毕业设计论文拨叉工艺设计说明书Word格式文档下载.docx
《毕业设计论文拨叉工艺设计说明书Word格式文档下载.docx》由会员分享,可在线阅读,更多相关《毕业设计论文拨叉工艺设计说明书Word格式文档下载.docx(10页珍藏版)》请在冰豆网上搜索。
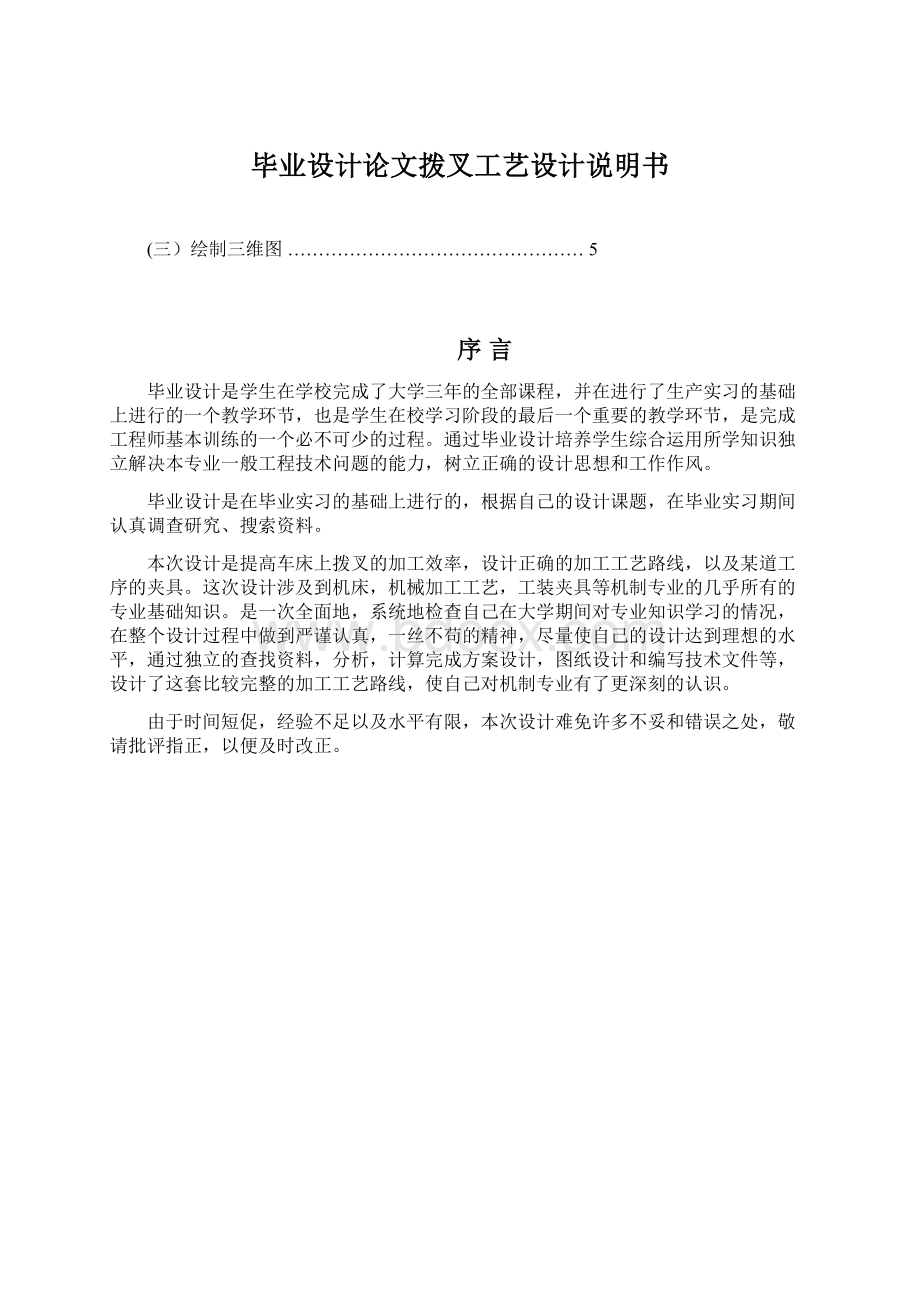
(1)小孔以及与之相通的锥孔、螺纹孔。
(2)大头半圆孔Φ50
(3)拨叉底面,小头孔端面,大头半圆孔端面,大头半圆孔端面与小头孔中心的垂直度误差为0.07mm,小头孔上端面与之中心线的垂直度误差为0.05,
由上面分析可知,可以粗加工拨叉底面,然后以此为粗基准采用专用夹具进行加工,并且保证位置精度,再根据加工方法的经济精度以及机床所能达到的位置精度,并且此拨叉零件没有复杂的加工曲面,所以根据上述要求,采用常规的加工工艺均可保证。
(三)绘制三维图
图1-1零件立体图
二、工艺规程设计
(一)基面的选择
基面的选择是工艺规程中的重要工作之一,基面选择正确与合理可以使加工质量得到保证,生产效率提高。
(1)粗基准的选择
在选择粗基准时,考虑的重点是如何保证各加工表面有足够多的余量,及保证不加工表面与加工表面间的尺寸,位置符合零件图样设计要求,粗基准的选择原则:
1)重要表面余量均匀原则
必须首先保证工件重要表面具有较小的加工余量,应选择该表面为粗基准。
2)表面间的相互位置要求原则
必须保工件上加工表面与不加工表面之间的相互位置要求,应以不加工表面作为粗基准,如果在工件上有很多不加工表面,应以其中与不加工表面相互位置要求较高的不加工表面作为粗基准,以求壁厚均匀外形对称等。
3)余量足够原则
如果零件上各个表面均需加工,则以加工余量较小的表面作为粗基准。
4)定位可靠性原则
作为粗基准的表面,应选用比较可靠,平整光洁的的表面,以便定位准确,夹紧可靠,在铸件上不应该选择有浇冒口的表面,分型面,有毛刺或夹砂的表面作为粗基准;
在锻件上不应该伴有飞边的表面作为粗基准,若工件上没有合适的表面作为粗基准,可以先铸出或焊上几个凸台,以后再去掉。
5)不重复使用原则
粗基准的定位精度低,在同一尺寸方向上只允许使用一次,不能重复使用。
对于一般类的叉杆类零件而言,以孔和端面作为粗基准,是完全合理的。
对于本零件而言,尽可能选择不加工便面为粗基准,而对于有若干个不加工表面的工件,则应以与不加工表面要求要求相对位置精度较高的不加工表面为粗基准,以求壁厚均匀外形对称等。
根据这个基准选择原则,现选取Φ20孔的不加工外轮廓作为粗基准,利用俩个V型块支撑Φ20俩个外轮廓表面作为粗基准的定位面,限制5个自由度在利用一个销钉限制一个自由度达到完全定位然后进行铣削。
对于拨叉零件而言,尽可能选择不加工表面为粗基准,而对于有若干个不加工表面的工件,则应以与不加工表面为粗基准,根据这个基准选择原则,现选取拨叉俩个φ20孔的下端面为粗基准,利用俩个φ20的外轮廓作为主要定位面,再以一个销钉限制最后一个自由度,达到完全定位。
(二)精基准的选择
精基准的选择原则主要考虑如何减少误差,保证加工精度和安装方便以及以及设计基准和工序基准重合问题。
