年产36万吨合成氨一氧化碳变换工段工艺设计Word文件下载.docx
《年产36万吨合成氨一氧化碳变换工段工艺设计Word文件下载.docx》由会员分享,可在线阅读,更多相关《年产36万吨合成氨一氧化碳变换工段工艺设计Word文件下载.docx(37页珍藏版)》请在冰豆网上搜索。
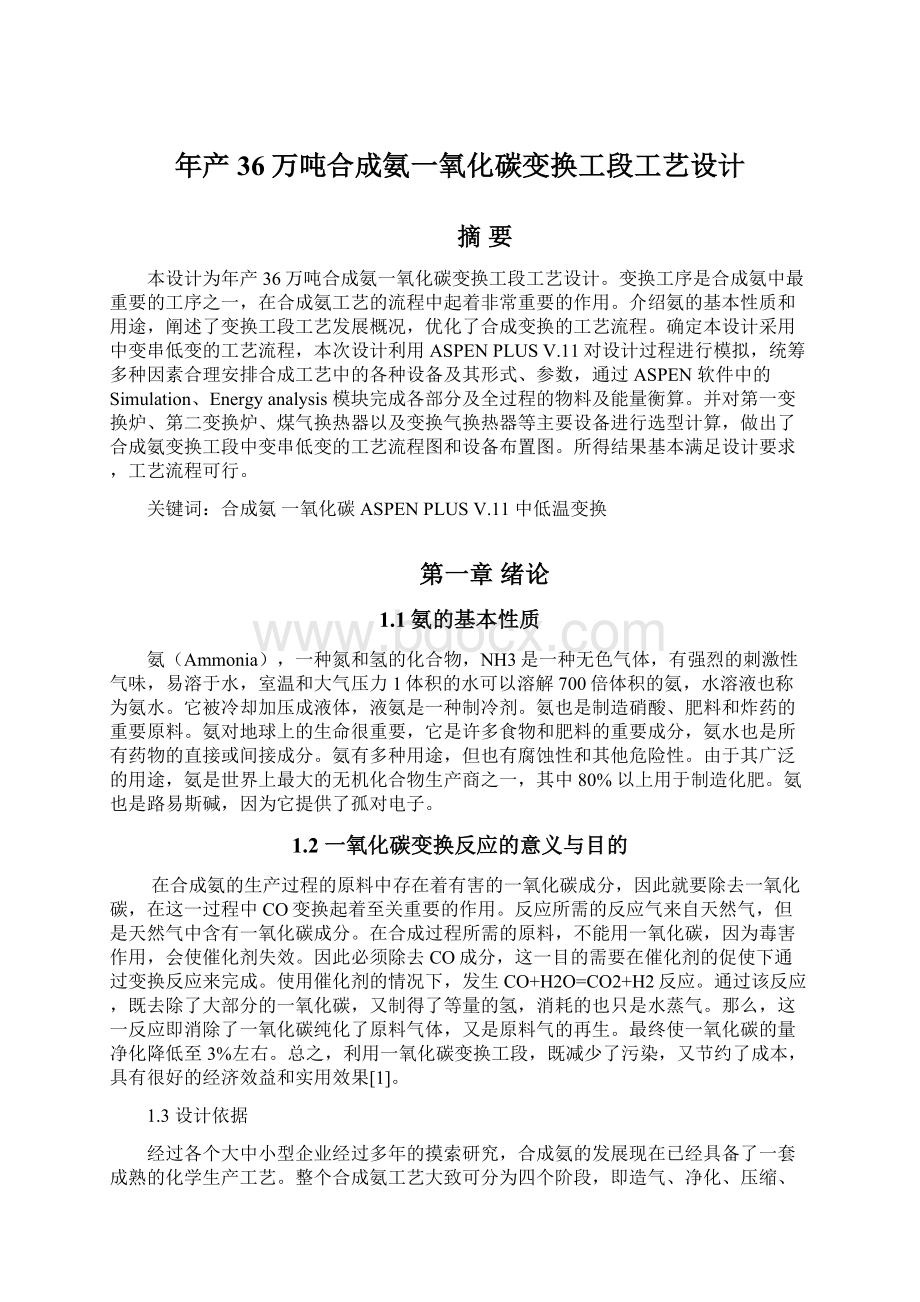
1.2一氧化碳变换反应的意义与目的
在合成氨的生产过程的原料中存在着有害的一氧化碳成分,因此就要除去一氧化碳,在这一过程中CO变换起着至关重要的作用。
反应所需的反应气来自天然气,但是天然气中含有一氧化碳成分。
在合成过程所需的原料,不能用一氧化碳,因为毒害作用,会使催化剂失效。
因此必须除去CO成分,这一目的需要在催化剂的促使下通过变换反应来完成。
使用催化剂的情况下,发生CO+H2O=CO2+H2反应。
通过该反应,既去除了大部分的一氧化碳,又制得了等量的氢,消耗的也只是水蒸气。
那么,这一反应即消除了一氧化碳纯化了原料气体,又是原料气的再生。
最终使一氧化碳的量净化降低至3%左右。
总之,利用一氧化碳变换工段,既减少了污染,又节约了成本,具有很好的经济效益和实用效果[1]。
1.3设计依据
经过各个大中小型企业经过多年的摸索研究,合成氨的发展现在已经具备了一套成熟的化学生产工艺。
整个合成氨工艺大致可分为四个阶段,即造气、净化、压缩、合成。
初始的反应气中通常存在着很多的的碳,因为一氧化碳对反应催化剂有毒,所以需要在进入氨合成工序之前将其中的CO经变换工艺将其转变为CO2除去。
合成所需要的H2。
因此,CO变换即消除了一氧化碳纯化了原料气体,同时是原料气的再生。
行如果仍然存在少量的CO,可以将氨溶解于水中,形成氨水,达到洗涤除去的目的。
变换工段是借助于一定温度,特定的催化剂,使一氧化碳与水蒸气发生反应生成有效气体氢气与二氧化碳。
在各个大中小型企业中发挥了至关重要的作用。
在这里采取中串低变的方法,中串低变这一概念是从上世纪80年代流的。
中变串低变是在B109,B1113,B114,B115等作为催化剂的前提下,以铁-铬系催化剂为主要添加物,然后再串进钴-钼系宽变催化剂的工艺。
这一工艺使反应所需的条件发生了很大的变化。
一方面最大程度的降低了入炉蒸汽比,另一方面又最大程度的降低了出炉气体中的CO含量。
因为中变后钴-钼系宽变催化剂的串入,不仅使反应所需的条件发生了很大的变化,而且还大大降低了能耗,更方便了变换系统操作。
1.4变换工艺的选择
变换工艺主要有4种:
全中变、中串低、全低变和中低低。
对于每一种变换工艺,由于采用不同的热回收方式而使变换工艺流程及设备结构有所不同。
合理选择变换工艺应考虑以下因素:
半水煤气、水和蒸汽的质量;
半水煤气中硫化氢含量;
变换气中CO含量要求;
对变换后续工段的影响;
企业现有的管理水平和操作水平。
中变段间的热回收方式最主要有3种:
煤气冷激、中变炉内喷冷激和中变炉外喷水增湿。
中变段间煤气冷激与中变炉内喷水冷激两种中低工艺流程各有优缺点。
现比较如下面:
①节能效果:
段间喷水热回收率高,直接将段间高位能转化为蒸气,增加了汽气比,降低了蒸汽消耗,节能效果比段间煤气冷激要好。
