煤浆槽制作方案Word格式.docx
《煤浆槽制作方案Word格式.docx》由会员分享,可在线阅读,更多相关《煤浆槽制作方案Word格式.docx(31页珍藏版)》请在冰豆网上搜索。
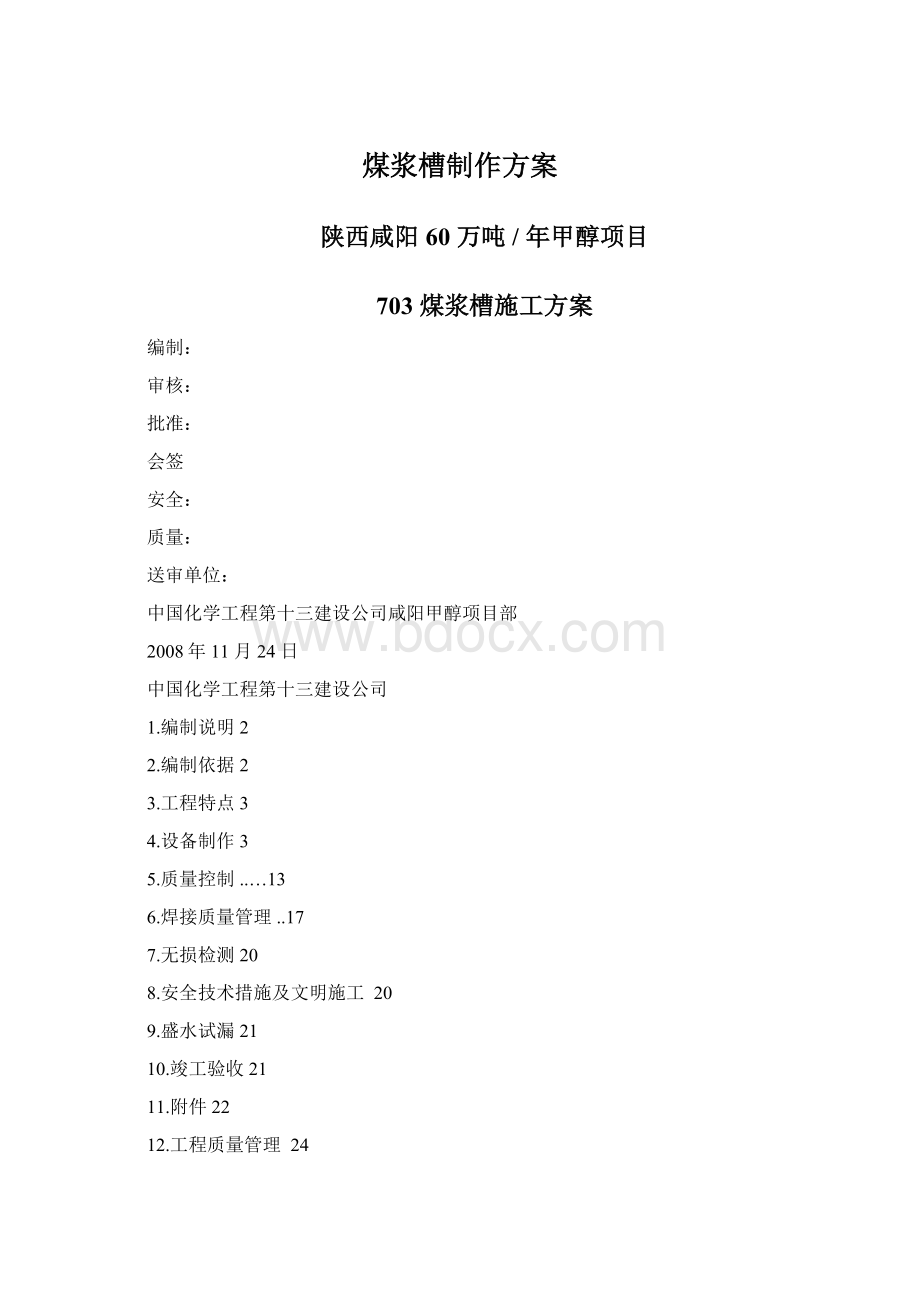
14.施工组织机构28
15.附表29
一、工程概况
咸阳化学工业有限公司60万吨/年甲醇项目的两台煤浆槽(VH
1301AB,由华陆工程科技有限公司(化学工业部第六设计院)设计,主体材质为Q235B设计规格©
8200X12500X20mm下为椭圆型封头,上口为焊接H型钢框架,顶为平顶,内部安装搅拌装置。
设备主要设计数据见表1
表1设备性能一览表
设备名称
煤浆槽
设备位号
VH1301A/B
设备规格
©
8200X12500X20
设备自重
106500
主体材质
Q235B
介质特性
有磨蚀
设计压力
操作压力
常压
设计温度C
80°
操作温度C
50°
操作介质
62%煤38%水
腐蚀裕量mm
3
容积m
626
焊接接头系数
0.85/0.85
焊缝无损检测方法比例及合格级别
射线检测20%
川
设备形式
立式
基础标咼
+7.8m
压力试验MPa
盛水试漏
编制依据
1)T5031-611HFE40-0200煤浆槽施工图。
2)《钢制焊接常压容器》GB/T4735-97。
3)《压力容器安全技术监察规程》(99版)。
4)《机械搅拌设备》HG/T20569-1994
5)《钢制化工容器制造技术要求》HG20584-1998
6)《钢制管法兰、垫片、紧固件》HG20592-9*HG20635-97。
7)《钢制压力容器焊接规程》JB/T4709-2000。
8)《压力容器无损检测》JB4730-94。
9)GB50236《现场设备、工业管道焊接工程施工及验收规范》
三、工程特点
本设备直径大、筒节质量大、设备基础高属高空作业范围、筒体板材厚、组对难度大、焊接工作量大、封头分片到货组对焊接难度大、质量要求高、内部安装传动搅拌装置,设备椭圆度要求精度高,筒体组装分片组装,需多次用大吨位吊车进行配合吊装,封头、顶板组对时必须在基础高度搭设临时组装平台进行封头组对焊接。
四、设备制作
4.1设备制造程序
设备制造程序如下:
8200椭圆形封头外协分瓣冲压,现场组焊安装筒体分片制造,校圆,组对,焊接纵缝,筒节组对,焊接环缝,封头组对焊接,槽钢架预制安装。
4.2设备分段情况
设备制作分5部分进行现场组焊,其中裙座、封头、顶盖、结构采用正装法,筒体采用倒装法。
表4.2设备分段及提升情况
分段号
