7第七章 叶片局部设计优化PPT文件格式下载.pptx
《7第七章 叶片局部设计优化PPT文件格式下载.pptx》由会员分享,可在线阅读,更多相关《7第七章 叶片局部设计优化PPT文件格式下载.pptx(36页珍藏版)》请在冰豆网上搜索。
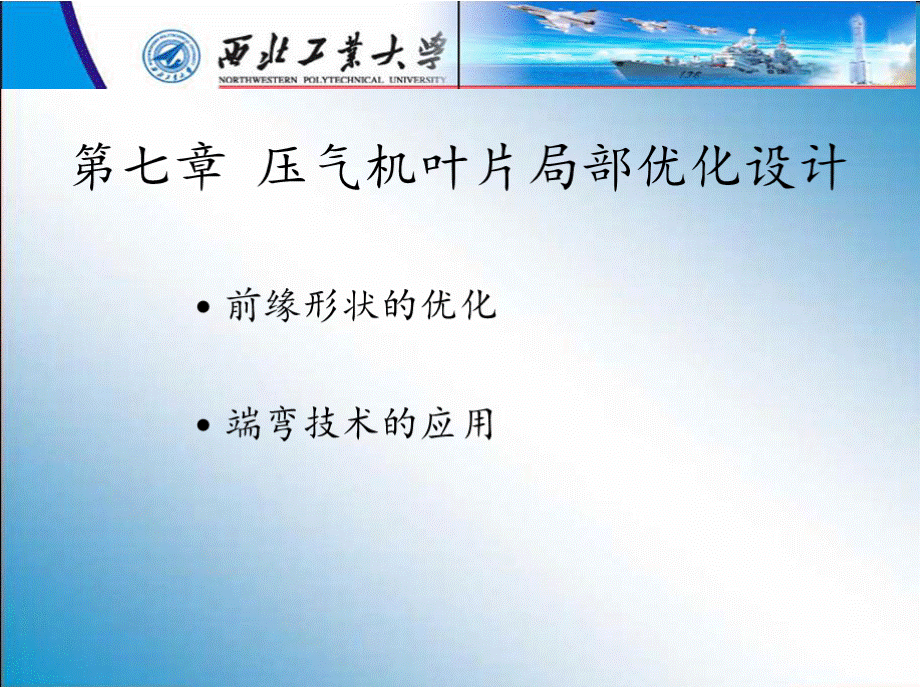
如果来流的湍流度较小,易在A点发生层流分离。
分离区内的扰动常常诱发流动转捩,由于湍流携带的能量比层流大,分离的流动转捩后重新附着,形成分离泡。
当来流攻角较小时,前缘表向的过度膨胀较弱,分离泡较短,对叶片的气动性能影响不大;
当来流攻角增大,前缘表面的过度膨胀加重,前缘与吸力向的切点处的逆压梯度增强;
如果来流湍流度、雷诺数较小,层流分离无法重新刚着,会发生伞叶向分离,叶片增压能力大为减小,造成流动堵塞,诱发失速。
环绕前缘后的流动往往严重过度膨胀,压力远低于叶片主流区的压力。
如图1,A点是吸力向与前缘圆弧相切的切点,A点后叶而直线段上的压力与叶片主流区的压力相近。
为了优化前缘形状改善叶片性能应当抑制前缘表向的过度膨胀从而降低吸力峰减小吸力峰内的逆压梯度避免前缘表面发生层流分离。
图3是本文研究的压气机各种前缘形状。
椭圆形前缘可以改善叶片的性能的原因在于:
椭圆形前缘与圆弧形前缘不同,椭圆形前缘表面的曲率半径从前缘前端点到与叶身的切点,是逐步增大的,而不是恒定的。
由公式
(1)可见,椭圆形前缘表向曲率半径逐步增大,可以减小前缘表面流动的法向压力梯度。
抑制前缘表面的过度膨胀,减弱吸力峰(图4)。
与圆弧形前缘相比,采用椭圆形前缘,叶片的工作范围士r大了约20%,流动损失也有所下降。
(图5),2.椭圆形前缘,对比椭圆(a/b-2)、椭圆(a/b-1)前缘的表面Ma1分布如图1所示。
相同厚度的椭圆形前缘。
长短轴比(a/b)越大,前缘吸力峰越弱,相应叶片的气动性能越好(图5)。
原因在于,长短轴比大的椭圆形前缘曲率半径r增大的幅度大,抑制前缘表向过度膨胀的能力增强,因此改善叶片性能的能力更强。
3.带平台的圆弧形前缘,椭圆形前缘可改善叶片性能,扩大工作范围,降低流动损失,但是椭圆形前缘的加工较困难。
应用到工程实践中还有一定难度。
本节提出了在圆弧形前缘上加工平台,得到一种新型前缘形状,既可以有效地抑制前缘表向的过度膨胀以改善叶片性能,又易于加工。
图6是在带平台的圆弧形前缘的前缘吸力面直线段AB上的压力与叶片主流区的压力相近。
OA段表向流动的过度膨胀,在AB直线段受到抑制。
前缘表面的流动,在A点速度下降,压力上升,形成一个弱吸力峰,同样在B点形成另一个弱吸力峰。
如图7所示,平台AB两端形成的两个弱吸力峰,取代了原始圆弧形前缘吸力面上的单个强吸力峰,形成带平台前缘吸力向多个弱吸力峰的典形表面速度分布。
带平台前缘的平台定位由两个参数决定:
平台的前端在原始圆弧形前缘上的位置;
倾斜角平台相对于水平方向的夹角(平台的两端用倒角光滑过渡)如下图8所示:
平台的前端在原始圆弧形前缘上的位置,理论上越接近滞止点,平台可以更及时地抑制前缘表向的过度膨胀,达到更好的气动效果。
考虑到当平台的倾斜角一定时。
平台切入过深会破坏前缘的强度。
平台前端的位置应在保证气动要求的前提下。
尽量靠后以保证前缘的强度。
平台的倾斜角,决定了平台两端的吸力峰的强弱分布。
平台倾斜角增大,平台后端的吸力峰比平台前端的吸力峰强;
反之,平台前端的吸力峰比后端的吸力峰强。
