课程设计冲裁模具设计说明书Word文件下载.docx
《课程设计冲裁模具设计说明书Word文件下载.docx》由会员分享,可在线阅读,更多相关《课程设计冲裁模具设计说明书Word文件下载.docx(24页珍藏版)》请在冰豆网上搜索。
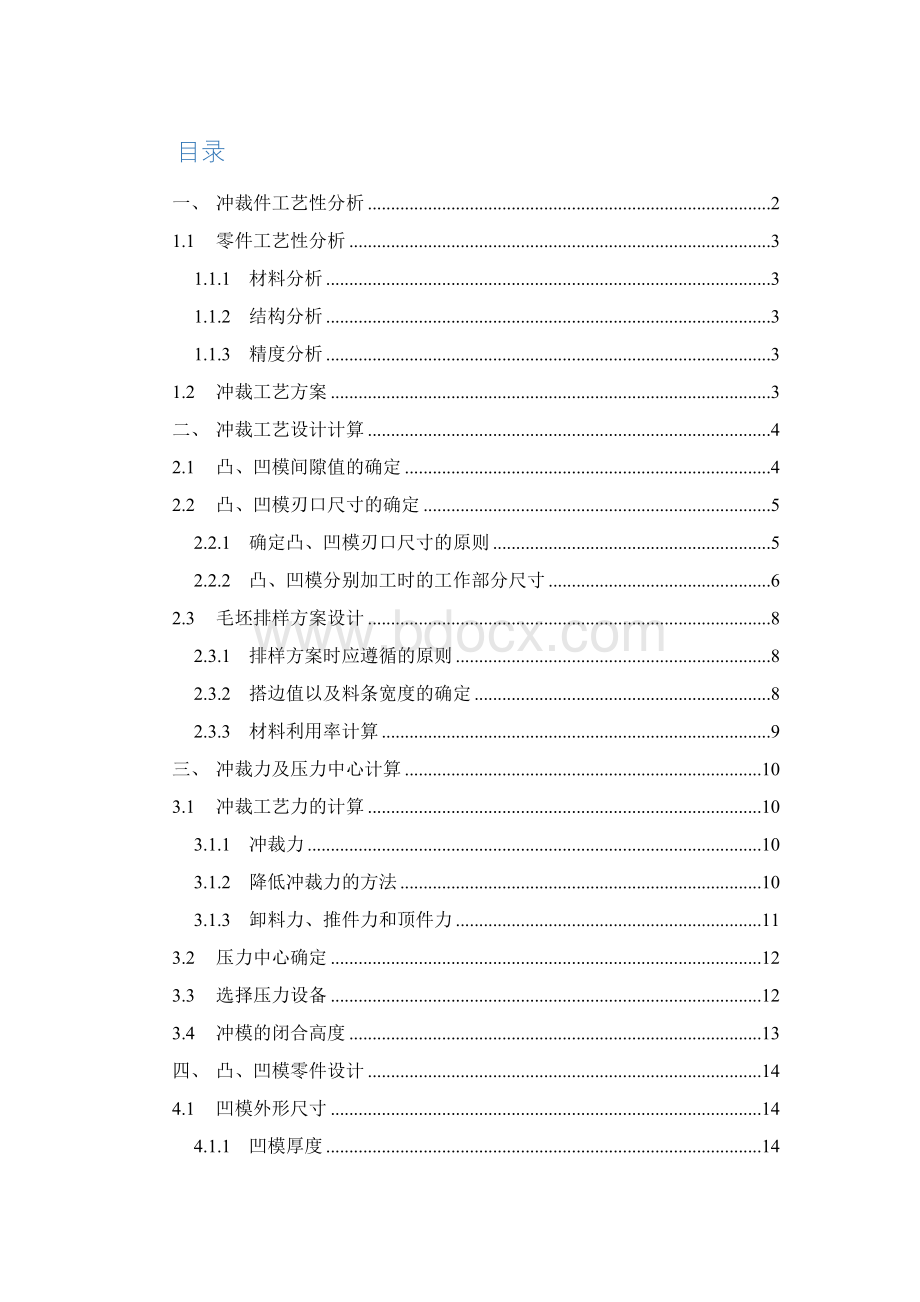
四、 凸、凹模零件设计 14
4.1 凹模外形尺寸 14
4.1.1 凹模厚度 14
4.1.2 刃口高度 14
4.2 凸凹模外形尺寸 15
4.3 冲孔凸模外形尺寸 16
4.4 凸、凹模装配结构设计 16
4.4.1 螺钉选择 16
4.4.2 定位板和定位销 16
4.4.3 螺钉定位 17
五、 模具总体结构设计 17
5.1 冲模模架标准设计 17
5.1.1 冲模模架设计 17
5.1.2 导柱及导套设计 19
5.2 模柄设计 19
六、 卸料装置和顶件装置设计 20
6.1 卸料装置设计 20
6.2 弹性元件的选择 20
6.2.1 橡胶压力P 20
6.2.2 橡胶自由高度H 20
6.3 顶件装置设计 21
七、 模具结构三维设计 21
一、冲裁件工艺性分析
制件零件图如图1-1所示:
图1-1制件结构图
1.1零件工艺性分析
1.1.1材料分析
304用途广泛,具有良好的耐腐蚀性,耐热性,低温强度和机械特性;
冲压弯曲等热加工性好,可用于冲裁工艺。
1.1.2结构分析
1)该零件形状简单,应力左右对称。
2)零件圆角R=6mm,远大于最小倒角0.7t,因此无锐角。
3)孔距边界之间的最小孔边距很足够,且远大于一个板厚。
4)存在的最小孔(直径5mm)大于1倍的板厚,因此可以冲裁。
5)无凸出悬臂,槽宽6mm大于2倍的板厚。
1.1.3精度分析
图示零件尺寸公差要求约为ST6。
1.2冲裁工艺方案
该工件包括落料、冲孔两个基本工序,可有以下三种工艺方案[1]:
方案一:
先落料,后冲孔。
采用单工序模生产。
方案二:
冲孔—落料级进冲压。
采用级进模生产。
方案三:
冲孔—落料复合冲压。
采用复合模生产。
方案一模具结构简单,但需要两道工序两套模具,成本高而生产效率低,精度低,难以满足大批量、高精度的生产要求。
“单工序模”,是指在冲压的一次行程中,只能完成一个冲压工序的模具。
这一工程打完了之后,需要人工或用机械手把产品从模具里面取出来,然后放到下一站的模具里面继续生产,直到模具的最后一个工序打完,整个产品才算完成。
这种模具维修起来简单,但生产起来费时费力,需要花费较多的人工和时间成本,产品报废率较高
