乳液聚合丁苯橡胶配方设计Word格式.docx
《乳液聚合丁苯橡胶配方设计Word格式.docx》由会员分享,可在线阅读,更多相关《乳液聚合丁苯橡胶配方设计Word格式.docx(12页珍藏版)》请在冰豆网上搜索。
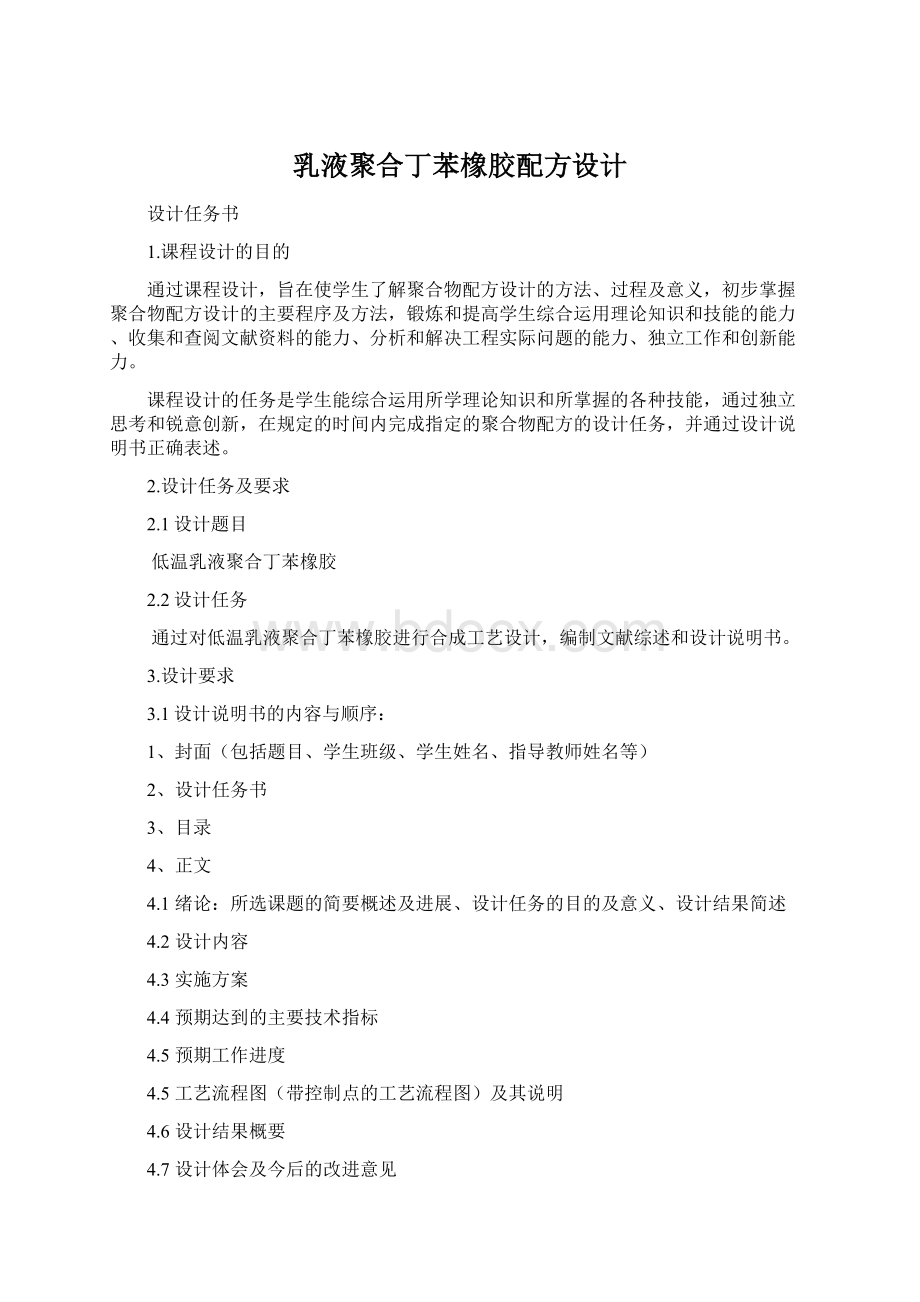
4.5预期工作进度
4.5工艺流程图(带控制点的工艺流程图)及其说明
4.6设计结果概要
4.7设计体会及今后的改进意见
5、参考文献
6、主要符号说明(必须注明意义和单位)
说明书必须书写工整、图文清晰。
说明书中所有公式必须写明编号。
3.2工艺流程图设计图纸的要求:
要求画“生产装置工艺流程图”一张,图纸大小为A2。
本图应表示出装置、单元设备、辅助设备和机器、管道、物料流向。
以线条和箭头表示物料流向,并以指引线表示物料的流量、温度和组成等。
辅助物料的管线以较细的线条表示。
工艺物料管道用粗实线,辅助物料管道用中粗线,其他用细实线。
横向管道标注在管道上方,竖向管道标注在管道右侧。
辅助物料(如冷却水、加热蒸汽等)的管线以较细的线条表示。
图表和表格中的所有文字写成长仿宋体。
设备以细实线绘制,画出能够显示形状特征的主要轮廓。
设备的高低和楼面高低的相对位置一般也按比例绘制。
设备的位号、名称标注在相应设备图形的上方或下方,或以指引线引出设备编号,在专栏中注明每个设备的位号、名称等。
要求工艺流程图有相应的标题栏,主要包括说明设备名称、图号、比例、设计单位、设计人、审校人等。
本设计标题栏规定如下所示:
图纸要求:
投影正确、布置合理、线型规范、字迹工整。
3.3参考文献的格式:
期刊类:
(序号)作者1,作者2,……作者n,文章名,期刊名(版本),出版年,卷次(期次)。
图书类:
(序号)作者1,作者2,……作者n,书名,版本,出版地:
出版社,出版年。
1.绪论
1.1概述
丁苯橡胶是丁二烯(Butadiene,简称B)和苯乙烯(Styrene,简称S)经共聚制得的一类共聚橡胶。
英文缩写名为SBR(Styrene-Co-ButadieneRubber)。
是一类用途广泛的高弹性材料。
其按聚合方法和产品特性可分为:
乳液丁苯橡胶(E-SBR);
溶液丁苯橡胶(S-SBR)和热塑性丁苯橡胶(SBS)。
目前乳液丁苯橡胶有固体丁苯橡胶和丁苯胶乳,溶液丁苯橡胶和热塑性丁苯橡胶只有固体橡胶。
若依照其最终产品状态可分为:
固体、粉末和胶乳。
乳液聚合是工业上利用自由基型共聚反应生产E-SBR的唯一方法。
在水乳液中乳化剂形成胶束,胶束能增溶溶解单体。
