白车身的焊点设计标准指南Word格式.doc
《白车身的焊点设计标准指南Word格式.doc》由会员分享,可在线阅读,更多相关《白车身的焊点设计标准指南Word格式.doc(8页珍藏版)》请在冰豆网上搜索。
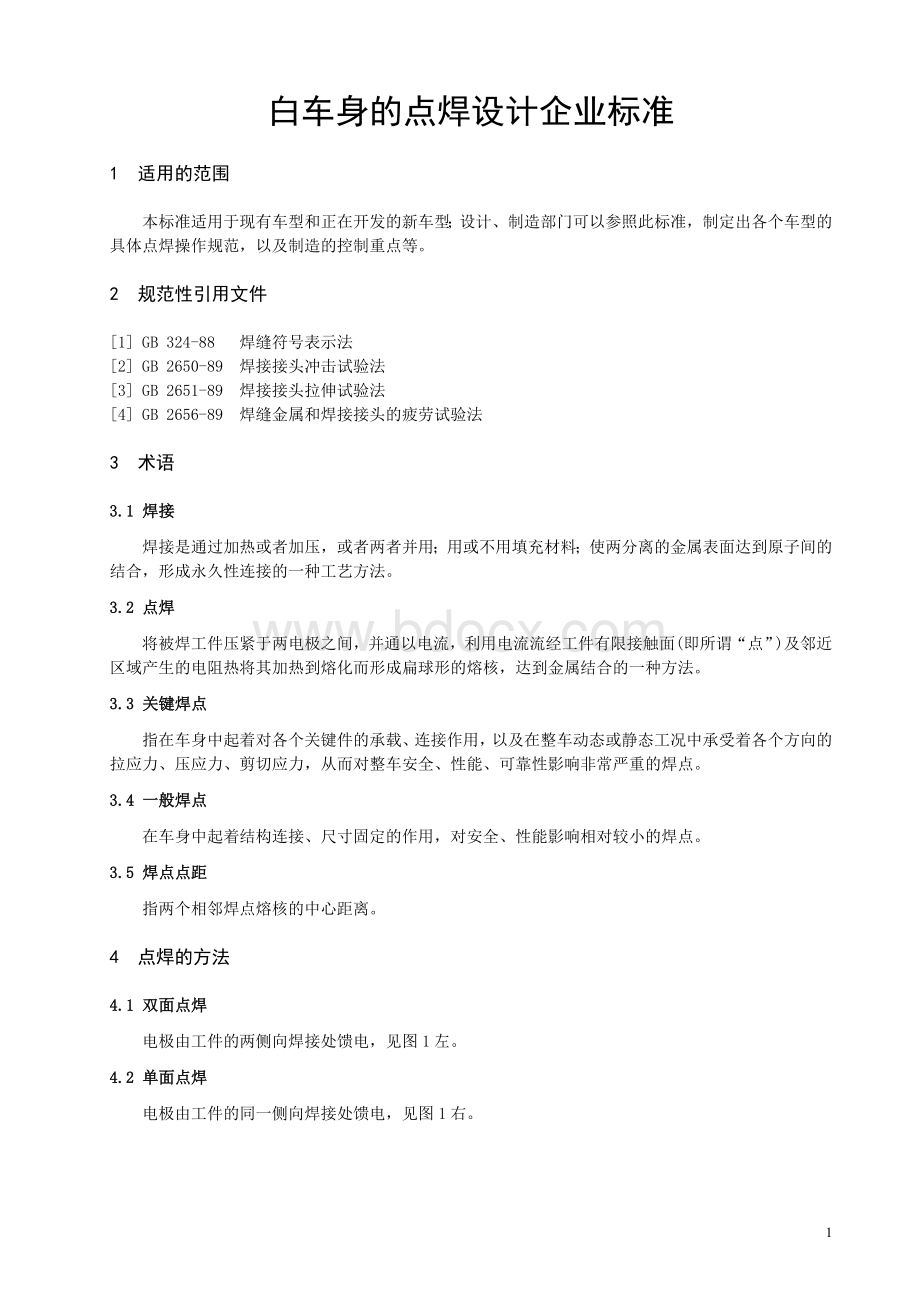
指两个相邻焊点熔核的中心距离。
4点焊的方法
4.1双面点焊
电极由工件的两侧向焊接处馈电,见图1左。
4.2单面点焊
电极由工件的同一侧向焊接处馈电,见图1右。
图1点焊方法示意图(左--双面点焊,右--单面点焊)
5点焊的工艺参数选择
5.1点焊的主要工艺参数
焊接电流、电极压力和焊接时间;
它们通常是根据工件的材料和厚度,同时参考该种材料的焊接条件表(几种常用金属点焊的焊接条件数据见附录A)来选取,具体由生产部门试生产、剖检后决定。
5.2工艺参数的确定步骤
1).确定电极的端面形状和尺寸。
2).初步选定电极压力和焊接时间,调节焊接电流,以不同的电流焊接试样。
3).检验试样的熔核直径,符合要求后,再在适当的范围内调节电极压力、焊接时间和焊接电流,进行试样的焊接和检验,直到焊点质量完全符合技术条件所规定的要求为止。
5.3试样的检验方法
1).撕开法,优质焊点的标志是:
在撕开试样的一片上有近似圆孔,另一片上附着从另一侧材料撕裂下来的近似圆凸台,断口呈撕裂状,无发脆整齐断裂。
2).由剪切的断口判断熔核的直径。
3).低倍测量、拉伸试验和X光检验,以判定熔透率、抗剪强度和有无缩孔、裂纹等。
6点焊的接头设计原则
6.1点焊的接头形式
搭接接头和折边接头,见图2,接头可以由两个或两个以上等厚度或不等厚度的工件组成;
对于不厚度的工件,薄件与厚件的厚度比不能小于1/3;
原则上不允许出现四层或四层以上的焊接接头结构,特殊的工艺焊点除外,如必须使用,需由白车身经理批准和规划设计院工艺部门确认。
图2点焊的接头形式(a—边距,b—搭接量)
6.2电极的可达性
点焊存在电极的可达性问题,即电极必须能方便地抵达工件的焊接部位。
设计点焊接头时,必须考虑到点焊机的机臂长度(喉深)和电极尺寸,才能保证所设计的接头在相应的点焊机上方便地进行焊接。
6.3接头的边距(a)
见图2,其最小值取决于被焊金属的种类,厚度和焊接条件(几种常用金属点焊的焊接条件数据见附录A);
对于屈服强度高的金属、薄件或采用强条件时可取较小值。
6.4接头的搭接量(b)
1).见图2,它是边距的两倍,同时搭接量与熔核大小、焊头直径密切相关;
表1示出了几种材料的最小搭接量,表中的数据都是最小的极限值,实际应用中可以以此为下限进行参考。
