质量工程课程设计总结报告Word文档下载推荐.doc
《质量工程课程设计总结报告Word文档下载推荐.doc》由会员分享,可在线阅读,更多相关《质量工程课程设计总结报告Word文档下载推荐.doc(20页珍藏版)》请在冰豆网上搜索。
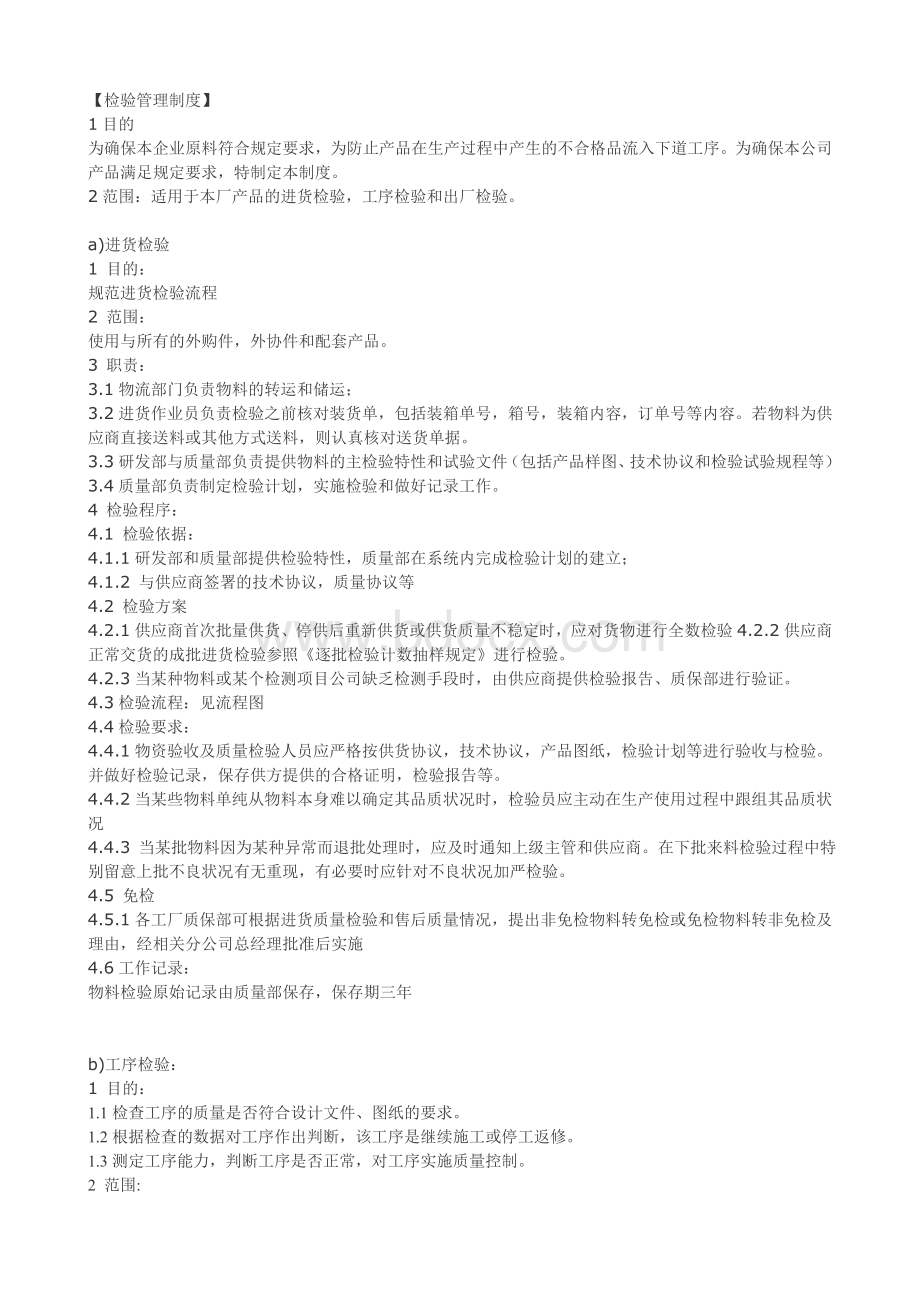
4.2.1供应商首次批量供货、停供后重新供货或供货质量不稳定时,应对货物进行全数检验4.2.2供应商正常交货的成批进货检验参照《逐批检验计数抽样规定》进行检验。
4.2.3当某种物料或某个检测项目公司缺乏检测手段时,由供应商提供检验报告、质保部进行验证。
4.3检验流程:
见流程图
4.4检验要求:
4.4.1物资验收及质量检验人员应严格按供货协议,技术协议,产品图纸,检验计划等进行验收与检验。
并做好检验记录,保存供方提供的合格证明,检验报告等。
4.4.2当某些物料单纯从物料本身难以确定其品质状况时,检验员应主动在生产使用过程中跟组其品质状况
4.4.3当某批物料因为某种异常而退批处理时,应及时通知上级主管和供应商。
在下批来料检验过程中特别留意上批不良状况有无重现,有必要时应针对不良状况加严检验。
4.5免检
4.5.1各工厂质保部可根据进货质量检验和售后质量情况,提出非免检物料转免检或免检物料转非免检及理由,经相关分公司总经理批准后实施
4.6工作记录:
物料检验原始记录由质量部保存,保存期三年
b)工序检验:
1.1检查工序的质量是否符合设计文件、图纸的要求。
1.2根据检查的数据对工序作出判断,该工序是继续施工或停工返修。
1.3测定工序能力,判断工序是否正常,对工序实施质量控制。
2范围:
物料进入生产线后至成品完工前所有过程
3职责:
3.1生产部和质量部负责编写作业指导书,产品工艺卡等。
3.2质量部负责制定检验计划,检验计划的实施并做好记录。
3.3质量部负责监控过程受控,工序能力。
对质量进行控制与改进。
4检验程序:
4.1检验依据:
产品工艺卡或设计文件,图纸等
4.2检验方案
4.2.1生产过程中,在生产开始时和工序要素变化后需进行首件检验。
4.2.2首件检验实行“首件三检制”
4.2.2.1装配人员在本工位作业结束时要进行自检,自检合格后放可进入下倒工序
4.2.2.2班组长或班组质量员对本组作业输出进行抽检,必要的时候进行全检。
检验合格后方可进入下倒工序。
若不合格,则对产品隔离标记并记录。
4.2.2.3专职检验员对完工产品进行终检。
一般采用抽样检验,必要时刻采用全检。
确认合格后方可进入下一环节,若有不合格,对产品进行隔离标记,做好记录后返工。
4.2.3对进入稳定生产状态的大批量产品进行巡回检验
4.2.3.1检验员应对刚加工出来的零件按规定的抽样方案进行检验。
若发现不合格,则应将巡回一次期间加工的所有零件作全检。
并且填写和保存好巡回检验记录表。
