光伏组件各工序常见问题点分析大全Word文档格式.docx
《光伏组件各工序常见问题点分析大全Word文档格式.docx》由会员分享,可在线阅读,更多相关《光伏组件各工序常见问题点分析大全Word文档格式.docx(11页珍藏版)》请在冰豆网上搜索。
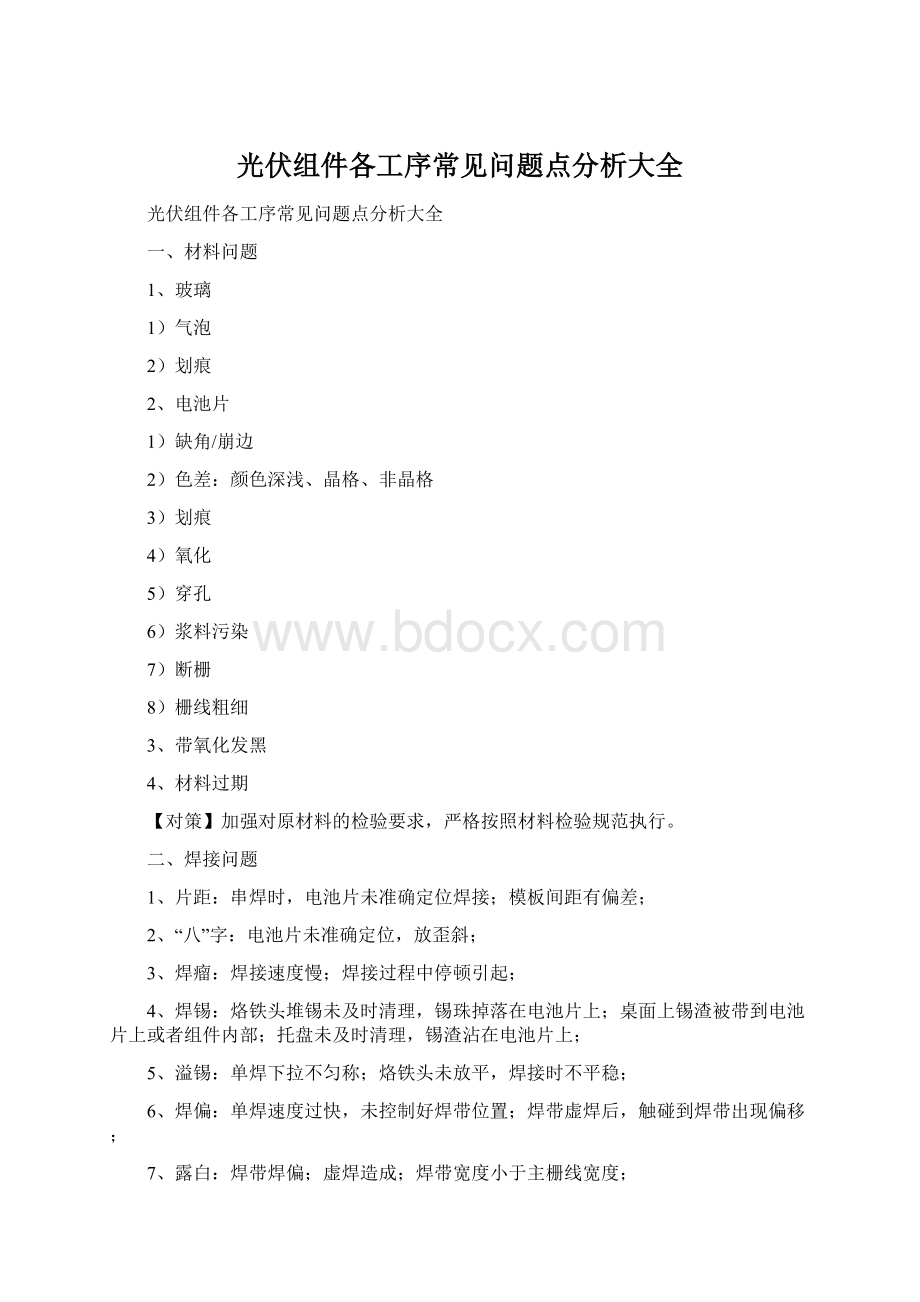
焊接过程中停顿引起;
4、焊锡:
烙铁头堆锡未及时清理,锡珠掉落在电池片上;
桌面上锡渣被带到电池片上或者组件内部;
托盘未及时清理,锡渣沾在电池片上;
5、溢锡:
单焊下拉不匀称;
烙铁头未放平,焊接时不平稳;
6、焊偏:
单焊速度过快,未控制好焊带位置;
焊带虚焊后,触碰到焊带出现偏移;
7、露白:
焊带焊偏;
虚焊造成;
焊带宽度小于主栅线宽度;
8、虚焊:
焊接速度过快;
焊接质量不佳;
电烙铁温度过低;
焊带或电池片的可焊性差;
助焊剂不匹配;
9、漏焊:
人为疏忽;
偷工减料;
虚焊后未及时补焊;
【对策】焊接时,必须保证焊接质量,并严格检查,发现焊接质量问题,及时要求返工,尽量做到一次性成型;
三、叠层问题
1、串距偏大/小:
胶带未粘贴牢靠;
胶带未按规定间距粘贴,或者粘贴不牢固,松动偏移;
2、电池串整体偏移:
叠层时未控制好电池串与玻璃边缘的距离;
搬运或返工导致;
拉扯下层EVA导致;
3、汇流带间距:
焊接不良;
未按模板规范焊接;
4、背膜整体偏移:
拉扯背膜;
搬运叠层件意外造成;
5、焊带弯曲:
未焊接妥当;
单串焊时造成;
返工返修时造成;
6、引出端不良:
穿引时瓣弯曲;
操作人员意外弯曲引出端;
7、条码
1)缺失
2)破损
3)脏污
4)重复
5)信息不实
6)字体不良
8、绝缘条歪斜:
铺设不到位;
裁剪不良;
员工粗心操作;
9、焊带短路:
末端焊带焊接靠近前一片电池片;
绝缘条未正确排版,不对称;
汇流带弯曲,相互接触;
10、串反:
正负极未相间排列;
未按左正右负顺序排列;
【对策】严格按照操作规程进行操作,并按照设计图纸进行生产制作。
四、层压问题
4.1、背膜不良
1)凹坑
【原因】
A.背膜上有硬杂质;
B.高温布上残留EVA杂质硬块;
C.高温布破损;
【对策】
A.保证车间干净整洁;
B.完全清理清洁高温布上残留的EVA;
C.及时更换破损的高温布;
2)起皱
A.原材料问题;
B.铺设背膜不平整;
C.高温布重叠不平整;
D.高温布破损;
A.裁剪背膜时,仔细检查原材料的质量及生产日期;
B.叠层铺背膜时注意背膜和EVA是否合格;
C.层压铺盖高温布时确保高温布平整不重叠;
D.及时更换高温布;
