空分原理Word文档格式.docx
《空分原理Word文档格式.docx》由会员分享,可在线阅读,更多相关《空分原理Word文档格式.docx(52页珍藏版)》请在冰豆网上搜索。
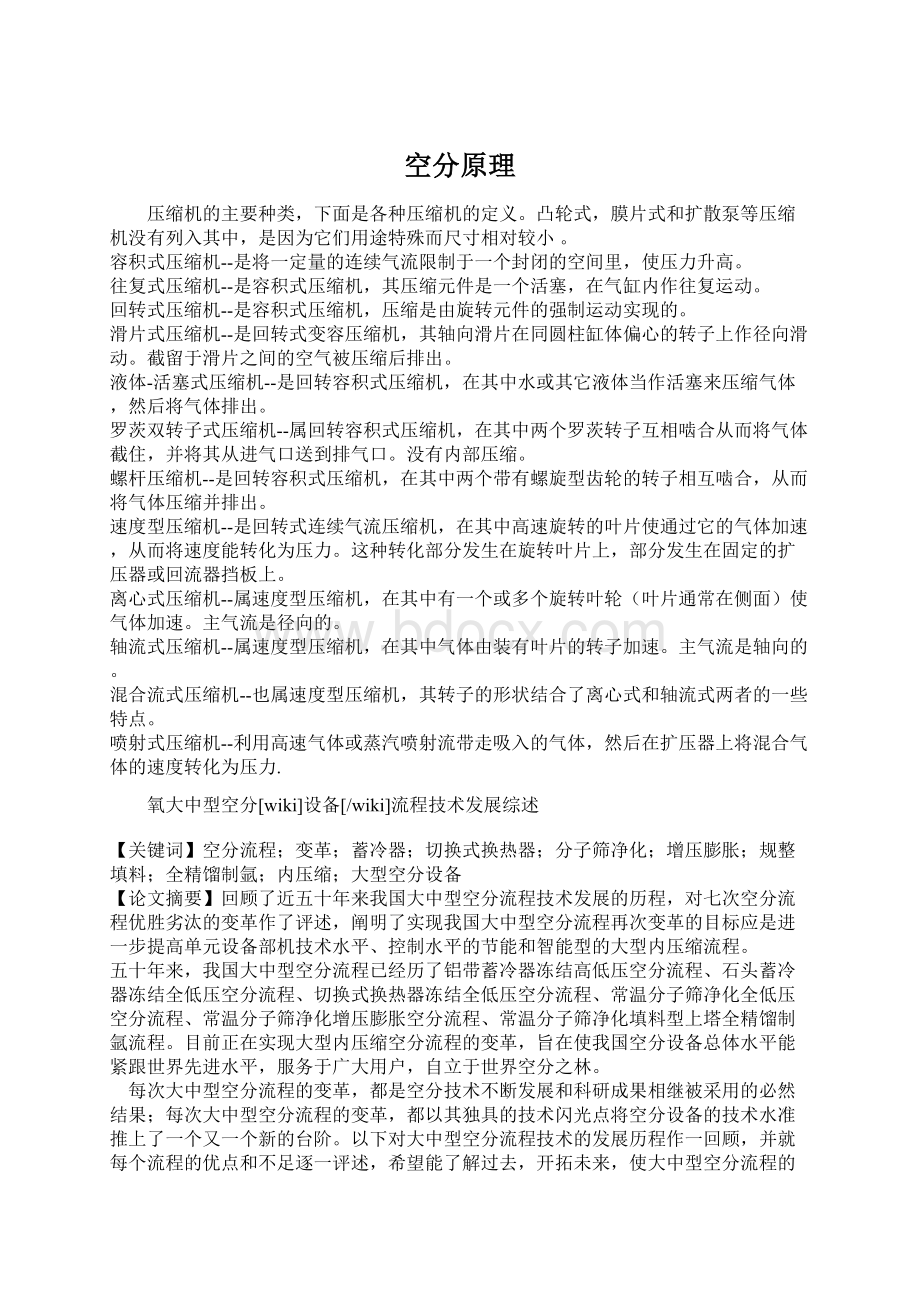
没有内部压缩。
螺杆压缩机--是回转容积式压缩机,在其中两个带有螺旋型齿轮的转子相互啮合,从而将气体压缩并排出。
速度型压缩机--是回转式连续气流压缩机,在其中高速旋转的叶片使通过它的气体加速,从而将速度能转化为压力。
这种转化部分发生在旋转叶片上,部分发生在固定的扩压器或回流器挡板上。
离心式压缩机--属速度型压缩机,在其中有一个或多个旋转叶轮(叶片通常在侧面)使气体加速。
主气流是径向的。
轴流式压缩机--属速度型压缩机,在其中气体由装有叶片的转子加速。
主气流是轴向的。
混合流式压缩机--也属速度型压缩机,其转子的形状结合了离心式和轴流式两者的一些特点。
喷射式压缩机--利用高速气体或蒸汽喷射流带走吸入的气体,然后在扩压器上将混合气体的速度转化为压力.