当二者不重合时,应该进行换算。
(1)基准重合原则
应尽可能选择零件的设计基准作为定位基准,以避免产生基准不重合原则。
(2)基准统一原则
应尽可能选用精基准定位加工各表面,以保证各表面之间的位置精度。
采用统一基准的好处在于:
可以在一次安装中加工几个表面,减少安装次数和安装误差,有利于保证各加工表面之间的相互位置精度;
准备时间,便于采用高效率的专用设备,大幅度的提高生产率。
(3)自为基准原则
有些精加工或光整加工工序要求加工余量小而均匀,应选择加工表面为精基准。
有关工序所采用的夹具结构比较统一,简化夹具的设计与制造,缩短生产。
(4)互为基准反复加工原则
有些相互位置精度要求较高的表面,可以采用互为基准反复加工的原则来保证定位可靠性原则精基准应凭整光洁,具有相应的精度,确保定位简单准确,便于安装,夹紧可靠。
如果工件上没有能作为精基准选用的恰当表面,可以在工件专门加工出定位基面,这种精基准成为辅助基准,辅助基准在零件的的工作中不起任何作用它仅仅是为加工的需要而设计的。
(5)加工阶段的划分
该拨叉加工质量要求较高,可将加工阶段划分成粗加工、半精加工和精加工几个阶段。
(6)工序的集中和分散
本拨叉选用工序集中原则安排拨叉的加工工序。
该拨叉的生产类型为成批生产,可以采用万能型机床配以专用工、夹具,以提高生产率;
而且运用工序集中原则使工件的装夹次数少,不但可缩短辅助时间,而且由于在一次装夹中加工了许多表面,有利于保证加工表面之间的相对位置精度要求。
(7)加工原则:
1)遵循“先基准后其他”原则,首先加工基准——拨叉下端面。
2)遵循“先粗后精”原则,先安排粗加工工序,后安排加工工序。
3)遵循“先主后次”原则。
4)遵循“先面后孔”原则。
考虑保证零件的加工精度和装夹准确方便,依据“基准统一和基准重合”原则,以粗加工底面为定位粗基准。
(三)制定工艺路线
制定工艺路线的出发点,应当是使零件的几乎形状,尺寸精度及位置精度等技术要求能得到合理保证,再生产纲领已确实,为大批量生产的条件下,可以考虑使用万能机床配以专用的夹具,并尽量使工序集中来提高生产率,除此之外,还应当考虑经济效果,以便使生产成本尽量降低。
图2-1铸件简图
具体工艺过程如下:
工序01粗铣Φ40、Φ50下端面,以T2为粗基准,采用X6140卧式铣床加专用夹具;
工序02粗铣Φ40上端面,以T1为定位基准,采用X6140卧式铣床加专用夹具;
工序03粗铣Φ50上端面,以T4为定位基准,采用X6140卧式铣床加专用夹具;
工序04钻、扩Φ20孔,以Φ32外圆和T2为基准,可采用多刀组合机床;
工序05粗铣Φ20台阶面,采用X6140卧式铣床加专用夹具;
工序06粗镗Φ50孔,以D1为定位基准,采用T616卧式镗床加专用夹具;
工序07精铣Φ40下端面,以T2为基准,保证其粗糙度为12.5um,采用X51立式铣床加专用夹具;
工序08精铣Φ40上端面,以T1为基准,保证其粗糙度为25um,采用X51立式铣床加专用夹具;
工序9拉20孔,以T2和34外圆为基准,保证其粗糙度为1.6um,采用卧式拉床加专用夹具;
