壳体设计说明书Word文件下载.docx
《壳体设计说明书Word文件下载.docx》由会员分享,可在线阅读,更多相关《壳体设计说明书Word文件下载.docx(20页珍藏版)》请在冰豆网上搜索。
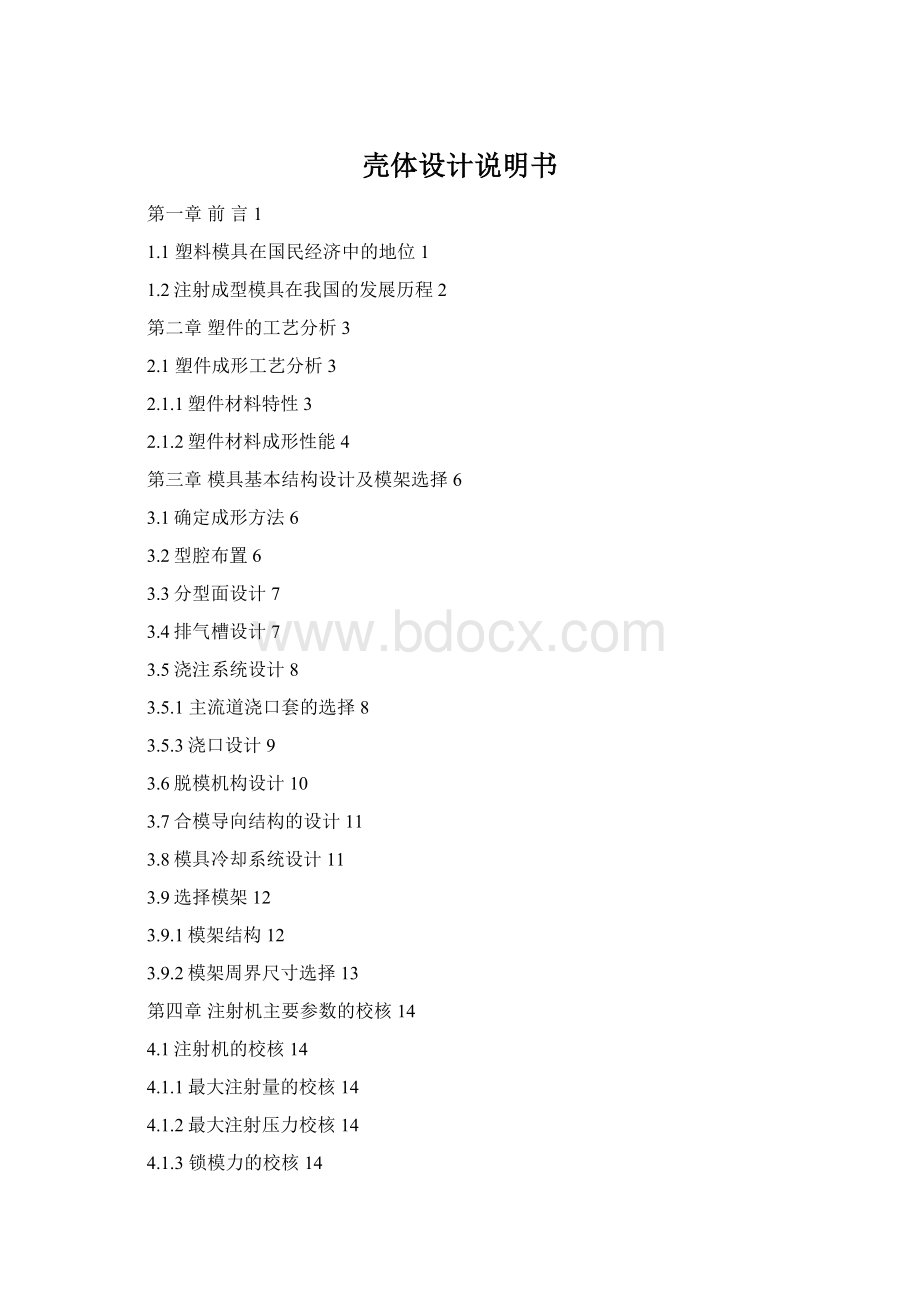
3.8模具冷却系统设计11
3.9选择模架12
3.9.1模架结构12
3.9.2模架周界尺寸选择13
第四章注射机主要参数的校核14
4.1注射机的校核14
4.1.1最大注射量的校核14
4.1.2最大注射压力校核14
4.1.3锁模力的校核14
4.1.4开模行程的校核15
第五章模具结构尺寸的设计计算15
5.1型腔、型芯的结构设计16
5.2型腔、型芯尺寸的计算16
第六章模具的装配、试模17
6.1模具的安装试模17
6.1.1安装17
6.1.2试模17
6.1.3修模18
6.1.4检验19
6.2模具的总装配图20
总结21
致谢22
参考文献23
第一章前言
1.1塑料模具在国民经济中的地位
随着现代工业发展的需要,塑料制品在工业、农业和日常生活等各个领域的应用越来越广泛,质量要求也越来越高。
注射成形是成形热塑件的主要方法,因此应用范围很广。
注射成形是把塑料原料放入料筒中经过加热熔化,使之成为高黏度的流体,用柱塞或螺杆作为加压工具,使熔体通过喷嘴以较高压力注入模具的型腔中,经过冷却、凝固阶段,而后从模具中脱出,成为塑料制品。
塑料注射成形工艺的最大特点是复制,能够复制出所需任意数量的可直接使用或稍作处理即可使用的制品,是一种适宜大批量生产的工艺。
虽然在设备上投入较大,但是可以生产制品的数量非常大,实属一种经济快捷的生产方式,因此得到广泛的应用和快速的发展。
在塑料制品的模具制造设备、合理的加工工艺,优质的模具材料和现代化的成型设备等是成型优质塑件的重要条件,所以模具是塑料成型加工的一种重要工艺装备,是工业化国家实现产品批量生产和新产品研发所不可缺少的工具。
用模具生产制品所表现出来的高效率、低消耗、高一致性、高精度和高复杂程度是其他任何制造方法所不及的,模具工业是国民经济的基础工业,其生产技术水平高低的重要标志。
1.2注射成型模具在我国的发展历程
模具技术是一门综合性很强的学科,是近年来飞速发展的学科之一。
目前为止,我国在塑料模的制造精度、模具标准化程度、制造周期、模具寿命以及塑料成型设备的自动化程度和精度等方面已经有了长足的进步,但及国外工业先进国家相比,仍有一定的差距。
许多精密技术,大型薄壁和长寿命塑料模具自主开发的生产能力还较薄弱。
要加速发展模具行业,应在模具先进的设计技术,先进的制造技术和开发研制优质的模具材料等方面下功夫,以提高模具的整体制造水平和模具在国内、国际的市场竞争能力。
进入20世纪90年代,我国国民经济的持续增长,带动了塑料工业的快速增长。
