洪晓明老师-医疗器械风险管理在体系各阶段的应用PPT文件格式下载.ppt
《洪晓明老师-医疗器械风险管理在体系各阶段的应用PPT文件格式下载.ppt》由会员分享,可在线阅读,更多相关《洪晓明老师-医疗器械风险管理在体系各阶段的应用PPT文件格式下载.ppt(78页珍藏版)》请在冰豆网上搜索。
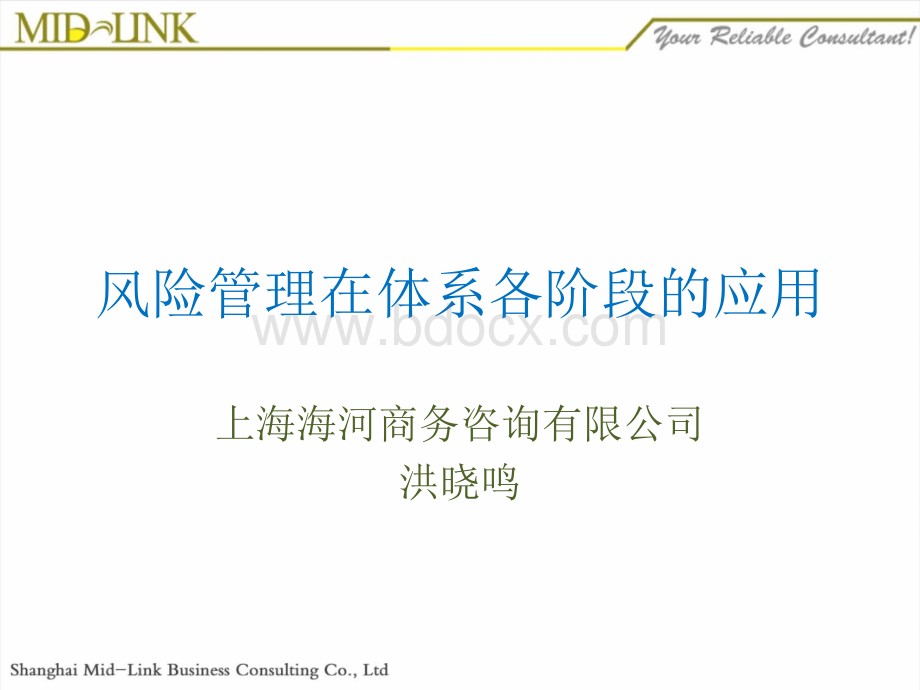
FMEA导入一般人对问题的思考方式和做事方法把关和预防的工作在前期做什么情况下我们不用这种思考方式?
时间限制强制命令执行麻木无知目的不良FMEA导入再来看看我们的期望能不能兑现?
一线作业人员设备维护人员检验人员作业指导书设备保养/点检计划控制计划/QC表严格把关,力争做到没有不合格品流到顾客手里。
FMEA导入应该怎么办?
一线作业人员设备维护人员检验人员作业指导书设备保养/点检计划控制计划/QC表让指令更精确,正确,完整。
并切实可操作。
让有经验的作业员能参与到指令制定。
让作业员完全了解指令,并遵照指令办事。
推荐的具体实施方法推荐的具体实施方法“FMEAFMEA”失效模式影响与分析失效模式影响与分析“FMEAFMEA”有什么了不起?
有什么了不起?
n宏观来讲,FMEA只是一种将我们一般逻辑思维方式的量化和程序化的方法。
n但其是目前最成功并应用最广泛的方法。
执行过程执行过程开发开发/改进过程改进过程FMEAFMEA的逻辑要点的逻辑要点列出各种潜在失效模式列出后果与原因判定失效模式的影响按影响程度排序,对影响大的进行改善对改善后情况进行评估对影响仍然大的严格控制观察/记录执行过程中的新失效模式。
了解/记录现实用户对质量的意见FMEAFMEA是什么?
是什么?
FMEA可以看作是有系统的一组活动,包括:
(a)辨认并且评估潜在的产品/工艺缺陷及该缺陷可能造成的影响;
(b)找出可以除去或减少潜在问题发生机会的方法;
(c)为整个过程提供文件资料。
FMEA是确定哪些设计或工艺必须要用才能使顾客满意的补充手段。
FMEAFMEA方法应用的要点方法应用的要点这是一套方法,不是一堆制式表格。
制式表格是推荐使用的工具;
这套方法是基于事实/经验而不是基于假设的;
FMEA过程是动态的,是持续不断的;
FMEA的动态过程,是企业知识库不断完善的过程。
FMEA应用的好坏与逻辑的严密体现了能力与经验产品产品/过过程的概念程的概念FMEAComponent部件部件System系统系统Sub-System子系统子系统过程过程FMEAAssembly装配装配Manufacturing制造制造System系统系统Component部件部件Sub-System子系统子系统System系统系统Component部件部件Sub-System子系统子系统机械机械FMEAFMEAFMEA类型(因应用环节不同而分)类型(因应用环节不同而分)设计设计FMEAFMEAFMEA的作用的作用从控制计划制定从控制计划制定FMEA导入DFMEA/PFMEA控制计划控制计划CC&
SC关键特性和重要特性清单关键特性和重要特性清单如何确定如何确定CC&
SC?
