脱氧与合金化Word文档格式.doc
《脱氧与合金化Word文档格式.doc》由会员分享,可在线阅读,更多相关《脱氧与合金化Word文档格式.doc(6页珍藏版)》请在冰豆网上搜索。
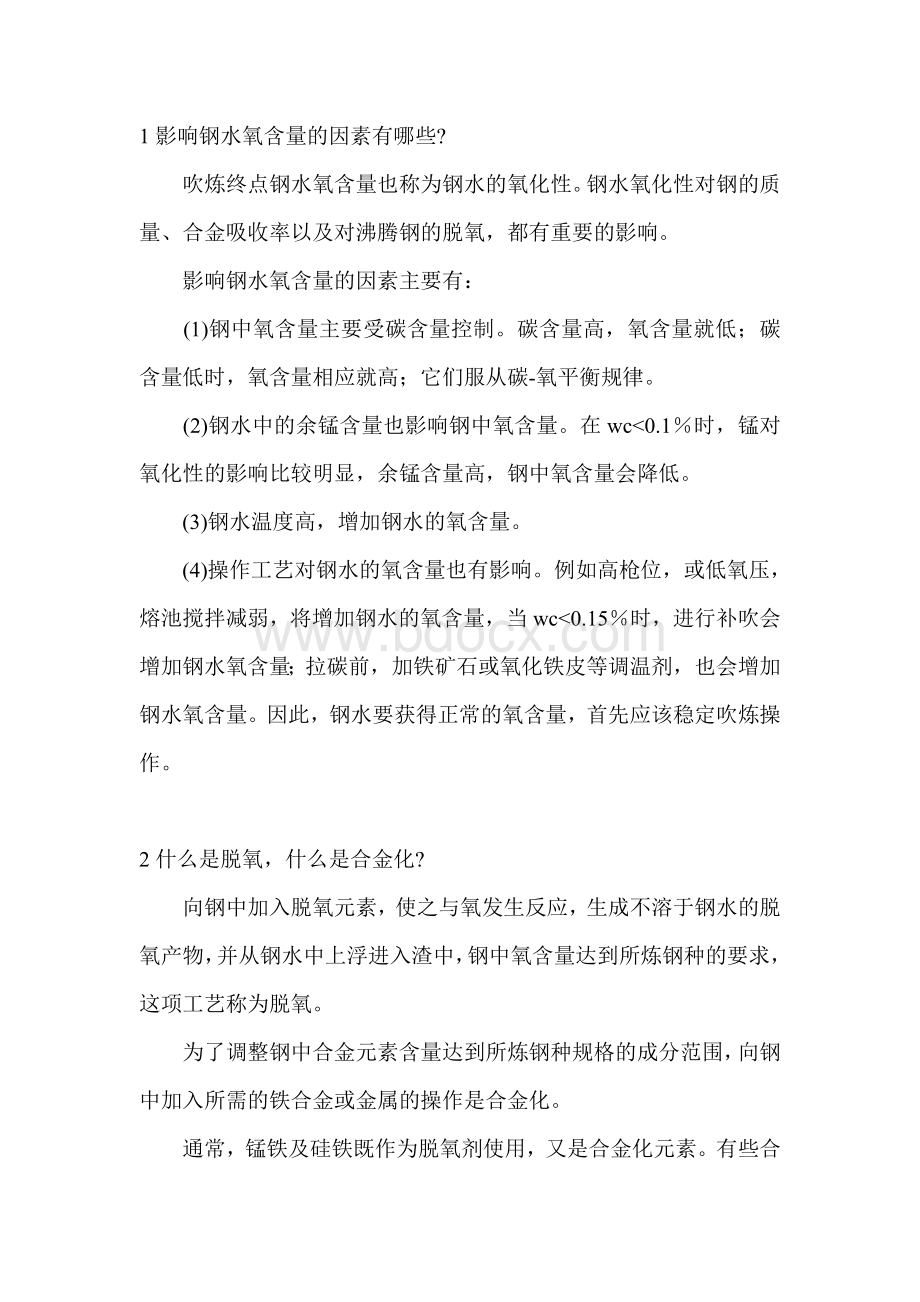
(3)钢水温度高,增加钢水的氧含量。
(4)操作工艺对钢水的氧含量也有影响。
例如高枪位,或低氧压,熔池搅拌减弱,将增加钢水的氧含量,当wc<
0.15%时,进行补吹会增加钢水氧含量;
拉碳前,加铁矿石或氧化铁皮等调温剂,也会增加钢水氧含量。
因此,钢水要获得正常的氧含量,首先应该稳定吹炼操作。
2
什么是脱氧,什么是合金化?