②设备:
段间喷水冷激需在中变炉内设置蒸发层和喷头,这样与煤气冷激相比中变炉的结构就更为复杂,设备高度亦需增加,煤气冷激流程有部分半水煤气不经过主热交换,因此主热换热面积也比炉内喷水流程要小。
③操作运行:
煤气冷激流程操作简单,但需防止中变下段发生偏流,造成床层漏氧,引起低变一段催化剂中毒失活,炉内喷水冷激操作要求高,冷激水最好能用脱氧软水,喷水冷激装置既要达到所需的喷淋量,又要保证雾化好,以免中变下段催化剂粉化和结块。
通过以上比较,中变炉内喷水冷激流程具有节能,运行费用低等优点,中变段间煤气冷激流程具有操作简单、投资省等优点。
因此本设计采用中变-低变串联流程,且中温变换炉采用段间煤气冷激流程。
第二章工艺原理和流程
2.1工艺原理
CO变换反应式为:
CO+H2O=CO2+H2+Q(2-1)
CO+H2=C+H2O(2-2)
以上是两次反应,(2-1)式是主要反应。
反应为可逆变化,为了避免反应反方向进行,进一步提高反应生成目的产物的效率,在合成氨过程中加入拥有良好选择性的催化剂。
(2-2)式是低温变换反应,也是(2-1)的副反应。
通过两次变换,一氧化碳含量减少到0.3%,从而纯化了原料气体,达到了优质、高效、节能、减排的目的。
2.2工艺流程
整个生产过程主要分为三部分,分别是一二段的转化和中-低变串联流程。
如图2-1所示,首先经过天然气加氢脱硫,在一定温度和压力下使水碳比为3.5,然后进入一段转化炉对流加热反应,在集气管中的温度升到850℃左右,在输气总管的作用下,加热后的气体进入二段转化炉。
然后再把经二段转化气连续送入到第一换热器、第二换热器,回收高位能废热并使之由最初的1000℃降温至360℃左右。
最后将气体送进变换工序,进一步处理。
此时,变换工艺原料气在360℃、3.0MPa下进入中变炉。
转化气到达锅炉后,不再有转化炉的高温,而是冷却到了330℃。
在锅炉出口处加入水蒸汽,把汽气比调控在在3~5之间。
要求一氧化碳含量下降3%以下,然后送入中变炉实现这一过程。
这个时候的气体温度仍然有些高。
是不可以进行气体变换的,需要用来加热其他工艺气体达到换热效果,使温度降到180℃左右时送入低变炉。
在此过程中,换气中一氧化碳含量将会下降到0.3%以下,这时就可以进行后续工段的净化了[10]。
图2-1工艺流程简图
2.3工艺条件
2.3.1压力
在一氧化碳变换工艺中压力虽不起决定性作用,但是,提高反应的压力将促使副反应发生。
从反应平衡来看的话,增加压力没有十分显著的好处。
不过从动力学角度来看,增加压力反而可以提高反应的速率,降低反应时间。
而且从耗能上看,增加压力可以减少能量的损耗。
由于干燥原料气体摩尔量小于干燥转化气体的摩尔量,增加压力后反应正向进行,因此,在转化前压缩原料气所需的能量低于在常压下压缩的能量消耗。
操作压力的确切数值,需要根据不同的工艺要求和合成氨厂配置来定,特别是投料过程中各个反应段的压力需求都不相同。
平常情况下,规模小点的合成氨工艺的数值在0.7-1.2MPa的范围,中型合成氨工艺的数值在1.2-1.8Mpa范围。