方案二只需要一副模具,生产效率高,但结构复杂,制造困难,成本高,且必须保证条料或带料的准确定位才可能保证冲压件的质量。
级进模的缺点是结构复杂,制造精度高,周期长,成本高。
因为级进模是将工件的内、外形逐次冲出的,每次冲压都有定位误差,较难稳定保持工件内、外形相对位置的一次性。
但精度高的零件,并非全部轮廓的所有内、外形相对位置要求都高,可以在冲内形的同一工位上,把相对位置要求高的这部分轮廓同时冲出,从而保证零件的精度要求。
方案三也只需一套模具,工作精度及生产效率都比较高,模具制造相对简单,制件精度高,采用倒装复合模能够有效的清理模具上的冲孔废料,操作不方便。
优点:
①工件同轴度较好,表面平直,尺寸精度较高;
②生产效率高,且不受条料外形尺寸的精度限制,有时废角料也可用以再生产。
缺点是:
模具零部件加工制造比较困难,成本较高,并且凸凹模容易受到最小壁厚的限制,而使得一些内孔间距、内孔与边缘间距较小的下件不宜采用。
所以经过比较,采用方案三最为合适。
二、冲裁工艺设计计算
2.1凸、凹模间隙值的确定
凸、凹模间隙对冲裁件断面质量、尺寸精度、模具寿命以及冲裁力、卸料力等有较大影响。
所以必须选择合理的间隙(图2-1)。
合理间隙值确定的方法如下。
图2-1冲裁模间隙
(1)理论确定法
依据上下裂纹重合,用几何方法推导,实用上意义不大。
(2)经验确定法
查表2-1和表2-2。
查表注意点如下。
①对冲件质量要求高时选用较小间隙值,查表2-1。
②对冲件质量要求一般时采用较大间隙,查表2-2。
本零件公差要求为ST6,采用2倍的小间隙值,查表2-1得Z的尺寸范围为(0.320mm~0.400mm)。
表2-2冲裁模初始双面大间隙Z
表2-1冲裁模初始双面小间隙Z
2.2凸、凹模刃口尺寸的确定
2.2.1确定凸、凹模刃口尺寸的原则
①设计落料模应先确定凹模刃口尺寸,以凹模为基准,间隙取在凸模上,即冲裁间隙通过减小凸模刃口尺寸来取得。
设计冲孔模先确定凸模刃口尺寸,以凸模为基准,间隙取在凹模上,冲裁间隙通过增大凹模刃口尺寸来取得。
②考虑刃口的磨损对冲件尺寸的影响:
刃口磨损后尺寸变大,其刃口的基本尺寸应接近或等于冲件的最小极限尺寸;
刃口磨损后尺寸减小,应取接近或等于冲件的最大极限尺寸。
③不管落料还是冲孔,冲裁间隙一般选用最小合理间隙值(Zmin)。
④考虑冲件精度与模具精度间的关系,在选择模具制造公差时,既要保证冲件的精度要求,又要保证有合理的间隙值。
一般冲模精度较冲件精度高2~3级。
⑤工件尺寸公差与冲模刃口尺寸的制造偏差原则上都应按“人体”原则标注为单向公差,所谓“人体”原则,是指标注工件尺寸公差时应向材料实体方向单向标注。
