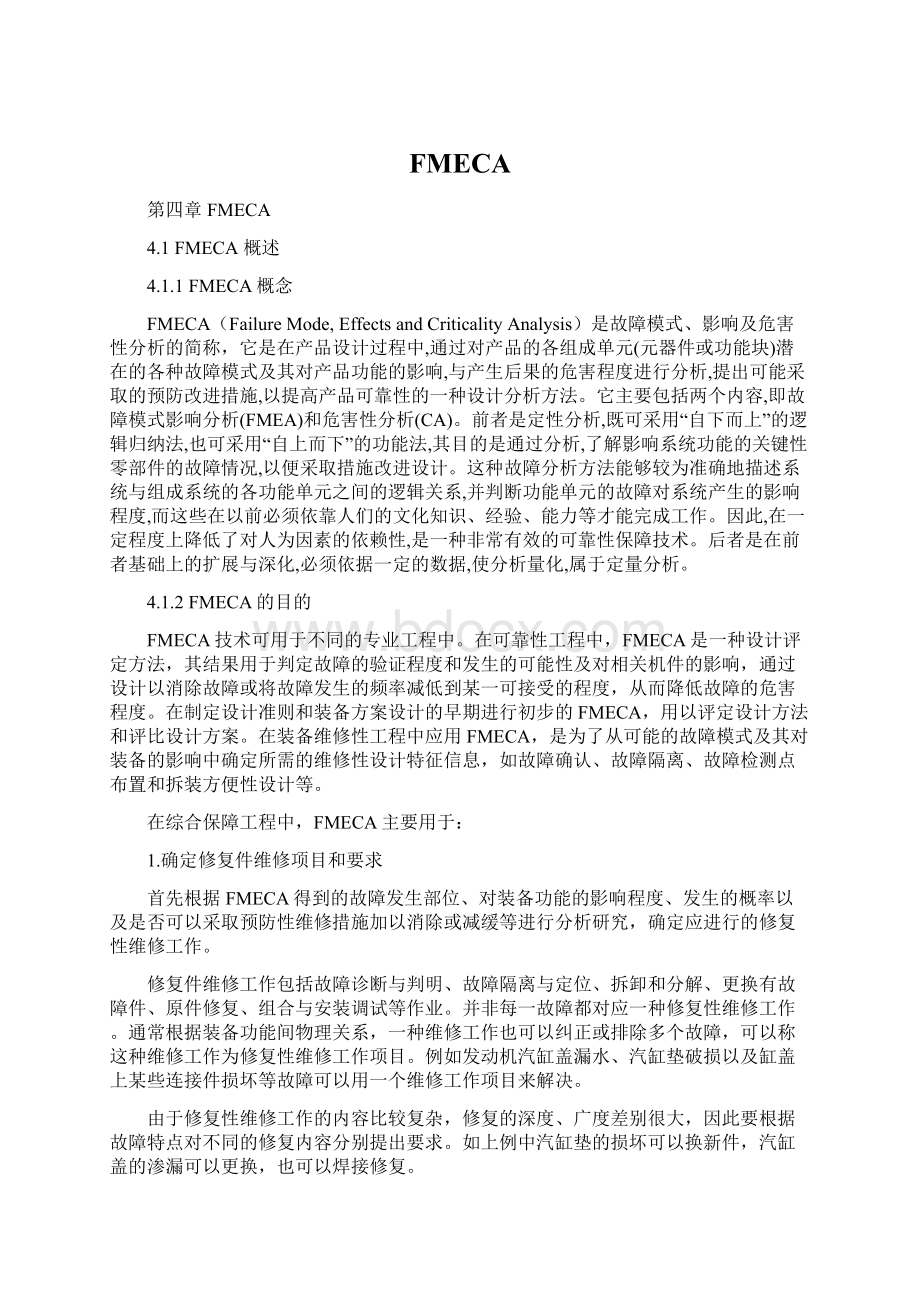
在制定设计准则和装备方案设计的早期进行初步的FMECA,用以评定设计方法和评比设计方案。
在装备维修性工程中应用FMECA,是为了从可能的故障模式及其对装备的影响中确定所需的维修性设计特征信息,如故障确认、故障隔离、故障检测点布置和拆装方便性设计等。
在综合保障工程中,FMECA主要用于:
1.确定修复件维修项目和要求
首先根据FMECA得到的故障发生部位、对装备功能的影响程度、发生的概率以及是否可以采取预防性维修措施加以消除或减缓等进行分析研究,确定应进行的修复性维修工作。
修复件维修工作包括故障诊断与判明、故障隔离与定位、拆卸和分解、更换有故障件、原件修复、组合与安装调试等作业。
并非每一故障都对应一种修复性维修工作。
通常根据装备功能间物理关系,一种维修工作也可以纠正或排除多个故障,可以称这种维修工作为修复性维修工作项目。
例如发动机汽缸盖漏水、汽缸垫破损以及缸盖上某些连接件损坏等故障可以用一个维修工作项目来解决。
由于修复性维修工作的内容比较复杂,修复的深度、广度差别很大,因此要根据故障特点对不同的修复内容分别提出要求。
如上例中汽缸垫的损坏可以换新件,汽缸盖的渗漏可以更换,也可以焊接修复。
2.确定预防性维修工作类型
确定预防性维修的工作类型是以可靠性为中心的维修分析RCMA的主要任务,但在预防性维修逻辑决断中首先是要进行故障后果的评定。
此时FMECA为故障后果评定提供了最基础而重要的信息,特别是研究影响任务和影响安全的后果时,可利用在FMECA中的危害性分析有关的结论再作进一步分析。
3.判定维修时故障查找程序
在FMECA中,要根据故障特征按照航空装备的结构和功能框图的层次对整体到零部件进行分析,以判定故障发生的原因和影响。
分析可以在任何一个层次上开始,分析的方向可以是上行的或下行的,下行以寻找故障来源,上行以判定影响的程度。
因此,通过FMECA找故障原因的过程为维修工程确定故障部位、制定查找程序提供很有价值的参考信息,在研制自动检测设备时尤为重要。
4.用于确定保障资源要求的输入信息
FMECA可确定出修复性维修项目和预防性维修工作类型,据此可以进行使用和维修工作任务分析。
从而确定出保障资源的要求。
4.1.3FMECA在综合保障中的应用
为了确定航空保障中所需要的全部保障资源,在保障性分析中需进行使用与维修工作任务分析,其分析过程可分为如下四个步骤:
1.确定使用与维修工作任务要求;
2.确定各种使用与维修工作任务
3.分析每项使用与维修工作任务,确定全部保障资源;
4.在保障性分析记录中形成工作分析结果文件。
其中,前两步工作需要进行FMECA。
通过FMECA工作,确定新研机型系统有哪些修复性维修工作要求;
利用FMECA结果产生的信息进行RCMA工作,判明故障对其分系统、组件、部件的可靠性关键项目产生的影响程度,其中包括对任务、安全性和经济性等各方面的影响程度,依据对这些数据资料的分析评估,做出预防性维修或改进设计的决断。
保障性分析中的使用维修工作任务分析就是以上述工作为起点,通过得到的使用与维修工作信息,包括全部预防性维修、修复性维修及其他使用与维修工作(如启封、调整、测定故障部位、检查、保养、修理、运输、装载等),进行使用与维修工作任务分析,最终得到各种保障资源要求。
4.1.4FMECA方法