内容
最大直径
高度
重量
(mm)
(kg)
第一部分
8200筒体
8200
10500
40544
第二部分
8200封头
2000
11325
第三部分
安装工字钢
I32
9585
4040
第四部分
8200裙座
8400
3000
14705
第五部分
顶盖
8800
21300
28500
4.3主要施工程序
431煤浆槽筒体分片制造程序(图431)
图431煤浆槽筒体组片制造
4.3.2煤浆槽各段组焊程序(图432)
4.4施工准备4.4.1组焊平台准备
根据封头筒体组焊情况及吊装施工需要,在设备基础旁铺设一处施工平台,平台规格为10mK10m在下面摆放20#槽钢并找平,水平度允许偏差为2mm/m然后相互焊接牢固并在上面铺设20mn厚的平台钢板。
平台平
面尺寸及用料布置见,图441
10m
平台材料表
名称
规格
数量
单位
槽钢
[20
100
m
钢板
S=20
m2
-4-
图441组装平台示意图
442临时设施及机具准备
在现场设置施工材料库(包括焊条库及烘箱等),吊装设备,组装卡具,焊接设备,空压机等组焊设施;
具体施工机具及数量见附表二。
4.4.3技术准备
熟悉施工图纸,做好焊接工艺评定、焊工培训、施工方案的编制、工艺文件编制、技术交底等工作。
4.5椭圆形封头制造
1)组装程序
大直径封头椭圆度控制是关键,也是难点,要求封头的下口以胎具定
位来控制,符合要求后再焊纵缝。
4.5.1椭圆形封头排板
煤浆槽下封头为椭圆形封头,规格8200伽,材质Q235-B,厚度20mm
封头按制造单位排版组对。
椭圆形封头共分三部分进行组装。
4.5.2椭圆形封头验收
压制好的椭圆形封头瓣片应在封头厂进行预组装,并验收合格再编号
发运。
椭圆形封头材料进场后,要根据瓣片几何尺寸及形状做好校验工作,几何尺寸偏差均不超过2mm坡口形状及尺寸应满足要求。
4.5.3椭圆形封头组装1)组对准备封头瓣片卡具方帽及组装吊耳位置见图3。
纵缝方帽在两端的位置已
给定,中间部分方帽按0.6—1米间距布置,方帽焊在封头瓣片外侧,吊耳焊在中部。
2)组装。
在组装平台上划出组装基准圆,并搭设圆形拼装制承胎具,
将下瓣片依次吊装就位,调整坡口间隙,对口错边量及上下口椭圆度,点焊定位,再将圆顶板进行组对,吊装是利用上级板的外表面上的三个吊耳作为吊点,钢丝绳与定位块的连接采用卡扣联通,用三个倒链连接吊钩找出合适角度吊装。
定位块
图-3
3)组对。
用吊车吊起一个图封头瓣片,将大端慢慢安放在划好的基准圆上,将上口提起到规定的高度后用临时支撑材料支撑。