氧大中型空分[wiki]设备[/wiki]流程技术发展综述
【关键词】空分流程;
变革;
蓄冷器;
切换式换热器;
分子筛净化;
增压膨胀;
规整填料;
全精馏制氩;
内压缩;
大型空分设备
【论文摘要】回顾了近五十年来我国大中型空分流程技术发展的历程,对七次空分流程优胜劣汰的变革作了评述,阐明了实现我国大中型空分流程再次变革的目标应是进一步提高单元设备部机技术水平、控制水平的节能和智能型的大型内压缩流程。
五十年来,我国大中型空分流程已经历了铝带蓄冷器冻结高低压空分流程、石头蓄冷器冻结全低压空分流程、切换式换热器冻结全低压空分流程、常温分子筛净化全低压空分流程、常温分子筛净化增压膨胀空分流程、常温分子筛净化填料型上塔全精馏制氩流程。
目前正在实现大型内压缩空分流程的变革,旨在使我国空分设备总体水平能紧跟世界先进水平,服务于广大用户,自立于世界空分之林。
每次大中型空分流程的变革,都是空分技术不断发展和科研成果相继被采用的必然结果;
每次大中型空分流程的变革,都以其独具的技术闪光点将空分设备的技术水准推上了一个又一个新的台阶。
以下对大中型空分流程技术的发展历程作一回顾,并就每个流程的优点和不足逐一评述,希望能了解过去,开拓未来,使大中型空分流程的发展迎来一个又一个技术的春天,在技术的百花丛中永葆鲜艳。
1铝带蓄冷器冻结高低压空分流程(简称第一代空分)
1956年4月,为了适应冶金工业、化肥工业等方面迫切需要大中型空气分离设备的新形势,杭州通用机器厂(杭氧集团有限公司前身)承担了设计试制高低压流程3350m3/h空分设备的艰巨任务,在参观、剖析了吉林化肥厂从苏联进口的3350m3/h空分设备的基础上,通过近两年的努力,于1958年4月30日试制成功第一套3350m3/h空分设备。
铝带蓄冷器冻结高低压空分流程(见图1)是我国最早的大中型空分设备的主导流程,标志着我国在空气分离设备的制造已实现了从小型向大型的飞跃发展。
典型产品:
3350m3/h(20℃状态)空分设备,这是我国第一代空分产品,流程组织较为复杂,主要由空气过滤压缩、高压空气压缩、C02碱洗、氨预冷、膨胀制冷、换热、精馏等系统组成。
主要性能指标:
氧气:
3120m3/h(标态),99%O2
氮气:
800m3/h(标态),99.8%N2
1.1流程特点
(1)加工空气压力分成低压(0.53~0.57MPa)和高压(16~20MPa)两个等级,这是因空分设备的冷量需要而确定的。
空分设备的冷量来源于两个压力等级下空气的焦汤效应、氮气膨胀制冷和氨预冷系统制冷等三个方面。
(2)采用了氧、氮蓄冷器各两只(分别一只走正流、另一只走返流),内充盘装铝带填料,供换热和清除低压空气中的水分和C02用。
蓄冷器的自清除效果采用返流气量大于正流气量来保证,通常返流与正流气的流量之比为1.03~1.04倍。
(3)采用了一对高压换热器来冷却高压空气,高压空气中的C02是通过碱洗塔碱液的洗涤、水分是通过氨预冷系统的冻结而清除的。
(4)将冷凝蒸发器分成主冷和辅冷两部分,辅助冷凝蒸发器放置位置低于主冷凝蒸发器,利用液氧液位落差使上塔液氧源不断流人辅助冷凝蒸发器,同时被下塔顶部引入的压力氮气气化成氧气后,导人乙炔分离器吸附掉乙炔,作为产品氧气的一部分输出,这就保证了精馏塔的安全运行。