3)脱层
A.背膜或EVA原材料问题;
B.材料污染;
C.玻璃未完全用酒精清洗干洁;
D.层压取件时拉拽背膜导致脱层;
E.层压件温度未降至80℃以下割边划出造成;
F.纸片或其他杂物夹入叠层件中;
G.EVA交联度不合格;
H.助焊剂用量过多,残留在EVA上,长期高温下,容易产生脱层;
A.仔细检查原材料质量、生产日期及包装密封性是否良好;
B.生产过程中确保物料不被污染,必须保证在规定的工作温湿度环境中操作;
C.钢化玻璃用酒精全面清洗干洁;
D.从层压机内取出层压件时注意避免拧起背膜边角;
E.割边时必须等待层压件温度降至80℃以下;
F.叠层完毕后严格检查,发现杂质及时取出;
G.加强EVA交联度的定期检验,对层压参数严格控制;
H.焊接时,要将助焊剂烘干,不允许有残留;
4)鼓包
B.材料兼容性;
C.温度异常;
D.层压机不密封;
E.高温胶带不合格;
F.层压时间较长;
B.对生产用的相同材料置于不同层压机试压测试,查看试样是否都是同样问题,如果问题一样,则材料不兼容或材料不符合要求,更换其他物料试压,观察对比;
C.层压机加热板温度不均匀,局部有温度异常现象,或者是温度偏高,层压前必须严格按要求测试层压机加热板温度,达到要求后方可层压;
D.层压机上下室不密封,抽真空失效,在层压过程中时刻观察真空表是否正常,层压时间是否准确,如有异常及时停机报修;
E.确保高温胶带合格,胶带粘合剂不会在高温环境下产生气体;
F.适当降低层压时间;
5)偏移
A.抬放拽偏;
B.拉扯高温布至偏斜;
C.层压加压不当;
A.抬放层压件时一定注意背膜及EVA不能偏移滑动,不能随便拽拉背膜或EVA,轻抬轻放;
B.铺盖高温布时要轻,不能生拉硬拽,高温布最好是一次铺盖到位;
C.层压机压力过大,加压过快,也易使背膜滑动偏移,发现问题,按实际情况及时处理;
6)正面脏污
A.裁剪弄脏;
B.放置位置脏;
C.员工操作未戴手套;
D.车间5S不良;
E.其他杂质污物;
A.背膜及EVA裁剪必须要保证物料的干净整洁;
B.裁剪完好的背膜和EVA放置特定位置,并保证其放置位置干净;
C.员工必须要戴手套,穿工作服,戴口罩等防护品,保证不让汗渍等污染物料;
D.做好车间5S工作并及时检查;
E.生产过程中严禁将其他杂质带入组件中,叠层检验人员需加强检查力度;
7)焊点凸出
A.温度过高;
B.EVA太薄;
C.层压压力过大;
D.背膜太薄太软;
E.缺少一层EVA;
F.背电极焊瘤过大;
a)适当降低层压温度;
b)对于大组件生产,使用厚度0.4mm以上的EVA;
c)适当降低加压压力或加压时间;