向钢中加入脱氧元素,使之与氧发生反应,生成不溶于钢水的脱氧产物,并从钢水中上浮进入渣中,钢中氧含量达到所炼钢种的要求,这项工艺称为脱氧。
为了调整钢中合金元素含量达到所炼钢种规格的成分范围,向钢中加入所需的铁合金或金属的操作是合金化。
通常,锰铁及硅铁既作为脱氧剂使用,又是合金化元素。
有些合金只是作为脱氧剂使用,如硅钙合金,硅铝合金及铝等。
冶炼含铝的钢种,铝也是合金化元素。
另有一些合金只用于合金化,如铬铁、铌铁,钒铁、钨铁、钼铁等。
在一般情况下,脱氧与合金化的操作是同时进行的。
3
由于脱氧工艺不同,脱氧产物的组成有何不同,怎样才有利于脱氧产物的排除?
钢包脱氧合金化后,钢中的氧[O]溶形成氧化物,只有脱氧产物上浮排除才能降低[O]夹,达到去除钢中一切形式氧含量的目的。
脱氧工艺有3种。
(1)用Si+Mn脱氧,形成的脱氧产物可能有:
固相的纯Si02;
液相的MnO·
Si02;
固溶体MnO-FeO。
通过控制合适的w(Mn)/w(Si)比,能得到液相的MnO·
Si02产物,夹杂物易于上浮排除。
(2)用Si+Mn+A1脱氧,形成的脱氧产物可能有蔷薇辉石(2MnO·
A1203·
5Si02);
硅铝榴石(3MnO·
3Si02);
A1203(wA1203>
30%)。
控制夹杂物成分在低熔点范围,为此钢中w[Al]≤0.006%,钢中[O]溶可达0.0020%(20ppm)而无A1203沉淀,钢水可浇性好,不堵水口,铸坯不会产生皮下气孔。
(3)用过量铝脱氧。
对于低碳铝镇静钢,钢中酸溶铝[Al]s含量为0.02%~0.04%,则脱氧产物全部为A1203。
A1203熔点高达2050℃,在钢水中呈固态;
若A1203含量多钢水的可浇性变差,易堵水口。
另外,A1203为不变形夹杂物,影响钢材性能。
通过吹氩搅拌加速A1203上浮排出,或者喂入Si—Ca线、Ca线的钙处理,改变A1203性态。
[Al]s含量较低,钙处理生成低熔点2CaO·
[Al]s较高,钙处理应保持合适的w(Ca)/w(Al)比,以形成12CaO·
7
A1203。
对于低碳铝镇静钢,通过钙处理,产物易于上浮排除纯净了钢水,改善了可浇性。
4
什么是合金元素的吸收率,影响合金元素吸收率的因素有哪些?
