化工锅炉筑炉方案DOCWord文件下载.docx
《化工锅炉筑炉方案DOCWord文件下载.docx》由会员分享,可在线阅读,更多相关《化工锅炉筑炉方案DOCWord文件下载.docx(10页珍藏版)》请在冰豆网上搜索。
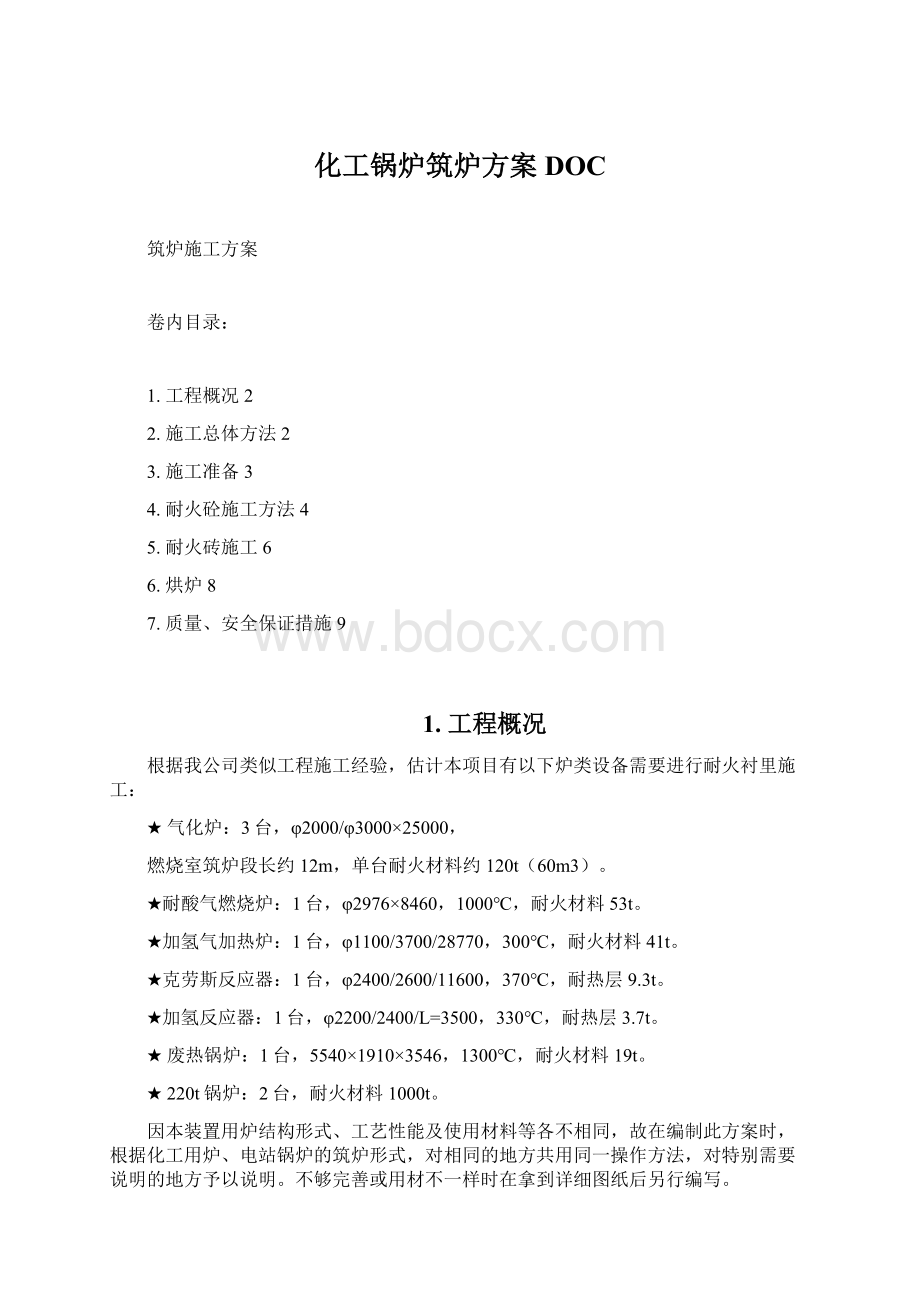
燃烧室筑炉段长约12m,单台耐火材料约120t(60m3)。
★耐酸气燃烧炉:
1台,φ2976×
8460,1000℃,耐火材料53t。
★加氢气加热炉:
1台,φ1100/3700/28770,300℃,耐火材料41t。
★克劳斯反应器:
1台,φ2400/2600/11600,370℃,耐热层9.3t。
★加氢反应器:
1台,φ2200/2400/L=3500,330℃,耐热层3.7t。
★废热锅炉:
1台,5540×
1910×
3546,1300℃,耐火材料19t。
★220t锅炉:
2台,耐火材料1000t。
因本装置用炉结构形式、工艺性能及使用材料等各不相同,故在编制此方案时,根据化工用炉、电站锅炉的筑炉形式,对相同的地方共用同一操作方法,对特别需要说明的地方予以说明。
不够完善或用材不一样时在拿到详细图纸后另行编写。
2.施工总体方法
2.1气化炉
★气化炉为直立式圆筒炉,耐火衬里位于燃烧室内,有顶部穹顶、中间筒体、底部炉座三种衬里形式,耐火衬里共有4层:
迎火层(砖)、中间过渡层(两层,砖)、外层(耐热纤维块),在拐角过渡处局部有耐火混凝土浇注料。
★筑炉时按照由外到里、由下而上的程序,材料堆放在框架平台和钢平台上,人由下部管口进入,材料由上部管口进入;
设置两台卷扬机作控制操作平台、提升斗用。
首先在筒体内搭设特殊脚手架(此脚手架由一根自上而下穿过整个设备的可旋转的钢管为骨架中轴,其上设置有可拆装的钢平台),然后开始自底部施工锥形封头处的耐火砼及砌体,逐渐向上延伸至顶部封头,再先支模、施工穹顶耐火砖,最后由顶部大盖处进行耐火砼的浇注(对于留口处需进行二次浇灌)。
2.2废热锅炉、加氢气加热炉
◆废热锅炉为立式箱形炉(中间有变径或三通),进料、进人均从顶部三通处进,进人时设置直爬梯;
加氢气加热炉为圆形炉、中间有变径。
◆废热锅炉砼、砖、毡施工;
在外部需搭设人员通道和卸料平台;
内部不搭设脚手架,可用可拆卸式平台,平台不得直接放在砌体上,立柱下应垫木板等。
◆加氢气加热炉需要在内部搭设脚手架。
本工程的操作平台为环形,同时作卸料平台。
该平台的外径为扣除内衬后的筒径再扣除100mm的活动空间;
该平台的内径为提升斗的外径减去100mm活动空间;
中间拱和顶部拱均制作胎膜(强度和刚度足以保证静载和活动荷载),在支设牢固后进行施工;
中间拱在胎膜上施工,顶拱在拱下施工;
施工时必须严格按照预砌筑的砖位置进行砌筑。
2.3克劳斯、加氢反应器
