钣金件数字化制造技术典型应用实例Word文档格式.docx
《钣金件数字化制造技术典型应用实例Word文档格式.docx》由会员分享,可在线阅读,更多相关《钣金件数字化制造技术典型应用实例Word文档格式.docx(7页珍藏版)》请在冰豆网上搜索。
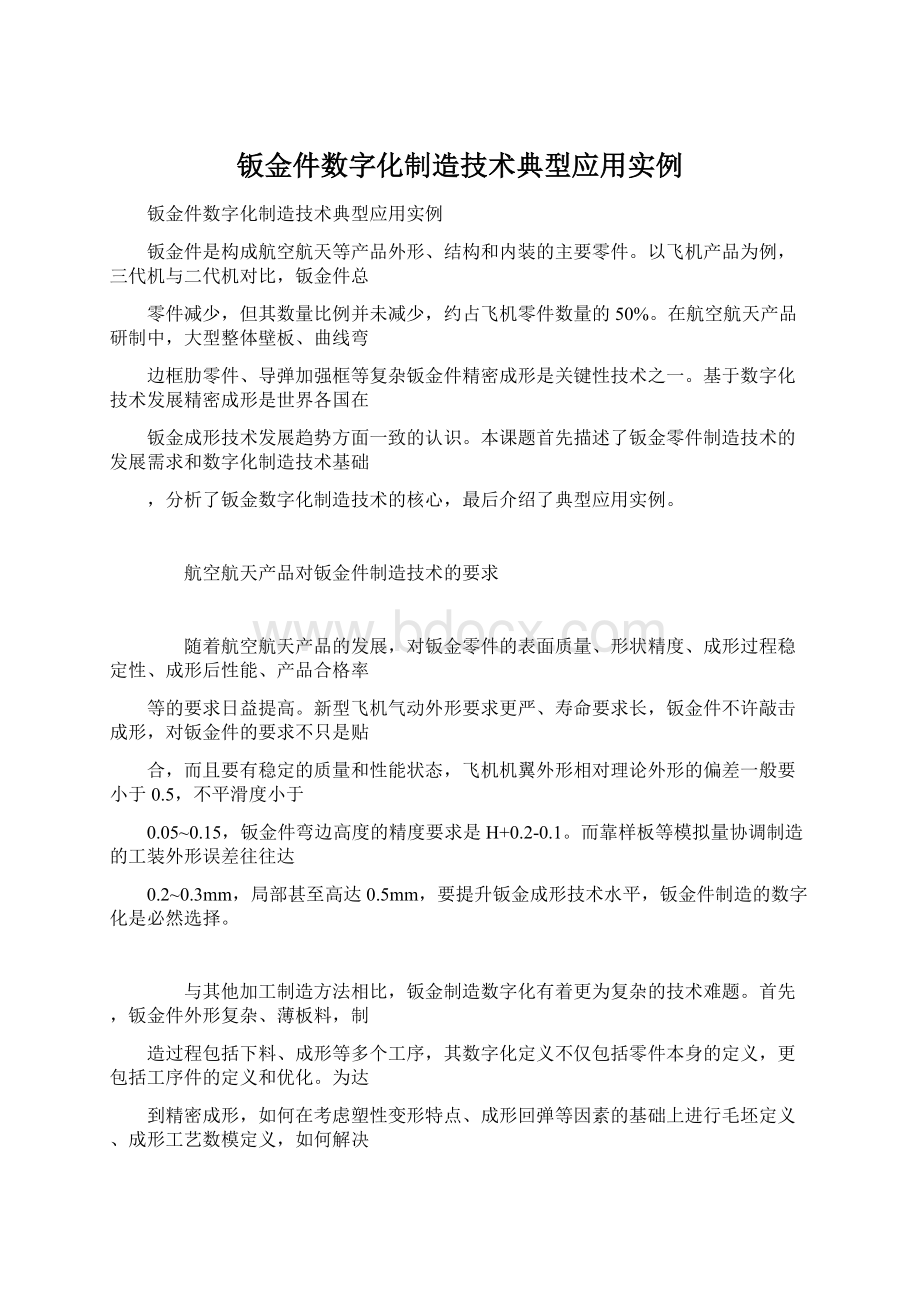
0.05~0.15,钣金件弯边高度的精度要求是H+0.2-0.1。
而靠样板等模拟量协调制造的工装外形误差往往达
0.2~0.3mm,局部甚至高达0.5mm,要提升钣金成形技术水平,钣金件制造的数字化是必然选择。
与其他加工制造方法相比,钣金制造数字化有着更为复杂的技术难题。
首先,钣金件外形复杂、薄板料,制
造过程包括下料、成形等多个工序,其数字化定义不仅包括零件本身的定义,更包括工序件的定义和优化。
为达
到精密成形,如何在考虑塑性变形特点、成形回弹等因素的基础上进行毛坯定义、成形工艺数模定义,如何解决
钣金件制造中模具型面的传递与控制等问题变得十分复杂。
其次,钣金件成形是塑性变形过程,由于物理上的非
线性所带来的不唯一性、不可逆性等引起的工艺上的不确定性,在影响钣金成形质量和生产效率的诸多因素中,
能够完全定量把握的并不多。
第三,钣金成形过程是一次性的,在较短时间内完成成形过程。
成形过程中需控制
的主要是成形力、温度等工艺过程参数,而非坐标等几何参数,控制难度更大。
由于材料性能的不稳定性和随机
性,使工艺参数设计和成形过程精确控制十分困难。
因此,需从成形工艺设计、制造模型定义、模具型面控制与
设计、工艺过程模拟与综合优化等方面展开研究,形成实现复杂钣金件精密成形的数字化制造整体解决方案。
钣金数字化制造技术基础
钣金件数字化制造是在考虑塑性变形特点、成形质量要求等因素基础上,以数字化技术为手段,通过合理的
制造模型数字化定义、模具数字化设计制造、优化的加工工艺参数及成形过程精确控制,使零件成形后不需要加
工或仅需少量加工就可满足质量要求,其过程见图1。
钣金件数字化制造技术基础包括以下方面。
(1)钣金件工艺数字化设计技术:
以钣金件制造模型信息为依据,完成制造指令设计、工艺参数计算,生成
钣金车间加工零件的生产性工艺文件。
通过对钣金材料性能数据、典型流程、工艺参数等工艺知识进行积累,把
大量经验和试验数据转化为企业内共享知识,通过知识重用技术在钣金制造过程中从知识库中提取合适知识用于
钣金成形工艺设计,提高钣金工艺设计效率和成形质量。
(2)钣金件制造模型定义技术:
钣金零件从毛坯到成品零件的成形过程由多个工序组成,下料工序的毛坯和
排样模型、成形工序的工件模型和回弹修正模型等共同构成了制造模型。
制造模型的精确定义是进行成形工艺过
程和模具设计的基本依据,控制着零件精密成形过程。
对钣金零件,需考虑零件材料、变形特性等因素,建立毛
坯和工艺模型的专用计算工具,为工装设计、工艺参数设计、数控编程等提供数据源,以满足零件精密成形的需
要。
(3)钣金件成形模具设计与制造技术:
钣金零件刚度小,橡皮囊液压成形、蒙皮拉形、型材拉弯、导管弯曲
、冲压成形等成形工艺,必须用体现零件尺寸和形状的成形模具来制造,以保证其形状和尺寸的准确度。
难点在
于为了避免成形缺陷(回弹、起皱、破裂等),实现精密成形,模具形状与最终零件形状并不相同。
以制造模型
