冲压模具设计及其工艺分析Word文件下载.docx
《冲压模具设计及其工艺分析Word文件下载.docx》由会员分享,可在线阅读,更多相关《冲压模具设计及其工艺分析Word文件下载.docx(25页珍藏版)》请在冰豆网上搜索。
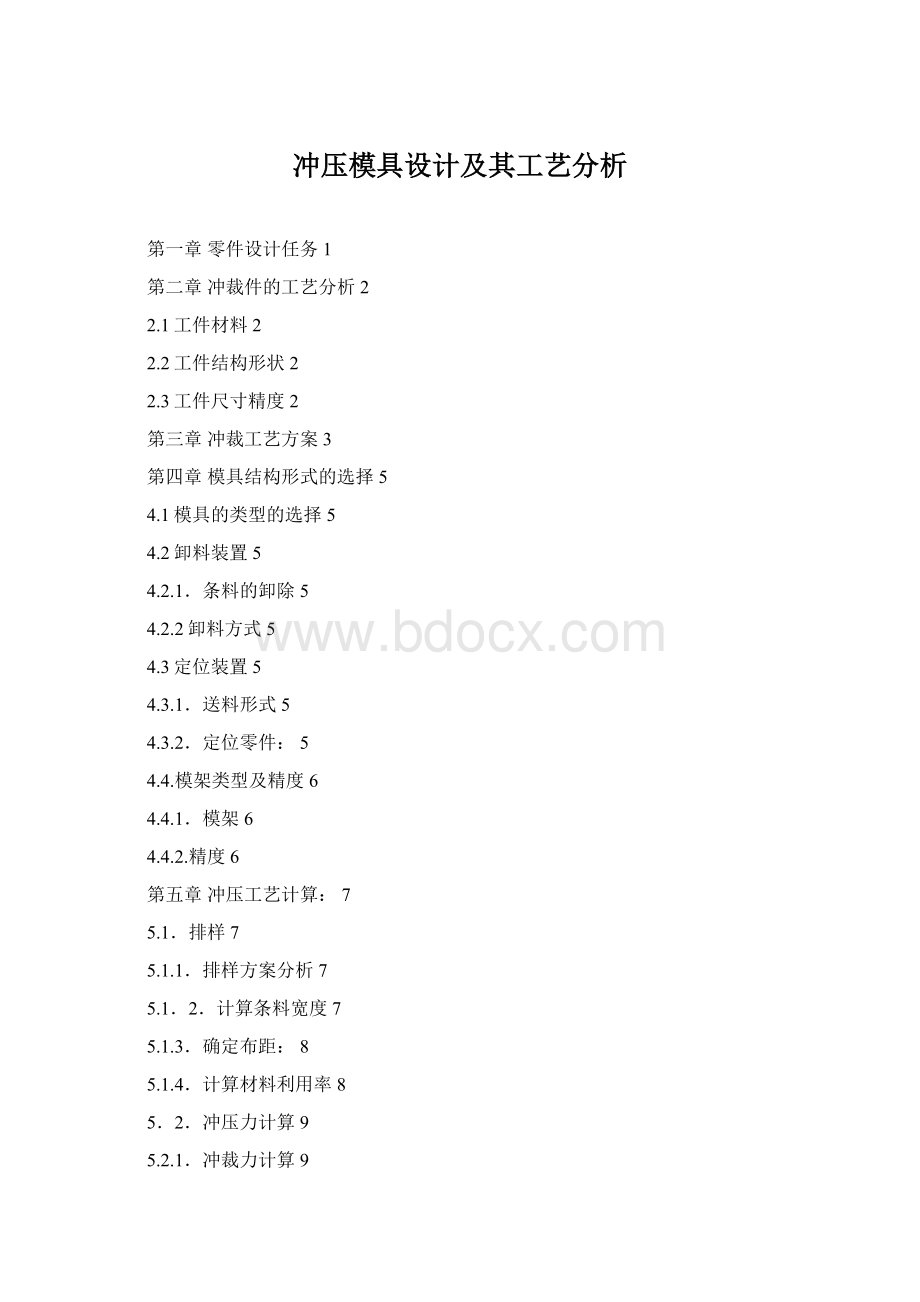
5.3.压力中心的计算11
5.4.模具工作部分尺寸及公差12
5.4.1.落料尺寸大小为12
5.4.2.冲孔尺寸大小为13
第六章主要零部件设计14
6.1.凹模的设计14
6.1.1.落料凹模14
6.1.2.冲孔凹模的设计16
6.2.凸模的设计17
6.2.1.冲孔圆形凸模:
17
6.2.2.腰孔的设计18
6.2.3.落料凸模18
6.2.4.凸模的校核:
19
6.3.卸料板的设计20
6.4.固定板的设计21
6.4.1.凹模固定板:
21
6.4.2.凸模固定板:
22
6.5.模架以及其他零部件的选用23
第7章校核模具闭合高度及压力机有关参数24
7.1校核模具闭合高度24
7.2冲压设备的选定24
第8章设计并绘制模具总装图及选取标准件25
第9章结论26
参考文献27
第一章零件设计任务
零件简图:
如图1-1所示
材料:
10号钢
材料厚度:
2mm
未标注尺寸按照IT10级处理.