●该型设备为圆筒设备,中间有变径,因内部介质腐蚀性强,可能选择耐酸耐火砼,一般为水玻璃耐热砼;
●水玻璃模数为2.6-2.8,水玻璃耐热砼作内衬时必须经酸化处理;
●材料拌合分为搅拌、闷料、再搅拌三个工序;
第一次加入所需磷酸的一半,闷料16小时,拌合料加入促凝剂后应在20-30分钟内用完。
2.4酸性气燃烧炉
该型炉为卧式圆筒炉,内衬耐火材料,在筒壁、顶上设有人孔、法兰孔,均采用从两侧进料;
在两侧外部搭设人员通道和卸料平台。
2.5200t锅炉
详见锅炉方案。
3.施工准备
3.1施工前将所有的耐火材料准备齐全,并按照使用的先后顺序放在库房内,以利防水防潮。
3.2对所有的耐火材料均作外形几何尺寸检查(除不定型耐火材料)及对材料质量有怀疑的在进场后进行复检。
3.3对到场的不定型耐火材料作相应试验后按照施工配合比作试块,到龄期后送到耐火材料检测中心检测其性能是否符合设计要求,以确定正式施工配合比后报设计、监理、业主备案。
3.4对所需筑炉的衬里设备在安装后,由安装与筑炉单位办理交接验收手续,必要时可请建设、监理、设计等单位到场共检。
3.5根据工程的需要准备相应的施工设备、工机具、周转材料、施工人员、临时设施等。
3.6组织参与炉窑砌筑施工的管理人员、技术人员、质量检查人员、施工生产人员等充分熟悉施工工艺、质量标准、安全注意事项等,始终将安全、质量、进度放在施工生产的第一位。
3.7建立质量检查组织机构、质量保证体系,加强过程检查,力争在施工过程中排除质量隐患。
3.8准备好脚手架、提升装置、卸料平台、临时用水、用电等设施。
3.9准备好施工计量、检测工具(经市级以上的检测单位检测合格)。
4.耐火砼施工方法
4.1施工程序
焊接V或Y型锚固件→除锈→刷沥青漆→中心线找正→模板支设→耐火浇注料浇注或捣找料施工→养护、拆模→烘炉
4.2施工方法
4.2.1焊接V或Y型锚固件的间距约为200×
200mm,呈错列形式布置,方向应成行互换(锚固件焊接应结实);
锚固件在焊接成型后的高度应小于耐火砼厚度10-20mm。
4.2.2对需衬里浇筑的部位,应进行除锈。
除锈等级为ST3或Sa2级,并清除浇筑部位的浮尘、铁锈、油污等杂物。
4.2.3对除锈部件外简体及锚固件均匀满涂刷1~2mm厚的沥青。
4.2.4在筒体的上部和下部或前后两端找准中心点,并在一端用红颜色的标识色标出中心点的位置。
在另一端用钢筋焊上“一”字型的横杆,并标出中心点的位置。
4.2.5制作扣除耐热砼厚度(筒壁内径)为外径的木模板各二组,每组可分为两到四片,每上升一层模板时,都应校检一次中心线是否准确,两边的浇注料厚度是否一致。
外环的模板表面应粗糙,内环的表面应光滑(右用三合板、镀锌铁皮作为面料);
亦可采用钢制整体模板(进筒内组装),利用卷扬机工倒链进行提升,每次提升高度在300-500mm,提升的时间控制在砼终凝后。