合金元素的吸收率又称收得率或回收率(η),是指进入钢中合金元素的质量占合金元素加入总量的百分比。
所炼钢种、合金加入种类、数量和顺序、终点碳以及操作因素等,均影响合金元素吸收率。
吸收率=(合金元素进入钢中质量/合金元素加入总量)×
100% (4-18)
不同合金元素吸收率不同;
同一种合金元素,钢种不同,吸收率也有差异。
影响合金元素吸收率的因素主要有:
(1)钢水的氧化性。
钢水氧化性越强,吸收率越低,反之则高。
钢水氧化性主要取决于终点钢水碳含量,所以,终点碳的高低是影响元素吸收率的主要因素。
(2)终渣TFe含量。
终渣的TFe含量高,钢中氧含量也高,吸收率低,反之则高。
(3)终点钢水的余锰含量。
钢水余锰含量高,钢水氧含量会降低,吸收率有提高。
(4)脱氧元素脱氧能力。
脱氧能力强的合金吸收率低,脱氧能力弱的合金吸收率高。
(5)合金加人量。
在钢水氧化性相同的条件下,加入某种元素合金的总量越多,则该元素的吸收率也高。
(6)合金加入的顺序。
钢水加入多种合金时,加入次序不同,吸收率也不同。
对于同样的钢种,先加的合金元素吸收率就低,后加的则高。
倘若先加入部分金属铝预脱氧,后继加入其他合金元素,吸收率就高。
(7)出钢情况。
出钢钢流细小且发散,增加了钢水的二次氧化,或者是出钢时下渣过多,这些都降低合金元素的吸收率。
(8)合金的状态。
合金块度应合适,否则吸收率不稳定。
块度过大,虽能沉人钢水中,但不易熔化,会导致成分不均匀。
但块度过小,甚至粉末过多,加入钢包后,易被裹入渣中,合金损失较多,降低吸收率。
5
对终点钢水余锰含量应如何考虑?
终点钢水余锰含量是确定含锰合金加入量的重要数据。
终点余锰与铁水锰含量、终点碳、炉渣氧化性及终点温度有关。
铁水锰含量高,终点温度高,终点碳含量高,钢中余锰含量高;
后吹次数多、喷溅大钢中余锰含量低。
此外,凡影响终渣TFe增高的因素,钢中余锰含量都会降低,相反余锰含量会增高。
目前转炉用铁水均为低锰铁水,终点钢中余锰很低。
表4-17是余锰含量占铁水锰含量的百分比,根据钢水终点碳含量确定,可供参考。
钢中余锰占铁水锰含量的比
终点w[C]/%
0.21-0.28
40-45
0.14-0.20
40
0.11-0.13
35
0.08-0.10
25-30
0.05-0.07
20
0.02-0.04
10-20
6
合金加入的顺序和原则是怎样的?
在常压下脱氧剂加入的顺序有两种。
(1)先加脱氧能力弱的,后加脱氧能力强的脱氧剂。
这样既能保证钢水的脱氧程度达到钢种的要求,又利于脱氧产物上浮,质量合乎钢种的要求。
因此,冶炼一般钢种时,脱氧剂加入的顺序是:
Fe-Mn→Fe-Si→Al。
(2)对拉低碳工艺,脱氧剂的加入顺序是:
先强后弱,即Al→Fe-Si→Fe-Mn。
实践证明,利于Al203上浮,减少钢中夹杂物,同时可以大大提高并稳定Si和Mn元素的吸收率,相应减少合金用量:
但必须采用相应精炼措施。
一般合金加入顺序应考虑以下原则:
(1)以脱氧为目的的元素先加,合金化元素后加。
(2)易氧化的贵重合金应在脱氧良好的情况下加入。
如Fe-V、Nb-Fe、Fe-B等合金应在Fe-Mn、Fe-Si、铝等脱氧剂全部加完以后再加,以减少其烧损。
为了成分均匀,加入的时间也不能过晚。
微量元素还可以在精炼过程中加入。
(3)难熔的、不易氧化的合金,如Fe-Cr、Fe-W,Fe-Mo,Fe-Ni等可加在精炼炉或转炉内。
其他合金均加在钢包内。
合金加入时间应如何掌握?
大多数钢种均在钢包内完成脱氧合金化。
这种方法简便,大大缩短冶炼周期,而且能提高合金元素的吸收率。
合金加入时间,一般在钢水流出总量的1/4时开始加入,流出3/4时加完。
为保证合金熔化和搅拌均匀,合金应加在钢流冲击的部位或同时吹氩搅拌。