主冷凝蒸发器为列管式(共17749根列管,温差1.8K),辅助冷凝蒸发器为盘管式(温差3.2K)。
A1、A2—乙炔吸附器AF—空气过滤器APl、AP2、AP3—碱液泵APC—空气往复压缩机APC1、APC2—氨预冷器ATC—空气透平压缩机AWC—碱洗塔C1—下塔C2—上塔CS—乙炔分离器E1、E2—主换热器E3—过冷器E4—膨胀前换热器ET—膨胀机K1—主冷凝蒸发器K2—辅助冷凝蒸发器LAFl、LAF2—二氧化碳过滤器NPC—氮预冷器NR1、NB2—氮蓄冷器ORl、OR2—氧蓄冷器RPC—馏分预冷器WC—水冷却器
图1铝带蓄冷器冻结高低压空分流程图
1.2流程缺点
(1)流程组织较复杂。
为了提供空分设备所需的部分冷量及由此而引起的高压空气中水分、C02的清除问题,在冷箱外增设了高压空气压缩机、碱洗塔、氨预冷系统等多套机组;
同时冷箱内设备也较多,给整套空分设备的操作、维护带来诸多不便。
(2)蓄冷器的自清除问题没有得到妥善解决,氧气(或氮气)和空气的传质和传热虽按不同时间间隔错开,但却在同一腔内进行,使产品的纯度受到较大污染,氧气纯度由99.5%02下降到99%02,氮气纯度由99.8%N2下降到98%N2,而后者由于纯度较低,只能放空;
此外蓄冷器热端温差较大(5℃),复热不足损失大。
(3)膨胀机结构为冲动式固定喷嘴的型式,效率较低,只有60%左右。
若用空气作膨胀介质,对膨胀后空气如何处理,没有得到妥善解决,影响了空分流程的组织水平。
(4)氧提取率低,一般只有83.3%。
(5)能耗高,设计值为0.66kWh/m302,而实际运行值高达0.7~0.9kWh/m302。
1.3主要用户
从1958年试制成功后,第一代空分设备共生产27套,主要用户为:
首都钢铁公司、吉林化肥厂、上海吴淞[wiki]化工[/wiki]厂、重庆钢铁公司、鞍山钢铁公司、杭州钢铁厂和南京钢铁厂等,其中出口朝鲜7套。
1969年后停止生产。
目前这些空分设备已完成历史使命,均已报废或停机。
2石头蓄冷器冻结全低压空分流程(简称第二代空分)
1964年,由于北京石景山(首都)钢铁公司的30吨转炉氧气顶吹炼钢试验成功,国务院决定迅速推广这种先进的炼钢方法,使发展全低压流程大中型空分设备显得更为紧迫。
杭氧在承接试制全低压6000m3/h空分设备任务后,参与了首都钢铁公司从日本神户制钢所引进的6000m3/h空分设备的验收工作,并获得了一些技术资料,在消化吸收这些资料的基础上,对部分单元设备进行了改造设计,在1965年11月完成了设计方案。
随着反动式透平膨胀机技术的开发、管式石头蓄冷器的出现及其自清除技术的改进等,1968年杭氧试制完成了第一台全低压流程的6000m3/h空分设备,这种管式石头蓄冷器冻结全低压空分流程(见图2),是我国第二代空分产品。
流程组织大为简化,主要由空气过滤压缩、空气预冷、膨胀制冷、换热、精馏等系统组成。
A1、A2—液空吸附器A3—液氧吸附器A4、A5—二氧化碳吸附器AC—空气冷却塔AF—空气过滤器ASC—空气螺杆压缩机C1—下塔C2—上塔E1—液空过冷器E2—液氮过冷器E3—污氮一空气液化器EFl、EF2—膨胀前空气过滤器ETl、ET2、ET3—膨胀机K1—冷凝蒸发器NRl、NR2—氮蓄冷器ORl、OR2—氧蓄冷器V1、V2、V3、V4—自动阀箱V5、V6、V7、V8—抽气阀箱WC—水冷却器WP—水泵