4.2.3.2检验员在负责的区域内,每班巡回次数需要达到6次以上
4.2.3.3每班的巡回要做到随机,均衡。
4.2.3.4质量不稳定的工序,要做重点检验,发现问题及时向有关部门反馈信息。
4.2.4完工检验
质检员在零件完成加工工序后,按完工零件检验卡片或产品图纸规定进行检验。
合格者要打印合格标记放可入库或进入下一流程。
c)出厂检验:
1.目的
对最终产品的质量特性进行检验和试验,以确保未经检验和试验的产品或不合格产品不出厂销售。
2.范围
适用于对最终产品的检验和试验。
3.职责
3.1质检部负责最终产品的检验和试验,并负责检验和试验的委托。
3.2相关部门负责协助质量检验员进行最终产品的检验和试验。
4检验程序
国家、行业及企业产品标准或与客户签订的技术协议
4.2检验方案:
4.2.1最终产品的检验和试验是全面考核产品质量是否满足客房的重要手段。
必须严格按产品图样、技术文件、标准、检验要求进行检验和试验。
4.2.2产品完工后,由生产部通知质量部质量检验员进行最终产品的检验和试验,并做好检验和试验记录。
4.2.3与最终产品相关的检验和试验未完成或未通过时,不能进行产品的最终检验格试验。
4.2.4如有合同要求时,应与用户和第三方一起对产品进行检验和试验。
检验和试验过程中发现的质量必须得到解决后才能发货。
4.2.5当某些检验和试验项目本公司不能进行时,由质量部委托有资格的单位进行检验和试验,并对所委托单位的检验和试验能力、资质等进行评价,填写供方评价记录。
4.2.6最终检验和试验项目完成后,由质量部检验技术人员或质量检验员判定最终产品是否合格,如产品判定为合格,可填写“产品合格证”等入库销售手续。
如判定为不合格,按《不合格控制制度》的规定进行处理。
4.2.7每一次检验和试验,质量检验员都应做好检验和试验记录,记录应及时、完整、清晰,并能准确地反映出最终产品实际质量状况。
4.2.8质量检验员应得到质量负责人的授权,并在授权的检验范围内实施质量检验工作。
【检验流程】
一,原材料检验(IQC)
检验范围包括:
用于生产的各种原材料、辅料、外购件、外协件的最初样品或成批进货检验。
原进厂检验包括3个方面:
①库检:
原材料品名规格、型号、数量等是否符合实际,一般由仓库管理人员完成。
②质检:
检验原材料物理、化学等特性是否符合相应原材料检验规定,一般采用抽检方式。
③试检:
取小批量式样进行生产,检查生产结果是否符合要求。
来料不合格的处理:
①标识:
在外包装上标明“不合格”,堆置于“不合格区”或挂上“不合格”标识牌等。
②处置:
退货或调货或其他特采。
③纠正措施:
对供应商提供相关要求或建议防止批量不合格的再次出现。
紧急放行:
因生产急需,在检验报告出来前需采用的物资,为紧急放行。
需留样检验,并对所放行物资进行页数标识并记录,以便需要是进行追踪。
特采:
①从非合格供应商中采购物资---加强检验。
②检验不合格而采用的物资---挑选或修复后使用。
