石油炼制技术进展Word下载.docx
《石油炼制技术进展Word下载.docx》由会员分享,可在线阅读,更多相关《石油炼制技术进展Word下载.docx(15页珍藏版)》请在冰豆网上搜索。
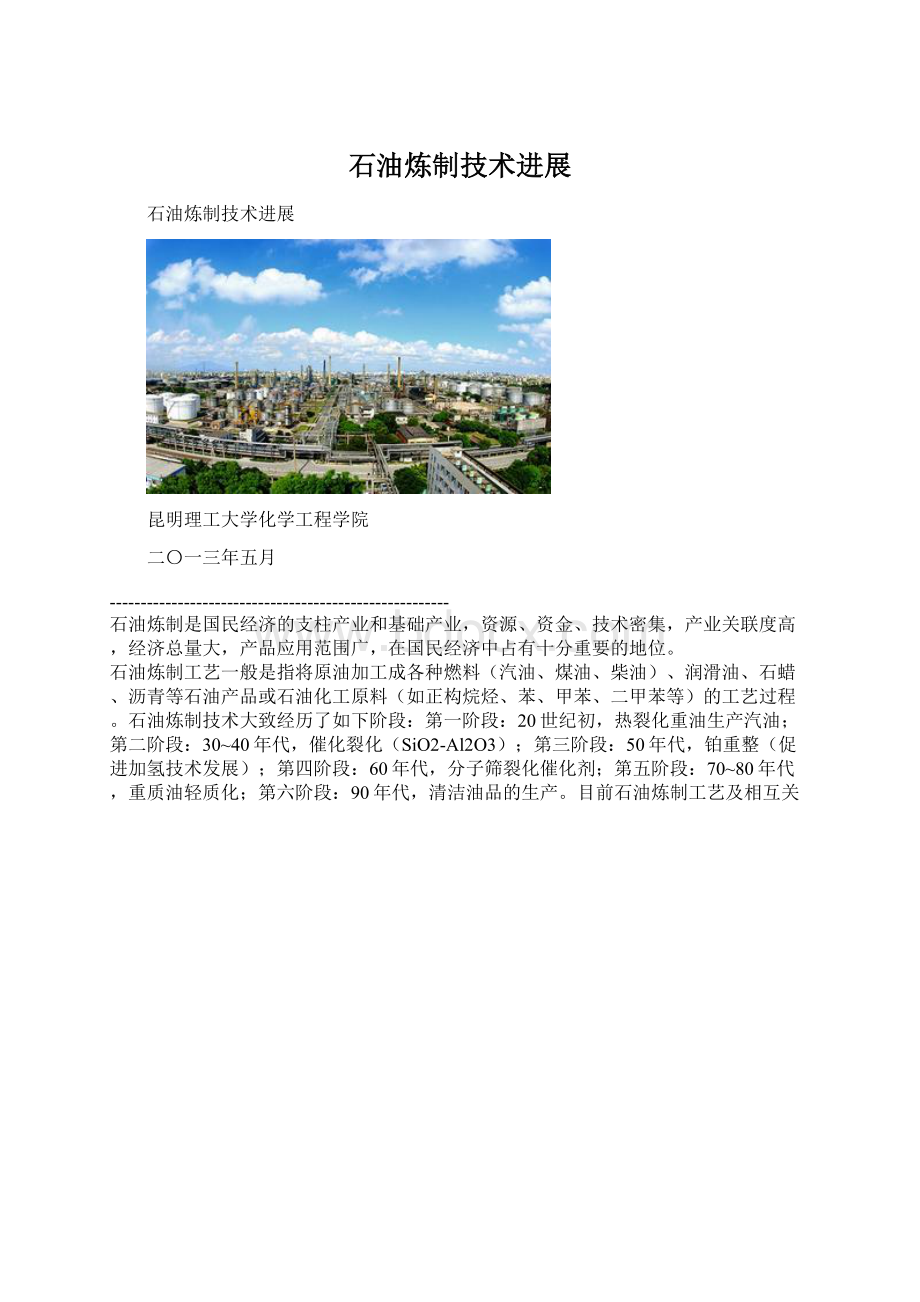
第五阶段:
70~80年代,重质油轻质化;
第六阶段:
90年代,清洁油品的生产。
目前石油炼制工艺及相互关系如图1。
催化对石油炼制技术的发展贡献巨大,如图2。
图1石油炼制工艺及其相互关系
图2催化对石油炼制技术发展的重要作用示意图
1、常减压蒸馏技术
常减压蒸馏是原油加工的第一道工序,将原油进行初步的处理、分离,为二次加工装置提供合格的原料,其流程简图如图3。
常减压蒸馏装置的构成:
一般包括:
电脱盐、常压蒸馏、减压蒸馏三部分,有些装置还有:
航煤脱硫醇、初馏塔等部分。
常减压蒸馏主要产品:
常压系统,石脑油、重整原料、煤油、柴油等产品。
减压系统:
润滑油馏分、催化裂化原料、加氢裂化原料、焦化原料、沥青原料、燃料油等。
常减压蒸馏发展的趋势:
总体原油加工能力不会有大的增长;
装置数目不断减少;
装置能力不断扩大。
图3常减压蒸馏流程简图
2、催化裂化技术
催化裂化是在酸性催化剂作用下,通过裂化反应将重质油转化为轻质油的加工工艺。
其操作条件:
460~570℃、1~2大气压。
催化裂化的化学反应包括,裂解、异构化、烷基转移、歧化、氢转移、环化、缩合、叠合、烷基化等反应是主要过程。
也含有非催化反应(热裂化),是次要过程。
催化裂化技术的变化和未来趋势:
五十年代引进前苏联移动床催化裂化(小球催化剂)。
1965年五朵金花之一流化催化裂化在抚顺石油二厂建成投产。
五朵金花:
催化裂化、催化重整、延迟焦化、尿素脱蜡、微球催化剂与添加剂。
七十年代分子筛催化剂的出现,带动了提升管催化裂化技术的发展。
1984年石家庄炼油厂大庆全常渣催化裂化的工业运行,翻开了我国重油催化裂化的新篇章。
九十年代初,前郭炼油厂实现了吉林原油全减压渣油催化裂化;
1998年大庆全减渣在燕化炼油厂实行了工业化。
九十年代,催化裂化家族技术生产低烯烃成为催化裂化技术的又一新领域。
DCC(CRP-1)最大量生产丙烯,丙烯12-18%;
丁烯11-14%。
MGG(ARGG)最大量生产LPG与优质汽油。
丙烯、丁烯10-11%;
汽油49-50%。
MIO最大量生产异丁烯、异戊烯与优质汽油。
HCC、CPP最大量生产乙烯。
新世纪初,两段提升管催化裂化技术工业化,是提升管催化裂化技术的又一新里程碑。
多种汽油降烯烃技术与催化剂的开发,提高了产品质量,满足环保法规要求。
MGD、MIP、FDFCC、ARFCC(辅助提升管)。
DOCO、LBO、GOR等系列降烯烃催化剂。
3、加氢裂化、加氢精制技术
