卷烟厂制丝工艺Word格式文档下载.docx
《卷烟厂制丝工艺Word格式文档下载.docx》由会员分享,可在线阅读,更多相关《卷烟厂制丝工艺Word格式文档下载.docx(15页珍藏版)》请在冰豆网上搜索。
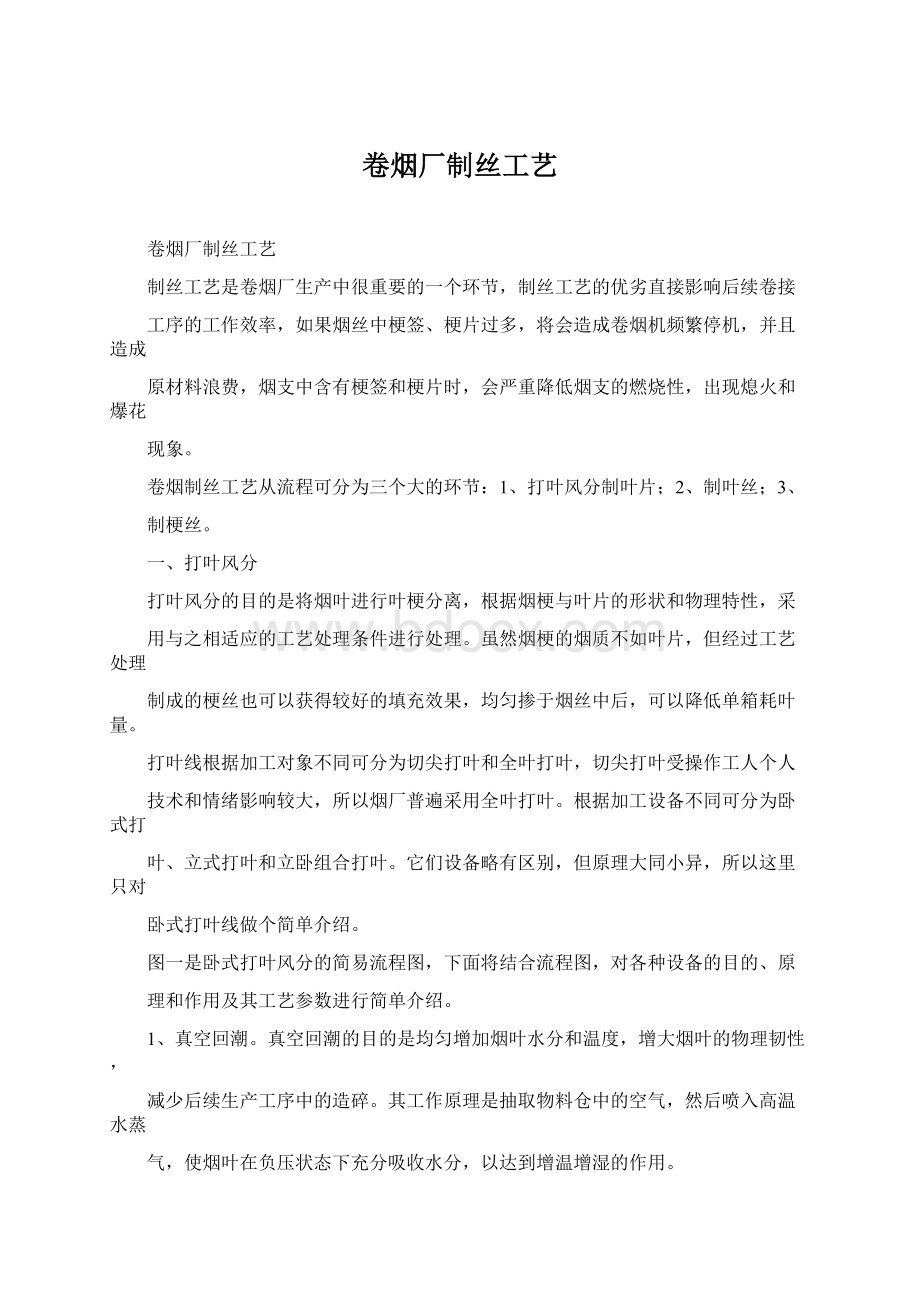
后烟叶存放时间不得超过
30min;
5、潮后烟叶应松散柔软,保持原有光泽,叶片无潮
红、水渍现象。
-1-
烟叶等级
回潮后包芯温度℃
回潮后含水率%
回透率%
上等烟
55~60
15.5~16.5
≥98
中等烟
65~75
16~17
下等烟
65~80
17~18
工艺参数:
见表格
1
表格
真空回潮机解把机仓式喂料机一次润叶
打叶机
定量喂料机二次润叶定量喂料机
叶片
风分器
风分器打叶机
风分器打叶机风分器风分器
带叶烟梗
烟梗
图一
打叶线流程图
-2-
一润
二润
温度℃
50~55
65
50~58
55~68
50~60
55~70
含水率%
16~18
17~20
17~19
19~21
18~20
19~22
散把率%
≥95
2、解把机。
解把机的目的是松散烟把,均匀混合烟叶,以利于打叶风分生产。
解
把率≥80%;
3、仓式喂料机。
仓式喂料机的目的和作用是调节生产线烟叶流量,达到均匀喂料;
4、一润、二润。
提高烟叶的温湿度,进一步松散物料。
1、来料水分
16~18%,解把率≥80%;
2、蒸汽压力、水压、压缩空气
等均应满足工艺条件要求,各仪表数据显示正确;
3、润叶筒内温度达到要求方可投料
生产;
4、润后烟叶无粘结、水渍、潮红、蒸片现象,确保烟叶原有色泽。
2
5、打叶风分的目的是使烟叶叶梗分离,为后续工序对叶片和烟梗采用相应的处理
工艺做准备。
打叶的原理,利用打叶机动刀与定刀和框栏之间的撕扯力,将叶片从烟梗上撕裂
下来。
风分的原理,利用叶片和烟梗的比重不同,在气流中比重较小的叶片被气流带出,
烟梗和带梗叶片因为比重较大而下落,从而达到叶梗分离的目的。
1、来料要求同表格
2
中的“二润”;
2、压缩空气的压力符合设计要求;
3、根据来料的具体情况,合理控制烟叶的进料流量,做好框栏、打棍转速、风速、风
量等设备的技术调整;
4、合理调节打叶线各级打叶风分量,一级打叶风分出片率
65~70%,二级打叶风分出片率
20%左右
-3-
叶片规格
>25.4mm
叶片率,
%
≥58
≥56
≥52
>12.5mm
≥87
≥85
≥81
>6mm
叶片率,%
≥96
>3mm
≥99.5
<3mm
<0.5
1、叶中含梗率≤2.5%;
2、梗中含叶率≤1.5%;
长度大于
20mm
的烟梗率:
上中等烟≥70%,下低次烟
≥60%;
3、叶片中直径大于
2.38mm
的烟梗率≤0.5%;
4、叶片结构见表格
3。
3
二、制叶丝