水溶性自由基进入胶束中引发聚合,链的增长始终在乳化剂包围的乳胶粒中进行,这就减小了增长链相互碰撞而终止的几率,即降低了链终止速率;
同时借助于乳胶粒内的自动加速效应,使制备分子量足够高的SBR成为可能。
而且在乳液聚合中还可利用硫醇类调节剂来抑制主链上烯丙基的链转移,减少侧乙烯基与自由基的加成,从而避免支化、凝胶等弊端。
另外硫醇还可以把带电荷的自由基转变为中性自由基:
SO4-·
+RSH
HSO4-+RS·
RS·
易于进入带强负电荷的胶束进行引发。
这样既提高了聚合速度,又抑制了凝胶的形成。
此外,乳液聚合还有聚合速度快,所得聚合物分子量高、散热和控温容易、粘度低、搅拌功率小、分散介质(水)价廉易得等技术经济优点。
1.2发展史
1912年,德国Bayer公司发表了丁二烯乳液聚合制取聚丁二烯橡胶的第一篇专利。
20世纪20年代,该国为改进乳聚丁二烯的性能,选用苯乙烯为单体,制得了乳聚丁苯橡胶,并将其命名为Buua-S。
1937年德国IGFarben建设成世界第一个乳聚丁苯橡胶生产装置并投产。
1943年,德国Buua-S的产量为112kt。
20世纪30年代,美国因获得价格低廉的天然橡胶满足通用制品的要求,故为重视Buua-S橡胶,而是致力于特种橡胶的开发。
直到第二次世界大战爆发,一是作为战略物资的橡胶需求量急增;
二是天然橡胶的来源被切断。
因而通用合成橡胶逐渐受到美国政府的高度重视和扶持。
在美国RubberReserve公司统筹下,迅速开展了乳聚丁苯橡胶的生产。
开始阶段,主要利用德国的Buua-S技术进行生产,以后改进了聚合配方,开发了称为GR-S乳聚丁苯橡胶的新技术。
1942年,美国乳聚丁苯橡胶的生产能力为37kt,1943年增长到182.3kt,到1944年已达673kt。
第二次世界大战结束前,德国和美国都采用热法(50℃)乳液聚合工艺生产丁苯橡胶。
第二次世界大战后,由于氧化还原体系聚合配方的出现,美国首先采用冷法(5℃)乳液聚合工艺,使乳聚丁苯橡胶的性能得到显著改善。
因而大部分用途已逐渐为冷法乳聚丁苯橡胶所取代。
但是由于热法乳聚丁苯橡胶也具有独特的性能和一定的应用领域,所以至今仍有少量生产。
1948年,前苏联在沃龙尼什建立了乳聚丁苯橡胶生产装置,采用热法间歇聚合生产丁苯橡胶,后来又开发了冷法连续聚合的生产技术。
其他国家的乳聚丁苯橡胶则发展较晚,包括西欧国家和日本,都是在20世纪50年代以后才实现工业生产的,而且多数是引进美国的生产技术。
其中日本发展速度很快。
目前,聚合工艺和聚合配方基本定型,单体转化率已从60%提高至70%,甚至更高。
为加速聚合反应,减少冷剂消耗,聚合温度也有所提高。
