注射模具设计说明书Word文件下载.docx
《注射模具设计说明书Word文件下载.docx》由会员分享,可在线阅读,更多相关《注射模具设计说明书Word文件下载.docx(24页珍藏版)》请在冰豆网上搜索。
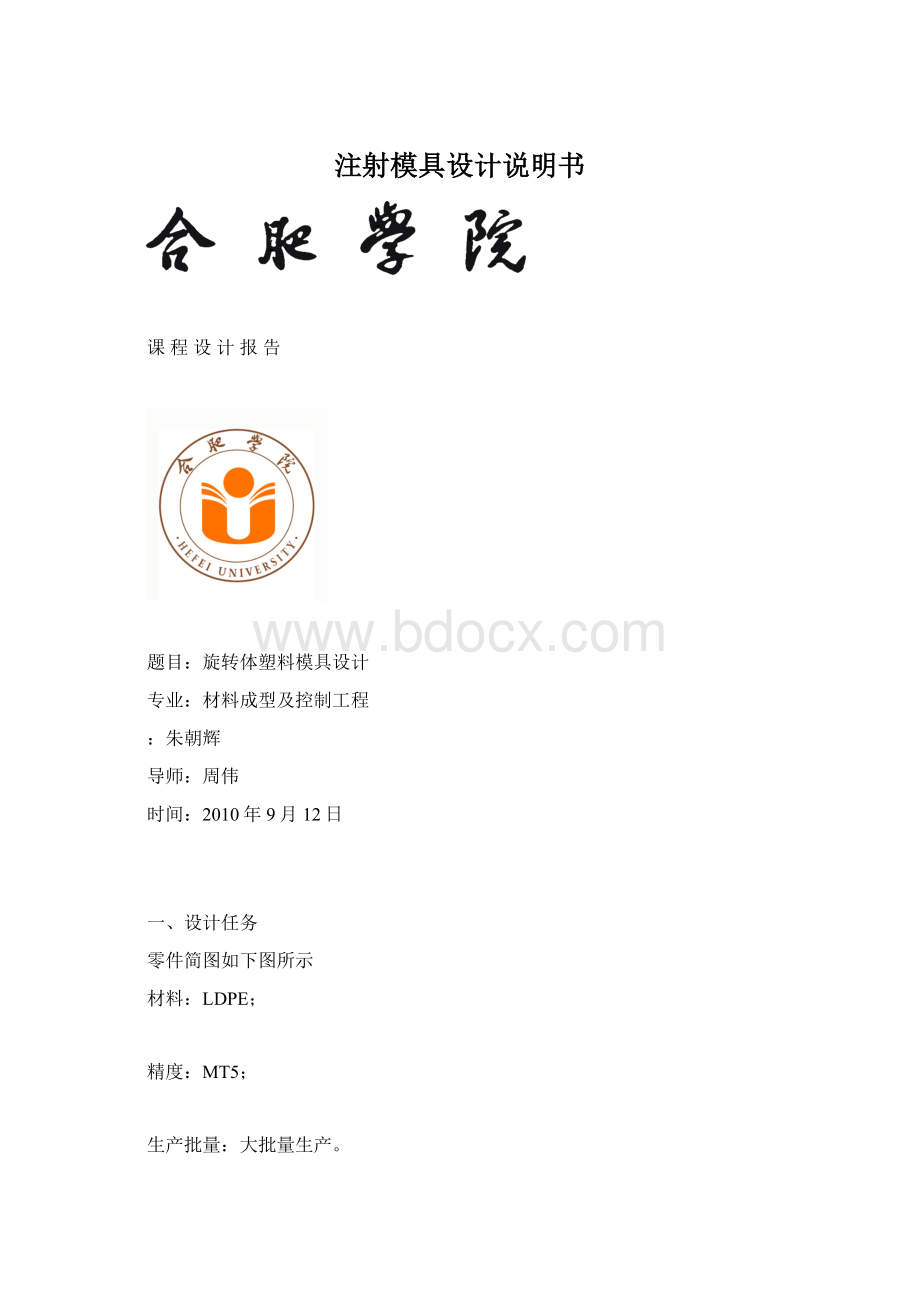
2.1、塑件的分析
(1)外形尺寸该塑件的壁厚为5mm,塑件的外形尺寸较大,塑件的熔体流程较长,但采用注射成型也是可行的
(2)精度等级该塑件的精度等级统一给定位MT5,精度等级一般,因此对模具的精度要求也是一般。
(3)脱模斜度LDPE的成型收缩率较小,收缩率约为1.02,参考文献[1]表2-10选择塑件上的凸凹模的脱模斜度统一为35’。
2.2、LDPE的性能分析
(1)低密度聚乙烯(LDPE)通常是以乙烯为单体,在98.0~294MPa的高压下,用氧或有机过氧化物为引发剂,经聚合所得的聚合物,密度为0.910~0.9259/cm3。
结晶度较低,分子量一般5~50万,它是一种乳白色呈半透明的蜡状固体树脂,无毒。
(2)软化点较低,超过软化点即熔融,其热熔接性、成型加工性能很好,柔软性良好,抗冲击韧性、耐低温性很好,可在-60℃~-80℃下工作,电绝缘性优秀(尤其是高频绝缘性),LDPE的机械强度较差,耐热性不高,抗环境应力开裂性、粘附性、粘合性、印刷性差,需经表面处理,如化学侵蚀、电晕等处理后方可改进其粘合性、印刷性。
(3)吸水性很低,几乎不吸水,化学稳定性优秀,如对酸、碱、盐、有机溶剂都较稳定。
对CO2、有机性臭气渗透性大,但对水蒸汽、空气的渗透性差。
(4)易燃烧,燃烧时有似石蜡昧;
在日光和热作用下容易老化降解而变色,由白转黄转褐色,最终呈黑色,且性能下降或龟裂,若加入一定量的抗氧剂、紫外线吸收剂等可改善性能、在化学交联剂或高能辐照下交联,可提高软化点、耐温性、刚度、耐溶剂性等。
(5)低密度聚乙烯(LDPE)适合热塑性成型加工的各种成型工艺,成型加工性好,如注塑、挤塑、吹塑、旋转成型、涂覆、发泡工艺、热成型、热风焊、热焊接等。
(6)LDPE主要用途是作薄膜产品,如农业用薄膜、地面覆盖薄膜、农膜、蔬菜大棚膜等;
包装用膜如糖果、蔬菜、冷冻食品等包装;
液体包装用吹塑薄膜(牛奶、酱油、果汁。
豆腐、豆奶);
重包装袋,收缩包装薄膜,弹性薄膜,内衬薄膜;
建筑用薄膜,一般工业包装薄膜和食品袋等。
LDPE还用于注塑制品,如小型容器、盖子、日用制品、塑料花、注塑一拉伸一吹塑容器。
医疗器具,药品和食品包装材料、挤塑的管材、板材,电线电缆包覆,异型材、热成型等制品;
吹塑中空成型制品,如食品容器有奶制品和果酱类,药物、化妆品、化工产品容器、槽罐等。
2.3、LDPE的注射成型过程及工艺参数
2.3.1注射成型过程