工序10精铣Φ50下端面,以D1为基准,保证其粗糙度为6.3um,采用X51立式铣床加专用夹具;
工序11精铣Φ50下端面,以D1为基准,保证其粗糙度为6.3um,采用X51立式铣床加专用夹具;
工序12拉Φ50孔,以D1做定位基准,保证其粗糙度为6.3um,可采用卧式拉床加专用夹具。
工序13钻、铰3锥孔,以T1和零件中线为基准,采用Z525立式钻床加专用夹具;
工序14钻、铰M8底孔,以T1和零件中线为基准,保证其粗糙度为3.2um,采用Z525立式钻床加专用夹具;
工序15钻M10底孔,以T1和零件中线为基准,采用Z525立式钻床加专用夹具;
工序16铣断,以D1为基准,采用X60卧式铣床加专用夹具;
工序17去毛刺;
工序18终检。
(四)机械加工余量,工序尺寸及毛坯的确定
拨叉零件材料為HT200,硬度為190-210HB,重量為1.0kg,生產类型为大批生产,采用在金属模机器造型,查《机械制造工艺简明手册》以下简称《简明手册》表2.2-5知;
毛坯的加工余量的等级为4,尺寸公差CT为8查表2.2-4单侧加工时,其加工余量为2.0mm,双侧加工时,每册加工余量为1.5mm。
1.根据上述原始资料及加工工艺,分别确定各加工表面的机械加工余量,工序尺寸及毛坯尺寸如下:
(1)φ20孔的加工余量的确定
查《机械制造工艺设计简明手册》表2.3-8得,各加工余量分别为拉孔0.20mm、扩孔1.8mm、钻孔18mm,总余量为20mm(由于该处孔径较小,未先预铸孔,故用φ18的钻头钻出φ18的孔)。
(2)Ф50圆弧和Ф54圆弧连接的孔的加工余量的确定
查《机械制造工艺设计简明手册》表2.3-9得,Ф50圆弧段各加工余量分别为粗镗4mm、拉孔1mm、总余量为5mm,(该处先已预铸出φ45的孔)。
(3)φ40的两个端面的加工余量的确定
查《机械制造工艺设计简明手册》表2.3-21得,各加工余量分别为精铣1mm、粗铣4mm,一个端面总余量为5mm。
(4)拨叉底面的加工余量的确定
查《机械制造工艺设计简明手册》表2.3-21得,其粗铣的加工余量为2mm。
2、为了更直观一些,做表如下
表2-1圆柱表面工序尺寸
加工表面
加工内容
加工余量
精度等级
工序尺寸
表面粗
糙度
工序余量
最小
最大
φ50IT12
(D2)
铸件
7.0
CT12
镗
4.0
IT12
6.3
0.95
6.8
拉
3.0
IT10
3.2
2.9
3.25
φ20IT7
(D1)
钻
18
IT11
17.89
扩
1.8
1.716
1.910
0.20
IT7
1.6
0.039
0.093
表2-2平面工序尺寸
工序号
工序内容
基本尺寸
经济精度
工序尺寸偏差
5.0
01
粗铣φ40孔下端面
36.0
12
1.5
7.75
02
粗铣φ40孔上端面
32.0
03
粗铣φ50孔上端面
14.0
6.38
07
精铣φ40孔下端面
1.0
31.0
8
0.75
1.283
08
精铣φ40孔上端面
30.0
10
精铣φ50孔端面
1.0×
2
12.0
0.951
1.016