再安装装相邻的瓣片,并用卡具连接固定。
吊耳
封头瓣片
挡板
支撑
组装平台
X
/
图4.5.3圭寸头安装示意图
4)找正。
端口直径(测外圆周长)、端口椭圆度、纵缝错边量、棱角度。
下端口利用定位块并辅以楔铁找正。
4.5.4椭圆形封头焊接
1)焊接方法
封头在平台上组装完毕,经检查合格,焊接时为防止焊接变形,焊接时由多名焊工同时对称施焊,焊接时必须严格执行焊接工艺,采用分段退步焊,先焊纵缝后焊环缝。
下段由多名焊工先在外侧同时对称进行焊接,先焊纵缝后焊环缝。
焊接第一遍打底焊时采取分段退步焊,以后可按照具体情况实施,(除最后盖面焊外),外侧焊接完毕,经气刨清根后进行内部焊接。
在对焊缝返修清除缺陷时长度约为100mn为宜。
返修时应该严格执行与正式焊接相同的焊接工艺。
同一部位返修次数不得超过两次,若超过两次,须经公司总工程师批准方可进行。
2)焊接要点
A焊接时应严格执行焊接工艺。
B焊接前必须用钢丝刷、角磨机对焊缝坡口进行清理。
C焊接时严格执行对称焊接,应采用分段退步焊。
D为防止焊接变形,内侧用圆弧板进行钢性固定,待所有焊缝焊接完毕方可去除。
4.6筒体组装
461筒节预制
筒体材质为Q235B直径©
8200mm厚度为20mrp总长10500。
筒节按供料情况排版,纵缝错开1000〜1/3周长,纵横缝避开关口边缘50伽以上。
每圈筒节可分3片卷制,共六圈板,卷圆应先压头,用样板检查合格后再卷制,,为防止筒节变形,卷制好的筒节瓣片应立放。
筒体预制前应先测量椭圆形封头周长,然后根据封头外圆周长确定筒节展开尺寸。
4.6.2筒节的拼装
由于预制现场与施工现场相邻,减少了设备运输环节,可直接现场组装。
1)在现场的水平胎面上划出筒体组装投影圆,在投影圆内每隔1000-1500mm焊一块定位板。
2)按照排版图将同一筒节的板片按顺序吊至投影圆处,用工卡具进行组装。
3)对口错边量用工卡具调整。
4)外圆周长的控制,外圆周长是通过对口间隙大小的调整来控制的,但同时应考虑焊缝的收缩量。
外圆周长可按下式计算:
L=LZ-NF
式中:
L——要求外圆周长,mm
组装控制的外圆周长,mm
N――简节焊缝数
F――单个焊缝焊接收缩量,与板厚、间隙大小、焊接方法等
因素有关,可按经验取值2.5~3mm
筒节外圆周长的控制目的是为了筒体环缝错边量能够符合要求。
在封
头已先加工的情况下,筒节外圆周长应以封头实测内径计算。
5)纵缝棱角度的控制,可通过焊制反变形板进行调整,在焊接中采用合理的焊接顺序也可进行部分的调整,但最关键是板片的卷制质量控制。
6)筒节端面不平度的控制,通过组装平台水平度来控制筒节端面的