1)成型前准备对LDPE的色泽、粒度和均匀度进行检测,并进行成型前的干燥处理。
2)注射过程塑料再注射机料筒内经过加热、塑化达到流动状态后,由模具浇注系统进入模具型腔成型,其过程可分为充模、压实、保压、倒流和冷却五个阶段。
3)塑件的后处理处理的介质为空气,处理温度为60~70,处理时间为20~25S。
2.3.2注射工艺参数
依据文献[1]P63表3-1常见塑料的注射工艺得到LDPE的注射工艺参数如下表所示:
干燥处理
料筒温度
螺杆转速
喷嘴结构
模具温度
注射
温度
时间
后部
中部
压力
__
140~160
170~200
直通式
30~55
60~100
1~5
保压
降温固化时间
成型周期
注射机类型
螺杆结构形式
40~50
15~60
40~140
螺杆式
三、拟定模具的结构形式
3.1分型面位置的确定
分型面是指分开模具取出塑件和浇注系统凝料的可分离的接触表面。
一副模具根据需要可能有一个或两个以上的分型面,分型面可以是垂直于合模方向,也可以与合模方向平行或倾斜,我们在这里选用与合模方向倾斜。
(1)分型面的形式:
分型面的形式与塑件几何形状、脱模方法、模具类型及排气条件、浇口形式等有关,我们常见的形式有如下五种:
水平分型面、垂直分型面、斜分型面、阶梯分型面、曲线分型面。
(2)分型面的选择原则:
a)便于塑件脱模:
Ⅰ、在开模时尽量使塑件留在动模内
Ⅱ、应有利于侧面分型和抽芯
Ⅲ、应合理安排塑件在型腔中的方位;
b)考虑和保证塑件的外观不遭损坏
c)尽力保证塑件尺寸的精度要求(如同心度等)
d)有利于排气
e)尽量使模具加工方便
(3)对于本次设计,分型面的选取如下图所示:
图3-1
3.2型腔数量和排列方式的确定
(1)型腔数量的确定该塑件采用的精度为5级,且为大批量生产,可采用一模多腔的形式。
同时,考虑到塑件的尺寸、模具结构尺寸的大小关系,以及各种成本费等因素,初步定为一模一腔的形式。
(2)模具结构形式的确定从上面的分析可知,本模具设计为一模一腔的形式,根据塑件的结构形状,推出机构拟采用推杆推出的形式。
浇注系统设计时,流道采用对称平衡式,浇口采用侧浇口,开设在分模面上。
为取出冷凝料,本次设计采用拉料杆取出凝料。
综合分析可确定选用带推杆的单分型面注射模。
3.3注射剂型号的确定
(1)注射量的计算
当加载的材料为PE时,通过三维软件进行质量查询,可得出如下的信息:
图3-2
则有塑件的体积为:
若取LDPE的密度为,则有塑件的质量为:
(2)浇注系统凝料体积的初步估算
浇注系统的凝料在设计之前是不能确定准确的数值,,但可以根据经验按照塑件体积的0.2~1倍来估算。
由于本次设计采用的流道简单并且较短,因此浇注系统的凝料按塑件体积的0.2倍计算,故一次注入模具型腔塑料熔料的总体积为