在催化剂作用下,存在于石油馏分中的硫、氮、氧杂原子及金属杂质,通过加氢反应分别转化成H2S、NH3、H2O、金属硫化物沉积物,以改善石油馏分的品质。
原料:
重整原料、汽油、煤油、柴油重油、渣油
操作条件:
随原料而定,200~420℃,2~20MPa,空速0.2~10h-1。
加氢精制流程简图如图5。
加氢工艺是现代炼油工艺中最重要的技术之一,世界各国的炼油厂加氢装置加工能力占其原料油加工能力的比例达到50.11%,它不仅是炼油工业生产清洁燃料的主要手段,而且也成为石油化工企业的关键技术,发挥着不可替代的作用。
国民经济持续、高速、健康的发展带动了汽车工业的快速发展,我国汽车的社会保有量逐年增加,致使汽车尾气排放的有害物质已成为城市(特别是大中城市)空气严重污染的最大公害。
据环保部门测报,城市空气污染的60%~70%来自汽车尾气的污染。
大幅度改善空气质量。
图4催化裂化装置工艺流程
实践证明,减少汽车尾气污染除了采取改进汽车设计、设置汽车尾气转化器等措施外,最重要而有效的是使用清洁燃料。
通过降低燃料中能造成尾气污染的组分(如硫、氮、芳烃、烯烃等)含量,提高有利于燃料燃烧的指标,可以显著减少空气污染。
中国大多数原油较重,减压渣油的含量一般在40%-50%。
随着原油需求量的增加,更多的稠油被开采出来。
原油总的趋势是变重、质量变差。
因此催化、焦化等二次加工油品占总量的比例增加。
大量加工进口高硫原油,使得各馏分的硫含量大幅度上升。
2000年进口原油量6880万吨。
2004年进口原油量达1亿吨以上,占原油消费量的40%以上。
进口原油主要是来自中东地区的含硫原油。
世界炼油工业的发展趋势是:
继续扩大馏分油和重油加氢处理装置的加工能力,以改进油品质量的适应环保要求;
加氢装置的加工能力将大幅度增加,年均增长8.3%,以满足增产清洁燃料生产的需要。
我国炼油装置构成不尽合理,催化裂化比例过高,加氢裂化、加氢精制、催化重整、烷基化和醚化装置比例过低。
加氢总能力占原油一次加工能力的17.82%,低于50.11%的世界平均水平。
由于更加严厉的硫排放标准,汽油和柴油的超深度加氢脱硫是目前本领域的挑战及研究核心。
图5加氢精制流程简图
4、催化重整技术
催化重整是在催化剂存在下,将直链烷烃或环烷烃转化为芳烃的过程。
它是炼厂生产高辛烷值汽油组分的重要过程,也是为石油化工生产芳烃的主要过程。
此外,它还富产廉价的氢气成为炼厂用氢的主要来源。
催化重整包含氢化、异构化、芳基化、裂化等反应。
催化重整技术经历了三个阶段的发展。
1940~1949年,临氢重整,辛烷值~80。
缺点:
催化剂活性低、寿命短(几个小时),辛烷值低,二战后停止发展。
1949~1967年,铂重整。
美国UOP,第一套铂重整装置Platfroming。
优点:
催化剂活性高、稳定性好、选择性好等。
1967年,铂铼重整。
1967年,Chevron开发PtRe/Cl-Al2O3。
石油炼制是国民经济的支柱产业,在社会经济发展过程中发挥重要作用,其技术的发展日新月异,对环境的危害受到越来越重视,相信我们一定会协调好与环境的关系。
下面以某地区800万吨/年炼油厂工艺流程、用水、用电、用地及环境保护等方面的要求为例,说明石油炼制的详细工艺及过程。
1.炼油厂工艺流程介绍
炼油厂主要包括常减压、催化裂化、延迟焦化、催化重整等典型装置。
1)常减压流程
原油在蒸馏前必须严格进行脱盐脱水,其目的是降低换热器或常压炉的热负荷和压力降,稳定常压分馏的操作以及减轻设备的腐蚀和结垢,一般要求原油含水<
0.5%,含盐<
20毫克/升。
脱盐、脱水后的原油换热到230~240℃,进入预汽化塔(也称初馏塔),从预汽化塔顶抽出轻汽油或重整原料油,其中一部分返回塔顶作塔顶回流。
侧线一般不出产品,也可抽出组成似重汽油的馏分,经换热后,一部分打入常压塔中段回流入口处(在常压塔侧一、二线之间),这样可以减轻常压炉和常压塔的负荷,另一部分则送回初馏塔侧作本塔的循环回流。
塔底拔头原油,经常压炉加热到360~370℃,进入常压塔,塔顶部打入冷回流,使塔顶温度约为90~100℃左右,由于塔顶到进料段温度逐渐上升,利用汽油、煤油、柴油等馏分的沸点范围不同,塔顶蒸出汽油蒸汽,煤油、轻柴油则呈液相依次从侧一线、侧二线、侧三线蒸出,这些侧线馏分经汽提塔、吹出重迭的轻组分后,与原油换热,回收一部分热量,然后分别经冷却到一定温度后送出装置。
塔底则为未汽化的重油,经过热水蒸汽汽提,吹出未被蒸出的轻组分后,作减压塔进料油。
为了使塔内上、下段汽液相负荷比较均匀,并充分利用回流热,一般在塔各侧线抽出口之间,打入1~2个中段循环回流。
常压塔底重油,用泵送入减压炉,加热到410℃左右送入减压塔。
塔顶分出不凝汽和水蒸汽,进入大气冷凝器,经冷凝冷却后,用二至三级蒸汽抽空器抽出不凝气,维持塔内残压20~80毫米汞柱,以利于油品充分蒸出,塔侧从第一、二、三侧线,抽出轻重不同的润滑油馏分或催化裂化原料油,它们分别经汽提、换热、冷却后,一部分可以返回塔侧作循环回流,一部分送出装置。
塔底渣油经水蒸汽汽提提高拔出率,然后用泵抽出经换热、冷却出装置,渣油用作丙烷脱沥青、氧化沥青或作为焦化原料时,也可以经换热,不经冷却,直接送入下一工序。
2)催化裂化流程
催化裂化装置一般由三个部分组成,即:
反应—再生系统、分馏系统和吸收—稳定系统。
反应再生部分:
由反应器、再生器、空气输送设备等组成。
原料油通过反应器与催化剂接触并反应,不断导出反应产物,催化剂则在反应器和再生器之间不断循环,在再生器中通空气烧去催化剂上积炭,恢复催化剂活性,烧焦放出的热量又以催化剂为热载体,不断带回反应器供给反应消耗的热量。