第二章冲裁件的工艺分析
2.1工件材料
由图1-1分析知:
10#钢为优质碳素结构钢,具有良好的塑性性、焊接性以及压力加工性,主要用于制作冲击件、紧固件,如垫片、垫圈等。
适合冲裁加工。
2.2工件结构形状
工件结构形状相对简单,有四个圆孔,孔与边缘之间的距离满足要求,料厚为2mm满足许用壁厚要求(孔与孔之间、孔与边缘之间的壁厚),可以冲裁加工。
2.3工件尺寸精度
根据零件图上所注尺寸,工件要求不高,尺寸精度要求较低,采用IT14级精度,普通冲裁完全可以满足要求。
根据以上分析:
该零件冲裁工艺性较好,综合评比适宜冲裁加工。
第三章冲裁工艺方案
完成此工件需要冲孔、落料两道工序。
其加工工艺方案分为以下3种:
1.方案一:
单工序模生产。
先冲孔,后落料;
2.方案二:
级进模生产。
冲孔—落料级进冲压;
3.方案三:
复合模生产。
冲孔—落料复合冲压。
各模具结构特点及比较如下表3-1:
表3-1各类模具结构及特点比较
模具种类比较项目
单工序模
(无导向)(有导向)
级进模
复合模
零件公差等级
低
一般
可达IT13~IT10级
可达IT10~IT8级
零件特点
尺寸不受限制厚度不受限制
中小型尺寸厚度较厚
小零件厚度0.2~6mm可加工复杂零件,如宽度极小的异形件
形状与尺寸受模具结构与强度限制,尺寸可以较大,厚度可达3mm
生产效率
较低
工序间自动送料,可以自动排除制件,生产效率高
冲件被顶到模具工作表面上,必须手动或机械排除,生产效率较低
安全性
不安全,需采取安全措施
比较安全
模具制造工作量和成本
比无导向的稍高
冲裁简单的零件时,比复合模低
冲裁较复杂零件时,比级进模低
适用场合
料厚精度要求低的小批量冲件的生产
大批量小型冲压件的生产
形状复杂,精度要求较高,平直度要求高的中小型制件的大批量生产
根据分析结合表分析:
方案一模具结构简单,制造周期短,制造简单,但需要两副模具,成本高而生产效率低,难以满足大批量生产的要求。
方案二只需一副模具,生产效率高,操作方便,精度也能满足要求,模具制造工作量和成本在冲裁简单的零件时比复合模低。
方案三只需一副模具,制件精度和生产效率都较高,且工件最小壁厚大于凸凹模许用最小壁厚模具强度也能满足要求。
冲裁件的内孔与边缘的相对位置精度较高,板料的定位精度比方案二低,模具轮廓尺寸较小。
综上对上述三种方案的分析比较,该工件的冲压生产采用方案二为佳。
第四章模具结构形式的选择
4.1模具的类型的选择
由冲压工艺分析可知,采用级进模方式冲压,所以模具类型为级进模。
4.2卸料装置
4.2.1.条料的卸除
因采用级进模生产,故采用向下落料出件。
4.2.2卸料方式
考虑零件尺寸较大,厚度较高,采用固定卸料方式,为了便于操作,提高生产率。
4.3定位装置
4.3.1.送料形式
因选用的冲压设备为开式压力机且垂直于送料方向的凹模宽度B小于送料方向的凹模长度L故采用横向手动送料方式,即由右向左(或由左向右)送料既能满足生产要求,又可以降低生产成本,提高经济效益。
零件尺寸较大,厚度较高,保证孔的精度及较好的定位,宜采用导料板导向,导正销导正,为了提高材料利用率采用始用挡料销和固定挡料销。
4.4.模架类型及精度
4.4.1.模架
1.若采用中间导柱模架,则导柱对称分布,受力平衡,滑动平稳,但只能一方送料;
2.若采用对角导柱模架,则受力平衡,滑动平稳,可纵向或横向送料;
3.若采用后侧导柱导柱模架,可三方送料,操作者视线不被阻挡,结构比较紧凑的,但模具受力不平衡,滑动不平稳。
综上,结合本冲孔、落料级进模的特点,决定采用后侧导柱模架。
4.4.2.精度
由于零件材料较厚,尺寸较大,冲裁间隙较小,又是级进模因此采用导向平稳的中间导柱模架,考虑零件精度要求不是很高,冲裁间隙较小,因此采用Ⅰ级模架精度。
5.1.排样
5.1.1.排样方案分析
方案一:
有废料排样沿冲件外形冲裁,在冲件周边都留有搭边。
冲件尺寸完全由冲模来保证,因此冲件精度高,模具寿命高,但材料利用率低。
方案二:
少废料排样因受剪切条料和定位误差的影响,冲件质量差,模具寿命较方案一低,但材料利用率稍高,冲模结构简单。
方案三:
无废料排样冲件的质量和模具寿命更低一些,但材料利用率最高。
通过上述三种方案的分析比较,综合考虑模具寿命和冲件质量,该冲件的排样方式选择方案一为佳。
考虑模具结构和制造成本有废料排样的具体形式选择直排最佳。
5.1.2.计算条料宽度
根据零件形状,查<
<
冲压模具设计手册>
>