聚合设备趋向大型化,连续聚合使用30~45m3的聚合釜。
在凝聚和后处理方面,以高分子絮凝剂代替氯化钠,大大减少了氯化钠的消耗量。
聚合工艺自动化水平的提高,改善了产品质量。
充油母炼胶、充炭黑母炼胶、充油充炭黑母炼胶的出现也使乳聚丁苯橡胶品种大大增加。
2.工艺设计
2.1配方
2.1.1配方
典型低温乳液聚合生产丁苯橡胶配方
原料及辅助材料
配方Ⅰ
配方Ⅱ
单体
丁二烯
70
72
苯乙烯
30
28
相对分子质量调节剂
叔十二烷基硫醇
0.20
0.16
介质
水
200
195
乳化剂
歧化松香酸钠
4.5
4.62
烷基芳基磺酸钠
0.15
—
引发剂体系
过氧化物
过氧化氢异丙苯
0.08
0.06~0.12
活化剂
还原剂
硫酸亚铁
0.05
0.01
雕白粉
0.04~0.10
螯合剂
EDTA
0.035
0.01~0.025
缓冲剂
磷酸钠
0.24~0.45
反应条件
聚合温度/
5
转化率,%
60
聚合时间/h
7~12
7~10
2.1.2条件确定
分散介质一般以水为分散介质。
要求必须采用去离子水,以保证乳液的稳定和聚合产物的质量。
用量一般为单体量的60%~300%,水量多少体系的稳定性和传热都有影响,水量少,乳液稳定性差,不利于传热;
尤其在低温下聚合这种影响更大,因此,低温乳液聚合生产丁苯橡胶要求乳液的浓度低一些为好,一般控制单体与水的比值为1∶1.05~1∶1.8(物质的量的比),而高温乳液聚合则为1∶2.0~1∶2.5。
单体纯度丁二烯的纯度>99%。
对于由丁烷、丁烯氧化脱氢制得的丁二烯中丁烯含量≯1.5%,硫化物≯0.01%,羰基化合物≯0.006%;
对于石油裂解得到的丁二烯中炔烃的含量≯0.002%,以防止交联增加丁苯橡胶的门尼粘度。
阻聚剂低于0.001%时对聚合没有明显影响,当高于0.01%时,要用浓度为10%~15%的NaOH溶液于30℃进行洗涤除去。
苯乙烯的纯度>99%,并且不含二乙烯基苯。
聚合温度与聚合采用的引发剂体系有关。
低温乳液聚合生产丁苯橡胶采用氧化-还原引发体系,可以在5℃或更低温度下(-10℃~-18℃)进行,同时,链转移少,产物中低聚物和支链少,反式结构可达70%左右。
低温乳液聚合所得到的丁苯橡胶又称为冷丁苯橡胶。
如果采用K2S2O8为引发剂,反应温度为50℃,反应转化率为72%~75%。
低温下聚合的产物比高温下聚合的产物的性能好。
转化率与聚合时间为了防止高转化下发生的支化、交联反应,一般控制转化率为60%~70%,多控制在60%左右。
未反应的单体回收循环使用。
反应时间控制在7~12h,反应过快会造成传热困难。