塑料机械产业明显的跃升,促使注射产品的应用领域从一般日用、民用行业向国民经济几乎所有的部门拓展,而且具有较高技术含量和高附加值的注射产品开发应用不断增多,提高了我国注射行业的整体水平。
塑料制品的广泛应用为塑机行业发展提供了不竭动
力,我国塑料行业的巨大发展潜力为中国塑料机械行业的迅猛成长开拓了广阔的空间。
从注射机问世起中小型注射机占绝大多数。
到了20世纪70年代后期,由于工程塑料的发展,特别是在汽车、船舶、宇航、机械以及大型家用电器方面的广泛应用,使大型注射机得到了迅速发展。
80年代以来,CAD/CAE/CAM计算机应用技术在注射机制造业的广泛采用,促使了我国注射机研发和制造水平的高速发展。
今后,随着高精度塑件应用范围的扩大,一些科技含量高的注射机有很大的发展。
随着新工艺、新设备的出现必将更好地推动我国注射行业的发展。
第二章塑件的工艺分析
2.1塑件成形工艺分析
如图2-1为塑件的二维工程图及实体图,单位mm。
图2-1塑件图
2.1.1塑件材料特性
材料简介:
ABS是AcrylonitrileButadieneStyrene的首字母缩写)是一种强度高、韧性好、易于加工成型的热塑型高分子材料。
因为其强度高、耐腐蚀、耐高温,所以常被用于制造仪器的塑料外壳。
ABS树脂是微黄色固体,有一定的韧性,密度约为1.04~1.06g/cm3。
它抗酸、碱、盐的腐蚀能力比较强,也可在一定程度上耐受有机溶剂溶解。
ABS树脂可以在-25℃~60℃的环境下表现正常,而且有很好的成型性,加工出的产品表面光洁,易于染色和电镀。
因此它可以被用于家电外壳、玩具等日常用品。
常见的乐高积木就是ABS制品。
ABS树脂可及多种树脂配混成共混物,如PC/ABS、ABS/PVC、PA/ABS、PBT/ABS等,产生新性能和新的应用领域。
ABS管材的特点
(1)工作压力高:
在常温2OC情况下压力为1.OMpa。
(2)抗冲击性好:
在遭受突然袭击时仅产生韧性变形。
(3)本产品化学性能稳定、无毒、无味,完全符合制药、食品等行业的卫生安全要求。
(4)流体阻力小,其内壁光滑,转弯处呈圆弧形,因而流动磨擦力小,大大减少了系统流体阻力和泵的马力。
(5)使用温度范围大:
其使用的温度范围为-2O℃~+70℃。
(6)使用寿命长:
本产品在室内一般可用50年之久,如埋在地下或水中寿命会更长,且无明显腐蚀。
(7)安装简便密封性好:
本产品安装采用承插式连接溶剂粘接密封,施工简便,固化速度快、粘合强度高,避免了一般管道存在的跑、冒、滴、漏的现象。
(8)重量轻,节省投资:
ABS的重量是钢铁的1/7,因而减轻了结构重量,减轻了工人劳动强度,并降低了原材料的消耗,可大大节省工程投资
2.1.2塑件材料成形性能