d)更换厚硬一点的背膜;
e)确保最上一层EVA铺盖到位,不能叠重;
f)保证焊接质量,杜绝大的焊瘤或其他不良;
8)破损划伤
a)割边意外造成;
b)硬杂质残留
a)割边避免将割边刀滑割误伤到背膜;
b)层压前及时清理高温布上的杂质,避免将硬物残留高温布或者背膜上;
4.2、EVA不良
1)EVA未熔/缺料
A.原材料问题,EVA原材料不均匀,厚薄不一致,局部特别薄稀或有气孔;
EVA材料中含有不容物杂质;
B.层压温度不均匀;
C.助焊剂或汗渍等污染物影响;
A.严格按照物料检验规程检验每批次物料各项指标是否符合要求,在叠层铺设EVA时,发现问题EVA及时更换;
B.层压前按要求仔细点检各点层压温度;
C.助焊剂未烘干或者徒手操作汗渍沾到物料EVA、电池片等上,造成EVA与电池片或焊带不相熔;
2)EVA局部缺失
A.叠层铺设背膜时,将下层EVA边角掀起重叠;
B.EVA尺寸误差偏大,员工未及时发现并更换;
A.叠层必须严格检查每一项目,保证EVA、背膜及电池串必须分开铺设好;
B.发现问题EVA必须及时更换;
3)EVA脏污
a)裁剪弄脏;
b)放置位置脏;
c)员工操作未戴手套;
d)车间5S不良;
e)其他杂质污物;
a)背膜及EVA裁剪必须要保证物料的干净整洁;
b)裁剪完好的背膜和EVA放置特定位置,并保证其放置位置干净;
c)员工必须要戴手套,穿工作服,戴口罩等防护品,保证不让汗渍等污染物料;
d)做好车间5S工作并及时检查;
e)生产过程中严禁将其他杂质带入组件中,叠层检验人员需加强检查力度;
4.3、杂质不良
1)焊锡
2)助焊剂
3)毛发
4)胶带
5)焊带残留
6)纤维
7)脏污(电池片、绝缘条、汇流带等)
8)其他杂质
【对策】保证车间生产环境,严格执行5S标准。
4.4、气泡
1)背膜/EVA/电池片等材料受污、受潮或过期;
2)EVA材料质量问题,纯度不高,有结块等;
3)层压温度过高,时间过长,导致有机氧化物分解,产生氧气或其他气体;
4)抽真空失效或时间过短;
5)杂质引起;
6)返工件挖片处未垫放EVA块料或返工撕背膜剥离EVA;
7)加热板温度不均匀,局部区域提前升温并固化;
1)保证物料在规定时间内使用完毕,按照相应温湿度要求储存;
2)提高并加强原材料的检验规范,发现问题及时上报,并跟供应商交涉;
3)层压之前要做交联度试验确保温度合格,温度严格控制在原材料参考温度左右,层压时要点检层压机加热板,如发现异常,停机检查;
4)查看层压机真空表、真空泵及密封圈是否完好无损,相应检查要完善,按照工艺要求参数设置抽真空时间;