2.2聚合原理
2.2.1原理
乳聚丁苯橡胶属于乳液法链式自由基聚合机理。
整个过程分为链引发、链增长、链转移和链终止四个步骤。
2.2.1.1链引发
这是形成单体自由基活性种的反应,首先由氧化还原引发体系在水相中产生初级自由基。
第二步是初级自由基与单体加成,形成单体自由基。
2.2.1.2链增长
在链引发阶段形成的单体自由基,活性很高,如无阻聚物质与之作用,就能进攻第二个单体分子的键,重新杂化结合,形成新的自由基,如此循环下去。
该反应过程放热,链增长速度极快(0.01--ns),其相关的速率方程为:
式中Rp—链增长速率,L/(mol·
s)
[I]—引发剂浓度,mol/l
f—引发剂引发效率,%
kd—引发剂分解速率常数
kp—链增长速率常数
kt—链终止速率常数
2.2.1.3链终止
乳聚丁苯橡胶聚合过程的终止主要是双基结合终止
此时的聚合体系中,除水相外,主要是表面层为乳化剂覆盖的聚合胶乳粒子。
2.2.2助剂的作用
2.2.2.1螯合剂EDTA的作用
为了防止产生的Fe(OH)2沉淀析出,工业上采用乙二胺四乙酸二钠盐(EDTA-二钠盐)作为螯合剂,与Fe2+生成水溶液性螯合物。
EDTA-二钠盐与Fe2+生成的水溶液性螯合物,其离解度小,在碱性条件和酸性条件下都很稳定,可在较长的时间内保持Fe2+的存在,而又不生成Fe(OH)2沉淀。
3.2.2.2雕白粉的使用
由链引发反应可知,Fe2+经氧化后变成Fe3+,Fe3+呈棕色,如果其浓度较高将影响丁苯橡胶的色泽。
为了减少Fe3+的浓度,工业上使用雕白粉(甲醛-亚硫酸氢钠二水合CH2O.NaHSO3.2H2O)作为二级还原剂,使Fe3+还原为Fe2+。
4Fe3++2CH2O.NaHSO3.2H2O→4Fe2++2HCOOH+Na2SO4+H2SO4+8H+
由于消耗了二级还原剂雕白粉,硫酸亚铁的用量显著减少。
2.2.2.3终止剂的相关作用:
甲基二硫代氨基甲酸钠为有效的终止剂,但在单体回收过程中仍有聚合现象发生,为此,添加了多硫化物、亚硝酸钠以及多乙烯多胺。
多硫化物有还原作用,可与残存的过氧化物反应,以消除回收过程中残存的过氧化物的引发作用,亚硝酸钠有防止菜化状的爆聚物生成的作用。
2.3影响因素
在乳液聚合反应中,主要影响因素为乳化剂种类和用量、引发剂种类和浓度、搅拌强度、反应温度等。
这些因素对乳液聚合过程及产品质量都有很大影响。
2.3.1乳化剂的影响
乳化剂种类和浓度对乳胶粒直径Dp及数目Np、聚合物分子量Mn、聚合反应速率Rp和聚合物乳液的稳定性等均有明显影响。
2.3.1.1乳化剂浓度[E]的影响
对于在合理的乳化剂