CC&
DFMEAYCYSS=58O=410S=9/10PFMEACCSCS=9/10S=58O=410谁来做谁来做FMEA?
FMEA?
设计FMEA(DFMEA):
应该是由负设计责任的产品工程师来做。
过程FMEA(PFMEA):
应该由制造工艺部门的工程师来做。
FMEA的更新由责任单位负责(产品,制造)。
什么时候做什么时候做FMEA?
DFMEA在设计概念前或决定时起动在该项目产品开发的各个阶段进行更新PFMEA在可行性分析前或开始时起动要求何时要求何时“阶段性阶段性”完成完成?
FMEA是动态的文档FMEA阶段性“完成”也针对特定项目的产品或过程DFMEA:
v基本上,在生产用图纸正式发放用于模具开发前应完成v要求是:
产品设计可以发布用于生产PFMEA:
v基本上,在生产用工装制造前完成v要求是:
所有的生产都被考虑到,所有的特殊特性都被适当安排,以及控制计划已经完成谁是谁是FMEAFMEA的顾客的顾客?
所有的FMEA:
最终用户售后服务DFMEA与设计有关的行动与制造有关的过程PFMEA:
下一工序或下游的制造或装配FMEA介绍介绍-失效模式失效模式潜在失效模式所谓潜在失效模式是指系统,子系统或零部件有可能未达到或未完成预期功能.FMEA介绍介绍-失效模式失效模式常见的失效模式1操作过程中的失效2遵从指示操作的失效3遵从指示停止操作的失效4过早的操作FMEA-潜在失效的起因潜在的失效起因是指一个设计弱点的迹象,其结果就是失效模式识别,描述失效的起因基于失效的影响和严重度给出缓解的建议失效起因识别的越精确,失效模式的影响就越清晰FMEA-潜在失效的后果潜在失效的后果是失效模式对操作,功能或系统状态方面的影响一个失效后果,可以是一个或者多个失效模式引起的FMEA-严重度(S)严重度是对一个已假定失效模式的最严重影响的评价等级确定级别要根据经验、要小组讨论,大家形成共识.对产品/系统的影响,假设零件(分析)装入整体运行可制作自己的FMEA中严重度分级,但要遵守大原则:
CC(关键性特性)910级SC(重要特性)58级(5级以上均要措施对策,5级以下可以考虑。
)FMEA-严重度分级后果后果顾客后果客后果等等级后果后果制造制造/组装后果装后果不符合安全或法规要求潜在失效模式影响产品安全使用和/或包含不符合政府法规情形。
失效发生时无警告。
1010不符合安全或法规要求可能危及作业员(机器或组装)而无警告潜在失效模式影响产品安全使用和/或包含不符合政府法规情形。
失效发生时有警告。
99可能危及作业员(机器或组装)但有警告主要功能丧失或降级丧失基本功能(产品不能使用,不影响产品安全性)88严重破坏产品可能必须要100%丢弃,生产线停止并停止装运主要功能降级(产品可使用,但是性能层次降低)77重大破坏生产使用一部分(少于100%)需被丢弃。
主要过程中出现的偏差(生产线速度降低或需增加人力)。
次要功能丧失或降级次要功能丧失(产品可使用,但是适用性/便利等功能失效)66中等破坏生产使用的100%需要进行下生产线返工,然后可被接受次要功能降低(产品可使用,但是适用性/便利等功能降低)55生产使用的一部分需要进行下生产线返工,然后可被接受烦扰的小问题产品可使用,但是外观或噪音等项目不合格,并且大多数(75%)顾客会发现这些缺陷。
44中等破坏生产使用100%需要在其使用前进行生产线的工站上返工产品可使用,但是外观或噪音等项目不合格,并且许多(50%)顾客会发现这些缺陷。
33生产使用的一部分需要在其使用前进行生产线的工站上返工产品可使用,但是外观或噪音等项目不合格,并且少数(25%)有辨识能力的顾客会发现这些缺陷。
22次要破坏对过程,作业或作业员带来轻微的不便没有影响没有可识别的后果11没有影响没有可识别的影响严重度(S)S=1:
外观缺陷S=2:
轻微的穿刺部位并发症S=3:
显著延长手术时间S=4:
显著偏离治疗目的S=5:
急性或亚急性血栓S=6:
死亡FMEA-频度(O)发生率的分级着重在其含义而不是数值。
频度是指在设计的寿命中某一特定失效的起因发生的可能性可以分“1”到“10”级来估计发生率的大小,只有导致相应失效模式的发生,才能考虑发生率分级。