FMECA是设计过程的一个组成部分。
FMECA在方案设计阶段就能进行。
随着设计的进展,FMECA要不断修改,以反映设计的变动。
通常在可靠性预计之前完成FMECA,以便提供基本信息(见图4-1)。
图4-1FMECA与其他工作的关系
FMECA是一种由因到果、自下而上的分析方法,即从元器件的故障开始逐级分析,确定其对系统工作的影响。
它属于单因素的故障分析技术,分析的结果记录在事先准备好的表格内。
在产品寿命周期内的不同阶段,FMECA应用的目的和方法略有不同,详见表4-1。
从表4-1中可以看出,在产品寿命周期的各个阶段虽有不同形式的FMECA,但其根本目的都是从产品策划、设计(功能设计、硬件设计、软件设计)、生产(生产可行性分析、工艺设计、生产设备设计与使用)和产品使用角度发现各种缺陷与薄弱环节,从而提高产品的可靠性水平。
在实际工程中,FMECA一般分为四类:
系统FMECA(SFMECA)、设计FMECA(DFMECA)、过程FMECA(PFMECA)、设备FMECA(EFMECA),分别应用于产品开发中的产品策划、产品设计、工艺设计、产品投入运行阶段。
表4-1产品寿命周期各阶段的FMECA方法
方法
系统
设计FMECA
过程
设备
功能
硬(软)件
阶段
规划阶段
方案阶段
研制阶段
生产阶段
使用阶段
目的
对产品开发、过程策划综合评估,通过系统、子系统、分系统不同层次展开,自上而下逐层分析,更注重整体性、逻辑性。
分析研究系统功能设计的缺陷与薄弱环节,为系统功能设计的改进和方案的权衡提供依据
分析研究系统硬件、软件设计的缺陷和薄弱环节,位系统的硬件、软件设计改进方案权衡提供依据。
分析研究所设计的生产工艺过程的缺陷与薄弱环节及其对产品的影响,为生产工艺的设计改进提供依据。
分析研究生产设备的故障对产品的影响,为生产设备的改进提供依据。
分析研究产品使用过程中实际发生的故障、原因及其影响,为评估、论证、研制、生产各阶段FMECA的有效性和进行产品的改进、改型或新产品的研制提供依据。
1.系统FMECA将研究系统结构化,并分成系统单元,说明各单元间的功能关系;
从己描述的功能中导出每一系统单元的可想象的失效功能(潜在缺陷);
确定不同系统单元失效功能间的逻辑关系,以便能在系统FMECA中分析潜在的缺陷、缺陷后果和缺陷原因。
2.设计FMECA可分为功能FMECA和硬件FMECA。
前者用于方案论证阶段,此时各部件设计未完成,目的是分析研究系统功能设计的缺陷与薄弱环节,为系统功能设计改进和方案权衡提供依据。
后者用于工程研制阶段,此时产品设计图纸及其工程设计资料已确定,目的是分析研究系统硬件、软件设计的缺陷与薄弱环节,为系统硬件、软件设计的改进和方案的权衡提供依据。
3.过程FMECA是负责制造/装配的工程师/小组主要采用的一种分析技术,用以最大限度地保证各种潜在失效模式及其相关的起因机理得到充分的考虑和论述。
4.设备FMECA是在新设备的投入运行时,进行预先EFMECA,主要是分析、考虑由于设备可能造成的产品品质问题及可靠度问题等,预先采取措施消除不良因素;
现有设备、特定的一种设备在运行中出现的设备故障等均可采用EFMECA进行改善,以确保设备的正常运转。
4.1.5FMECA步骤
对系统进行FMECA分析时,一般按照如下步骤,具体流程如图4-2所示。