应特别关注不合格品所造成的损失:
①投入阶段发现,损失成本为1元。
②生产阶段发现,损失成本为10元。
③在客户手中发现,损失成本为100元。
二,过程检验(IPQC)
①产品:
半成品、成品的质量。
②人员:
操作员工艺执行质量,设备操作技能差异。
③设备:
设备运行状态,负荷程度。
④工艺、技术:
工艺是否合理,技术是否符合产品特性要求。
⑤环境:
环境是否适宜产品生产需要。
工序产品检验:
对产品的检验,检验方式有较大差异和灵活性,可依据生产实际情况和产品特性,检验方式更灵活。
①质检员全检:
适用于关键工序转序时,多品种小批量,有致命缺陷项目的工序产品。
工作量较大,合格的即批准转序或入库。
②质检员抽检:
适用于工序产品在一般工序转序时,大批量,单件价值低,无致命缺陷的工序产品。
③员工自检:
操作员对自己加工的产品先实行自检,检验合格后方可发出至下道工序。
可提高产品流转合格率和减轻质检员的工作量,不易管理控制,时有突发异常现象。
④员工互检:
下道工序操作员对上道员工的产品进行检验,可以不予接受上道工序的不良品,相互监督,有利于调动积极性,但也会引起包庇,吵执等造成成品质量异常现象。
⑤多种方式的结合:
有机结合各种检验方案,取长补短,杜绝不良品流入下道工序或入库,单检验成本较高。
工序品质检验:
对人员、设备、工艺技术、环境等的检验。
三,成品检验
①组装检验
②产品外观检验
③完整性检验
④性能检验
⑤精度检验
⑥清洁度检验
⑦可靠性检验
四,成品包装检验
检验项目包括:
①查包装用材料,包装箱制造是否符合包装设计要求;
②检查包装的防雨,防锈,防霉,防震等是否符合特性;
③检查包装的外观及包装的标志是否符合包装设计要求;
④检查随机应带的文件:
产品说明书、合格证和装箱清单等是否齐全完好;
⑤检查随机应带的附件、备件和工具是否符合规定;
⑥检查包装是否牢固,符合防压要求;
⑦检查包装的起吊运输设置是否符合要求。
以上各项检查符合要求后,需经检验员在装箱清单上签章,才可封装验收入库。
五,出厂检验
检查是否存在致命缺陷、重大缺陷
检验流程图画:
总流程图:
百度图片的
1。
进货流程图:
2.过程检验流程图:
见下页
3.出厂检验流程图
《过程检验流程图》
责任部门/人员输入主要流程输出/输入部门
生产部
成品仓库
产品加工
质保部
技术部
操作者
质监员
自检
巡检
合格?
Y
N
缺陷分析
财务分析
控制计划
报废单
检验记录
成品、合格证
质量统计
交库单
报废
特许让步
评价
标识/隔离
/
返工/返修
不合格品处理报告
不合格品管理程序
返工/返修指导书
技术部/顾客
6
质量统计表
财务部
总经理质保部
质量成本统计表
图示说明:
流程路线
信息路线
相关部门
纠正/预防措施
XX电能表有限公司
零部件进货检验记录表
产品名称
规格型号
零部件代号
零部件名称
文件编号
版本号