FMEA-频度分类等级失效可能性失效可能性起因起因发生可能性生可能性定定级很高100件/每千件每10件中有1件10高50件/每千件每20件中有1件920件/每千件每50件中有1件810件/每千件每100件中有1件7中等2件/每千件每500件中有1件60.5件/每千件每2,000件中有1件50.1件/每千件每10,000件中有1件4低0.01件/每千件每100,000件中有1件30.001件/每千件每1,000,000件中有1件2很低通过预防控制消除失效1FMEA-现行设计控制列出预防措施,设计确认/验证或者其它活动,这些活动的完成或承诺将确保该设计对于所考虑的失效模式来说是充分的.FMEA-现行过程控制现行过程控制是叙述制程方法现行过程控制是叙述制程方法,用来预防可用来预防可能扩大的失效模式和探测出失效模式的发能扩大的失效模式和探测出失效模式的发生。
生。
FMEA-现行过程控制过程控制方法过程控制方法:
预预防防(优先采用)优先采用)侦测侦测查出失效模式。
查出失效模式。
针对参数选择不当的控制的方法可以是:
11)试验;
)试验;
22)以往经验;
)以往经验;
33)变换方法等)变换方法等对操作或达不到工艺参数要求时的控制方法可以是:
对操作或达不到工艺参数要求时的控制方法可以是:
1)检验(首检)检验(首检/巡检巡检/终检)终检)探测度(D)探测度是结合了列在设计控制中最佳的探测控制等级.以统计原理为基础的抽样检测以统计原理为基础的抽样检测是有效改善是有效改善探测度的措施探测度的措施探测可能性准准则:
设计控制探控制探测可能性可能性等等级几乎不可能设计控制将不能和/或不可能找出潜在的原因/机理及后续的失效模式,或根本没有设计控制10很微小设计控制只有很微小的机会能找出潜在的原因/机理及后续的失效模式9微小设计控制只有微小的机会能找出潜在的原因/机理及后续的失效模式8非常低设计控制只有非常低的机会能找出潜在的原因/机理及后续的失效模式7低设计控制只有较低的机会能找出潜在的原因/机理及后续的失效模式6中等设计控制有中等的机会能找出潜在的原因/机理及后续的失效模式5中上设计控制有中上的机会能找出潜在的原因/机理及后续的失效模式4高设计控制有较高的机会能找出潜在的原因/机理及后续的失效模式3很高设计控制有很高的机会能找出潜在的原因/机理及后续的失效模式2几乎肯定设计控制几乎肯定能找出潜在的原因/机理及后续的失效模式1可探可探测的机率的机率准准则:
过程控制探程控制探测可能性可能性等等级探探测可能性可能性没有探测的可能没有现行的过程控制,不能探测或不可分析10几乎不可能在任何阶段不太可能探测失效模式和/或错误(原因)不容易被探测到(如,随机的审核)9很微小后加工问题探测操作人员通过视觉/触觉/听觉在后加工进行失效模式探测8微小从源头进行的问题探测操作人员通过视觉/触觉/听觉的方式进行工位上的失效模式探测或通过使用特性测量(通/止,手工扭转检查/点击扳手等)进行后加工时的失效模式探测。
7非常低加工后问题探测操作人员通过使用各种测量进行后加工失效模式探测或操作人员通过使用各种特性测量(通/止,手工扭转检查/点击扳手等)进行工位上的失效模式探测。
6低从源头进行的问题探测由操作人员通过使用各种测量进行后加工失效模式或错误(起因)探测或由工位上的由自动化的控制设备探测不符合零件并通过(指示灯,鸣声)通知操作人员。
在作业前准备和首件检查时进行测量(仅用于探测作业前准备的起因)5中等加工后问题探测由自动化控制进行后加工失效模式探测。
这种自动化控制能探测不符合零件并锁定零件以防止进一步的操作。
4中上从源头进行的问题探测由自动化控制进行工位上失效模式探测。
这种自动化控制能探测不符合零件,并自动锁定工位上的零件以防止进一步的操作。
3高错误探测和/或问题预防由自动化控制进行工位上错误(起因)探测,这种自动化控制能探测错误和预防不符合零件的制造。
2很高探测不可行:
错误预防错误(起因)预防是通过固定设施设计,机械设计或零件设计而产生的。
通过过程或产品设计进行防错而避免制造不符合零件。
1几乎肯定风险顺序数(RPN)RPN是产品严重度(S),频度(O)