该生产工艺所需的原料气,是在规模不大的合成氨厂通过变换反应来的,取1.7MPa的压力。
2.3.2温度
变换反应是可逆放热反应。
从动力学的角度看,升温使反应速率常数增大,减少了反应正向进行的时间。
但是从热力学角度考虑,升高温度反应朝着吸热方向进行,即逆反应,平衡常数随之变小,CO平衡含量随之增大。
这时就要从动力学方面对反应所需的最适宜的温度进行计算。
Tm=(2-3)
上式中,Tm是最佳反应温度,是反应平衡时的温度。
Tm随反应物组分和催化剂的种类变化而发生改变。
第三章工艺计算及流程模拟
3.1中变炉一段催化剂床层的物料衡算
3.1.1确定转化气组成
一氧化碳变化工艺原料气组成见表3-1。
表3-1原料气组成
组分
CO2
CO
H2
N2
CH4
O2
合计
%
9.6
11.42
55.71
22.56
0.38
0.33
100
计算基准:
1吨氨
年产36万吨合成氨生产能力:
年生产时间:
8000
流量:
45000kg/h
要求出中变炉变换气组成(干基)中CO摩尔百分含量小于2%。
表3-2中变炉进口气组分(干基)
组分
含量,%
kmol
581.76
692.052
3376.026
1367.136
19.998
23.028
6060
中变炉进口气体温度为330℃,中变炉出口气体温度为360.74℃。
进中变炉干气压力=1.75Mpa.
3.1.2水汽比的确定
已知变换气为半水煤气制合成气工艺,因此取水碳比为3.5。
故N(水)=5544kmol
表3-3中变炉进口气组分(湿基)
H2O
含量%
5.01
5.96
29.09
11.78
0.20
47.77
5544
11604
图3-1中变炉ASPEN模拟流程图
以100kmol转换气(湿基)为计算基准,其中CO含量5.96%,要求经变换工艺后的原料气(湿基)中CO含量为2%,故根据变换反应:
CO+H2O=H2+CO2
则CO的实际变换率为:
%=×
100=74%
式中Ya、分别为原料及变换气中CO的摩尔分率(湿基)
则反应掉的CO的量为:
5.96%×
74%=4.41%
则反应后的各组分的量分别为:
H2O%=47.77%-4.41%+0.4%=43.76%
CO%=5.96%-4.41%=1.55%
H2%=29.09%+4.41%-0.4%=33.1%
CO2%=5.01%+4.41%=9.42%
中变炉出口的平衡常数:
K=(H2%×
CO2%)/(H2O%×
CO%)=4.6
查《小合成氨厂工艺技术与设计手册》可知K=4.6时温度为510℃。
中变的平均温距为510℃-360℃=150℃
上述核算中变炉平均温差合理,故一氧化碳变换工艺水碳比为3.2。
3.1.3中变炉一段催化剂床层物料衡算
查阅资料并结合年产36万吨合成氨变换工段工艺设计要求,可假定一段催化剂床层CO实际变换率为60%。
表3-4中变炉一段催化剂床层进口气组成(湿基)
3376.02
1367.13
一段催化剂床层中CO的变化量为:
60%×
692.052=415.23kmol
一段催化剂床层出口气中CO含量:
692.052-415.23=276.82kmol
令式O2+2H2=2H2O存在并完全反应