(3)选择注塑机
根据上面计算得出的一次注入模具型腔的塑料的总体积为,并参考文献[1]P95式4—18有
根据以上的计算,初步选定公称注射量为,注射机的型号选定为XS—ZY—500卧式注射机,其主要技术参数如下表所示:
标称注射量/
500
模板的最大厚度/mm
450
螺杆直径/mm
65
模板的最小厚度/mm
300
合模力/N
模板尺寸
750×
870
注射压力/MPa
104
拉杆空间/mm
650×
550
注射行程/mm
490
合模方式
液压机械
螺杆转速/(r/mm)
0~47
电机功率/KW
22
模板最大行程/mm
700
定位圈尺寸/mm
150
喷嘴球半径/mm
18
喷嘴孔直径/mm
7.5
注射方式
最大成型面积/
1000
注射时间/s
2.7s
(4)注射机相关参数的校核
1)注射压力的校核
该项工作是校核所选注射机的公称压力P能否满足塑件所成型时需要的注射压力P0,其值一般为60~100MPa,我们这里选80MPa。
注射压力的安全系数为
=1.25~1.4,这里我们取为=1.3,则有:
,所以注射机压力合格。
2)锁模力的校核
锁模力是指注射机的锁模机构对模具所施加的最大夹紧力,当高压的塑料熔体充填模腔时,会沿锁模方向产生一个很大的胀型力。
为此,注射机的额定锁模力必须大于该胀型力,即:
=A×
P
F—注射机的额定锁模力(N);
P—模具型腔内塑料熔体平均压力(MPa);
一般为注射压力的0.2~0.4倍,通常取20~40MPa。
我们这里选P=30MPa。
A—塑料和浇注系统在分型面上的投影面积之和(mm2)
塑件在分型面上的投影面积为:
浇注系统在分型面上的投影面积为:
则有塑件和浇注系统在分型面上的投影面积之和为:
模具型腔的内压力P通常取为注射压力的0.2~0.4倍,大致范围为16~32MPa,这里取为30MPa。
则模具型腔内的涨型力为:
P=32012.928×
30N=960387.84.32N=960.387KN<
3500KN
符合要求。
四、浇注系统的设计
4.1主流道的设计
所谓注射模的浇注系统是指从主流道的始端到型腔之间的熔体流动通道。
其作用是使塑件熔体平稳而有序地充填到型腔中,以获得组织致密、外形轮廓清晰的塑件。
因此,浇注系统十分重要。
而浇注系统一般可分为普通浇注系统和无流道浇注系统两类。
我们在这里选用普通浇注系统,它一般是由主流道、分流道、浇口和冷料穴四部分组成,如图四所示:
主流道是连接注射机喷嘴与分流道的一段通道,通常和注射机喷嘴在同一轴线上,断面为圆形,带有一定的锥度,其主要设计点为:
1)主流道尺寸
主流道的小端直径:
;
主流道的球面半径为:
主流道锥角:
取;
主流道长度:
取L=20mm;
主流道的大端直径:
2)主流道衬套的形式