2).对于白车身焊接,通常情况下,搭接量的取值范围为12-20mm;
由于目前焊接电极一般为φ13mm或φ16mm,所以搭接量必须在15mm以上,特殊位置如门玻璃导槽位置等可以在12mm以下,但应允许半个焊点。
表1接头的最小搭接量(板厚值指被焊板中的较薄者,单位:
mm)
板厚
单排焊点
双排焊点
结构钢
不锈钢及高温合金
轻合金
0.5
8
6
12
16
14
22
0.8
9
7
18
1.0
10
20
24
1.2
11
26
1.5
30
2.0
28
34
2.5
32
40
3.0
36
46
3.5
38
48
4.0
42
50
注:
此表摘录于“中国机械工程学会焊接学会编的《焊接手册(第1卷)—焊接方法及设备》”。
6.5焊点的点距
1).即相邻两焊点的中心距,其最小值与被焊金属的厚度、导电率、表面清洁度、以及熔核大小有关,同时点距与被焊板件的层数(两层或三层)也密切相关,表2示出了几种材料的最小点距,表中的数据都是最小的极限值,实际应用中可以以此为下限进行参考。
2).对于白车身焊点的点距,通常情况下,其最小值为15-18mm,最大值为45-55mm。
如一般低碳钢点焊间隙在30-35mm左右,可以在局部位置采用锯齿型布置。
表2焊点的最小点距(板厚值指被焊板中的较薄者,单位:
点距
15
25
35
6.6装配间隙
装配间隙必须尽可能小,因为靠压力消除间隙将消耗一部分电极压力,使实际的焊接压力降低。
间隙的不均匀性又将使焊接压力波动,从而引起各焊点强度的显著差异,过大的间隙还会引起严重飞溅,许用的间隙值取决于工件刚度和厚度,刚度、厚度越大,许用间隙越小,通常为0-1mm。
7焊点的直径与接头强度
7.1焊点的最小直径
1).焊点的直径与被焊工件的材料、料厚有关,它是评定点焊接头质量的主要指标之一。
表3示出了几种材料焊点的最小直径,表中的数据都是最小的极限值,实际应用中可以以此为下限进行参考。
2).对于白车身的焊点直径,通常情况下,其取值范围为4-8mm;
另外一般焊点直径可取为6mm,关键焊点直径可取为7mm。
表3焊点的最小直径(板厚值指被焊板中的较薄者,单位:
焊点直径
低碳钢、低合金钢
不锈钢、耐热钢
6.0
6.5
0.6
7.5
7.0
8.0
9.0
10.0
4.5
此表摘录于“傅积和,孙玉林主编的《焊接数据资料手册》”。
7.2点焊接头强度
1).点焊接头强度常用室温或高温单点抗剪力表示,此抗剪力取决于两板交界上熔核的面积。