一个合适的倾斜角应当使平台前后端的吸力峰强度相近,或前端的吸力峰比后端的吸力峰略弱。
4.结论,
(1)优化前缘形状的机理为,抑制前缘表向的过度膨胀,从而降低吸力峰,减小吸力峰内的逆压梯度避免叶片表面的层流分离,改善叶片气动性能;
(2)椭圆形前缘可以改善叶片性能的原因在于,椭圆形前缘从前缘前驻点到与叶身的切点,曲率半径是逐步增大的。
曲率半径逐步增大,可以减小前缘表面流动的法向压力梯度,抑制前缘表向的过发膨胀,削弱吸力峰;
(3)带平台的圆弧形前缘在平台的两端形成两个弱吸力峰,取代了原始圆弧形前缘上的单个强吸力峰;
(4)带平台前缘的平台定位由两个参数决定:
一是平台的前端在原始圆弧形前缘上的位置;
二是倾斜角平台相对于水平方向的灾角(平台的两端川倒角光滑过渡);
(5)在圆弧形前缘上加工个平台就可以得到与长短轴比为2(b/a=2)的椭圆形前缘相近的优化效果。
由于带平台的圆弧形前缘优良的气动特性和易于加工的特点,在工程实践应用中会很有发展前途。
第二节端弯技术的应用,轴流压气机是在三维、可压缩、粘性、非定常等气动环境中工作的。
而气动计算时假设为二维、不可压缩、无粘、定常的气动环境。
这就导致计算的流场与实际流场不一致,使叶片造型偏离实际流动。
端弯的目的在于按实际流动情况对叶片造型、气动计算进行修正。
60年代Smith等发现:
多级轴流压气机中轴向速度沿径向分布的不均匀程度逐级增大,从第四级开始轴向速度沿径向分布的形状不再改变,出现了所谓“重复级”现象,如图1所示。
该“重复级”的概念,给端弯设计技术的普遍推广提供了依据。
据此,对我们生产的涡喷发动机叶片从第四级(即高压压气机的第一级)开始,按实际气流情况在叶片两端壁处重新修改设计了能改善压气机端壁区性能的叶型形状和速度三角形。
由于工厂生产中同时改变转、静子叶片、重新制造难度大,成本高,故把考虑附面层流动对转、静子叶片的影响集中在静子叶片上处理,使静子叶型前缘适合于前排转子叶片的实际出口气流条件,而叶型的后缘,使用了加大静叶出口预旋角,使在较小的轴向速度下,以保持下排转子设计进口气流角。
这就需要局部扭转接近端壁区的叶型剖面,致使叶片两端壁附近叶型弯扭很大,称之谓“端弯”叶片。
1.端弯设计对压气机性能影响的分析,多级压气机中大约总损失的一半与端壁附面层有关,采用端弯技术主要目的是降低端壁区的损失以提高压气机效率,扩大压气机稳定工作裕度。
在叶轮机中,由于粘性的作用,机匣壁面和轮毂处附面层区域内气流流动及二次流形成的展向掺混等,使多级压气机中实际的轴向速度沿叶展分布如图2所示。
轴向速度偏离设计值,引起了叶栅攻角偏离设计值。
在叶片两端壁附近轴向速度减小,攻角增大;
而为保持流量连续,叶片中部轴向速度必须增大,引起叶栅攻角减小。
从叶栅特性图3可知,设计时选取的叶栅工作点为A。
但实际工作时,近端壁区的叶栅工作点偏移到B点,基元叶栅的转折角增加,因而加功量增大,损失增,基元效率下降。
而叶展中部区域因轴向速度增大、攻角减小、其工作点偏离到C点,加功量减小、基元效率下降。
实际压气机出口的总温和基元级效率变化呈图4所示。
近端壁区的效率下降,使级平均效率降低。
采用端弯技术后,根据实际压气机中沿叶展向轴向速度分布规律来修改叶型构造角(见图5)。
使静子叶片两端进口构造角适应于轴向速度降低后的气流角,从而使静子叶片的工作点与原设计选定工作点相一致;
在静子出口,用设置(或改变)预旋的方法使转子进口相对气流角与设计值相一致。
在图5中,假设转子或静子出口气流角并不因攻角的改变而变化。