模板的整体强度和刚度不得因砼浇筑、提升等因素而变形;
模板的下部支撑应坚固,不得因静载、施工荷载而变形;
模板的形式必须与设计的形式相符,厚度必须达到设计要求。
4.2.6浇注料浇注前,木模板表面应浇水湿润,对免模板吸水太多,影响浇注料的强度。
4.2.7耐火砼的搅拌及浇注应满足下列要求:
●骨料应于使用前4h洒水闷料;
对于用非水类液态材料作胶结料(如磷酸、水玻璃溶液),根据各种材料对闷料时间的不同要求进行闷料,如磷酸耐火砼需用50%浓度16%的重量的磷酸溶液进行闷料24小时;
●严格控制浇注料的水灰比,以防水灰比过大造成强度损失,对于小于60mm厚的浇注料可用人工捣固、拍打及捣打方式进行,对于厚度大于60厚可采用机械振捣、人工捣打等方式进行施工;
●浇注料的用水一定要清净,不得含有油污、有机物及碱性物质;
●每次搅拌好的不定形耐火材料应在30分钟或规定时间内用完,未用完的不得再加胶结料、水或促凝剂拌制继续使用;
●不定形耐火材料应尽量连续施工,若中途有特殊情况(相隔时间超过先浇层砼的初凝时间)中途中断,应在已灌砼表面打毛并清扫干净,用水淋湿后,涂抹1~2m/m厚的细浇注料或胶泥后,继续浇注;
●不定形耐火材料的捣固一定要细致、紧密,使不定形耐火材料密实;
●不定形耐火材料浇筑后,用水养护的砼应在初凝后每隔0.5~1小时对其喷水养护,使其表面始终保持潮湿。
对于不需浇水养护的应覆盖好;
●对于整体面积较大,设计未考虑留设膨胀缝位置,经请示设计单位认可后,用手持切割机切割小缝后用硅酸铝纤维毡或其它材料填充;
●球拱处制作胎膜后,在下部支撑支设牢固,从端部法兰孔、人孔处进行浇注料浇灌,不停敲打胎膜,机械振捣或人工捣固;
若为捣打料时不需支设模板。
5.耐火砖施工
5.1施工说明
本工程的耐火砖一般为硅藻土保温砖、粘土质、高铝质、刚玉质等材质,耐火砖与耐火泥一定要配套使用,不得混用或滥用。
5.2施工程序
选砖→预排→磨切→砌筑→质量检查→缺陷修补→烘炉→交工
·
耐火泥在使用前24小时,应将耐火泥按生熟料分别计量,配制好后,放入灰槽中闷料。
在闷料过程中要经常进行搅拌,使气泡排出。
一般1~2小时应彻底搅拌一次。
制作比设备衬砌耐火砖后的内径小10mm的半圆拱型胎,模板的骨架应用40×
70mm的木方,辅助支撑可用30×
50mm的木方,拱型面使用三合板,以保证环向的平整度(用于卧式设备)。
需浇筑耐火浇注料的地方,施工方法同不定形耐火材料的施工方法。
隔热、耐火砖的灰浆应饱满;
砌体上挤出的灰浆应及时清理干净。
砌筑时,先从底部或密封端开始;
卧式设备应先砌下半圆(约200左右),再砌筑耐火砖。
耐火砖、隔热砖之间均应错缝砌筑;
每次砌筑长度约460mm左右;
砌完下半圆之后,即支设半圆拱型胎砌筑上半圆,砌筑顺序与下半圆相反,先砌筑高铝砖,再砌筑粘土质隔热砖。