分镏部分:
从反应器不断导出的反应产物一油气混合物,通过分镏塔等设备分离出裂化富气、粗气油、轻柴油、重柴油等产物,还有一部分回炼油、渣油可以送回反应器重新裂化(回炼)。
吸收稳定部分:
由压缩机、吸收塔、解吸塔、稳定塔、汽油碱洗等设备组成。
目的是从裂化富气、粗汽油中进一步分离出干气、液化气和合格的稳定汽油。
3)延迟焦化流程
原料油经换热及加热炉对流段升温到350℃左右,进入分馏塔下部蒸发段与焦炭塔来的焦化油气直接换热,将原料油中轻组分油分出,同时又加热了原料油。
蒸发段温度调节在360~380℃,蒸发段温度低,冷凝下来的循环油量就大,循环比(即回炼比:
循环油量/新鲜原料油量)就大,蒸发段温度高,则循环油量小,循环比(回炼比)就小。
分馏塔底温度控制在390~395℃,并且有塔底循环油泵保持油料的不断循环,以尽量减少塔底结焦的机会。
经过换热的塔底原料油和循环油经过粗细过滤器,送入加热炉辐射段,辐射入口压力为30~40大气压,快速升温到500~505℃。
为减少加热炉管结焦,入口处注入约为原料油量的2℃(重)、300℃的软化水,使油品以强烈湍流状态通过油品的临界反应区,气液混合物流速提高到30~45米/秒,达到延迟焦化反应的目的。
炉出口油料通过四通阀进入焦炭塔,依靠本身降温放出的显热进行反应(绝热条件下),分解生成的油气约430~440℃,从焦炭塔顶挥发线引出,主要进入分馏塔进行产品分离,缩合生成的焦炭层从下至上逐渐集结在焦炭内,焦层上部有泡沫层,是反应中的中间产物在高温中起泡所致,泡沫层应该低于焦炭塔的安全高度。
焦炭塔为低压操作,一般不超过3.5大气压,塔内线速不超过0.15/秒,油气停留时间为1.5~6.5分钟。
焦炭塔是间歇操作,一般有2~4个焦炭塔切换使用。
切换周期一般为48小时,其中结焦24小时,除焦等其它操作时间24小时。
在生产中,焦炭塔焦炭及泡沫层料位逐步增高达到全塔高度的2/3~3/4即停止进料,炉出口油料切换到另一个焦炭塔。
老塔停止进进料后,必须立即吹汽,赶走残余油气,减少焦炭塔的挥发分,吹汽后进行水冷,最后进行除焦。
新塔在切换进料前就要进行试压、油气预热,预热过程中塔底有部分油气冷凝下来的凝缩油,在进料前通过油泵将其抽出。
4)催化重整流程
预处理合格的原料油与循环氢气混合后,与重整生成油换热,然后进入加热炉加热至规定温度,进入第一反应器,进行重整反应。
由于芳构化等反应为强吸热反应,反应器床层温度随之下降,为了保持较高的反应温度,以保持较高的反应速度,需要不断地在反应过程中补充热量。
因此,流程中三个反应器之间都有加热炉,重整反应物每进入下一个反应器之前,都先加热到指定的反应温度,再进入到下一个反应器。
如此,可维持较高的平均反应温度。
自反应器出来的重整生成油,温度仍很高,为了回收热量,该反