5)确保在车间无尘生产,避免一切杂质掺入组件内部,做好车间5S并及时检查;
6)返工组件时要细心,保证返修部位干净整洁,填补EVA缺失地方;
7)经常测量层压机加热板表面温度,建议每4小时测量一下,发现异常,停用报修;
4.5、并片
1)EVA收缩率大;
2)胶带未粘牢,掉落;
3)铺盖或拉扯高温布时,移动电池串,使电池串并靠一起;
4)抬放待层压件歪斜,使电池串或EVA偏移滑动;
5)叠层工序人为操作失误;
1)尽量考虑使用收缩率小的EVA;
2)固定间距的高温胶带必须按要求粘贴牢固;
3)铺盖高温布时要避免在组件上拖拉拽等现象;
4)抬放组件时要平正,不得歪斜;
5)叠层工序确保叠层时电池串间距在要求范围内,做好叠层检验工作,发现问题件,及时挑出返修;
4.6、裂片
1)杂质引起;
2)抬板或铺盖高温布时压裂;
3)层压压力过大,充气速率过快;
4)焊带虚焊翻折压碎;
5)过焊引起;
6)引出端卷曲压裂;
7)叠层造成的碎片未能检验出;
8)缺角或崩边引起;
9)抽真空时间过长;
10)单焊正面堆锡严重;
11)单焊时,电池片未预热直接高温焊接,出现膨胀造成隐裂;
1)确保在车间无尘生产,避免一切杂质掺入组件内部,做好车间5S并及时检查;
2)抬放组件、铺设高温布等操作要保证轻拿轻放;
3)按照正常压力值层压,若压力偏大,适当降低;
4)确保焊接工段不出现虚焊现象,若有虚焊必须及时补焊;
5)单焊尽量避免过焊,否则拧电池串时易出现缺角崩边,间接造成电池片隐裂;
6)保证汇流带引出端平直,不卷起弯曲,可用高温布垫放;
7)加强叠层件检验要求和力度;
8)缺角或崩边的电池片尽量少用,或及时更换;
9)适当减少抽真空时间;
10)防止单焊堆锡或溢锡,严重的必须返工重新焊接;
11)单焊时要提前预热加热板,确保电烙铁焊接温度达到要求;
4.7、断栅/栅线模糊
1)电池片过期并氧化;
2)电池片栅线印刷不良;
3)栅线不牢靠,高温或反复搓擦易掉落;
1)保证电池片在有效期内,且必须密封保存;
2)严格检查电池片质量和生产日期,分选工段严格按要求挑选电池片;
3)投产前,用橡皮擦拭电池片栅线,若不合格及时退换电池片;
五、其他问题
5.1、报废
1)撞击爆板;
2)玻璃自爆爆板;
3)层压抽真空失效造成大面积气泡,报废;
1)搬运层压件时注意安全,避免磕碰;
2)严格检查玻璃表面是否有气泡杂质等不良,有的话及时挑出不使用;
3)避免层压抽真空失效,平时经常检验密封圈是否完好,真空泵是否正常运转,真空表是否正常指示;
5.2、降级
1)整体偏移严重;
2)色差严重;
3)返工外观不良;