工件之间搭边值a=1.2mm,工件与侧边之间搭边值a1=1.5mm,条料是有板料裁剪下料而得,为保证送料顺利,规定其上偏差为零,下偏差为负值—△
公式(5-1)
式中:
Dmax—条料宽度方向冲裁件的最大尺寸;
a1---冲裁件之间的搭边值;
b1---侧刃冲切得料边定距宽度;
(其值查表6)可得△=2.0mm。
△—板料剪裁下的偏差;
(其值查表5)可得△=0.6mm。
B0△=75+2×
1.5+2×
2.0
=82.00-0.60mm
故条料宽度为82.0mm。
送料步距S:
条料在模具上每次送进的距离称为送料步距,每个步距可冲一个或多个零件。
进距与排样方式有关,是决定侧刃长度的依据。
条料宽度的确定与模具的结构有关。
级进模送料步距S
公式(5-2)
Dmax零件横向最大尺寸,a1搭边
S=75+1.5=76.5mm
排样图如图2所示。
5.1.4.计算材料利用率
一个步距内的材料利用率
η=A/BS×
100%公式(5-3)
式中 A—一个步距内冲裁件的实际面积;
B—条料宽度;
S—步距;
一个步距内冲裁件的实际面积
A=π×
37.52-π×
13.52-3×
π×
3.752-3(π×
302×
34/360-π×
26.252×
34/360)
=3807.73539mm2
所以一个步距内的材料利用率
Η=A/BS×
100%
=3807.73539/(76.5×
82)×
100%
=60.7%
考虑料头、尾料和边角余料消耗,一张板材上的总利用率η总为
η总=nA1/LB×
100%公式(5-4)
式中n—一张板料上冲裁件的总数目;
A1—一个冲裁件的实际面积;
L—板料长度;
B—板料宽度。
查板材标准,宜选用850mm×
1700mm的钢板,每张钢板可剪裁为11张条料(82mm×
1700mm),每张条料可以冲25个工件,所以每张钢板的材料利用率
η总=nA1/LB×
=25×
3807.73539/82×
1700×
=68.3%
根据计算结果知道选用直排材料利用率可达68.3%,满足要求。
5.2.冲压力计算
5.2.1.冲裁力计算
用平刃冲裁时,其冲裁力F一般按下式计算:
公式(5-5)
F—冲裁力;
L—冲裁周边长度;
t—材料厚度;
τb—材料抗剪强度;
10钢τb的值查《《冲压成型工艺与模具设计》》附录表2为255-333Mpa,取τb=300Mpa
K—系数;
一般取K=1.3。
1、冲孔力计算
冲孔周长:
L=π×
27+3π×
3.75×
2+3π(26.25+33.75)×
34/360+2×
76.5+2×
12
=764.98mm
所以冲孔力
F=KLtτb=1.3×
764.98×
2×
300
=596.69kN
2.落料力的计算
落料周长
落料冲裁力F2=KLtτb=1.3×
75×
300=183.78kN。
5.2.2.卸料力、顶件力的计算
一般按以下公式计算:
卸料力
公式(5-6)
顶件力
公式(5-7)
(为卸料力系数,其值查表5-1可得)
所以总冲压力
公式(5-8)
表5-1卸料力、推件力和顶件力系数
料厚t/mm
KX
KT
KD
钢
≤0.1
>0.1~0.5
>0.5~2.5
>2.5~6.5
>6.5
0.06~0.075
0.045~0.055
0.04~0.05
0.03~0.04
0.02~0.03
0.1
0.063
0.050
0.045
0.025
0.14
0.08
0.06
0.05
0.03
铝、铝合金
纯铜,黄铜
0.025~0.08
0.02~0.06
0.03~0.07
0.03~0.09
由,即冲压时工艺力的总和不能大于压力机公称压力的50%-60%,取,则公称压力.初选压力机的公称压力为1600Kn,即JA21-160型压力机。
5.3.压力中心的计算
用解析计算法求出冲模压力中心。
X0=(L1x1+L2x2+…Lnxn)/(L1+L2+…Ln)公式(5-9)
Y0=(L1y1+L2y2+……Lnyn)/(L1+L2+…+Ln)
用解析法计算压力中心时,先画出凹模形口图,如图5-3所示。
在图中将XOY坐标系建立在建立在图示对称中心线上,将冲裁轮廓线按几何图形分解成L1~L5共3组基本线段(注:
由于图中3个圆弧形孔均以一个点为圆心的等分列阵排列,所以其几何图形为一组),用解析法求得该模具压力中心的坐标。
由以上计算结果可以看出,该工件冲裁力不大,压力中心偏移坐标原点O较小,为了便于模具的加工和装配,模具压力中心依然选在坐标原点。
图5-3
5.4.模具工作部分尺寸及公差
5.4.1.落料尺寸大小为
为保证冲出合格冲件。
冲裁件精度IT10