2).以单点正拉力和单点抗剪力之比作为判断接头延性的指标,此比值越大,则接头的延性越好;
一般认为此比值≥25%时,接头的延性尚可,≥40%时,接头的延性良好。
3).多个焊点形成的接头强度还取决于点距和焊点分布,必须兼顾点距和焊点数量,多列焊点最好交错排列而不要作矩形排列。
4).焊点的抗剪强度测量示意图,如图3所示。
图3抗剪强度测量示意图
5).几种材料焊点的最小直径和抗剪强度见表4
表4焊点的最小直径和强度
工件厚度
(mm)
抗剪强度(N/点)
10钢
30CrMnSiA
1Cr18Ni9Ti
LY12
LF2
LF21
0.5+0.8
3500
4400
4800
1350
1000
900
1.0+1.0
4500
6000
6500
1600
1400
1200
1.2+1.2
5.0
7000
10000
2100
1800
1.5+1.5
12000
3000
2500
1700
2.0+2.0
14000
18000
4200
3800
—
2.5+2.5
16000
22000
5500
3.5+3.5
24000
34000
9000
7200
8焊点的分类
8.1关键焊点
一般来说,关键焊点的位置,可以从以下几个方面进行判定:
关键件的承载部位:
这些部位主要指动力总成、悬挂、副车架、座椅、安全带、铰链、门锁、拖曳臂、后轴等关键件的相应安装部件上的焊点。
应力危险部位:
对白车身总成进行CAE分析,得到白车身整体或局部的应力分布图,然后根据各部位的应力恶劣情况来确定关键焊点的位置;
或根据长时间经验积累和试验,以及通过与做过CAE分析的车型进行类比,给出受力情况比较恶劣的应力危险点。
白车身常见的应力危险部位有以下:
前、后悬架的安装点部位,后悬架减振器座部位,前悬架减振器座部位,后拖曳臂支架部位、铰链安装点部位等。
影响安全性的部位:
在车辆碰撞或翻滚的情况下,车身结构将产生弯曲变形和扭转变形,所有构件之间均将产生作用力,通过碰撞仿真模拟、力学分析或实车碰撞,可以确定影响碰撞安全的主要传力部件和受力最危险的构件,从而确定出关键焊点的分布。
白车身常见的影响碰撞安全性的部件有以下:
前纵梁、后纵梁、门槛、顶盖、地板横梁、A柱、B柱、C柱等骨架结构部件;
这些部件总成上的焊点以及这些部件总成互相连接处的焊点均属于关键焊点。
对车身结构进行静态、动态应力分析以及安全结构分析,可以得出危险的构件截面、应力集中点以及各个部件的受力情况。
但是,考虑到同一个名称的部件在不同的车身结构型式中,对整车安全性影响不同,所以这种判定有很大的局限性和相对性;
因此