打叶风分出来的叶片进入制叶丝环节,经过制丝过程中加温加湿和干燥冷却等工
艺处理,使叶丝吃味改善、刺激性减小、去除部分杂气,同时叶丝的松散性、卷曲性
和弹性提高,填充能力变强,使之达到后续生产所需水分含量。
制丝效果的好坏,不
仅直接影响后续卷接包设备的生产率,而且直接影响卷烟的质量。
图二是制叶丝的简易流程图,下面就简单介绍一下,制叶丝工艺中关键工序的作
用及其工艺参数。
加料
贮叶
定量喂料
叶片增温
异物剔除
洪丝干燥筛分
图二
制叶丝工艺流程图
-4-
1、振筛。
打叶风分后的叶片经振筛筛选为四个档位,叶片直径大于
6mm
的叶片
可直接进入加料筒进行加料;
直径在
3~6mm
的叶片可均匀掺入加料叶片中进入后续工
序;
0.8~3mm
的碎末,可直接做为薄片生产原料,也可降等级后掺入低档烟丝中使用,
掺兑方式有两种:
1、直接掺兑;
2、掺入加料后叶片并儲叶
小时,出柜时再筛分出
来,然后掺兑。
2、加料。
加料是制丝的关键工序,对烟片准确均匀的施加料液,适当提高烟片的
含水率和温度,掩盖杂气,减小刺激。
1、烟片流量均匀,流量波动小于
1.0%;
2、料液流量计的计量精度为
0.5%;
3、烟片要充分松散,无粘连结块现象,充分筛除
以下的碎片;
4、保证料
液温度恒定在
45~60℃,以防料液粘稠;
5、蒸汽压力、水压、压缩空气和料液喷射压
力应符合工艺设计要求,蒸汽、水、料液控制准确。
1、加料精度
2、叶片含水率
18.0~21.0%,允差±
1.0;
3、叶片
温度
45~65℃,允差±
3.0
2、贮叶。
贮叶的目的是使叶组进一步混配均匀,平衡叶片的水分和温度,使叶片
充分吸收料液,同时具有调节叶片和制丝工段生产能力的作用。
贮叶的工艺要求:
1、贮存时间最短
小时,最长以不得使叶片品质降低为限;
2、同批次叶片完全进柜后方可出柜,不得边进边出;
3、贮叶高度不大于
1300mm;
4、底带不得有残留,要及时清理,以防霉变。
3、切前叶片增温。
切前叶片增温可使叶片达到切丝机对物料的要求。
1、叶片流量稳定均匀;
2、蒸汽和压缩空气工作压力符合工艺要求;
3、各类控制装置和仪表工作正常,读数准确;
1、叶片温度:
40.0~50.0℃;
2、叶片水分
18~21%;
3、叶片舒展、松散
无结团现象。
4、切叶丝。
将烟片制成纯净度高,整碎度适宜,填充能力强,耐加工性能好,水
分均匀,适宜于卷制要求,一定宽度的叶丝。
-5-
含水率
允差
℃
隧道振槽式
22.8~26.0
±
1.0
>80.0
滚筒式
25.0~40.0
1.5
>60.0
1、来料叶片流量均匀稳定,水分温度适宜;
2、设备稳定无故障。
1、烟丝宽度为
0.7~1.1mm,允差±
0.1mm;
2、切后烟丝松散,无严重
粘连现象;
3、烟丝颜色不得转深,感官质量不得降低。
5、叶丝增温增湿。