为依据,运用数值模拟等技术手段建立模具型面和尺寸修正的综合优化技术,保证精密成形。
(4)钣金件成形数控编程与设备控制技术:
钣金数控成形设备已得到广泛应用,一些重点钣金成形设备均采
用了数控化,如数控下料铣、数控拉形机、数控弯管机、数控拉弯机、数控喷丸机等。
钣金成形设备的数控化使
生产效率、精度和产品适应性较手工成形大为提高。
对蒙皮拉形、喷丸成形、数控拉弯等设备,需要控制的主要
是成形力、时间等工艺过程参数,传统上采用经过多次试验的“录返式”方法得到控制程序,无法适应提高加工
效率和质量的要求。
通过解析各类设备控制程序文件的格式,开发根据工艺参数自动生成数控指令的工具,实现
数控编程的自动化和设备的精确控制。
钣金件数字化制造技术核心
钣金件数字化制造过程中,各种信息均以数字形式表达和存储,通过网络在钣金制造的工艺、生产等各业务
部门内传递和交换。
从以传统的模拟量为载体向以数字量为载体的制造模式的变革,核心在于2个方面:
一方面是
面向工艺链数字化定义制造模型,作为工艺、工装设计和数控代码生成的依据;
另一方面是对工艺知识进行建库
和使用,作为信息定义的支撑,从而建立以数字量定义、传递与控制为主的技术体系。
1基于制造模型的数字量传递与控制
在钣金件设计模型向最终零件的移形过程中,由于成形过程中材料性能的影响以及回弹等因素,成形钣金件
的模具形状与设计的零件最终形状存在一定偏差,而不是设计模型的简单传递。
制造模型与设计模型是同一对象
的2个不同部分,适用于2个不同阶段。
在基于模拟量传递为主的钣金件制造模式中,钣金件制造工艺过程各环节
的几何形状没有严密的数字定义,零件制造准确度难以提高。
钣金件设计模型准确描述了最终形状和尺寸,但未
考虑钣金件工艺过程的中间状态,无法解决设计信息向制造延拓的矛盾。
确定工序顺序和内容后,制造模型是考
虑工艺因素,把传统制造模式中以模拟量作为载体的零件形状和尺寸信息采用如图2所示,
基于制造模型的数字量传递与控制是通过面向工艺过程定义工件模型和工艺模型——移形到工艺装备——生
成数控程序——以数字量传递至数控设备这样一个并行数字化制造过程,其实质在于毛坯组合排样模型、成形工
艺模型等下料、成形、检验各控形节点中的CAD几何模型直接用于成形模具设计、检验工装设计、制造指令设计
、工艺参数设计、数控加工等环节;
基于工装的数字化模型,能在样板制造、模具制造中始终保持给定的公差;
考虑如图2所示,基于制造模型的数字量传递与控制是通过面向工艺过程定义工件模型和工艺模型——移形到工艺
装备——生成数控程序——以数字量传递至数控设备这样一个并行数字化制造过程,其实质在于毛坯组合排样模
型、成形工艺模型等下料、成形、检验各控形节点中的CAD几何模型直接用于成形模具设计、检验工装设计、制
造指令设计、工艺参数设计、数控加工等环节;
基于工装的数字化模型,能在样板制造、模具制造中始终保持给
定的公差;
考虑回弹等因素直接修正后进行模具设计;
这就消除了从检验标准装备到工作装备再到零件的模拟量
传递的若干中间环节引起的误差,减少了人为不确定因素的影响,改变了反复试错的制造方式,从而实现精密、
快速和低成本的制造。
2基于工艺知识的钣金件工艺过程设计
钣金件及其成形工艺的种类繁多、成形过程的多因素性决定了钣金件制造依赖于在长期实践中积累的经验知
识,钣金件工艺过程设计是知识需求密集的过程。