不平度的。
组装平台用U形玻璃管液面计找水平,水平度允许偏差为1mm以下口为基准通过测量筒节各处的高度,来确定上口的不平度。
若上口不平度超标影响筒体组装,则应局部修整。
7)圆度及同心度调整。
在筒节组装时,首先通过板片的垂直度控制上端口的圆度(下口有投影圆和定位板控制)。
然后在距上端口200mn处用组成轮辐状的钢丝绳以花篮螺丝牵拉调整椭圆度(沿径向均分12—16点),待达到要求后再进行焊接。
该端口的牵拉钢丝绳待与相对的筒体组焊后再拆除。
4.6.3基准圆划线
筒节合格后,应按排版图定出0°
、90°
、180°
、270°
四条方位基准线,并在距下端口100mm的位置划出基准圆周线,内外位置一致均划,并进行标记。
4.6.4筒体组装
4.6.4.1筒体现场组装方法
分段筒体现场组装采用立式倒装法。
现场组装时需75吨汽车吊进行配合。
4.642组装程序
1)测量已组焊好的封头与筒节的端口周长,标记在封头与筒节端口上。
并计算出相邻两端口的直径差,以便为组装时均匀分布错边量提供数据。
2)在下部封头上口的外侧约每隔800mm|t旱一块定位板,再将最上面一节筒节加固后吊放上去。
在对口处每隔约800mn距离放间隙片一块,间隙片的厚度以保证对口间隙为原则。
3)调整方位基准线,组装时上下两圈筒节的四条方位基准线必须对称,其偏差不得大于5mm必要时,可设置方位调整定位块。
4)用组装卡具调整对口错边量,使其沿圆周均匀分布,防止局部超标,并通过调整组对间隙而确保直线度符合要求。
不应进行强行组装。
5)组装合格后,进行定位焊接。
6)安装槽钢支撑圈。
7)依次安装第一、二、三、……筒节,最后加顶盖。
8)最后组焊接管。
4.6.3筒体端部加固措施
由于煤浆槽筒体直径较大、钢性较差,其端部因重力或吊装会产生变形,影响其后的组对安装,必须采取钢性支撑加固措施。
如图465所示,采用多点支撑。
支撑加固材料选用4-8根规格为©
108X4.5的碳钢无缝钢管,支撑钢管所用垫板规格为200X200x16mm8-16块。
间隙片平台
加固管
图465筒体加固示意图
图464.2筒体组装示意图
4.6.4筒节焊接
筒体的焊接主要对纵缝棱角度进行控制,可通过焊制反变形板进行调整,反变形量约为3〜5mm在焊接中采用合理的焊接顺序也可进行部分的调整,如进行多道多层焊,但最关键是板片的卷制质量控制。
在焊接环缝时,应由多名焊工同时均布对称焊接,以防止焊缝受热不均出现变形。
主要控制纵缝的焊接变形(棱角)。
Hj
4.7该设备下封头有一块耐磨板
1)预制。
规格为4