由于主流道入口处与注射机喷嘴反复接触,极易损坏,对材料的要求比较高,因而主流道设计为浇口套,采用T10A,热处理为50HRC-55HRC
4.2冷料井的设计
冷料穴一般位于主流道对面的动模板上。
其作用就是存放料流前峰的“冷料”,防止“冷料”进入型腔而形成接缝;
此外,在开模时又能将主流道凝料从定模板中拉出。
冷料穴的尺寸宜稍大于主流道大端的直径,长度约为主流道大端直径。
冷料穴的形式有三种:
一种是与推杆匹配的冷料穴;
二种是与拉料杆匹配的冷料穴;
三种是无拉料杆的冷料穴。
我们这里选用与推出杆匹配的倒锥形冷料穴,其结构如图所示:
图4-1
4.3分流道的设计
4.3.1分流道的布置形式
分流道就是主流道与浇口之间的通道,一般开设在分型面上,起分流和转向的作用。
多型腔模具必定设计分流道,单型腔大型腔塑件在使用多个点浇口时也要设置分流道。
本次设计采用两个侧交口,所以也要有分流道。
4.3.2分流道的截面形状
通常分流道的断面形状有圆形、矩形、梯形、U形和六角形等。
为了减少流道内的压力损失和传热损失,提高效率,我们这里就选用圆形分流道。
为了让分流道要能满足良好的压力传递和保持理想的填充状态,使凝料熔体尽快地分配到型腔,因此,采用如图4-1所示平衡式分流道结构:
4.3.3分流道的截面尺寸
因为各种塑料的流动性有差异,所以可以根据塑料的品种来粗略地估计分流道的直径。
由参考文献[1]P94表4-7常用塑料的分流道直径推荐值表,取分流道的直径为8mm。
4.3.4分流道的长度
因为两浇口点之间的距离为46mm,所以取分流道的长度为34mm。
4.3.5凝料体积
分流道长度:
L=34mm。
分流道截面积:
A=
凝料体积:
L×
A=50.24×
34=1708.16
4.3.6校核剪切速率
由参考文献[1]P95表4-8查的注射时间为:
t=2.5S
分流道体积流量:
剪切速率:
该分流道的剪切速率处于浇口主流道与分流道的最佳剪切速率~之间,所以分流道内的熔体放入剪切速率合格。
4.4浇口的设计
浇口是连接分流道与型腔之间的一段细短通道,它是浇注系统的关键部分。
浇口的形状、位置和尺寸对塑件的质量影响很大。
浇口的理想尺寸很难用理论公式计算,通常根据经验确定,取其下限,然后在试模过程中逐步加以修正。
一般浇口的截面积为分流道截面积的3%~9%,截面形状常为矩形或圆形,浇口长度为0.5~2mm,表面粗糙度Ra不低于0.4μm。
浇口的结构形式很多,按照浇口的形状可以分为点浇口、扇形浇口、盘形浇口、环形浇口、及薄片式浇口。
而我们这里选用的是矩形浇口。
浇口的截面一般只取分流道截面积的3%~9%,浇口的长度约为0.5mm~2mm,现在可算出我们需要的浇口面积S=5%×
s=2.512。
浇口位置的选择直接影响到制