在钣金数字化制造中,除了使用CAx系统辅助设计工作之外,
同时还需要钣金制造知识的支持。
对已有知识的重用包括知识建库和知识使用2个基本的过程。
如图3所示,
基于知识的钣金制造要素定义是对钣金制造领域知识进行建库存储,在钣金件数字化制造过程中,应用系统
根据钣金零件信息从知识库中检索已有知识而使知识重现,形成问题的解,同时创建的新知识不断更新到知识库
中。
在对企业钣金工艺设计大量调研的基础上,对钣金工艺知识进行分类形成型谱图,对基本类型知识进一步分
解为信息后建立钣金工艺知识库框架;
对知识采集和入库,首先定义钣金工艺领域术语,在此基础上创建制造指
令知识、各种成形工艺参数设计知识、成形模具设计知识等内容。
采用基Web的架构对知识进行管理,分布式环
境便于工艺人员查阅、选用、修正和不断积累。
典型应用案例
1框肋零件橡皮囊液压成形
框肋零件是飞机机体骨架中的组件,担负着确定飞机外形和承受气动载荷的双重任务。
框肋零件的结构要素
包括腹板、弯边、加强窝、加强槽、减轻孔、下陷等。
弯边按几何形状分为直线弯边、凸曲线弯边、凹曲线弯边
,有气动外形要求的零件弯边有较严格的精度要求。
采用基于制造模型的数字量传递方法,橡皮囊液压成形模具外形的设计(见图4)依赖于制造模型中的成形工
艺模型而不是直接依赖零件原始数模。
成形工艺模型考虑了零件的回弹等因素,给出修正方案及修正参考值,对
型面和尺寸进行了合理的预修正。
通过对框肋零件回弹修正设计知识的整理和存储,建立框肋零件回弹修正模型
设计知识库,支持框肋零件回弹量的预测。
以制造模型为框肋零件橡皮囊液压成形工艺过程的数据源,改变了反
复试错的制造方式,简化了模具设计的工作,减少了人为不确定因素的影响,提高了模具设计的效率,同时可保
证零件成形后的精度,提高零件制造的质量,实现零件的精密、快速和低成本的制造。
2型材拉弯成形
航空航天产品结构中型材零件有框、肋梁的缘条和长桁零件等,是构成产品骨架的主要结构件。
以导弹加强
框为例,该类零件是导弹横向承力元件,除了维持弹身外形,其主要的功用是承受弹身的横向集中载荷,由于导
弹产品对零件强度的要求使得零件壁厚、材料硬度大,难于成形。
通过发展拉弯过程精确成形与智能控制技术,
建立数字化拉弯系统,如图5所示。
根据拉弯毛料的材料特性、几何形状、模具外形尺寸、机床工作参数、加载方式、摩擦润滑情况,结合塑性
力学与工艺参数设计知识库,计算拉弯工艺参数,根据计算参数自动生成数控加工程序,用以控制数控拉弯机成
形过程,该技术已将回弹角控制精度由1.2°
提高至0.2°
,实现型材零件精密成形。
结束语
数字化是现代制造技术发展的核心。
航空航天产品钣金件种类繁多、结构复杂,既具有共同的生产特性,又
具有各自的工艺特点,制造模型和工艺知识是钣金件数字化制造的核心所在。
由于钣金工艺的特点其实现数字化
的难点,钣金精密制造技术发展需要从基础研究、应用研究、成果工程化这样一个过程紧密衔接,经过长时间的
自主研究和工程化过程,绝非引入几套设备、软件就可以形成实现精密成形的钣金件数字化制造技术能力。
近年
来,国内在国防基础科研、民机专项等项目支持下,结合型号产品的研制,已突破了多项关键技术,为我国全面
掌握精密成形技术奠定了基础。
数字量表达和定义,是工艺资源设计和工艺过程进一步设计的依据。
其作用包括用于工艺装备设计、工艺参
数和数控程序设计。