(1)确定分析的主要范围:
根据系统的重要度、复杂度、分析工作进度、费用的允许度以及技术成熟度等,确定系统FMECA分析的主要范围;
(2)对系统任务进行分析:
表述系统任务的要求和系统完成任务的环境,系统任务分析结果通常使用任务剖面来表述;
(3)对系统功能进行分析:
分析系统完成任务所需的工作时间、工作方式、功能等;
(4)确定系统的故障判据:
分析判断和确定系统产生故障和正常工作的准则;
(5)选择FMECA方法:
根据产品寿命周期的不同阶段,选择相应的FMECA分析手段,编制确定FMECA分析的实施步骤与规范;
(6)实施FMECA分析:
FMECA分析分为FMEA分析和CA分析两个部分,首先进行FMEA分析,根据故障判据、使用信息、相似产品故障信息、试验信息与工程经验确定系统所有可能的故障模式,然后按照系统内外部与工程经验确定故障模式原因以及可能产生的影响,确定每个故障模式的检测方法,并制定其可以使用的补偿措施已经改进方法,确定故障模式的严酷度等级;
再进行CA分析,CA分析是对系统中的每个部件按照故障发生的概率和严重程度进行综合评估的过程;
(7)给出FMECA的分析结论:
根据FMCEA的分析结果,找出系统的薄弱环节及关键项目,并制定和实施各种控制措施和改进方法,以提高系统的质量与可靠性;
(8)给出FMECA分析报告:
在系统设计完成后,可以提供相对应的FMECA分析报告。
图4-2FMECA分析流程图
4.1.6FMECA研究现状
1.FMECA技术在国外发展现状
FMECA最早是由美军提出的。
在20世纪50年代初,美国第一次将FMECA技术用于某战斗机操作系统的设计分析上,并取得较好的效果。
由于FMECA不需什么高深的数学理论,易于掌握,所以有很高的实用价值,受到工程部门的高度重视。
到了60年代中期,FMECA技术正式用于航天工业(Apollo计划)。
1976年,美国国防部颁布FMECA的军用标准。
70年代末,FMECA技术开始进入汽车工业和医疗设备工业。
80年代初,进入微电子工业。
到了1988年,美国联邦航空局发布咨询通报,要求所有航空系统的设计及分析都必须使用FMECA。
1991年,ISO-9000推荐使用FMECA提高产品和过程的设计。
1994年,FMECA又成为ISO-900的认证要求。
目前,FMECA已在工程实践中形成一套完整的分析方法,并根据产品故障产生机理的不同,FMECA与设计、制造、使用、承包商/供应商以及服务等整个产品寿命周期联系起来,又被细分为设计FMECA、过程FMECA、使用FMECA和服务FMECA四类。
尽管FMECA得到非常广泛的应用和认可,但从分析方法上看,FMECA仍然存在缺陷与不足:
系统复杂时,很难明确确定每一故障模式的故障影响;
当系统中元器件过多,分析工作枯燥繁琐,工作量大,难免造成遗漏和错误。
为此,人们不断进行研究来改善FMECA的分析效果。
目前,主要改进方法有:
(1)基于MIL-HDBK-217的FMECA方法。
这种分析方法是目前可靠性分析使用比较广泛的一种分析方法。
是美国国防部在大量统计数据的支撑下,1995年2月颁发MIL-HDBK-217标准。
该标准给出大量电子元器件的基本可靠性数据。
以此为基础,各工业部门及其相关的一些公司研制、开发FMECA软件,如Relex系统和Item系统。
这些分析系统主要采用硬件