但对磨损后无变化的尺寸,一般标注双向偏差。
2.2.2凸、凹模分别加工时的工作部分尺寸
图2-2零件尺寸公差
落料件的尺寸为D-Δ0,冲孔件尺寸为d0-Δ,冲制件上孔距为L±
Δ2两孔。
查ST公差等级表得图2-2。
落料:
DA=(Dmax-xΔ)0+δA
DT=(Dmax-xΔ-Zmin)-δT0
冲孔:
dT=(dmax+xΔ)-δT0
dA=(dmax+xΔ+Zmin)0+δA
孔心距:
Ld=Lmin+0.5Δ±
0.125Δ=L±
18Δ
表2-3冲模制造精度与冲裁件精度之间的关系
式中DT,DA——落料凸、凹模的刃口尺寸,mm;
dT,dA——冲孔凸、凹模的刃口尺寸,mm;
Dmax——落料件的最大极限尺寸;
Dmin——冲孔件孔的最小极限尺寸;
表2-4凸、凹模刃口尺寸表
X——磨损系数,工件精度ST12,x取0.75;
Δ——制件的制造公差,mm;
L,Ld——工件孔心距和凹模孔心距的公称尺寸;
δT,δA——凸、凹模的制造公差,查表2-3得取IT7和IT8。
落料件尺寸
冲孔件尺寸
孔距
零件尺寸
12-0.10
50+0.06
54-0.2+0.2
22-0.12+0.12
84-0.2+0.2
凸模刃口尺寸
11.605-0.020
5.045-0.020
54-0.025+0.025
22-0.015+0.015
84-0.025+0.025
凹模刃口尺寸
11.9250+0.02
5.3650+0.02
最大间隙
0.36
0.05
0.03
经过校核,凸、凹模之间的间隙符合设计。
2.3毛坯排样方案设计
2.3.1排样方案时应遵循的原则
①公差要求较严的零件,排样时工步不宜太多。
以减小累积误差保证零件精度。
②零件孔距公差要求较严时,应尽量在同一工步冲出或在相邻工步冲出。
③对孔壁较小的冲裁件,其孔可以分步冲出,以保证凹模孔壁的强度。
④适当设置空工位,以保证模具具有足够的强度,并避免凸模安装时相互干涉,同时也便于试模、调整工序时用。
⑤尽量避免复杂型孔,对复杂外形零件的冲裁,可分步冲出,以减小模具制造难度。
⑥零件较大或零件虽小但工位较多时,应尽量减少工位数,可采用连续一复合成形的排样法,以减小模具轮廓尺寸。
⑦当材料塑性较差时,在有弯曲工步的连续成形排样中,必须使弯曲线与材料纹向成一定夹角。
2.3.2搭边值以及料条宽度的确定
毛坯最大尺寸96mm,不算太小,为保证冲裁件的质量、模具寿命和操作方便,采用有搭边,单排排样,根据卸料方式、制件长度和厚度。
查表2-5得如下图2-3搭边值。
图2-3排样
料条宽度:
B=Dmax+2a=96+2×