1材料干燥温度在70℃-90℃,烘料时间2T-4T,待机生产烘料温度为10℃-20℃;
2.注塑成型温度即炮筒温度在180℃-250℃,最后一段温度应低于较前一段温度15℃左右;
3.注塑成型时料在炮筒的停留时间应不超过30分钟,超过30分钟易发黄、分解,应对炮筒里的残余料进行空射几次,5次为宜;
塑化时的压力应取中高压,速度应取中速偏上,背压应取适当为宜;
注射胶位段应采取多级段位控制,第一段射胶位要较小而速度要较慢为宜,因ABS料在成型时,易发生浇口位有气纹现象;
4.ABS料的成型飞边系数为0.04MM,即大于0.04MM的间隙就会产生飞边;
故模具排气尺寸要小于0.04MM;
生产时模具分型面易产生料屑,应及时清理;
模温在15℃-65℃范围内,生产大件产品时,定模模温应高于动模模温5℃为宜;
5.停机时要将炮筒里的余料射空,最好能用PP(1.5KG)或PE(1.5KG)料清理镙杆一次为宜;
开机前升温设定值,应低于正常生产温度的10℃左右,待实际温度度达到设定值再加升上去;
成型前应对物料的外观色泽、颗粒情况,有无杂质的进行检验,并测试其热稳定性,流动性和收缩率等指标。
第三章模具基本结构设计及模架选择
3.1确定成形方法
塑件采用注射成形法生产。
因为该产品设计为大批量生产,模具需较快的注塑效率,因此模具设计了一模二腔,塑件采用了侧浇口,故选用单分型面注射模(二板式注射模)结构。
3.2型腔布置
根据塑件的几何结构特点、尺寸精度要求、批量大小、模具制造难易、模具成本等确定型腔数量及其排列方式。
据设计要求可知,由于该塑件形状较简单,质量较小,且需要大批量生产所以模具选用一模一腔结构且平衡布置,采用单分型面注塑模,这样模具尺寸较小,制造加工方便,利于充满型腔,塑件质量高,生产效率高,塑件成本低。
其排列方法如下图3—1所示:
图3-1型腔布置示意图
3.3分型面设计
选择分型面时应遵循的原则:
分型面应选择在塑件外形的最大轮廓处;
将同心度要求高的同心部分放于分型面的同一侧,以保征同心度;
分型面作为主要排气面时,分型面应设于熔体料流的末端;
塑件开模后留在动模上;
分型面所产生的痕迹不影响塑件的外观,且易清除;
浇注系统和浇口的合理安排
推杆的痕迹不露在塑件的外观上
使塑件易于脱模
塑件分型面的选择应保证塑件的质量要求,本塑件的分型面有多种选择,图中分型面选择在塑件的下端面这样的选择使塑件的外表面可以在整体凹模型腔内成形,塑件大部分外表面光滑,仅在抽芯处留有分型面痕迹。
因此,塑件选择如图中所示的分型面。
图3-2分型面
3.4排气槽设计
当塑料熔体充填型腔时,热固性塑料在固化时会放出大量的气体,易阻塞缝隙,如果气体不能顺利地排出,塑件会由于填充不足而出现气泡,接缝式表面轮廓不清等缺陷,甚至气体受压而产生高温,使塑件焦化,所以必须开设专用排气槽排出气体。