增温增湿可以提高叶丝的温度和水分含量,改善和提高叶丝的
感官质量,为洪丝做好准备。
1、叶丝流量均匀稳定;
2、蒸汽、水工作压力稳定,计量准确,流量
计精度
3、设备正常,管、网、喷孔无堵塞;
4、控制设备正常,仪表读数准确。
1、叶丝柔软、松散,无结团、湿团现象;
2、叶丝温湿度要求见表格
4。
4
6、叶丝干燥。
叶丝经过增温加湿后含水率在
22%以上,需经干燥去湿,使其含水
率将至
12~14%,才能适应卷制工艺要求。
除此之外,叶丝在干燥过程中在高温作用下,
叶丝中的化学物质发生反应生成棕色反应产物,可以有效的改善吃味、减轻刺激性、
去除杂气。
同时叶丝物理形状得到提升,提高了叶丝的填充能力和耐加工性。
1、叶丝流量均匀稳定,叶丝含水率稳定,允差<1%;
2、蒸汽、水、
压缩空气工作压力符合工艺设计要求,蒸汽、水流量计计量准确,计量精度
3、设备无故障,各管网无污垢、无堵塞、无跑冒滴漏现象;
4、当各种参数达
到工艺要求时方可进料;
5、定期矫正水分仪和温度仪;
6、及时处理不符合要求的叶
丝。
1、干燥后叶丝松散,手感柔软,感官质量得到提高;
干头干尾每批不
超过
0.6%;
3、各质量指标见表格
5。
%温度
℃填充值
-6-
12~1455.0~75.0≥4.03.3≥80.0≤3.0
三、制梗丝
烟梗是烟叶的重要组成部分,通过叶梗分离,可得到约烟叶总重量
25%左右的烟
梗。
烟梗的烟质不如叶片,表现在香气不足,吸味平淡,刺激性和劲头较小,木质性
杂气较重。
虽然烟梗的品质不如叶片,但通过合理的工艺处理,仍可以获得较好的填
充能力,并且能够均匀的掺入烟丝中进行卷制生产,从而降低卷烟的单箱耗叶量。
图三为梗丝加工的简易流程图,接下来就简单介绍一下梗丝加工工艺中各工序的
工艺要求和工艺参数。
烟
梗
干燥膨胀
定量喂料
贮
梗
增温增湿
切
丝
压
梗丝风选混合掺配
图三
制梗丝工艺流程图
1、筛分、一次回潮及二次回潮。
烟梗不同于叶片,烟梗在含水率
30%左右,温度
在
80℃以上时可塑性最强。
所以打叶后的烟梗要通过回潮来达到适合加工的物理性状。
1、烟梗流量稳定,来料烟梗长度适中,长梗率≥85%,尽可能除去长
度
10mm
以下、直径
1.5mm
以下的碎梗及金属和非金属杂物;
2、对于水洗梗的要求:
水温
30~50℃,水速
2m/s,烟梗落水速度
4.5m/s
以上,虑水时间
6s
以上,至少
3
小
时更换一次循环水;
3、设备完好,各设备参数可满足工艺要求。
两次回潮后烟梗温湿度见表格
5
项目含水率
%温度℃
-7-
第一次回潮
水槽式
26.0~32.0
≤50
≥85.0
螺旋式
烟梗第二次回潮
28.0~36.0
设备类型
填充值
(cm
/g)
碎丝率
梗丝膨胀
32.0~36.0
≥100.0
梗丝干燥
12.5~14.5
≥60.0
≥6.5
≤3.