1.76=99.52≈99.6mm
Dmax——条料宽度方向冲裁件的最大尺寸。
mm
表2-5搭边a和a1的数值(低碳钢)
2.3.3材料利用率计算
冲裁件的实际面积与所用板料面积的百分比称为材料利用率,它是衡量合理利用材料的技术经济指标。
一个步距内的材料利用率可用下式表示:
η=ABS×
100%
A——为一个步距内冲裁件的实际面积(mm2)
B——为条料宽度(mm)
S——为步距(mm)
若考虑到料头、料尾和边余料的消耗,则一张板料(或带料、条料)上总的材料利用率为
η2=nA1BL×
n——为一张板料(或带料、条料)上的冲裁件总数目
A1——为一个冲裁件的实际面积(mm2)
B——为板料(或带料、条料)宽度(mm)
L——为板料(或带料、条料)长度(mm)
所以
η2=A1BS×
100%=792.1999.6×
13.76×
100%=57%
三、冲裁力及压力中心计算
3.1冲裁工艺力的计算
3.1.1冲裁力
冲裁模设计时,为了合理地设计模具及选用设备。
必须计算冲裁力。
压力机的吨位必须大于所计算的冲裁力。
通常说的冲裁力是指冲裁力的最大值,它是选用压力机和设计模具的重要依据之一。
用普通平刃口模具冲裁时,其冲裁力F一般按下式计算
F=KLtτb=1.3×
360.82×
2×
416N=3.9×
105N
F——冲裁力:
L——冲裁周边长度:
T——材料厚度;
τb——材料抗剪强度,304不锈钢τb=416MPa;
K——系数。
系数K是考虑到实际生产中,模具间隙位的波动和不均匀、刃口的磨损、材料力学性能和厚度波动等因素的影响而给出的修正系数。
一般取K=1.3。
为计算简便,也可按下式估算冲裁力
F≈Ltσb=360.82×
520N=3.75×
σb——材料抗拉强度,304不锈钢σb=520MPa;
3.1.2降低冲裁力的方法
当冲裁力过大时,可用下述方法降低。
图3-1阶梯凸模布置法
①加热冲裁:
加热冲裁易破坏工件表面质量同时会产生热变形,精度低,因此应用比较少。
此法只适于材料厚度大,表面质最及精度要求不高的零件。
②阶梯凸模冲裁:
在多凸模冲裁中,将凸模做成不同高度,使各凸模冲裁力的最大峰值不同时出现,结构如图3-1所示。
对于薄材料(t<3mm),H一般取材料厚度t。
③斜刃冲裁:
为了得到平整地零件,落料时凹模做成一定斜度,凸模为平刃口,而冲孔时,则凸模做成一定斜度,凹模为平刃口。
一般在大型冲件及厚板冲裁中采用。
3.1.3卸料力、推件力和顶件力
卸料力、推件力和顶件力一般采用经验公式进行计算
F——冲裁力;
KX,KT,KD——卸料力、推件力及顶件力系数,见