通常排气
槽设计有多种方式,大多数都采用配合间隙排气的方式,由于此制件尺寸不大,利用分型面和推杆配合间隙排气即可。
3.5浇注系统设计
3.5.1主流道浇口套的选择
主流道是指浇注系统中从注射机喷嘴及模具接触处开始到分流道为止的塑料熔体的流动通道。
熔体从喷嘴中以一定的动能喷出。
由于熔体在料筒内已被压缩,此时流入模的空腔内,其体积必然要增大,流速也略为减小。
由于主流道的浇口套为标准件,考虑ABS的流动性较差,即主流道的浇口套的选择如下:
锥度为、mm、D=8mm、mm。
主流道断面尺寸:
主流道设在定模板上,并且位于模具的中心,及注射喷嘴
在同一轴线上。
表3-3主流道衬套中尺寸关系表
8
14
16
20
d
注射机喷嘴直径+(0.5~1)
D
及注射机定位孔间隙配合
SR
注射机喷嘴球面半径+(1~2)
3.5.3浇口设计
浇口不仅对塑件熔体的流动性和充模特征有关,而且及塑件的成形质量有着密切的关系。
侧浇口又称边缘浇口,侧浇口一般开设在分型面上,塑料熔体于型腔的侧面充模。
确定侧浇口的尺寸,应考虑它们对成型工艺的影响。
浇口的长度越长,浇口上的压力降的越大,浇口的厚度越厚,浇口封闭的时间越长;
填充速度越低,流动阻力越小。
侧浇口的尺寸计算的经验公式如下:
式中b——侧浇口宽度()
t——塑件在浇口处的壁厚()
A——型腔表面积(),采用UG软件计算得
k——塑料系数,k=0.6~0.9,在此ABS塑料取0.9
代入公式计算得:
=1.75mm
=0.58mm
由上计算可知,浇口的宽度、厚度及计算数据的相当,塑件采用侧浇口成型,其浇注系统如下图所示,主流道为圆锥形,上部直径及注塑机喷嘴相配合,分流道采用梯形截面流道,其梯形宽度为3~5.5㎜;
在此取经验值,取侧浇口宽度为2.0㎜,侧浇口厚度为1.0㎜。
图2-3分流道示意图
3.6脱模机构设计
塑件在模腔中成形后,便可以从模具中取下,但在塑件取下以前,模具必须完成一个将塑件从模腔中推出的动作,模具上完成这一动作机构称为脱模推出机构。
推出机构的组成:
第一部分是直接作用在塑件上将塑件推出的零件;
第二部分是用来固定推出零件的零件,有推杆固定板、推板等;
第三部分是用作推出零件推出动作的导向及和模时推迟推出零件复位的零件。
推出机构应使塑件脱模时不发生变形或损伤塑件的外观;
推力的分布依脱模阻力的大小合理合理安排;
推出机构的结构力求简单,动作可靠,不发生误动作,和模时要正确复位。
,推模力的计算要将塑件从模腔中推出必须克服推出所遇到的阻力,因此塑件脱模时必须有一个足够大的脱模力,脱模力可用下式计算:
式中——脱模力();
——型芯的脱模斜度;
取1°
——塑件包容型芯的面积();
由UG软件计算得
——塑件对钢的摩擦系数,一般取0.1~0.3;
——塑件对型芯的单位