砌完一段后继续往后退,同时检查前一环的砖的圆弧度及中心线;
每层每环砌体均应有2~4块锁砖,锁砖打进砌体时,其表面应垫上木板或木方。
立式设备先铺设耐火纤维,砌筑隔热砖后再砌筑耐火砖,每砌一层耐火砖后应检查一次中心线有无偏移。
耐火砖需加工时,严禁用手工加工,应用磨砖机或切砖机加工,然后才能砌筑。
无论是环缝还是纵缝,高铝砖缝厚均宜为2mm,超出2mm的砖应重新选砖后,再砌筑。
粘土质隔热砖的砖缝为3mm。
耐火砖加工面和有缺陷的表面不得朝向火炉内侧。
炉墙的耐火砖不得使用砖长1/3以下的断砖,每层大于1/3的断砖数量不宜超过三块。
断砖时,应使用切砖机进行切割,不得使用手锤直接断砖。
砌砖时的留岔应是台阶形,内侧墙应每隔九层砖向外侧墙伸出1/2砖长的拉砖,每段砖墙不得少于3块。
砌筑拉钩砖时,相对的两块拉钩砖互相对齐,拉钩与砖之间的缝隙应用碎硅酸铝耐火纤维填充密实。
左右墙每隔一段距离,内外侧砖墙均应设置一道膨胀缝,膨胀缝的内外层之间的位置应错缝1/2砖长以上。
拱砖的砌筑
①拱的拱脚斜面在同一平面上,拱两边拱脚砖的斜面形成的夹角与弧形拱的角度一致,弧形拱两端拱脚砖跨度也应一致。
②拱脚砖的后面应用坚硬的耐火砖顶紧,拱胎要支立牢固,无松动现象。
③当弧形拱顶砖筑时,应从两边拱脚同时向拱顶中心进行,同时应错缝砌筑;
错缝砌筑时,可从拱脚砖开始一趟一趟往中心砌,也可在两端同时砌两环同样配比的砖环,然后从两环拉线砌筑,砌筑过程中,要经常用靠尺和塞尺检查,控制拱砖砌筑的平整度、圆弧度和砖缝。
④烟道拱和左右墙应按图纸间距设置δ=38mm的膨胀缝。
5.3膨胀缝的设置
膨胀缝内应用硅酸铝纤维毡填满塞紧。
膨胀缝的位置、厚度、尺寸一定要按图纸设计施工,不得随意改动。
砖的切削面不得朝向膨胀缝。
膨胀缝应上下整齐,缝内无泥浆及砖渣等硬物、杂物。
拱顶膨胀缝与墙上、烟道、底部支柱的膨胀缝间距均应一致。
5.4硅酸铝纤维毡的铺设
硅酸铝纤维毡在金属体的铺设处刮满高温胶泥后,用手压紧压平硅酸铝纤维毡,并将毡之间的缝隙填密实;
每层毡之间的纵横缝均应错开,错缝间距不小于150mm。
6.烘炉
6.1必须在安装及砌筑工作全部完成经检查合格后才允许进行烘炉。
6.2烘炉前应关闭好全部门类,开启烟囱挡板使其自然通风,不小于10天。
6.3烘炉前必须详细检查炉膛、炉顶及烟囱等部位,并应进行清扫;
同时检查煤气管和各种蒸汽管上的阀门是否关闭严密,开闭是否灵活,烟囱挡板与门类是否完善,转动灵活,热电偶与测压计是否装好,并校对准确,经检查合格后,方可开始烘炉。
6.4烘炉前炉管内必须先通入蒸汽或软水,不允许在炉管内没有蒸汽或软水的情况下开始点火烘炉。
6.5烘炉时在炉管内先通往蒸汽进行烘烤,使炉膛温度升到100~120℃在此温度下维持3天然后改用煤气烘炉。
6.6在烘炉的2~3小时内烟囱挡板只准开放烟囱的1/3左右,待炉膛温