这在一定的攻角变化范围内是符合实际情况的。
采用静子端弯技术后,转、静子叶栅的工作点,都从工作点B返回到设计点A。
与未采用静子端弯技术时的原压气机相比较,端壁区内的基元级效率提高,加功量减少。
出口湿度沿叶展的分布将趋于均匀。
即端壁区内的出口温度将降低,端壁区加功量的减少,可毹引起出口总压的降低,但由于该处基元级效率的提高,其降低量是不大的。
在叶展中部,由于气流轴向速度大于设计值,静子叶型的构造角需按与图5相反的方向修改,见图6:
图6叶展中部速度三角形的变化,2.高压压气机性能试验,将某原型高压压气机与第四、五级静子叶片采用端弯技术修型后的高压压气机在同一台压气机试验器上做对比试验。
压气机性能试验结果如图7(a)所示。
从图中可明显看到,采用端弯技术后,压气机接近失速时的压比,流量特性显著改善,压气机喘振边界明显上移。
在各转速下压气机效率、压比明显提高;
仅流量偏小约0.2kg/s。
在n=1.0、节气门角=56时,原=0.823,喘=O.858,提高了4.3。
各转速下喘振裕度均有增加,按设计工作点压比=2.654,按各自堵塞流量GB原=23.6kg/s,GB喘=23.42kg/s,计算得喘振裕度SM原=9%SM喘=14%,裕度增加了SM=5%。
端弯高压压气机压比咄在各转速下均有提高。
n=1.0,相同节气门=56时压比由2.642提高到2.718,端弯的压比提高了2.9%。
高压压气机空气流量在n=1.0时原型流量GBH原=23.6kgs,端弯流量GBH端=23.42kg/s,流量差GBH=0.76%。
在另一台五级高压压气机上采用了同样的修改设计。
修改前、后压气机性能对比试验结果见图7(b)。
由图可知,各转速下压气机稳定工作裕度均有增加,喘振边界明显上移,节气门=53时,n=1.0原=2.718,喘=2.656,端弯压比增加2.3%;
喘=0.890,原=0.862,端弯效率提高3.4%。
3.高压流场测量,高压压气机流场测量,主要由五孔探针完成。
沿径向移动共测了13个位置。
某型三级高压压气机测量结果如图8、图9所示。
图8(a)、图8(b)、图8(c)、图8(d)为气流流经第四级端弯静叶后,在第五级转子出口测得的向速度、总压、静压、总温沿径向分布图:
图9(a)、图9(b)、图9(c)、图9(d)为流经第四五级端弯静叶片在第六级静叶后(即高压压气机出口)测得的轴向速度、总压、静压、总温沿叶展向分布图。
由以上组图可看出,气流流经两级端弯静叶后沿叶展向温度、压力、轴向速度分布的变化比流经一级端弯静叶后更为明显。
端弯的高压出口总、静压比原型的高;
总温Tf略低且趋于均匀分布。
某型五级高压压气机测试结果如图10、图11和图12。
图10为各转速下高压压气机各级间静压分布曲线。
可以看出,五级高压压气机的流场分布与三级的趋势一致。
图11为各转速下高压压气机出口压力分布对比曲线。
图12为各转速下高压压气机出口温度分布对比曲线。
4.结论,在排气边缘采用加大静子出口预旋角,使后排叶片进口相对气流角与叶片构造角相适应;
在进气边缘则减小前缘进口构造角,以适应前排出口气流角。
在端壁区沿叶展向因各截面附面层及二次流对流作用程度不同,需分别选用合适的速度三角形,以适合实际的流动。
在接近端壁区采用局部扭转剖面,成端壁弯曲,由于两端壁处轴向速度的减少,为保持流量的连续,在叶展中部轴向速度要加大,由此叶展中部各剖面的速度三角形也相应改变,剖面形状也改变。
两种涡喷发动机的高压压