图2管式蓄冷器冻结全低压空分流程图
6600m3/h(标态),100×
10-602
氧气:
6000m3/h(标态),99.6%02
2.1流程进步点
(1)随着透平膨胀机技术的发展,出现了反动式固定喷嘴透平膨胀机。
空气在固定喷嘴和叶轮中进行两次膨胀,使膨胀机效率有了很大的提高(可达80%),空分设备的制冷手段得到了改善,因此使加工空气由第一代空分流程的两个压力等级转变到只要0.5MPa(G)的一个压力等级成为可能,实现了高低压空分流程向全低压空分流程的变革。
(2)将铝带蓄冷器改为石头蓄冷器,让产品氧气、氮气始终走蛇管内部换热,保证了氧、氮纯度不受污染,使氧的纯度达到99.6%02,氮的纯度达到100×
10-602。
(3)为了清除冻结在石头上的CO2和水分,除了采用正流空气和返流污氮气交替切换的方法外,还采用了中间抽气法,即在蓄冷器中部抽出了相当于加工空气量10%的空气,这就保证了抽口以下正流气量小于返流气量的自清除要求,进一步缩小了蓄冷器冷端温差,使自清除更为彻底。
(4)对膨胀后空气如何合理处理,有了新的技术:
送人上塔中部参与精馏,充分利用了上塔的精馏潜力,提高了氧提取率(可达84%)。
(5)用循环液氧泵OP和液氧吸附器A3组成的强制循环来清除液氧中的乙炔等碳[wiki]氢[/wiki]化合物,确保了空分设备的安全运行,取消了前一流程的辅助冷凝蒸发器。
(6)能耗比第一代空分有了明显的下降,可达到0.55-0.60kWh/m302。
2.2流程缺点
(1)管式石头蓄冷器中的石头填料单位体积所具有的比表面积只有铝带的1/5,而密度却远比铝带大,因而处理同样的空气量,石头蓄冷器比铝带蓄冷器体积要大5倍以上,这就使得石头蓄冷器体积庞大、笨重,所需的安装基础必须深沉坚实,而且占地面积大,工程费用多。
(2)由于采用中间抽气法来保证蓄冷器的不冻结性,因而设置了相应的抽气阀箱、(V5~V8)和C02吸附器,使冷箱内设备及配管复杂化。
(3)膨胀机采用的固定喷嘴,只能依靠调节压力来调节气量,因而膨胀量调节范围较小,对空分变工况生产需要大量冷量时的适应性较差,只能增设备用膨胀机来解决冷量的调节问题,这显得很不经济。
(4)主冷凝蒸发器仍为长列管式,管子数目仍然较多,体积大,制造难。
•
2.3首家用户
1970年10月,第一套全低压流程的6000m3/h空分设备在武汉钢铁公司投入生产,标志着我国气体分离和液化设备工业正式进入了全低压空分流程的时代。
3切换式换热器冻结全低压空分流程(简称第三代空分)
随着高效率板翅式换热器的研制成功和反动式透平膨胀机技术的进一步发展,空分流程水平又大大向前推进了一步,出现了切换式换热器冻结全低压空分流程(图3)。
1970~1978年杭氧采用该流程自行设计了1000、6000、10000m3/h三种规格的空分设备,但质量不稳定。
1979~1991年杭氧在引进了10000m3/h空分设备的设计制造技术的基础上,经过消化吸收及二次开发,先后成功设计制造了1000~10000m3/h空分设